焊缝质量检验
焊接质量的检验方法有哪些检测各种焊缝的质量的

焊接质量的检验方法有哪些检测各种焊缝的质量的.范本 1 (正式风格):正文:一、焊接质量的检验方法概述焊接质量的检验方法是评估焊接工艺的有效手段,可以确保焊缝的质量符合标准要求。
下面是几种常用的焊接质量检验方法。
二、外观检验方法焊接的外观质量是评估焊缝质量的重要指标之一。
外观检验方法主要有以下几种:1. 目测检验:通过肉眼观察焊缝表面质量,如焊缝的形状、颜色等。
2. 放大镜检验:使用放大镜观察焊缝细节,如焊缝的裂纹、气孔等缺陷。
3. 比较标准检验:将焊缝与标准焊缝进行对比,判断其差异。
三、物理性能检验方法焊缝的物理性能是评估焊接质量的重要指标之一。
物理性能检验方法主要有以下几种:1. 强度测试:使用拉伸试验机测试焊缝的拉伸强度、屈服强度等。
2. 断裂韧性测试:使用冲击试验机测试焊缝的抗冲击能力。
3. 硬度测试:使用硬度计测试焊缝的硬度值,判断其强度。
四、成分分析方法焊缝的成分分析是评估焊接质量的重要手段之一。
成分分析方法主要有以下几种:1. 化学成分分析:使用化学分析仪器对焊缝材料的成分进行定量分析。
2. 元素分析:使用光谱仪等仪器对焊缝材料中的元素进行分析。
五、无损检测方法无损检测方法是评估焊接质量的非破坏性手段。
无损检测方法主要有以下几种:1. 超声波检测:使用超声波探测仪对焊缝进行缺陷检测。
2. 射线检测:使用射线设备对焊缝进行缺陷检测。
3. 磁粉检测:使用磁粉检测仪对焊缝进行表面缺陷检测。
附件:本文档涉及的附件包括相关测试报告、图表和数据表格。
法律名词及注释:1. 焊接质量检验方法:指对焊接质量进行评估的检验手段。
2. 焊缝表面质量:指焊缝表面的外观特征,如形状、颜色等。
3. 拉伸强度:指焊缝材料在拉伸条件下的最大承载能力。
4. 屈服强度:指焊缝材料在拉伸过程中开始发生塑性变形的能力。
5. 韧性:指焊缝材料抵抗断裂的能力。
6. 无损检测方法:指通过非破坏性手段对焊缝进行缺陷检测。
范本 2 (非正式风格):正文:一、焊接质量的检验方法概述哎呀呀,说起来各种检测焊缝质量的方法可真是多啊!下面给你盘点一下常用的几种吧!二、外观检验方法首先,最容易想到的当然是目测检验咯!别说,有时候肉眼观察焊缝表面的质量也是很准确的。
焊缝质量检验标准

焊缝质量检验标准随着焊接技术的广泛应用,焊接质量成为保障工程安全和可靠性的重要因素。
焊缝质量的检验是确保焊接结构强度和可靠性的关键步骤。
本文将介绍常见的焊缝质量检验标准及其应用。
一、焊缝质量指标焊缝质量的评定主要涉及以下几个方面:1. 外观质量:焊缝应满足表面光洁、无裂纹、夹渣、气孔等缺陷,并符合相关图表要求。
2. 尺寸偏差:焊缝应符合图纸要求的尺寸偏差范围,如焊缝高度、厚度、宽度等。
3. 焊接强度:焊缝的强度应达到或超过要求的标准值,以确保焊接结构的可靠性和安全性。
4. 焊缝成分分析:通过对焊缝的成分进行分析,可以判断焊接材料的质量和一致性。
二、焊缝质量检验方法焊缝质量的检验方法通常包括以下几种:1. 目测检查:通过肉眼观察焊缝的外观质量,如表面光洁度、无缺陷、夹渣、气孔等。
2. 尺寸测量:使用相应的测量工具,测量焊缝的尺寸,如高度、宽度、长度等。
3. 无损检测:采用无损检测技术,如超声波检测、射线检测和磁粉检测等,对焊缝进行缺陷探测。
4. 化学成分分析:通过取样并进行化学分析,了解焊缝的成分情况,以判断焊接材料的质量和一致性。
