物理气相沉积
物理气相沉积技术

• 在电场E作用下,电子与氩 原子碰撞,电离产生Ar+和 新的电子。
• 新电子飞向衬底,Ar+电场 作用加速飞向阴极靶,以 高能量轰击,发生溅射。
• 靶原子沉积成膜,产生的 二次电子沿EXB所指方向 漂移。碰撞次数增加,二 次电子能量下降,逐渐远 离靶表面,最终沉积在衬 底上。传递能量很小,致 使衬底温升较低。
• ⑤溅射工艺适用于淀积合金,而且具有保持复杂 合金元组分的能力。比如常用的溅射AlSiCu合金中 靶材含有0.5%的Cu,那么淀积的薄膜也含有0.5% 的Cu。
3.溅射镀膜的缺点
• 溅射设备复杂,需要高压装置 • 溅射淀积的成膜速度低,真空蒸发镀膜淀积速率
为0.1~5μm/min,溅射速率为0.01~0.5 μm/min。 • 基片温升较高,易受杂质气体影响。
• 2).汤生放电区:这时,放电电流迅速增加,但是电压变 化不大。
• 3).辉光放电:在汤生放电之后,气体发生电击穿现象,I↑,U↓ • 继续增大电流,放电就会进入正常辉光放电区,显然电流的增大与电压
无关。 • 正常辉光放电时的电流密度比较小,所以溅射不选在这个区,而选在反
常辉光放电区。
• 4).反常辉光放电:I ↑,U ↑,发光仍为辉光(异于正常),增大至f点,不 稳定,I ↑,U ↓,放电系统马上会过渡到电弧放电区。
三、溅射方法
• 具体溅射方法较多。 • 直流溅射,射频溅射,磁控溅射,反应溅射,离
子束溅射,偏压溅射等。
1).直流溅射
• 靶材置于阴极,阳极 为衬底。
• 常用氩气作为工作气 体。
• 溅射电压1~5kV,靶电 流密度0.5mA/cm2,薄 膜淀积速率低于0.1 μm/min
物理气相沉积

图1 真空蒸镀装置示意图 1.衬底加热器;2.衬底;3. 原料;4.料舟;5.真空罩
蒸发源类型
(1)电阻加热蒸发源
选择原则:在所需蒸发温度下不软化,饱和蒸气压小,不发生反应; 一般采用高熔点金属如钨、钽、钼等材质,常作成螺旋丝状或箔舟状,如图2.所示。 特点:结构简单,造价低,使用广泛;存在污染,也不能蒸镀高Tm材料。
4. 二级溅射
影响溅射工艺的主要因素: a.放电气体压强P; b.放电电压VDC; c.放电电流IDC; d.可调参量: IDC ; P; 特点:方法及设备简单;放电不稳, 常因局部放电引起IDC变化;沉 积速率低。 最早采用的一种溅射方法,现在已经渐趋于淘汰。 图4 二极溅射装置示意图
5. 磁控溅射
离,使辉光放电持续不断的进行下去。
3. 溅射机理的两种假说
(1)Hippel理论(1926提出)
离子轰击靶产生的局部高温使靶材料(阴极材料)的局部蒸发,在阳极上沉积制膜。
(2)动能转移机理(Stark,1909,Langmuir, Henschk) (I) 溅射出的原子能量比热蒸发原子能量高一个数量级; (II) 轰击离子存在一个临界能量,低于这个能量,不能产生溅射; (Ⅲ) 溅射系数=溅射原子数/轰击离子数,既与轰击离子的能量有关,也与轰击离子的质量有关; (Ⅳ) 离子能量过高,溅射系数反而下降,可能是因为离子深入到靶材内部,能量没有交给表面附近原子的缘故; (Ⅴ) 溅射原子出射的角分布,对于单晶靶材,粒子主要沿几个方向出射。 最强的出射方向对应于晶格中原子最密集排列的方向,这种现象可用“聚焦碰撞”解释。
