数控技术的发展及行业新技术.共70页
数控机床技术发展现状及趋势
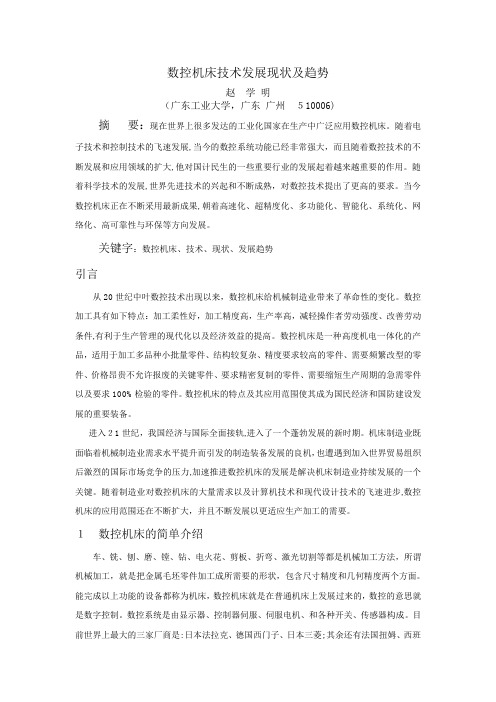
数控机床技术发展现状及趋势赵学明(广东工业大学,广东广州510006)摘要:现在世界上很多发达的工业化国家在生产中广泛应用数控机床。
随着电子技术和控制技术的飞速发展,当今的数控系统功能已经非常强大,而且随着数控技术的不断发展和应用领域的扩大,他对国计民生的一些重要行业的发展起着越来越重要的作用。
随着科学技术的发展,世界先进技术的兴起和不断成熟,对数控技术提出了更高的要求。
当今数控机床正在不断采用最新成果,朝着高速化、超精度化、多功能化、智能化、系统化、网络化、高可靠性与环保等方向发展。
关键字:数控机床、技术、现状、发展趋势引言从20世纪中叶数控技术出现以来,数控机床给机械制造业带来了革命性的变化。
数控加工具有如下特点:加工柔性好,加工精度高,生产率高,减轻操作者劳动强度、改善劳动条件,有利于生产管理的现代化以及经济效益的提高。
数控机床是一种高度机电一体化的产品,适用于加工多品种小批量零件、结构较复杂、精度要求较高的零件、需要频繁改型的零件、价格昂贵不允许报废的关键零件、要求精密复制的零件、需要缩短生产周期的急需零件以及要求100%检验的零件。
数控机床的特点及其应用范围使其成为国民经济和国防建设发展的重要装备。
进入21世纪,我国经济与国际全面接轨,进入了一个蓬勃发展的新时期。
机床制造业既面临着机械制造业需求水平提升而引发的制造装备发展的良机,也遭遇到加入世界贸易组织后激烈的国际市场竞争的压力,加速推进数控机床的发展是解决机床制造业持续发展的一个关键。
随着制造业对数控机床的大量需求以及计算机技术和现代设计技术的飞速进步,数控机床的应用范围还在不断扩大,并且不断发展以更适应生产加工的需要。
1数控机床的简单介绍车、铣、刨、磨、镗、钻、电火花、剪板、折弯、激光切割等都是机械加工方法,所谓机械加工,就是把金属毛坯零件加工成所需要的形状,包含尺寸精度和几何精度两个方面。
能完成以上功能的设备都称为机床,数控机床就是在普通机床上发展过来的,数控的意思就是数字控制。
我选择数控专业的原因及发展前景分析

我选择数控专业的原因及发展前景分析我选择数控专业的原因及发展前景分析在不久的将来,机械制造业将迎来一次重要的技术变革,数控技术将会成为制造业的主要发展方向。
因此,我选择了数控专业,希望能够更好地适应未来社会的发展趋势。
本文将详细介绍我选择数控专业的原因以及对数控技术未来发展的分析。
一、我选择数控专业的原因1.职业前景广阔数控技术是目前最为先进的制造技术之一,与传统的手工加工方式相比,数控技术具有效率高、精度高、稳定性好等优点。
在未来的社会中,数控技术将有着广泛的应用场景,如航空航天、汽车制造、电子、信息技术等领域,都对数控专业人才有着较高的需求。
因此,选择数控专业能够为我未来的职业发展打下坚实的基础。
2.技术含量高、不断创新随着科技的不断发展,数控技术也在不断地更新换代,更新速度极快。
选择数控专业,能够不断学习更新的技术,不断提高自己的技术含量,适应行业不断变化的需求,保证自身的竞争力。
而且,随着数控技术的不断发展,更多的应用领域将会被数控技术所覆盖,这将给从事数控行业的人带来更多的发展机会。
3.数控技术是未来制造业的发展方向未来,制造业将会迎来技术变革的浪潮,数控技术无疑是未来制造业的发展方向。
由于数控技术具有高效、环保、精度高等特点,将会在未来的制造业中得到广泛的应用。
选择数控专业能够适应未来的行业发展趋势,也能够适应市场的需求,确保职业的稳定,同时也为未来创业打下基础。
二、数控技术的发展趋势1.技术将会更加智能化随着人工智能技术的不断发展,数控技术将会更加智能化。
未来的数控系统将会拥有更多的人工智能技术,能够更好地适应市场和消费者的需求,实现更高效率、更精准的加工。
