延迟焦化工艺流程教学提纲
延迟焦化装置吸收稳定系统工艺与操作资料

第二章:吸收稳定系统工艺流程
2.2吸收稳定系统的任务是处理来自分馏塔 顶油气分离器的粗汽油和来自压缩机的富 气,分离出干气(C2及C2以下),得到稳 定汽油和液化气。稳定汽油和液化气产率 的高低,主要取决于焦化反应系统的工艺 过程,但吸收稳定系统的回收程度与操作 水平也对收率有很大的影响。目的是要求 吸收后的干气中尽量少含C3,同时要求 解吸后的脱乙烷汽油中尽可能不含C2。
制偏低,再吸收效果不好,成干气不干,压力控制偏 高,造成吸收系统压力上升,气压机出口压力上升, 装置能耗上升。
控制目标:再吸收塔顶压力:≯1.3 MPa 控制范围:再吸收塔压力:1.10-1.20MPa 相关参数:压缩机出口压力、压缩机出口流量、干气
背压、再吸收剂温度
控制方式:通过压力控制阀PC6604来控制再吸收 塔顶部压力
置
控制方式: 正常生产时,稳定汽油的初馏 点是由塔底温度来控制的
第三章:质量控制及操作
正常调整:
影响因素 稳定塔底温度 稳定塔顶压力
进料位置
异常处理:
调整方法
塔底温度升高,初馏点降升高,反之初馏点降低 稳定塔顶压力升高,初馏点降低,反之初馏点升 高 进料位置往上,初馏点升高,反之初馏点降低
现象 稳定汽油初馏点偏低
第二章:吸收稳定系统工艺流程
改造过
第二章:吸收稳定系统工艺流程
改造过
改造过
第三章:质量控制及操作
3.1稳定汽油初馏点控制 稳定汽油初馏点是稳定汽油的主要指标,它
的指标大小关系到稳定汽油在加工、储存、 运输和使用中的安全。
控制目标: 以工艺卡片为准 相关参数: 塔底温度、塔顶压力、进料位
第三章:质量控制及操作
正常调整:
影响因素
延迟焦化工艺流程

延迟焦化工艺流程延迟焦化1. 延迟焦化工艺流程:本装置的原料为温度90℃的减压渣油,由罐区泵送入装置原料油缓冲罐,然后由原料泵输送至柴油原料油换热器,加热到135℃左右进入蜡油原料油换热器,加热至160℃左右进入焦化炉对流段,加热至305℃进入焦化分馏塔脱过热段,在此与来自焦炭塔顶的热油气接触换热。
原料油与来自焦炭塔油气中被凝的循环油一起流入塔底,在380~390℃温度下,用辐射泵抽出打入焦化炉辐射段,快速升温至495~500℃,经四通阀进入焦碳塔底部。
循环油和减压渣油中蜡油以上馏分在焦碳塔内由于高温和长时间停留而发生裂解、缩合等一系列的焦化反应,反应的高温油气自塔顶流出进入分馏塔下部与原料油直接换热后,冷凝出循环油馏份;其余大量油气上升经五层分馏洗涤板,在控制蜡油集油箱下蒸发段温度的条件下,上升进入集油箱以上分馏段,进行分馏。
从下往上分馏出蜡油、柴油、石脑油(顶油)和富气。
分馏塔蜡油集油箱的蜡油在343℃温度下,自流至蜡油汽提塔,经过热蒸汽汽提后蜡油自蜡油泵抽出,去吸收稳定为稳定塔重沸器提供热源后降温至258℃左右,再为解吸塔重沸器提供热源后降温至242℃左右,进入蜡油原料油换热器与原料油换热,蜡油温度降至210℃,后分成三部分:一部分分两路作为蜡油回流返回分馏塔,一路作为下回流控制分馏塔蒸发段温度和循环比,一路作为上回流取中段热;一部分回焦化炉对流段入口以平衡大循环比条件下的对流段热负荷及对流出口温度;另一部分进水箱式蜡油冷却器降温至90℃,一路作为急冷油控制焦炭塔油气线温度,少量蜡油作为产品出装置。
