abaqus损伤准则总结
abaqus 损伤参数定义位移

Abaqus是一款常用的有限元分析软件,在工程领域具有广泛的应用。
在使用Abaqus进行有限元分析时,损伤参数的定义是非常重要的一环。
本文将围绕着Abaqus中损伤参数的定义及其与位移的关系展开讨论。
1. 损伤参数的概念在有限元分析中,损伤参数通常用于描述材料在加载过程中的损伤程度。
当材料受到外力作用时,其内部会产生损伤,损伤参数可以用来表示材料的损伤程度,通常用0到1之间的数值表示,0表示无损伤,1表示完全破坏。
2. 损伤参数在Abaqus中的定义在Abaqus软件中,损伤参数可以通过定义材料的本构模型来实现。
用户可以根据材料的特性和试验数据来设定材料的本构参数,包括损伤参数。
在定义损伤参数时,需要考虑材料的弹性模量、泊松比、拉伸和压缩的材料性能等因素。
3. 位移在有限元分析中的作用位移是有限元分析中的一个重要参数,它用来描述材料在加载过程中的变形情况。
在Abaqus中,用户可以通过定义边界条件和加载条件来模拟材料的位移响应,进而分析材料的性能。
4. 损伤参数与位移的关系损伤参数和位移是密切相关的。
在有限元分析中,材料的损伤程度会影响其位移响应。
当材料内部发生损伤时,会导致材料的刚度和强度发生变化,进而影响材料的位移响应。
在Abaqus中定义损伤参数不仅可以用来描述材料的损伤程度,还可以与位移的响应相结合,来分析材料的性能。
5. 如何在Abaqus中定义损伤参数与位移在Abaqus中,用户可以通过选择合适的材料本构模型来定义损伤参数,然后在模拟加载条件时,可以通过定义合适的加载和边界条件来模拟材料的位移响应。
用户可以根据具体的工程要求和材料的特性来进行调整和优化,以获得准确的分析结果。
损伤参数的定义与位移在Abaqus中的分析是密切相关的。
在有限元分析中,合理的定义损伤参数,并与位移的响应相结合,能够更准确地描述材料的性能及其在加载过程中的行为。
通过深入理解和合理运用Abaqus中的损伤参数定义与位移分析,可以为工程实践提供更可靠的分析结果和科学的参考建议。
XFEM总结

一、 ABAQUS 中XFEM 的实现(基于牵引分离规则的损伤力学理论)1、选择模型中可能出现裂纹的区域,将其单元设置为具有扩展有限元性质的富集单元;2、选择合适的破坏准则,使得单元在达到条件时发生破坏,裂纹得以扩展。
二、 ABAQUS 中XFEM 的简化1、富集单元内不能存在两条裂缝,说明ABAQUS 放弃了两个形函数带来的耦合问题,所以ABAQUS 中不能模拟分叉裂缝;2、在计算过程中会发现裂缝是不能停留在单元内部,说明ABAQUS 放弃了单元内部对裂尖的描述;3、ABAQUS 在计算XFEM 的损伤时采用的是基于能量释放率的Paris 法则,虽然这是基于弹塑性断裂力学的经典手段,但由于承认了裂尖位置的塑性效应,使得在模拟损伤时也只能对低周疲劳能有比较好的近似。
三、 破环准则——最大主应力准则:1、破坏法则(用以控制损伤的起始)max max max max 0,0,0σσσσ<⎧⎫<>=⎨⎬>⎩⎭0max σ为最大临界主应力(通过实验给定,武汉岩土所为320Pa ),为了避免纯压缩状态下发生损伤。
当上式f 范围为0<f<1+f tol ,其中f tol为一个公差,默认为0.05,当f>1+f tol时,认为达到损伤断裂准则,开始起裂。
2、Damage Evolution损伤演化(用以控制损伤的发展情况)(1)Damage Evolution 中的所有选项是用来确定单元达到强度极限以后的刚度降阶方式,包括基于位移损伤演化规律和基于能量损伤演化规律(武汉岩土所给定基于能量)。