因此,从事数控行业的人,需要具备更高的智能化水平,适应未来的技术趋势。
2.应用场景将更加广泛数控技术在制造业中的应用场景已经比较广泛,未来更多领域也将会应用数控技术,如教育、医疗等。
因此,数控技术的发展将不再局限于制造业,将会覆盖更广泛的领域,给数控行业带来更多的挑战和机遇。
数控发展趋势

数控发展趋势一数控技术简介数控机床是以数控系统为代表的新技术对传统机械制造产业的渗透形成的机电一体化产品;其技术范围覆盖很多领域:1机械制造技术;2信息处理、加工、传输技术:3自动控制技术;4伺服驱动技术;5传感器技术:6软件技术等;计算机对传统机械制造产业的渗透,完全改变了制造业;制造业不但成为工业化的象征,而且由于信息技术的渗透,使制造业犹如朝阳产业具有广阔的发展天地;数控技术的应用不但给传统制造业带来了性的变化,使制造业成为工业化的象征,而且随着数控技术的不断发展和应用领域的扩大,他对国计民生的一些重要行业IT、汽车、轻工、医疗等的发展起着越来越重要的作用,因为这些行业所需装备的数字化已是现代发展的大趋势;从目前世界上数控技术及其装备发展的趋势来看,其主要研究热点有以下几个方面;数控机床是以数控系统为代表的新技术对传统机械制造产业的渗透形成的机电一体化产品;其技术范围覆盖很多领域:1机械制造技术;2信息处理、加工、传输技术:3自动控制技术;4伺服驱动技术;5传感器技术:6软件技术等;计算机对传统机械制造产业的渗透,完全改变了制造业;制造业不但成为工业化的象征,而且由于信息技术的渗透,使制造业犹如朝阳产业具有广阔的发展天地;二数控技术国内外现状1 开放结构的发展数控技术从发明到现在,已有近50年的历史;按照电子器件的发展可分为五个发展阶段:电子管数控,晶体管数控,中小规模IC数控,小型计算机数控,微处理器数控;从体系结构的发展,可分为以硬件及连线组成的硬数控系统、计算机硬件及软件组成的CNC数控系统,后者也称为软数控系统:从伺服及控制的方式可分为步进电机驱动的开环系统和伺服电机驱动的闭环系统;数控系统装备的机床大大提高了加工精度、速度和效率;人类发明了机器,延长和扩展人的手脚功能:当出现数控系统以后,制造厂家逐渐希望数控系统能部分代替机床设计师和操作者的大脑,具有一定的智能,能把特殊的加工工艺、管理经验和操作技能放进数控系统,同时也希望系统具有图形交互、诊断功能等;首先就要求数控系统具有友好的人机界面和开发平台,通过这个界面和平台开放而自由地执行和表达自己的思路;这就产生了开放结构的数控系统;机床制造商可以在该开放系统的平台上增加一定的硬件和软件构成自己的系统;目前,开放系统有两种基本结构:1CNC+PC主板:把一块PC主板插入传统的CNC机器中,PC板主要运行实时控制,CNC主要运行以坐标轴运动为主的实时控制;2PC+运动控制板:把运动控制板插入PC机的标准插槽中作实时控制用,而PC机主要作非实时控制;开放结构在90年代初形成;对于许多熟悉计算机应用的系统厂家,往往采用第2方案;但目前主流数控系统生产厂家认为数控系统最主要的性能是可靠性,象PC机存在的死机现象是不允许的;而系统功能首先追求的仍然是高精高速的加工;加上这些厂家长期已经生产大量的数控系统:体系结构的变化会对他们原系统的维修服务和可靠性产生不良的影响;因此不把开放结构作为主要的产品,仍然大量生产原结构的数控系统;为了增加开放性,主流数控系统生产厂家往往采用1方案,即在不变化原系统基本结构的基础上增加一块PC板,提供键盘使用户能把PC和CNC联系在一起,大大提高了人机界面的功能比较典型的如FANUC的150/160/180/210系统;有些厂家也把这种装置称为融合系统fusionsystem;由于它工作可靠,界面开放,越来越受到机床制造商的欢迎;2 