公差带分析基础上理论公差叠加分析
基础公差分析_20170606

当给定双向公差,品质数据分布中心 ( X ) 与规格中心 ( M ) 相一致时,用符号 Cp 表示。
当给定双向公差,品质数据分布中心 ( X ) 与规格中心 ( M ) 不一致时,即存在中心偏移量 (ε)时,
用符号 Cpk 表示。
T 2
2
CPK 6S
| M X | k CA T
程度。
偏离度k衡量了产品加工尺寸均值与公差中心的偏离度,在上表中设定偏移量为1.5σ PPM:上表中的PPM计算值都是考虑了尺寸均值与公差中心偏移了1.5σ距离。如果无偏移,则PPM会少很多;如果实际偏移大于1.5σ,PPM还会高;在实际的工序能力计算中,是按照实际偏移 量计算得到的。
WC和RSS比较
– 统计手法,假设名义值在大批量加工零件的尺寸中心值 均分根公差法基于这样一个假设
– 用于较多的零件或尺寸堆叠
理论:大多数的零部件在它们的
– 用于产量大的零件 – 尺寸环多于4个 – 每个环节的制程水平(Cp)相同
公差范围内呈正态概率分布,此 时由它们所构成的系统与各个零 部件线性相关,则系统的分布也 可以用一个正态分布或近似正态
简单来说,如果某个制造企业的生产业务流程为6西格玛水平:则一百万个产品中,有 3.4 个次品; 6个西格玛 意味着卓越的管理,强大的竞争力和忠诚的客户 5个西格玛=230失误/百万机会-意味着优秀的管理、很强的竞争力和比较忠诚的客户 4个西格玛= 6,210失误/百万机会-意味着较好的管理和运营能力,满意的客户 3个西格玛=66,800失误/百万机会-意味着平平常常的管理,缺乏竞争力 2个西格玛=308,000失误/百万机会-意味着企业资源每天都有三分之一的浪费 1个西格玛-每天有三分之二的事情做错的企业无法生存
两维公差_RSS_叠加法
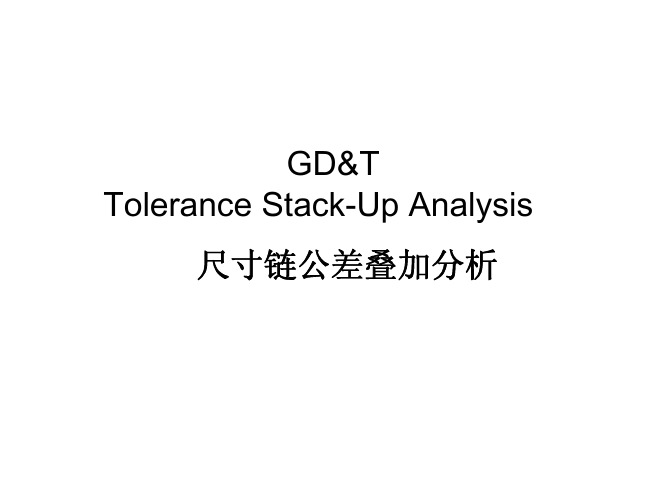
尺寸链公差叠加分析
There are two major types of Tolerance Analysis
1. Worst-case (arithmetic) straight stack or limit stack: 极限法 Worst-case tolerance analysis represent the largest (worstcase) possible variation 得出可能最大的误差
2. DEFINE THE DIRECTION OF THE STUDY. X, Y, OR Z ?
3. DEFINE THE PATH OF ENABLERS.
4. RETRIEVE THE ITEMS NECESSARY TO DO THE STUDY.
ITEMS NEEDED
1. GD&T DWGS FOR ALL PARTS RELATED TO STUDY.
Normal distribution: +/-3 σ = 6 σ = Tolerance range
正态分布
σ = range/6
Uniform +/-(square root3) σ = 2(Square Root3)σ
均匀分布
=Tolerance range
σ = range/2(square root)
零部件总成装配分析(1D ANALYSIS - RSS )
GETTING STARTED
1. DEFINE THE STUDY OBJECTIVE. EXAMPLES: a. ANALYSIS OF DTS. b. CALCULATION OF ASSEMBLY TOLERANCE. c. HOLE/PIN CLEARANCE STUDY.
