天然气液化流程工艺选择优化
液化天然气工艺流程
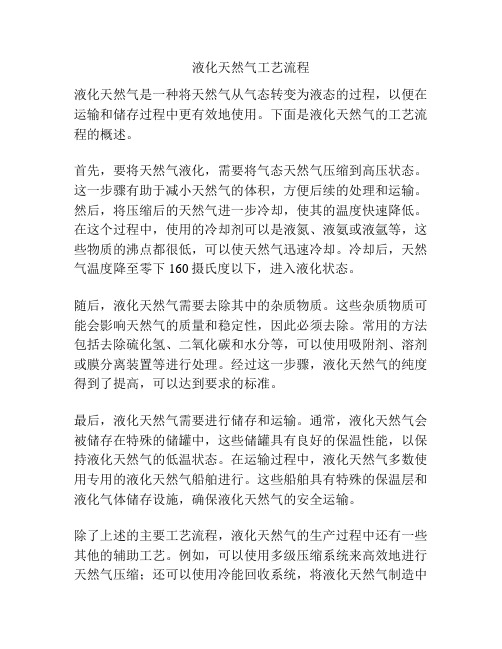
液化天然气工艺流程液化天然气是一种将天然气从气态转变为液态的过程,以便在运输和储存过程中更有效地使用。
下面是液化天然气的工艺流程的概述。
首先,要将天然气液化,需要将气态天然气压缩到高压状态。
这一步骤有助于减小天然气的体积,方便后续的处理和运输。
然后,将压缩后的天然气进一步冷却,使其的温度快速降低。
在这个过程中,使用的冷却剂可以是液氮、液氨或液氩等,这些物质的沸点都很低,可以使天然气迅速冷却。
冷却后,天然气温度降至零下160摄氏度以下,进入液化状态。
随后,液化天然气需要去除其中的杂质物质。
这些杂质物质可能会影响天然气的质量和稳定性,因此必须去除。
常用的方法包括去除硫化氢、二氧化碳和水分等,可以使用吸附剂、溶剂或膜分离装置等进行处理。
经过这一步骤,液化天然气的纯度得到了提高,可以达到要求的标准。
最后,液化天然气需要进行储存和运输。
通常,液化天然气会被储存在特殊的储罐中,这些储罐具有良好的保温性能,以保持液化天然气的低温状态。
在运输过程中,液化天然气多数使用专用的液化天然气船舶进行。
这些船舶具有特殊的保温层和液化气体储存设施,确保液化天然气的安全运输。
除了上述的主要工艺流程,液化天然气的生产过程中还有一些其他的辅助工艺。
例如,可以使用多级压缩系统来高效地进行天然气压缩;还可以使用冷能回收系统,将液化天然气制造中产生的余热回收利用,提高能量利用效率。
此外,液化天然气的解析过程也需要精密控制,以保证解析后天然气的品质和使用效果。
总之,液化天然气的工艺流程是一个复杂而精密的过程,需要高度的技术和设备支持。
通过适当的压缩、冷却、杂质去除和储存运输等工艺处理,可以将天然气转化为液态,方便储存和运输。
液化天然气被广泛应用于能源供应、航运和工业等领域,成为一种重要的替代能源。
天然气处理工艺流程改造及优化
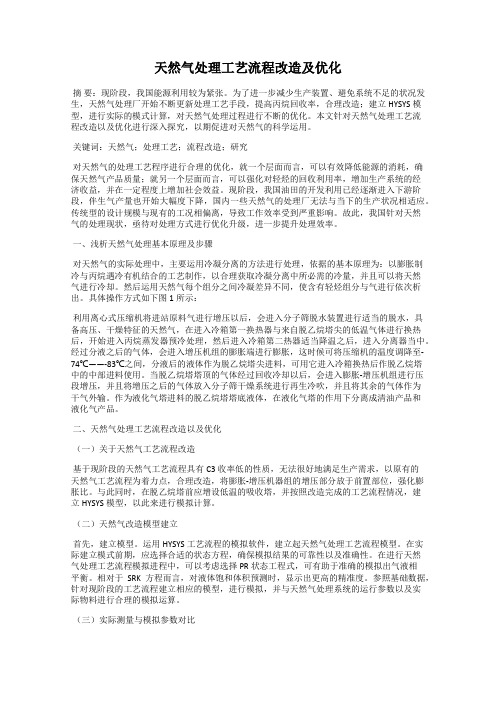
天然气处理工艺流程改造及优化摘要:现阶段,我国能源利用较为紧张。
为了进一步减少生产装置、避免系统不足的状况发生,天然气处理厂开始不断更新处理工艺手段,提高丙烷回收率,合理改造;建立HYSYS模型,进行实际的模式计算,对天然气处理过程进行不断的优化。
本文针对天然气处理工艺流程改造以及优化进行深入探究,以期促进对天然气的科学运用。
关键词:天然气;处理工艺;流程改造;研究对天然气的处理工艺程序进行合理的优化,就一个层面而言,可以有效降低能源的消耗,确保天然气产品质量;就另一个层面而言,可以强化对轻烃的回收利用率,增加生产系统的经济收益,并在一定程度上增加社会效益。
现阶段,我国油田的开发利用已经逐渐进入下游阶段,伴生气产量也开始大幅度下降,国内一些天然气的处理厂无法与当下的生产状况相适应。
