旋风除尘器设计方案.doc
旋风除尘器方案
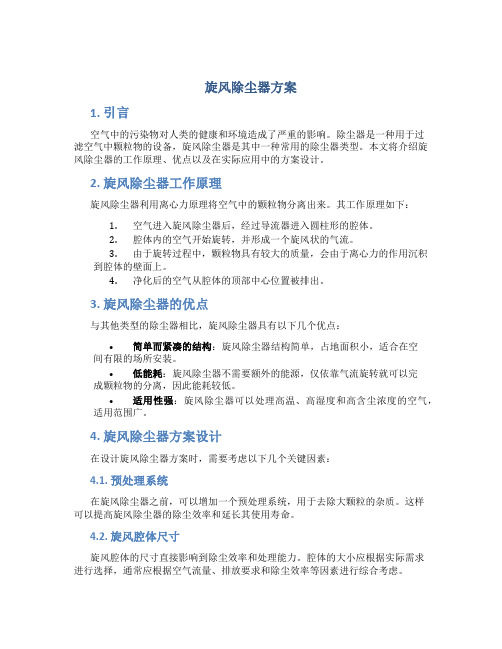
旋风除尘器方案1. 引言空气中的污染物对人类的健康和环境造成了严重的影响。
除尘器是一种用于过滤空气中颗粒物的设备,旋风除尘器是其中一种常用的除尘器类型。
本文将介绍旋风除尘器的工作原理、优点以及在实际应用中的方案设计。
2. 旋风除尘器工作原理旋风除尘器利用离心力原理将空气中的颗粒物分离出来。
其工作原理如下:1.空气进入旋风除尘器后,经过导流器进入圆柱形的腔体。
2.腔体内的空气开始旋转,并形成一个旋风状的气流。
3.由于旋转过程中,颗粒物具有较大的质量,会由于离心力的作用沉积到腔体的壁面上。
4.净化后的空气从腔体的顶部中心位置被排出。
3. 旋风除尘器的优点与其他类型的除尘器相比,旋风除尘器具有以下几个优点:•简单而紧凑的结构:旋风除尘器结构简单,占地面积小,适合在空间有限的场所安装。
•低能耗:旋风除尘器不需要额外的能源,仅依靠气流旋转就可以完成颗粒物的分离,因此能耗较低。
•适用性强:旋风除尘器可以处理高温、高湿度和高含尘浓度的空气,适用范围广。
4. 旋风除尘器方案设计在设计旋风除尘器方案时,需要考虑以下几个关键因素:4.1. 预处理系统在旋风除尘器之前,可以增加一个预处理系统,用于去除大颗粒的杂质。
这样可以提高旋风除尘器的除尘效率和延长其使用寿命。
4.2. 旋风腔体尺寸旋风腔体的尺寸直接影响到除尘效率和处理能力。
腔体的大小应根据实际需求进行选择,通常应根据空气流量、排放要求和除尘效率等因素进行综合考虑。
4.3. 腔体材料选择旋风腔体材料的选择应考虑其耐磨性和耐腐蚀性。
常见的材料有碳钢、不锈钢和橡胶内衬等,根据工作环境的特点选择合适的材料能够提高旋风除尘器的使用寿命。
4.4. 排放系统设计除尘后的空气需要进行排放处理,排放系统的设计需要考虑到处理量、净化效果和环保要求。
常见的排放系统包括直排和循环排放两种。
5. 结论旋风除尘器是一种简单、高效的除尘设备,能够有效分离空气中的颗粒物。
其简单而紧凑的结构、低能耗和广泛的适用性使其在各个行业得到了广泛应用。
旋风除尘器的设计资料
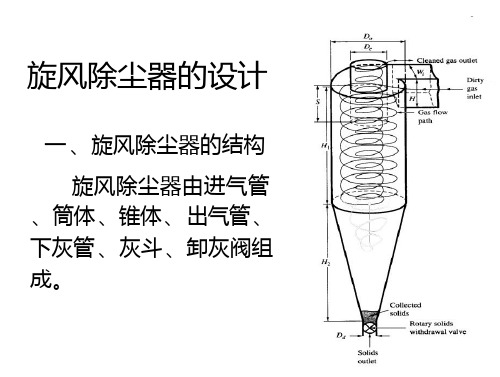
•有0一6 •锅炉,0. •理烟气0 =
m3/h,0排 •
2000:kg率/m度3T,180粒度8,分浓布度见5 表2体,性要质8求、效76粉率5>008005%尘密, 设9 计旋风
除尘=器。
9度91ρp = 99
2. 初定入口风速: 18m/s; 3. 确定入口断面积、进气管宽和高 :
A=Q/3600Vc ,=0.077m2 ,取尺寸比H/W=2.5 , A=HW, 所以H=0.42m , W=0. 18m
2)螺栓孔距确定
需满足JB/ZQ4248-86 。如螺栓直径为8mm ,孔距大于28mm 。对于旋风 除尘器法兰 , 总满足 。故可视法兰尺寸而定 ,见法兰设计图
3)孔径确定
采用通孔 。10~ 15mm
4)螺栓直径、长度及螺纹长度的确定(C级全螺纹) 考虑时间关系 ,不作受力分析 。螺栓直径视孔径而定 ,GB5277-85 。选
将分割径代入筛分理论效率公式 ,将所计算的 分级效率填入表中 。其总效率为
因ηT >85%,故满足设计要求。
八 、压力损失估算
压力损失取上限 ,旋风除尘器阻力近似为1300Pa。