(2)软化定义:线性软化、指数软化、表格定义软化曲线(武汉岩土所为指数软化)(3)Mixed-mode definitiona. 接触点处的正常和剪切分离的相对比例定义了该点处的模式混合。
b.定义等效断裂能释放率:BK准则:(武汉岩土所为软化BK准则,幂指数为2.284,断裂能释放率各向同性均为28)Power准则:Reeder准则(仅适用于三维问题,且Gц≠Gш时最为适用):3、损伤稳定系数:用以改善收敛,一般取1E-5。
abaqus损伤演化参数
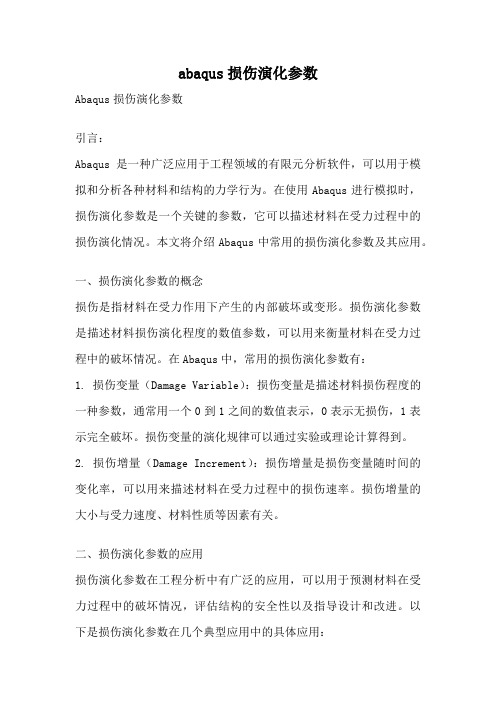
abaqus损伤演化参数Abaqus损伤演化参数引言:Abaqus是一种广泛应用于工程领域的有限元分析软件,可以用于模拟和分析各种材料和结构的力学行为。
在使用Abaqus进行模拟时,损伤演化参数是一个关键的参数,它可以描述材料在受力过程中的损伤演化情况。
本文将介绍Abaqus中常用的损伤演化参数及其应用。
一、损伤演化参数的概念损伤是指材料在受力作用下产生的内部破坏或变形。
损伤演化参数是描述材料损伤演化程度的数值参数,可以用来衡量材料在受力过程中的破坏情况。
在Abaqus中,常用的损伤演化参数有:1. 损伤变量(Damage Variable):损伤变量是描述材料损伤程度的一种参数,通常用一个0到1之间的数值表示,0表示无损伤,1表示完全破坏。
损伤变量的演化规律可以通过实验或理论计算得到。
2. 损伤增量(Damage Increment):损伤增量是损伤变量随时间的变化率,可以用来描述材料在受力过程中的损伤速率。
损伤增量的大小与受力速度、材料性质等因素有关。
二、损伤演化参数的应用损伤演化参数在工程分析中有广泛的应用,可以用于预测材料在受力过程中的破坏情况,评估结构的安全性以及指导设计和改进。
以下是损伤演化参数在几个典型应用中的具体应用:1. 材料疲劳寿命预测:通过实验或数值模拟得到材料的损伤演化规律,可以预测材料在复杂循环载荷下的疲劳寿命。
根据损伤变量的演化规律,可以确定材料的破坏准则,从而评估材料的寿命。
2. 结构强度评估:损伤演化参数可以用来评估结构在受力过程中的强度。
通过实验或数值模拟得到结构的损伤演化规律,可以计算结构的损伤变量,进而评估结构的安全性和承载能力。
3. 材料优化设计:通过调整材料的损伤演化参数,可以改变材料的破坏模式和破坏程度,从而实现材料的优化设计。
例如,在汽车碰撞中,可以通过调整车身材料的损伤演化参数,来改善车身的抗碰撞性能。
4. 材料损伤模型改进:损伤演化参数也可以用于改进材料的损伤模型。
19.Abaqus累积损伤与失效
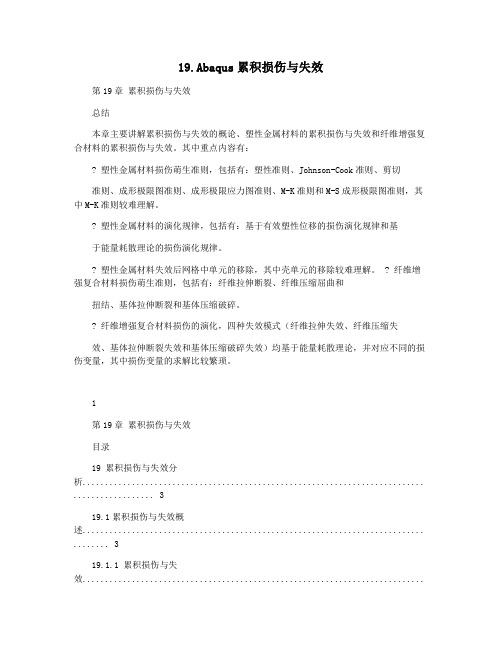
19.Abaqus累积损伤与失效第19章累积损伤与失效总结本章主要讲解累积损伤与失效的概论、塑性金属材料的累积损伤与失效和纤维增强复合材料的累积损伤与失效。
其中重点内容有:? 塑性金属材料损伤萌生准则,包括有:塑性准则、Johnson-Cook准则、剪切准则、成形极限图准则、成形极限应力图准则、M-K准则和M-S成形极限图准则,其中M-K准则较难理解。
? 塑性金属材料的演化规律,包括有:基于有效塑性位移的损伤演化规律和基于能量耗散理论的损伤演化规律。
? 塑性金属材料失效后网格中单元的移除,其中壳单元的移除较难理解。
? 纤维增强复合材料损伤萌生准则,包括有:纤维拉伸断裂、纤维压缩屈曲和扭结、基体拉伸断裂和基体压缩破碎。
? 纤维增强复合材料损伤的演化,四种失效模式(纤维拉伸失效、纤维压缩失效、基体拉伸断裂失效和基体压缩破碎失效)均基于能量耗散理论,并对应不同的损伤变量,其中损伤变量的求解比较繁琐。