5. 强度测试:采用相应的力学测试方法,对焊缝进行拉伸、剪切等强度测试,以评估焊缝的强度性能。
三、焊缝质量标准为了确保焊接工程的质量,并便于评定焊缝质量,制定了一系列的焊缝质量标准。
下面介绍几个常见的焊缝质量标准:1. GB/T 1499.1-2018 钢筋焊接接头技术规范:该标准适用于钢筋焊接接头的质量评定,包括焊点外观质量、尺寸偏差、焊点强度等指标。
2. GB/T 25121-2010 碳素钢和低合金钢焊接结构工程技术规范:该标准规定了碳素钢和低合金钢焊接结构质量检验的要求,包括焊缝外观、尺寸、力学性能等指标。
3. ASME SEC IX-2019 锅炉及压力容器焊接与热处理规范:该规范适用于锅炉和压力容器的焊接质量评定,包括各种焊接方法的质量要求以及焊缝强度、外观等方面的检验标准。
焊接质量的五种检验方法
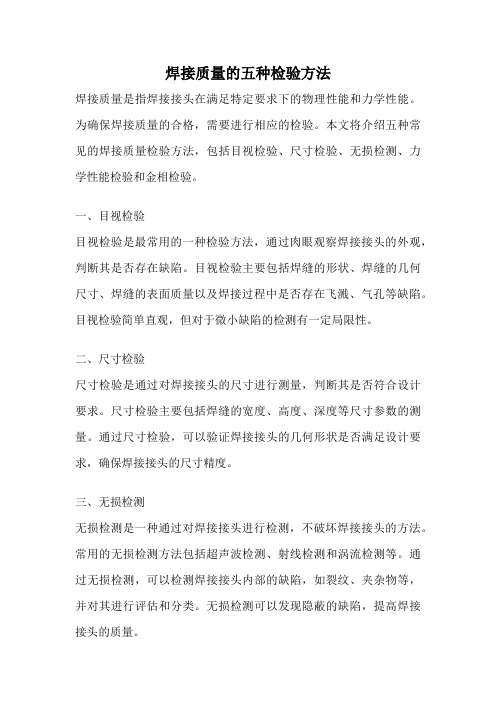
焊接质量的五种检验方法焊接质量是指焊接接头在满足特定要求下的物理性能和力学性能。
为确保焊接质量的合格,需要进行相应的检验。
本文将介绍五种常见的焊接质量检验方法,包括目视检验、尺寸检验、无损检测、力学性能检验和金相检验。
一、目视检验目视检验是最常用的一种检验方法,通过肉眼观察焊接接头的外观,判断其是否存在缺陷。
目视检验主要包括焊缝的形状、焊缝的几何尺寸、焊缝的表面质量以及焊接过程中是否存在飞溅、气孔等缺陷。
目视检验简单直观,但对于微小缺陷的检测有一定局限性。
二、尺寸检验尺寸检验是通过对焊接接头的尺寸进行测量,判断其是否符合设计要求。
尺寸检验主要包括焊缝的宽度、高度、深度等尺寸参数的测量。
通过尺寸检验,可以验证焊接接头的几何形状是否满足设计要求,确保焊接接头的尺寸精度。
三、无损检测无损检测是一种通过对焊接接头进行检测,不破坏焊接接头的方法。
常用的无损检测方法包括超声波检测、射线检测和涡流检测等。
通过无损检测,可以检测焊接接头内部的缺陷,如裂纹、夹杂物等,并对其进行评估和分类。
无损检测可以发现隐蔽的缺陷,提高焊接接头的质量。
四、力学性能检验力学性能检验是通过对焊接接头进行拉伸、弯曲、冲击等试验,评估焊接接头的力学性能。
力学性能检验可以验证焊接接头的强度、韧性和冲击性能是否满足要求。
常用的力学性能检验方法包括拉伸试验、冲击试验和硬度试验等。
五、金相检验金相检验是通过对焊接接头进行金相组织观察和分析,评估焊接接头的组织性能。
金相检验可以检测焊接接头的晶粒尺寸、晶体结构、相含量和相组成等。
金相检验可以发现焊接接头的晶粒异常、相变和相分离等缺陷,对焊接接头的质量评估具有重要意义。
焊接质量的检验方法包括目视检验、尺寸检验、无损检测、力学性能检验和金相检验。
这些检验方法各具特点,可以对焊接接头的质量进行全面评估,确保焊接接头的质量合格。
在实际焊接过程中,应根据具体情况选择合适的检验方法,以保证焊接质量的可靠性和稳定性。
焊缝外观质量检验标准
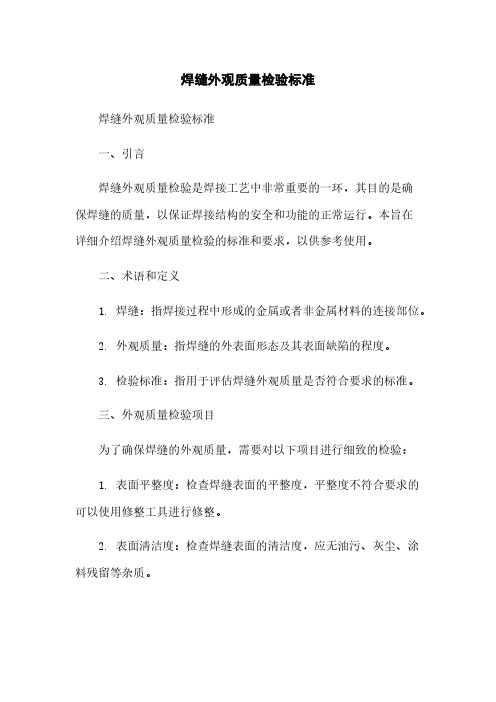
焊缝外观质量检验标准焊缝外观质量检验标准一、引言焊缝外观质量检验是焊接工艺中非常重要的一环,其目的是确保焊缝的质量,以保证焊接结构的安全和功能的正常运行。
本旨在详细介绍焊缝外观质量检验的标准和要求,以供参考使用。
二、术语和定义1. 焊缝:指焊接过程中形成的金属或者非金属材料的连接部位。