软件伺服驱动技术伺服技术是数控系统的重要组成部分;广义上说,采用计算机控制,控制算法采用软件的伺服装置称为“软件伺服”;它有以下优点:1无温漂,稳定性好;2基于数值计算,精度高;3通过参数对设定,调整减少;4容易做成ASIC电路;70年代,美国GATTYS公司发明了直流力矩伺服电机,从此开始大量采用直流电机驱动;开环的系统逐渐由闭环的系统取代;但直流电机存在以下缺点:1电动机容量、最高转速、环境条件受到限制;2换向器、电刷维护不方便;交流异步电机虽然价格便宜、结构简单,但早期由於控制性能差,所以很长时间没有在数控系统上得到应用;随着电力电子技术的发展,1971年,德国西门子的发明了交流异步机的矢量控制法;1980年,德国人Leonhard为首的研究小组在应用微理器的矢量控制的研究中取得进展,使矢量控制实用化;从70年代末,数控机床逐渐采用异步电机为主轴的驱动电机;如果把直流电机进行“里翻外”的处理,即把电驱绕组装在定子,转子为永磁部分,由转子轴上的编码器测出磁极位置,这就构成了永磁无刷电机;这种电机具有良好的伺服性能;从80年代开始,逐渐应用在数控系统的进给驱动装置上;为了实现更高的加工精度和速度,90年代,许多公司又研制了直线电机;它由两个非接触元件组成,即磁板和线卷滑座:电磁力直接作用于移动的元件而无需机械连接,没有机械滞后或螺距周期误差,精度完全依赖于直线反馈系统和分级的支承,由全数字伺服驱动,刚性高,频响好,因而可获得高速度;但由于它的推力还不够大,发热,漏磁及造价也影响了它的广泛应用;对现代数控系统,伺服技术取得的最大突破可以归结为:交流驱动取代直流驱动、数字控制取代模拟控制、或者把它称为软件控制取代硬件控制;这两种突破的结果产生了交流数字驱动系统,应用在数控机床的伺服进给和主轴装置;由于电力电子技术及控制理论、微处理器等微电子技术的快速发展,软件运算及处理能力的提高,特别是DSP的应用,使系统的计算速度大大提高,采样时间大大减少;这些技术的突破,使伺服系统性能改善、可靠性提高、调试方便、柔性增强;大大推动了高精高速加工技术的发展;3 CNC系统的连网数控系统从控制单台机床到控制多台机床的分级式控制需要网络进行通信;网络的主要任务是进行通信,共享信息;这种通信通常分三级:1工厂管理级;一般由以太网组成;2车间单元控制级;一般由DNC功能进行控制;通过DNC功能形成网络可以实现对零件程序的上传或下传:读、写CNC的数据:PLC数据的传送;存贮器操作控制;系统状态采集和远程控制等;更高档次的DNC还可以对CAD/CAM/CAPP以及CNC的程序进行传送和分级管理;CNC与通信网络联系在一起还可以传递维修数据,使用户与NC生产厂直接通信:进而,把制造厂家联系一起,构成虚拟制造网络;3现场设备级;现场级与车间单元控制级及信息集成系统主要完成底层设备单机及I/0控制、连线控制、通信连网、在线设备状态监测及现场设备生产、运行数据的采集、存储、统计等功能,保证现场设备高质量完成生产任务,并将现场设备生产运行数据信息传送到工厂管理层,向工厂级提供数据;同时也可接受工厂管理层下达的生产管理及调度命令并执行之;因此,现场级与车间级是实现工厂自动化及CIMS系统的基础;传统的现场级大多是基于PLC的分布式系统;其主要特点是现场层设备与控制器之间的连接是一对一,即一个I/0点对设备的一个测控点;所谓I/0接线方式为传递4-20ma模拟量信息或24VDC开关信息;这种系统的缺点是:信息集成能力不强、系统不开放、可集成性差、专业性不强、可靠性不易保证、可维护性不高;现场总线是以单个分散的、数字化、智能化的测量和控制设备作为网络节点,用总线相连接,实现相互交换信息,共同完成自动控制功能的网络系统与控制系统;因此,现场总线是面向:工厂底层自动化及信息集成的数字网络技术;现场总线技术的主要特点为:它是数控系统通信向现场级的延伸、数字化通信取代4-20ma模拟信号、应用现场总线技术,要求现场设备智能化可编程或可参数化:它集现场设备的远程控制、参数化及故障诊断为一体:由于现场总线具有开放性、互操作性、互换性、可集成性,因此是实现数控系统设备层信息集成的关键技术;它对提高生产效率、降低生产成本非常重要;目前在工业上采用的现场总线有PROFIBUS-DP,SERCOS,JPCN-1,Deviconet,CAN,hterbus—S,Marco等;有的公司还有自己的总线,比如FANUC的FSSB,I/OLINK相当于JPCN—1,YASKAWA的MOTIONLINK等;目前比较活跃的是Prof主bus-DP,为了允许更快的数据传送速度,它由0SI的七层结构省去3-7层构成;西门子最新推出802D的伺服控制就是由PROFIBOUS-DP控制的;4功能不断发展和扩大WIDTH=200 