第2章超精密切削与金刚石刀具汇总
论述金刚石刀具超精密切削的机理丶条件和应用范围

金刚石刀具超精密切削的机理丶条件和应用范围
金刚石刀具是超精密切削中常用的刀具材料,其切削机理、条件和应用范围如下:
1.切削机理:
⏹金刚石刀具的切削刃非常锋利,在切削过程中能够实现“切入式切削”,
使切削力大大减小。
⏹金刚石的硬度极高,切削时不易被工件材料磨损,能够保持良好的切削刃
形状。
⏹金刚石的传热性能极佳,能够快速地将切削热量传递出去,从而降低切削
温度,减少热损伤。
1.切削条件:
⏹刀具刃口半径:为了实现超精密切削,需要将刀具的刃口半径减小到亚微
米级,以提高切削的精度和表面粗糙度。
⏹切削用量:为了减小切削力和热量,需要选择较小的切削深度和进给速度,
以提高切削效率。
⏹工件材料:金刚石刀具适用于加工各种硬材料,如淬火钢、硬质合金等。
但是,对于一些韧性较大的材料,需要进行预处理或选择其他刀具材料。
1.应用范围:
⏹金刚石刀具广泛应用于超精密切削领域,如光学零件、轴承、硬盘磁头、IC
芯片等高精度、高表面质量的零件加工。
⏹在加工过程中,金刚石刀具还可以用于制作各种微细结构,如微孔、微槽
等。
综上所述,金刚石刀具的超精密切削需要满足一定的条件,并具有广泛的应用范围。
超精密加工中的金刚石刀具及刀具磨损分析

理论与实践经济与社会发展研究超精密加工中的金刚石刀具及刀具磨损分析齐齐哈尔工程学院 武晓迪摘要:各种超精密加工应用中将金刚石用作切削工具已经成为现实,然而其目的与意义并没有得到实质性分析。
据此,本文对超精密加工中应用金刚石作为切削刀具的现实意义进行分析。
关键词:超精密加工;切削工具;刀具磨损一、技术背景分析使用高速超精密车床加工玻璃和硅等脆性材料时,当所施加的切削深度低于临界值时,则认为其处于延性模式,并且可以容易地加工而不会形成裂纹。
因此,对于这些材料的延性至脆性转变具有重要意义,在这些材料中,临界切削深度的大小取决于零件的特性而变化。
通常,单晶硅经常用在微机电系统(MEMS)中,在该系统中,最终将材料加工成优质产品,并进行超精密研磨和抛光操作。
尽管硅材料的行为在室温下很脆,但建议使用金刚石车削工具以延性模式加工硅。
这减少了由陶瓷材料的脆性断裂引起的损坏,并提高了最终零件的生产率。
使用金刚石工具对铜,铝和镍等有色金属材料进行高速加工,以评估工具的磨损,切削力和表面光洁度。
实验针对不同的切割速度进行,例如较低的150m/min的速度和较高的4500m/min的速度。
在较低的切削速度下观察到的刀具磨损率大于较高的切削速度。
这可能是由于以较高的速度减少了刀具与工件啮合的时间。
它还降低了工具和工件界面之间的化学亲和力。
具有高负前角的金刚石工具可用于以超精密精度精加工该材料。
二、金刚石作为切削工具的意义制备塑料模具的需求不断增加,而塑料模具是制造CD光学头的非球面透镜和照相机的智能透镜所必需的。
刀具的切削刃必须锋利且没有不规则形状,以加工高精度非球面。
基于工具的清晰度,单晶金刚石(SCD)和多晶金刚石(PCD)之间存在主要差异。
SCD工具的切削刃是均匀的且没有不规则性,而PCD工具的切削刃则显示出微观的不规则性,从而导致金刚石颗粒的去除。
与PCD工具相比,SCD工具的主要缺点是其磨损寿命短。
它还用于将铝基板加工成精细的镜面涂层,该涂层用于计算机存储系统的硬盘驱动器中。
第2章超精密切削与金刚石刀具详解
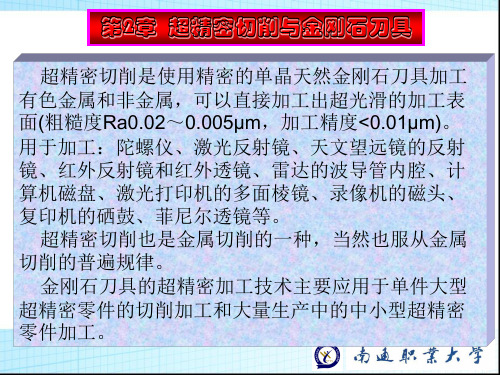