2. 外观质量:指焊缝的外表面形态及其表面缺陷的程度。
3. 检验标准:指用于评估焊缝外观质量是否符合要求的标准。
三、外观质量检验项目为了确保焊缝的外观质量,需要对以下项目进行细致的检验:1. 表面平整度:检查焊缝表面的平整度,平整度不符合要求的可以使用修整工具进行修整。
2. 表面清洁度:检查焊缝表面的清洁度,应无油污、灰尘、涂料残留等杂质。
3. 焊缝几何形状:检查焊缝的几何形状,包括焊缝的高度、宽度、间隙等。
4. 焊缝表面缺陷:检查焊缝表面是否存在气孔、夹杂物、裂纹等缺陷,这些缺陷会对焊接结构的强度和密封性产生影响。
四、检验方法和标准1. 目视检查:通过肉眼观察焊缝表面,检查表面平整度、清洁度和几何形状等项目。
如果有明显的缺陷,可以进一步进行放大镜检查。
2. 放大镜检查:通过放大镜观察焊缝表面,对焊缝表面缺陷进行详细的检查和评估。
根据焊接规范和标准,确定缺陷的等级和接受标准。
3. 尺寸测量:使用尺子或者测量仪器测量焊缝的高度、宽度、间隙等,以确保其符合设计要求和规范要求。
五、缺陷等级和接受标准根据焊接规范和标准,焊缝表面缺陷可分为多个等级,包括一级(最严重)至五级(最轻微)。
不同焊接结构的缺陷等级和接受标准可能有所不同,需根据实际情况进行确定。
六、附件本所涉及的附件如下:1. 图表附件:包括焊接结构示意图、焊缝缺陷示意图等。
2. 检验记录表:用于记录焊缝外观质量检验结果。
七、法律名词及注释1. 建造法规:指国家对建造行业所制定的法律法规,包括《建筑法》、《建造工程施工合同管理办法》等。
2. 焊接规范:指国家对焊接工艺和质量的规范文件,如《焊接工艺规范》、《焊接接头验收标准》等。
焊缝质量无损检验方法

焊缝质量无损检验方法一、检验标准及依据1.1GBT34628-2017《焊缝无损检测金属材料应用通则》;1.2GBT11345-2013《焊缝无损检测超声波检测技术、检测等级和评定》;二、无损检验方法根据GB34628表1,无损检验可分为6种,详见下表。
三、3.1涡流检测(ET):是利用探头线圈内流动的高频电流可在焊缝表面感应出涡流的效应,有缺陷会改变涡流磁场,引起线圈输出变化来反映缺陷。
其检验参数控制相对困难,可检验导中材料表面或焊缝与堆焊层表面或近表面缺陷。
3.2磁性检测(MT):是利用铁磁性材料表面与近表面缺陷引起磁率发生变化,磁化时在表面上产生漏磁场,再采用磁粉、磁带或其他磁场测量方法记录与显示缺陷。
主要用于检测焊缝表面或近表面起磁率发生变化,磁化时在表面上产生漏磁场,再采用磁粉、磁带或其他磁场测量方法记录与显示缺陷。
主要用于检测焊缝表面或近表面缺陷。
3.3渗透检测(PT):采用含有颜料或荧光粉剂的渗透液喷洒或涂敷在被检焊缝表面上,利用液体的毛细作用,使其渗入表面开口的缺陷中,然后清洗去除表面上多余的渗透液,干燥后施加显像剂,将缺陷中的渗透液吸附到焊缝表面上,观察缺陷的显示痕迹。
此法主要用于焊缝表面检测或气创清根后的根部缺陷检测。
3.4射线检测(X、Y)方法(RT):是利用X、Y,射线源发出的贯穿辐射线穿透焊缝后使胶片感光,焊缝中的缺陷影像便显示在经过处理后的射线照相底片上,是目前应用较广泛的无损检验方法,能发现焊缝内部气孔、夹渣、裂纹及未焊透等缺陷,射线探伤基本不受焊缝厚度限制。
但无法测量缺陷深度,检验成本较高,时间长,射线对探伤操作人员有损伤。
