铸造铝合金热处理
铝合金铸件的热处理

铝合金铸件的热处理铝合金铸件的热处理是指按某一热处理规范,控制加热温度、保温时间和冷却速度,改变合金的组织,其主要目的是:提高力学性能,增强耐腐蚀性能,改善加工性能,获得尺寸的稳定性。
铝合金铸件的热处理工艺可以分为如下四类:1 退火处理将铝合金铸件加热到较高的温度,一般约为300 ℃左右,保温一定的时间后,随炉冷却到室温的工艺称为退火。
在退火过程中固溶体发生分解,第二相质点发生聚集,可以消除铸件的内应力,稳定铸件尺寸,减少变形,增大铸件的塑性。
2 固溶处理固溶处理把铸件加热到尽可能高的温度,接近于共晶体的熔点,在该温度下保持足够长的时间,并随后快速冷却,使强化组元最大限度的溶解,这种高温状态被固定保存到室温,该过程称为固溶处理。
固溶处理可以提高铸件的强度和塑性,改善合金的耐腐蚀性能。
固溶处理的效果主要取决于下列三个因素:(1)固溶处理温度。
温度越高,强化元素溶解速度越快,强化效果越好。
一般加热温度的上限低于合金开始过烧温度,而加热温度的下限应使强化组元尽可能多地溶入固溶体中。
为了获得最好的固溶强化效果,而又不便合金过烧,有时采用分级加热的办法,即在低熔点共晶温度下保温,使组元扩散溶解后,低熔点共晶不存在,再升到更高的温度进行保温和淬火。
固溶处理时,还应当注意加热的升温速度不宜过快,以免铸件发生变形和局部聚集的低熔点组织熔化而产生过烧。
固溶热处理的悴火转移时间应尽可能地短,一般应不大于15s,以免合金元素的扩散析出而降低合金的性能。
(2)保温时间。
保温时间是由强化元素的溶解速度来决定的,这取决于合金的种类、成分、组织、铸造方法和铸件的形状及壁厚。
铸造铝合金的保温时间比变形铝合金要长得多,通常由试验确定,一般的砂型铸件比同类型的金属型铸件要延长20%-25% 。
(3)冷却速度。
淬火时给予铸件的冷却速度越大,使固溶体自高温状态保存下来的过饱和度也越高,从而使铸件获得高的力学性能,但同时所形成的内应力也越大,使铸件变形的可能性也越大。
铝合金铸件热处理工艺参数

------
------
-------
180±5
3~5
空冷
轻载荷的零件
T2
------
------
-------
290±5
2~4
空冷
要求尺寸稳定并消除应力的零件
T5
515±5
3~6
60~100℃
175±5
3~5
空冷
在低于175℃下下重载荷的零件
T7
515±5
3~6
60~100℃
230±5
3~5
空冷
10~14
空冷
要求高强度高硬度的零件
175±5(J)
7~14
T7
510±5
3~5
80~100℃
200±250
3
空冷
高温下工作的零件如活塞
ZL203
T4
515±5
10~15
60~100℃
------
------
-------
要求高强度高塑性的零件
T5
515±5
10~15
60~100℃
150±5
2~4
空冷
__
680~750
1.2~1.4
铝合金铸件热处理工艺参数(一)
代号
热处理状态
淬火
时效
用途举例