九、结构设计
1.外形图的画法
1020 6 5
技术要求
7 壳体均采用6mm厚Q235-A钢板制作采取连续焊
接 ,器外表面刷铁红防锈底漆一遍 ,完全干后
A.蜗壳的画法
1)蜗壳出口断面 寸确定
出口风速:v =12 15m/s abv =Q ,取a =b;
a =(Q/v)1/2 =〔5000/(15×3600)〕 1/2 = 0.304~0.340 取a =b =320mm 2)确定偏心距 考虑焊接方便 ,蜗壳出口内壁距旋风出气管20mm, 于是中心线到出口蜗壳出口内壁距半径: r =230mm,
旋风除尘器的设计
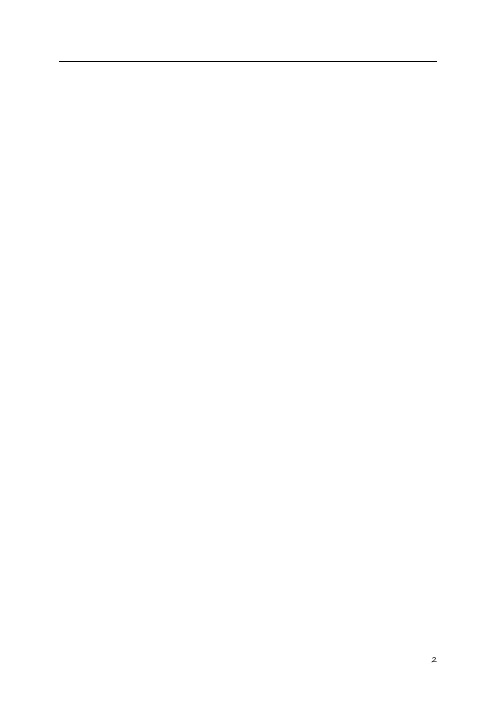
1.066 0.466 0.166 0.466 0.078 7.75 2.54 切线 矩形
2.3 旋风除尘器的参数计算
4
许多学者都致力于旋风除尘器的研究,通过各种假设,他们提出了许多不同的计算 方法。由于旋风除尘器内实际的气、尘两相流动非常复杂,因此根据某些假设条件得出 的理论公式目前还不能进行较精确的计算。
1.分割粒径(dc50) 计算旋风除尘器的分割粒径(dc50)是确定除尘器效率的基础。在计算时,因假设条 件和选用系数不同,计算分割粒径的公式也各不同。下面简要介绍一种计算方法,以说 明旋风除尘器的除尘原理。 处于外涡旋的尘粒在径向会受到两个力的作用: 惯性离心力
(2-3-1) 式中 vt——尘粒的切线速度,可以近似认为等于该点气流的切线速度,m/s;
2
二.说明书
2.1 图形设计:
旋风除尘器图
(图 1)
2.2 设计数据: 表 1 旋风除尘径 r 粉尘出口管半径 r 出口管到底部高 h
数据 0.4 0.2 0.2 2.07
3
园部高 h 气体出口管长度 l 入口管宽度 b 入口管高度 h 入口管面积 A 锥角
3.1 旋风除尘器的原理
旋风除尘器是利用旋转气流所产生的离心力将尘粒从合尘气流中分离出来的除尘 装置。它具有结构简单,体积较小,不需特殊的附属设备,造价较低.阻力中等,器 内无运动部件,操作维修方便等优点。旋风除尘器一般用于捕集 5-15 微米以上的颗 粒.除尘效率可达 80%以上,近年来经改进后的特制旋风除尘器.其除尘效率可达 5% 以上。旋风除尘器的缺点是捕集微粒小于 5 微米的效率不高. 旋风除尘器内气流与尘粒的运动概况: 旋转气流的绝大部分沿器壁自圆简体,呈螺旋状由上向下向圆锥体底部运动,形成下 降的外旋含尘气流,在强烈旋转过程中所产生的离心力将密度远远大于气体的尘粒甩 向器壁,尘粒一旦与器壁接触,便失去惯性力而靠入口速度的动量和自身的重力沿壁 面下落进入集灰斗。旋转下降的气流在到达圆锥体底部后.沿除尘器的轴心部位转而 向上.形成上升的内旋气流,并由除尘器的排气管排出。 自进气口流人的另一小部分气流,则向旋风除尘器顶盖处流动,然后沿排气管外侧向 下流动,当达到排气管下端时,即反转向上随上升的中心气流一同从诽气管排出,分 散在其中的尘粒也随同被带走。
旋风除尘设计方案
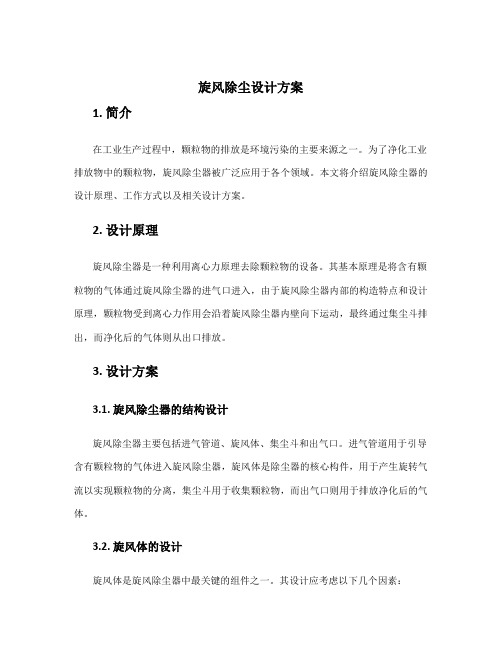
旋风除尘设计方案1. 简介在工业生产过程中,颗粒物的排放是环境污染的主要来源之一。
为了净化工业排放物中的颗粒物,旋风除尘器被广泛应用于各个领域。
本文将介绍旋风除尘器的设计原理、工作方式以及相关设计方案。