3.5超声波检测(UT):是利用压电换能器通过瞬间电激发产生脉冲振动,借助于声耦合介质传入金属中形成超声波,并在传播时遇到缺陷反射并返回到换能器,再把声脉冲转换成电脉冲,测量该信号的幅度及传播时间就可评定工件中缺陷的位置及严重程度。
超声波比射线探伤灵敏度高、灵活方便、周期短、成本低、效率高、对人体无害,但显示缺陷不直观,对缺陷判断不精确,靠探伤人员经验和技术熟练程度影响较大。
焊缝的外观质量检验

焊缝的外观质量检验1. 概述在焊接工艺中,焊缝的外观质量检验是一项非常重要的工作。
焊缝的外观质量直接关系着焊接件的使用寿命和工作性能。
因此,在焊接过程中,对焊缝的外观质量进行全面的检验是必不可少的。
本文将介绍焊缝外观质量检验的一些常见方法和标准。
2. 检验方法焊缝的外观质量检验可以通过目视检查、放大镜检查和显微镜检查等多种方法来进行。
2.1 目视检查目视检查是最常用的检验方法,也是最直观的方法之一。
通过目视检查可以初步了解焊缝的外观情况,包括焊缝的形状、尺寸、表面平整度以及是否存在缺陷等。
在目视检查时,应注意以下几个方面:•焊缝形状:焊缝应平直、均匀,无明显的凹陷或突起。
•焊缝尺寸:焊缝尺寸应符合设计要求,没有明显的偏差。
•表面平整度:焊接表面应平整,无明显的凹凸不平或波纹。
2.2 放大镜检查在目视检查的基础上,可以使用放大镜对焊缝进行更加详细的检查。
通过放大镜的放大效果,可以更清晰地观察焊缝的表面状况,包括焊缝的颜色、纹理以及是否存在裂纹、夹渣等明显的缺陷。
放大镜检查时,应注意以下几个方面:•焊缝颜色:焊缝应呈现均匀的金属光泽,无明显的色差。
•纹理:焊缝的纹理应均匀细腻,无明显的粗糙感。
•缺陷:注意观察焊缝的裂纹、夹渣等明显的缺陷。
2.3 显微镜检查显微镜检查是一种更加精细的检验方法,适用于对特别小型的焊接件进行检验。
通过显微镜的放大效果,可以更详细地观察焊缝的微观结构,以及一些细微缺陷的存在。
显微镜检查时,应使用高倍放大镜,并注意以下几个方面:•微观结构:观察焊缝的晶粒结构,应呈现均匀细致的晶粒。
•气孔:观察焊缝中是否存在气孔,气孔应尽量避免。
•夹渣:观察焊缝中是否存在夹渣,夹渣应及时清除。
3. 标准参考对于焊缝外观质量的检验,可参考以下标准:•GB/T 50235-1996《焊接接头评定和外观质量检验标准》;•DL/T 5146-2003《钢结构工程焊缝质量检验标准》;•AWS D1.1/D1.1M:2020《钢结构工程焊接规范》。
常用检验焊缝的几种方法

焊接过程中检验包括检验在焊接过程中焊接工艺参数是否正确,焊接设备运行是否正常,焊接夹具夹紧是否牢固,在操作过程中可能出现的焊接缺陷等。
焊接过程中检验主要在整个操作过程中完成。
成品的焊接质量检验检验方法很多,应根据产品的使用要求和图样的技术条件选用。
1.非破坏性检验非破坏性检验是指在不损坏被检验材料或成品的性能、完整性的条件下进行检测缺陷的方法,包括外观检验、致密性检验和无损探伤检验。
(1)外观检验焊接接头的外观检验是以肉眼直接观察为主,一般可借助于焊缝万能量规,必要时利用5-10倍放大镜来检查。
外观检测主要是为了发现焊接接头的表面缺陷,如焊缝的表面气孔、咬边、焊瘤、烧穿及焊接表面裂纹、焊缝尺寸偏差等。
检验前,须将焊缝附近10-20mm范围内的飞溅物和污物清除干净。
(2)致密性检验:致密性检验是检验焊接管道,盛器,密闭容器上焊缝是否存在不致密的缺陷。
常用的检验方法有:气密性实验;氨气实验;煤油实验;水压试验和气压实验。