加热温度℃
保温时间h
冷却(水中)
加热温度℃
保温时间h
冷却
ZL101
T1
------
------
-------
230±5
7~9
空冷
改善被切削性能
T4
535±5
2~6
60~100℃
铝的热处理

铝的热处理铝合金铸件的热处理是指按某一热处理规范,控制加热温度、保温时间和冷却速度,改变合金的组织,其主要目的是:提高力学性能,增强耐腐蚀性能,改善加工性能,获得尺寸的稳定性。
铝合金铸件的热处理工艺可以分为如下四类:1。
退火处理将铝合金铸件加热到较高的温度,一般约为300 ℃左右,保温一定的时间后,随炉冷却到室温的工艺称为退火。
在退火过程中固溶体发生分解,第二相质点发生聚集,可以消除铸件的内应力,稳定铸件尺寸,减少变形,增大铸件的塑性。
2。
固溶处理把铸件加热到尽可能高的温度,接近于共晶体的熔点,在该温度下保持足够长的时间,并随后快速冷却,使强化组元最大限度的溶解,这种高温状态被固定保存到室温,该过程称为固溶处理。
固溶处理可以提高铸件的强度和塑性,改善合金的耐腐蚀性能。
固溶处理的效果主要取决于下列三个因素:(1)固溶处理温度。
温度越高,强化元素溶解速度越快,强化效果越好。
一般加热温度的上限低于合金开始过烧温度,而加热温度的下限应使强化组元尽可能多地溶入固溶体中。
为了获得最好的固溶强化效果,而又不便合金过烧,有时采用分级加热的办法,即在低熔点共晶温度下保温,使组元扩散溶解后,低熔点共晶不存在,再升到更高的温度进行保温和淬火。
固溶处理时,还应当注意加热的升温速度不宜过快,以免铸件发生变形和局部聚集的低熔点组织熔化而产生过烧。
固溶热处理的悴火转移时间应尽可能地短,一般应不大于15s,以免合金元素的扩散析出而降低合金的性能。
(2)保温时间。
保温时间是由强化元素的溶解速度来决定的,这取决于合金的种类、成分、组织、铸造方法和铸件的形状及壁厚。
铸造铝合金的保温时间比变形铝合金要长得多,通常由试验确定,一般的砂型铸件比同类型的金属型铸件要延长20%-25% 。
(3)冷却速度。
淬火时给予铸件的冷却速度越大,使固溶体自高温状态保存下来的过饱和度也越高,从而使铸件获得高的力学性能,但同时所形成的内应力也越大,使铸件变形的可能性也越大。
热处理对铸造铝合金材料的晶界特性和耐蚀性能的影响

热处理对铸造铝合金材料的晶界特性和耐蚀性能的影响热处理是一种常用的金属加工方法,可以改善材料的力学性能和耐腐蚀性。
在铸造铝合金材料中,热处理也被广泛应用。
本文将探讨热处理对铸造铝合金材料晶界特性和耐蚀性能的影响。
一、热处理对晶界特性的影响晶界是材料中各个晶体之间的交界面,对材料的性能起着重要的作用。
热处理可以改变晶界的结构和性质,进而影响材料的力学性能和耐蚀性。
1. 晶界结构的改变热处理过程中的加热和冷却可以引起晶界结构的变化。
例如,固溶热处理可以使溶质在晶界区域的浓度得到调整,从而改善晶界的结构。
此外,热处理还可以促使晶界清晰化和去除一些晶格缺陷,提高晶界的强度。
2. 晶界位错的行为晶界中的位错是晶界强度的重要因素。