2. 设计原理旋风除尘器是一种利用离心力原理去除颗粒物的设备。
其基本原理是将含有颗粒物的气体通过旋风除尘器的进气口进入,由于旋风除尘器内部的构造特点和设计原理,颗粒物受到离心力作用会沿着旋风除尘器内壁向下运动,最终通过集尘斗排出,而净化后的气体则从出口排放。
3. 设计方案3.1. 旋风除尘器的结构设计旋风除尘器主要包括进气管道、旋风体、集尘斗和出气口。
进气管道用于引导含有颗粒物的气体进入旋风除尘器,旋风体是除尘器的核心构件,用于产生旋转气流以实现颗粒物的分离,集尘斗用于收集颗粒物,而出气口则用于排放净化后的气体。
3.2. 旋风体的设计旋风体是旋风除尘器中最关键的组件之一。
其设计应考虑以下几个因素:•直径:旋风体的直径决定了旋风除尘器的处理能力。
较大的直径可以处理更大量的气体,但也需要更大的空间。
•高度:旋风体的高度影响颗粒物的分离效果。
较高的旋风体可以提高颗粒物的分离效率。
•锥角:旋风体的锥角决定了颗粒物的分离效果。
较小的锥角可以提高分离效率,但同时增加阻力。
•入口形状:入口形状的设计应考虑颗粒物的流动性,以确保颗粒物能够顺利进入旋风体。
3.3. 集尘斗的设计集尘斗是用于收集被除尘的颗粒物,其设计应考虑以下几个因素:•斗形:集尘斗的斗形应尽可能兼顾容积和流动性,以确保颗粒物能够顺利流动到出料口。
•出料口:集尘斗的出料口设计应考虑颗粒物的排出方式,可以选择手动清理或自动排出。
•材料选择:集尘斗的材料应选用耐磨损和耐腐蚀的材料,以提高设备的使用寿命。
4. 工作方式旋风除尘器的工作方式可以分为以下几个步骤:1.气体进入旋风除尘器的进气口,并通过进气管道进入旋风体。
2.在旋风体内,气体产生旋转气流,颗粒物受到离心力作用沿着旋风除尘器内壁向下运动。
【设计计算】旋风除尘器
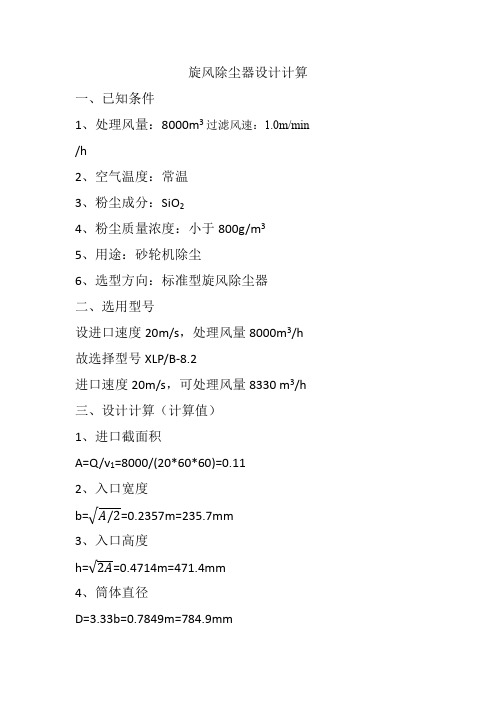
旋风除尘器设计计算一、已知条件1、处理风量:8000m3过滤风速:1.0m/min /h2、空气温度:常温3、粉尘成分:SiO24、粉尘质量浓度:小于800g/m35、用途:砂轮机除尘6、选型方向:标准型旋风除尘器二、选用型号设进口速度20m/s,处理风量8000m3/h 故选择型号XLP/B-8.2进口速度20m/s,可处理风量8330 m3/h三、设计计算(计算值)1、进口截面积A=Q/v1=8000/(20*60*60)=0.112、入口宽度b=√A/2=0.2357m=235.7mm3、入口高度h=√4、筒体直径D=3.33b=0.7849m=784.9mm5、排出管直径d e=0.6D=470.94mm6、筒体长度L=1.7D=1334.33mm7、椎体长度H=2.3D=1805.27mm8、排灰口直径d1=0.43D=337.507mm9、排气管插入深度s=h=471.4mm四、设计计算(选用型号XLP/B-8.2)根据“三、设计计算”选用型号XLP/B-8.2D=820mm压力损失ξρv12=1150(根据《大气污染控制工程》参考得出)Δρ=12ξρv12=1150反算,设计参数如下:根据D=820mm;Δρ=121、进口截面积v1≦18.29取v1=18m/sA=Q/v1 =0.123’2、入口宽度b=D/3.33=246.25mm3、入口高度h=A/b =499.49mm取h=500mm3、筒体直径D=3.33b=820mm4、排出管直径d