• 1)极高的硬度、极高的耐磨性和极高的弹性模量。 • 2)刃口能磨得极其锋锐,刃口半径值极小,能实现超薄切削厚度。 • 3)刀刃无缺陷,切削时刃形将复制在被加工表面上,从而得到超光滑的 镜面。 • 4)与工件材料的抗粘性好、化学亲和性小、摩擦系数低,以得到极好的 加工表面完整性。 • 不可替代的超精密切削刀具材料:单晶金刚石。
刃口半径为0.6μm、0.3μm
刃口锋锐度对加工表面有一 定的影响,相同条件下(背 吃刀量、进给量),更锋锐 的刀具切出的表面粗糙度更 小;速度的影响不是很大。
2.4 刀刃锋锐度对切削变形和加工表面质量的影响
二、刀刃锋锐度对切削变形和切削力的影响
锋锐车刀切削变形系数明显低于 较钝的车刀。 刀刃锋锐度不同,切削力明显不 同。刃口半径增大,切削力增大, 即切削变形大。背吃刀量很小时, 切削力显著增大。因为背吃刀量很 小时,刃口半径造成的附加切削变 形已占总切削变形的很大比例,刃 口的微小变化将使切削变形产生很 大的变化。所以在背吃刀量很小的 精切时,应采用刃口半径很小的锋 锐金刚石车刀。
2.7 刀具的要求及金刚石的性能和晶体结构
二、金刚石晶体的性能
• • • • 硬度最高,各向异性,不同晶向的物理性能相差很大。 优质天然单晶金刚石:多数为规整的8面体或菱形12面体,少数为6面立方体 或其他形状,浅色透明,无杂质、无缺陷。 大颗粒人造金刚石在超高压、高温下由子晶生长而成,并且要求很长的晶体 生长时间。 人造单晶金刚石已用于制造超精密切削的刀具。
2.3 切削参数变化对加工表面质量的影响
一、切削速度、进给量、修光刃和背吃刀量的影响
3、修光刃的影响
修光刃长度常取0.05~ 0.20mm。 修光刃的长度过长,对 加工表面粗糙度影响不 大。 修光刃有直线和圆弧两 种,加工时要精确对 刀,使修光刃和进给方 向一致。圆弧刃半径一般 取2~5mm。
第2章 精密超精密加工技术概论

8
材料去除单位与相关因素
去除材料的单位为10 时将以龟裂的形式发生破坏; 去除材料的单位为 -3cm时将以龟裂的形式发生破坏;以微米 时将以龟裂的形式发生破坏 以微米(µm) 级尺寸去除,则表现为位错;而以Å级去除则为原子单位去除 级去除则为原子单位去除。 级尺寸去除,则表现为位错;而以 级去除则为原子单位去除。 按去除尺寸单位分,可以把Ⅲ 区间称为普通精度, 按去除尺寸单位分,可以把Ⅲ一Ⅳ区间称为普通精度,Ⅱ一Ⅲ区间 为精密加工,I—Ⅱ区间为超精密加工。 为精密加工, Ⅱ区间为超精密加工。
13
超 精 密 加 工 的 材 料
各种产品与所要求的精度范围
加工精度范围 普 通 加 工 精密 加工 200um 300um 机械产品
一般机器零件、 家用机器、 一般机器零件 、 家用机器 、 通用齿轮、 通用齿轮 、 螺纹 、 打字机零 汽车零件、 件、汽车零件、缝纫机零件
电子产品
光学产品
通用电气机具( 开关、 通用电气机具 ( 开关 、 电 照相机壳体 动机) 动机) 照相机快门、照相机镜筒。 照相机快门、照相机镜筒。 电子零件外壳、小型电机、 电子零件外壳、小型电机、 半导体、二极管。 半导体、二极管。 透镜、棱镜、半导体纤维、 透镜、棱镜、半导体纤维、 接口。 接口。
0.5um 超 精 密 加 工
VTR 磁头、磁尺、电荷耦 精密透镜、精密棱镜、光 磁头、磁尺、 精密透镜、精密棱镜、 曝光版、 合器件、 石英振子、磁泡、 学分析尺、 曝光版 合器件 、 石英振子 、 磁泡 、 学分析尺、IC曝光版、激 IC元件、磁控管。 元件、 元件 磁控管。 光反射镜、多面反射镜、 光反射镜、多面反射镜、 X射线反射镜 射线反射镜 光学平晶、 光学平晶、精密非涅尔透 衍射光栅、光盘。 镜、衍射光栅、光盘。
