压铸模具设计基本流程
压铸模具的设计步骤

压铸模具的设计步骤如下:
1、压铸件工艺性分析,包括合金、铸件结构和压铸件技术分析;
2、工艺方案设计,包括分型面、浇口位置、浇注排溢系统、型腔数量、抽芯方案和数量、压铸件顶出方案、压铸机选用等方面确定和设置;
3、浇注和排溢系统设计。
包括工艺参数确定、内浇口尺寸的计算、浇注系统形状尺寸确定和排气槽渣包的位置尺寸计算;
4、压铸模结构设计。
包括镶块、型腔、抽芯、顶出、冷却水、加热管道等方面的设计。
5、压铸模具总图的设计。
6、压铸模具零件的设计。
压铸件工艺流程
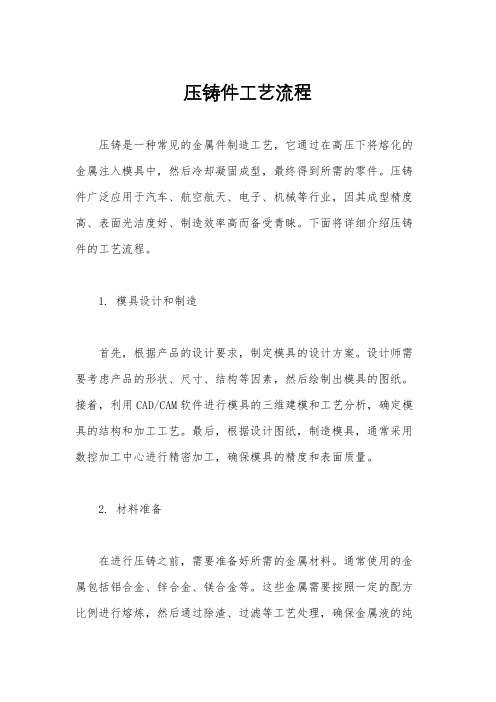
压铸件工艺流程压铸是一种常见的金属件制造工艺,它通过在高压下将熔化的金属注入模具中,然后冷却凝固成型,最终得到所需的零件。
压铸件广泛应用于汽车、航空航天、电子、机械等行业,因其成型精度高、表面光洁度好、制造效率高而备受青睐。
下面将详细介绍压铸件的工艺流程。
1. 模具设计和制造首先,根据产品的设计要求,制定模具的设计方案。
设计师需要考虑产品的形状、尺寸、结构等因素,然后绘制出模具的图纸。
接着,利用CAD/CAM软件进行模具的三维建模和工艺分析,确定模具的结构和加工工艺。
最后,根据设计图纸,制造模具,通常采用数控加工中心进行精密加工,确保模具的精度和表面质量。
2. 材料准备在进行压铸之前,需要准备好所需的金属材料。
通常使用的金属包括铝合金、锌合金、镁合金等。
这些金属需要按照一定的配方比例进行熔炼,然后通过除渣、过滤等工艺处理,确保金属液的纯净度和稳定性。
3. 熔炼和保温将准备好的金属材料加入熔炉中进行熔炼,直至达到所需的温度和流动性。
然后将熔融金属倒入保温炉中进行保温,以保持金属液的温度和流动性,为后续的压铸工艺做准备。
4. 压铸成型在保温炉中保持金属液的温度和流动性后,将金属液注入压铸机的射出室。
通过高压注射系统,将金属液压入模具腔内,填充整个模腔。
在一定的压力和温度下,金属液在模具中凝固成型,形成所需的压铸件。
5. 冷却和固化在金属液填充模腔后,需要等待一定时间,让压铸件在模具中冷却和固化。
冷却时间的长短取决于金属的种类和厚度等因素。
在固化完成后,打开模具,取出成型的压铸件。
6. 修磨和处理取出的压铸件通常会存在一些毛刺、气孔等缺陷,需要进行修磨和处理。
通过去毛刺、抛光、喷砂等工艺,使压铸件的表面光洁度达到要求。
同时,还可以进行热处理、表面处理等工艺,提高压铸件的性能和表面质量。
7. 检验和包装最后,对成型的压铸件进行检验,包括尺寸、外观、化学成分等方面的检测。
合格后,对压铸件进行包装,通常采用防震防潮的包装方式,以确保产品的质量和运输安全。
压铸模具开发流程

压铸模具开发流程
1. 设计与概念阶段
- 与客户就产品要求进行沟通和确认
- 定义产品的功能和性能参数
- 进行产品的外观设计和结构设计
2. 模具设计阶段
- 根据产品设计进行模具结构设计
- 选择合适的模具钢材料
- 设计浇口、冷却系统、顶出系统等模具功能部件 - 进行模流分析和应力分析,优化模具设计
3. 模具制造阶段
- 加工模具零件
- 装配和调试模具
- 进行模具试模和优化改进
- 对模具进行热处理和机加工
4. 模具试生产阶段
- 安装模具在压铸机上
- 调试压铸工艺参数
- 生产小批量试制品
- 对产品进行检测和评估,并对模具进行修改完善
5. 量产阶段
- 正式投产