e=0.6D=492mm5、筒体长度L=1.7D=1394mm6、椎体长度H=2.3D=1886mm7、排灰口直径d1=0.43D=352.6mm8、排气管插入深度要求s>h;这里取s=600mms=600mm>h=500mm10、取v=18m/s时的压力损失标况下ρ1=1.293kg/m3换算得常温下ρ2=1.185kg/m3这里取ξ=5.8Δρ1=1ξρv12=1113.43Pa<1450Pa211、椎体角度θ=7°。
回转窑石膏粉尘旋风除尘器工艺设计

回转窑石膏粉尘旋风除尘器工艺设计首先,设备选型是工艺设计的基础。
石膏粉尘旋风除尘器主要由旋风筒、进气口、出气口、排灰口、旋风锥等组成。
根据生产工艺要求和现场环境条件,选择合适的设备型号和规格,确保除尘设备能够满足粉尘净化效果和处理能力的要求。
其次,系统配置是工艺设计的重要环节。
石膏生产过程中的粉尘除尘系统通常包括进风系统、旋风分离系统、灰尘输送系统和排气系统等,需要根据生产工艺要求和现场条件进行合理配置。
进风系统要确保稳定的进风量和均匀的进风分布,旋风分离系统要选择适当的旋风筒结构和旋风锥设计,灰尘输送系统要考虑到粉尘的输送距离和输送方式,排气系统要设计合理的排气阻力和排气流速。
再次,运行参数是工艺设计的关键因素。
石膏粉尘旋风除尘器的运行参数包括进风速度、旋风筒内径、旋风筒长度、旋风锥角度等。
这些参数的选取要考虑到生产工艺要求、粉尘特性和设备性能等多方面因素。
进风速度要控制在合适的范围内,旋风筒内径和长度要根据处理能力和除尘效果进行合理的选择,旋风锥角度要满足旋风分离的要求。
最后,工艺设计还需考虑到安全性和环保性。
在石膏粉尘除尘系统中,需要考虑设备的操作安全和人员防护措施,避免因操作不当而引发事故。
同时,工艺设计还要合理利用资源,减少能耗和粉尘排放,确保环境保护的要求。
在进行回转窑石膏粉尘旋风除尘器工艺设计时,需要充分考虑以上各个方面的因素,并结合具体的生产工艺要求和现场环境条件进行合理的设计。
通过科学的工艺设计,可以提高石膏粉尘的净化效果和除尘设备的性能,实现资源的合理利用和环境的保护。
旋风除尘设计方案
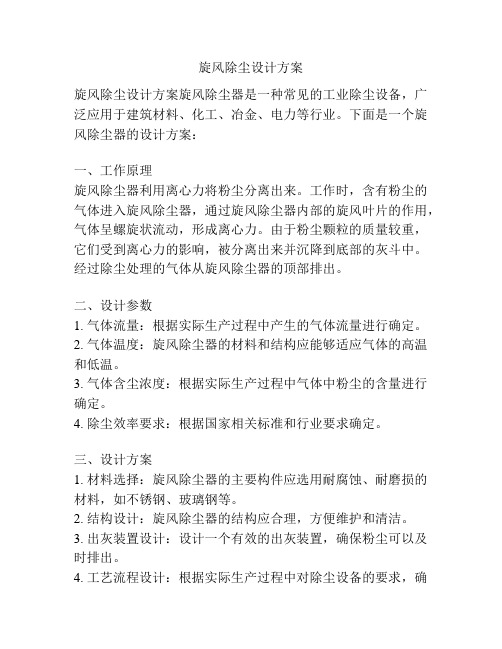
旋风除尘设计方案旋风除尘设计方案旋风除尘器是一种常见的工业除尘设备,广泛应用于建筑材料、化工、冶金、电力等行业。
下面是一个旋风除尘器的设计方案:一、工作原理旋风除尘器利用离心力将粉尘分离出来。
工作时,含有粉尘的气体进入旋风除尘器,通过旋风除尘器内部的旋风叶片的作用,气体呈螺旋状流动,形成离心力。
由于粉尘颗粒的质量较重,它们受到离心力的影响,被分离出来并沉降到底部的灰斗中。
经过除尘处理的气体从旋风除尘器的顶部排出。
二、设计参数1. 气体流量:根据实际生产过程中产生的气体流量进行确定。
2. 气体温度:旋风除尘器的材料和结构应能够适应气体的高温和低温。
3. 气体含尘浓度:根据实际生产过程中气体中粉尘的含量进行确定。
4. 除尘效率要求:根据国家相关标准和行业要求确定。
三、设计方案1. 材料选择:旋风除尘器的主要构件应选用耐腐蚀、耐磨损的材料,如不锈钢、玻璃钢等。
2. 结构设计:旋风除尘器的结构应合理,方便维护和清洁。
3. 出灰装置设计:设计一个有效的出灰装置,确保粉尘可以及时排出。
4. 工艺流程设计:根据实际生产过程中对除尘设备的要求,确定旋风除尘器的位置、排气管道等。