基于6西格玛的乘用车尺寸链质量控制方法与应用

《装备维修技术》2021年第14期33基于6西格玛的乘用车尺寸链质量控制方法与应用何剑(恒大新能源汽车全球研究总院,上海201616)摘要:6西格玛理论是一套符合统计学原理且实用的质量控制理论,本文基于该理论,推导了不同尺寸链计算方法并比较其在最终质量控制中的优劣,并选择其中的均方值法作为实际乘用车尺寸链控制的基本算法,并以此指导实际工作。
关键词:六西格玛、尺寸链、极差法、均方值法、质量控制一、6西格玛理论介绍6西格玛:一种衡量质量水平的方法。
如果被评价为6个西格玛,则指3.4ppm 的缺陷率(约6个标准偏差)。
USL (Upper Specification Limit):公差值上限。
LSL (Lower specification Limit):公差值下限。
Cp:制造过程精密度,6西格玛质量体系的特定代号,是制造过程变化的范围与设计公差范围差异的情况,代表制作过程一致性能力的水平,其值越大则代表制造结果的落点越集中,而值越小则代表其落点越分散。
Cp 值越高,代表在一定的技术要求条件下,加工过程能力越强,精密度越高越高,如表1所示。
其中σ是标准偏差,标准偏差具体方法可以参考论文《统计公差分析方法概述》。
(公式1)表1等级Cp 值处理原则公差范围A+Cp≥1.67无缺点。
可考虑降低成本。
T=10σA 1.33≤Cp≤1.67制造能力非常棒,需要保持。
T=8~10σB 1.00≤Cp≤1.33制造能力需要提升。
T=6~8σC 0.67≤Cp≤1.00制造能力不足,亟需提升能力。
T=4~6σDCp≤0.67制造能力太差,全部重新设计。
T=2~4σCa:制造过程准确度,6西格玛质量体系的特定代号,是衡量制造过程落点与设计状态的偏差,偏差越明细,产品不良率就越大,如表2所示。
(公式2)表2等级Ca 值处理原则A |Ca|≤12.5%满足设计偏差要求,需要维持此制造水平。
B 12.5%≤|Ca|≤25%水平略有不足,需要改进。
公差叠加分析方法概述

2 极 值 法
极 值法 即极 限公 差 分析 法 ( r aeT lrne Wos C s o a c t e A a s ) 它建立 在零 件 1 0%互换 基 础 上 ,是 尺 寸 nl i , ys 0
链 计算 最简 单 的一 种 方 法 ,极 值 法 基 本 上是 应 用 于
师 和产 品设 计 师必须 规定 足够 严格 的公 差 , 以确 保做
到 规定公 差 范 围 内的产 品都 能 达到 预期 的功 能 , 格 严 的公 差是 为 了产 品有 一 致 的性 能 , 而 , 于严 格 的 然 过
卜挑 - s 1 :1 s, _ . _ s
[卫 [二口 [二 ]
Ab t a t h mp r n e o lr n e sa k—u n l ssi p e e td,i h c i oe a c t c s r c :T ei o t c ft ea c tc a o pa ayi s rsne n w i h t man t lr e sa k—u ay i t — wo n p a l ssmeh n o s—w rtc s d sait a si u tae .T e t o meh d r t d e d c mp r d wi r p r e d a a tb l i s d o a e a t t i l i l sr td s n sc l h w to sa e su i d a o a e t p o e is a d pa i t . n h t n ie Ke r s o ea c y wo d :tl rn e;sa k—u ay i ;w rtc s ;sait s o ts n—o —s u r s tc p a l ss o s a e tt i ;ro u n sc f q ae
公差分析

☆.產品設計變更的可行性評估. 產品設計變更的可行性評估.
設計變更後的組裝性的檢查,看部件的配合性. 設計變更後的組裝性的檢查,看部件的配合性.
BACK
公差分析--公差分析---做公差分析和方法和步驟 ★. 做公差分析方法和步驟
☆. 原始數據的收集. 原始數據的收集.