金刚石刀具知识点

⾦刚⽯⼑具知识点⼑具基础知识⼀、⼑具材料应具备的性能;A,⾼的硬度和⾼耐磨性1.硬度是⼑具材料应具备的基本特性2.耐磨性是指材料抵抗磨损的能⼒。
B,⾜够的强度和韧性1.强度是⼑具材料抵抗破坏的能⼒2,韧性是指材料发⽣断裂时外界做功的⼤⼩。
3.⾼的耐热性和热传性4.良好的⼯艺性和经济性1)切削性能⽬前⼑具材料分四⼤类:⼯具钢、硬质合⾦、陶瓷及超硬⼑具材料等。
常⽤的⼑具材料⼀、⼯具钢1. 碳素⼯具钢碳素⼯具钢是含碳量为0.65%~1.3%的优质碳素钢。
常⽤的钢号有T7A、T8A等。
耐热温度:200℃~300℃。
2. 合⾦⼯具钢1868年,英国的穆舍特制成含钨的合⾦⼯具钢。
在碳素⼯具钢中加⼊适当的元素铬(Cr)、硅常⽤的合⾦⼯具钢有9CrSi,CrWMn等(Si)、锰(Mn)、钒(V)、钨(W)等炼成的。
耐热温度:325℃~400℃。
主要⽤于制造细长的或截⾯积⼤、刃形复杂的⼑具。
⼆,⾼速钢⾼速钢是⼀种富含钨(W)、铬(Cr)、钼(Mo)、钒(V)等元素的⾼合⾦⼯具钢。
美国的F.W.泰勒和M.怀特于1898年创制的。
含碳量⼀般在0.70~1.65%之间。
耐热温度:500℃~650℃。
⾼速钢的抗弯强度是硬质合⾦的3~5倍,冲击韧性是硬质合⾦的6~10倍1.普通⾼速钢(HSS)2.钨系⾼速钢:W18Cr4V (W18)3.具有较好的综合性能,可制造复杂刃型的⼑具。
但由于钨是稀有⾦属,现在很少使⽤。
4.钨钼系⾼速钢:W6Mo5Cr4V2 (M2)5.M2的碳化物颗粒⼩,分布均匀,具有较⾼的抗弯强度、塑性、韧性和耐磨性。
⼜因为钼的存在,使其热塑性⾮常好。
2. ⾼性能⾼速钢(HSS-E)⾼性能⾼速钢是在普通⾼速钢中增加⼀些碳、钒及添加钴(Co)、铝等元素的新钢种。
钴⾼速钢:W2Mo9Cr4VCo8 (M42)⼀种含钴的超硬⾼速钢,常温硬度67HRC-69HRC,具有良好的综合性能。
铝⾼速钢:W6Mo5Cr4V2Al在M2的基础上加Al、增C,提⾼了钢的耐热性和耐磨性。
LECTURE2-超精密车削

超精密加工技术广东工业大学机电工程学院魏昕一、概述¾超精密加工技术的内涵¾超精密加工技术的地位与作用¾超精密加工技术所涉及的技术领域¾超精密加工技术的现状与发展趋势一、概述1. 超精密加工技术的内涵精密加工技术:加工精度1—0.1μm,表面粗糙度Ra <0.1 μm的加工技术;超精密加工技术:加工精度<0.1μm,表面粗糙度Ra <0.02μm的加工技术;纳米加工技术:加工精度达0.001μm(1nm),表面粗糙度Ra <0.005 μm的加工技术。
随着加工技术的不断发展,超精密加工的技术一、概述2、超精密加工技术的地位与作用(1)超精密加工技术是实现现代制造业发展目标(提高机电产品的性能、质量和发展高新技术)的重要手段。
例如,集成电路的集成度。
(2)超精密加工技术已成为国际竞争中取得成功的关键技术。
所能达到的精度水平代表了一个国家的制造业能力和水平。
(3)精密工程、微细工程和纳米技术是现代制造技术的前沿。
