铝合金正四面体点阵夹芯材料准静态压缩行为研究
泡沫铝填充薄壁铝合金方管轴向压缩性能的数值模拟
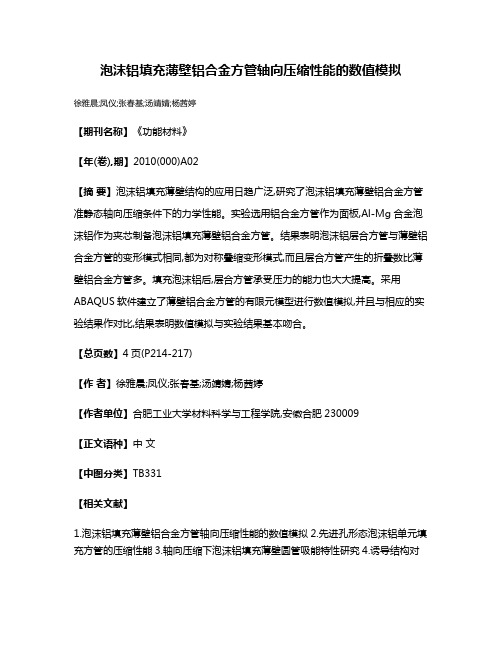
泡沫铝填充薄壁铝合金方管轴向压缩性能的数值模拟
徐雅晨;凤仪;张春基;汤靖婧;杨茜婷
【期刊名称】《功能材料》
【年(卷),期】2010(000)A02
【摘要】泡沫铝填充薄壁结构的应用日趋广泛,研究了泡沫铝填充薄壁铝合金方管准静态轴向压缩条件下的力学性能。
实验选用铝合金方管作为面板,Al-Mg合金泡沫铝作为夹芯制备泡沫铝填充薄壁铝合金方管。
结果表明泡沫铝层合方管与薄壁铝合金方管的变形模式相同,都为对称叠缩变形模式,而且层合方管产生的折叠数比薄壁铝合金方管多。
填充泡沫铝后,层合方管承受压力的能力也大大提高。
采用ABAQUS软件建立了薄壁铝合金方管的有限元模型进行数值模拟,并且与相应的实验结果作对比,结果表明数值模拟与实验结果基本吻合。
【总页数】4页(P214-217)
【作者】徐雅晨;凤仪;张春基;汤靖婧;杨茜婷
【作者单位】合肥工业大学材料科学与工程学院,安徽合肥230009
【正文语种】中文
【中图分类】TB331
【相关文献】
1.泡沫铝填充薄壁铝合金方管轴向压缩性能的数值模拟
2.先进孔形态泡沫铝单元填充方管的压缩性能
3.轴向压缩下泡沫铝填充薄壁圆管吸能特性研究
4.诱导结构对
泡沫铝填充薄壁方管轴向压溃特性影响的研究5.泡沫铝填充非等长双方管的轴向压溃特性研究
因版权原因,仅展示原文概要,查看原文内容请购买。
2195铝合金中温变形条件下的静态再结晶机理及动力学

2195铝合金中温变形条件下的静态再结晶机理及动力学张京京;易幼平;黄始全;何海林;董非;王当【期刊名称】《材料导报》【年(卷),期】2024(38)4【摘要】具有高强度、低密度的2195铝合金是航空航天构件减重的首选材料。
2195铝合金在中温热变形过程中常会伴随着静态再结晶的发生,静态再结晶晶粒对材料最终的力学性能有着重要影响。
因此,本工作采用热压缩试验、硬度测试、EBSD和XRD测试技术研究了静态再结晶晶粒判别方法,研究了不同变形温度(160~240℃)和不同保温时间(0~30 s)对静态再结晶行为和位错演变行为的影响,探明了静态再结晶的演变机理。
结果表明,晶粒平均取向差角度分布值(GOS值)小于或等于0.4°的晶粒为静态再结晶晶粒;当变形温度为160~240℃、应变速率为0.01 s^(-1)以及变形程度为30%时,随着保温时间t(t<20 s)延长,静态再结晶增加,晶粒尺寸逐渐增大。
然而,当变形温度为240℃、保温时间大于20 s时,静态再结晶晶粒没有明显增加,仅有略微长大。
在静态保温过程中,160℃的变形样品比200℃的变形样品能够更快、更易形成细小静态再结晶晶粒。
基于以上研究规律,建立了2195铝合金中温变形条件下的静态再结晶动力学模型,该模型具有良好的预测效果。
本研究对优化2195铝合金热变形和热处理工艺参数具有重要的理论价值和实际意义。
【总页数】9页(P170-178)【作者】张京京;易幼平;黄始全;何海林;董非;王当【作者单位】中南大学机电工程学院;极端服役性能精准制造全国重点实验室;中南大学轻合金研究院;湖南工业职业技术学院机械学院【正文语种】中文【中图分类】TG146.2【相关文献】1.Q235钢动态再结晶过程中的温度变化和变形道次间的静态软化2.7075铝合金热塑性变形动态再结晶动力学模型3.采用动态再结晶临界应变估算静态再结晶动力学方程4.热变形低碳钢中奥氏体静态再结晶介观尺度模拟5.Fe-0.1C-5Mn中锰钢在双道次热压缩变形期间的静态再结晶行为因版权原因,仅展示原文概要,查看原文内容请购买。
铝合金半固态变形时的微观组织特征
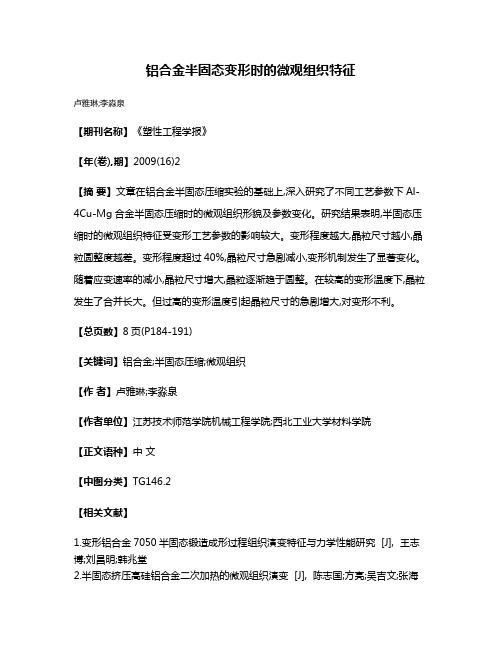
铝合金半固态变形时的微观组织特征
卢雅琳;李淼泉
【期刊名称】《塑性工程学报》
【年(卷),期】2009(16)2
【摘要】文章在铝合金半固态压缩实验的基础上,深入研究了不同工艺参数下Al-4Cu-Mg合金半固态压缩时的微观组织形貌及参数变化。
研究结果表明,半固态压缩时的微观组织特征受变形工艺参数的影响较大。
变形程度越大,晶粒尺寸越小,晶粒圆整度越差。
变形程度超过40%,晶粒尺寸急剧减小,变形机制发生了显著变化。
随着应变速率的减小,晶粒尺寸增大,晶粒逐渐趋于圆整。
在较高的变形温度下,晶粒发生了合并长大。
但过高的变形温度引起晶粒尺寸的急剧增大,对变形不利。
【总页数】8页(P184-191)
【关键词】铝合金;半固态压缩;微观组织
【作者】卢雅琳;李淼泉
【作者单位】江苏技术师范学院机械工程学院;西北工业大学材料学院
【正文语种】中文
【中图分类】TG146.2
【相关文献】
1.变形铝合金7050半固态锻造成形过程组织演变特征与力学性能研究 [J], 王志博;刘昌明;韩兆堂
2.半固态挤压高硅铝合金二次加热的微观组织演变 [J], 陈志国;方亮;吴吉文;张海
筹;马文静;白月龙
3.半固态加工变形温度对Ti14微观组织及变形机制的影响 [J], 陈永楠;魏建锋;赵永庆