(規格,實際量測數據) 規格,實際量測數據)
☆.互換性的分類: 互換性的分類:
按照互換範圍的不同,可分為完全互換(絕對互換)和不完全互換(有限互換)。完全互換在機械製造中 按照互換範圍的不同,可分為完全互換(絕對互換)和不完全互換(有限互換)。完全互換在機械製造中 應用廣泛。但是,在單件生產的機器中(特重型、特高精度的儀器),往往採用不完全互換。這是因為在這種 情況下,完全互換將導致加工困難(甚至無法加工)或製造成本過高。為此,生產中往往把零、部件的精度適 當降低,以便於製造。然後再根據實測尺寸的大小,將製成的相配零、部件各分成若干組。使每組內尺寸差別 比較小。最後再把相應組的零、部件進行裝配。這樣既解決了零部件的加工困難,又保證了裝配的精度要求。
☆.Shielding Frame折彎角度從90設計變更性99的評估. Frame折彎角度從90設計變更性99的評估.
此設計變更的可行性評估,折彎角度變更後shielding Frame內空間能否容納高度增加後的電容,干涉 此設計變更的可行性評估,折彎角度變更後shielding Frame內空間能否容納高度增加後的電容,干涉 性的檢查。
☆.Shielding Frame折彎角度從90設計變更性99的評估. Frame折彎角度從90設計變更性99的評估.
BACK
公差分析--公差分析---結束 ★.結束
END
BACK
尺寸链及公差叠加分析

课程培训目标:•能够计算装配零件的最小和最大壁厚、间隙、或干涉,•能够创建几何公差或正负公差的尺寸链,分析公差叠加结果,•能够创建、分析复杂的公差叠加分析工具,包含几何公差,名义尺寸,实效条件尺寸,和正负公差,•能够分析通用装配条件的公差叠加分析,•能够分析浮动紧固件的公差叠加分析,如何定义螺栓,轴类,或孔类公差,•能够分析固定紧固件的公差叠加分析,如何定义螺栓,间隙孔,槽,凸缘,和整体尺寸的公差,以及螺纹孔的投影公差,•能够计算在不同的基准方案下的最大,最小间隙,•掌握一套逻辑的,系统的,数量化的公差分析方法,课程包含主要内容:课程参与者能够解决实际工作中面对的从简单到复杂的装配体的公差叠加分析。
培训中以理论讲授和实践练习相结合来分析尺寸公差和几何公差的叠加分析,比较分析不同的基准设置情况下的输出结果。
•尺寸链分析的起点•创建正负尺寸链•如何计算,如何确定影响贡献公差叠加结果的尺寸因素•如何分析:最差条件法Wost Case•哪些几何公差影响公差叠加结果?•均值分析:Mean•边界计算:GD&T,MMC,LMC和RFS材料条件修正情况下,•等边正负公差转换2.复杂装配体的正负尺寸公差叠加分析•计算方法•尺寸链分析工具制作•分析工具的应用•最大、最小间隙的分析结果输出•合格率的计算•Cpk与公差叠加分析•统计公差的分析及计算•6Sigma公差设计方法3.公差叠加的2D分析法–水平方向公差叠加和竖直方向的公差叠加分析•尺寸链分析的起点•创建正负尺寸链•最小、最大间隙的分析结果输出4.装配体的公差叠加分析•装配体中零件间的尺寸链如何建立•不同的尺寸布局方案的公差叠加分析•尺寸公差定义的装配体中公差叠加分析复杂性•最小,最大间隙结果输出•公差的优化•合格率的计算•与几何公差的比较5.浮动螺栓装配分析•几何公差控制的实效边界和补偿公差•内边界,外边界,均值边界•公差叠加分析中直径到半径的转化方法•轮廓度的叠加分析分解方法•基准浮动因素•几何公差浮动因素•复杂装配体的几何公差尺寸链建立方法•分析的标准化模板,6.固定螺丝装配分析•计算装配体的最大、最小间隙•投影公差的因素•正向设计固定螺栓装配总成•逆向设计固定螺栓装配总成•对于孔类、槽类、凸缘和轴类装配体的分析•确定所有的几何公差因素•独立特征和阵列特征的不同分析方法7.几何公差复杂装配体实例分析•对零件进行GD&T定义•装配设计方案•螺纹特征•组合公差控制框分析•投影公差•最差条件法分析的理论和实际误差•统计方法分析8.