柴油自分馏塔由柴油泵抽出,仅柴油原料油换热器、柴油富吸收油换热器后一部分返回分馏塔作柴油回流,另一部分去柴油空冷器冷却至55℃后,再去柴油水冷器冷却至40℃后分两路:一路出装置;另一路去吸收稳定单元的再吸收塔作吸收剂。
由吸收稳定单元返回的富吸收油经柴油富吸收油换热器换热后也返回分馏塔。
分馏塔顶油气经分馏塔顶空冷器,分馏塔顶水冷器冷却到40℃,流入分馏塔顶气液分离罐,焦化石脑油由石脑油泵抽出送往吸收稳定单元。
延迟焦化工艺流程
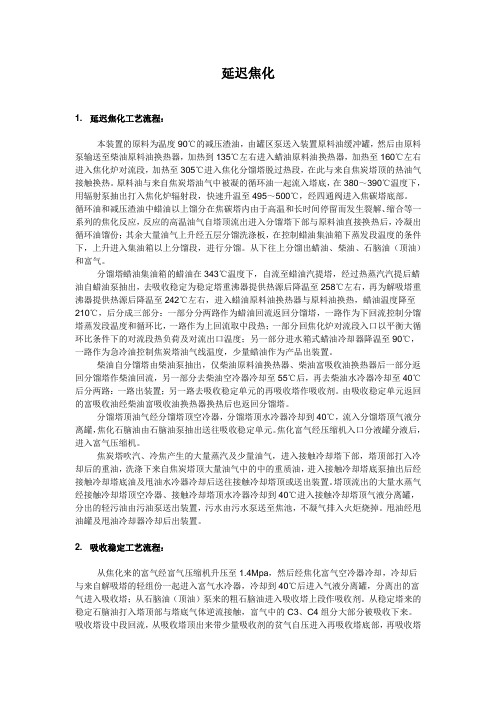
延迟焦化1. 延迟焦化工艺流程:本装置的原料为温度90℃的减压渣油,由罐区泵送入装置原料油缓冲罐,然后由原料泵输送至柴油原料油换热器,加热到135℃左右进入蜡油原料油换热器,加热至160℃左右进入焦化炉对流段,加热至305℃进入焦化分馏塔脱过热段,在此与来自焦炭塔顶的热油气接触换热。
原料油与来自焦炭塔油气中被凝的循环油一起流入塔底,在380~390℃温度下,用辐射泵抽出打入焦化炉辐射段,快速升温至495~500℃,经四通阀进入焦碳塔底部。
循环油和减压渣油中蜡油以上馏分在焦碳塔内由于高温和长时间停留而发生裂解、缩合等一系列的焦化反应,反应的高温油气自塔顶流出进入分馏塔下部与原料油直接换热后,冷凝出循环油馏份;其余大量油气上升经五层分馏洗涤板,在控制蜡油集油箱下蒸发段温度的条件下,上升进入集油箱以上分馏段,进行分馏。
从下往上分馏出蜡油、柴油、石脑油(顶油)和富气。
分馏塔蜡油集油箱的蜡油在343℃温度下,自流至蜡油汽提塔,经过热蒸汽汽提后蜡油自蜡油泵抽出,去吸收稳定为稳定塔重沸器提供热源后降温至258℃左右,再为解吸塔重沸器提供热源后降温至242℃左右,进入蜡油原料油换热器与原料油换热,蜡油温度降至210℃,后分成三部分:一部分分两路作为蜡油回流返回分馏塔,一路作为下回流控制分馏塔蒸发段温度和循环比,一路作为上回流取中段热;一部分回焦化炉对流段入口以平衡大循环比条件下的对流段热负荷及对流出口温度;另一部分进水箱式蜡油冷却器降温至90℃,一路作为急冷油控制焦炭塔油气线温度,少量蜡油作为产品出装置。
柴油自分馏塔由柴油泵抽出,仅柴油原料油换热器、柴油富吸收油换热器后一部分返回分馏塔作柴油回流,另一部分去柴油空冷器冷却至55℃后,再去柴油水冷器冷却至40℃后分两路:一路出装置;另一路去吸收稳定单元的再吸收塔作吸收剂。
由吸收稳定单元返回的富吸收油经柴油富吸收油换热器换热后也返回分馏塔。
分馏塔顶油气经分馏塔顶空冷器,分馏塔顶水冷器冷却到40℃,流入分馏塔顶气液分离罐,焦化石脑油由石脑油泵抽出送往吸收稳定单元。
延迟焦化讲课201911

用分馏塔底含有焦粉的循环油作为分馏塔下冲洗涤换热段换热洗涤油使用,在同样
操作负荷下会增加焦粉随上升油气夹带入柴、蜡油馏份中的份量
含有大量焦粉的塔底循环油,若外送出装置,会对换热和冷却设备的正常使用和循
13.977 3
0.023 2.76 100
占原油一次加工能力% 6.47 5.45 5.01 3.57 2.935 0.63 0.005 0.58 21.08
7
一. 延迟焦化工艺和工程
2 延迟焦化工艺特点
技术成熟、对原料适应性强 产品的灵活性 通过调节温度、压力和循环比等参数增加操作弹性
延迟焦化工艺和参数
晁可绳
2019年11月