align=right BBCOLOR=e5ebba BORDERCOLIRIGHT=006600BORDER=1>快速移动速度m/min分辨率μm2401100101NC技术经过50年的发展,已经成为制造技术发展的基础;这里以FANUC最先进的CNC控制系统15i/150i为例说明系统功能的发展;这是一台具有开放性,4通道、最多控制轴数为24轴、最多联动轴数为24轴、最多可控制4个主轴的CNC系统;其快速移动速度与分辨率关系如右表;它的技术特点反映了现代NC发展的特点:开放性:系统可通过光纤与PC机连接,采用Window兼容软件和开发环境;功能以高速、超精为核心,并具有智能控制;特别适合于加工航空机械零件,汽车及家电的高精零件,各种模具和复杂的需5轴加工的零件;15i/150主具有高精纳米插补功能;即使系统的设定编程单位为1μm,通过纳米插补也可提供数字伺服以1nm为单位的指令,平滑了机床的移动量,提高了加工表面光洁度,大大减少加工表面的误差;当分辨率为时,快速可达240m/min速度;系统还具有高速高精加工的智能控制功能:1预计算出多程序段刀具轨迹,并进行预处理;2智能控制,计及机床的机械性能,可按最佳的进率和最大的允许加速度工作,使机床的功能得到最大的发挥;以便降低加工时间,提高效率,同时提高加工精度;3系统可在分辨率为1nm时工作,适用于控制超精机械;高级复杂的功能:15i/150i可进行各种数学的插补,如直线、圆弧、螺旋线、渐开线、螺旋渐开线、样条等插补;也可以进行NURBS非均匀有理B样条插补;采用NURBS插补可以人人减少NC程序的数据输入量,减少加工时间,特别适用模具加工;NURBS插补不需任何硬件;强力的联网通信功能;适应工厂自动化需要,支持标准FA网络及DNC的连接;1工厂干线或控制层通信网络:由PC机通过以太网控制多台15i/150i组成的加工单元,可以传送数据、参数等;2设备层通信网络:15i/150i采用I/0LINK与日本标准JPCN-1相对应的一种现场总线;3通过RS-485接口传送I/0信号:或且也可采用PRELLBUS—DP符合欧洲1标准EN50170以12Mbps进行高速通信;具有高速度内装的PMC有的厂商称为PLC,以减少加工的循环的时间:1梯形图和顺序程序由专用的PMC处理器控制,这种结构可进行快速大规模顺序控制;2基本PMC指令执行时间为:;最大步数:32,000步;3可以用C语言编程;32位的C语言处理器可作为实时多任务运行;它与梯形图计算的PMC处理器并行工作;4可在PC机上进行程序开发;先进的操作:性和维修性;(1)具有触摸面板,容易操作;2可采用存储卡来改变输入输出三数控发展趋势1、高速、高精加工技术及装备的新趋势效率、质量是先进制造技术的主体;高速、高精加工技术可极大地提高效率,提高产品的质量和档次,缩短生产周期和提高市场竞争能力;为此日本先端技术研究会将其列为5大现代制造技术之一,国际生产工程学会CIRP将其确定为21世纪的中心研究方向之一;在轿车工业领域,年产30万辆的生产节拍是40秒/辆,而且多品种加工是轿车装备必须解决的重点问题之一;在航空和宇航工业领域,其加工的零部件多为薄壁和薄筋,刚度很差,材料为铝或铝合金,只有在高切削速度和切削力很小的情况下,才能对这些筋、壁进行加工;近来采用大型整体铝合金坯料“掏空”的方法来制造机翼、机身等大型零件来替代多个零件通过众多的铆钉、螺钉和其他联系方式拼装,使构件的强度、刚度和可靠性得到提高;这些都对加工装备提出了高速、高精和高柔性的要求;从EMO2001展会情况来看,高速加工中心进给速度可达80m/min,甚至更高,空运行速度可达100m/min左右;目前世界上许多汽车厂,包括我国的上海通用汽车公司,已经采用以高速加工中心组成的生产线部分替代组合机床;美国CINCINNATI公司的HYPERMACH机床速度最大达60m/min,快速为100m/min,加速度达2g,主轴转速已达60 