铝合金应力腐蚀开裂ASTM G139(中文翻译版)
铝合金型材性能

第二节铝合金材料铝合金材料是幕墙工程大量使用的材料,幕墙金属杆件以铝合金建筑型材为主(占95%以上)。
幕墙面板也大量使用单层铝板、铝塑复合板等。
一.牌号与状态GB/T16474—1996《变形铝及铝合金牌号表示方法》规定了变形铝及铝合金的牌号表示方法。
这个标准是根据变形铝及铝合金国际牌号注册协议组织推荐的国际四位数字体系牌号命名方法制定的,这是国际上比较通用的牌号命名方法。
这个标准包括国际四位数字体系牌号和四位字符体系牌号两种牌号的命名方法。
按化学成份,已在国际牌号注册组织命名的铝及铝合金,直接采用国际四位数字体系牌号,国际牌号注册组织未命名的铝及铝合金,则按四位字符体系牌号命名。
牌号的第一位数字表示铝及铝合金的组别,如表2-14所示。
基础状态代号用一个英文大写字母表示。
基础状态分为五种,如表2-15所示。
细分状态代号采用基础状态代号后跟一位或多位阿拉伯数字表示。
1.H的细分状态在字母H后面添加两位阿拉伯数字(称作H××状态)表示H的细分状态。
A.H后面的第一位数字表示获得该状态的基本处理程序,如下所示:H1—单纯加工硬化状态。
适用于未经附加热处理,只经加工硬化即获得所需强度的状态。
H2—加工硬化及不完全退火的状态。
适用于加工硬化程度超过成品规定要求后,经不完全退火,使强度降低到规定指标的产品。
对于室温下自然时效软化的合金,H2与对应的H3具有相同的最小极限抗拉强度值;对于其它合金,H2与对应的H1具有相同的最小极限抗拉强度值,但延伸率比H1稍高。
H3—加工硬化及稳定化处理的状态。
适用于加工硬化后经低温热处理或由于加工过程中的受热作用致使其化学性能达到稳定状态的产品。
H3状态仅适用于在室温下逐渐时效软化(除非经稳定化处理)的合金。
H4—加工硬化及涂漆处理的状态。
适用于加工硬化后,经涂漆处理导致了不完全退火的产品。
B.H后面的第2位数字表示产品的加工硬化程度。
数字8表示硬状态。
API SPEC 5CT-2012译文(第九版)
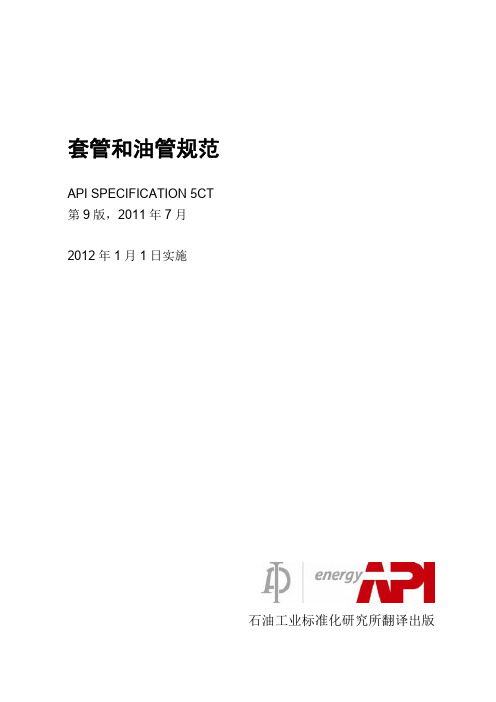
方伟 秦长毅 夏咏华 赵淑兰
主 编:高圣平 副主编:杜德林
本标准由石油工业标准化研究所组织翻译、出版和发行。 本标准翻译单位:中国石油集团石油管工程技术研究院。 本标准翻译责任人:方 伟、徐 婷 本标准一校责任人:秦长毅 本标准二校责任人:许晓锋 本标准三校责任人:方 伟
本标准译文难免有不妥之处,欢迎各位读者批评指正。
AUTHORIZED BY API
This standard has been translated by Petroleum Standardization Research Institute (PSRI) with the permission of the American Petroleum Institute (API). This translated version shall not replace nor supersede the English language version which பைடு நூலகம்emains the official version. API shall not be responsible for any errors, discrepancies or misinterpretations arising from this translation. No additional translation or reproduction may be made of the standard without the prior written consent of API.