1第19章累积损伤与失效目录19 累积损伤与失效分析............................................................................ (3)19.1累积损伤与失效概述............................................................................ .. (3)19.1.1 累积损伤与失效................................................................................ 3 19.2 金属塑性材料的损伤与失效.. (6)19.2.1 金属塑性材料损伤与失效概论........................................................ 6 19.2.2 金属塑性材料损伤初始阶段 (8)19.2.3 塑性金属材料的损伤演化与单元的移除......................................24 19.3 纤维增强复合材料的损伤与失效 (35)19.3.1纤维增强复合材料的损伤与失效:概论....................................... 35 19.3.2 纤维增强复合材料的损伤初始产生.............................................. 38 19.3.3 损伤演化与纤维增强复合材料的单元去除 (41)2第19章累积损伤与失效19 累积损伤与失效分析19.1累积损伤与失效概述 19.1.1 累积损伤与失效Abaqus提供了以下材料模型来预测累积损伤与失效:1)塑性金属材料的累积损伤与失效:Abaqus/Explicit拥有建立塑性金属材料的累积损伤与失效模型的功能。
abaqus损伤准则总结

損傷失效模型簡介■ ABAQUS提供的金屬損傷失效模理♦离應變率玻壊Shear failuretensile failure♦礼傥成核、戎長與合徉之破壤Ductile damageJohn-Cook (J-C) damage♦剪力帶破壞Shear damage♦飯金成型破壞Forming limit diagram (FLD) damageForming limit stress d agram (FLSD) darrageMarciniak-Kuczynski (M-K) damage Muschenbom・Sonne forming limitdiagram (MSFLD) damageABAQUS中有四种初始断裂准则:在高应变速率下变形时,有shear failure和tensile failure (旋爪川不到,不再介绍)对于断裂延性金属:可以选用A:韧性准则(ductile criteria)和B:明切准则(shearcriteria)对于缩颈不稳定性可以使用(锻金):C:FLD、FLSD、M・K以及MSFLD对于铝合金、镁合金以及岛强钢在变形过程中会出现不同机制的断裂,可能会将以上准则联合起来进行使用。
损伤的感念如下图所示:Ductile damage概念說明卑軸向拉仲试驗之真賞應力禺變的绿1・韧性断裂准则中提供的韧性断裂准则需要输入的参数为:1.1 ABAQUS断裂应变;应力三轴度;应变速率要测量不同应力三轴度下的断裂应变需要进行大量的实验,这是不可取的。