热处理过程中,晶界位错的行为可以被改变。
通过适当的热处理,可以增加晶界位错的密度和移动性,从而提高晶界的强度和塑性。
3. 晶界扩散和再结晶热处理还能促进晶界扩散和晶界再结晶。
晶界扩散可以导致溶质在晶界区域的聚集和分布均匀,从而提高晶界的强度和韧性。
晶界再结晶是指在高温下,原本的晶粒被新的晶粒所取代,更加细小的晶粒有利于提高材料的强度和韧性。
二、热处理对耐蚀性能的影响铸造铝合金材料在暴露于大气、水和化学介质中时,会出现腐蚀现象。
热处理可以改变铝合金材料的晶界特性和晶粒尺寸,从而影响其耐蚀性能。
1. 晶界腐蚀晶界是金属腐蚀的薄弱环节之一。
晶界中的异质相或溶质偏聚可能会引发晶界腐蚀。
适当的热处理可以改善晶界结构,减少晶界的偏聚现象,提高晶界的抗腐蚀能力。
2. 晶粒尺寸和耐蚀性热处理可以影响铸造铝合金材料的晶粒尺寸。
通常情况下,细小的晶粒比大晶粒具有更好的耐蚀性能。
热处理过程中,晶界的清晰化和晶界的再结晶可以使晶粒尺寸细化,从而提高材料的耐蚀性。
3. 化学成分和相变热处理还可以改变铝合金材料的化学成分和相变行为,进而影响其耐蚀性。
例如,固溶热处理可以调整合金中的溶质含量,进而影响材料的耐蚀性。
铸造铝合金热处理质量缺陷及其消除与预防
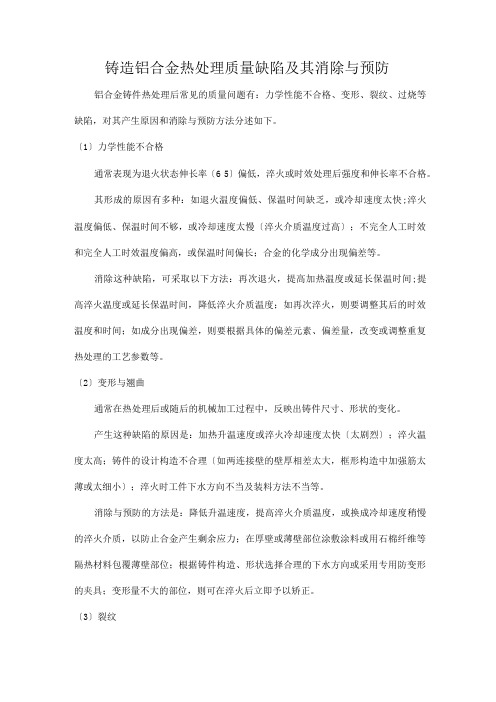
铸造铝合金热处理质量缺陷及其消除与预防铝合金铸件热处理后常见的质量问题有:力学性能不合格、变形、裂纹、过烧等缺陷,对其产生原因和消除与预防方法分述如下。
〔1〕力学性能不合格通常表现为退火状态伸长率〔6 5〕偏低,淬火或时效处理后强度和伸长率不合格。
其形成的原因有多种:如退火温度偏低、保温时间缺乏,或冷却速度太快;淬火温度偏低、保温时间不够,或冷却速度太慢〔淬火介质温度过高〕;不完全人工时效和完全人工时效温度偏高,或保温时间偏长;合金的化学成分出现偏差等。
消除这种缺陷,可采取以下方法:再次退火,提高加热温度或延长保温时间;提高淬火温度或延长保温时间,降低淬火介质温度;如再次淬火,则要调整其后的时效温度和时间;如成分出现偏差,则要根据具体的偏差元素、偏差量,改变或调整重复热处理的工艺参数等。
〔2〕变形与翘曲通常在热处理后或随后的机械加工过程中,反映出铸件尺寸、形状的变化。
产生这种缺陷的原因是:加热升温速度或淬火冷却速度太快〔太剧烈〕;淬火温度太高;铸件的设计构造不合理〔如两连接壁的壁厚相差太大,框形构造中加强筋太薄或太细小〕;淬火时工件下水方向不当及装料方法不当等。
消除与预防的方法是:降低升温速度,提高淬火介质温度,或换成冷却速度稍慢的淬火介质,以防止合金产生剩余应力;在厚壁或薄壁部位涂敷涂料或用石棉纤维等隔热材料包覆薄壁部位;根据铸件构造、形状选择合理的下水方向或采用专用防变形的夹具;变形量不大的部位,则可在淬火后立即予以矫正。
〔3〕裂纹表现为淬火后的铸件外表用肉眼可以看到明显的裂纹,或通过荧光检查肉眼看不见的微细裂纹。
裂纹多曲折不直并呈暗灰色。