- 持续监控产品质量和模具状态
- 定期对模具进行维护保养
- 根据需求对模具进行改造或更新
在整个压铸模具开发过程中,需要密切关注客户需求,严格执行质量控制,确保模具的精度和性能,以满足产品的功能和质量要求。
同时,也要注重成本控制和工艺优化,提高模具的使用寿命和生产效率。
压铸模具设计教程
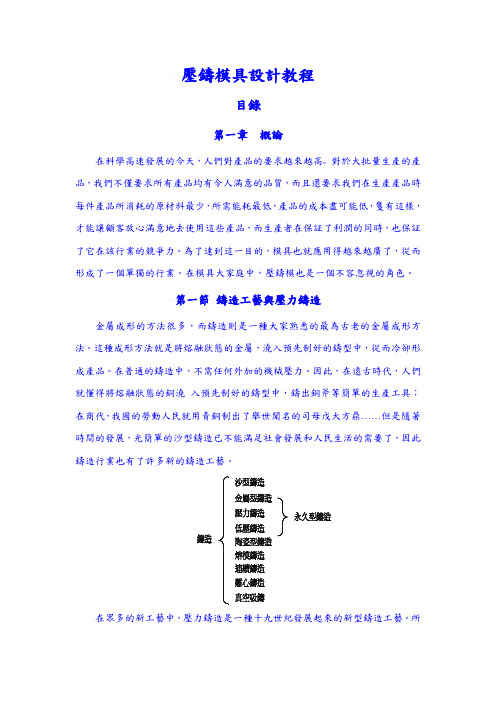
壓鑄模具設計教程目錄第一章概論在科學高速發展的今天,人們對產品的要求越來越高。
對於大批量生產的產品,我們不僅要求所有產品均有令人滿意的品質,而且還要求我們在生產產品時每件產品所消耗的原材料最少,所需能耗最低,產品的成本盡可能低,隻有這樣,才能讓顧客放心滿意地去使用這些產品,而生產者在保証了利潤的同時,也保証了它在該行業的競爭力。
為了達到這一目的,模具也就應用得越來越廣了,從而形成了一個單獨的行業。
在模具大家庭中,壓鑄模也是一個不容忽視的角色。
第一節鑄造工藝與壓力鑄造金屬成形的方法很多,而鑄造則是一種大家熟悉的最為古老的金屬成形方法。
這種成形方法就是將熔融狀態的金屬,澆入預先制好的鑄型中,從而冷卻形成產品。
在普通的鑄造中,不需任何外加的機械壓力。
因此,在遠古時代,人們就懂得將熔融狀態的銅澆入預先制好的鑄型中,鑄出銅斧等簡單的生產工具;在商代,我國的勞動人民就用青銅制出了舉世聞名的司母戊大方鼎……但是隨著時間的發展,光簡單的沙型鑄造已不能滿足社會發展和人民生活的需要了,因此鑄造行業也有了許多新的鑄造工藝。
和其他幾種鑄造和模鍛相比,它具有以下特性:第二節壓力鑄造與壓鑄模在壓力鑄造(Die Casting)成型工藝中,用於成型鑄件所使用的金屬模具稱為壓鑄模(Die-Casting Dies)。
壓力鑄造的最終產品是壓鑄件。
隨著壓鑄件在現代工業和日常生活中越來越廣泛的應用,人們對壓鑄件的質量,性能和使用范圍也提出了越來越高的要求。
降低壓鑄件的成本,在最低的材料消耗和制造費用的前提下達到結構的功能特性及滿足其使用要求,以期在壓鑄件的生產中獲得技術經濟性,這就是現代壓鑄生產的基本特征。
現代壓鑄生產中,壓鑄件的質量與壓鑄模,壓鑄設備及壓鑄工藝這三個要素的關系密不可分。
面在這三個要素中,壓鑄模是最為重要的,它的作用是雙重的:賦予熔化後的金屬液以期望的形狀、性能和質量,冷卻並頂出壓鑄成形的制件。
模具是決定最終產品性能、規格、形狀及尺寸精度的載體,壓鑄模是使壓鑄生產過程順利進行,保証壓鑄質量的不可缺少的工藝裝備,是體現壓鑄設備高效率、高性能和壓鑄工藝優質先進的具體實施者,也是工藝改進和新產品開發的決定性環節。
压铸模具设计步骤(3D)(精)

1.老方法:也就是最基本的方法COPY SURFACE,这是一位台湾教授教材上讲 得最多的一种方法;也是最土的方法!如果用此方法分一些复杂模具的话太麻 烦了! 2.切割法:许多时候,当我们做好分型面后进行分模才发现,分不开并且出 现了许多绿线线和红点点,这时我们可选择切割法,具体做法是:直接将分型面 复制一个后往前模方向延伸到前模仁的厚度,封闭起来生成前模仁,而后做一 实体为后模仁,用分模切掉前模部分,再用参考零件直接CUTOUT出后模仁型 腔来; 3.当然针对2所出现的情况,也可采用精度修改法来解决,适当的调整一下 精度,也可解决一些情况,还可在设计过程中调整模具精度和产品精度保持一 致,(最好是在CONFIG)中直接就设置为产品精度和模具精度保持一致; 4.补洞法:在做型面时,不要去COPY SURFACE(推荐使用),直接将有破孔 的地方做一些比较简单的曲面来堵住,有时曲面不太好做也可直接长出一块 0.01mm厚的实体来,然后再一些比较简单的大分型面来就可分出来; 5.裙边法:对于大部分的壳体类产品,建议使用裙边来做分型面,这样不仅 易分模而且往做出来的分型面比较漂亮;