4.不同半固态加工变形量的Ti14合金的微观组织和晶界特征 [J], 陈永楠;魏建锋;赵永庆
5.铸造ZL109铝合金和变形7050铝合金半固态成形过程组织演变的对比研究 [J], 翟彦博;刘昌明;王开;韩兆堂
因版权原因,仅展示原文概要,查看原文内容请购买。
加强型蜂窝准静态压缩应力的理论、数值模拟及试验研究

加强型蜂窝准静态压缩应力的理论、数值模拟及试验研究
许鹏;夏东伟;王成强;宋扬
【期刊名称】《机械强度》
【年(卷),期】2024(46)1
【摘要】为拓宽加强型蜂窝应用,研究其力学性能与结构参数的关系。
首先,分析加强型蜂窝的结构,提取Y型胞元,以此为基础分析塑性铰单元。
然后,将简化超折叠理论应用到Y型胞元结构折叠变形吸能分析,并分别利用基于屈雷斯佳和米塞斯屈服
准则,推导蜂窝异面方向准静态平台应力理论模型。
再次,选用壁厚为0.15 mm、边长为2.5 mm的铝合金5052H18,通过Ls⁃Dyna建立蜂窝仿真模型,获得平均应力,并将理论值与仿真值进行对比。
结果表明,2种屈服准则下,理论值与仿真结果相关
性为0.96,偏差在-12.16%~3.60%。
最后,对普通型和“4+1”型蜂窝制样进行准
静态压缩测试,结果表明,2种规格理论强度与实际测试强度偏差在-2.51%~1.56%。
说明理论计算式正确,可为加强型蜂窝选型提供有效的设计依据,为工程应用提供一
定的指导价值。
【总页数】9页(P87-95)
【作者】许鹏;夏东伟;王成强;宋扬
【作者单位】中车长春轨道客车股份有限公司;深圳市乾行达科技有限公司
【正文语种】中文
【中图分类】U270.34
【相关文献】
1.准静态压缩下蜂窝纸板应力-应变模型
2.煤体水压爆破准静态应力理论计算及数值模拟
3.仿生BCC结构的准静态压缩数值模拟及吸能性
4.碳纤维复合材料缠绕铝合金管准静态轴向压缩的数值模拟
5.蜂窝纸板静态压缩试验研究及其模拟分析
因版权原因,仅展示原文概要,查看原文内容请购买。
2A14铝合金热压缩变形流变行为研究的开题报告
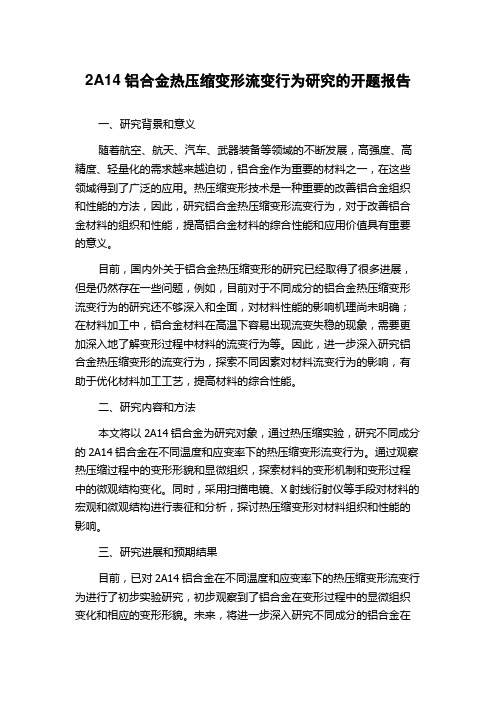
2A14铝合金热压缩变形流变行为研究的开题报告一、研究背景和意义随着航空、航天、汽车、武器装备等领域的不断发展,高强度、高精度、轻量化的需求越来越迫切,铝合金作为重要的材料之一,在这些领域得到了广泛的应用。
热压缩变形技术是一种重要的改善铝合金组织和性能的方法,因此,研究铝合金热压缩变形流变行为,对于改善铝合金材料的组织和性能,提高铝合金材料的综合性能和应用价值具有重要的意义。
目前,国内外关于铝合金热压缩变形的研究已经取得了很多进展,但是仍然存在一些问题,例如,目前对于不同成分的铝合金热压缩变形流变行为的研究还不够深入和全面,对材料性能的影响机理尚未明确;在材料加工中,铝合金材料在高温下容易出现流变失稳的现象,需要更加深入地了解变形过程中材料的流变行为等。
因此,进一步深入研究铝合金热压缩变形的流变行为,探索不同因素对材料流变行为的影响,有助于优化材料加工工艺,提高材料的综合性能。
二、研究内容和方法本文将以2A14铝合金为研究对象,通过热压缩实验,研究不同成分的2A14铝合金在不同温度和应变率下的热压缩变形流变行为。
通过观察热压缩过程中的变形形貌和显微组织,探索材料的变形机制和变形过程中的微观结构变化。
同时,采用扫描电镜、X射线衍射仪等手段对材料的宏观和微观结构进行表征和分析,探讨热压缩变形对材料组织和性能的影响。
三、研究进展和预期结果目前,已对2A14铝合金在不同温度和应变率下的热压缩变形流变行为进行了初步实验研究,初步观察到了铝合金在变形过程中的显微组织变化和相应的变形形貌。
未来,将进一步深入研究不同成分的铝合金在不同条件下的热压缩变形流变行为和相应的微观结构变化,探索变形机理和变形过程中的影响因素。
预计将进一步提高研究成果的深度和广度,为铝合金材料的优化设计和应用提供有力的支持。
219515805_金属纤维钩织复合结构压缩行为分析

第15卷第6期精密成形工程2023年6月JOURNAL OF NETSHAPE FORMING ENGINEERING19金属纤维钩织复合结构压缩行为分析赵顺秋,吴菲,洪熠豪,陈雅婷,郑氏韦(广东工业大学材料与能源学院,广州 510006)摘要:目的针对金属薄壁复合管在轴向压缩时初始峰值载荷高、吸能效果不佳、结构耐撞性不好等问题,研究金属纤维钩织复合结构以及填充6063铝合金管试件的轴向准静态压缩行为和吸能特性。
方法利用短针钩织与烧结工艺制备不同孔隙率的金属纤维钩织结构,将它们填充到6063薄壁管之后,在万能试验机上进行轴向压缩试验,引入评价指标,对试验数据进行处理分析。
结果孔隙率为85.9%、87.9%、89.4%的金属纤维钩织结构的初始峰值力分别为0.48、0.38、0.32 kN,平均压缩力分别为0.72、0.55、0.45 kN。
它们的初始峰值力和平均压缩力都非常小,都小于0.8 kN。
然而,它们的压缩力效率非常高,分别为1.5、1.45、1.41。