传统型的设计规模与现有的工况相偏离,导致工作效率受到严重影响。
故此,我国针对天然气的处理现状,亟待对处理方式进行优化升级,进一步提升处理效率。
一、浅析天然气处理基本原理及步骤对天然气的实际处理中,主要运用冷凝分离的方法进行处理,依据的基本原理为:以膨胀制冷与丙烷遇冷有机结合的工艺制作,以合理获取冷凝分离中所必需的冷量,并且可以将天然气进行冷却。
然后运用天然气每个组分之间冷凝差异不同,使含有轻烃组分与气进行依次析出。
具体操作方式如下图1所示:利用离心式压缩机将进站原料气进行增压以后,会进入分子筛脱水装置进行适当的脱水,具备高压、干燥特征的天然气,在进入冷箱第一换热器与来自脱乙烷塔尖的低温气体进行换热后,开始进入丙烷蒸发器预冷处理,然后进入冷箱第二热器适当降温之后,进入分离器当中。
经过分液之后的气体,会进入增压机组的膨胀端进行膨胀,这时候可将压缩机的温度调降至-74℃——-83℃之间,分液后的液体作为脱乙烷塔尖进料,可用它进入冷箱换热后作脱乙烷塔中的中部进料使用。
当脱乙烷塔塔顶的气体经过回收冷却以后,会进入膨胀-增压机组进行压段增压,并且将增压之后的气体放入分子筛干燥系统进行再生冷吹,并且将其余的气体作为干气外输。
中原油田天然气液化工艺流程优化设计研究
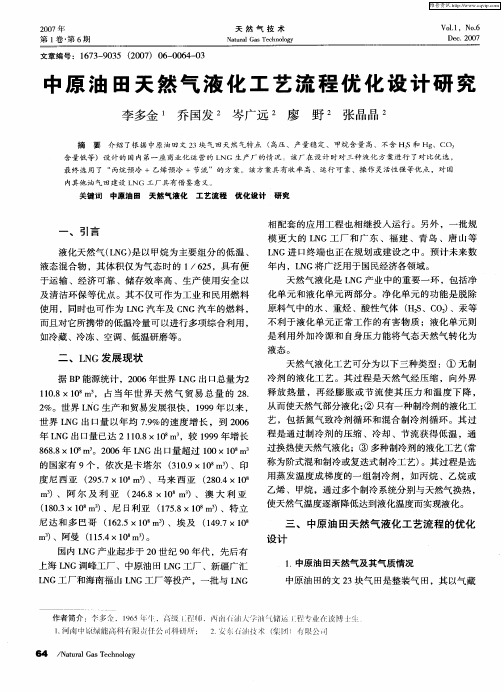
的 国家 有 9个 ,依 次 是 卡塔 尔 (1. 0 3、印 309×18 ) m
度 尼 西 亚 (9 . 2 57×1 )、马 来 西 亚 (8 . 0 0 m3 2 04×1 8 m )、 阿 尔 及 利 亚 ( 4 . 。 2 68×1s )、 澳 大 利 亚 0 m3 (8 - 0 m。 1 03×1 )、尼 日利 亚 (7 . 158×1 3 、特 立 0 m) 尼 达 和 多 巴 哥 (6 . 125×1 ) 0 m3 、埃 及 (4 . 0 197×18 I。、阿曼 ( l . 0 m3。 n ) 1 54×1 )
天 然 气液 化 是 L G产业 中 的重要 一 环 ,包 括 净 N
液化 天 然气 ( N 是 以 甲烷 为主 要 组 分 的低 温 、 L G)
液态混合物 ,其体积仅为气态时 的 1 65 / 2 ,具有便
于运 输 、经 济 可靠 、储 存 效 率 高 、生产 使用 安 全 以 及 清 洁环 保 等 优 点 。其 不 仅 可 作 为 工 业 和 民用 燃 料 使用 ,同 时也 可作 为 L G汽 车 及 C G汽 车 的燃 料 , N N 而且对 它 所携 带 的低 温冷 量 可 以进行 多项 综合 利 用 , 如冷藏 、冷 冻 、空调 、低 温研磨 等 。
维普资讯
2 7钲 00
天 然 气 技 术
Na u a sTe h o o y t r lGa c n l g
Vo . . No6 1 1 .