API 授权声明
本标准由美国石油学会(API)授权许可,由石油工业标准化研究所 (PSRI)组织翻译。翻译版本不代替、不取代英文版本,英文版本仍为 具备法律效力的版本。API 对翻译工作中出现的错误、偏差、误解均不承 担任何责任。在未经 API 书面许可的情况下,不得将翻译版本进行再翻 译或复制。
ASTM E139 金属材料传导蠕变、蠕变断裂和应力断裂的标准试 验方法DOC

金属材料传导蠕变、蠕变断裂和应力断裂的标准试验方法1、适用范围1.1、本标准适用于在恒定温度和恒定拉伸载荷下,测量材料由时间函数决定的变形量(蠕变试验)和加载后的断裂时间(断裂试验)。
同时还规定了对试验设备的基本要求。
需要参考产品的规范,来确定试验的数量和最长试验时间。
1.2、本标准列出了各试验报告中必须包括的内容。
这是为了确保相关感兴趣的组织都能获得这些有用且容易获得的信息。
由于以下原因,报告必须认真对待:(1)采用不同的试验方法获得的试验结果并不相同,因此必须具体说明使用了那种试验方法;(2)实验报告中缺少详细信息往往会妨碍后续研究中重要试验变量的确定;(3)由于持久试验的时间很长,一般很少重复试验,并且很难保证一些变量始终保持在推荐范围以内。
一份详细的报告,并不需要包括所有不在控制精度范围内的试验数据1.3、本标准不包括缺口试样的试验,这些试验在E292中有详细规定1.4、本标准不包括短时试验,短时试验在E21中有详细规定。
1.5、本标准中所有单位都采用国际单位。
1.6、本标准不对所有的安全问题负责,使用本标准的用户有责任建立必要的安全保障并根据需要,对标准的适用范围限制进行调整。
2、引用标准2.1、ASTM标准:E4测试仪的负荷校准E6机械试验方法的有关术语E8金属材料的拉伸试验方法E21金属材料的高温抗拉试验方法E29使用试验数据中重要数字以确定对规范的适应性E74检验试验机力示值用测力仪的校准E83伸长仪的检验和分类E177ASTM试验方法中精密度和偏倚术语的使用E220用比较技术校准热电偶的标准试验方法E292材料断裂时间的凹口张力试验E633空气中1800°F(1000°C)作蠕变和应力断裂试验使用热电偶的规则E1012在拉伸负载下试样调直的验证2.2、军事标准MIL-STD-120量规检验3、术语3.1、定义:E6部分的术语与蠕变试验相关的术语的定义应该适用于实践。
ASTM G139-05用断裂负荷法测定热处理铝合金制品抗应力腐蚀开裂性的标准试验方法(中文翻译版)

ASTM G139-05(R2011)ASTM G139-05(R2015)最新用断裂负荷法测定热处理铝合金制品抗应力腐蚀开裂性的标准试验方法(中文翻译版)1本试验方法由ASTM金属腐蚀委员会G01管辖,并由环境辅助开裂小组委员会G01.06直接负责。
当前版本于2011年9月1日批准。
2011年9月出版。
最初于2005年批准。
上一版于2005年批准为G139-05。
DOI: 10.1520/G0139-05R11。
本标准以固定名称G139发布;紧跟在名称后面的数字表示最初采用的年份,如果是修订,则表示最后修订的年份。
括号中的数字表示上次重新批准的年份。
上标(ε)表示自上次修订或重新批准以来的编辑性更改。
1、范围1.1本试验方法涵盖了通过断裂荷载试验方法评估抗应力腐蚀开裂(SCC)性的程序,该方法使用剩余强度作为损伤演化(在这种情况下为环境辅助开裂)的测量方法。
1.2本试验方法包括试样类型和复制、试验环境、应力水平、暴露时间、最终强度测定和原始残余强度数据的统计分析。
1.3本试验方法适用于热处理铝合金,即2XXX合金和7XXX,含1.2%至3.0%铜,且试样的取向与晶粒结构(1,2)2相关,横向较短。