初始峰值力、平均压缩力和压缩力效率均随孔隙率的增加而减小。
这一特性有利于提高结构的耐撞性,表明不存在初始冲击效应,能够直接进入吸能阶段。
结论通过填充金属纤维钩织结构,可以在初始峰值力几乎没有增加的情况下提高6063管材的准静态耐撞性。
此外,钩织结构孔隙率对金属纤维钩织结构的准静态力学行为有明显影响。
关键词:金属纤维;钩织结构;复合填充管;压缩变形;能量吸收DOI:10.3969/j.issn.1674-6457.2023.06.003中图分类号:TG302 文献标识码:A 文章编号:1674-6457(2023)06-0019-08Compression Behavior Analysis of Metal FiberCrocheted Composite StructuresZHAO Shun-qiu, WU Fei, HONG Yi-hao, CHEN Ya-ting, ZHENG Shi-wei(School of Materials and Energy, Guangdong University of Technology, Guangzhou 510006, China)ABSTRACT: The work aims to study the quasi-static compression behavior and energy absorption characteristics of metal fiber crocheted composite structure and 6063 aluminum alloy pipe specimen filled with such structure, so as to solve the problems of high initial peak load, poor energy absorption effect and poor crashworthiness of metal thin-walled composite pipe during axial收稿日期:2023–02–28Received:2023-02-28基金项目:青年科学基金(500170074)Fund:Youth Science Foundation Project (500170074)作者简介:赵顺秋(1998—),男,硕士生,主要研究方向为金属连续纤维多孔材料/复合结构设计/制备、力学行为及吸能抗冲击应用。
泡沫铝夹芯双管构件横向压缩吸能性能研究

第44卷第23期包装工程2023年12月PACKAGING ENGINEERING·293·泡沫铝夹芯双管构件横向压缩吸能性能研究吴鹏1,鲍海英2*,李爱群3,4(1.东南大学建筑设计研究院有限公司,南京210096;2.安徽工业大学建筑工程学院,安徽马鞍山243002;3.东南大学土木工程学院,南京210096;4.北京建筑大学土木与交通工程学院,北京100044)摘要:目的研究截面构型及几何参数对泡沫铝夹芯双管结构在横向载荷作用下变形失效机制和吸能性能的影响。
方法运用有限元软件Abaqus/Explicit对泡沫铝夹芯双管构件受横向载荷作用进行数值仿真分析。
结果泡沫铝夹芯双管构件在横向压缩过程中表现出3个阶段:初始压缩阶段、塑性变形阶段和致密化阶段,并发现外方内圆双管夹芯结构的耐撞性能显著强于双方管夹芯结构。
随着外管径的增大、内管径的减小,外方内圆双管夹芯结构的承载力和吸能能力越高;内管壁厚的增加使外方内圆双管夹芯结构的能量吸收、比吸能、平均压溃载荷和压溃力效率均表现出增大趋势。
结论泡沫铝芯材的变形失效模式受内管截面形状的影响,与传统双方管夹芯结构相比,外方内圆双管夹芯结构是一种更优秀的吸能构件,在横向碰撞安全防护中展现出更大的应用潜力。
通过增加内外管间距和内管壁厚,可以提高外方内圆双管夹芯结构的吸能性能。
关键词:泡沫铝;夹芯双管;横向压缩;吸能性能;数值模拟中图分类号:TB485.1;O347 文献标识码:A 文章编号:1001-3563(2023)23-0293-09DOI:10.19554/ki.1001-3563.2023.23.035Energy Absorption Performance of Aluminum Foam Sandwiched Double-tube underTransverse CompressionWU Peng1, BAO Hai-ying2*, LI Ai-qun3,4(1. Southeast University Architectural Design and Research Institute Co., Ltd., Nanjing 210096, China;2. School of Architecture and Engineering, Anhui University of Technology, Ma'anshan 243002, China;3. School of Civil Engineering, Southeast University, Nanjing 