六﹐COPY母模面﹕
MODIFY---MOD PART---F01---FEATER---CREAT-SURFACE---NEW---COPY DONE。 修补母模面﹐拆出母模。 七﹐处理母模仁 八﹐CUT OUT公模仁 九﹐作入子﹐斜销﹐滑块﹐套筒等零部件。 十﹐回头点检﹕ 1.有无干涉 2.有无倒勾 3.拔模角度 4.其它特征上否已作齐全﹕基准角﹐倒角(C角和R角)﹐逃料﹐逃气﹐ 入子沉头﹐模仁上的逃孔﹐火山口﹐浇道﹐水路等等。
6.产品中做分型面法:有的时候就是很奇怪的事,直接模具版块中做分型面 分不出来的产品,换作到产品板块中去做分型面,然后到模具板块中去分模会 比较容易分出,据小可了解有不少的高手就是用这个方法进行分模的; 7.体积块法:有时也可用直接做体积块的方法来完成,包括做成成品的体积 块和先随意做成几个体积块后再进行体积块的分割与合并; 8.调包法:在某些时候,当用主分型面进行分模时会出现分不开的情况,但 不要轻易放弃,试换一个分型面(如镶件.镶针或者滑块)来分一下也会出现惊喜 的; 9.修改产品法:此法做法是针对于一些用第三方软件做图转换的图档和一 些产品曲面质量较差的的产品较有用.可将产品上一些局部的地方做适当的修 改,但要注意不能随意更改产品外观和功能部位.也可重新做一个PART来,利用 数据共享插入原产品的实体表面,不足是在产品设变时模具文件不能再生变更; 10.黄牛法:这是没有办法的办法,但绝对可行,就是对于一些产品造型质量 特差且模具结构简单的产品,与其想尽各种方法来寻找分模的***之招不如老老 实实做他一回黄牛,对于各个模具零件直接利用产品上的曲面一个个地做出来, 当然这样的东西的确让人讨厌,但一旦遇到而且你的计算机又不太好的情况下 法还是可以给你带来方便的
压铸成形工艺与模具设计
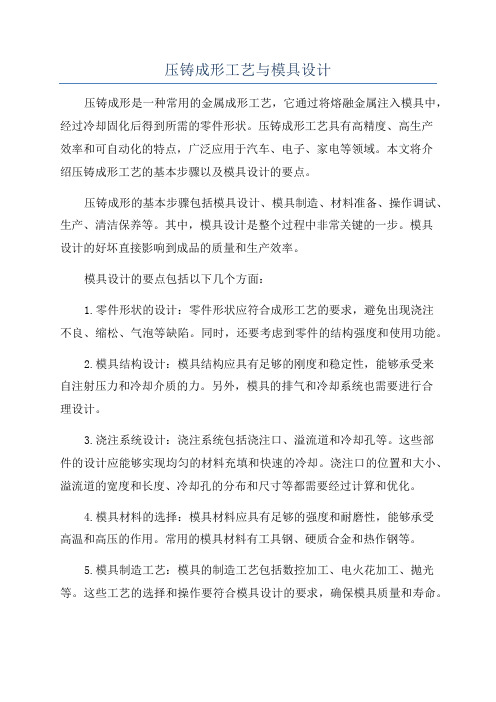
压铸成形工艺与模具设计压铸成形是一种常用的金属成形工艺,它通过将熔融金属注入模具中,经过冷却固化后得到所需的零件形状。
压铸成形工艺具有高精度、高生产效率和可自动化的特点,广泛应用于汽车、电子、家电等领域。
本文将介绍压铸成形工艺的基本步骤以及模具设计的要点。
压铸成形的基本步骤包括模具设计、模具制造、材料准备、操作调试、生产、清洁保养等。
其中,模具设计是整个过程中非常关键的一步。
模具设计的好坏直接影响到成品的质量和生产效率。
模具设计的要点包括以下几个方面:1.零件形状的设计:零件形状应符合成形工艺的要求,避免出现浇注不良、缩松、气泡等缺陷。
同时,还要考虑到零件的结构强度和使用功能。
2.模具结构设计:模具结构应具有足够的刚度和稳定性,能够承受来自注射压力和冷却介质的力。
另外,模具的排气和冷却系统也需要进行合理设计。
3.浇注系统设计:浇注系统包括浇注口、溢流道和冷却孔等。
这些部件的设计应能够实现均匀的材料充填和快速的冷却。
浇注口的位置和大小、溢流道的宽度和长度、冷却孔的分布和尺寸等都需要经过计算和优化。