独立零件分析•位置度控制•基准框的公差叠加计算分析•MMC修正的基准特征•MMC修正的几何公差•轮廓度和平面度分析•MMC条件下的包容边界•考虑方向性的要求下创建MMC条件下包容边界•同步要求及独立要求•三角函数的公差叠加分析•组合位置度公差控制框分析9.统计公差分析及优化方法•统计学基础-概率分布曲线-标准差-Sigma水平-Cp,Cpk,Pp,Ppk•统计公差分析的理论•统计公差的应用RSS-正负公差的应用-几何公差的应用•统计公差和最差条件法应用目的,优缺点对比•统计公差的逻辑方法•统计公差的修正因数。
孔的公差带与轴的公差带相互交叠

孔的公差带与轴的公差带相互交叠以孔的公差带与轴的公差带相互交叠为题,我们将探讨孔与轴配合时的公差带的重要性和相互交叠的影响。
孔的公差带和轴的公差带是机械元件配合时的重要参数。
孔的公差带是指孔的尺寸允许的上下限范围,轴的公差带是指轴的尺寸允许的上下限范围。
当孔和轴配合时,公差带的相互交叠决定了配合的质量和性能。
公差带的相互交叠对配合的紧密程度有直接影响。
如果孔的公差带和轴的公差带相互交叠较小,配合就会较为紧密,能够提供更好的传力和定位精度。
相反,如果公差带的相互交叠较大,配合就会较为松散,容易产生游隙和摆动,影响机械元件的工作性能。
公差带的相互交叠还对配合的可靠性和耐久性有影响。
当公差带的相互交叠较小时,孔和轴的配合面积较大,接触面压力较高,能够提供更好的承载能力和抗疲劳性能,从而增加配合的可靠性和耐久性。
但是,如果公差带的相互交叠过小,可能会导致装配困难和使用寿命的缩短。
公差带的相互交叠还对配合的拆卸和维修产生影响。
如果公差带的相互交叠过大,孔和轴之间的间隙会较大,拆卸和维修时会比较容易,但是可能会导致配合的精度降低。
相反,如果公差带的相互交叠过小,孔和轴之间的间隙会较小,拆卸和维修时可能会比较困难。
在实际应用中,为了满足不同的配合要求,可以根据机械元件的功能和使用条件选择合适的公差带。
一般情况下,传动部件和定位部件要求配合较紧密,需要选择较小的公差带;而连接部件和调整部件则要求拆卸和维修方便,需要选择较大的公差带。
总结起来,孔的公差带与轴的公差带的相互交叠对配合的紧密程度、可靠性、耐久性、拆卸和维修等方面都有影响。
在机械设计和制造中,合理选择公差带的相互交叠是保证机械元件配合质量和性能的重要因素。
公差分析基础理论

公差分析基础理论公差分析是产品设计与制造过程中的重要环节之一,通过对零部件尺寸与形位公差的合理分配和控制,确保产品能够在规定的公差范围内满足设计要求,保证产品质量的稳定性和可靠性。
公差分析的基础理论主要包括公差、公差堆积、公差链等。
1.公差的概念与种类公差是描述零部件尺寸与形位误差的一个重要参数,是指零件尺寸或形状在一定范围内的允许偏差。
根据公差的不同性质,可以分为线性公差、形位公差和配合公差。
(1)线性公差:是指零部件尺寸的允许偏差范围。
一般用尺寸的上限(最大值)和下限(最小值)来表示,如直径10±0.05mm。
(2)形位公差:是指零部件几何形状、位置、方向的允许偏差范围。
形位公差分为位置公差、形状公差和方向公差等。
(3)配合公差:是指零部件之间的配合关系的允许偏差范围。
如传动轴与轴承配合时,要求轴与轴孔的尺寸公差和形位公差都要满足要求,以使轴与轴孔能够达到合适的配合。
2.公差分配原则公差分配是指在零部件与装配件之间合理分配公差,以满足产品性能要求。
公差分配的原则包括最大材料原则、最小材料原则、最大孔最小轴原则和最大间隙最小重合原则等。
(1)最大材料原则:将零件尺寸的上限与装配件尺寸的下限相对应,以保证零件和装配件都能满足设计要求。
(2)最小材料原则:将零件尺寸的下限与装配件尺寸的上限相对应,以保证零件和装配件都能满足设计要求。