1
延迟焦化工艺和参数
2
目录
• 延迟焦化工艺和工程 • 延迟焦化工艺流程 • 延迟焦化基本参数 • 加热炉长周期运行考虑 • 焦化产品收率和质量预测 • 延迟焦化工艺技术的发展 • 几点看法
3
一. 延迟焦化工艺和工程
4
一. 延迟焦化工艺和工程
• 延迟焦化工艺在炼油厂重油深加工中作用 • 延迟焦化工艺特点 • 延迟焦化工艺和工程设计考虑
油和焦炭收率之间最佳平衡和经济的操作点
• 加工重质劣质“四高”原料量,一般采用低压、高温和低循环比
操作条件,以实现最大馏份油收率,但务必注意弹丸焦生成问题。
• 调整循环比,在达到最大馏份油收率和处理量时,应满足对蜡油
(HCGO)质量要求
• 在采用低压操作时,务必考虑到焦炭塔内气速以及造成的设备、
管线及系统压降,从而对气压机产生的影响
延迟焦化讲义

延迟焦化讲义目录1 延迟焦化的发展 (2)2 延迟焦化生产过程 (3)2.1 工艺流程 ................................................................... (3)2.2 焦炭塔的操作 (6)2.3 水力除焦 (7)3 质量控制 (8)3.1 液体产品 (8)3.2 焦炭 (10)3.3 石油焦用途: .................................................... (11)3.3.1 石油焦用作电厂CFB锅炉的燃料 (11)3.3.2 焦炭的气化组合循环一体化装置(IGCC) ............... .. (11)3.3.3 冶金等行业 .............................................................. (12)4 我公司焦化装置状况介绍................................................. .. (13)4.1 装置主要操作参数 (13)4.2 装置生产负荷 (14)4.3 产品收率 ............................................................................. .. (14)5 我公司延迟焦化装置存在问题及解决方法 (15)5.1 降低3#焦化工艺用汽是当前重中之重的工作 (15)5.2 1#延迟焦化新鲜水耗水大、效率低,急需节能改造 ..... (16)5.3 3#延迟焦化接触冷却塔空冷用电效率低,有待改进 (16)5.4 现有装置的加工能力有待进一步挖掘 (16)5.5 电机用电量需要大力降低 (17)5.6 循环比有待进一步优化 (18)延迟焦化是在较长反应时间下,使原料深度裂化,以生产固体石油焦炭为主要目的,同时获得气体和液体产物。
延迟焦化工艺手册
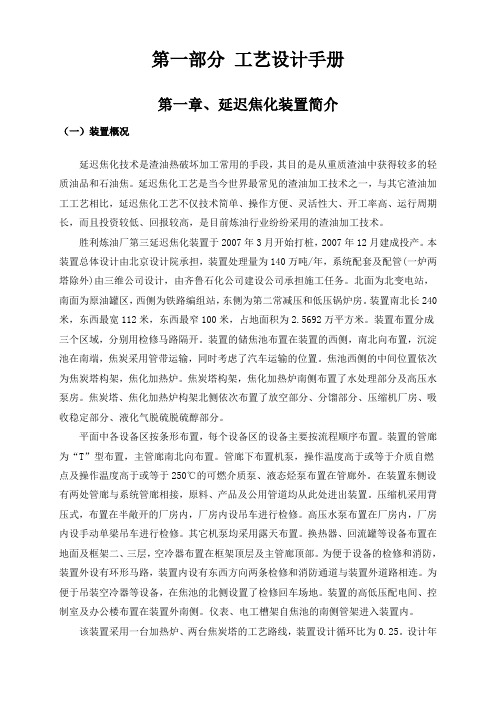
第一部分工艺设计手册第一章、延迟焦化装置简介(一)装置概况延迟焦化技术是渣油热破坏加工常用的手段,其目的是从重质渣油中获得较多的轻质油品和石油焦。
延迟焦化工艺是当今世界最常见的渣油加工技术之一,与其它渣油加工工艺相比,延迟焦化工艺不仅技术简单、操作方便、灵活性大、开工率高、运行周期长,而且投资较低、回报较高,是目前炼油行业纷纷采用的渣油加工技术。