/序超精密机械精度要求1导弹、飞机的惯性导航系统中的气浮陀及其马达轴承尺寸精度、圆度、圆柱度要求达到亚微米级2人造卫星仪表轴承表面粗糙度达到1纳米,圆度、圆柱度达纳米级3激光陀螺反光镜表面粗糙度达纳米,平面度达0.05微米4精确制导仪表零件精度达纳米级,若其陀螺转子轴线偏离0.5纳米,就会引起100米左右射程误差5计算机硬盘驱动器、光盘、复印机的精密零件精度达100纳米6微电子芯片刻线机刻线宽度在50纳米以下7基因操作机械移动距离在纳米级,移动精度在0.1纳米(原子尺度)现代超精密机械对精度的要求超精密加工是尖端技术产品发展不可缺少的关键加工手段关系到现代飞机、潜艇、导弹性能和命中率的惯性陀螺框架;激光核聚变用的反射镜;大规模集成电路的各种基片;计算机磁盘基底及复印机磁鼓;各种高精度的光学元器件;各种硬盘及记忆体的衬底等。
×一、概述3、超精密加工技术所涉及的技术领域(1)加工技术即加工方法与加工机理。
第二章 金刚石刀具精密切削加工

复习晶体结构
晶格模型
面心结构
晶体结构指晶体内部原子规则排列的方式.晶体结构不同, 其性能往往相差很大。为了便于分析研究各种晶体中原子 或分子的排列情况,通常把原子抽象为几何点,并用许多 假想的直线连接起来,这样得到的三维空间几何格架称为 晶格。
晶胞
Z
晶胞
c
b Y
a
X
晶格常数 a , b, c
人造单晶金刚石刀具 金刚石刀具 PCD刀具
多晶金刚石刀具
CVD金刚石薄膜涂层刀具
CVD金刚石刀具 金刚石厚度膜焊接刀具
金刚石刀具的性能特点
极高的硬度和耐磨性:硬度达HV10000,是自然界最硬的物质, 具有极高的耐磨性,天然金刚石耐磨性为硬质合金80-120倍,人 造金刚石耐磨性为硬质合金60-80倍。 各向异性能:单晶金刚石晶体不同晶面及晶向的硬度、耐磨性能 、微观强度、研磨加工的难易程度以及与工件材料之间的摩擦系 数等相差很大,因此,设计和制造单晶金刚石刀具时,必须进行 晶体定向。
二、典型机床简介
Pneumo 公司的MSG-325超精密车床
采用T形布局,机床空气主轴的径向圆跳动和轴向 跳动均小于等于0.05μm。床身溜板用花岗岩制造,导 轨为气浮导轨;机床用滚珠丝杠和分辨率为0.01μm的 双坐标精密数控系统驱动,用HP5501A双频激光干涉仪 精密检测位移。
DTM-3大型超精密车床
分为:液体静压和空气静压
供油压力恒定的液体静压轴承
主轴始终悬浮 在高压油膜上
液体静压轴承与气压轴承
1、液体静压轴承主轴
优点
回转稳定性好 刚度高 无振动
缺点
回转运动有温升 回油时有空气进入油源 注:空气静压轴承原理与静
《精密和超精密加工技术(第3版)》第2章超精密切削与金刚石刀具

三、使用切削液减小积屑瘤,减小加工表面粗糙 度值
图2-11 超精密切削时切削速度对加工表面粗糙 度的影响 f=0.0075mm/r ap=0.02mm
加工硬铝时,如将航空汽油作为切削液,可明显减小 加工表面粗糙度值,并且在低速时表面粗糙度值也很 小。这说明使用切削液后,已消除了积屑瘤对加工表 面粗糙度的影响,从污染环境看,应在保证加工表面 质量的条件下,尽量少用切削液。加工黄铜时,切削 液无明显效果,低速时加工表面粗糙度值不大,故加 工黄铜时可不使用切削液。
加的原因如下:
1)鼻形积屑瘤前端的圆弧半径R为2~3μm,较原来金刚 石车刀的切削刃钝圆半径rn(0.2~0.3μm)大得多。
2)积屑瘤存在时,它代替金刚石切削刃进行切削,积屑 瘤和切屑间的摩擦及积屑瘤和已加工表面之间的摩擦 都很严重,摩擦力很大,大大超过金刚石和这些材料之 间的摩擦力,这导致切削力的增加。
超精密切削刀具磨损和寿命
图2-2 磨损的金刚石切削刃
正常刀具磨损情况,一般磨 损主要在后刀面上。