极),使其熔化便实现蒸镀。蒸镀时,基片加上负偏压即可从等离
子体中吸引氩离子向其自身轰击,从而实现离子镀。
物理气相沉积(PVD)

控制镀料成分:A1B25, 保证:P A :P B 1: 0 2 0 5 4 :1 A4B1膜料成分 若:一次性加料,A消耗快; ∴ 连续加料,保证熔池料为 A1B25, 从而膜料成分为A4B1;
dP Lv dT TV
(1)
∵ ∴
积分:
VV汽V固 、液V汽P 1R, T
dP dT
PLV RT 2
lnp ALV 1 RT
(2)
图8.2.2 几种材料的蒸气压——温度曲线
(3)蒸发速率和凝结速率
① 蒸发速率Ne:
——热平衡条件下,单位时间内,从蒸发源每单位 面积上射出的平均原子数。
N e1 4n 2 P m k3 .5 T1 13 20 2M P(T 1/cm2·s) (3)
设:物质含A,B成分,MA、MB,PA、PB, 则由(3)式,得 :
NA CA PA MB NB CB PB MA
(14)
改进工艺:
1)选择基片温度,使之有利于凝聚而不是分凝;
2)选用几个蒸发源,不同温度下分别淀积,但控制困难; 3)氧化物,可采用反应蒸镀法,引入活性气体。
4. 蒸发源类型
(1)电阻加热蒸发源
70年代,在阴极溅射基础上发展起来,能有效克服溅射速 率低,电子碰撞使基片温度升高的弱点。
(1)基本原理
在阴极靶面上加一环行磁场,使 BE , 控制二次电子运动轨迹,
电子运动方程: d e (EB)
(16)
dt m
运动轨迹为一轮摆线,电子在靶面上沿着垂直于E、B的方向前进,电 子被束缚在一定的空间内,减少了电子在器壁上的复合损耗;同时,延长 了电子路径,增加了同工作气体的碰撞几率,提高了原子的电离几率,使
物理气相沉积 CVD
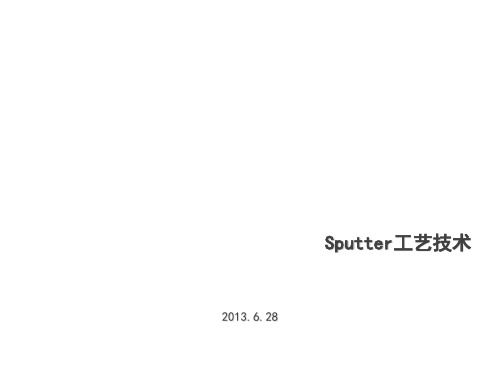
Nodule
ITO 靶材表面突起
3. Sputter常见异常介绍
17
➢Nodule形成与增殖
3. Sputter常见异常介绍
ITO屑吸附在靶材上
ITO Sputter
Nodule
Arcin g
增殖
Nodule爆开形成更多ITO屑Biblioteka Nodule形成18
Sputter 在LTPS 中应用
4. Sputter工艺应用
13
➢Hillock起因分析-应力分析
3. Sputter常见异常介绍
成膜条件: 0.4Pa,110W(DC)
从上图可以看出在薄膜之弹性形变内,薄膜之应力由张应力至压应力呈线性变 化,而当压应力到达薄膜之降服点时(190℃),薄膜产生突起以释放薄膜之压 应力。 薄膜产生Hillock的主要起因是为了释放薄膜应力之产生。
Sputter工艺技术
2013.6.28
Summary
1
1.Sputter工艺介绍
PVD---物理气相沉积技术(Physical Vapor Deposition) ➢定义