De .2 7 c 0o
第 1 ・ 6期 卷 第
文章编号:1 7 — 0 5 (0 7 0 — 0 4 0 6 3 9 3 2 0) 6 0 6— 3
冷 剂 的液 化 工 艺 。其 过 程 是 天然 气 经 压 缩 , 向外 界 释 放 热 量 ,再 经 膨 胀 或 节 流 使 其 压 力 和 温 度 下 降 , 从而 使天 然气 部分 液化 ; 只有一 种 制冷剂 的液化工 ② 艺 ,包 括 氮 气 致 冷 剂循 环 和混 合 制 冷 剂 循 环 。其 过 程是 通 过 制 冷 剂 的压缩 、冷却 、节 流 获得 低 温 ,通 过 换热 使 天然气 液化 ;③ 多种 制冷 剂 的液化 工艺 ( 常 称 为 阶式 混 和制 冷或 复迭 式 制 冷工 艺) 。其 过 程是 选 用 蒸 发 温 度 成 梯 度 的一 组 制 冷 剂 ,如 丙烷 、乙烷 或 乙烯 、甲烷 ,通过 多个 制 冷 系统 分别 与 天 然气 换热 , 使 天然气 温 度逐 渐 降低达 到液 化温度 而 实现液 化 。
lng 工艺流程

lng 工艺流程LNG(液化天然气)工艺流程是将天然气转化为液态状态的过程。
液化天然气作为一种清洁、高效的能源,已广泛应用于工业、航运和能源供应等领域。
下面将详细介绍LNG的工艺流程。
LNG的工艺流程通常包括天然气处理、液化、储存和运输等环节。
首先,天然气处理是指将原始天然气中的杂质和杂质物质去除,并使之适合液化的过程。
这一环节对天然气进行除水、除硫、除酸等处理,以获得高纯度的天然气。
一般来说,除硫处理是天然气处理的关键步骤之一,其中最常见的方法是采用酸性氨法。
此外,还需要将天然气中的水分去除,以免在后续液化过程中引起腐蚀和结冰等问题。
在天然气处理完成后,液化过程开始。
液化天然气的核心原理是通过降低天然气的温度将其转化为液态。
常见的液化方法有自然液化法和制冷循环液化法。
自然液化法是通过降低天然气的温度使其达到饱和汽化压力,进而从气态转变为液态。
而制冷循环液化法则是通过制冷剂来降低天然气的温度,使其液化。
制冷剂通常采用液氮或制冷机组来实现。
液化过程完成后,液化天然气被储存起来。
LNG的储存通常使用特殊的储罐,这些储罐由保温层和内胆组成,以保持液化天然气的低温状态。
储罐的设计主要考虑到LNG的膨胀系数和膨胀速度,以及安全性和可持续性等因素。
最后,液化天然气被运输到目的地。
LNG的运输主要有两种方式:海上运输和陆上运输。
在海上运输中,LNG被装载到LNG船上,通过管道或船舶进行运输。
在陆上运输中,LNG通常被装载到特殊的储罐车或储罐,通过公路或铁路进行运输。
总之,LNG的工艺流程包括天然气处理、液化、储存和运输等环节。
通过这一系列的工艺过程,天然气能够转化为液态状态,提供清洁高效的能源供应。
随着LNG的应用越来越广泛,相信其工艺流程也将不断优化和创新。
天然气液化工艺流程分析及其优选
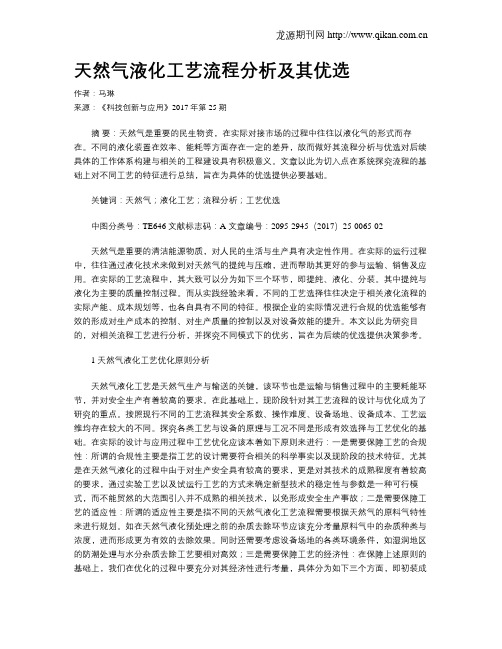