Hooputia et汶2004通过实验和理论推导得到了在定应变速率下,断裂应变和应力三轴度的关系:才 sinh[Mi(7? 对]+ 巧sinh[A\)(?7 “1)]sinh[fco(T|- - 帀+)]公式中::应力三轴度。
即平均应力和屈服应力的比值;为等双轴拉伸时的应力三:等双轴拉伸时,断裂时的等效塑性应变,轴度,其值为2/3;为等双轴圧缩时的应:等双轴圧缩时,断裂时的等效塑性应变,力三轴度,其值为・2/3:因此,为了得到断裂时等效塑性应变和应力三轴度的关系,只需要求出和参数三个参数即可。
(仅供参考)Abaqus混凝土损伤塑性模型的参数标定
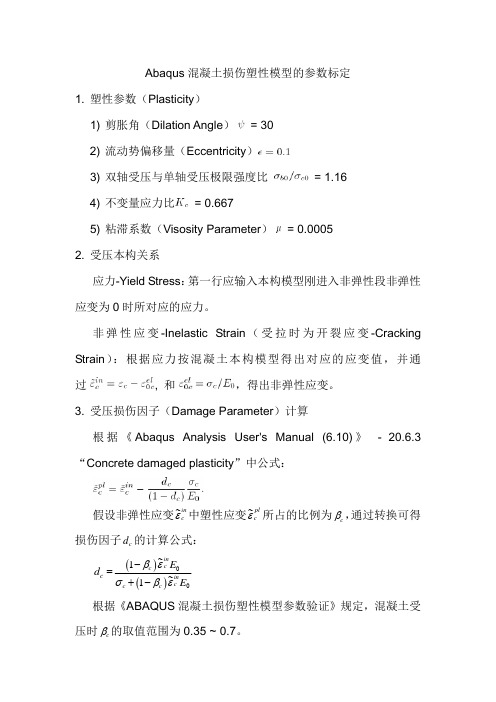
Abaqus 混凝土损伤塑性模型的参数标定1. 塑性参数(Plasticity )1) 剪胀角(Dilation Angle )= 30°2) 流动势偏移量(Eccentricity )3) 双轴受压与单轴受压极限强度比= 1.164)不变量应力比 = 0.667 5) 粘滞系数(Visosity Parameter) = 0.00052. 受压本构关系应力-Yield Stress :第一行应输入本构模型刚进入非弹性段非弹性应变为0时所对应的应力。
非弹性应变-Inelastic Strain (受拉时为开裂应变-Cracking Strain ):根据应力按混凝土本构模型得出对应的应变值,并通过, 和 ,得出非弹性应变。
3. 受压损伤因子(Damage Parameter )计算根据《Abaqus Analysis User's Manual (6.10)》 - 20.6.3 “Concrete damaged plasticity ”中公式:假设非弹性应变 in c ε中塑性应变 plc ε所占的比例为c β,通过转换可得损伤因子cd 的计算公式:() () 0011in c c in c c c c E E d βεσβε-=+-根据《ABAQUS 混凝土损伤塑性模型参数验证》规定,混凝土受压时c β的取值范围为0.35 ~ 0.7。
4. 受拉损伤因子(Damage Parameter )计算受拉损伤因子的计算与受压损伤因子的计算方法基本相同,只需将对应受压变量更换为受拉即可:() () 0011int t in t t t t E E d βεσβε-=+- 而根据参考文献混凝土受拉时t β的取值范围为0.5 ~ 0.95。
5. 损伤恢复因子受拉损伤恢复因子(Tension Recovery ):缺省值0t w =。
受压损伤恢复因子(Compression Recovery ):缺省值1c w =。
19.Abaqus累积损伤与失效要点(最新整理)

总结本章主要讲解累积损伤与失效的概论、塑性金属材料的累积损伤与失效和纤维增强复合材料的累积损伤与失效。
其中重点内容有:●塑性金属材料损伤萌生准则,包括有:塑性准则、Johnson-Cook准则、剪切准则、成形极限图准则、成形极限应力图准则、M-K准则和M-S成形极限图准则,其中M-K准则较难理解。
●塑性金属材料的演化规律,包括有:基于有效塑性位移的损伤演化规律和基于能量耗散理论的损伤演化规律。
●塑性金属材料失效后网格中单元的移除,其中壳单元的移除较难理解。
●纤维增强复合材料损伤萌生准则,包括有:纤维拉伸断裂、纤维压缩屈曲和扭结、基体拉伸断裂和基体压缩破碎。
●纤维增强复合材料损伤的演化,四种失效模式(纤维拉伸失效、纤维压缩失效、基体拉伸断裂失效和基体压缩破碎失效)均基于能量耗散理论,并对应不同的损伤变量,其中损伤变量的求解比较繁琐。