000r/min;加工薄壁飞机零件,只用30min,而同样的零件在一般高速铣床加工需3h,在普通铣床加工需8h;德国DMG公司的双主轴车床的主轴速度及加速度分别达12000r/mm和1g;在加工精度方面,近10年来,普通级数控机床的加工精度已由10μm提高到5μm,精密级加工中心则从3~5μm,提高到1~μm,并且超精密加工精度已开始进入纳米级μm;在可靠性方面,国外数控装置的MTBF值已达6 000h以上,伺服系统的MTBF值达到30000h 以上,表现出非常高的可靠性;为了实现高速、高精加工,与之配套的功能部件如电主轴、直线电机得到了快速的发展,应用领域进一步扩大;2、轴联动加工和复合加工机床快速发展采用5轴联动对三维曲面零件的加工,可用刀具最佳几何形状进行切削,不仅光洁度高,而且效率也大幅度提高;一般认为,1台5轴联动机床的效率可以等于2台3轴联动机床,特别是使用立方氮化硼等超硬材料铣刀进行高速铣削淬硬钢件时,5轴联动加工可比3轴联动加工发挥更高的效益;但过去因5轴联动数控系统、主机结构复杂等原因,其价格要比3轴联动数控机床高出很多,加之编程技术难度较大,制约了5轴联动机床的发展;当前由于电主轴的出现,使得实现5轴联动加工的复合主轴头构造大为简化,其制造难度和成本大幅度降低,数控系统的价格差距缩小;因此促进了复合主轴头类5轴联动机床和复合加工机床含5面加工机床的发展在EMO2001展会上,新日本工机的5面加工机床采用复合主轴头,可实现4个垂直平面的加工和任意角度的加工,使得5面加工和5轴加工可在同一台机床上实现,还可实现倾斜面和倒锥孔的加工;德国DMG公司展出DMUVOUTION系列加工中心,可5面加工和5轴联动加工,可由CNC系统控制或CAD/CAM直接或间接控制;3、智能化、开放式、网络化成为当代数控系统发展的主要趋势21世纪的数控装备将是具有一定智能化的系统,智能化的内容包括在数控系统中的各个方面:为追求加工效率和加工质量方面的智能化,如加工过程的自适应控制,工艺参数自动生成;为提高驱动性能及使用连接方便的智能化,如前馈控制、电机参数的自适应运算、自动识别负载自动选定模型、自整定等;简化编程、简化操作方面的智能化,如智能化的自动编程、智能化的人机界面等;还有智能诊断、智能监控方面的内容、方便系统的诊断及维修等;为解决传统的数控系统封闭性和数控应用软件的产业化生产存在的问题;目前许多国家对开放式数控系统进行研究,如美国的NGCThe Next Generation Work-Station/Machine Control、欧共体的OSACAOpen System Architecture for Control within Automation Systems、日本的OSECOpen System Environment for Controller,中国的ONCOpen Numerical Control