天然气液化工艺流程分析及其优选作者:马琳来源:《科技创新与应用》2017年第25期摘要:天然气是重要的民生物资,在实际对接市场的过程中往往以液化气的形式而存在。
不同的液化装置在效率、能耗等方面存在一定的差异,故而做好其流程分析与优选对后续具体的工作体系构建与相关的工程建设具有积极意义。
文章以此为切入点在系统探究流程的基础上对不同工艺的特征进行总结,旨在为具体的优选提供必要基础。
关键词:天然气;液化工艺;流程分析;工艺优选中图分类号:TE646 文献标志码:A 文章编号:2095-2945(2017)25-0065-02天然气是重要的清洁能源物质,对人民的生活与生产具有决定性作用。
在实际的运行过程中,往往通过液化技术来做到对天然气的提纯与压缩,进而帮助其更好的参与运输、销售及应用。
在实际的工艺流程中,其大致可以分为如下三个环节,即提纯、液化、分装。
其中提纯与液化为主要的质量控制过程。
而从实践经验来看,不同的工艺选择往往决定于相关液化流程的实际产能、成本规划等,也各自具有不同的特征。
根据企业的实际情况进行合规的优选能够有效的形成对生产成本的控制、对生产质量的控制以及对设备效能的提升。
本文以此为研究目的,对相关流程工艺进行分析,并探究不同模式下的优劣,旨在为后续的优选提供决策参考。
1 天然气液化工艺优化原则分析天然气液化工艺是天然气生产与输送的关键,该环节也是运输与销售过程中的主要耗能环节,并对安全生产有着较高的要求。
在此基础上,现阶段针对其工艺流程的设计与优化成为了研究的重点。
按照现行不同的工艺流程其安全系数、操作难度、设备场地、设备成本、工艺运维均存在较大的不同。
探究各类工艺与设备的原理与工况不同是形成有效选择与工艺优化的基础。
在实际的设计与应用过程中工艺优化应该本着如下原则来进行:一是需要保障工艺的合规性:所谓的合规性主要是指工艺的设计需要符合相关的科学事实以及现阶段的技术特征。
尤其是在天然气液化的过程中由于对生产安全具有较高的要求,更是对其技术的成熟程度有着较高的要求,通过实验工艺以及试运行工艺的方式来确定新型技术的稳定性与参数是一种可行模式,而不能贸然的大范围引入并不成熟的相关技术,以免形成安全生产事故;二是需要保障工艺的适应性:所谓的适应性主要是指不同的天然气液化工艺流程需要根据天然气的原料气特性来进行规划。
混合制冷天然气液化工艺模拟及优化研究
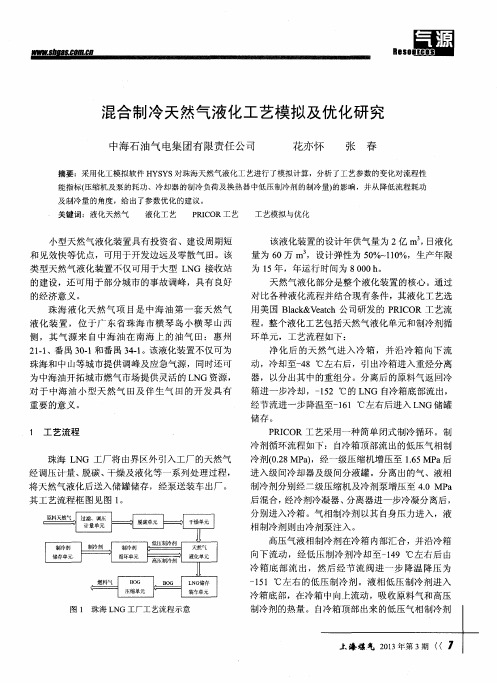
流程 中只 有一 级 压缩机 耗 功
、级 问冷 却 器制 冷
Байду номын сангаас
负荷 Q 及 低压 制冷 剂 的制 冷量 Q 发生 变化 。
类 型 天然 气液 化装 置 不仅 可用 于大 型 L NG 接 收 站 的建 设 ,还 可用 于 部分 城市 的事 故调 峰 ,具有 良好
的经济 意 义 。
天 然气 液化 部 分是整 个 液化 装置 的核 心 。通过 对 比各 种液 化流 程 并结合 现 有条件 ,其液 化工 艺选