胜利炼油厂第三延迟焦化装置于2007年3月开始打桩,2007年12月建成投产。
本装置总体设计由北京设计院承担,装置处理量为140万吨/年,系统配套及配管(一炉两塔除外)由三维公司设计,由齐鲁石化公司建设公司承担施工任务。
北面为北变电站,南面为原油罐区,西侧为铁路编组站,东侧为第二常减压和低压锅炉房。
装置南北长240米,东西最宽112米,东西最窄100米,占地面积为2.5692万平方米。
装置布置分成三个区域,分别用检修马路隔开。
装置的储焦池布置在装置的西侧,南北向布置,沉淀池在南端,焦炭采用管带运输,同时考虑了汽车运输的位置。
焦池西侧的中间位置依次为焦炭塔构架,焦化加热炉。
焦炭塔构架,焦化加热炉南侧布置了水处理部分及高压水泵房。
焦炭塔、焦化加热炉构架北侧依次布置了放空部分、分馏部分、压缩机厂房、吸收稳定部分、液化气脱硫脱硫醇部分。
平面中各设备区按条形布置,每个设备区的设备主要按流程顺序布置。
装置的管廊为“T”型布置,主管廊南北向布置。
管廊下布置机泵,操作温度高于或等于介质自燃点及操作温度高于或等于250℃的可燃介质泵、液态烃泵布置在管廊外。
在装置东侧设有两处管廊与系统管廊相接,原料、产品及公用管道均从此处进出装置。
压缩机采用背压式,布置在半敞开的厂房内,厂房内设吊车进行检修。
高压水泵布置在厂房内,厂房内设手动单梁吊车进行检修。
其它机泵均采用露天布置。
换热器、回流罐等设备布置在地面及框架二、三层,空冷器布置在框架顶层及主管廊顶部。
为便于设备的检修和消防,装置外设有环形马路,装置内设有东西方向两条检修和消防通道与装置外道路相连。
延迟焦化装置吸收稳定系统工艺与操作资料

延迟焦化装置吸收稳定系统工艺与操作资料xx年xx月xx日•延迟焦化装置介绍•吸收稳定系统介绍•延迟焦化装置操作资料•吸收稳定系统操作资料目•延迟焦化装置与吸收稳定系统的关系•实际操作中的注意事项录01延迟焦化装置介绍延迟焦化是将重质烃类在高温高压下进行裂解和缩合反应,生成气体、汽油、柴油、蜡油等产品的过程。
延迟焦化是一种热裂解过程,具有原料适应性强、产品灵活性大、原料中芳烃含量高的优点。
延迟焦化的定义和特点1 2 3原料油进入焦化装置,在加热炉中加热到400-500°C,进入焦炭塔进行反应。
在反应过程中,原料油发生裂解和缩合反应,生成气体、汽油、柴油、蜡油等产品。
反应后的油气进入分馏塔,分离出各种产品,残渣进入焦炭塔底部。
焦炭塔是反应的主要设备,底部有进料口和出料口,顶部有油气出口。
加热炉用于加热原料油至反应温度。
分馏塔用于分离出各种产品,如气体、汽油、柴油、蜡油等。
吸收稳定系统用于吸收和稳定各种产品,达到合格的指标。
冷凝器用于冷却油气,使其液化。
02吸收稳定系统介绍定义吸收稳定系统是延迟焦化装置中的重要部分,主要作用是降低混合碳四烃中各组分的含量,增加液化气中丙烷和丁烷的含量。
作用通过吸收稳定系统,可以降低混合碳四烃中C4、C5轻组分和C6以上的重组分的含量,同时增加液化气中丙烷和丁烷的含量,从而满足液化气产品的质量要求。
吸收稳定系统的定义和作用进入吸收稳定系统的原料主要是来自延迟焦化装置的混合碳四烃。
工艺流程混合碳四烃进入吸收塔,与脱乙烷塔来的贫油逆流接触,C4以下组分被吸收到油相中,从塔顶排出;C5以上组分从塔釜排出进入分馏塔,在分馏塔中切割成液化气和富气。