(3)最大孔最小轴原则:在配合公差分配时,以确保最大孔与最小轴间隙达到设计要求。
(4)最大间隙最小重合原则:在配合公差分配时,以确保最大间隙与最小重合满足设计要求。
3.公差堆积与公差链公差堆积是指在装配过程中,由于零部件尺寸与形位公差的叠加或堆积所引起的总公差。
公差堆积的结果可能是零部件与装配件的配合间隙大于或小于设计要求,从而影响产品的装配性能。
因此,公差堆积的分析是确保产品装配质量的重要一环。
公差链是指由多个零部件按照一定的装配次序组成的装配关系链。
每个零部件的公差都对最终产品质量产生影响,因此,需要通过公差链的分析,确定各个零部件的公差堆积情况,以确保产品装配尺寸要求的可靠性。
- 1、下载文档前请自行甄别文档内容的完整性,平台不提供额外的编辑、内容补充、找答案等附加服务。
- 2、"仅部分预览"的文档,不可在线预览部分如存在完整性等问题,可反馈申请退款(可完整预览的文档不适用该条件!)。
- 3、如文档侵犯您的权益,请联系客服反馈,我们会尽快为您处理(人工客服工作时间:9:00-18:30)。
公差带分析基础上的理论公差叠加分析E.E.林和H.-C.张德克萨斯理工大学工业工程学系拉伯克德州美国摘要在本文中,在一维,二维,三维空间中,尺寸公差叠加和形位公差叠加都是从理论上进行分析的。
在这项研究中的公差分析是建立在公差带分析的基础上。
制造误差分为两种基本类型:定位误差和加工误差。
本文对公差叠加的一般公式进行了探讨。
最后对一个三维几何公差叠层的仿真例子予以说明。
关键词:尺寸;公式化;几何;公差叠加;公差带1.介绍1.1本文研究目的本文的目的是如下:1.公差叠加分析常被用于一维方向上的尺寸公差,由此产生的最终公差始终是组件公差的总和[1]。
相对于几何公差,尺寸公差的分析和控制都比较完善[2]。
而几何公差叠加通常被忽略或被组件公差叠加所取代。
在本文中,尺寸公差和几何公差在一维,二维,三维空间中的情况都将被考虑。
2.数值表示是尺寸和公差的特性[3]。
HB Voelcker预测在未来十年中在几何形位公差领域的最重要进展之一将会是“一个或多个几何形位公差的公式化的方法将产生,一个生成的公式化将比目前的方法更普遍但应包含当前特殊情况下的尺寸链的描述。
这种公式化方法应该是在工科院校中传授,因为它会基于对基本的数学原理的小部分的运用[4]。
本文对于生成的几何形位公差的公式化方法做出贡献。
1.2公差叠加与误差叠加公差是允许尺寸的变动量,它是最大极限尺寸和最小极限尺寸之差[5]。
误差(的变化)是一个特征(几何元素,表面或线)偏离其基本尺寸或形状[6],因此公差是用于(标定,表达)对处理加工中的误差进行控制。
而叠加误差用于处理虚拟变量,在本文中,公差叠加的分析是基于误差的叠加分析,公差叠加和误差叠加的数学公式与公差变量和误差变量相吻合。
1.3公差独立性原则在误差和公差分析中,同时考虑尺寸公差和形位公差是复杂的。
国际标准委员会ISO / TC10/SC5“技术图纸,尺寸和公差”和ISO/TC3“极限与配合”在ISO8015表示,独立原则是基本公差原则。
它的含义如下:“图样上给定的尺寸公差与形位公差相互独立,除非有特别关系被指定如最大实体要求,最小实体要求或包容要求。
”本研究遵循公差独立原则。
1.4公差带蔡斯等人,考虑到在机械装配公差分析中的几何特征变化[7],将公差带视为特征变化的限制。
在这项研究中的公差分析建立在公差带分析的基础上,henzold讨论了各种公差带,这些公差带可归纳为典型的类型,如图 1所示。
图1.典型公差带.(a)一维,(b)二维,(c)三维公差带图2.公差带的投影关系公差带的大小通常是特征尺寸的10-3到10-5,在下面的数据中,为了说明,公差带被放大。
t表示公差值。
有三种典型的公差带:1.一维公差带2.二维公差带3.三维公差带类型1,类型2和3的尺寸公差带参考几何公差带。