用 美 国 Bl a c k &V e a t c h公 司研 发 的 P R I C O R 工 艺流
小型 天 然气 液化 装置 具有 投 资省 、建 设 周期 短
和见 效快 等优 点 ,可用 于 开发 边远及 零 散气 田。该
该液 化装 置 的设计 年供 气量 为 2亿 1 T 1 , 日液 化
量为 6 O万 r n ,设 计弹性 为 5 0 %~ 1 1 0 %,生产 年 限 为l 5年 ,年运 行 时 间为 8 0 0 0 h 。
上 海煤 气 2 0 1 3 年第 3 期 ( (7
R 。 s o 嗣 { 黜
。
说 明:根据 目前 的原料 气组 分 ,预计 装 置 中不 会 有 重烃产 生 ,故分 析 时做 了简 化 处理 ,去掉 重烃
分 离器 ,冷 箱 用一 个 多股流 换热 器 代替 。 3 . 1 天然 气入 口压 力 和温 度 的影 响 3 . 1 . 1 天然气 入 口压 力 的影 响
液化天然气应用的工艺流程
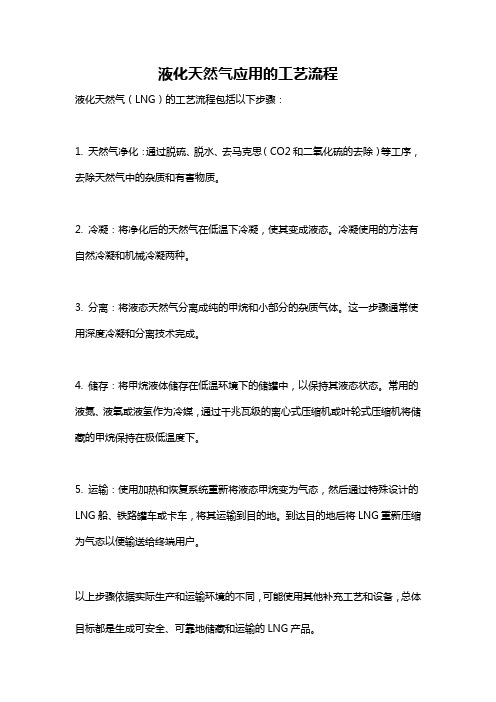
液化天然气应用的工艺流程
液化天然气(LNG)的工艺流程包括以下步骤:
1. 天然气净化:通过脱硫、脱水、去马克思(CO2和二氧化硫的去除)等工序,去除天然气中的杂质和有害物质。
2. 冷凝:将净化后的天然气在低温下冷凝,使其变成液态。
冷凝使用的方法有自然冷凝和机械冷凝两种。
3. 分离:将液态天然气分离成纯的甲烷和小部分的杂质气体。
这一步骤通常使用深度冷凝和分离技术完成。
4. 储存:将甲烷液体储存在低温环境下的储罐中,以保持其液态状态。
常用的液氮、液氧或液氢作为冷媒,通过千兆瓦级的离心式压缩机或叶轮式压缩机将储藏的甲烷保持在极低温度下。
5. 运输:使用加热和恢复系统重新将液态甲烷变为气态,然后通过特殊设计的LNG船、铁路罐车或卡车,将其运输到目的地。
到达目的地后将LNG重新压缩为气态以便输送给终端用户。
以上步骤依据实际生产和运输环境的不同,可能使用其他补充工艺和设备,总体目标都是生成可安全、可靠地储藏和运输的LNG产品。
天然气处理工艺流程优化分析
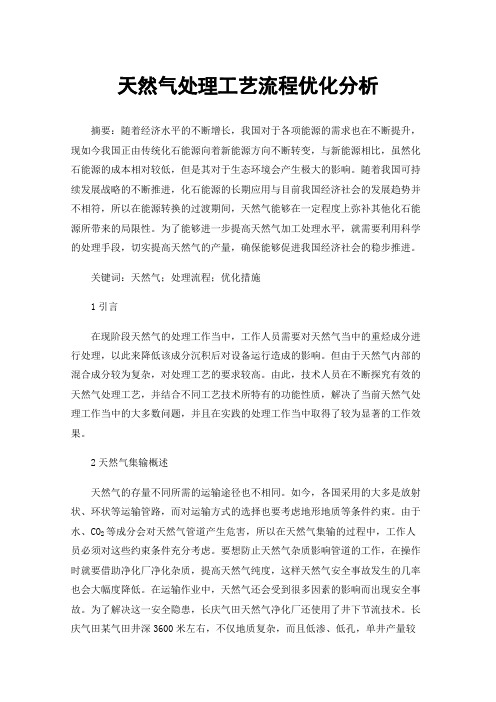
天然气处理工艺流程优化分析摘要:随着经济水平的不断增长,我国对于各项能源的需求也在不断提升,现如今我国正由传统化石能源向着新能源方向不断转变,与新能源相比,虽然化石能源的成本相对较低,但是其对于生态环境会产生极大的影响。
随着我国可持续发展战略的不断推进,化石能源的长期应用与目前我国经济社会的发展趋势并不相符,所以在能源转换的过渡期间,天然气能够在一定程度上弥补其他化石能源所带来的局限性。
为了能够进一步提高天然气加工处理水平,就需要利用科学的处理手段,切实提高天然气的产量,确保能够促进我国经济社会的稳步推进。
关键词:天然气;处理流程;优化措施1引言在现阶段天然气的处理工作当中,工作人员需要对天然气当中的重烃成分进行处理,以此来降低该成分沉积后对设备运行造成的影响。