03脱乙烷塔主要作用是将吸收剂中的C2组分脱除,避免C2组分进入吸收塔影响吸收效果。
01吸收塔是吸收稳定系统的核心设备,主要作用是进行吸收操作,使混合碳四烃中的C4、C5轻组分被吸收剂吸收。
02分馏塔主要作用是将吸收剂中的C5以上组分分离成液化气和富气。
简述延迟焦化工艺流程

简述延迟焦化工艺流程延迟焦化工艺流程,那可真是个挺有趣的东西呢。
一、原料准备。
咱先说这原料啊,一般就是减压渣油之类的。
这些原料被送到装置里,就像是一群小士兵,要开始它们的奇妙之旅啦。
这些原料的性质可重要了呢,如果原料太稠或者杂质太多,那后面的工序可能就会有点小麻烦。
就好比你做饭,食材要是不新鲜或者没处理好,做出来的菜可能就不太美味啦。
二、加热炉加热。
然后啊,这些原料就被送到加热炉里去加热。
加热炉可就像一个大火炉,给原料们加足了热量。
这个时候,原料的温度会变得特别高,就像是被火烤得热烘烘的小土豆。
在加热的过程中,原料会发生一系列的反应,像是分子结构开始有了变化。
这就好比是一个人在经历了一场火热的历练之后,内心和外在都有了改变一样。
三、焦炭塔反应。
从加热炉出来后,原料就进入了焦炭塔。
在焦炭塔里,那可就是大变化的地方喽。
原料在这里会发生热裂解和缩合反应。
热裂解就像是把一个大的团体打散成一个个小的个体,而缩合反应呢,就像是这些小个体又重新组合起来,不过组合的方式可不一样啦。
慢慢地,在焦炭塔里就会形成焦炭和油气。
焦炭就像是沉淀在塔底的小硬块,而油气就像是轻盈的小仙子,它们要继续往别处去呢。
四、分馏过程。
接着,从焦炭塔出来的油气就进入了分馏塔。
分馏塔就像是一个大的分拣器,把油气按照不同的沸点分成不同的产品。
就像你把一堆不同颜色的小珠子按照颜色分类一样。
比如说,轻汽油、柴油、蜡油这些产品就被分出来了。
这个过程可不能马虎,要是分馏得不好,那产品的质量可就没法保证啦。
就像你把东西分类分错了,后面用的时候肯定会出问题。
五、焦炭处理。
再说说焦炭塔底部的焦炭吧。
这些焦炭可是不能一直留在塔里的,得把它们弄出来。
这就像是清理家里的垃圾一样,要及时处理。
有的时候是通过水力除焦的方式,就像用水枪把焦炭冲出来,这个过程看着还挺带劲的呢。
把焦炭处理好了,焦炭塔才能继续迎接下一轮的原料反应。
六、产品精制。
最后呢,那些分馏出来的产品也不是就直接能用啦,还得经过精制。
- 1、下载文档前请自行甄别文档内容的完整性,平台不提供额外的编辑、内容补充、找答案等附加服务。
- 2、"仅部分预览"的文档,不可在线预览部分如存在完整性等问题,可反馈申请退款(可完整预览的文档不适用该条件!)。
- 3、如文档侵犯您的权益,请联系客服反馈,我们会尽快为您处理(人工客服工作时间:9:00-18:30)。
延迟焦化工艺流程炼油厂的炼油工艺流程介绍上传时间:2009-07-31 12:03 点击:110正文:延迟焦化、加氢精制、制氢工艺流程工艺流程简述前言:根据济南炼油厂、海化集团等公司的延迟焦化装置、加氢装置、制氢装置的工艺流程整理而成。
并参考洛阳设计院、北京设计院、华西所提供材料。
一、100万吨/年延迟焦化装置本装置原料为减压渣油,温度为150℃,由常减压装置直接送入焦化装置内与柴油换热,换热后温度为170℃,进入原料油缓冲罐(D-101)。