然而,用于分析数据的残余强度测量和统计数据并非针对可热处理铝合金,可用于其他试样取向和不同类型的材料。
2括号中的黑体数字是指本标准末尾的参考文献列表。
1.4本标准并非旨在解决与其使用相关的所有安全问题(如有)。
本标准的使用者有责任在使用前建立适当的安全和健康实践,并确定法规限制的适用性。
2、参考文件2.1 ASTM标准:33有关参考的ASTM标准,请访问ASTM网站,或通过Service@联系ASTM客户服务。
有关ASTM标准年鉴卷信息,请参阅ASTM网站上的标准文件摘要页。
E8金属材料拉伸试验的试验方法E691进行实验室间研究以确定试验方法精度的实施规程G44在中性3.5%氯化钠溶液中交替浸入金属和合金的暴露规程G47测定2XXX和7XXX铝合金产品应力腐蚀开裂敏感性的试验方法G49直接拉伸应力腐蚀试样的制备和使用规程G64热处理铝合金抗应力腐蚀开裂分类3、术语3.1本标准专用术语定义:3.1.1审查—一个统计术语,表明由于试验程序或条件的原因,单个观察值可能超出可测量的范围。
应力腐蚀开裂临界应力强度因子

应力腐蚀开裂临界应力强度因子
应力腐蚀开裂(Stress Corrosion Cracking,SCC)是一种金属在受到应力和特定介质(如水、气体、化学物质等)共同作用下发生的腐蚀和开裂现象。
而临界应力强度因子(Critical Stress Intensity Factor)是指在材料开始出现裂纹扩展的临界点上所受到的应力强度。
在研究应力腐蚀开裂时,需要考虑多种因素。
首先是材料的特性,包括化学成分、晶粒结构、热处理状态等。
其次是环境因素,如介质的PH值、温度、压力等。
还有作用在材料上的应力,可以是外部加载的应力,也可以是由材料自身的残余应力引起的。
这些因素共同作用下,会导致材料在特定条件下发生应力腐蚀开裂。
临界应力强度因子是评价材料抗应力腐蚀开裂能力的重要参数之一。
它反映了材料在特定环境中抵抗裂纹扩展的能力,是用来描述材料在应力腐蚀作用下抗裂纹扩展的能力的参数之一。
临界应力强度因子的大小与材料的性能密切相关,对于不同的材料和不同的环境条件,临界应力强度因子也会有所不同。
研究人员通常会通过实验和数值模拟的方法来确定材料在特定
条件下的临界应力强度因子。
这些数据对于工程实践具有重要意义,可以帮助工程师们选择合适的材料和设计合理的工程结构,以减少
或避免应力腐蚀开裂的发生。
总之,了解应力腐蚀开裂的临界应力强度因子对于材料科学和
工程实践都具有重要意义,它涉及材料的特性、环境因素和应力状
态等多个方面,需要综合考虑和研究。
1-5应力腐蚀开裂
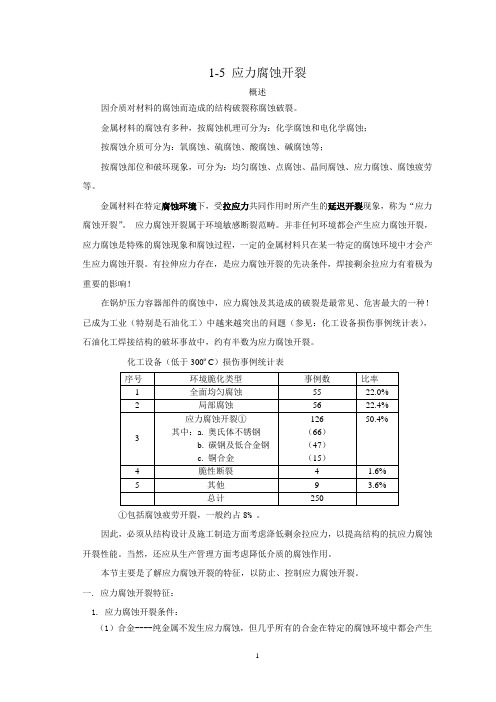
1-5 应力腐蚀开裂概述因介质对材料的腐蚀而造成的结构破裂称腐蚀破裂。
金属材料的腐蚀有多种,按腐蚀机理可分为:化学腐蚀和电化学腐蚀;按腐蚀介质可分为:氧腐蚀、硫腐蚀、酸腐蚀、碱腐蚀等;按腐蚀部位和破坏现象,可分为:均匀腐蚀、点腐蚀、晶间腐蚀、应力腐蚀、腐蚀疲劳等。
金属材料在特定腐蚀环境下,受拉应力共同作用时所产生的延迟开裂现象,称为“应力腐蚀开裂”。
应力腐蚀开裂属于环境敏感断裂范畴。
并非任何环境都会产生应力腐蚀开裂,应力腐蚀是特殊的腐蚀现象和腐蚀过程,一定的金属材料只在某一特定的腐蚀环境中才会产生应力腐蚀开裂。
有拉伸应力存在,是应力腐蚀开裂的先决条件,焊接剩余拉应力有着极为重要的影响!在锅炉压力容器部件的腐蚀中,应力腐蚀及其造成的破裂是最常见、危害最大的一种!已成为工业(特别是石油化工)中越来越突出的问题(参见:化工设备损伤事例统计表),石油化工焊接结构的破坏事故中,约有半数为应力腐蚀开裂。
