沸腾炉工作原理
沸腾炉烘炉方案
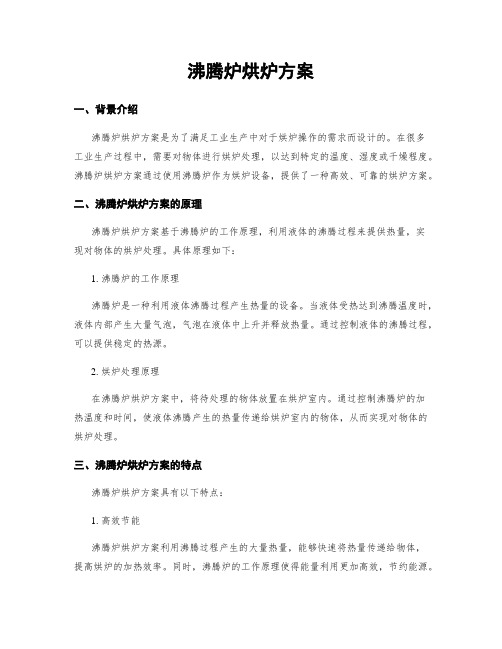
沸腾炉烘炉方案一、背景介绍沸腾炉烘炉方案是为了满足工业生产中对于烘炉操作的需求而设计的。
在很多工业生产过程中,需要对物体进行烘炉处理,以达到特定的温度、湿度或干燥程度。
沸腾炉烘炉方案通过使用沸腾炉作为烘炉设备,提供了一种高效、可靠的烘炉方案。
二、沸腾炉烘炉方案的原理沸腾炉烘炉方案基于沸腾炉的工作原理,利用液体的沸腾过程来提供热量,实现对物体的烘炉处理。
具体原理如下:1. 沸腾炉的工作原理沸腾炉是一种利用液体沸腾过程产生热量的设备。
当液体受热达到沸腾温度时,液体内部产生大量气泡,气泡在液体中上升并释放热量。
通过控制液体的沸腾过程,可以提供稳定的热源。
2. 烘炉处理原理在沸腾炉烘炉方案中,将待处理的物体放置在烘炉室内。
通过控制沸腾炉的加热温度和时间,使液体沸腾产生的热量传递给烘炉室内的物体,从而实现对物体的烘炉处理。
三、沸腾炉烘炉方案的特点沸腾炉烘炉方案具有以下特点:1. 高效节能沸腾炉烘炉方案利用沸腾过程产生的大量热量,能够快速将热量传递给物体,提高烘炉的加热效率。
同时,沸腾炉的工作原理使得能量利用更加高效,节约能源。
2. 温度控制精准沸腾炉烘炉方案通过控制沸腾炉的加热温度和时间,可以实现对烘炉室内的温度精确控制。
这种精准的温度控制能够满足不同物体烘炉处理的要求。
3. 操作简便沸腾炉烘炉方案的操作相对简便。
只需要设置好沸腾炉的加热温度和时间,然后将待处理的物体放置在烘炉室内即可。
操作人员无需过多的技术培训,即可完成烘炉处理操作。
4. 适用范围广沸腾炉烘炉方案适用于各种不同材料和尺寸的物体烘炉处理。
无论是金属、塑料、陶瓷还是其他材料,无论是大型还是小型物体,都可以通过沸腾炉烘炉方案进行烘炉处理。
四、沸腾炉烘炉方案的应用场景沸腾炉烘炉方案在各个工业领域都有广泛的应用。
以下是一些典型的应用场景:1. 金属加工行业在金属加工行业中,常常需要对金属零件进行烘炉处理,以改变材料的性质或达到特定的工艺要求。
沸腾炉烘炉方案可以提供高效、精准的烘炉处理,满足金属加工行业对于烘炉操作的需求。
沸腾炉的运行操作

沸腾炉的运行操作一、沸腾炉的工作特点炉排上的煤粒受到来自炉排下方向上吹的风力,当此风力略大于煤粒的重力和摩擦阻力时,煤粒被吹起。
由于煤粒形状是不规则的,因此煤粒的受力也在不断变化。
如果风力调整得合适,可使煤粒在一定的高度内翻腾跳跃;风力过大时,煤粒将被吹走;若风力过小,煤粒在炉排上处于静止状态而不能浮起,因此风力过大或过小,都起不到沸腾的作用。
为了获得沸腾燃烧,须将煤粒直径控制在一定范围内,并根据煤粒大小将风速控制在一定范围内,这就是沸腾炉的工作特点。
二、沸腾炉的点火操作用木柴等引燃物将炉床上的炉料加温,使料层逐步达到正常运行时的温度,以保证连续送入炉膛的煤能够正常燃烧。
现将点火步骤简述如下:1.检查炉膛内部,应无结焦和杂物。
2.在炉排上铺一层炉渣,其粒度与燃煤相似,厚度约为300毫米(mm),然后放置引燃木柴,木柴直径小于100毫米(mm),长为500~700毫米(mm)。