4.模具材料的选择:模具材料应具有足够的强度和耐磨性,能够承受高温和高压的作用。
常用的模具材料有工具钢、硬质合金和热作钢等。
5.模具制造工艺:模具的制造工艺包括数控加工、电火花加工、抛光等。
这些工艺的选择和操作要符合模具设计的要求,确保模具质量和寿命。
总之,压铸成形工艺与模具设计是密不可分的,模具设计的好坏直接影响到产品的质量和生产效率。
要设计出性能良好的模具,需要综合考虑零件形状、模具结构、浇注系统、材料选择和制造工艺等方面的因素。
只有不断优化和改进,才能满足不同产品的要求,推动压铸成形工艺的发展。
压铸件的工艺流程
压铸件的工艺流程压铸件是一种常见的金属制品,广泛应用于汽车、电子、通讯、航空航天等领域。
下面将详细介绍压铸件的工艺流程。
压铸件的工艺流程主要包括模具设计、原料准备、熔炼、注射、冷却、脱模、修整和表面处理等步骤。
首先需要进行模具设计。
模具是压铸件生产的核心工具,决定着产品的形状、大小和表面质量。
模具设计要根据产品的需求确定产品的结构和尺寸,合理设计产品内部的浇注系统和冷却系统,以确保产品的一致性和质量。
接下来是原料准备。
压铸件的原料通常是金属合金,如铝合金、锌合金等。
原料需要经过严格的质检和筛选,确保符合要求的成分和性能,以保证产品的质量和可靠性。
然后进行熔炼。
将选定的合金原料放入熔炉中进行加热,使得原料在高温下融化成液态。
熔炼的温度和时间要依据具体的合金材料进行控制,以保证原料完全融化并达到所需的成分。
注射是压铸件工艺中的重要步骤。
将熔融的金属合金倒入注射机的料斗中,在机器的作用下,将熔融的金属注射进预先制作好的模具中。
注射机会对注入模具中的金属合金进行高压射流,确保金属材料充满整个模具腔,以获得完整的产品。
在注入后,需要进行冷却。
冷却的目的是使得注射进模具中的金属快速固化。
通过冷却系统,可以加速金属的固化过程,并提高产品的密度和强度。
冷却时间和方式也需要根据不同的合金材料进行控制,以获得最佳的冷却效果。
脱模是将已经固化的金属件从模具中取出的过程。
通常采用冷却水或气体冷却模具,使得金属件与模具分离,然后通过机械设备将金属件取出。
脱模过程需要谨慎操作,以避免金属件损坏。
在脱模后,压铸件需要进行一些修整工序。
例如,修剪去除多余的闪边和浇道,进行打磨和抛光,以提高产品的外观和精度。
修整过程需要依据产品要求进行,确保产品达到设计要求的尺寸和表面质量。
最后是表面处理。
根据产品的需求,压铸件可以进行各种表面处理,如喷漆、电镀、喷砂等,以增加产品的防腐性、美观性和功能性。
以上就是压铸件的工艺流程。
通过这些步骤,可以制造出符合要求的金属零件。
压铸成型的工艺和流程
压铸成型的工艺和流程压铸是一种常用的金属加工方法,其在工业生产中拥有广泛应用。
压铸成型的工艺和流程是非常关键的,可以影响产品质量和生产效率。
在本文中,我们将会详细介绍压铸的工艺和流程。
1. 压铸的基本概念压铸是一种通过将金属加热至液态,然后注入模具,通过高压将金属填充模具形成所需形状的加工方法。
压铸通常用于生产复杂形状的零部件,具有良好的表面光洁度和尺寸精度。
2. 压铸的工艺流程2.1 模具设计压铸的第一步是设计模具。
模具需要考虑产品的设计要求、材料流动性等因素,以确保最终产品的质量。
2.2 材料准备在压铸之前,需要将金属加热至液态。
不同的金属需要不同的熔点和加热温度。
2.3 注射一旦金属达到液态,就会被注入模具中。
注射过程需要控制温度和压力,以确保金属填充模具完全。