(3)无损探伤检验:是非破坏性检验中的一种特殊的检验方式,是利用渗透,磁粉,超声波,射线等检验方法来发现焊缝表面的细微缺陷及存在于焊缝内部的缺陷。
目前,这类检验方法已在重要的焊接结构中被广泛应用。
2.破坏性检验破坏性检验是从焊件或试件上切取试样或以产品的整体破坏做试验,以检查其力学性能等的检验方法。
它包括力学性能试验,化学分析,腐蚀试验,金相试验,焊接性试验等。
在生产中,焊接成品的质量检验很重要占有很重要的地位。
它不仅在于发现焊接缺陷,检验焊接接头的性能,以确保产品的焊接质量和安全使用,严重的缺陷可导致受压容器的爆炸,造成直接经济损失或灾难性事故而且通过各种检验可对缺陷作出客观的判断,才能对焊缝作出可靠的结论,看其是否所规定的技术要求和保证结构使用的安全可靠。
下面介绍几种检验焊缝质量的方法:(1)气密性实验:一般检验管道,盛器,密闭容器上焊接是否存在不致密的缺陷,以便及时发现,进行排除并修复。
焊缝质量分级检验
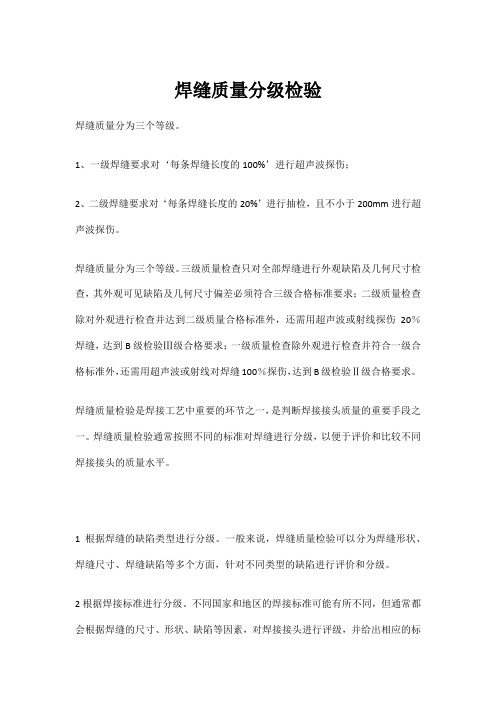
焊缝质量分级检验焊缝质量分为三个等级。
1、一级焊缝要求对‘每条焊缝长度的100%’进行超声波探伤;2、二级焊缝要求对‘每条焊缝长度的20%’进行抽检,且不小于200mm进行超声波探伤。
焊缝质量分为三个等级。
三级质量检查只对全部焊缝进行外观缺陷及几何尺寸检查,其外观可见缺陷及几何尺寸偏差必须符合三级合格标准要求;二级质量检查除对外观进行检查并达到二级质量合格标准外,还需用超声波或射线探伤20%焊缝,达到B级检验Ⅲ级合格要求;一级质量检查除外观进行检查并符合一级合格标准外,还需用超声波或射线对焊缝100%探伤,达到B级检验Ⅱ级合格要求。
焊缝质量检验是焊接工艺中重要的环节之一,是判断焊接接头质量的重要手段之一。
焊缝质量检验通常按照不同的标准对焊缝进行分级,以便于评价和比较不同焊接接头的质量水平。
1根据焊缝的缺陷类型进行分级。
一般来说,焊缝质量检验可以分为焊缝形状、焊缝尺寸、焊缝缺陷等多个方面,针对不同类型的缺陷进行评价和分级。
2根据焊接标准进行分级。
不同国家和地区的焊接标准可能有所不同,但通常都会根据焊缝的尺寸、形状、缺陷等因素,对焊接接头进行评级,并给出相应的标准和要求。
3根据焊接材料进行分级。
焊接材料的质量也会影响焊接接头的质量,因此在进行焊缝质量检验时,也需要考虑焊接材料的质量和选用情况,以便于进行合理的评价和分级。
4根据焊接工艺进行分级。
不同的焊接工艺也会影响焊接接头的质量,因此在进行焊缝质量检验时,需要考虑使用的焊接工艺和具体操作情况,以便于进行评价和分级。
5根据应用要求进行分级。
不同的焊接接头在实际应用中,可能有不同的要求和标准,因此在进行焊缝质量检验时,需要考虑具体的应用要求和标准,以便于进行合理的评价和分级。
- 1、下载文档前请自行甄别文档内容的完整性,平台不提供额外的编辑、内容补充、找答案等附加服务。
- 2、"仅部分预览"的文档,不可在线预览部分如存在完整性等问题,可反馈申请退款(可完整预览的文档不适用该条件!)。
- 3、如文档侵犯您的权益,请联系客服反馈,我们会尽快为您处理(人工客服工作时间:9:00-18:30)。
焊缝质量控制一、焊接工艺1、材料1).电焊条:按照设计及规范要求选用焊条,焊条必须具有出厂合格证明,如须焊条型号,必须征得设计部门同意。
严禁使用过期、药皮脱落、焊芯生锈的焊条。