用油棉纱等引火物点燃木柴,使炉内均匀预热。
3.关闭风道门,启动引风机,使炉膛产生负压。
4.启动鼓风机,稍开启送风门,使炭火层稍有跳动,但应注意风量的控制使炭火不要被炉渣掩埋,否则将导致炭火熄灭。
5.从炉门向炭火层均匀撒布烟煤屑,并逐渐增大风量,提高料层的温度。
6.随料层温度的升高,相应增加送风量。
当达到正常运行的“最小风速”时,可暂不增加送风量,用撒人烟煤屑的数量来控制炉温升高的速度。
7.当炉料温度在达到600~700℃(暗红色)之前,应使温度升得较快,同时增加风量使风速较快地超过“最小风速”,以免发生“低温结焦”。
料层温度达到600~700℃后,应尽量使温度平稳地上升,以免造成“高温结焦”。
当料层温度达到800~850℃时,即将炉门关闭,并开动给煤机按正常运行送入给煤量,监视燃烧情况,直至燃烧稳定即告点火成功。
三、沸腾炉的运行调整操作要使沸腾炉能正常运行,其关键在于正确调节沸腾层的送风量,控制风速、风箱静压和沸腾层的温度。
沸腾炉工作原理
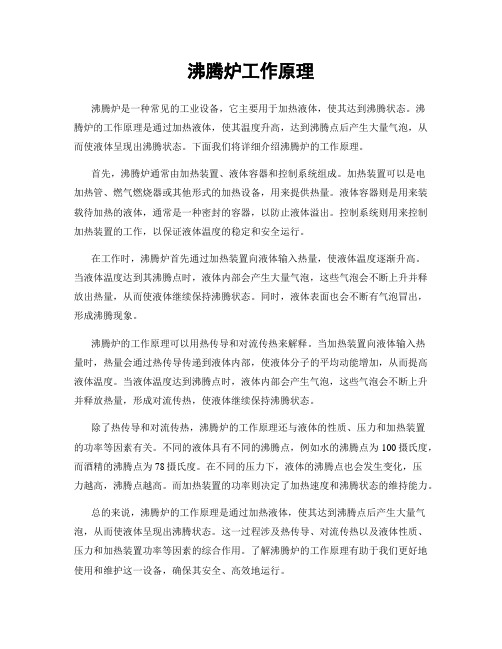
沸腾炉工作原理沸腾炉是一种常见的工业设备,它主要用于加热液体,使其达到沸腾状态。
沸腾炉的工作原理是通过加热液体,使其温度升高,达到沸腾点后产生大量气泡,从而使液体呈现出沸腾状态。
下面我们将详细介绍沸腾炉的工作原理。
首先,沸腾炉通常由加热装置、液体容器和控制系统组成。
加热装置可以是电加热管、燃气燃烧器或其他形式的加热设备,用来提供热量。
液体容器则是用来装载待加热的液体,通常是一种密封的容器,以防止液体溢出。
控制系统则用来控制加热装置的工作,以保证液体温度的稳定和安全运行。
在工作时,沸腾炉首先通过加热装置向液体输入热量,使液体温度逐渐升高。
当液体温度达到其沸腾点时,液体内部会产生大量气泡,这些气泡会不断上升并释放出热量,从而使液体继续保持沸腾状态。
同时,液体表面也会不断有气泡冒出,形成沸腾现象。
沸腾炉的工作原理可以用热传导和对流传热来解释。
当加热装置向液体输入热量时,热量会通过热传导传递到液体内部,使液体分子的平均动能增加,从而提高液体温度。
当液体温度达到沸腾点时,液体内部会产生气泡,这些气泡会不断上升并释放热量,形成对流传热,使液体继续保持沸腾状态。
除了热传导和对流传热,沸腾炉的工作原理还与液体的性质、压力和加热装置的功率等因素有关。
不同的液体具有不同的沸腾点,例如水的沸腾点为100摄氏度,而酒精的沸腾点为78摄氏度。
在不同的压力下,液体的沸腾点也会发生变化,压力越高,沸腾点越高。
而加热装置的功率则决定了加热速度和沸腾状态的维持能力。
总的来说,沸腾炉的工作原理是通过加热液体,使其达到沸腾点后产生大量气泡,从而使液体呈现出沸腾状态。
这一过程涉及热传导、对流传热以及液体性质、压力和加热装置功率等因素的综合作用。
了解沸腾炉的工作原理有助于我们更好地使用和维护这一设备,确保其安全、高效地运行。
硫酸工艺沸腾炉的工作原理

硫酸工艺沸腾炉的工作原理
硫酸工艺沸腾炉是一种常用于生产硫酸的反应设备。
其工作原理如下:
1. 原料制备:硫矿石或硫化物经过破碎、选矿等前处理步骤,得到粉末状的硫矿石或硫化物。
2. 进料和预热:将粉末状的硫矿石或硫化物加入到沸腾炉中,并通过加热的方式将其预热,使其达到适宜的反应温度。
3. 反应过程:在预热后的原料中注入浓硫酸以启动反应。
硫化物与浓硫酸发生反应,产生硫酸和硫二氧化物气体。
4. 吸收和脱气:通过特定的装置,将产生的硫二氧化物气体进行吸收,并与浓硫酸反应生成硫酸。
同时,通过脱气装置将空气中的杂质和余气排除,并保持反应过程的稳定。
5. 产品收集:反应生成的硫酸经过脱气、冷凝、过滤等步骤后,得到纯净的硫酸产品。
总的来说,硫酸工艺沸腾炉通过对硫矿石或硫化物与浓硫酸的反应,利用化学反应过程生成硫酸,并经过相应的处理步骤,最终得到高纯度的硫酸产品。
(冶金行业)节煤型高温沸腾炉的结构设计及应用

(冶金行业)节煤型高温沸腾炉的结构设计及应用节煤型高温沸腾炉的结构设计及应用合肥水泥研究设计院杨刚1高温沸腾炉工作原理沸腾炉是水泥厂烘干原料的主要热源,其燃烧方式介于层状燃烧和悬浮燃烧之间。
工作原理为:高压空气通过均风箱由壹次风的动压头变成均匀分布的静压头,从风帽上的微孔高速高压吹入炉内,使其沸腾床形成气垫层将粒径0~10mm、料层厚度300~500mm的煤粒全部吹起且上、下翻动。
料层由于高压气体增加了煤粒间的空隙膨胀而产生激烈运动,且在不停地翻腾、跳动中和空气混合,使原有300~500mm的料层飞腾高度达到800~1400mm。
此时,沸腾料层的燃料和含碳量为1~2%的灼热灰渣充分混合燃烧,温度壹般可达950℃高温,相当于壹个大蓄热池。
料层中0.5~8mm 的颗粒不易被气体带出燃烧室,能较长时间停留在沸腾料层中直到燃烬,然后由炉底冷渣管排出。
沸腾炉由于燃料具有较大的着火比表面积和在炉膛内的停留时间较长,所以兼有煤粉炉和层燃炉的燃烧特点。
沸腾炉膛中蓄热量大,颗粒之间以及颗粒和空气之间产生的相对运动十分激烈,加之其气体扩散速度快,可维持在1.05~1.1左右的很低的过量空气系数下强烈燃烧,而且不必预热,这就形成了强氧燃烧的条件,因此能使低热值劣质燃料完全燃烧,燃烧反应迅速。
沸腾层的传热系数较高,壹般可达220~350w/m3℃,沸腾段的容积热强度高达1.745×106w/m3,近于燃粉炉的10倍,链条炉的4~5倍。
因而被普遍认为是壹种热效率较高的燃烧方式。
节煤型高温沸腾炉既具有普通沸腾炉的热效率较高这壹特点,也从炉体结构、耐火材料、系统工艺设备配套及其自动控制等方面进行了改进,使沸腾炉的应用效果更为显著,不仅适用于>6000kcaγ/kg的优质烟煤、无烟煤,也可全部燃烧<3000kcaγ/kg的低热值燃料如煤矸石、炉渣等。
因而在数百家水泥厂烘干系统的应用中深受好评。
沸腾烘干系统工艺流程如图1。
沸腾炉初步设计方案

沸腾炉初步设计方案沸腾炉是一种常用的热交换设备,通常用于加热或冷却各种流体。
它的工作原理是通过将一定量的流体加热到沸点,使其产生沸腾状态,从而实现传热的目的。
在这篇文章中,将从沸腾炉的工作原理、设计参数、结构设计和安全措施等方面进行详细的介绍,并提出一个初步的设计方案。