物理气相沉积技术(Physical Vapor Deposition,PVD)表示在真空条件下, 采用物理方法,将材料气化成气体原子、分子或电离成离子,并通过气相过程, 在基体表面沉积具有特殊功能薄膜的技术。 ➢沉积基本过程 从原材料中发射粒子(通过蒸发、升华、溅射等过程) 粒子输运到基板(粒子间发生碰撞,产生离化、复合、反应,能量的交换和运 动方向的变化) 粒子在基板上凝结。成核、生长和成膜。 ➢分类
14
Splash
➢产生原因
治具
3. Sputter常见异常介绍
靶材局部散热不均,造成融化滴在基板上
物理气相沉积x

,
汇报人:
目录 /目录
01
点击此处添加 目录标题
04
物理气相沉积 技术的优缺点
02
物理气相沉积 技术概述
05
物理气相沉积 技术的发展趋 势
03
物理气相沉积 技术的应用领 域
06
物理气相沉积 技术的前景展 望
01 添加章节标题
02 物理气相沉积技术概述
物理气相沉积技术的定义
物理气相沉积技术 是一种利用物理方 法将气态物质转化 为固态薄膜的技术。
增强与其他表面处理技术的结合应用如电镀、化学镀等以提高沉积效率和 质量。
开发新型物理气相沉积技术如脉冲电弧放电、激光诱导等离子体等以满足 更广泛的应用需求。
深入研究物理气相沉积的机理和过程控制提高沉积层的均匀性和致密性。
加强与其他表面处理技术的结合应用如电镀、化学镀等以提高沉积效率和 质量。
06
物理气相沉积技术的前 景展望
新能源领域
太阳能电池: 物理气相沉积 技术用于制备 高效太阳能电 池提高光电转
换效率。
锂离子电池: 通过物理气相 沉积技术制备 电极材料提高 锂离子电池的 能量密度和循
环寿命。
燃料电池:利 用物理气相沉 积技术制备质 子交换膜和催 化剂降低燃料 电池的成本和
提高性能。
储能技术:物 理气相沉积技 术在储能领域 也有广泛应用 如超级电容器 和电池储能系
拓展应用领域和提高应用水平
拓展应用领域:随着技术的不断发展物理气相沉积技术的应用领域正在不断拓展例如在新能源、生物医学、 航空航天等领域的应用。
提高应用水平:通过不断的技术创新和改进物理气相沉积技术的应用水平也在不断提高例如在薄膜的均匀性、 附着力、耐久性等方面的提升。
物理沉积法

物理沉积法物理气相沉积法用物理的方法使镀膜材料气化,在基体表面沉积成膜的方法物理气相沉积(Physical Vapor Deposition简称PVD) 是用物理的方法(如蒸发、溅射等)使镀膜材料气化,在基体表面沉积成膜的方法。
除传统的真空蒸发和溅射沉积技术外,还包括近30 多年来蓬勃发展起来的各种离子束沉积,离子镀和离子束辅助沉积技术。
其沉积类型包括: 真空蒸镀、溅射镀、离子镀等。
物理气相沉积技术虽然五花八门,但都必须实现气相沉积三个环节,即镀料(靶材) 气化一气相输运一沉积成膜。
中文名物理气相沉积法沉积类型真空蒸镀、溅射镀、离子镀等各种沉积技术的不同点主要表现为在上述三个环节中能源供给方式不同,同一气相转变的机制不同,气粒子形态不同,气相粒子荷能大小不同,气相粒子在输运过程中能量补给的方式及粒子形态转变不同,镀料粒子与反应气体的反应活性不同,以及沉积成膜的基体表面条件不同而已。