产生裂纹的原因是:加热速度太快,淬火时冷却太快〔淬火温度过高或淬火介质温度过低,或淬火介质冷却速度太快〕;铸件构造设计不合理〔两连接壁壁厚差太大,框形件中间的加强筋太薄或太细小〕;装炉方法不当或下水方向不对;炉温不均匀,使铸件温度不均匀等。
消除与预防的方法是:减慢升温速度或采取等温淬火工艺;提高淬火介质温度或换成冷却速度慢的淬火介质;在壁厚或薄壁部位涂敷涂料或在薄壁部位包覆石棉等隔热材料;采用专用防开裂的淬火夹具,并选择正确的下水方向。
热处理对铸造铝合金材料的热导率和电导率的影响分析

热处理对铸造铝合金材料的热导率和电导率的影响分析热处理是一种常见的金属加工方法,可通过改变金属的组织结构和性能来满足特定的工程需求。
本文将重点分析热处理对铸造铝合金材料的热导率和电导率的影响。
一、热处理对铝合金材料的热导率的影响热导率是材料导热性能的指标之一。
对于铸造铝合金材料,热处理可以显著影响其热导率。
具体分析如下:1. 固溶处理固溶处理是铝合金热处理的常见方法之一,主要目的是通过固溶处理来溶解材料中的固溶体和析出相,从而调整材料的组织结构和性能。
在固溶处理过程中,高温加热可以促使固溶体中的溶质原子进入固溶体晶格,从而增加晶格的热导率。
此外,固溶处理还会通过晶格缺陷的消除和晶粒尺寸的细化,使材料的热导率得到提高。
2. 相转变处理相转变处理是指金属材料在经历一系列热处理过程后,从一种晶体结构转变为另一种晶体结构的过程。
对于铸造铝合金材料,相转变处理可以改变材料的组织结构和晶格形态,从而对热导率产生显著影响。
例如,在固溶处理的基础上,通过人工时效处理可以使材料中的少量溶质原子析出为细小的弥散相颗粒,这会显著增加材料的热导率。
二、热处理对铝合金材料的电导率的影响电导率是材料导电性能的指标之一,对于铝合金材料的应用十分重要。
热处理对铝合金材料的电导率也有着不可忽视的影响,具体分析如下:1. 凝固过程中的稀溶质元素在铸造铝合金材料的凝固过程中,稀溶质元素的添加可以显著影响材料的电导率。
例如,在凝固过程中添加少量的微合金化元素,如Cr、Zr等,可以有效提高材料的电导率。
这是因为这些微合金元素与铝发生化学反应,形成稳定的间隙溶质原子或弥散相颗粒,从而显著增加材料的电导率。
2. 热处理对晶体结构的影响热处理可以通过改变铝合金材料的晶体结构来影响材料的电导率。
例如,在固溶处理和时效处理过程中,溶质原子的扩散和分布会引起晶体的再结晶,从而改变晶体的结构和形态。
这种晶体结构的变化会影响电子在材料中的传导,进而影响材料的电导率。
铸造铝合金热处理标准
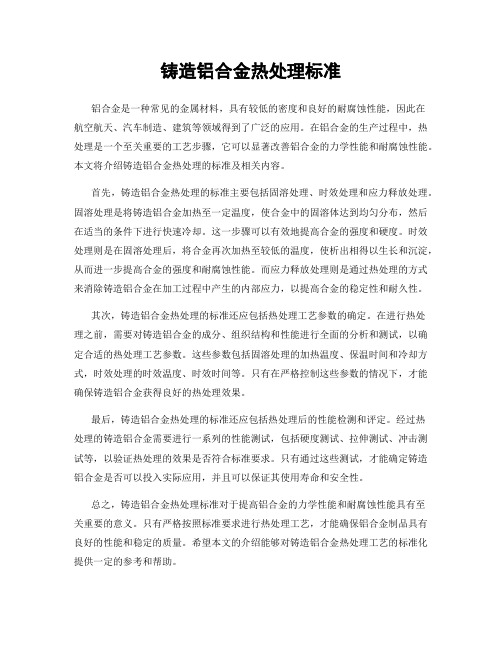
铸造铝合金热处理标准铝合金是一种常见的金属材料,具有较低的密度和良好的耐腐蚀性能,因此在航空航天、汽车制造、建筑等领域得到了广泛的应用。
在铝合金的生产过程中,热处理是一个至关重要的工艺步骤,它可以显著改善铝合金的力学性能和耐腐蚀性能。
本文将介绍铸造铝合金热处理的标准及相关内容。
首先,铸造铝合金热处理的标准主要包括固溶处理、时效处理和应力释放处理。