四、设备运行维护1. 启动前检查旋风除尘器的各个部件是否完好,如有损坏及时更换。
2. 定期清理除尘器内部的粉尘,避免积灰影响除尘效果。
3. 定期检查旋风除尘器的运行情况,如有异常及时处理。
4. 注意旋风除尘器的安全问题,防止因设备故障引发火灾等事故。
通过合理设计和有效运行维护,旋风除尘器可以有效地将生产过程中产生的粉尘除去,提高了生产环境的清洁度,保护了工作人员的身体健康。
旋风除尘器设计详解
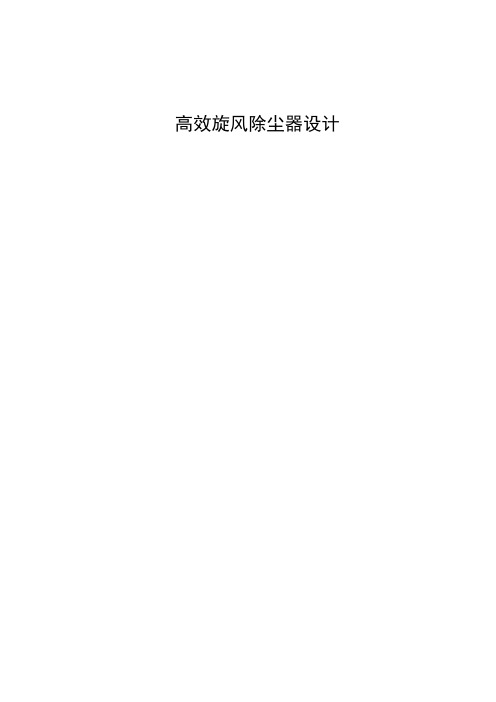
高效旋风除尘器设计摘要00论文主要介绍了旋风除尘器各部分结构尺寸的确定以及旋风除尘器性能的计算。
以普通旋风除尘器设计为基础,结合现代此类相关课题的研究方法,设计出符合一定压力损失和除尘效率要求的除尘器,在CAD/CAM软件辅助设计的基础上,绘制旋风除尘器装配图、零件图、以及除尘系统原理图。
本文分以下几部分对以上内容进行了讨论:首先,通过查阅资料计算出旋风除尘器各部分尺寸;其次,绘制出旋风除尘器装配图及旋风除尘器各零部件图;最后,整理资料,选取与论文相关的英文文献进行翻译完成设计说明书。
关键词:旋风除尘器压力损失除尘效率目录1.引言 (1)2.旋风除尘器的除尘机理及性能 (2)2.1旋风除尘器的基本工作原理 (2)2.1.1旋风除尘器的结构 (2)2.1.2旋风除尘器内的流场 (2)2.1.3旋风除尘器内的压力分布 (5)2.2 旋风除尘器的性能及其影响因素 (5)2.2.1旋风除尘器的技术性能 (5)2.2.2 影响旋风除尘器性能的主要因素 (6)2.2.3 旋风除尘器选型原则 (10)3.旋风除尘器的设计 (12)3.1旋风除尘器各部分尺寸的确定 (12)3.1.1形式的选择 (12)3.1.2 确定进口风速 (12)3.1.3 确定旋风除尘器的尺寸 (12)3.2旋风除尘器强度的校核 (14)3.2.1筒体和锥体壁厚s和气压试验强度校核 (14)3.2.2排气管尺寸的确定 (15)3.2.3.支座的选择计算 (17)3.2.4支腿的设计计算及校核 (19)3.3旋风除尘器压力损失及除尘效率 (20)3.3.1计算压力损失 (20)3.3.2除尘效率的计算 (21)3.4风机的选择 (22)3.5排尘阀的选择 (22)3.6连接方式的选择 (22)结论 (24)致谢 (25)参考文献 (26)外文资料 (27)1.引言旋风除尘器设计是我通过学习全部基础课、专业课和以往的课程设计的基础上进行的一次综合性的设计。
- 1、下载文档前请自行甄别文档内容的完整性,平台不提供额外的编辑、内容补充、找答案等附加服务。
- 2、"仅部分预览"的文档,不可在线预览部分如存在完整性等问题,可反馈申请退款(可完整预览的文档不适用该条件!)。
- 3、如文档侵犯您的权益,请联系客服反馈,我们会尽快为您处理(人工客服工作时间:9:00-18:30)。
设计原始资料:锅炉型号:DLP2-13即,单锅筒纵置式抛煤机炉,蒸发量2t/h,出口蒸汽压力13MPa设计耗煤量: 360kg/h( 按学号增加 5)Y Y Y Y Y Y Y设计煤成分: C=60.5% H =3% O=4% N =1% S =1.5% A =18% W=12%; V Y= 15%;属于中硫烟煤排烟温度: 165℃空气过剩系数= 1.4飞灰率= 21%烟气在锅炉出口前阻力650Pa污染物排放按照锅炉大气污染物排放标准中 2 类区新建排污项目执行。