与化学气相沉积相比,主要优点和特点如下:I)镀膜材料广泛,容易获得:包括纯金属、合金、化合物,导电或不导电,低熔点或高熔点,液相或固相,块状或粉末,都可以使用或经加工后使用。
2)镀料汽化方式:可用高温蒸发,也可用低温溅射。
3)沉积粒子能量可调节,反应活性高。
通过等离子体或离子束介人,可以获得所需的沉积粒子能量进行镀膜,提高膜层质量。
通过等离子体的非平衡过程提高反应活性。
4)低温型沉积:沉积粒子的高能量高活性,不需遵循传统的热力学规律的高温过程,就可实现低温反应合成和在低温基体上沉积,扩大沉积基体适用范围。
可沉积各类型薄膜:如金属膜、合金膜、化合物膜等。
5)无污染,利于环境保护。
物理气相沉积技术已广泛用于各行各业,许多技术已实现工业化生产。
其镀膜产品涉及到许多实用领域。
物理气相沉积法名词解释

物理气相沉积法名词解释
物理气相沉积法(Physical相沉积法)是一种化学沉积技术,通过物理过程
将化学物质沉积到基材表面,从而制备出具有特殊结构或功能的膜、涂层或颗粒。
物理气相沉积法通常涉及三个基本步骤:气相沉积反应、沉积时间和冷却。
其中,气相沉积反应是指将化学物质溶解在气相中,并通过气相流在基材表面形成沉积物的过程。
沉积时间是指沉积物从气相中形成到脱落的时间。
冷却则是指使用气流或喷淋等方式将沉积物表面降温,从而使其更加稳定。
物理气相沉积法的应用非常广泛,包括制备膜材料、涂层材料、纳米材料、生物材料、催化剂等。
其中,膜材料是物理气相沉积法最为著名的应用之一。
膜材料可以用于水处理、废气处理、药物分离等领域,具有高效过滤、分离、浓缩等功能。
此外,物理气相沉积法还可以用于制备纳米材料、生物材料等,具有治疗疾病、提高材料性能等潜在应用价值。
除了应用价值外,物理气相沉积法还存在一些挑战和限制。
例如,沉积物质量的影响因素很多,包括气相组成、反应条件、温度、压力等。
因此,在实际应用中需要不断调整反应条件,以达到最优的沉积效果。
此外,由于沉积物表面通常需要经过清洗和表征等步骤,因此需要对沉积物表面进行处理,以获得所需的表征结果。
总之,物理气相沉积法是一种制备高性能材料的有效方法,具有广泛的应用前景和研究价值。
随着技术的不断发展和完善,相信它将在未来发挥更加重要的作用。
物理气相沉积
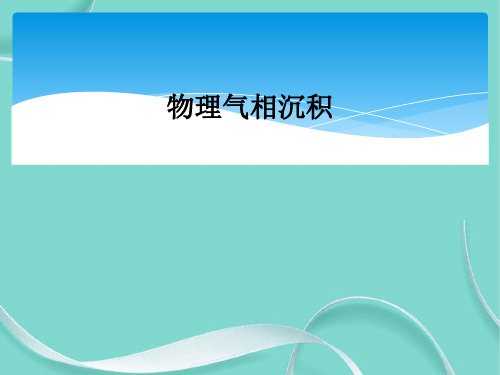
工料件;不带后电者,真包空括条件电下、金属磁加、热蒸声发、沉积光到等工件功表能面薄 无物膜气理材孔 气,相料但沉等膜积层。(PV缺D陷) 较多。
而物理气相沉积,并不需要发生化学反应,其只是通过各种方法(如加热蒸发,溅射等等),将源材料气化,然后沉积于基片表面成
膜,沉积前会后的被物溅质都射是出一样来的而。 沉积到工件表面。
低温时密度较小但表面平滑
物等理能气 量相形沉式溅积产生(P射h气ys镀相ica原l膜V子ap纯、or分度De子p高、osi离t、io子n,均(气P态V匀D,)是,等指离而把子固且态态)基进(液行板态输)温镀运料,度通在低过固高态。温表因蒸面发上此、沉适溅积射凝用、聚性电(包子广括束与,、其可等他离沉反子应积体气、纯相离物金子质束进、行激化光学束反、应电生弧
气孔少,但混入溅射气体较多