固溶处理是将铸造铝合金加热至一定温度,使合金中的固溶体达到均匀分布,然后在适当的条件下进行快速冷却。
这一步骤可以有效地提高合金的强度和硬度。
时效处理则是在固溶处理后,将合金再次加热至较低的温度,使析出相得以生长和沉淀,从而进一步提高合金的强度和耐腐蚀性能。
而应力释放处理则是通过热处理的方式来消除铸造铝合金在加工过程中产生的内部应力,以提高合金的稳定性和耐久性。
其次,铸造铝合金热处理的标准还应包括热处理工艺参数的确定。
在进行热处理之前,需要对铸造铝合金的成分、组织结构和性能进行全面的分析和测试,以确定合适的热处理工艺参数。
这些参数包括固溶处理的加热温度、保温时间和冷却方式,时效处理的时效温度、时效时间等。
只有在严格控制这些参数的情况下,才能确保铸造铝合金获得良好的热处理效果。
最后,铸造铝合金热处理的标准还应包括热处理后的性能检测和评定。
经过热处理的铸造铝合金需要进行一系列的性能测试,包括硬度测试、拉伸测试、冲击测试等,以验证热处理的效果是否符合标准要求。
只有通过这些测试,才能确定铸造铝合金是否可以投入实际应用,并且可以保证其使用寿命和安全性。
总之,铸造铝合金热处理标准对于提高铝合金的力学性能和耐腐蚀性能具有至关重要的意义。
只有严格按照标准要求进行热处理工艺,才能确保铝合金制品具有良好的性能和稳定的质量。
希望本文的介绍能够对铸造铝合金热处理工艺的标准化提供一定的参考和帮助。
铸造铝合金热处理

铸造铝合金热处理铝合金是一种重要的结构材料,具有优良的力学性能和耐腐蚀性能。
为了进一步提高铝合金的性能,通常需要进行热处理。
铸造铝合金热处理是指将铸造铝合金加热到一定温度,保持一段时间后进行冷却处理的过程。
铸造铝合金热处理的目的主要有以下几点:1.改善材料的力学性能:通过热处理,可以使铝合金的强度、硬度和耐磨性得到提高,从而满足不同工程应用的要求。
2.消除材料内部的应力:在铝合金的铸造过程中,由于冷却速度不均匀等原因,会产生内部应力。
热处理可以通过自然回火或人工回火的方式,消除这些内部应力,提高材料的稳定性和可靠性。
3.改善材料的耐腐蚀性能:铝合金在热处理过程中,会形成一种致密的氧化膜,可以有效地提高材料的耐腐蚀性能,延长使用寿命。
铸造铝合金热处理的过程通常包括以下几个步骤:1.加热:将铸造铝合金件放入炉中进行加热,使其达到所需的热处理温度。
加热温度和时间的选择取决于铝合金的成分和要求的性能。
2.保温:在加热到所需温度后,保持一段时间,使铝合金内部的组织达到均匀的热平衡状态。
保温时间的长短也是影响热处理效果的重要因素之一。
3.冷却:根据具体的要求,选择适当的冷却方式。
常用的冷却方式有水淬、油淬和自然冷却等。
不同的冷却方式对于铝合金的性能影响也不同。
铸造铝合金热处理过程中需要注意以下几点:1.温度控制:加热过程中需要严格控制温度,避免温度过高或过低,以免对铝合金的性能产生不良影响。
2.保温时间:保温时间的长短直接影响铝合金的组织和性能。
过长或过短的保温时间都会导致热处理效果不理想。