System等;数控系统开放化已经成为数控系统的未来之路;所谓开放式数控系统就是数控系统的开发可以在统一的运行平台上,面向机床厂家和最终用户,通过改变、增加或剪裁结构对象数控功能,形成系列化,并可方便地将用户的特殊应用和技术诀窍集成到控制系统中,快速实现不同品种、不同档次的开放式数控系统,形成具有鲜明个性的名牌产品;目前开放式数控系统的体系结构规范、通信规范、配置规范、运行平台、数控系统功能库以及数控系统功能软件开发工具等是当前研究的核心;网络化数控装备是近两年国际着名机床博览会的一个新亮点;数控装备的网络化将极大地满足生产线、制造系统、制造企业对信息集成的需求,也是实现新的制造模式如敏捷制造、虚拟企业、全球制造的基础单元;国内外一些着名数控机床和数控系统制造公司都在近两年推出了相关的新概念和样机,如在EMO2001展中,日本山骑马扎克MAZAK公司展出的“CYBERPRODUCTION Center”智能生产控制中心,简称CPC;日本大尉Okuma机床公司展出“IT plaza”信息技术广场,简称IT广场;德国西门子Siemens公司展出的Open Manufacturing Environment开放制造环境,简称OME等,反映了数控机床加工向网络化方向发展的趋势;4、重视新技术标准、规范的建立如前所述,开放式数控系统有更好的通用性、柔性、适应性、扩展性,美国、欧共体和日本等国纷纷实施战略发展计划,并进行开放式体系结构数控系统规范OMAC、OSACA、OSEC的研究和制定,世界3个最大的经济体在短期内进行了几乎相同的科学计划和规范的制定,预示了数控技术的一个新的变革时期的来临;我国在2000年也开始进行中国的ONC数控系统的规范框架的研究和制定;数控标准是制造业信息化发展的一种趋势;数控技术诞生后的50年间的信息交换都是基于ISO6983标准,即采用G,M代码描述如何how加工,其本质特征是面向加工过程,显然,他已越来越不能满足现代数控技术高速发展的需要;为此,国际上正在研究和制定一种新的CNC系统标准ISO14649STEP-NC,其目的是提供一种不依赖于具体系统的中性机制,能够描述产品整个生命周期内的统一数据模型,从而实现整个制造过程,乃至各个工业领域产品信息的标准化;STEP-NC的出现可能是数控技术领域的一次,对于数控技术的发展乃至整个制造业,将产生深远的影响;首先,STEP-NC提出一种崭新的制造理念,传统的制造理念中,NC加工程序都集中在单个计算机上;而在新标准下,NC程序可以分散在互联网上,这正是数控技术开放式、网络化发展的方向;其次,STEP-NC数控系统还可大大减少加工图纸约75%、加工程序编制时间约35%和加工时间约50%;目前,欧美国家非常重视STEP-NC的研究,欧洲发起了STEP-NC的IMS计划;参加这项计划的有来自欧洲和日本的20个CAD/CAM/CAPP/CNC用户、厂商和学术机构;美国的STEP Tools公司是全球范围内制造业数据交换软件的开发者,他已经开发了用作数控机床加工信息交换的超级模型Super Model,其目标是用统一的规范描述所有加工过程;目前这种新的数据交换格式已经在配备了SIEMENS、FIDIA以及欧洲OSACA-NC数控系统的原型样机上进行了验证;。
数控技术现状及发展趋势

数控技术现状及发展趋势
一、数控技术简介
二、数控技术现状
1、数控技术的发展史
数控技术在20世纪50年代开始被使用,当时它只能控制简单的机器
工具,用于简单的加工操作,如磨削、切削和拧紧。
时至今日,随着计算
机技术的发展,数控技术也逐渐成熟,得到了广泛的应用,如自动装配、
自动焊接、自动吹塑、仿生机械手等。
2、数控技术的应用领域
数控技术主要应用于机械加工领域,如机床、定位机床、冲床、刨床、模具加工中心等。
数控技术还推动了机器人技术的发展,广泛应用于机器
人加工中心等设备,大大提升了机械加工的精度和灵活性,为现代制造业
带来了极大的改善。
此外,数控技术还被广泛应用于航空航天、汽车、电子等行业,用于
制造部件及装配、焊接等工作,大大提高了效率、精度和灵活性,进而推
动了各个行业的发展。
三、数控技术的发展趋势
1、智能化及多个联动。
数控技术的发展趋势
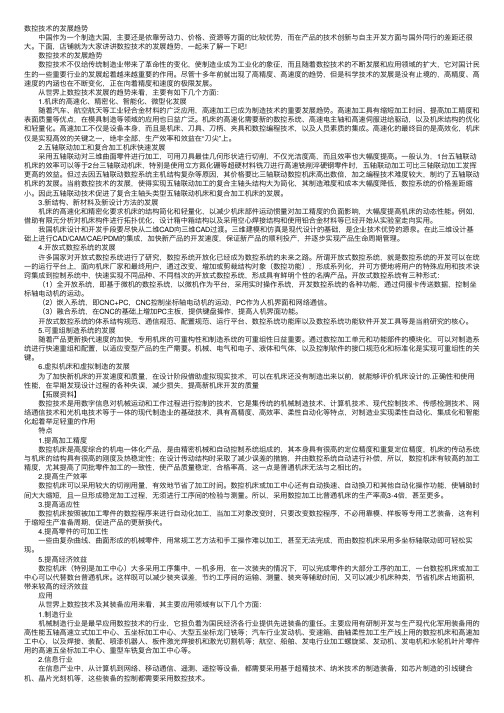