目录19 累积损伤与失效分析 (3)19.1累积损伤与失效概述 (3)19.1.1 累积损伤与失效 (3)19.2 金属塑性材料的损伤与失效 (6)19.2.1 金属塑性材料损伤与失效概论 (6)19.2.2 金属塑性材料损伤初始阶段 (8)19.2.3 塑性金属材料的损伤演化与单元的移除 (24)19.3 纤维增强复合材料的损伤与失效 (35)19.3.1纤维增强复合材料的损伤与失效:概论 (35)19.3.2 纤维增强复合材料的损伤初始产生 (38)19.3.3 损伤演化与纤维增强复合材料的单元去除 (41)19 累积损伤与失效分析19.1累积损伤与失效概述19.1.1 累积损伤与失效Abaqus提供了以下材料模型来预测累积损伤与失效:1)塑性金属材料的累积损伤与失效:Abaqus/Explicit拥有建立塑性金属材料的累积损伤与失效模型的功能。
此功能可以与the Mises, Johnson-Cook, Hill, 和Drucker-Prager等塑性材料本构模型一起使用(塑性材料的损伤与失效概论,19.2.1节)。
Abaqus损伤总结

Abaqus损伤总结初始损伤初始损伤对应于材料开始退化,当应力或应变满足于定义的初始临界损伤准则,则此时退化开始。
Abaqus 的Damage for traction separation laws 中包括:Quade Damage、Maxe Damage、Quads Damage、Maxs Damage、Maxpe Damage、Maxps Damage 六种初始损伤准则,其中前四种用于一般复合材料分层模拟,后两种主要是在扩展有限元法模拟不连续体(比如crack 问题)问题时使用。
前四种对应于界面单元的含义如下:Maxe Damage 最大名义应变准则:Maxs Damage 最大名义应力准则:Quads Damage 二次名义应变准则:Quade Damage 二次名义应力准则:其中σ1 层间正应力σ2 σ3 层间剪应力对应的分别是有实验测的极限正应力第一二剪应力ε1 层间正应变ε2 ε3 层间剪应变对应的分别是有实验测的极限正应变第一二剪应变1、三维空间中任一点应力有6个分量,在ABAQUS中分别对应S11,S22,S33,S12,S13,S23。
2、一般情况下,通过该点的任意截面上有正应力及其剪应力作用。
但有一些特殊截面,在这些截面上仅有正应力作用,而无剪应力作用。
称这些无剪应力作用的面为主截面,其上的正应力为主应力,主截面的法线叫主轴,主截面为互相正交。
主应力分别以表示,按代数值排列(有正负号)为。
其中在ABAQUS中分别对应Max. Principal、Mid. Principal、Min. Principal,这三个量在任何坐标系统下都是不变量。
在ABAQUS中对应变的部分理解1、E—总应变;Eij—应变分量2、EP---主应变;EPn----分为Minimum, intermediate, and maximum principal strains (EP1 EP2 EP3)3、NE----名义应变;NEP---主名义应变;4、LE----真应变(或对数应变);LEij---真应变分量;LEP---主真应变;5、EE—弹性应变;6、IE---非弹性应变分量;7、PE---塑性应变分量;8、PEEQ---等效塑性应变---在塑性分析中若该值〉0,表示材料已经屈服;描述整个变形过程中塑性应变的累积结果;若单调加载则PEEQ=PEMAG ;9、PEMAG----塑性应变量(幅值Manitude)---描述变形过程中某一时刻的塑性应变,与加载历史无关;10、THE---热应变分量;损伤曲线如果是玻璃这种脆性材料,那肯定是线性下降,如果是金属等塑性很好的材料,肯定是抛物线下降。