焊接前将焊条进行烘陪处理。
2).作业条件a.审阅施工图纸,拟定焊接工艺。
b.准备好所需施焊工具,焊接电流。
c.在钢结构车施焊区施焊。
d.焊工经过考试,并取得合格证才可上岗,如停焊超过半年以上时,则重新考核后才准上岗。
e.施焊前焊工复查组装质量和焊缝区的处理情况,如不符合要求,修整合格后方能施焊。
2、操作工艺1).焊条使用前,必须按照质量说明书的规定进行烘陪后,放在保温箱内随用随取。
2).首次采用的钢种和焊接材料,必须进行焊接工艺性能和物理性能实验,符合要求后才采用。
3).多层焊接应连续施焊,其中每一层焊道焊完后应及时清理,如发现有影响焊接质量缺陷,必须清除后再焊。
4).要求焊成凹面贴角焊缝,可采用船位焊接使焊道金属与母材平缓过渡。
5).焊道出现裂纹时,焊工不得擅自处理,须申报焊接技术负责人查清原因,订出修补措施后才可处理。
6).严禁在焊缝区以外的母材上打火引弧,在坡口内起弧的局部面积应熔焊一次,不得留下弧坑。
7).重要焊缝接头,要在焊件两端配置起弧和收弧板,其材质和坡口形式应与焊件相同。
8).要求等强度的对接和丁字接头焊缝,除按设计要求开坡口外,为了确保焊缝质量,焊接前采用碳弧气刨刨焊根,并清理根部氧化物后才进行焊接。
9).为了减少焊接变形与应力,我公司常采取如下措施:a.焊接时尽量使焊缝能自由变形,钢构件的焊接要从中间向四周对称进行。
b.收缩量大的焊缝先焊接。
c.对称布置的焊缝由成双数焊工同时焊接。
d.长焊缝焊接可采用分中逐步退焊法或间断焊接。
e.采用反变形法,在焊接前,预先将焊件在变形相反的方向加以弯曲或倾斜,以消除焊后产生的变形,从而获得正常形状的构件。
f.采用刚性固定法:用夹具夹紧被焊零件能显著减少焊件残余变形及翘曲。
g.锤击法:锤击焊缝及其周围区域,可以减少收缩应力并变形。
二、焊缝质量检验标准1、适用范围1.1本标准适用于手工电弧焊,埋弧焊,气体保护焊等方法焊接的碳素结构钢或低合金钢焊接结构件的焊缝质量检验1.2凡本公司产品的焊缝检验,均按本标准执行,本标准包括焊缝外部质量和内部质量两方面的内容,其中内部质量涵盖焊缝分级适合本公司的重要内容,其他均按GB/T 3323—2005等一些文件执行。
2、焊缝质量的检验焊缝质量分为三级,各级检验项目和方法见表2.1表2.1 焊缝质量分级机检验内容和方法注:VT—目检、MT—磁粉检验、PT—渗透检验、UT—超声波检验、RT—射线检2.1:I级焊缝的无损探伤仅适合用特别构件的受拉对接焊缝(如桥式起重机主梁的下翼缘板拼缝,门座起重机臂架系统上、下翼缘、腹板拼接和其他载荷明确的受拉拼缝等)或周期载荷非管材连接的对接焊缝,一般被探钢材厚度≥12mm 时,均可采用超声波探伤;厚度<8mm时均可采用射线探伤;8mm或10mm的手工电弧焊焊缝出超声波探伤外,需要时还可以采用RT抽查5%焊缝累积柴杜,并拍片≥1张。
2.2:II级焊缝的无损探伤一般适用于受压对接焊缝(如桥式起重机主梁的上翼缘板拼缝和其他载荷明确的受压拼缝等)或静载荷非管连接的焊缝。
2.3:当采用目测发现焊缝有明显缺陷,并需进一步了解焊缝缺陷实际情况,可采用磁粉检测或渗透检测的方法作为辅助手段多焊缝评定外观质量等级。
2.4:对于角焊缝(1)箱体纵向角焊缝一般不需要探伤;(2)对于起重臂、变幅支座附近、吊耳和图纸重要注明要求探伤的角焊缝均采用超声波探伤。