工4、件离为基子阳镀片极膜,温(靶镀升材膜为较材阴料高极蒸,,发利、易用离氩受化离、杂子加溅质速射、气,沉靶体积材)影原子响击。出而沉积。
物④理无气环溅相境沉射污积染的(P;V用D) 途
因此适溅用性射广薄, 可膜沉积按纯其金属不、同合金的或功化合能物和。 应用可 原会大理被致是 溅充射分氩出为(来Ar而机)气沉械的积真到功空工能条件件表膜下面和,。使物氩理气进功行能辉光膜放两电,大(Ar)
★ 缺点:设备复杂,一次 较大。
(1)真空蒸镀
真空蒸镀基本原理是在真空条件下,使金属、金属合金或化合物蒸发,然后 沉积在基体表面上,蒸发的方法常用电阻加热,高频感应加热,电子束、激 光束、离子束高能轰击镀料,使蒸发成气相,然后沉积在基体表面。
真空蒸镀的设备相对简单, 工艺操作容易, 可镀材料广, 镀膜纯洁, 广泛用于光 学、电子器件和塑料制品的表面处理。缺点是膜一基结合力弱,镀膜不耐磨, 并有方向性。
- 1、下载文档前请自行甄别文档内容的完整性,平台不提供额外的编辑、内容补充、找答案等附加服务。
- 2、"仅部分预览"的文档,不可在线预览部分如存在完整性等问题,可反馈申请退款(可完整预览的文档不适用该条件!)。
- 3、如文档侵犯您的权益,请联系客服反馈,我们会尽快为您处理(人工客服工作时间:9:00-18:30)。
五 纳米加工平台现有设备介绍
热蒸发操作注意事项
不要用坚硬物品敲击触摸屏。 如果系统有异常声音或气味应马上停止工作,关闭总 电源,查出问题后再工作。 如果系统长期不用,要使真空腔处于真空状态关闭机 器。 充气阀充气完毕后要及时关闭。 单独用一个真空室工作时,一定要保持另一个真空室 处于低真空状态,不可是大气压状态。 束源炉在升温的过程中通过面板上的调节旋钮调节电 流不能超过3A,蒸发过程中温度不稳定可增加电流。 束源炉的温度或蒸发舟的温度必须降低到100度以下才 可关闭真空系统,开启真空室。
三 PVD薄膜沉积中常见问题
基片与蒸发源间的距离 镀膜时的压力 基片加偏压
四 PVD薄膜的表征
PVD薄膜的表征
电学性能:四探针 粘附性:划痕法 内应力:X射线衍射法 膜厚:台阶仪 表面粗糙度:AFM
21
五 纳米加工平台现有设备介绍
磁控溅射-LAB18
22
五 纳米加工平台现有设备介绍
LAB18系统组成 控 制 系 统 电源 加热 抽 真 空 系 统
Thick(A)
39
五 纳米加工平台现有设备介绍
ei-5z操作注意事项
开机前注意检查水电气正常; 做工艺之前检查坩埚源的状态,如源不够及 时通知相应工作人员; 禁止在低真空条件下打开电子枪电源; 蒸发前注意晶振片的频率和所要蒸发材料的 量 蒸镀过程中,注意观察所蒸发的材料是否正 确,电子束斑位置; 禁止非授权操作人员执行开机和关机步骤。
3
一 PVD薄膜沉积的基本原理
PVD技术的分类
物理气相沉积(PVD) 真空蒸镀 电子束(EB)蒸发 热蒸发 溅射镀膜 直流溅射 射频溅射 脉冲直流溅射 离子镀
4
一 PVD薄膜沉积的基本原理
真空蒸镀
真空蒸镀是将镀料在真空中加热、蒸发,使蒸 发的原子或原子团在温度较低的基板上凝结, 形成薄膜。 热蒸发、EB蒸发。
五 纳米加工平台现有设备介绍