2.4 冷却填充模具后,金属需要冷却凝固。
冷却速度影响最终产品的组织结构和性能。
2.5 脱模冷却后,产品会从模具中取出。
脱模过程需要小心操作,以避免损坏产品。
2.6 完成加工脱模后,产品可能需要进一步的加工,如去除毛刺、打磨等,以达到最终要求。
3. 压铸的优缺点3.1 优点•可以生产复杂形状的产品•生产效率高•产品表面光洁度好3.2 缺点•初始投资较高•模具制造和维护成本较高•一些特殊形状难以实现4. 压铸的应用领域压铸广泛应用于汽车、航空航天、电子产品等领域。
由于其高效率和精度,越来越多的行业开始采用压铸技术。
5. 结语通过本文的介绍,相信读者对压铸成型的工艺和流程有了更深入的了解。
压铸作为一种重要的金属加工方法,将继续在工业生产中扮演重要角色,推动各行各业的发展和进步。
压铸工艺流程
压铸工艺流程压铸工艺流程是指通过对金属加热熔化后进行高压注射入模具中形成所需铸件的工艺过程。
下面是压铸工艺流程的详细介绍。
1. 原料准备压铸工艺的原料主要是金属合金,常用的有铝合金、锌合金、镁合金等。
在开始压铸工艺之前,首先要准备好所需的金属合金材料。
根据需要铸造的铸件材料进行相应的选材和配比。
2. 熔炼和熔炼处理将所需的金属合金材料放入熔炼炉中进行加热熔化。
熔化后的金属合金经过熔炼处理,如除杂、调整合金成分等。
这一步骤主要是为了保证铸件的质量和性能。
3. 模具设计和制造根据铸件的形状和尺寸要求,设计制作相应的模具。
模具的设计需要考虑到金属液态流动和凝固过程的特点,以及铸件的收缩率等因素。
模具制造一般采用数控加工或者精密雕刻加工等工艺。
4. 模具预热和涂料处理将制作好的模具进行预热处理,主要是为了防止模具在注射过程中发生变形或者产生应力。
预热后,模具表面需要涂上一层特殊的涂料,以保证铸件的表面光洁度和质量。
5. 注射将熔化处理好的金属合金注入注射机中。
注射机在高压下将金属液态材料注射到模具腔中,填充整个空腔。
这个过程需要控制注射速度和注射压力,以确保铸件的完整和一致性。
6. 冷却和固化注射完成后,模具中的金属液态材料会迅速冷却凝固。
在这个过程中,需要对模具进行适当的冷却措施,例如喷水冷却、通风散热等,以防止铸件产生缺陷。
同时,还需要对铸件进行固化处理,使其达到所需的力学性能。
7. 模具开启和脱模当铸件完全冷却固化后,模具开始开启。
脱模时需要小心操作,避免因剥离过快导致铸件破损。
脱模后,可以对铸件进行涂装、抛光等表面处理,使其达到所需的外观要求。
8. 修磨和后处理对于一些不合格的铸件,需要进行修磨处理,消除表面缺陷或尺寸偏差。
修磨后的铸件需要进行清洁、除锈等后处理,以便进行下一步的装配和加工。
9. 检验和质量控制对于每个生产批次的铸件,需要进行严格的检验和质量控制。
检验项目包括尺寸、外观、力学性能等。
铝压铸工艺流程
铝压铸工艺流程
铝压铸工艺流程是一种将铝合金熔化后注入模具中进行成型的工艺。
它是一种高效、精准、节能的铸造方法,广泛应用于汽车、航空、船舶、电子等领域。
下面将详细介绍铝压铸工艺流程。
1. 模具设计
首先,需要根据产品的形状、尺寸、要求等设计模具。
模具设计要考虑到材料的选择、结构的合理性、加工工艺的可行性等因素,确保模具能够满足生产需要。
2. 原材料准备
铝压铸的原材料主要是铝合金。
在生产前需要对原材料进行检验,检查其化学成分、物理性能等指标是否符合要求。
同时,还需要将原材料进行熔炼,将其熔化成为可注入模具中的流体状态。