化工设备(低于300ºC)损伤事例统计表①包括腐蚀疲劳开裂,一般约占8% 。
因此,必须从结构设计及施工制造方面考虑洚低剩余拉应力,以提高结构的抗应力腐蚀开裂性能。
当然,还应从生产管理方面考虑降低介质的腐蚀作用。
本节主要是了解应力腐蚀开裂的特征,以防止、控制应力腐蚀开裂。
一. 应力腐蚀开裂特征:1. 应力腐蚀开裂条件:(1)合金----纯金属不发生应力腐蚀,但几乎所有的合金在特定的腐蚀环境中都会产生应力腐蚀裂纹。
极少量的合金或杂质都会使材料产生应力腐蚀。
各种工程实用材料几乎都有应力腐蚀敏感性。
(2)拉应力-----引起应力腐蚀的应力必须是拉应力,且应力可大可小,极低的应力水平也可能导致应力腐蚀破坏(不管拉应力多么小,只要能引起变形滑移,即可促使产生应力腐蚀开裂)。
应力既可由载荷引起,也可是焊接、装配或热处理引起的残余应力。
(3)腐蚀性介质----产生应力腐蚀的材料和腐蚀性介质之间有选择性和匹配关系,即当二者是某种特定组合时才会发生应力腐蚀。
ANSINACE MR0103ISO 17945 2016石油石化和天然气工业—金属材料在腐蚀性石油精炼环境中抗硫化应力开裂

ANSI/NACE MR0103/ISO 17945: 2016石油,石化和天然气工业—金属材料在腐蚀性石油精炼环境中抗硫化应力开裂(中文翻译版)美国国家标准2015年11月23日批准版权保护文件ISO和NACE材料都受到版权保护。
没有获得NACE国际的书面许可,本出版物任何部分不能通过任何形式进行复制,包括电子检索系统。
所有与ANSI/NACE MR0103/ISO 17945相关的申请应提交给NACE。
版权所有。
国际标准化组织(ISO)ISO中央秘书处BIBC II地址:Chemin de Blandonnet 8CP4011214Vernier, GenevaSwitzerland电话:+41 22 749 01 11传真:+41 22 749 09 47Web: www.ISO .chNACE 国际地址:15835 Park Ten PlaceHouston, TX 77084-5145电话:+1281-228-6223传真:+1281-228-6300Web: 在美国由NACE印刷目录...............................................................................................................................页码前言 (6)引言 (7)1.范围 (8)2.规范性引用文件 (8)3.术语和定义 (9)4.符号和缩略语 (10)5.责任 (11)5.1最终用户的责任 (11)5.2制造商的责任 (12)6.导致硫化应力开裂(SSC)的因素 (12)6.1影响硫化应力开裂(SSC)的常规参数 (12)6.2材料状态及应力水平对SSC敏感性的影响 (12)6.3氢渗透流量对SSC的影响 (12)6.4高温暴露对SSC的影响 (13)6.5由于SSC造成的失效时间的影响因素 (14)6.6确定设备是否涵盖在本国际标准范围内的依据 (14)7.本国际标准收录的材料 (14)8.硬度要求 (15)9.增添新材料或新工艺的程序 (16)9.1一般投票要求 (16)9.2现场经验数据要求 (16)9.3实验室试验数据要求 (16)10.新的限制条件和废止材料 (17)11.特定用途的未列出的合金、工况和/或工艺的鉴定 (17)12.标准线路图 (19)13.