原料油缓冲罐内的减压渣油由原料油泵抽出,与热蜡油经过两次换热再进加热炉对流段(Ⅱ)加热后分两股入焦化分馏塔(C-102)下段的五层人字挡板的上部和下部,在此与焦炭塔(C-101/1,2)顶来的油气接触,进行传热和传质。
原料油中蜡油以上馏分与来自焦炭塔顶油气中被冷凝的馏分(称循环油)一起流入塔底,在384℃温度下,用加热炉幅射进料泵抽出打入加热炉幅射段,在这里快速升温至500℃,然后通过四通阀入焦炭塔底。
循环油和原料油中蜡油以上馏分在焦炭塔内由于高温和长停留时间,产生裂解和缩合等一系列复杂反应,最后生成油气(包括富气、汽油、柴油和蜡油),由焦炭塔进入分馏塔,而焦炭则结聚在焦炭塔内。
从焦炭塔顶逸出的油气和水蒸气混合物进入分馏塔,在塔内与加热炉对流段来的原料换热,冷凝出循环油馏分,其余大量油气从换热段上升进入蜡油集油箱以上的分馏段,在此进行传热和传质过程,分馏出富气、汽油、柴油和蜡油。
焦化分馏塔油集油箱的蜡油经换热至90℃出装置进蜡油罐;另外引出两分路90℃冷蜡油作焦炭塔顶急冷油和装置封油用。
中段回流经中段回流蒸汽发生器发生蒸汽。
分馏塔顶回流从分馏塔抽出,经冷却后返回。
柴油从分馏塔进入汽提塔,经蒸汽汽提,柴油由汽油塔下部抽出,经换热冷却至70℃后分成两路,一路至加氢装置;另一路冷却至40℃进入柴油吸收塔作吸收剂来自压缩富气分液罐的富气进入柴油吸收塔下部,经吸收后,塔顶干气出装置进入全厂燃料气管网;塔底吸收油利用塔的压力(0.4MPa 表)自压入分馏塔作回流。
分馏塔顶油气经分馏塔顶空冷器和分馏塔顶油气后冷器冷却后进入分馏塔顶油气分离罐分离,分离出的汽油由汽油泵抽出分两路,一路去加氢装置,另一路返回塔顶作回流(不常用)。
油气分离罐顶的富气经富气压缩机加压后经压缩富气空冷器、压缩富气后冷器冷却后进入压缩富气分液罐,冷凝液凝缩油至加氢装置;富气进入柴油吸收塔下部(一些装置的实际生产证明,经柴油吸收后的干气带残液比较严重,约占干气的20%,我公司设计时可以将油气分离罐顶的富气经富气压缩机加压后并入芳构化装置的吸收稳定系统或催化装置的吸收稳定系统,以防止干气带残液。
)。
此外,为了防止分馏塔底部结焦,分馏塔底设分馏塔底循环泵。
切焦采用有井架双钻具方式,切焦水用高压水泵抽高位水箱的水,打到焦炭塔面,进行水力除焦。
焦炭和水一同流入贮焦池,经分离后切焦水流入沉淀池重新利用。
焦炭塔吹汽时,油气首先进入油气闪蒸罐,罐底污油经污油泵送出装置;罐顶油气进入水箱冷却器,冷却后进入吹汽放空油水分离罐,罐底污油经污油泵送出,含硫油污水经污水泵送至装置外污水处理场。
不凝气进入放空油气脱水罐,然后进入瓦斯系统去火炬烧掉。
二、60万吨/年加氢装置1、反应部分焦化汽油、焦化柴油从延迟焦化装置直接进料,为控制加氢反应平稳,应严格控制其进料比例。
两种原料进装置后经原料混合罐(D-201)混合,再经原料油泵(P-201/1、2)、过滤器(SR-201/1、2)、原料油脱水罐(D-202)进入原料油缓冲罐(D-203)。
原料油过滤和脱水的目的是为了脱除堵塞反应器上部床层的固体颗粒和影响催化剂强度的水分。
D-201、D-203用氮气气封保护。