210096, China;4. School of Civil andTransportation Engineering, Beijing University of Architecture, Beijing 100044, China)ABSTRACT: The work aims to study the effects of section configuration and geometric parameters on the deformation mechanism and energy absorption performance of aluminum foam sandwiched double-tube under transverse load. Finite element software Abaqus/Explicit was used to carry out numerical simulation on the aluminum foam sandwiched double-tube under transverse load. The aluminum foam sandwiched double-tube exhibited three stages in the process of transverse compression, namely, the initial compression stage, the plastic deformation stage, and the densification stage. It was also found that the crashworthiness of a novel aluminum foam sandwiched double-tube, comprised of square outer and circular inner tubes, was significantly stronger than that of the double square tube structure. As the outer tube diame-ter increased and the inner tube diameter decreased, the load-bearing capacity and energy absorption capacity of the novel aluminum foam sandwiched double-tube increased. The increase in wall thickness of the inner tube resulted in an in-creasing trend in energy absorption, specific energy absorption, average crushing load, and crushing force efficiency. The收稿日期:2023-05-22基金项目:安徽工业大学校自然基金青年项目(QZ202211)·294·包装工程2023年12月deformation failure mode of aluminum foam core material is affected by the section shape of the inner tube. Compared with the traditional double square tube structure, the novel sandwiched double-tube is a better energy-absorbing compo-nent, which shows greater application potential in the safety protection of lateral collision. By increasing the tance between the inner and outer tubes and the wall thickness of the inner tube, the energy absorption performance of the novel sandwiched double-tube can be improved.KEY WORDS: aluminum foam; sandwiched double-tube; transverse compression; energy absorption performance; nu-merical simulation薄壁金属管结构具有比刚度和比强度高的优点,在压缩过程中可以吸收大量的动能并将其转化为塑性应变能[1],常作为吸能元件应用于汽车、航空航天、交通等领域,但存在易发生欧拉屈曲失稳、非轴向承载能力差等问题。
铝蜂窝的电阻点焊工艺及其结构的压缩性能