铁基材料 (19)13.1碳钢和合金钢 (19)13.1.1所有碳钢和合金钢要求 (19)13.1.2 ASME BPVC第IX章中列出的P-No.1组别1或组别2的碳钢要求 (19)13.1.3其他碳钢要求 (20)13.1.4 ASME BPVC第IX章中所列的P系列合金钢要求 (20)13.1.5其他合金钢的要求 (20)13.1.6碳钢和合金钢的冷成型要求 (20)13.1.7 ASME BPVC第IX章中所列的P-No.1系列碳钢的焊接要求 (21)13.1.8 ASME BPVC第IX章中所列的P-No.3,4,或5A系列合金钢的焊接要求 (21)13.1.9碳钢和合金钢表面的耐腐蚀堆焊层,堆焊硬质层,覆盖层及热喷涂覆层 (21)13.2铸铁和球墨铸铁 (22)13.3铁素体不锈钢 (22)13.4马氏体不锈钢 (22)13.4.1常规马氏体不锈钢 (22)13.4.2低碳马氏体不锈钢 (23)13.4.3马氏体不锈钢的焊接和堆焊 (23)13.5奥氏体不锈钢 (24)13.6特定的奥氏体不锈钢牌号 (24)13.7高度合金化的奥氏体不锈钢 (24)13.8双相不锈钢 (25)13.8.1双相不锈钢的一般要求 (25)13.8.2双相不锈钢的焊接要求 (25)13.9沉淀硬化的不锈钢 (26)13.9.1奥氏体沉淀硬化型不锈钢 (26)13.9.2马氏体沉淀硬化型不锈钢 (26)13.9.3沉淀硬化不锈钢的焊接要求 (27)14.有色金属材料 (27)14.1镍合金 (27)14.1.1固溶镍合金 (27)14.1.2可沉淀硬化的镍合金 (28)14.2钴镍铬钼合金 (28)14.3钴镍铬钨合金 (29)14.4钛合金 (29)14.5铝合金 (30)14.6铜合金 (30)15.装配要求 (30)15.1一般装配要求 (30)15.2耐腐蚀堆焊层,硬质堆焊层以及覆盖层 (31)15.3焊接 (31)15.4碳钢、合金钢和马氏体不锈钢镀层 (31)15.5标识的打印 (32)15.6螺纹的加工 (32)15.6.1机械切削螺纹 (32)15.6.2冷作成形(套扣)螺纹 (32)15.7冷作成形工艺 (32)16.栓接 (32)16.1一般栓接要求 (32)16.2裸露的栓接 (33)16.3非裸露的栓接 (33)17.镀层、喷涂和扩散工艺 (33)18.特殊部件 (34)18.1特殊部件的一般要求 (34)18.2轴承 (34)18.3弹簧 (34)18.4仪器和控制装置 (34)18.4.1仪器和控制装置的一般要求 (34)18.4.2隔膜、测压装置和压力密封件 (35)18.5密封环和垫片 (35)18.6止动环 (35)18.7特殊工艺部件 (35)19.阀门 (35)20.压缩机和泵 (36)附录A(资料性附录)硫化物种类分布图 (37)附录B(资料性附录)硬度试验和要求的背景信息 (38)附录C(规范性附录)焊接程序评定硬度调查布局 (43)参考文献 (52)前言ISO(国际标准化组织)是各国的国家标准机构(ISO成员单位)的世界性联盟。
ASTM翻译

使用三氯化铁溶液做不锈钢及其合金的耐麻点腐蚀和抗裂口腐蚀性试验的标准方法本标准在固定代号G48下发行;紧随此代号之后的号码表示原正式通过的年份,或在修订版情况下,表示最新修订版年份。
括号中的数字表示最新复审年份。
上标ε表示自上次修订或重审以来的编辑变更。
1范围1 .1本试验方法包括若干测定规程,用于测定不锈钢及其台金暴露于氯-氧化环境时的耐麻点和裂口腐蚀性(见术语CL5)。
介绍六种规程,命名为方法A、B、C、D、E和F。
1 .1 .1方法A——三氯化铁麻点腐蚀试验。
I.1.2方法B——三氯化铁裂口腐蚀试验。
1.1.E方法C——镍基和铬包复合金的临界麻点腐蚀温度试验。