D-203中的原料经反应进料泵(P-202/1、2)升压至9.6MPa(A),经流量控制,与来自新氢压缩机(K-201/1、2)和循环氢压缩机(K-202/1、2)的混合氢混合,首先经混氢原料(I)/反应产物换热器(E-204/1、2)换热,再经由混氢原料(Ⅱ)/反应产物换热器(E-201)与反应产物换热至199℃进入反应加热炉(F-201),加热至303℃进入至加氢反应器(R-201)中,该反应器设置二段催化剂床层,两床层间设有注急冷氢设施。
自反应器(R-201)来的反应产物经混氢原料(Ⅱ)/反应产物换热器(E-201)、汽提塔底油/反应产物换热器(E-202)、低分油/反应产物换热器(E203)、混氢原料(I)/反应产物换热器(E-204/1、2)换热,然后依次经反应产物空冷器(EC-201/1、2)、反应产物后冷器(E-207/1、2)冷却至40℃,进入高压分离器(D-204)。
为了防止反应产物中的铵盐在低温部位结晶,通过脱氧水泵(P-207/1、2)将脱氧水注入到(EC-201/1、2)或(E-204/1、2)上游的管道中。
冷却后的反应物在D-204中进行油、气、水三相分离。
高分气(循环氢)经K-202/1、2入口分液罐(D-208)分液后,进入循环氢压缩机(K-202/1、2)升压至8.8MPa(G),然后分两路:一路作为急冷氢进入R-201,一路与来自新氢压缩机(K-201/1、2)的新氢混合,混合氢与原料油混合作为反应进料。
含硫、含氨污水自D-204底排出,至装置外统一处理。
D-204油相在液位控制下,经减压调节阀进入低压分离器(D-205),D-205闪蒸气排至燃料气管网。
低分油经低分油/分馏塔底油换热器(E-206/1、2)和E-203分别与精制重石脑油、反应产物换热至200℃后去分馏部分汽提塔(C-201)。
汽提塔底油经汽提塔底油/分馏塔底油换热器(E-205)和E-202分别与精制重石脑油、反应产物换热至245℃后去分馏部分分馏塔(C-202)。
新氢自制氢装置来,经新氢压缩机入口分液罐(D-207)分液后进入K-201/1、2并经三级升压至8.8MPa(G),再与K-202/1、2出口的循环氢混合。
2、分馏部分从反应部分来的低分油经换热后进入C-201。
塔底用0.8MPa过热蒸汽汽提。
塔顶油气经汽提塔顶空冷器(EC-202/1、2)和汽提塔顶后冷器(E-208)冷凝冷却至40℃,进入汽提塔顶回流罐(D-210)进行气、油、水三相分离。
闪蒸出的气体作为燃料进入燃料气管网。
含硫污水送出装置。
油相经汽提塔顶回流泵(P-203/1、2)升压后作为塔顶回流全部返回汽提塔(C-201)。
塔底油自压经E-205与精制重石脑油换热后去反应部分E-202换热器。
从反应部分来的低分油经换热后进入C-202。
塔底用重沸炉提供热源。
塔顶油气经分馏塔顶空冷器(EC-203/1、2)和分馏塔顶后冷器(E-209)冷却至40℃,进入分馏塔顶回流罐(D-211)进行气、油、水三相分离。
闪蒸出的气体通过放空罐至火炬。
含硫污水送出装置。
油相经分馏塔顶回流泵(P-204/1、2)升压后一部分作为塔顶回流,一部分作为精制轻石脑油出装置。
塔底精制重石脑油一小部分经分馏塔底产品泵(P-206/1、2)增压后经E-205和E-206/1、2分别与汽提塔底油、低分油换热至100℃左右,然后进入精制重石脑油后冷器(E-210)冷却至60℃出装置。
塔底精制重石脑油大部分经分馏塔底循环泵(P-205/1、2)增压后用分馏塔底重沸炉(F-202)加热至290℃左右返回分馏塔下部,以补充分馏所需能量。