图2-3 剧烈磨损的金刚石切削刃
剧烈磨损情况,从图中可看 到磨损区呈层状,即刀具磨 损为层状微小剥落,这大概 是由金刚石沿(111)晶面有 解理现象产生而造成这样的 磨损形式。
超精密切削刀具磨损和寿命
一、超精密切削时切削参数对积屑瘤生成的影响
图2-8 背吃刀量㊀ap对积屑瘤高度的影响
硬铝v=314m/min f=0.0075mm/r
在实验的切削参数范围内都有积屑瘤产生。
背吃刀量ap<25μm时,积屑瘤的高度h0变化 不大,但ap大于25μm后,积屑瘤高度h0将随 ap值的增加而增加,这种变化的原因大概是
- 1、下载文档前请自行甄别文档内容的完整性,平台不提供额外的编辑、内容补充、找答案等附加服务。
- 2、"仅部分预览"的文档,不可在线预览部分如存在完整性等问题,可反馈申请退款(可完整预览的文档不适用该条件!)。
- 3、如文档侵犯您的权益,请联系客服反馈,我们会尽快为您处理(人工客服工作时间:9:00-18:30)。
3. 刀刃形状对加工表面粗糙的影响 ✓ 直线修光刃(国内)、圆弧修光刃(国外)。 ✓ 修光刃太长对加工表面粗糙度影响不大。 ✓ 圆弧修光刃刀具加工表面质量较高,但是,制造、刃
磨复杂,成本高。
4. 背吃刀量对加工表面粗糙的影响 ✓ 在超精密加工中,背吃刀量一般都比较小,对加工
表面粗糙度的影响很小。 ✓ 但是如果ap太小,挤压严重,切削困难, 加工表面
材料、机床特性、切削环境等因素有关。 ✓ 目前,使用极其锋利的金刚石刀具在机床最佳条
件下可以实现纳米级连续稳定的切削。
常规切削与超精密切削加工
常规切削与超精密切削加工
常规切削与超精密切削加工
超精密切削加工
2. 刃口半径(钝圆半径)rn与最小切削厚度的关系
✓ 可见,最小切削厚度与刀具锋锐度、切削力、摩擦系数有关。
切削时,积屑瘤可增大刀具 前角,从而使切削力下降。
积屑瘤越高,切削力越大的主要原因 ✓ 积屑瘤圆弧半径 R 约为2-3 m,远远大于金刚石刀具刃
口半径 0.1-0.3 m。 ✓ 积屑瘤代替金刚石刀刃切削,积屑瘤与切屑间摩擦很严
重,摩擦力大大增加。 ✓ 积屑瘤的存在,导致切削厚度增加。 ✓ 积屑瘤的存在,加工表面粗糙度增加。 ✓ 使用切削液,可减小积屑瘤高度,减小加工表面粗糙度
防止积屑瘤的办法:
✓ 低速切削、或高速切削 ✓ 添加润滑液、较小摩擦 ✓ 增大刀具前角,减小刀—屑间的压力 ✓ 提高工件硬度,减小加工硬化
超精密切削刀时积屑瘤的生成规律
切削速度对积屑瘤产生的影响。 ✓ 与普通切削不同 ✓ 切削速度越高, 积屑瘤高度越低。
超精密切削刀时积屑瘤的生成规律
积屑瘤对切削力的影响 ✓ 积屑瘤越高,切削力越大 ✓ 与普通切削正好相反,普通
第四节 切削参数对加工表面质量的影响
1. 切削速度的影响 ✓ 不同的切削速度,均能得到表面粗糙度极小的加工
表面,切削速度对加工表面质量的影响不显著。 ✓ 在机床、刀具、环境条件符合要求的条件下,从高
速到低速,都能得到粗糙度极小的加工表面。
2. 进给量和修光刃的影响 ✓ 金刚石一般带有修光刃,切削时进给量很小。 ✓ 使用带修光刃的刀具加工时,进给量减小对表面
二、金刚石刀具晶面选择对切削变形 和加工表面质量的影响
1. 金刚石晶体的摩擦系数 ✓ 金刚石晶体具有强烈的各向异性,不同表
面、不同方向的摩擦系数差别明显。 ✓ (100)晶面的摩擦系数曲线有四个波峰和
波谷。 ✓ (110)晶面的摩擦系数曲线有两个波峰和
波谷。 ✓ (111)晶面的摩擦系数曲线有三个波峰和波