1.1.4 方法D——镍基和铬包复合金的临界裂口腐蚀温度试验。
1.1.5 方法E——不锈钢的临界麻点腐蚀温度试验。
1.1.6 方法F——不锈钢的临界裂口腐蚀温度试验。
1.2 方法A用于测定不锈钢和镍基、铬包复合金的相对耐麻点腐蚀性,方法B 可用于侧定这些合金的耐麻点和裂口腐蚀性。
方法C、D、E和F可在标准三氯化铁溶液中,按导致不锈钢、镍基和铬包复合金各自开始麻点腐蚀和裂口腐蚀的最低(临界)温度,为这些合金划分等级。
1 .3 这些试验可用于测定合金填加剂、热处理和表面光洁度对耐麻点腐蚀性和耐裂口腐蚀性的影响。
1.4 以SI单位表示的值被认为标准。
在括号中给出其它单位,仅供参考。
1.5 本标准并不意味已提及与其使用相关的所有安全事项。
制定合适的安全和健康规范,确定规章限制的适用性,是本标准用户的职责。
2 引用文件2.1 ASTM标准A262 检测奥氏体不锈钢晶间腐蚀敏感性规范②。
D1193 试剂水技术规范③。
E691 进行实验室间研究以测定试验方法精度的规范④。
E1338 计算机化材料性能数据库中金属与合金识别指南⑤。
G1 制备、清洗和评估腐蚀拭验试样的规范⑥。
G15 与腐蚀和腐蚀试验相关的术语⑦。
G46 麻点腐蚀检验和评估指南⑧。
G107 计算机化数据库输入用金属腐蚀数据采集和编辑格式准则⑨。
- 1、下载文档前请自行甄别文档内容的完整性,平台不提供额外的编辑、内容补充、找答案等附加服务。
- 2、"仅部分预览"的文档,不可在线预览部分如存在完整性等问题,可反馈申请退款(可完整预览的文档不适用该条件!)。
- 3、如文档侵犯您的权益,请联系客服反馈,我们会尽快为您处理(人工客服工作时间:9:00-18:30)。
用断裂负荷法测定热处理铝合金制品抗应力腐蚀开裂性的标准试验方法(等同采用ASTMG139-05(R2011))(中文翻译版)编制: 日期:审核: 日期:批准: 日期:修订历史修订序号对应的条号修订内容修改人批准人日期1. 目的Purpose本标准试验方法涵盖了通过断裂荷载试验方法评估抗应力腐蚀开裂(SCC)性的程序,该方法使用剩余强度作为损伤演化(在这种情况下为环境辅助开裂)的测量方法。
包括试样类型和复制、试验环境、应力水平、暴露时间、最终强度测定和原始残余强度数据的统计分析。
2. 范围Scope本标准试验方法适用于热处理铝合金,即2XXX合金和7XXX,含1.2%至3.0%铜,且试样的取向与晶粒结构相关,横向较短。
然而,用于分析数据的残余强度测量和统计数据并非针对可热处理铝合金,可用于其他试样取向和不同类型的材料。
3. 职责Responsibility程序执行:实验室授权制样人员程序监督:实验室技术负责人及相关责任人4. 原理Principle4.1本试验方法描述了使用暴露于腐蚀环境后的残余强度评估热处理铝合金产品形式(如板材、板材、挤压件、锻件和棒材)的应力腐蚀开裂敏感性的程序。
这些产品通常在板材的长横方向、板材、挤压件和锻件的短横方向以及棒材和棒材的横方向上最易发生应力腐蚀开裂。
在本试验中,根据规程G49制备的拉伸钢筋或直接拉伸板试样暴露于3.5重量%的氯化钠水溶液(规程G44)中,在其失效前移除,并进行拉伸试验,以确定已发生的腐蚀损伤量。
然后计算平均剩余强度,并使用Box-Cox变换对结果进行统计分析。
4.2该程序要求暴露无应力试样,用于排除点蚀、晶间腐蚀和一般腐蚀的影响。
这些现象会降低残余强度,但不需要施加应力。
4.3本试验方法适用于高强度铝合金(2XXX和含有7XXX的铜),通常在3.5%氯化钠中通过交替浸泡进行试验。
然而,使用剩余强度作为损伤演化度量的概念(在这种情况下,环境辅助开裂)原则上可以应用于任何合金和环境系统。