在直角坐标系,三维公差带可以投射到二维公差带,二维公差带可以投射到到一维公差带,如图2所示。
大多数的公差带都是三维的,然而公差链和公差分析通常都是在二维或一维的环境中进行的。
1.5制造误差的分类K. Whybrew和G. A. Britton为以下加工中的八个项目归纳出二十七个加工误差源[4]:机床、刀具、夹具、工件、冷却液、操作者、环境条件、过程变量上述误差源的各个方面在精密制造过程中都值得具体研究,这些误差可以分为两大类:一类是随机的、不可预测和无法控制的,另一类是固有的、随时间变化或者能被控制的。
固有误差是代数相加,随机误差是算术相加,一个由此产生的误差可以由下列公式(1)计算: ))((12m 1∑==+Σ=Δn j j j i i i θβφα (1) 其中:Δ:合成误差αi(i=1,2,3……m ): 固有误差分量的权重。
Φi(i=1,2,3……m ): 固有误差分量。
βi(i=1,2,3……m ): 随机误差分量的权重。
θi(i=1,2,3……m ): 随机误差分量。
βi 的值取决于随机误差分量的分布状况和由此产生的误差的几何关系。
还有许多工作需要建立公式的权重和误差分量。
然而,在这项研究中探索具体的定位误差和加工误差来源是不必要的。
在这项研究中,所有类型的误差源进行分类根据自己的定位功能和在线部分的加工功能的几何位置的影响。
因此,有两种类型误差,是直接关系到零件精度:1.定位误差:实际基准特征对理想基准特征在位置上允许的变动量。
定位和夹紧工件后已设置误差保持不变,除非工件从夹具中移除。
因此,在每一个设置之内定位误差都是确定。
2.加工误差:实际加工特征对理想加工特征在位置上允许的变化量。
加工误差是随机误差。
定位误差和加工误差都是系统误差和随机误差的结果2.尺寸公差叠加如图1所示,尺寸的公差带是严格一维的,因此生成的的尺寸公差叠加是相对简单的。
假设在一个空间中,由此产生的尺寸与元件尺寸的关系如下: ),,,,,,,(212,121n m l z z z y y y x x x f d = (2) 其中:d : 合成尺寸x i (i=1,2,3......l ):组件在X 坐标上的尺寸y i (i=1,2,3......l ):组件在X 坐标上的尺寸z i (i=1,2,3......l ):组件在X 坐标上的尺寸从理论上说,在最坏的情况下:∑∑∑===Δ∂∂+Δ∂∂+Δ∂∂=Δn k k k m j j j l i i i z z f y y f x x f d 111 (3)其中:Δd :合成尺寸的变化量x i ,y j ,z k :组件尺寸的变化量在数理统计的情况下:∑∑∑===Δ∂∂+Δ∂∂+Δ∂∂=Δn k k k l i m j j j i i z z f y y f x x f d 12121122])()()([ (4)在下面的文本,只有最坏的情况下被处理,统计情况和最坏情况可以用来得出在定性分析中的类似结论。
例如:在一个平面上的三个孔的三维关系如图3所示。
为简化分析水平尺寸被省略。
图3.一个平面上的三个孔的尺寸关系加工步骤和加工要求:第一步,将平面A 作为加工基准面钻孔1,孔1到平面A 的垂直尺寸是a 。
第二步,将平面A 和孔1作为基准钻孔2,孔2到平面A 的垂直尺寸是b 。
孔1与孔2的连线与水平线之间的角度为θ。
第三步,将平面A 作为基准钻孔3,孔3到平面A 的垂直尺寸是b'。
由此产生的尺寸为尺寸C 和C'。
对于尺寸C',它的尺寸链如图4所示:c'= b'-a (5)图4. C'的尺寸链在最坏的情况下: ''''''ΔΔΔ∂∂Δ∂∂Δb a b b c a a c c +=+= (6)C'的尺寸链是一维的,它也是尺寸链通常的状况。
在一维的状况下,可变的公差叠加量独立于组件的尺寸值。
,对于尺寸C ,有一个如图5所示的尺寸链。