3. 注射成型
在模具准备好后,需要将熔化的铝合金通过注射机注入模具中进行成型。
注射成型过程需要控制注射机的温度、压力等参数,确保铝合金能够充分填充模具中的空腔,并且形成所需的形状。
4. 热处理
成型后的铝制品需要进行热处理。
热处理可以改善铝制品的硬度、强度等性能,提高其耐腐蚀性和耐磨性。
常见的热处理方法有时效处理、退火处理、淬火处理等。
5. 机加工
经过热处理后,铝制品需要进行机加工。
机加工可以对铝制品进行精密加工,以达到所需的尺寸和形状。
常见的机加工方法有车床加工、铣床加工、钻床加工等。
6. 表面处理
最后,需要对铝制品进行表面处理。
表面处理可以提高铝制品的美观度和耐腐蚀性。
常见的表面处理方法有电镀、喷涂、阳极氧化等。
以上就是铝压铸工艺流程的详细介绍。
在实际生产中,还需要根据具体情况进行调整和优化,以达到最佳的生产效果。
- 1、下载文档前请自行甄别文档内容的完整性,平台不提供额外的编辑、内容补充、找答案等附加服务。
- 2、"仅部分预览"的文档,不可在线预览部分如存在完整性等问题,可反馈申请退款(可完整预览的文档不适用该条件!)。
- 3、如文档侵犯您的权益,请联系客服反馈,我们会尽快为您处理(人工客服工作时间:9:00-18:30)。
压铸模具设计基本流程一、模具设计之前二、模具设计之中三、模具设计审核及图纸输出客户资料审查制品样板3D产品设计结果回馈客户客户承认模具设计与开发计划的制订﹑设计参数的审核与分析制品参数评审a﹑制品用在何处(外观要求)﹔怎样使用(力学性能要求)﹖b﹑成型锌(铝)合金的收缩率多少﹖制品CAD图面3D产品设计c﹑制品是否要同其它零件进行配合(公差要求)﹖d﹑制品结构脱模角分别是多少﹖制品3D档案3D审查e﹑浇口位置﹑流线﹑结合线﹑顶出痕要求﹖f﹑制品外观面有无特殊要求﹕喷砂﹑电镀...﹖制品3D档与样板图样比对模具参数评审a﹑客户指定制品成型的材料特性如何﹖b﹑预期将模具寿命多少件制品﹖制品CAD档与样板图样比对c﹑预期的出模周期多长﹖d﹑需要何种类型的流道及排气系统﹕单流道﹑多流道,渣包排气、大排气,真空排气。
制品3D档与CAD档图图比对e﹑模腔的布局﹖天地方向的选择﹖f﹑制品出模方式的选择﹕手动拿出或自动落下﹔机械顶出﹑液压顶出设计规划设计日程的确定﹔该项目设计师指定﹑技术负责人指定《模具设计之前》模具结构设计1﹑制品能否从模腔中拉出﹖能否从模芯上脱下﹖首先确定出模方向﹕首先根据制品Boss﹑倒勾等结构确定出模方向﹐若无法正常成型和脱模则考虑设计内(外)滑块侧面抽芯。
2﹑确定分型面以模具制造加工条件的要求为根据﹐满足制品外形要求来确定模具分型面位置﹐便利简化磨削﹑铣削﹑CNC加工3﹑设计合理的浇口位置﹑浇口形状以及浇口数目根据制品大小﹑流动性能﹑可能出现的料流结合线﹑模塑周期的长短﹔借用AnyCasting模流分析软件(公司尚未安装)等工具来确定浇口位置/大小/型式(直胶口、内八字、外八字、反水口…)/数目。