Hale Waihona Puke 举例:金刚石刀具切削铝合金
Fy 0.9Fx , 0.12, hDmin 0.322 rn Fy 0.9Fx , 0.26, hDmin 0.249 rn
✓ 可见,如果要得到小的最小切削厚度,就必须有小的刀具锋锐 度(刃口半径)。
hDmin 1nm, rn 3 4nm
✓ 我国现行金刚石刀具锋锐度: rn 0.2 0.5m
VT m Co
超精密切削的切削速度的选择
超精密切削时速度的选择:通常根据机床的动态特 性和整个切削系统的动态特性选择。
一般选择机床振动最小时的切削速度,以保证加工 表面质量。
第二节 超精密切削刀具磨损与寿命
金刚石刀具的寿命一般以切削路程(Km,公里)表示。 如果无意外,用金刚石刀具加工有色金属,刀具寿
,
法应力
=s 剪应力,=
O
A
B
刀具
OA—粘结区(内摩擦区):摩擦系数是变化的 AB—滑动区(外摩擦区):摩擦系数是常数 影响前刀面摩擦系数的主要因素 ✓ 工件材料,切削厚度,切削速度,刀具前角
积屑瘤
形成原因:高温、高压,粘结、冷焊 积屑瘤的作用:
✓ 增大前角 ✓ 增大切削厚度 ✓ 表面粗糙增大 ✓ 保护刀具
谷。
金刚石晶体的摩擦系数 ✓ 以 波 谷 最 低 值 比 较 , (100) 晶 面 的 摩 擦 系 数 最 低 ,
(110)晶面的摩擦系最高。 ✓ (100)晶面的摩擦系数差别最大,(111)晶面的摩擦系
命极高,可达到数百公里。 由于磨损极小,刀具寿命高,同一把刀具可以加工
多个零件,零件尺寸一致性极好。
超精密切削刀具磨损与寿命
超精密切削刀具磨损与寿命
实际生产中,金刚石刀具的寿命达不到上述值。 原因:金刚石韧性、强度低,实际生产中容易崩刃
,(机床振动等)。 金刚石刀具的晶体定向问题。
第三节 超精密切削刀时积屑瘤的生成规律
第二章超精密切削与金刚石刀 具
车刀和车削
超精密切削加工
加工4.5mm陶瓷球
金刚石车床及其加工照片
第一节 超精密切削的切削速度的选择
金刚石刀具硬度很高,耐磨性好,摩擦系数低,寿命 很长。加工有色金属时,切削速度可以很高。
切削速度对金刚石刀具的磨损影响很小,切削速度不 受刀具寿命的制约。与普通切削不同,泰勒公式:
4. 刀刃锋锐度对加工表面硬化、组织位错 和残余应力的影响
✓ 越小(刀刃越锋利),位错密度越小、加工硬化越小。
✓ 越小(刀刃越锋利),残余应力越小。
第六节 金刚石刀具超精密切削中的若干理论问题
一、超精密切削最小切削厚度 1. 最小切削厚度定义:超精密切削实际达到的最小切
削厚度。 ✓ 超精密切削最小切削厚度与刀具、锋锐度、工件
粗糙度增加。
5. 背吃刀量对加工表面残余应力的影响 ✓ ap减小,加工表面残余应力减小。 ✓ 但当ap太小(小于某临界值时),挤压严重,加工
表面残余应力增加。此临界值的大小与刀刃锋锐度 有关(刃口半径、钝园半径)。
第五节 刀刃锋锐度对切削变形和加工表面质量的影响
1. 刀刃锋锐度定义: ✓ 刃口半径、钝园半径(前后刀面之间),刀刃的锋利程度 ✓ 刀尖圆弧半径:主副切削刃之间,刀尖锋利程度。
刃口半径
2. 刀刃锋锐度的测量: 普通刀具:金相显微镜测量(= 5-30 m) 金刚石刀具:扫描电子显微镜SEM测量
(= 0.001-0.2 m)
3. 刀刃锋锐度对加工表面粗糙度、切削变形和切小 力的影响
✓ 越小(刀刃越锋利),加工表面粗糙度越小。
✓ 越小(刀刃越锋利),切削力越小。
✓ 越小(刀刃越锋利),切削变形越小。