LAB18现有靶材 Au、Pt、Ti、Ni、V、AlN、PZT、Al、 Cr、SiO2、Ag、ITO 、Fe、Pd、Ge、 Cu、W、TiN
五 纳米加工平台现有设备介绍
LAB18 工艺参数
工艺条件
本底真空 序 号 1 靶材 2E-6 预溅 时间 120 温度 22 衬底转速 20 压 气 力 流量 体 (mT orr) Ar 4 19.2 工作真 空 2.8E-3 溅射 功率 电压 电流 时间 (W) (V) (A) 300 200 426 0.46
真空腔体
冷却系统
五 纳米加工平台现有设备介绍
LAB18 Vacuum界面
24
五 纳米加工平台现有设备介绍
LAB18 Deposition界面
25
五 纳米加工平台现有设备介绍
LAB18 腔体内部
26
五 纳米加工平台现有设备介绍
LAB 18的性能指标
真空度:2E-7Torr 工艺气体:Ar、O2、N2 衬底升温:450℃ 反溅功率:100W 直流源:500W 射频源:300W 脉冲直流:300W 厚度均匀性:< ±5% 可加工样品尺寸:6寸和4寸每次一片,2寸每 次4片,小样品夹具
PVD(物理气相沉积)薄 膜工艺及设备介绍
赵德胜
1
主要内容
一 二 三 四 五 PVD薄膜沉积的基本原理 PVD薄膜沉积各种方式的比较 PVD薄膜沉积中常见问题 PVD薄膜的表征 纳米加工平台现有设备介绍
2
一 PVD薄膜沉积的基本原理
在半导体行业PVD主要用于金属化
物理气相沉积(Physical Vapor Deposition, PVD)技术:表示在真空条件下,采用物理方 法,将材料源-固体或液体表面气化成气体原 子、分子或部分电离成离子,并通过低压气体 (或等离子体)过程,在基体表面沉积具有特 殊功能薄膜的技术。
12
一 PVD薄膜沉积的基本原理
离子镀:在真空条件 下,利用气体放电使 气体或蒸发物质离化 ,在气体离子或被蒸 发物质离子轰击作用 的同时,把蒸发物或 其反应物蒸镀在基片 上。 离子镀把辉光放电、 等离子体技术与真空 蒸发镀膜技术结合在 一起
一 PVD薄膜沉积的基本原理
物理气相沉积技术基本原理的三个过程
电极 约5MHZ
晶体
膜厚
蒸气
34
五 纳米加工平台现有设备介绍
ei-5z腔体内部
35
五 纳米加工平台现有设备介绍
ei-5z主界面
36
五 纳米加工平台现有设备介绍
ei-5z的性能指标
真空度:5E-6Pa 基片最高温度:300℃ 电子枪功率:8KW 厚度均匀性:< ±5% 可加工样品尺寸:6寸每次8片,4寸每次8片, 2寸每次180片,以及小样品夹具 现有蒸发源:Au、Ti、Ni、Cr、Au88Ge12、Al 、In、Sn、Ag、Pd
38
五 纳米加工平台现有设备介绍
Power(%)
40 30 20 10 0 5 0 50 100 150 200
Time(S)
Power
250
Rate
Rate(A/S)
0 0 50 100 150 200 250 400 200 0 0 50 100 150 200 250
Time(S) Time(S) Thick
一 PVD薄膜沉积的基本原理
什么是辉光放电?