摘要本文以蜂窝吸能结构件为应用需求背景,研究了铝蜂窝的电阻点焊制备工艺,制备了点焊方形铝蜂窝结构单元试样,在不同温度条件下测试了试样的轴向准静态压缩性能,与相同规格的胶接铝蜂窝结构试样的准静态压缩试验结果进行了对比,探究点焊方形铝蜂窝结构单元试样的性能特性;同时采用Abaqus有限元模拟电阻点焊铝蜂窝结构单元的轴向压缩行为,观察分析了铝蜂窝壁板变形及焊点周围的应力分布状态。
通过焊点熔池微观形貌的观察及焊点剪切力的测定确定了铝蜂窝电阻点焊的优化工艺参数(焊接电压为250V、焊接时间为1.4s、电极压力为60N),单个焊点的剪切力达到66.5N,正拉力达到30.9N。
铝蜂窝结构单元试样的压缩应力应变曲线分线弹性变形、初始峰值屈服、稳定屈服平台和密实化四个阶段。
通过改变焊点数目制备不同焊点距的铝蜂窝进行准静态压缩试验发现,铝蜂窝压缩的稳定屈服平台应力随着焊点距减小而增大,而焊点距对铝蜂窝的初始峰值屈服强度没有明显影响。
电阻点焊铝蜂窝对环境温度的敏感性较小,从-50°C升至100°C,电阻点焊铝蜂窝的初始峰值屈服强度降低9.02%,胶接铝蜂窝的初始峰值屈服强度降低38.97%。
通过电阻点焊铝蜂窝结构单元试样的压缩过程观察和有限元模拟,蜂窝的初始屈服堆叠发生在结构的端部,随后依次扩展,铝蜂窝结构焊点附近没有明显的应力集中。
关键词:方形铝蜂窝;电阻点焊;准静态压缩;压缩机制;有限元分析AbstractFor the application requirement of the honeycomb as an energy absorbing structure, in the present paper, the resistance spot welding technology of the aluminum honeycomb is detailed and square aluminum honeycomb structure specimen is prepared. The axial quasi-static compression performances of the resistance spot welding aluminum honeycomb and the same size adhesive aluminum honeycomb were tested under different temperatures to explore performance characteristics of square aluminum honeycomb specimen. Meanwhile, Abaqus finite element simulation is adopted to observe the axial compression behavior of the aluminum honeycomb specimen, analyze the deformation of aluminum honeycomb panel and the stress distribution around the solder joint.The optimized technological parameters for aluminum honeycomb resistance spot welding are determined by observing the microstructure and testing the shearing force of solder joint (the welding voltage is 250V, the welding time is 1.4s, the electrode pressure is 60N).The shearing force of single solder joint is 66.5N, the positive tension is 30.9N.Compression stress-strain curve of aluminum honeycomb is characterized by linear elastic deformation , initial peak yield, stable yield and densification . Quasi-static compression tests are carried outwith different numbers of solder joints, which indicates thatthe plateau stress increases with the decrease of weld spacing, while the weld spot spacing has no obvious influence on the initial peak yield strength. The resistance spot welded aluminum honeycomb is less sensitive to the changeof