但由于天然气内部的混合成分较为复杂,对处理工艺的要求较高。
由此,技术人员在不断探究有效的天然气处理工艺,并结合不同工艺技术所特有的功能性质,解决了当前天然气处理工作当中的大多数问题,并且在实践的处理工作当中取得了较为显著的工作效果。
2天然气集输概述天然气的存量不同所需的运输途径也不相同。
如今,各国采用的大多是放射状、环状等运输管路,而对运输方式的选择也要考虑地形地质等条件约束。
由于水、CO2等成分会对天然气管道产生危害,所以在天然气集输的过程中,工作人员必须对这些约束条件充分考虑。
要想防止天然气杂质影响管道的工作,在操作时就要借助净化厂净化杂质,提高天然气纯度,这样天然气安全事故发生的几率也会大幅度降低。
在运输作业中,天然气还会受到很多因素的影响而出现安全事故。
为了解决这一安全隐患,长庆气田天然气净化厂还使用了井下节流技术。
长庆气田某气田井深3600米左右,不仅地质复杂,而且低渗、低孔,单井产量较低,其天然气含有大量的CH4,H2S、CO2含量较小,气体除了含有C2-C6外,还有少许C7+重烃。
该气井天然气的地面集输工艺经历了高压集气、井口加热管道保温以及井下节流等阶段形成了中低压集气模式。
- 1、下载文档前请自行甄别文档内容的完整性,平台不提供额外的编辑、内容补充、找答案等附加服务。
- 2、"仅部分预览"的文档,不可在线预览部分如存在完整性等问题,可反馈申请退款(可完整预览的文档不适用该条件!)。
- 3、如文档侵犯您的权益,请联系客服反馈,我们会尽快为您处理(人工客服工作时间:9:00-18:30)。
天然气液化工艺流程方案选择优化
液化厂的工艺系统主要包括净化工艺系统、液化工艺系统和存储系统。
工艺优化主要体现在:液化中制冷方式的优化和储存方式的优化。
一、液化制冷方式的选择:
天然气液化为低温过程。
天然气液化所需冷量是靠外加制冷循环来提供,配备的制冷系统就是要使得换热器达到最小的冷、热流之温差,并因此获得极高的制冷效率。
天然气液化的制冷系统已非常成熟,常用的工艺有:阶式制冷循环、混合冷剂制冷循环、膨胀机制冷循环。
1、阶式制冷循环
阶式制冷循环1939 年首先应用于液化天然气产品,装于美国的Cleveland,采用NH3、C2H4为第一、第二级制冷剂。
经典阶式制冷循环由三个独立的制冷系统组成。
级联式液化流程图
第一级采用丙烷做制冷剂,经过净化的天然气在丙烷冷却器中冷却到-35~-40℃,分离出戊烷以上的重烃后进入第二级冷却。
由丙烷冷却器中蒸发出来的丙烷气体经压缩机增压,水冷却器冷却后重新液化,并循环到丙烷冷却器。
第二级采用乙烯做制冷剂,天然气在第二级中被冷却到-80~-100℃,并被液化后进入第三级冷却。
第三级采用甲烷做制冷剂,液化天然气在甲烷冷却器中被过冷到-150~-160℃,然后通过节流阀降压,温度降到-162℃后,用泵输送到LNG 贮槽。
甲烷冷却器中蒸发出来的气体经增压、水冷后,在丙烷冷却器中冷却、在乙烯冷却器中液化后,循环到甲烷冷却器。