3.冷却速度:不同的冷却速度会对铝合金的组织和性能产生不同的影响。
需要根据具体的要求选择合适的冷却方式和速度。
铸造铝合金热处理的效果主要通过显微组织观察、硬度测试和力学性能测试等手段来评价。
通过这些测试可以了解材料的晶粒尺寸、相组成等信息,从而判断热处理是否达到预期的效果。
铸造铝合金热处理是提高铝合金性能的重要手段,通过加热、保温和冷却等过程,可以改善材料的力学性能、消除内部应力、提高耐腐蚀性能等。
- 1、下载文档前请自行甄别文档内容的完整性,平台不提供额外的编辑、内容补充、找答案等附加服务。
- 2、"仅部分预览"的文档,不可在线预览部分如存在完整性等问题,可反馈申请退款(可完整预览的文档不适用该条件!)。
- 3、如文档侵犯您的权益,请联系客服反馈,我们会尽快为您处理(人工客服工作时间:9:00-18:30)。
1.铸造铝合金热处理的特点和目的
前面提到,铸造铝合金的金相组织比变形铝合金的金相组织粗大,因而在热处理时也有所不同。
前者保温时间长,一般都在2h以上,而后者保温时间短,有的只要几十分钟。
因为金属型铸造、低压铸造、差压铸造的铸件是在比较大的冷却速度和压力下结晶凝固的,其结晶组织比石膏型铸造、砂型铸造的铸件细很多,故其热处理的保温时间也短很多。
铸造铝合金与变形铝合金的另一不同点是壁厚不均匀,有异形截面或内通道等复杂结构形状,为保证热处理时不变形或开裂,有时还要设计专用夹具予以保护,并且淬火介质的温度也比变形铝合金高,故一般多采用
人工时效来缩短热处理周期和提高铸件的性能。
铸造铝合金热处理的目的是,提高力学性能和耐腐蚀性能,稳定尺寸,改善切削加工性和焊接性等工艺性能。
因为许多铸态铝合金的力学性能都不能满足使用要求,除Al-Si系的ZL102、Al-Mg 系的ZL302和Al-Zn系的ZL401合金外,其余的铸造铝合金都要通过热处理来进一步提高铸件的力学性能和其他使用性能。
其具体作用有以下几个方面:
1)消除由于铸件结构(如壁厚不均匀、转接处厚大)等原因使铸件在结晶凝固时因冷却速度不均匀所造成的内应力;
2)提高合金的强度和硬度,改善金相组织,保证合金有一定的塑性和切削加工性能、焊接性能; 3)稳定铸件的组织和尺寸,防止和消除高温相变而使体积发生变化;
4)消除晶间和成分偏析,使组织均匀化。
2.铸造铝合金热处理方法及操作技术要点
(1)热处理方法铸造铝合金的热处理,目前有退火、淬火(固溶处理)、时效和循环处理等工艺,分述如下:
1)退火。
退火的作用是消除铸件的铸造应力和机械加工引起的内应力,稳定加工件的形状和尺寸,并使Al-Si系合金的部分Si晶体球状化,改善合金的塑性。
其工艺是:将铝合金铸件加热到280~300℃,保温2~3h,随炉冷却到室温,使固溶体慢慢发生分解,析出的第二质点聚集,从而消除铸件的内应力,达到稳定尺寸、提高塑性、减少变形的目的。
热处理状态代号为T2。
2)淬火。
淬火也叫固溶处理或急冷处理。
其工艺是:将铝合金铸件加热到较高的温度(一般在接近于共晶体的熔点,大多在500℃以上),保温2h以上,使合金内的可溶相充分溶解。