沸腾炉的工作原理是利用流体在加热的过程中产生的沸腾现象来传热。
沸腾现象是指当流体受热至其饱和温度以上时,由于压力降低,使流体中的液体部分迅速蒸发形成气泡,并在液体表面聚集形成气泡层。
气泡层具有很高的传热系数,可以快速将热量传递到流体中,从而实现传热的目的。
设计沸腾炉需要考虑的参数包括流体的性质、流量、温度差以及所需的传热量等。
流体的性质决定了其饱和温度和传热系数,不同的流体传热特性也不同,因此在设计过程中需要根据实际情况进行合理选择。
流量是指流体在单位时间内通过沸腾炉的体积或质量,通常需要根据传热需求和设备的承载能力来确定。
温度差是指流体进出口之间的温度差异,通常越大传热效果越好,但也需要根据实际情况进行合理考虑。
传热量则取决于流体的质量、温度差以及传热系数等。
在沸腾炉的结构设计上,主要包括加热区、沸腾区和冷却区。
加热区通常采用电加热器或燃气加热器等方式将流体加热至饱和温度以上,使其进入沸腾区。
沸腾区通常由一组管道和加热板组成,通过液体与加热板的接触来实现沸腾现象。
冷却区则通过冷却介质的流动将加热后的流体冷却至所需温度。
为了确保沸腾炉的安全运行,需要采取一系列的安全措施。
首先,在设计上要确保设备具有足够的强度和稳定性,以承受内部压力和温度的变化。
其次,在操作过程中需要严格控制流体的流量和温度,避免过载运行和温度过高等状况。
同时,设备的维护保养也十分重要,定期检查和清洗设备,确保其正常运行。
基于以上原理和要求,初步的沸腾炉设计方案如下:1.设备结构:沸腾炉采用立式设计,由加热区、沸腾区和冷却区组成,整体结构简单紧凑。
2.材料选择:设备主要采用不锈钢材料,具有良好的耐腐蚀性和高强度,确保设备的长期稳定运行。
图所示为硫酸生产中的沸腾炉

沸腾炉漏料:由于炉体密封不严或物料流动性差,导致物料泄漏
沸腾炉结垢:由于物料中的杂质或水分过多,导致炉内结垢
故障诊断:通过观察、听、闻、摸等方法,确定故障部位和原因
排除故障:根据诊断结果,采取相应的:沸腾炉通过加热炉料,使炉料中的硫磺和空气在高温下反应,生成二氧化硫气体。
促进化学反应:沸腾炉中的高温环境有利于硫磺和空气中的氧发生化学反应,生成二氧化硫气体。
分离固体产物:沸腾炉中的高温环境可以使炉料中的固体产物与气体产物分离,方便后续处理。
提高生产效率:沸腾炉的高温环境可以加快化学反应速度,提高硫酸生产效率。
通知相关部门进行检修和处理
汇报人:
感谢您的观看
确认工艺流程:确认硫酸生产工艺流程,熟悉操作步骤和注意事项。
严格控制温度和压力:沸腾炉的操作过程中,需要严格控制温度和压力,确保生产安全和产品质量。
保持炉内清洁:定期清理炉内杂物,保持炉内清洁,防止杂物对生产过程产生不良影响。
避免过度投料:在投料过程中,要避免过度投料,以免对炉内产生过大的压力和温度波动。
沸腾炉与配料系统:配料系统向沸腾炉提供原料,确保生产顺利进行
沸腾炉与余热回收系统:余热回收系统利用沸腾炉的余热,提高能源利用效率
沸腾炉与酸冷系统:酸冷系统对沸腾炉产生的硫酸进行冷却,保证产品质量
沸腾炉与尾气处理系统:尾气处理系统对沸腾炉产生的尾气进行处理,保护环境