environmental temperature. From -50°C to 100°C, the initial peak yield strength of aluminum honeycomb specimen decreases about 9.02%, and the initial peak yield strength of the adhesive aluminium honeycomb decreases about 38.97%.By observing the compression process of aluminum honeycomb specimen and Abaqus finite element simulation, the initial yield stack of the honeycomb occurs at the end of the honeycomb structure, then expands sequentially. There is no obvious stress concentration near the solder joint of aluminum honeycomb structure.Keywords:Square aluminum honeycomb, Resistance spot welding, Quasi-static compression, Compression mechanism, Finite element analysis目录摘要 (I)Abstract (II)第1章绪论 (1)1.1 课题研究背景及意义 (1)1.2 蜂窝结构概述 (1)1.2.1. 蜂窝结构种类及胞元形状 (1)1.2.2. 蜂窝结构性能特点 (2)1.2.3. 蜂窝结构的应用 (2)1.3 蜂窝结构的制备研究现状 (3)1.4 蜂窝结构的压缩性能研究现状 (5)1.4.1 铝蜂窝的压缩力学行为研究 (5)1.4.2 不同胞元结构铝蜂窝力学性能研究 (8)1.4.3 不同温度下铝蜂窝压缩性能研究 (9)1.5 电阻点焊原理概述 (11)1.6 主要研究内容 (12)第2章试验材料及方法 (13)2.1 试验材料 (13)2.2 铝蜂窝结构及制备方法 (14)2.3 力学性能测试方法 (16)2.3.1 焊点剪切力和正拉力测试 (16)2.3.2 铝蜂窝准静态压缩测试 (17)2.4 材料分析测试方法 (18)2.4.1XRD测试 (18)2.4.2SEM测试 (18)2.4.3 显微硬度测试 (18)2.4.4 玻璃化转变温度(Tg)测试 (18)2.5Abaqus有限元模拟 (19)第3章铝蜂窝电阻点焊工艺参数优化 (21)3.1 焊点形貌及熔池组织的观察 (21)3.2 焊点剪切力的测试 (23)3.3U、t s、Q对焊点剪切力F的影响 (25)3.4 焊点正拉力的测试 (29)3.5 本章小结 (30)第4章铝蜂窝结构的准静态压缩性能 (31)4.1 铝蜂窝的准静态压缩力学行为 (31)4.2 电阻点焊铝蜂窝在不同温度下的压缩性能 (32)4.3 焊点距对电阻点焊铝蜂窝压缩性能的影响 (36)4.4 胶接铝蜂窝在不同温度下的压缩性能 (39)4.5 两种蜂窝结构压缩性能对比分析 (41)4.6 本章小结 (44)第5章铝蜂窝结构的压缩失效过程及有限元分析 (45)5.1 胶接铝蜂窝结构的强度变化机理分析 (45)5.2 电阻点焊铝蜂窝结构的变形行为及强化机理 (46)5.2.1 电阻点焊铝蜂窝结构的压缩过程 (46)5.2.2 焊点距对铝蜂窝结构变形行为的影响 (47)5.2.3 电阻点焊铝蜂窝结构的焊点失效及强化机理 (49)5.3 点焊铝蜂窝的Abaqus有限元模拟 (54)5.3.1 铝蜂窝结构模块建模 (54)5.3.2 有限元材料参数 (54)5.3.3 有限元边界条件 (56)5.3.4 有限元网格划分 (56)5.3.5 焊点建立方式-Fasteners (56)5.4 点焊铝蜂窝结构模块有限元分析 (57)5.4.1 铝蜂窝模块的压缩过程 (57)5.4.2 铝蜂窝模块焊点的应力应变分布 (58)5.5 本章小结 (62)结论 (63)参考文献 (64) (69)致谢 (70)第1章绪论1.1课题研究背景及意义早在20世纪40年代,人类将桃花芯木制成的蒙皮材料和轻木制成的低密度芯子复合用来制造飞机机翼。
- 1、下载文档前请自行甄别文档内容的完整性,平台不提供额外的编辑、内容补充、找答案等附加服务。
- 2、"仅部分预览"的文档,不可在线预览部分如存在完整性等问题,可反馈申请退款(可完整预览的文档不适用该条件!)。
- 3、如文档侵犯您的权益,请联系客服反馈,我们会尽快为您处理(人工客服工作时间:9:00-18:30)。