辉光放电是指在稀薄气体中,两个电极之间加 上电压时产生的一种气体放电现象。
10
一 PVD薄膜沉积的基本原理
直流溅射:适用于金 属材料 射频溅射:是适用于 各种金属和非金属材 料的一种溅射沉积方 法
一 PVD薄膜沉积的基本原理
脉冲溅射:一种用于消除直流反应溅射 中异常放电技术。 反应溅射:在溅射过程中,在工艺气体 中混入活性气体,在溅射过程中发生反应 生成氧化物、氮化物等的溅射方式。
31
五 纳米加工平台现有设备介绍
电子束蒸发- ei-5z
操作界面 真空腔体
32
五 纳米加工平台现有设备介绍
ei-5z系统组成 控 制 系 统
膜 厚 控 制 坩 埚 电 子 枪
真空腔体
抽 真 空 系 统
冷却系统
五 纳米加工平台现有设备介绍
膜厚控制
监视蒸镀速率的方法 是利用共振的石英晶 体。结晶的石英晶体 具有压电性的,在共 振频率时,石英晶体 产生震荡电压,晶体 放大并回授以驱动晶 体,就可监督蒸镀速 率。
五 纳米加工平台现有设备介绍
ei-5z工艺参数
材料名称 High Vol(KV) 本底真空(Pa) 蒸发温度(℃) 蒸发功率(%) 蒸发速率(A/S) 蒸发厚度(A) Ti 7.5 8E-5 23 28 2 50 坩埚号 X/Y—Position X/Y—Sweep 衬底转(r/m) 预蒸发时间 Gain/Time-C/Limit Tooling 5 3 3 8 2min 5 85 10 3 3.5 0
40
五 纳米加工平台现有设备介绍
热蒸发设备外观
液晶显示器 腔体
加热控制显示
41
五 纳米加工平台现有设备介绍
热蒸发真空示意图
42
五 纳米加工平台现有设备介绍
• 热蒸发操作界面
五 纳米加工平台现有设备介绍
热蒸发的性能指标
真空度:5E-6Pa 基片最高温度:200℃ 可蒸发材料:Al、Au、In、Ag、Ni等金 属
15
三 PVD薄膜沉积中常见问题
如何提高PVD薄膜 的粘附性
基片的预处理 水洗 有机溶剂清洗 超声波清洗 蚀刻
三 PVD薄膜沉积中常见问题
镀膜前对基片进行离子轰击
三 PVD薄膜沉积中常见问题
镀膜时的加热 衬底和膜之间加 入接触金属(Cr、 Ni、Ti、W等)
三 PVD薄膜沉积中常见问题
如何在大台阶表面沉积厚度均匀的 薄膜
镀料的气化 镀料原子、分子或离子的迁移 镀料原子、分子或离子在基体上凝结
14
二 PVD薄膜沉积各种方式的比较
真空蒸镀、溅射镀膜和离子镀的比较
方法
真空 蒸镀 溅射 镀膜 离子 镀
优点
工艺简便,纯度高,通 过掩膜易于形成所需要 的图形 附着性能好,易于保持 化合物、合金的组分比
缺点
蒸镀化合物时由于热分解现象 难以控制组分比,低蒸气压物 质难以成膜 需要溅射靶,靶材需要精制, 而且利用率低,不便于采用掩 膜沉积 附着性能好,化合物、 装置及操作均较复杂,不便于 合金、非金属均可成膜 采用掩膜沉积
五 纳米加工平台现有设备介绍
三种设备的比较
性质 沉积 粘附 均匀 致密 速率 性 性 性 方法 LAB 18 ei-5z 热蒸发 可控 可控 优 良 优 优 良 优 良 差 可控 可控 差 高 高 低
46
膜厚 控制
成本
不可 一般 控
上机培训价格(暂定)
• 溅射(LAB 18):450元/人 • 电子束蒸发(ei-5z):450元/人 • 热蒸发:350元/人
熔融的 蒸镀源 电子束
水 水冷 坩埚
一 PVD薄膜沉积的基本原理
溅射镀膜
溅射-用带有几十电子伏以上动能的粒子或粒 子束照射固体表面,靠近固体表面的原子会获 得入射粒子所带能量的一部分进而向真空中放 出,这种现象称为溅射。
一 PVD薄膜沉积的基本原理
溅射镀膜
磁控溅射-电子在电场的作用下加速飞向基片 的过程中与氩原子发生碰撞,电离出大量的氩 离子和电子,电子飞向基片,氩离子在电场的 作用下加速轰击靶材,溅射出大量的靶材原子 ,呈中性的靶原子(或分子)沉积在基片上成 膜。
一 PVD薄膜沉积的基本原理
热蒸发原理及特点
热蒸发是在真空状况下,将所要蒸镀的材料 利用电阻加热达到熔化温度,使原子蒸发, 到达并附着在基板表面上的一种镀膜技术。 特点:装置便宜、操作简单广泛用于Au、Ag、 Cu、Ni、In、Cr等导体材料。