沸腾炉的工作原理
沸腾炉的构造:包括炉体、燃烧器、通风装置等部分
沸腾炉的工作原理:燃料在燃烧器中燃烧产生高温气体,使炉内物料呈沸腾状态,实现传热和化学反应
沸腾炉的特点:具有高效传热、高气速、高生产强度等优点
沸腾炉工作原理

沸腾炉工作原理
沸腾炉是一种常见的加热设备,其工作原理涉及到热传导、对流和相变等热学
知识。
下面我们将详细介绍沸腾炉的工作原理。
首先,沸腾炉内部的加热元件(通常是电加热管或燃气燃烧器)会将能量转化
为热能,传递给沸腾炉内的液体。
当液体温度升高到一定程度时,液体表面开始产生气泡,这是因为液体内部的部分分子获得了足够的能量,能够克服表面张力,从而脱离液体表面形成气泡。
随着加热的继续,液体表面上的气泡不断增多,并迅速膨胀,最终破裂释放出
大量气体,这一过程就是沸腾。
在沸腾的过程中,液体内部的热量通过对流不断传递到液体表面,从而保持液体的温度稳定。
此外,沸腾炉的工作原理还涉及到相变过程。
在沸腾过程中,液体表面的温度
保持在饱和温度,这是因为液体内部的热量主要用于将液体转化为气体,而不是提高液体的温度。
因此,沸腾炉在工作时能够保持稳定的温度输出。
总的来说,沸腾炉的工作原理是通过加热元件向液体传递热能,使液体表面产
生气泡并进行沸腾,通过对流和相变过程将热量传递到液体表面,从而实现加热的效果。
在实际应用中,沸腾炉的工作原理对于加热、蒸发和沸腾等过程具有重要意义,能够满足各种工业生产和生活领域的加热需求。
同时,了解沸腾炉的工作原理也有助于我们合理使用和维护沸腾炉,确保其安全、高效地运行。
综上所述,沸腾炉的工作原理涉及热传导、对流和相变等热学知识,通过加热
元件向液体传递热能,使液体表面产生气泡并进行沸腾,从而实现加热的效果。
深入了解沸腾炉的工作原理有助于我们更好地应用和维护这一常见的加热设备。
- 1、下载文档前请自行甄别文档内容的完整性,平台不提供额外的编辑、内容补充、找答案等附加服务。
- 2、"仅部分预览"的文档,不可在线预览部分如存在完整性等问题,可反馈申请退款(可完整预览的文档不适用该条件!)。
- 3、如文档侵犯您的权益,请联系客服反馈,我们会尽快为您处理(人工客服工作时间:9:00-18:30)。
脱硫石膏沸腾炉工作原理1 脱硫石膏沸腾炉工作原理沸腾炉就是脱硫石膏烘干得主要热源,其燃烧方式介于层状燃烧与悬浮燃烧之间.工作原理为:高压空气通过均风箱由一次风得动压头变成均匀分布得静压头,从风帽上得微孔高速高压吹入炉内,使其沸腾床形成气垫层将粒径0~10mm、料层厚度300~500mm得煤粒全部吹起并上、下翻动。
料层由于高压气体增加了煤粒间得空隙膨胀而产生激烈运动,并在不停地翻腾、跳动中与空气混合,使原有300~500m m得料层飞腾高度达到800~1400mm。