Material Sciences 材料科学, 2016, 6(2), 115-123Published Online March 2016 in Hans. /journal/ms/10.12677/ms.2016.62015Quasi-Static Compressive Behaviorof Tetrahedral Lattice TrussStructures Made fromAluminiumYongsheng Wei1,2, Keda Jiang2,3, Yunlai Deng1,2,3, Jin Zhang2,3,Qingsong Dai1,21School of Materials Science and Engineering, Central South University, Changsha Hunan2Key Laboratory of Nonferrous Materials Science and Engineering, Ministry of Education, Central SouthUniversity, Changsha Hunan3Light Alloy Research Institute, Central South University, Changsha HunanReceived: Mar. 2nd, 2016; accepted: Mar. 24th, 2016; published: Mar. 29th, 2016Copyright © 2016 by authors and Hans Publishers Inc.This work is licensed under the Creative Commons Attribution International License (CC BY)./licenses/by/4.0/AbstractTetrahedral lattice truss structures have been made by folding perforated 6061 aluminum alloy sheets. Simple air brazing was used to construct sandwich panels with cellular core; relative den-sity was 0.05. The behavior of quasi-static compression (initial strain rate is 10−3 S−1) was studied in the present study, and three kinds of heart-treatment were investigated, which were T6, T7 and anneal. The results showed that: three distinct stages of deformation show in quasi-static com-pressive stress-strain curves, namely the linear elastic stage, the longer yield stage and the stage of densification, and densification strain is 0.4; energy absorption mainly occurs in the stage of longer yield, in which severe plastic deformations occur, and the energy absorption of T6 is higher than T7, while the anneal is the lowest; energy absorption efficiency is determined by the material plasticity and strength, and the energy absorption efficiency of T7 is greater than T6, while the annealed state is minimum at the beginning, and finally between T6 and T7.KeywordsTetrahedral Lattice Structures, 6061 Aluminum Alloy, Energy Absorption, Energy AbsorptionEfficiency魏永生等铝合金正四面体点阵夹芯材料准静态压缩行为研究魏永生1,2,姜科达2,3,邓运来1,2,3,张劲2,3,戴青松1,21中南大学材料科学与工程,湖南长沙2中南大学有色金属材料科学与工程教育部重点实验室,湖南长沙3中南大学轻合金研究院,湖南长沙收稿日期:2016年3月2日;录用日期:2016年3月24日;发布日期:2016年3月29日摘要本文通过冲压折叠法制造6061铝合金正四面体点阵夹芯芯体结构,采用钎焊连接面板及芯体,研究了相对密度为0.05正四面体点阵夹芯材料在T6、T7及退火三种不同热处理状态下的准静态压缩(初始应变速率为10−3S−1)行为。