数控技术的发展趋势 中国作为⼀个制造⼤国,主要还是依靠劳动⼒、价格、资源等⽅⾯的⽐较优势,⽽在产品的技术创新与⾃主开发⽅⾯与国外同⾏的差距还很⼤。
下⾯,店铺就为⼤家讲讲数控技术的发展趋势,⼀起来了解⼀下吧! 数控技术的发展趋势 数控技术不仅给传统制造业带来了⾰命性的变化,使制造业成为⼯业化的象征,⽽且随着数控技术的不断发展和应⽤领域的扩⼤,它对国计民⽣的⼀些重要⾏业的发展起着越来越重要的作⽤。
尽管⼗多年前就出现了⾼精度、⾼速度的趋势,但是科学技术的发展是没有⽌境的,⾼精度、⾼速度的内涵也在不断变化,正在向着精度和速度的极限发展。
从世界上数控技术发展的趋势来看,主要有如下⼏个⽅⾯: 1.机床的⾼速化、精密化、智能化、微型化发展 随着汽车、航空航天等⼯业轻合⾦材料的⼴泛应⽤,⾼速加⼯已成为制造技术的重要发展趋势。
⾼速加⼯具有缩短加⼯时间、提⾼加⼯精度和表⾯质量等优点,在模具制造等领域的应⽤也⽇益⼴泛。
机床的⾼速化需要新的数控系统、⾼速电主轴和⾼速伺服进给驱动,以及机床结构的优化和轻量化。
⾼速加⼯不仅是设备本⾝,⽽且是机床、⼑具、⼑柄、夹具和数控编程技术,以及⼈员素质的集成。
⾼速化的最终⽬的是⾼效化,机床仅是实现⾼效的关键之⼀,绝⾮全部,⽣产效率和效益在“⼑尖”上。
2.五轴联动加⼯和复合加⼯机床快速发展 采⽤五轴联动对三维曲⾯零件进⾏加⼯,可⽤⼑具最佳⼏何形状进⾏切削,不仅光洁度⾼,⽽且效率也⼤幅度提⾼。
⼀般认为,1台五轴联动机床的效率可以等于2台三轴联动机床,特别是使⽤⽴⽅氮化硼等超硬材料铣⼑进⾏⾼速铣削淬硬钢零件时,五轴联动加⼯可⽐三轴联动加⼯发挥更⾼的效益。
但过去因五轴联动数控系统主机结构复杂等原因,其价格要⽐三轴联动数控机床⾼出数倍,加之编程技术难度较⼤,制约了五轴联动机床的发展。
当前数控技术的发展,使得实现五轴联动加⼯的复合主轴头结构⼤为简化,其制造难度和成本⼤幅度降低,数控系统的价格差距缩⼩。
数控加工技术的应用及发展

数控技术 是传感 系统的 体水平也在不断上升。数控技术结合 计算机 技 护 正常的生产过程 中 , 计算 机控制系统 ,自动停 术 、自动控制 、精密检测技术、网络通信技术 生产和传 输的信息 , 和信息处 理技术。利用其优势 , 提高整 体水平 的传统制造 业向更高水平发展 的领 先地位 , 在 激烈的市场环境使得机械制造行业在 中国。然 而, 发展数控 技术在整个 中国仍 然处 于初始阶 段 的探 索 , 在实际应用 中还需要 不断转型、发 展, 为 此全封 闭动 态模式控 制 , 论述 了数控 加 工 技术的发展 , 我们国家 的未来 动态 从许多方 叶片 加工 国际竞 争主要 是反 映在 汽轮机 止和反应 来保护 。
3 . I生 产 制 造 业
1 前 言
随着网络技术的迅速发展 , 广泛应用于工 业社 会的一 个重 要体 现是一 个组 合的机 械设 备, 提高 制造业和计 算机编程 , 所 以他们称为 数控加工 技术 , 已经被 广泛的关注和青 睐机械
自动化控制。
3 数 控 技 术 的 应 用领 域
实现不同的控制方法 。这样 的一个装置 的核心
是 一 个 特 殊 的 电脑 系 统 , 主要的程序 , 这 个 软
实现数控加工生产 线 , 实现生产 的 自动化和集 成处理。编程的优点为数控机床是 改变 加工设备 , 核心设备分析 和处理 后输出到驱动 电路 、实时控 制和操作 。主要设备的数控技术 是 以下几点 : ( 1 ) 机械设计和加工精度分析 。传 输设备和机械部件加工成 为大 多数数控机床 的 结构 , 以确保高速数控机 械制造和高精度的要 工程序的 案例 : 方法 的数控机床主要用于切割 和尝 试 , 减少设计错 误的机器零件 , 可以大大 工 、装配指令程序 可以实现输入 , 处理相应的 代码 , 编程加 工需 求 , 多 样化生 产 的要求 , 数
数控机床发展历史
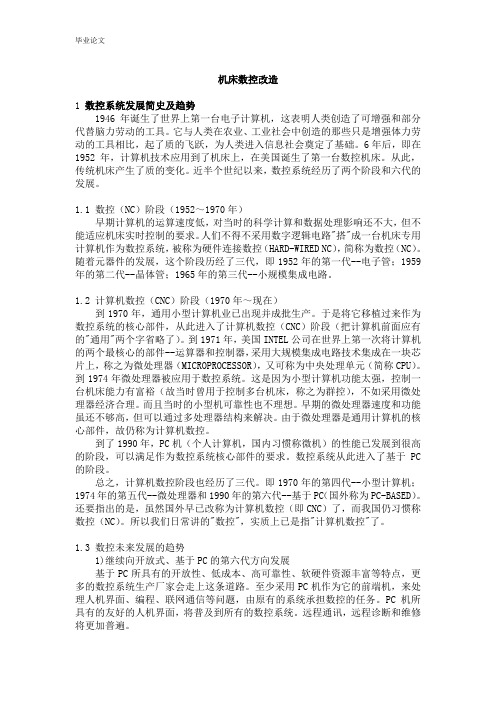