然后,急速淬人60~100℃的水中,由于铸件受到急冷,使其在合金中得到最大限度溶解的强化相固定并保存到室温。
3)时效。
其工艺是:将经过淬火的铝合金铸件加热到某个温度,保温一定时间出炉空冷到室温,使过饱和的固溶体分解,让合金基体组织稳定。
合金在时效过程中,大致需经过几个阶段:随着温度的上升和时间的延长,过饱和固溶体点阵内原子的重新组合,生成溶质原子富集区(称为G-PⅠ区);随着G-PⅠ区消失,第二相原子按一定规律偏聚并生成G-PⅡ区,之后生成亚稳定的第二相(过渡相);大量的G-P II区和少量的亚稳定相结合以及亚稳定相转变为稳定相、第二相质点聚集几个阶段。
时效处理又分为自然时效和人工时效两大类。
自然时效是在室温下进行时效强化的处理。
人工时效又分为不完全人工时效、完全人工时效、过时效三种。
①不完全人工时效。
将铸件加热到150 ~ 170℃(较低温度下),保温3 ~ 5h,以获得较好的抗拉强度、良好的塑性和韧性,但耐蚀性降低。
②完全人工时效。
将铸件加热到175~185℃(较高温度下),保温5~24h,以获得足够的抗拉强度(即最高的硬度),但伸长率降低。
③过时效。
也称稳定化回火。
其工艺是:将铸件加热到190~230℃,保温4~9h,使强度有所下降,塑性有所提高,以获得较好的抗应力腐蚀能力。
4)循环处理。
把铝合金铸件冷却到零下某个温度(如一50℃,—70℃或一195℃)并保温一定时间,再把铸件加热到350℃以下,使合金中的固溶体点阵反复收缩和膨胀,并使各相的晶粒发生少量位移,以使这些固溶体结晶点阵内的原子偏聚区和金属间化合物的质点处于更加稳定的状态,从而达到产品零件尺寸、体积更加稳定。
这种反复加热、冷却的热处理工艺,即循环处理,仅适于处理在使用中要求尺寸很稳定、极精密的零件(如检测仪器上的某些零件);一般铸件均不作这种处理。
(2)热处理操作技术要点
1)应根据铸件结构形状、尺寸、合金特性等制定的热处理工艺进行热处理。
2)热处理前应检查热处理设备、辅助设备、仪表等是否合格和正常,炉膛各处的温度差是否在规定的范围之内(±5℃)。
3)装炉前铸件应吹砂或冲洗,应无油污、脏物、泥土,合金牌号不应相混。
4)形状易产生变形的铸件应放在专用的底盘或支架上,不允许有悬空的悬壁部分。
5)检查铸件性能的单铸或附铸试棒应随工件一起同炉热处理,以真实反映铸件的性能。
6)在保温期间应随时检查、校正炉膛各处温度,防止局部高温或烧化。
7)在断电后短时间不能恢复时,应将在保温中的铸件迅速出炉淬火,等恢复正常后,再装炉、保温和进行热处理。
8)在盐槽中淬过火的铸件,应在淬火后立即用热水冲洗,清除残盐,防止腐蚀。
9)发现淬火后铸件变形,应立即予以校正。
10)需要时效处理的铸件,应在淬火后0.5h内进行时效处理。
11)如经热处理后发现性能不合格,可重复进行热处理,但次数不得超过两次。
3.铸造铝合金热处理状态代号和工艺参数
(1)铸造铝合金热处理状态代号、状态名称及其目的与应用见表2-29.