浇口的设计决定料流结合线﹐而结合线的汇集将使内应力集中﹐这对于制品将是一个致命的破坏因素4﹑制品模穴排气渣包布局合理吗﹖针对制品模穴排气渣包问题﹐必须要排布在模穴的料流结合线处及料流最易包气位置5﹑镶件和成孔销的设计针对一些精巧细小的部件采取模仁镶件的方法﹐如成形深而小的孔位﹔模仁成型面在工作过程中容易磨损破坏的结构﹔在分型面下方深处无法加工或难以加工的结构.6﹑排气结构设计针对制品一些尖锐薄的位置﹐在压铸过程因排气不良而容易形成真空以致压射压力损失大且粘料难以充饱产生射出制品缺料现象﹐我们需在该处设置渣包及排气槽﹑开设镶件孔或将顶针设置于该处7﹑顶出机构设计跟据产品类型确定合适的顶出方法(脱模板﹑顶杆﹑直推块)8﹑冷却水路、油路设计我们根据预期模塑量﹑模塑周期来确定冷却水路的有或没有﹕a:对于较低模塑量的样件模﹐可以不设冷却水路﹔b:对预期模塑量上万的模具我们精确的设计合理高效的冷却条件﹐避免出现冷却不均匀甚至有些地方无法被冷却的现象。
注意前后模水路要相互配合﹑不能重垒平行﹐防止制品冷却不均匀,模具结构设计9﹑公母模仁定位装置设计将模腔/模芯/滑块进行良好的定位﹐可以补偿制造误差﹑热膨胀﹑磨损等失效因素。
公母模仁可用卡入模座之定位梢保证定位准确﹔对于分型面落差较大的小型模具用导柱定位即可﹐而对于大型模具/非平衡高保压力模具﹑分型面平整无咬合的模具我们还可以采用方型/圆型导柱辅助器﹑T型辅助器﹑锥形锁﹑模楔等添加结构来确保可靠的定位10﹑滑块抽芯驱动机构﹑锁紧机构的设计我们在给予滑块足够的抽芯力和足够的抽芯距离的同时。
应根据滑块的体积大小和所需的抽芯距离设计适合的滑块驱动机构以及滑块复位锁紧机构﹕a:斜导柱(驱动件)配合铲机﹔b:斜导柱配合模板斜面11﹑滑块定位装置设计滑块抽芯行程的定位使用较多的两种方式﹕一﹑采用弹簧珠定位﹔二﹑采用压力弹簧配合停止销定位(压铸模中一般多采用弹簧式)。
12﹑顶针板强制复位装置在模具中有滑块机构时、大模具落差比较大时,都要增加顶针板倒拉装置,每套模具的倒拉孔位置是按照模具外观尺寸确定压铸设备机台,再按照客户提供的压铸机机台设备资料(含2D压铸机平面图)来确定倒拉螺丝孔在顶针板的位置。
14﹑模具压板的厚度设置a﹕一般情况下﹐我们可采用模架制造商提供的标准值﹔b﹕根据客户提供的要求值设计﹐如配合压铸机的快速装夹模装置需要特定的面板﹑底板厚度15﹑唧嘴规格选择根据制品重量、投影面积﹑模具大小来确定所用唧嘴规格﹐设计唧嘴零件图自行加工,唧嘴下沉模板深度不大于5mm以上。
16﹑定位环规规格选择根据所用压铸机台吨位的大小﹑压铸机喷头尺寸选择适合规格的定位环模具结构设计17﹑模仁尺寸的确定视制品大小给定模仁长﹑宽﹑高尺寸﹕小件(模仁周边距制品轮廓最近处长/宽方向单边30~45mm﹔高度方向35~45mm);大件(模仁周边距制品轮廓最近处长/宽方向单边45~60mm﹔高度方向45~80mm) 18﹑A/B板尺寸确定视制品大小给定A/B长﹑宽﹑高尺寸﹕小件(A/B板周边距模仁轮廓长/宽方向单边45~50mm﹔高度方向A板30~40mm﹔B板40~60);大件(A/B板周边距模仁轮廓长/宽方向单边50~100mm﹔高度方向A板40~60mm﹔B板60~100mm)19﹑方铁(模脚)高度确定以制品顶出所需距离:(=制品高度+顶针面板厚度+顶针底板厚度+垃圾钉头厚+20mm安全值)计算顶针板的推动行程L来确定所需方铁的高度20﹑K.O孔大小倒拉杆的确定根据客户压铸机条件按客户机台的要求﹑模具大小来设置K.O孔的大小及倒拉杆的位置21﹑复位﹑先复位机构设计顶针板的复位在无特殊要求的情况下一般采用复位杆(回针)由前模板合模时推动复位﹔但在一些特殊情况下如﹕滑块与顶针行程相干涉时必须采用顶针板先复位机构(在压铸模中一般使用倒拉杆装置)22﹑螺丝的设置调整模块上的螺丝位置﹐避开水路﹔滑块的行程﹐防止发生干涉现象﹔锁公母模仁之螺