连接锅炉、净化设备及烟囱等净化系统的管道假设长度50m,90°弯头 10 个。
1.燃烧计算1.1实际耗空气量的计算在标准状况下,以1Kg应用煤为基准进行计算,结果见表1-1 。
1Kg 该煤完全燃烧时所需要标准状况下的氧气的体积V o为:V o=(50.4+7.5+0.47-1.25)× 22.4=1279.448 L(1-1)假设空气中氮氧的摩尔数之比为N/O=3.78,则 1Kg 低硫煤完全燃烧时所需要的空气体积 V k为:V k =( 1+3.78 )× 1279.448=6115.953 L (1-2 )实际消耗的空气体积V k为:V k=1.4 V k=1.4×6115.953=8562.333 L ( 1-3 )表 1-1 1Kg应用煤的相关计算质量摩尔数燃烧耗氧量生成气体量生成气体体积成分( g)(mol )(mol )( mol)( L )C 605 50.4 50.4 50.4 1128.96H 30 15 7.5 15 336O40 1.25————28N100.36——0.367.84S 15 0.47 0.47 0.47 10.528水分120 6.67————149.408 灰分180————————1.2产生烟气量的计算1Kg 该煤完全燃烧后生成的烟气量V y =149.408+10.528+7.84+336+1128.96+8562.333=10195.069 L =10.195 m3 ( 1-4 )则,在 160℃时的实际烟气体积为V y为:V y=10.195×(160+273.15)=16.17 m3 ( 1-5 )273.15该锅炉一小时产生的烟气流量Q 为:Q =16.17×360=5821.2m3/h=1.617 m3/s(1-6)1.3灰分浓度及二氧化硫浓度的计算烟气中灰分的质量M h为:M h =180× 21%=37.8g=37800mg (1-7 )烟气中灰分的浓度h 为:h =37800/16.17=2337.662mg/ m3 ( 1-8 )烟气中 SO2质量 M S为:M S =0.47 ×64=30.08g=30080mg ( 1-9 )烟气中 SO2的浓度s 为:s =30080/16.17=1860.235mg/ m3 (1-10 )2.净化方案设计及运行参数选择本设计中采用旋风除尘设备进行净化处理。
2.1旋风除尘器的工作原理旋风除尘器一般有带有一锥形的外圆筒,进气管,排气管,圆锥观和贮灰箱的排气阀组成。
当含尘气流以一定的速度(一般在14~ 25m/s 之间,最大不超过35m/s)由进气管进入旋风除尘器后,气流由直线运动变为圆周运动。
由于受到外圆筒上盖及圆筒壁的限流,迫使气流作自上而下的旋转运动。
旋转过程中产生较大的离心力,尘粒在离心力的作用下,被甩向外筒壁,失去惯性后在重力的作用下,落入贮灰箱中,与气体分离。
而旋转下降的气流到达锥体时,因锥体收缩的影响,而向除尘器中心汇集,根据“旋转矩”不变理论,其切向速度不断升高,气流下降到一定程度时,开始方向上升,经排气管排出[1]。
2.2旋风除尘器的特点现在的旋风除尘器具有结构简单;应用广泛;分离效率高可以有效地清除微粒;处理气体量大且阻力低;适用于高温和腐蚀性气体;运行费用低;应用广泛等优点[2] 。