4.4本试验方法用于研究抗应力腐蚀性能提高的合金和回火。
试验结果允许将不同的材料变体与高置信度进行比较,并且比通过/失败试验的结果具有更高的精度。
因此,它对于比较具有类似抗应力腐蚀开裂水平的材料特别有用。
该程序可以修改以用作质量保证工具,但在其开发过程中,这并不是主要目的。
4.5本试验方法中所述的暴露时间和条件特别适用于高强度铝合金,但统计技术应适用于具有不同暴露条件的其他合金系统。
4.6尽管该特殊程序主要用于在短横向应力方向上测试产品,但对于其他应力方向,尤其是薄板和薄板产品中的长横向,该程序是有用的。
4.7确定材料的实际适用性需要在与最终用途有关的条件下,在预期的使用环境中进行应力腐蚀试验,包括涂层和抑制剂等保护措施,且不在本试验方法的范围内。
4.7.1没有很好的方法将测试环境与实际服务进行比较,因为大多数服务环境对于可能经历许多不同环境的单个结构或对于在不同位置服务的两个相同结构具有很大的内在可变性。
除非样品能在实际使用环境中测试部件的预期寿命,否则不能确定特定材料是否适合特定应用。
因此,设计师必须根据对材料和使用环境的了解,对特定材料的适用性作出判断。
为了避免服务故障,用于初步评估的环境通常是根据导致故意高估腐蚀损害的最坏情况选择的。
5. 术语及定义Terms and Definition5.1审查—一个统计术语,表明由于试验程序或条件的原因,单个观察值可能超出可测量的范围。
5.2取样—从中获得单个应力腐蚀开裂试样的名义上均匀的散装材料。
6. 干扰Interferences6.1断裂负荷试验根据实施规程G44排除了在环境中发生的点蚀,例如在交替浸没试验中使用的3.5%NaCl溶液。
使用断裂负荷试验的主要问题是选择适当的暴露应力。
如果暴露压力太低,则不会累积损伤。
另一方面,如果施加的应力过高,许多试样将在预定的暴露期结束前失效。
本试验方法中包含的统计程序可以容纳少量的失效试样,但不能容纳大量的试样。
6.2断裂负荷试验适用于暴露在自然和使用环境中的试样。
然而,这些环境中的条件可能不是恒定的,因此必须考虑暴露的时间和周期,以避免产生偏差。
例如,温度、湿度和污染物浓度等季节性变化的环境条件可能会影响室外暴露站的腐蚀性。
应使用相同的环境条件进行直接的材料比较。
6.3当对比样品具有不同的原始(未腐蚀)拉伸强度和断裂韧性值时,需要注意。
初始性能的大变化可以减少或增加样品SCC性能的明显差异。
为了避免由于拉伸性能而产生的偏差,本试验方法中包含的统计程序基于原始强度的百分比。
然而,为了检验影响残余强度的断裂韧性的影响,必须使用断裂力学技术进行缺陷尺寸计算。
7. 试样Specimens7.1断裂荷载程序可使用夹具中可承受轴向应力的任何试样进行,该夹具将承受施加的位移。
然而,使用不同的试件几何形状或应力方法获得的结果不能直接进行比较。
虽然样品的相对磁化率不会改变,但绝对值可能会大不相同。
7.2只要金属试样的几何形状允许,应使用根据规程G49制备的光滑圆形拉伸试样进行试验。
如果薄板和其他产品太薄,无法产生抗拉钢筋,则可使用薄板拉伸试样。
试验灵敏度随试样标距截面表面积与体积比的增大而增大,但用圆形拉伸试样进行的试验表明,不同尺寸的试样(1)可以达到相同的相对排名。
8. 程序Procedure8.1应力程序和暴露条件—试样应按照规程G49图1中的恒定挠度型夹具进行轴向加载,并按照规程G44进行3.5%NaCl交替浸没试验。
每个应力水平/暴露时间组合的试样数量应至少为3个;最好为5个或更多。
8.2应力水平—应力水平的最小数量为两个,其中一个是无外加应力暴露的整套试样。
对于具有未知应力腐蚀抗力的试样,除了无应力试样外,最好从两个或三个应力水平开始。