θsin -a b c = (7)图5.C 的尺寸链在最坏的情况下: Δθθsin θcos )-(Δθsin 1Δθsin 1Δθ∂θ∂Δ∂∂Δ∂∂Δ2a b b a c b b c a a c c ++=++=(8) C 的尺寸链是二维的,从公式(6)可以看出,二维公差叠加不仅独立于组件的尺寸公差而且还独立于组件的基本尺寸。
尺寸公差叠加分析通常用公差图来表示。
对于回转体零件来说,每个工件的单一图表都足以控制沿工件轴的公差,所以没有可能发生径向的公差叠加。
对于棱柱形零件,为了控制公差叠加每个工件至少要给出两个尺寸和三个图表。
这些图表在一般情况下是不独立的,因为一些表面的公差可能出现在多个图表中。
图表通过共同的表面联系在一起[8]。
3.形位公差叠加3.1一维形位公差叠加分析一维形位公差叠加分析应用于组件公差类型相同与基本尺寸不影响公差叠加的情况。
作为一个例子;图表6给出了一个有五个相同平行槽的零件.平面A 、B 、C 、D 、E 分别被设置为加工平面B 、C 、D 、E 、F 的基准平面,如图6所示。
图6.一维形位公差叠加分析以下是用于公差叠加分析的表示法:C B A M M ,,=Γ 定位平面相对于理想垂直面的平行度,也称为定位误差 C B A M M ,,=λ 加工平面相对于理想垂直面的平行度,也称为加工误差 C B A MN MN ,,=Τ 平面M 与平面N 的平行度在图6中平行度公差叠加可以简述如下:B A AB λ+Γ=Τ (9)C B B A CB AB AC λλλ++Γ+Γ=+Γ+Τ=Τ (10)D C B C B A DC AC AD λλλλ+++Γ+Γ+Γ=+Γ+Τ=Τ (11)E C C B D C B A ED AD AE λλλλλ++++Γ+Γ+Γ+Γ=+Γ+Τ=Τ (12)F E D C B E D C B A FE AE AF λλλλλλ+++++Γ+Γ+Γ+Γ+Γ+Γ+Τ=Τ (13)显然,在一维情况下,由此产生的公差始终是等于组件公差的总和。
编号几何公差的情况的种类是有限的。
一维几何公差叠加的一些典型案例的公差带分布图如图7所示。
图6情况属于图7中的(a)情况。
图7.一维公差叠加的公差带分布图在图6中的零件的加工方法是将平面A 作为加工的基准面并且以同样的基准加工平面A 、B 、C 、D 、E 、F 。
这中加工方法在数控机床中很常见。
在这种情况下,调刀基准、设计基准和定位基准是同一平面-A ,因此没有误差叠加。
误差关系如下:()F E D C B N A M N M MN ,,,,,,==+Γ=Τλ (14) 3.2二维几何公差叠加分析图8显示出了平面B 的公差带的二维视图。
图8.零件面B 的二维公差叠带图9.平面B 平移的影响从图8可以看到,公差带表示出了零件的两个可能的最大变动量:大小为 B Δ的水平的平行移动和大小为θ的转角。
假设平面B 被作为加工基准面来加工平面D 和平面C 并且平面B 的误差带等于它的公差带。
平面D 的误差通常认为与平面B 的平移变化量相等(如图9所示):B D Δ=Δ (15) 平面B 的平移对平面C 的误差没有影响,平面B 的误差对平面C 的影响通过转角θ来体现,如图10所示。
图10.面B 转动的影响从图10可知:13tan L L C B Δ≈Δ≈θ (16) B C L L Δ=Δ31 (17)然而,有两个问题:1. 在这里θ是否是最大的旋转角度?2. 如果L 3≠L 3'公式14是否仍然正确?对于第一个问题答案是否定的。
一个实际的特征可能大于或者小于转角θ此外,在实际的定位和夹紧过程中,其他定位平面和夹紧面都可能影响旋转角度。
然于,对于理论分析,θ可以充分表示旋转角度的平均值。
对于第二个问题,如果L 3≠L 3',公式14应该改为: B c L L Δ=Δ3'3 (18)也就是说,它也受到旋转角度θ的影响。