丝﹐设计时愈多愈好﹐且需平均分配﹐使模仁与模座接触面更密合﹐且须为公制规格23﹑导柱的设置在设置导柱时需防呆﹐必须在基准角的那一支导柱在X﹑Y方向偏移2mm24﹑确定模具的最小外形尺寸根据制品出模方向的投影面积和成形结构部件的布局确定模架的最小外形尺寸﹐选择最接近尺寸的标准模架或非标准模架2D组立图绘制组立(装配)图纸保证所有零件的工作位置﹑装配关系以及工作状况等信息在视图上都有表达清楚明了﹐要求视图以第三视角摆放汇审阶段性设计审查《新模开发检讨会》组织加工执行单位(CNC﹑钳工、压铸)代表在适当阶段参与设计评审工作﹐对进行到目前为止的所有工作做全面的讨论与确认﹐对需要改进的方案做相关的记录并交付模具设计人员执行结构﹑材质确认最终确定模架外形尺寸并确定模具各零部件的材质A:确定模架外形尺寸,模架规格确定;B:成型部件之结构确认﹔C:根据产品的产量、模具结构的复杂度和模具的切削加工性来确定,前﹑后模仁﹑滑块﹑束仔(斜楔)﹑唧嘴、分流锥、垫块﹑耐磨块﹑镶件的材质3D组立3D分模及模具零件建构使用UG﹑PRO/E软件进行模具3D组立建构模具2D零件图绘制绘制零件图模胚图﹑公模水路图﹑母模水路图﹑公模机加工图﹑母模机加工图﹑模仁线割图﹑顶针位置图﹑电极加工图﹑放电位置图﹑模仁螺丝/销钉位置图﹑公(母)模仁检测图等加工﹑检测之所需2D图面的绘制﹐必须依照制订的2D图面要求规范进行绘图作业﹔该部细化见附表﹕模具2D零件图面规范BOM零件BOM建立附于装配图纸上﹐将所有模具零部件编号列表﹕详尽列出每一个零件的名称﹑编号﹑尺寸﹑材质﹑备注说明《模具设计审核及图纸输出》设计审核设计评审及设计确认对设计进行重审﹐这是推敲图纸以及在模具细部设计和开始制造之前更改设计的最后机会,这是对模具至关重要的一个环节。
a﹕零件图尺寸标识是否完整﹖有无过标﹑漏标尺寸﹖尺寸格式是否统一﹖精度要求为0.01b﹕零件图所标示之尺寸是否符合钳工机加工﹑品管检测之便利﹖c﹕冷却水路之水径和分布合理吗﹖有没有与其它模具结构产生干涉现象﹖有没有模仁存在冷却不均匀﹑冷却不到现象﹔在水嘴位必须标示IN#﹑OUT#字样(#__流水号)d﹕结合3D组立检查模具活动部件的设计是否正确﹖2D图面尺寸标注是否详尽无误﹖水路是否安全﹖e﹕结合3D组立滑块抽芯行程足够吗﹖束仔﹑楔块的可靠的锁紧强度够足吗﹖所有活动构件的材料选择合理吗﹖f﹕制品脱模是否可靠﹖顶出机构(顶针﹑推块﹑推件板)的选择与数目布局是否合理﹖设计输出图纸放行填好标题栏并完成图纸正式图纸的标题栏信息要求完整﹕模具编号﹑制品名称﹑成型原料﹑原料收缩率﹑图纸比例尺﹑图纸版次﹑图纸完成日期﹑审核日期﹑交付车间日期﹑设计变更栏填写以及设计者/审查者/核准者签名《模具的出模方向》首先确定出模方向﹕首先根据制品Boss﹑倒勾等结构确定出模方向﹐若无法正常成型和脱模则考虑设计内(外)滑块侧面抽芯。
《进胶方式》直胶口外八字内八字反水口《制品模穴排气渣包位置》《公母模定位装置设计》規格型自然型補強柱《滑块抽芯驱动机构﹑锁紧机构》A.(铲机留自然)滑块背部与母模板相靠处,母B.铲机采嵌入方式,如图模板留自然斜面,如图C.铲机兼斜导梢采嵌入方式,如图D.滑块厚度过厚铲机须插入公模(做反铲),如图《滑块定位装置》《顶针板强制复位装置》《导柱的位置》《模具2D组立图》《基本模座零件名称》《成型部分结构确认》《3D分模》《零件BOM 建立》《标题栏》《设计变更栏》《技术要求》Thank You。