经典阶式制冷循环,包含几个相对独立、相互串联的冷却阶段,由于制冷剂一般使用多级压缩机压缩,因而在每个冷却阶段中,制冷剂可在几个压力下蒸发,分成几个温度等级冷却天然气,各个压力下蒸发的制冷剂进入相应的压缩机级压缩。
各冷却阶段仅制冷剂不同,操作过程基本相似。
从发展来看,最初兴建LNG 装置时就用阶式制冷循环的着眼点是:能耗最低,技术成熟,无需改变即可移植用于LNG 生产。
随着发展要求而陆续兴建新的LNG 装置,这时经典的阶式制冷循环就暴露出它固有的缺点:
1)经典的阶式制冷循环由三个独立的丙烷、乙烯、甲烷制冷循环复迭而成。
机组多(三台压缩机)、冷剂用量大、级间管路连接复杂,导致造价高昂;
2)为使实际级间操作温度尽可能与原料天然气的冷却曲线(Q-T 曲线)贴近,以减少熵增,提高效率。
可是随着效率的提高,工艺流程也将变得十分复杂。
3)需要相当一部分资金购置和贮存制冷剂。
2、混合冷剂循环
有鉴于阶式制冷循环装置复杂、投资高,为此开发了混合制冷循环(Mixed Refrigerant Cycle, MRC)。
用一种制冷剂(一般是烃类混合物,如N2、C1~C5等),其Q-T 曲线与原料天然气接近一致。
闭式混合制冷液化工艺流程
利用混合物部分冷凝的特点来达到所需的不同温度水平,既保留了阶式制冷循环的优点,而且又只有1 台压缩机,使流程大于简化,造价也可降低。
从原则上讲,由N2、C1~C5等组成的混合物,其组成比例应依照原料天然气组成、工艺流程、工艺压力而异。
一旦确定后组成不易调整,即使能作到这一点,要使整个液化过程(从常温到-162℃)都按冷却曲线来提供所要求的冷量也是很困难的,充其量只能局部或一部分做到贴近原料天然气的Q-T 曲线。
因此MRC 的流程是简单了,但它的效率要比经典阶式制冷循环低。
3)膨胀机制冷循环
膨胀机制冷循环是指利用高压制冷剂通过透平膨胀机绝热膨胀的克劳德循环制冷来实现天然气的液化。
气体在膨胀机中膨胀降温的同时,能输出功,可用于驱动流程中的压缩机。
膨胀液化工艺流程及其设备
根据制冷剂的不同,膨胀机制冷循环可分为:氮膨胀机制冷循环、氮-甲烷膨胀机制冷循环、天然气膨胀制冷循环。
与阶式制冷循环和混合冷剂制冷循环工艺相比,氮气膨胀循环流程非常简单、紧凑,造价略低。
起动快,热态起动2~4 小时即可获得满负荷产品,运行灵活,适应性强,易于操作和控制,安全性好,放空不会引起火灾或爆炸危险。
制冷剂采用单组分气体,因而消除了像混合冷剂制冷循环工艺那样的分离和存储制冷剂的麻烦,也避免了由此带来的安全问题,使液化过程更简化和紧凑。
但能耗要比混合冷剂液化流程高40%左右。
为了降低膨胀机制冷循环的功耗,采用N2-CH4双组分混合气体代替纯N2,发展了N2-CH4膨胀机制冷循环。
与混合冷剂循环相比,N2-CH4
膨胀机制冷循环具有起动时间短、流程简单、控制容易、制冷剂测定和计算方便等优点。
同时由于缩小了冷端换热温差,它要比纯氮膨胀机制冷循环节省电耗,但是投资相对较高。