无应力试样允许计算一般、点蚀和晶间腐蚀引起的损伤,并将其与外加应力引起的损伤分开。
必须通过考虑样品的预期性能,为每个样品选择其他应力水平。
试样抗应力腐蚀能力越强,应力越高。
理想的最大应力应为通过开裂导致显著损伤的最大应力,但在预定暴露期(2)结束前,不会导致超过几个试样实际断裂成两片。
可以使用一个应力水平,但统计计算仅评估该应力水平下样品的性能。
换言之,如果不实际进行测试,就没有很好的方法来推断和估计较高或较低应力水平下的性能。
8.3暴露时间—必须针对待测样品和试样的尺寸和方向调整该参数。
一般来说,对于2XXX和7XXX合金的短期横向试验,应使用2到4个时间段(加上零天无应力),最大时间约为10天。
一般来说,长的横向试样和更耐腐蚀的合金系统(如6XXX合金)应暴露更长的时间。
G64分类给出了这些情况的时间段,可用于估计合理的最大暴露时间。
注1:对于在试验环境中具有未知SCC性能的材料变体,建议根据试验方法G47中的程序对有限数量的合格/不合格试样进行试验。
这将为选择适当的应力水平和样品暴露时间提供指导。
这可以防止花费大量的时间和金钱在没有提供重要价值信息的标本上。
8.4残余强度的测定—在每个暴露期结束后,应根据试验方法E8从试验中取出一组试样,进行冲洗、无应力和拉伸试验。
建议在试样从暴露中取出的当天完成拉伸试验。
如果在完成暴露和拉伸试验之间不可避免地存在时间延迟,则必须用去离子水彻底冲洗试样,并将其存放在干燥的环境中,并且应记录延迟时间。
必须计算并记录每个试样的断裂强度。
8.5残余强度数据可用于通过简单计算每个应力/时间组合的平均残余强度来显示样品之间的趋势,如图1所示。
然而,必须使用统计程序来评估趋势是真实的还是仅仅是数据分散的。
8.5.1在断裂负荷试验方法的发展过程中,单个单元(单个样品/应力/时间组合)内的数据方差显示,随着抗SCC 能力的降低而增加。
这种方差随残余强度降低而增加的趋势意味着,对于性能较好的单元,断裂负荷试验解决单元间差异的能力可能比性能较差的单元大得多。
因此,平均剩余强度图可能会产生误导。
注1:本组中的一些试样在预定的暴露期结束前确实发生了故障,但这些故障试样并未包含在平均值中。
平均值仅代表幸存下来进行拉伸试验的试样。
在310 MPa下,九天数据的上升是由于不包括失效试样。
图1 代表性数据集(一个实验室)的平均剩余强度值图9. 报告Report报告应包括以下信息:a)所有样品的标识,包括合金、回火、产品形状、厚度、样品位置和方向。
b)所有原始数据,包括每个腐蚀试样的原始抗拉强度、暴露时间、应力水平和原始断裂强度。
这最好以表格形式进行,使用每个应力/时间组合的单元格。
该表应记录在从试验中取出之前以及检测到故障当天发生故障的任何试样。
只要有可能,建议报告断裂韧性与SCC裂纹扩展方向相同。
例如,对于使用短横向SCC试样测试的轧制钢板,最合适的值是S-L平面应变断裂韧度(K IC)。
c)所有计算的统计数量。
最小值是每个数据单元的平均断裂强度和标准偏差。
d)与上述程序的所有偏差。
10. 相关记录表式Record FormJC-YS-2019-023 电化学原始记录表JC-ZL-0808 仪器设备使用记录表11. 参考文件ReferenceASTM G139-05(R2011) Standard Test Method for Determining Stress-Corrosion Cracking Resistance of Heat-Treatable Aluminum Alloy Products Using Breaking Load Method。