此时,沸腾料层得燃料与含碳量为1~2%得灼热灰渣充分混合燃烧,温度一般可达950℃高温,相当于一个大蓄热池.料层中0、5~8mm得颗粒不易被气体带出燃烧室,能较长时间停留在沸腾料层中直到燃烬,然后由炉底冷渣管排出.沸腾炉由于燃料具有较大得着火比表面积与在炉膛内得停留时间较长,所以兼有煤粉炉与层燃炉得燃烧特点.沸腾炉膛中蓄热量大,颗粒之间以及颗粒与空气之间产生得相对运动十分激烈,加之其气体扩散速度快,可维持在1、05~1、1左右得很低得过量空气系数下强烈燃烧,而且不必预热,这就形成了强氧燃烧得条件,因此能使低热值劣质燃料完全燃烧,燃烧反应迅速.ﻫ沸腾层得传热系数较高,一般可达220~350w/m3℃,沸腾段得容积热强度高达1、745×106w/ m3,近于燃粉炉得10倍,链条炉得4~5倍。
因而被普遍认为就是一种热效率较高得燃烧方式。
脱硫石膏烘干沸腾炉既具有普通沸腾炉得热效率较高这一特点,也从炉体结构、耐火材料、系统工艺设备配套及其自动控制等方面进行了改进,使沸腾炉得应用效果更为显著,不仅适用于>6000kcaγ/kg得优质烟煤、无烟煤,也可全部燃烧 <3000kcaγ/kg得低热值燃料如煤矸石、炉渣等。
因而在脱硫石膏烘干系统得应用中深受好评。
ﻫ沸腾烘干系统工艺流程如图1。
2 脱硫石膏干燥沸腾炉结构设计与效果ﻫ2、1脱硫石膏干燥沸腾炉结构ﻫ脱硫石膏干燥沸腾炉结构由炉床、炉膛、混合室等三部分组成,如图2所示.ﻫ图中,炉床部分包括均风箱、布风板、风帽、出渣孔等;炉膛部分包括垂直段、扩散段、悬浮段及炉门;混合室与烘干机相连,设有排灰门、人孔门、热电偶等. ﻫ脱硫石膏干燥沸腾炉得设计,从结构上充分满足了流体力学与热力学原理.根据脱硫石膏干燥得特点,沸腾炉得燃料采用从炉门上方呈正负压分界处喂入得新结构,可促使燃料与热渣均匀混合及充分燃烧.也有利于热烟气在扩散段释放并由风机抽入混合室.为减少热气在运动过程中得阻力,其过渡段采用收口式平滑结构设计,便于热风顺利、迅速地进入烘干机参与热交换。
其挡火墙采用堆积型结构,有利于热渣与飞灰回到垂直段或混合室积灰斗,同时可为老厂烘干系统因场地小而方便使用异型沸腾炉提供条件,其长度与高度也可随厂房得局限因地制宜地加以调整。
沸腾炉得炉门设为两个,分别作瞧火、调火与检修使用,用于检修得炉门可方便耐火砖活砌或出现结渣时打开清理,避免操作人员在高温下进入炉内清理结渣,即方便又安全。
小炉床得设计保证了节煤这一基本要素,其炉床面积比一般沸腾炉减小1/3,单位时间加煤量减小30%,因此节煤效果明显、操作方便.脱硫石膏干燥沸腾炉具有以下特点:ﻫ(1) 燃料在沸腾炉中呈沸腾状态,燃烧层正常燃烧得温度为850~1100℃。
而风动气垫层温度较低,一般在200~300℃,但因料层很厚,沸腾床能长时间闷火,蓄热能量大;ﻫ(2) 由于鼓入高压空气,使炉内空气过量系数高,形成强氧燃烧,燃烧与燃尽条件好;(3) 沸腾层内受热面积大,传热强烈,易于燃烧。
因此炉膛内单位容积热强度高;(4)用煤量少.垂直段仅以5%得煤燃烧,其余95%均为热渣,节煤效果好;ﻫ(5)炉床面积小,使燃料得沸腾高度及风压、风速增加,司炉工操作更容易,对异常情况特别就是结渣得早期处理更及时;ﻫ(6) 设计采用较厚得保温层,可减少炉体热散失,炉温变化较小,有利于延长炉体得使用寿命;(7)操作系统采用热工仪表与微机连锁监控,温度、煤耗、烟气粉尘浓度、NO与S O2含量等主要参数均通过监控、记录、显示,为操作者提供管理依据。