2.3运行参数的选择与设计根据相关资料及实际运行情况,本设计中烟气的入口速度取为v020m / s 。
根据国家相关规定及标准确灰分风的最高允许排放浓度为200mg / m 3 [3] 。
则本设中要求达到的除尘效率为:2337.662 200 100% 91.45% (2-1)2337.6622.4净化效率的影响因素2.4.1 旋风除尘器结构尺寸对净化效率的影响在旋风除尘器结构尺寸中主要的影响因素有:除尘器的外筒直径,高度,气体进口和排气管形状和大小。
这些部件一般都有一较适宜的尺寸及组合。
过大或过小都会降低设备效率。
2.4.2操作条件对旋风除尘器性能的影响操作条件应控制在一个较适宜的范围内,过大会降低设备效率,过小会增加阻力损失,两种情况均不利于设备的高效运转。
3.设备结构设计与计算3.1进气口设计计算根据已有经验及实际运行已确定本设计中烟气的入口速度为:v020m / s 。
考虑设备漏风及安全运行等因素,假定实际进入设备的烟气量为 1.2Q。
则进气口部分的面积s r 为:s r = 1.2Q=1.2×1.617/20=0.097 m2 (3-1) v0现有旋风除尘器的进口有三类:直入切向进入式,蜗壳切向进入式,轴向进入反转式(见图 3-1 )。
直入切向进入式蜗壳切向进入式轴向进入反转式图 3-1现有的几类进气管本设计中采用蜗壳切向进入式,它可减少进口系统对筒体内气流的撞击和干扰,其处理量大,压力损失小。
其尺寸一般为高(a) 宽 (b) 之比 a / b 在2~3之间。
本设计中取 a / b 2 。
则进口的宽度 b 为:b 220mm (3-2)进口高 a 为:0.0970.4409m 441mm (3-3)a0.22则实际的高宽比:a /b 441/ 220 2.005 (在2~3之间) ( 3-4 )实际进口面积 s r为:s0.441 0.22 0.097m 2(3-5)5实际的入口速度 v 0 为:1.2Q 1.2 1.617 m / s ( 3-6 )v 00.09720s r3.2 旋风除尘器外筒直径的设计计算一般旋风除尘器, 其进口高 a ,宽 b 分别为旋风除尘器外筒直径 D 0 的 0.4 ~0.75 倍和 0.2 ~ 0.25 倍。
本设计中假定宽为外筒直径的 0.25 倍,则高应为 0.501 倍,则旋风除尘器的外筒直径 D 0 为:D 00.22 0.88m( 3-7 )0.253.3 旋风除尘器高度的设计计算性能较好的旋风除尘器,其直筒部分高度一般为其外筒直径的1~2 倍,锥体部分高度为外筒直径的 1~ 3 倍,锥部底角在 20°~ 40°之间。
本设计中直筒部分高度 H 1 ,锥体部分高度 H 2 ,分别取为旋风除尘器外筒直径的 1.4 倍及 2 倍。
则:H 1 1.4 0.88 1.232m(3-8)H 2 2 0.88 1.76m(3-9)旋风除尘器的总高度 H 为:HH 1 H 2 1.2321.762.992m(3-10)3.4 旋风除尘器排气管的设计计算现有的排气管有两类:底部收缩式和直管式(见图3-2 )。
直管式底部收缩式图 3-2排气管的类型无论哪一类排气管,其管径一般取为旋风除尘器外筒直径的0.3 ~0.5 倍。
本设计采用直管式,其管径D1取为 0.4D0,则排气管管径:D10.4 0.88 325mm(3-11)排气管插入旋风除尘器外筒内深度一般与进气管下缘平齐或稍低。