(2)部分铸造铝合金热处理工艺参数常用铸造铝合金(27种)的热处理工艺参数,将在第6章作介绍,此处从略。
除此之外的部分铸造铝合金热处理工艺参数,也是几十年生产实践的总结,现介绍如下,见表2-30。
①T1一T8含义见表2-29。
4.铸造铝合金热处理质量缺陷及其消除与预防
铝合金铸件热处理后常见的质量问题有:力学性能不合格、变形、裂纹、过烧等缺陷,对其产生原因和消除与预防办法分述如下。
(1)力学性能不合格通常表现为退火状态伸长率(δ5)偏低,淬火或时效处理后强度和伸长率不合格。
其形成的原因有多种:如退火温度偏低、保温时间不足,或冷却速度太快;淬火温度偏低、保温时间不够,或冷却速度太慢(淬火介质温度过高);不完全人工时效和完全人工时效温度偏高,或保温时间偏长;合金的化学成分出现偏差等。
消除这种缺陷,可采取以下方法:再次退火,提高加热温度或延长保温时间;提高淬火温度或延长保温时间,降低淬火介质温度;如再次淬火,则要调整其后的时效温度和时间;如成分出现偏差,则要根据具体的偏差元素、偏差量,改变或调整重复热处理的工艺参数等。
(2)变形与翘曲通常在热处理后或随后的机械加工过程中,反映出铸件尺寸、形状的变化。
产生这种缺陷的原因是:加热升温速度或淬火冷却速度太快(太激烈);淬火温度太高;铸件的设计结构不合理(如两连接壁的壁厚相差太大,框形结构中加强筋太薄或太细小);淬火时工件下水方向不当及装料方法不当等。
消除与预防的办法是:降低升温速度,提高淬火介质温度,或换成冷却速度稍慢的淬火介质,以防止合金内产生残余应力;在厚壁或薄壁部位涂敷涂料或用石棉纤维等隔热材料包覆薄壁部位;根据铸件结构、形状选择合理的下水方向或采用专用防变形的夹具;变形量不大的部位,则可在淬火后立即予以矫正。
(3)裂纹表现为淬火后的铸件表面用肉眼可以看到明显的裂纹,或通过荧光检查肉眼看不见的微细裂纹。
裂纹多曲折不直并呈暗灰色。
产生裂纹的原因是:加热速度太快,淬火时冷却太快(淬火温度过高或淬火介质温度过低,或淬火介质冷却速度太快);铸件结构设计不合理(两连接壁壁厚差太大,框形件中间的加强筋太薄或太细小);装炉方法不当或下水方向不对;炉温不均匀,使铸件温度不均匀等。
消除与预防的办法是:减慢升温速度或采取等温淬火工艺;提高淬火介质温度或换成冷却速度慢的淬火介质;在壁厚或薄壁部位涂敷涂料或在薄壁部位包覆石棉等隔热材料;采用专用防开裂的淬火夹具,并选择正确的下水方向。
(4)过烧表现为铸件表面有结瘤,合金的伸长率大大下降。
产生过烧的原因是:合金中的低熔点杂质元素如Cd, Si, Sb等的含量过高;加热不均匀或加热太快;炉内局部温度超过合金的过烧温度;测量和控制温度的仪表失灵,使炉内实际温度超过仪表指示温度值。
消除与预防的办法是:严格控制低熔点合金元素的含量不超标;以不超过3℃/min的速度缓慢升温;检查和控制炉内各区温度不超过±5℃;定期检查和校准温度测控仪表,确保仪表测温、示温、控温准确无误。
(5)表面腐蚀表现为在铸件的表面出现斑纹或块状等,其色泽与铝合金铸件表面明显不同。
产生这种缺陷的原因是:硝盐液中氯化物含量超标(>0.5%)而对铸件表面(尤其是疏松、缩孔处)造成腐蚀;从硝盐槽中取出后没得到充分的清洗,硝盐粘附在铸件表面(尤其是窄缝隙、不通孔、通道中)造成腐蚀;硝盐液中混有酸或碱,或者铸件放在浓酸或浓碱附近受到腐蚀等。
消除与预防的办法是:尽量缩短铸件从炉内移到淬火槽中的时间;检查硝盐中氯化物的含量是否超标,如超标,则应降低其含量,从硝盐槽中加热的铸件应立即用温水或冷水冲洗干净;检查硝盐中酸和碱的含量,如有酸或碱则应中和或停止使用;不要把铝合金铸件放在有浓酸或浓碱的附近。
(6)淬火不均匀表现为铸件的厚大部位(特别是其内部中心)的伸长率和硬度偏低,薄壁部位(特别是其表层)的硬度偏高。
产生这类缺陷的原因是:铸件加热和冷却不均匀,厚大部位冷却和传热较慢。
消除与预防的办法是:重新进行热处理,降低升温速度,延长保温时间,使厚薄部位温度均匀一致;在薄壁部位涂敷保温性的涂料或包覆石棉等隔热性材料,尽量使铸件各部位同时冷却;使厚大部位先下水;换成有机淬火剂,降低冷却速度。