3、焊缝质量检测标准3.1 焊缝外部质量目测(VT)焊缝外部质量检测可用目视及焊缝尺寸量具进行100%检验,检验前应将焊缝表面的熔渣清理干净,检测内容及标准见表3.1焊缝外部成型尺寸达不到表3.1的要求时,必须将焊缝尺寸打磨至规定值,此外其它焊缝需打磨的应在图纸上标明,打磨符号集说明见表3.1A表3.1 焊缝外部质量标准3.1.1、K 为最小角焊缝尺寸时(见下表),则I 级的下公差应为(最下尺寸)+0.5,II 级下公差为0。
注:非一般结构件取括号内数值。
3.2.2、在大量两端的2倍翼板宽度内,腹板与翼板的焊缝不允许欠焊(0-=∆K )。
表3.1A 焊缝打磨符号 注:1、要求齐平的对接接头(0G )表面进行修整时,不得使较薄母材或焊缝金属的厚度有减薄量≤0.8mm 或5%厚度、取值较小值;打磨后的余高≤0.8mm 。
2、角焊缝的1G 、2G 在修整后焊角尺寸不小于标准值或图纸注明尺寸。
C —气孔或熔合型缺陷沿焊缝纵轴测定的最小间距(相邻缺陷以较大者为准) 注:1、从E 作水平投影至B ,确定缺陷的最大容许尺寸(任何接头或焊缝尺寸)。
2、从E 作水平投影至C ,以确定任何尺寸的相邻缺陷边缘之间最小容许间距。
3、相邻缺陷间距小于本图规定最小间距者,在测定时算作一段长度,即两缺陷长度加上其间距的合计值,并作为一个缺陷评定。
38mm 有限焊高的极限值适用于所有>28mm 有效提高。
图3.2.1 I 级焊缝(气孔及熔合型缺陷的限度)RT 标准3.2.1 对于I 级焊缝:任何最大尺寸≥2.0mm 的气孔或熔合型缺陷都不应超过图4.2.1中E 线(被验有效焊高)对应于B 线(缺陷最大尺寸)上的数值。
任何上述气孔或熔合型缺陷至另一同样的缺陷的距离、至边缘或至翼—腹板交叉焊0 12 25 40 50 65 75 90 100 11538 32 252012 612最大 235缺陷的最大尺寸(6810 11B-mm )CmmE- 焊接尺寸(mm )缝趾或根部的距离都不得小于图4.2.1中的C 线上对应于所检查的缺陷尺寸的最小允许间距值。
.E -焊接尺寸(m m )Cmm最大20383225201260C —气孔或熔合型缺陷沿焊缝纵轴测定的最小间距(相邻缺陷以较大者为准)注:1、从E 作水平投影至B ,确定缺陷的最大容许尺寸(任何接头或焊缝尺寸)。
2、从E 作水平投影至C ,以确定任何尺寸的相邻缺陷边缘之间最小容许间距。
*位于里板边缘这一距离内的缺陷的最大尺寸应为3mm ,但3mm 的缺陷距板边应≥6.0mm 。
位于此距离内的尺寸<3mm 的各缺陷总长度应≤5mm ,而在其他位置,但间距小于2L 的要受此限制(L 为较大缺陷的长度),以及此种缺陷应算作一段长度,其中等于缺陷合计长度加间距,按本图作评定。
38mm 有效焊高的限值适用于所有>38mm 的有效焊高。
图3.2.2 II 级焊缝(气孔及熔合型缺陷的限度)RT 标准3.2.2、对于II 级焊缝:任何最大尺寸≥3.0mm 的气孔或熔合型缺陷都不应超过图4.2.2中E 线(被验有效焊高)对应于B 线(缺陷最大尺寸)上的数值;相邻缺陷间距都不得小于图4.2.2中的C线上对应于所检查的缺陷尺寸的最小允许间距值。
3.2.3 缺陷的最大尺寸岁<2mm,但各缺陷尺寸之和咋子任何25mm长度焊缝内>10mm时,应视为不合格,而不受4.2.1和4.2.2的限制。
3.3 焊缝内部超声波检验及检测工艺AWSD1.1M第六章(检验)规定执行。
3.3.1 对于I级焊缝。