本设计中为避免气体短路,伸入长度H 3取为500mm。
即 H 3500mm。
3.5排灰管的设计计算及卸灰装置的选择旋风除尘器的排灰管直径 D 2一般取为外筒直径的0.25倍,即D2 0.25D0 0.25 0.88 220mm。
结合实际取为220mm。
实际 D2 0.25D0。
底部锥角为:1050 220(在20 °~40 °之间)2 arctan 26.52 1760(3-12)卸灰装置兼有卸灰和密封两种功能,是影响除尘器的关键部件之一。
若有漏风现象,不但影响正常排灰,而且严重影响除尘器效率。
现有的卸灰装置有两类:二级翻板式和回转式(见图 3-3 )。
本设计采用二级翻板式。
二级翻板式回转式图 3-3现有的两类卸灰装置3.6流体阻力计算旋风除尘器内的压力损失一般可按下式计算:u i 2 (3-14)p2式中:——烟气密度,约为0.748Kg / m3;u i——除尘器内含尘气体的流速,m / s ;——流体阻力系数,无量纲;其中16 A(3-15) d e 2式中: A ——旋风除尘器的进口截面积,m2;d e——排气管直径, m带入相关值,得16 0.09714.69 (3-16)0.3252所以,202 0.7482198.15 pa (在500pa~1500pa之间)p 14.69 24.烟囱的设计计算由于烟囱有一定的高度,烟囱中的热气体受到大气浮力的作用,而具有一定的几何压头,在烟囱底部造成负压—“抽力”。
如果这种抽力正好能克服气体在窑炉中流动的各种阻力,就能使窑内热气体能源源不断地流入烟囱底部,并通过烟囱排入大气。
4.1烟囱直径的计算烟囱内烟气的流速选为12m / s,则直径可用下式计算:4 1.2 Q)d ( 4-13600 v0式中: Q ——烟气流量, m3 / h ;v0——烟气流速,m / s;1.2 ——修正系数。
所以烟囱的直径为:4 1.2 5821.2( 4-2 )d 454mm3600 12取为 455mm ,则实际烟气流速为:v011.99m / s4.2烟囱高度的设计计算本设计中,参照国家标准,确定烟囱高度为H S50m ,则烟气抬升高度为:Q H 0.35 paQ vT( 4-3 )T s式中: Q H——烟气的热释放功率,Kw ;T s——地区环境温度,KQ v——烟气释放速率,m3 / s ;pa ——大气压强, pa ;T —— 温差, K代入相关值得:165 20 Q H 0.35 900 1.56162.68Kw165 273由于 Q H 162.68Kw <1700 Kw ,所以:H2 (1.5v 0 d 0.01Q H ) / u 8.17m所以烟囱的总高度 H 为:H H s H 58.17m ( 4-4 )4.3 烟囱阻力损失计算烟囱亦采用钢管,其阻力可按下式计算:l v 2p m( 4-5 )d 2式中: ——摩擦阻力系数,无量纲;v ——管内烟气平均流速, m / s ;——烟气密度, Kg / m 3 ;l ——管道长度, m ;d ——管道直径, m已知钢管的摩擦系数为 0.02 ,所以烟囱的阻力损失为:P m 118.17pa则地面最大浓度为:max200 2 1.6170.6 0.005595mg / m 3 0.5mg / m 33.14 2.4 58.172 2.72可见地面最大浓度小于国家规定,烟囱高度设计合理。