研究结果表明:准静态压缩应力应变曲线均表现为三个明显的变形阶段,即线弹性阶段、较长的屈服阶段及致密化阶段,致密化应变为0.4;能量吸收主要发生在芯体剧烈的塑性变形阶段即较长的屈服阶段,吸能量T6态大于T7态,退火态最低;吸能效率由材料的塑性及强度共同决定,吸能效率T7总是大于T6,退火态开始最小,最后处于两者之间。
关键词正四面体点阵夹芯,6061铝合金,吸能,吸能效率1. 引言在航空航天及武器防护等需求下,新型多孔材料的缓冲吸能特性的研究获得了广泛的关注[1]。
金属多孔材料具有轻质、高比强度、高比刚度、高比表面积、吸能减振、消音降噪、散热隔热以及电磁屏蔽等诸多优异性能,因而广泛用于汽车、军舰、航空航天、电子、生物等工业领域,是一种具有结构与功能双重属性的新型工程材料[2]-[4]。
金属多孔材料根据其内部孔洞的分布规则程度可分为有序和无序两大类,前者称为金属点阵材料,后者则为金属泡沫材料。
据报道,在众多的多孔材料中,周期性的有序材料比随机的无序材料具有更优良的综合性能,这是由于有序的多孔材料其夹芯结构可以理论计算进行优化设计,设计与制造更加可控[5]。
本文以铝合金正四面体金属点阵夹芯复合板材为研究对象,通过准静态压缩实验研究正四面体点阵夹芯结构不同热处理状态下的压缩能力,获得其应力-应变曲线,评估其静态吸能特性。
2. 实验材料及实验方法2.1. 实验材料实验用面板及芯体材料均为6061铝合金,采用冲压折叠法制造正四面体夹芯,最后采用钎焊的方法连接面板与夹芯。
由于正四面体点阵夹芯材料无尺寸效应[5],故本实验采用正四面体点阵夹芯单体,魏永生等图1为从钎焊后的大块试样中线切割的正四面体点阵夹芯单体,其相对密度约为0.05。
相对密度为单体内的正四面体夹芯的体积比上整个夹芯的所占有的长方体的体积[6]-[9],其试样详细尺寸见表1,面板跟芯体板材的厚度均为1.5 mm。
2.2. 实验方法本文研究不同热处理状态下正四面体点阵夹芯的吸能特性,选取了退火态、T6态、T7态三种不同的热处理状态。
将出炉的试样清洗后进行530℃/1h固溶处理,固溶完成后水淬。
淬火完成后,将其中一块退火处理,退火制度200℃/2h,并标记为Annealed;其中的一块进行峰值时效处理,时效制度为165℃/19h,标记为T6;另外一块进行过时效处理,时效制度为260℃/10h,标记为T7。
对基体材料进行初始应变速率为10−3 S−1的拉伸,得到T6、T7及Annealed的屈服强度分别为300 MPa、236 MPa及170 MPa。
试样的准静态压缩在电液伺服万能材料实验机MTS810上进行,初始的压缩应变速率为10−3 S−1,根据芯体的高度,换算后设定的压缩速率约为0.72 mm/min,总压下量不小于50%。
3. 实验结果及分析3.1. 正四面体点阵夹芯准静态压缩应力–应变分析将准静态压缩的数据进行处理转化为应力应变,得到不同热处理状态下的应力–应变压缩曲线图。
图2为不同热处理状态下的应力–应变压缩曲线图,由图2可知,四面体点阵夹芯准静态压缩表现为3个明显的变形阶段,即线弹性阶段、较长的屈服阶段、致密化阶段。
正四面体点阵夹芯在压缩的初始阶段首先呈现出一段变形范围非常小的线弹性变形区,T6及T7的弹性变形发生在应变小于0.05,而退火态的弹性变形区域行对较大,其应变范围为0到0.10,这是由于T6及T7的强度大于退火态。
在弹性变形区间内,应力应变基本呈现线性关系,此阶段的变形机理为正四面体夹芯的3条芯体杆单元发生弹性变形。
线弹性阶段结束后,芯体开始发生塑性屈服,应力出现一个压缩峰值,在整体压缩变形过程中呈现出一个较长的屈服阶段,应变从0.1开始直至0.4。
由图2发现,不同热处理的正四面体点阵夹芯试样的对应的峰值压缩强度不同,峰值时效(T6)最高约为 6.5 Mpa,而过时效(T7)次之约为 4.6 Mpa,退火态(Annealed)最小约为3.9 Mpa,峰值压缩强度的大小与材料的热处理状态所对应的强度大小关系保持一致。
而夹芯的压缩屈服应变点,退火态在0.1左右,而T7跟T6在0.08左右。
由于正四面体芯体杆元由之前的弹性弯曲转为塑性屈服,所以出现应力突然下降的坍塌屈服阶段,图中应力直线下滑处,但此时夹芯体内部仍存在大量孔洞,在随后的压缩过程中,金属骨架杆单元不会立即接触,这为压缩过程提供了可以继续压缩的空间,继续压缩将导致正四面体点阵夹芯体发生“软化”现象,应变逐渐增大而应力却不断减小,一直持续到应变量为0.4左右,即致密化应变点。
当压缩应变大于0.4后,夹芯体发生材料致密化,随着应变的增加,点阵夹芯体的压缩强度显著升高。
这是因为此时点阵夹芯结构已经几乎被压实,杆元弯曲且与面板相互接触,继而压缩过程变形为基体材料所承受,于是夹芯体出现压缩应力随应变的增大而急剧升高的致密化变形阶段。
不同热处理的致密化应变都约为0.4左右,这是由于夹芯内部的孔隙空间相同即拥有相同的相对密度,此时压缩变形中点阵夹芯结构所起的作用基本消失,更多的是基体材料在发挥作用。
为了直观的观察整个压缩过程中夹芯杆单元的应变情况,压缩过程进行了拍照记录,图3为其中几个典型的压缩阶段。