应符合表4.3.1要求。
3.3.2 对于II级焊缝,应符合表4.3.2的要求。
表3.3.1 I级焊缝UT标准注:①B级和C级缺陷应为≥2L,L为较长缺陷的长度、但下列情况除外:当≥2个此类缺陷相隔不是最小2L,但各缺陷及其间距合计小于或等于B或C级规定的最大允许长度,侧此类缺陷应视为单个可接受的缺陷;②B级和C级缺陷距焊缝端部应≥2L,L为缺陷长度;③接头全焊透CJP双面坡口焊缝根部钝边区域以“扫查水平”测到缺陷如焊缝在图纸上标注为“受拉焊缝”或“I级焊缝”者,应采取AWSD1.1M中的6.26/6.5所述灵敏度高出4dB的指示(从指示额定值d中减去4dB)做评定;如果接头焊缝系背部清根至完好金属以清除钝边,并用MT证实钝边以清除;④对移动接头而留在屏上的指示,*焊缝厚度定义为两连接部件中较薄的公称厚度。
** 指声程距离而非材料厚度A级(大缺陷),任何这类指示应判为不合格(不考虑长度);B级(中等缺陷),任何>20mm的指示应判;为不合格;C级(小缺陷)在焊缝厚度中部一般范围内,任何>50mm的指示或缺陷位于焊缝厚度的顶部或底部1/4范围内>20mm的指示均应判为不合格;D级(细微缺陷),不论长度及所处焊缝位置,此类指示应判为合格表3.3.21 I级焊缝UT标准扫查水平注:①B级和C级缺陷应为≥2L,L为较长缺陷的长度、但下列情况除外:当≥2个此类缺陷相隔不是最小2L,但各缺陷及其间距合计小于或等于B或C级规定的最大允许长度,侧此类缺陷应视为单个可接受的缺陷;②B级和C级缺陷距焊缝端部应≥2L,L为缺陷长度;③接头全焊透(CJP)双面坡口焊缝根部钝边区域以“扫查水平”测到缺陷如焊缝在图纸上标注为“受拉焊缝”或“II级焊缝”者,应采取AWSD1.1M中的6.26/6.5所述灵敏度高出4dB的指示(从指示额定值d中减去4dB)做评定;如果接头焊缝系背部清根至完好金属以清除钝边,并用MT证实钝边以清除;则严禁应用本要求。
④气电焊焊缝:当以“扫查水平”探查的缺陷>50mm长度时,应考虑其为管状气孔,并应进一步用RT进行评定;⑤对移动接头而留在屏上的指示,* 焊缝厚度定义为两连接部件中较薄的公称厚度。
** 指声程距离而非材料厚度A 级(大缺陷),任何这类指示应判为不合格(不考虑长度);B 级(中等缺陷),任何>20mm 的指示应判为不合格;C 级(小缺陷)任何>50mm 的指示均应判为不合格;D 级(细微缺陷),不论长度及所处焊位置,此类指示应判为合格。
4、其他规定4.1焊缝内部检验用UT 或RT (主要是对接焊缝)方法进行检验,其检验部位、检验长度和数量应在图纸和技术文件中注明。
4.2、焊缝UT 、RT 、MT 、PT ,按表3.1/4.1/4.3.1/4.3.2规定评定。
4.3经无损探伤,如果发现有低于质量标准的焊缝缺陷时,应在缺陷的延伸方向上或可以不为补充RT 检查,补查的数量和部位是具体条件而定,但对于10m 长的焊缝补查的数量≥3张。
如果补查合格,侧缺陷可修补,如补查不合格,原则上该焊缝应铲除重焊,对重焊处必须在进行检查直至合格为止,但修补次数不超过3次。
若经3次返修尚未合格,要经技术部门和检验部门决定是否允许返修。
4.4对重要构件,发现下列情况者应进行钻孔检验: 4.4.1无法用超声波及射线进行检验时;扫查水平4.4.2对超声波及射线无损探伤结果需要进一步证实时;4.4.3如检验员发现其他现象如果需要进行钻孔检验时,应进行钻孔检验。