为了抑制硫化氢对塔顶管道和冷换设备的腐蚀,在塔顶管道注入缓蚀剂。
缓蚀剂自缓蚀剂罐(D-212)经缓蚀剂泵(P-209/1,2)抽出后分两路,一路注入C-201塔顶管道;另一路注入C-202塔顶管道。
3、催化剂预硫化部分为了使催化剂具有良好的活性,新鲜的或再生后的催化剂在使用前都必须进行预硫化。
本设计采用湿法硫化,以直馏煤油为硫化油,二硫化碳为硫化剂。
催化剂进行预硫化操作时,系统内氢气经循环氢压缩机(K-202/1、2)按正常操作流程进行全量循环。
二硫化碳自二硫化碳桶用硫化剂泵(P-208)升压后至反应进料泵入口,经反应进料泵(P-202/1、2)后与氢气混合,经反应产物与混氢原料油换热器(E-204/1、2、E-201)换热,经反应进料加热炉(F-201)升温,然后经过催化剂床层,对催化剂进行预硫化。
自反应器底部出来的硫化油和循环氢等经E-201、E-202、E-203、E-204/1、2换热,经EC-201/1、2、E-207/1、2冷却后至高压分离器(D-204)进行气、油、水三相分离。
气体自顶部出来,经D-208入K-202/1、2实现循环氢的循环,硫化油自高分罐(D-204)下部出来经调节阀降压后进入低分罐(D-205)阀蒸分离,液相返至原料油缓冲罐(D-203)入口实现循环流化,闪蒸出来的低分气至燃料气系统,催化剂预硫化过程中产生的水间断从高分罐(D-204)底部排出。
催化剂预硫化结束后,硫化油改进原料油出装置线退出装置。
三、10000标方/小时制氢装置1、进料系统由装置外来的干气进入原料气缓冲罐,经过原料气压缩机压缩后进入原料气脱硫部分。
2、脱硫部分进入脱硫部分的原料气经原料预热炉予热升温至380℃,进入加氢反应器发生反应,使有机硫转化为硫化氢后进入氧化锌脱硫反应器,硫化氢与氧化锌反应生成固体硫化锌被吸收下来。
脱除硫化氢后的气体硫含量小于0.2PPm,进入转化部分。
具体反应如下:硫醇: RSH+H2→RH+H2s硫醚: R1SR2+2H2→R1H+R2H+H2S二硫醚: R1SSR2+3H2→R1H+R2H+2H2S噻吩: C4H4S+4H2→C4H10+H2S氧硫化碳: COS+H2→CO+H2S二硫化碳: CS2+4H2→CH4+2H2SZnO(固)+H2S=ZnS(固)+H2O △Ho 298 =-76.62kJ/mol3、转化部分精制后的原料气按水碳比3.5与水蒸汽混合,再经转化炉对流段予热至500℃,进入转化炉辐射段。
在催化剂的作用下,发生复杂的水蒸汽转化反应,从而生产出氢气、甲烷、一氧化碳、二氧化碳和水的平衡混合物。
主要反应有:CnHm+nH2O =nCO+(n+m/2)H2 ①CO+3H2=CH4+H2O △Ho298 =-206kJ/mol ②CO+H2O=CO2+H2 △Ho298 =-41kJ/mol ③以甲烷为主的气态烃,蒸汽转化过程较为简单,主要发生上述反应,最终产品气组成由反应②③平衡决定。
而轻石脑油,由于其组成较为复杂,有烷烃、环烷烃、芳烃等,因此,除上述反应外,在不同的催化床层,还发生高级烃的热裂解、催化裂解、脱氢、加氢、积炭、氧化、变换、甲烷化等反应,最终产品气组成仍由反应②③平衡决定。
烃类水蒸汽转化反应是体积增大的强吸热反应,低压、高温、高水碳比有利于上述反应的进行。