N2-CH4膨胀机制冷循环的液化流程由天然气液化系统与N2-CH4膨胀机制冷系统两个各自独立的部分组成。
在天然气液化系统中,经过预处理装置脱酸气、脱水后的天然气,经预冷器冷却后,在气液分离器中分离重烃,气相部分进入液化器进行液化,在过冷器中进行过冷,节流降压后进入LNG 贮槽。
在N2-CH4制冷系统中,制冷剂N2-CH4经循环压缩机和增压机(制动压缩机)压缩到工作压力,经水冷却器冷却后,进入预冷器被冷却到膨胀机的入口温度。
一部分制冷剂进入膨胀机膨胀到循环压缩机的入口压力,与返流制冷剂混合后,作为液化器的冷源,回收的膨胀功用于驱动增压机;另外一部分制冷剂经液化器和过冷器冷凝和过冷后,经节流阀节流降温后返流,为过冷器提供冷量。
膨胀机制冷流程中,由于换热器的传热温差很大,可采用预冷的方法对制冷剂和天然气进行预冷,则液化过程的能耗可大幅度降低。
从上面的对比可看出级联式制冷循环能耗最低,效率最高,但是系统的复杂程度最高,所以级联式制冷循环逐渐被混合制冷剂制冷循环代替。
带膨胀机的制冷循环虽然复杂程度最低,但是比功耗最高,运行成本最高,经济性不好,而且使用了较多高速转动机械,降低了可靠性,和其它制冷循环比不具有优势。
而混合制冷剂制冷循环具有流程简单、适应性强、操作运行比较容易的优点,且功耗相对较低,目前被广泛采用,因此工程中常推荐采用混合制冷剂制冷循环工艺。
二、存储方式的选择:
液化天然气LNG在常压下沸点大约为-162℃,目前对于LNG的储存大约存在两种工艺,一种是常压低温储存;另一种是带压子母罐储存,对两种储存工艺对比列举如下:
1、常压低温储存
LNG常压储存是采用常压拱顶低温储罐储存LNG,储罐为平底拱盖、立式双层壁结构,外罐底板铺设在平台上,底板上铺设泡沫玻璃砖(作为底部保温层及负荷承载层),内罐底板铺设在负荷分配板上,内罐及液体重力通过负荷分配板均匀分布在玻璃砖上,内罐四周通过多个锚带紧固,防止内槽在举升力作用下,底部产生外凸变形,
内外夹层间填充珍珠砂保温层,并且充干氮气保护,采用自动调节阀控制,保证夹层压力稳定。
储存压力大约为10kPa,BOG通过BOG压缩机增压后返回系统,在每座储罐上至少配备两台低温装车泵用于LNG装车等。
常压储存方式尤其适用于大规模储存,特点是投资较省,但是工艺比较复杂。
2、带压子母罐储存
立式子母型储罐结构示意图
LNG带压储存通常是采用子母罐储存,子罐一般采用压力罐,设计压力约为0.8MPa,储存压力大约为0.3MPa,母罐主要作用是保冷和抗风荷载,内外罐之间填满保温层。
子母罐由于子罐的制造容积受到限制,目前国内最大能够做到250m3,而且目前一个母罐最多容纳子罐12个即1座子母罐最大储存容积为3000m3,因此子母罐储存方式难以满足大规模的LNG储存。
带压子母罐储存方式不需要配备BOG压缩机,只需配备普通低温泵用于装车等操作。
子母罐储存方式优点是工艺简单,缺点是在较大储存规模时投资高。
一般较大规模的LNG储存多采用常压储罐储存。