机床数控改造1 数控系统发展简史及趋势1946年诞生了世界上第一台电子计算机,这表明人类创造了可增强和部分代替脑力劳动的工具。
它与人类在农业、工业社会中创造的那些只是增强体力劳动的工具相比,起了质的飞跃,为人类进入信息社会奠定了基础。
6年后,即在1952年,计算机技术应用到了机床上,在美国诞生了第一台数控机床。
从此,传统机床产生了质的变化。
近半个世纪以来,数控系统经历了两个阶段和六代的发展。
1.1 数控(NC)阶段(1952~1970年)早期计算机的运算速度低,对当时的科学计算和数据处理影响还不大,但不能适应机床实时控制的要求。
人们不得不采用数字逻辑电路"搭"成一台机床专用计算机作为数控系统,被称为硬件连接数控(HARD-WIRED NC),简称为数控(NC)。
随着元器件的发展,这个阶段历经了三代,即1952年的第一代--电子管;1959年的第二代--晶体管;1965年的第三代--小规模集成电路。
1.2 计算机数控(CNC)阶段(1970年~现在)到1970年,通用小型计算机业已出现并成批生产。
于是将它移植过来作为数控系统的核心部件,从此进入了计算机数控(CNC)阶段(把计算机前面应有的"通用"两个字省略了)。
到1971年,美国INTEL公司在世界上第一次将计算机的两个最核心的部件--运算器和控制器,采用大规模集成电路技术集成在一块芯片上,称之为微处理器(MICROPROCESSOR),又可称为中央处理单元(简称CPU)。
到1974年微处理器被应用于数控系统。
这是因为小型计算机功能太强,控制一台机床能力有富裕(故当时曾用于控制多台机床,称之为群控),不如采用微处理器经济合理。
而且当时的小型机可靠性也不理想。
早期的微处理器速度和功能虽还不够高,但可以通过多处理器结构来解决。
由于微处理器是通用计算机的核心部件,故仍称为计算机数控。
到了1990年,PC机(个人计算机,国内习惯称微机)的性能已发展到很高的阶段,可以满足作为数控系统核心部件的要求。
数控技术的发展及国内外现状
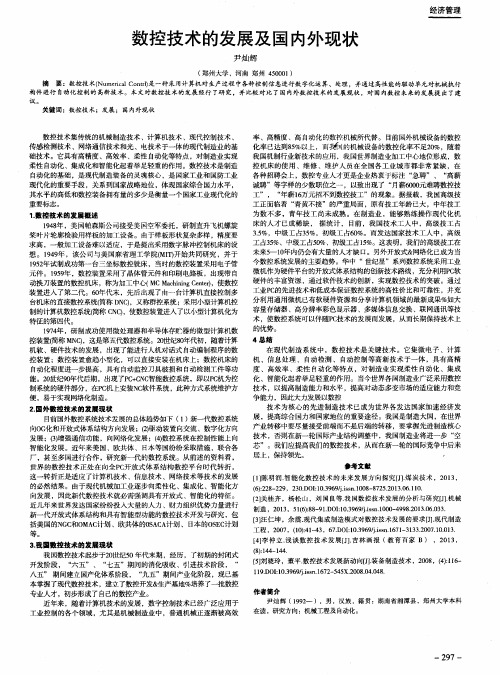
4总 结
Байду номын сангаас
1 9 4 8 年 ,美同帕森斯公 司接受 美国空军 委托 , 研制直升飞机螺旋 桨叶片轮廓检验用样板 的加工设备 。由于样板形状复杂 多样 ,精度要 求 高,一般加T设备难 以适应 ,于是提出采用数字 脉冲控制机床 的设 想 。1 9 4 9 年 ,该公司与美 国麻省理工学 院( M I T ) 开始共 同研 究 ,并于 1 9 5 2 年试制成功第一 台三坐标数控铣床 ,当时的数控装置采用 电子管 元 件。1 9 5 9 年 ,数控装置采用 了晶体管元件和印刷 电路板 ,出现带 自 动换刀装置的数控机床 , 称为加工中心( M C M a c h i n i n g C e n t e r ) , 使数控 装 置进入 了第二代 。6 0 年代末 ,先后 出现了南一 台计算机直接控制多 台机床的直接数控系统( 简称 D N C 1 ,又称群控系统 ;采用小型计算机控 制的计算机数控 系统( 简称 C N C ) ,使数控装置进入 了以小型计算机化为 特征的第 四代。 1 9 7 4 年 ,研制成功使用微处理器和半导体存贮 器的微 型计算机数 控装置( 简称 M N C 1 ,这是第五代数控系统。2 0 世纪8 O 年代初 ,随着计算 机软 、硬件技 术的发展 ,出现 了能进行人机对话 式 自动编制程序 的数 控装置 ;数控装 置愈趋小 型化 ,可 以直接安装在机床上 ;数控机床 的 自动化程度进一步提 高,具有 自 动监控刀具破损和 自动检测工件 等功 能。2 o t / t 纪9 0 年代后期 ,出现了P C + C N C 智能数控系统,即以P C 机为控 制系统 的硬件部分 , 在P c 机上安装N C 软件 系统 ,此种方式系统维护方 便, 易于实现网络化制造。