- 1、下载文档前请自行甄别文档内容的完整性,平台不提供额外的编辑、内容补充、找答案等附加服务。
- 2、"仅部分预览"的文档,不可在线预览部分如存在完整性等问题,可反馈申请退款(可完整预览的文档不适用该条件!)。
- 3、如文档侵犯您的权益,请联系客服反馈,我们会尽快为您处理(人工客服工作时间:9:00-18:30)。
ABAQUS中有四种初始断裂准则:
在高应变速率下变形时,有shear failure和tensile failure(旋压用不到,不再介绍)
对于断裂延性金属:可以选用A:韧性准则(ductile criteria)和B:剪切准则(shear
criteria)
对于缩颈不稳定性可以使用(钣金):C:FLD、FLSD、M-K以及MSFLD
对于铝合金、镁合金以及高强钢在变形过程中会出现不同机制的断裂,可能会将以上准则联合起来进行使用。
损伤的感念如下图所示:
1.韧性断裂准则中提供的韧性断裂准则需要输入的参数为:1.1ABAQUS断裂应变;应力三轴度;应变速率
要测量不同应力三轴度下的断裂应变需要进行大量的实验,这是不可取的。
Hooputra et al,2004通过实验和理论推导得到了在定应变速率下,断裂应变和应力三轴度的关系:
公式中::应力三轴度。
即平均应力和屈服应力的比值;
为等双轴拉伸时的应力三:等双轴拉伸时,断裂时的等效塑性应变,轴度,其值为2/3;
为等双轴压缩时的应:等双轴压缩时,断裂时的等效塑性应变,
力三轴度,其值为-2/3;
因此,为了得到断裂时等效塑性应变和应力三轴度的关系,只需要求出
和参数三个参数即可。
根据方程已得到不同应力三轴度下的断、裂应变。
、和在一个应变速率下只需要三组数据,就可以求出方程中的。
帮助文件中的建议:ABAQUS
==2/3方程一(是不是:例如在杯突试验中,应力三轴度为已知量杯突实验和等双轴拉伸的变形时等效的,杯突实验如何在高温下进行,能否用双向拉伸实验代替?)
=此时,通过对进行杯突实验的板料印制网格,可以得
到其成形极限(。
)
:例如三点弯曲试验中,应力三轴度为已知量(印制方程二=0.57735。
网格测量,具体如何测量不是很清楚)
:例如在单轴拉伸实验中,应力三轴度为已知量=0.333方程三。
平均应力为屈服应力的三分之一。
SIMUWE论坛中的建议:
这个应该通过单轴拉伸实验、压缩实验和纯剪切实验。
各测得各自的应变量。
应力三轴度拉伸是0.33,压缩是-0.33,纯剪切时0。
实验好做。
方程求解后,就可以得到(不同温度、不同应变速率下)不同三轴应力对应的断裂初始时的等效塑性应变。
例子中提供的断裂应变和应力三轴度的关系如下图所示,材料为7018铝:态T6合金,
2.剪切断裂准则:(参数计算过程和韧性差不多)
其中:
,=0.3
:等双轴拉伸时,剪切断裂时的等效塑性应变
:等双轴压缩时,剪切断裂时的等效塑性应变
方程中只有三个未知数,可以通过三组实验结果联立求而出。
方程一:设计拉伸试样,在和拉伸方向呈45°的方向上切取矩形截面的沟槽,
其厚度为试样厚度的一半。
方程二:设计拉伸试样,在和拉伸平行的方向上切取矩形截面的沟槽,其厚
度为试样厚度的一半。
杯突实验。
方程三:
和。
,联立三个方程求出:
3.FLD、FLSD、M-K以及MSFLD
以应变为基础的FLD断裂准则,仅适用于完全线性的加载路径,同样以应力为基础的FLSD断裂准则对于应变的路径也是相当的不敏感。
M-K断裂准则可以准确的反应非线性的应变加载路径,但是当引入大量的缺陷时,其计算成本很高。
实验证明,MSFLD准则和M-K准则的预测结果十分接近,能够大量的减少计算成本。
同时MSFLD。