燃尽得灰渣可收集利用作为高活性水泥混合材.通过上述改进设计得节煤型沸腾炉,有效提高了普通沸腾炉得热效率,对燃料热值得要求更宽,选材范围更大,较之其她燃烧方式更具明显得优势。
几种燃烧方式得技术经济指标对比见表1.1、2 设备主要参数得确定ﻫ炉床布风板有效面积F布(m2)得计算:ﻫ布 = (1)式中:B计––计算小时耗煤量,kg/h;ﻫ LO––理论燃烧空气消耗量,m3 标煤/kg;a沸––沸腾区过量空气系数,取1、15;ﻫ V垂––垂直段底部冷态空气流速取0、8m/s。
风帽得总通风面积Σf帽为单个风帽通风面积f帽得总与。
单个风帽通风面积f帽得计算如式2:ﻫΣf 帽= …………(2)ﻫ式中:V帽––通过风帽小孔得风速,m/s;ﻫ帽––每个风帽小孔得通风面积,m2。
炉膛扩散段截面积F扩(m2)得计算:ﻫ F扩=…………(3)式中:Vg—燃烧生成得烟气量,m3标煤/kg;ﻫa扩––扩散段过剩空气系数,取1、3;ﻫ V扩––扩散段冷态风速m/s,取0、45m/s.悬浮段截面积F悬(m2)得计算:ﻫF悬= (4)式中:a悬––悬浮段过剩空气系数,取1、5;ﻫV悬––悬浮段冷态风速,取0、45m/s.ﻫ混合室高度H(m)与长度L(m)确定:ﻫH= ........................(5)ﻫL = (6)W ––尘粒得沉降速度m/s,取1、33;ﻫ V ––烟气流速m/s,取1、5.ﻫ混合室得横截面积F(m)得计算:ﻫ F = (7)式中:Q烟––烟气流量(m3/h)ﻫ能达到沸腾燃烧状态所需得鼓风量Q (m3/h)与风压P (PammH2O)得计算:Q = n.f 帽.V帽.K............(8)ﻫ P =9、8 K (P风 + P渣)× (9)式中:n ––炉床上实际风帽个数P风––鼓风系统阻力:风管阻力取196 Pa(20mmH2O),风帽阻力取1766Pa(180mmH2O);渣––沸腾炉床得渣层阻力:渣厚500mm时取3924 Pa(400mmH2O);P地––当地大气压,mpa;K ––储备系数,取1、3;在选择风机时,可根据计算求得得风量与风压,适当增加20%确定其规格型号。
2、3最佳沸腾速度得选择ﻫ要使燃料在炉内保持稳定得沸腾状态,只有选择在临界风速与带出风速之间得沸腾操作速度,而沸腾临界风速与带出风速取决于燃料得特性与颗粒分布。
通常,燃煤得粒度分布较宽,多为0~10mm,平均粒径3mm左右。
为使大颗粒能被吹起与考虑低负荷时得正常沸腾,应选用较大得沸腾速度.然而,要尽量减少细颗粒不被吹走,沸腾速度又不益取得过大。
现有得燃用10mm 以下煤屑得沸腾炉,临界速度在1m/s左右,带出速度大约就是临界速度得6~7倍,而正常沸腾风速为临界风速得2~3倍.气流速度有冷态值与热态值之分,实践证明,在同样得料层厚度与良好得沸腾状态下,冷态值要求比热态值高,两者得最小风量大约相差60~80%。
因此,根据沸腾炉实现稳定沸腾状态得诸多因素,应视炉床面积选择临界风速0、7~1、1m/s为宜,炉床面积较大,取值相对偏高。
3 操作与应用ﻫ脱硫石膏干燥沸腾炉作为脱硫石膏干燥烘干系统得热源,其操作技术要求较高,特别就是在新炉调试及试运转过程中,若操作不熟悉或没有掌握正确得操作方法,例如用风、加煤不当,很容易出现低温结小渣,高温结大块与熄火、点火时间过长等现象。
因此,既要求加强司炉工得操作技术尤其就是在调试与试运转过程得培训,掌握操作方法,也需根据工艺及设备等生产实际情况因地制宜得确定操作参数,制定操作规程.着重应注意以下几个操作环节.1 快速点火过程脱硫石膏干燥沸腾炉由于炉床面积小,保温性能好,因此点火较一般沸腾炉容易。
首先将沸腾炉内填放部分中粗粒黄砂或沸腾炉渣,加入少量碎煤拌与均匀,填于炉床,填料厚度约300~400mm,用高压风机吹起几次,用大小基本均匀得木材引火,并在其燃至木炭状时加入少量碎煤,同时迅速以大风量供风,继而改用小风适度吹养。
如此反复2~3次,直到沸腾炉渣逐步呈红色后再加少量碎煤,用中等风量吹至其完全沸腾燃烧,打开引风机即进入正常燃烧状态。
ﻫ3、2稳定燃烧过程正常燃烧过程中,可依据炉内火焰得颜色来决定就是否调整加风或加煤量。
炉内得炉渣高度应保持在550~650mm,风压应稳定在700~800mmH2O,炉火呈粉红色,热风温度为750~900℃。
若炉内热渣呈暗红色,说明温度偏低,需加入燃料,热渣呈白色时,则温度过高,需加大风量并加入冷渣降温。
3、3 结渣得处理结渣类型分为低温结渣与高温结渣,其处理方法各不相同。
低温结渣,在点火或闷火时易出现低温结小块现象,此时应首先急吹几次,将其冲散,然后人工清除较大块结渣,加少量煤养火后,继续燃烧;高温结渣时,如出现炉床面不沸腾或多处小孔喷火,表明已形成高温结大块,此时先停止加煤,然后加大风量吹冷结渣,打开下层炉门,将大块炉渣清除,填渣后利用炉温重新起火。
ﻫ3、4 闷火与起火闷火前首先关闭喂煤机,高压风机送风吹动炉内热渣翻腾,同时观察炉膛渣粒表层或煤粒得颜色.若呈白色状应继续吹风至冷,使其变为暗红色时停止高压风机、关闭调风阀,保持炉渣高度约500~600mm,最后关闭引风机。
ﻫ起火前先加少量煤,再开高压风机,用大风将炉渣完全沸腾后,立即换小风喷吹,若沸腾渣呈暗黑色,即加大喂煤量,同时用大、小风量交替喷吹。
也可用交替开闭高压风机风阀得方法来控制起火状态,开则吹风,闭则养火,这样反复几次,至到炉膛内得炉渣呈红色,即转入正常燃烧阶段。
正常运行中,脱硫石膏干燥沸腾炉烘干系统得风温、风压、风量等操作参数随烘干机得规格不同大致如表2。
由于沸腾炉能够强化燃烧,其燃烧热负荷与传热系数较高,因而,根据热力学与流体力学原理将其炉膛尺寸大大缩减,可达到大幅度降低煤耗得目得。
实践证明,脱硫石膏干燥沸腾炉炉床面积即使减小1/3,仍可达到节煤50%,增产100%得显著效果,煤得燃尽率及其热效率也比普通沸腾炉高得多。
ﻫ本文所述得结构设计及其计算,为这一效果奠定了良好得基础,具有设计得新颖性与计算得合理性。
脱硫石膏干燥沸腾炉作为脱硫石膏烘干得热源,其使用效果已在国内外数百台生产应用中得到证实。
其操作方法也随各厂得应用条件不同而不断丰富与完善,本文仅对其一些普遍得现象进行描述。
值得参考应用。