自动化生产线安装与调试
自动化生产线的安装与调试
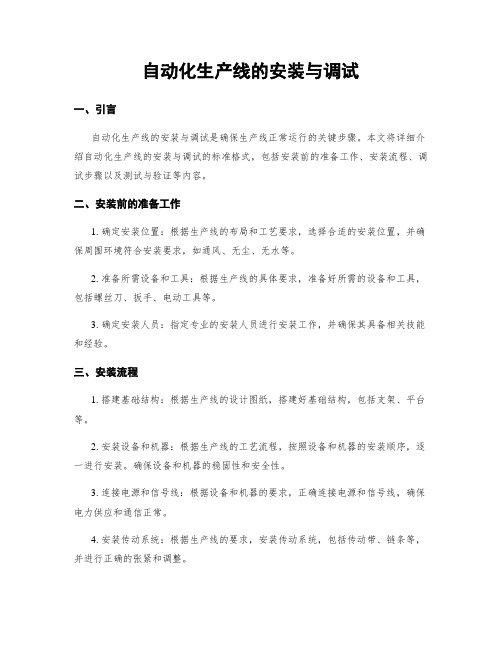
自动化生产线的安装与调试一、引言自动化生产线的安装与调试是确保生产线正常运行的关键步骤。
本文将详细介绍自动化生产线的安装与调试的标准格式,包括安装前的准备工作、安装流程、调试步骤以及测试与验证等内容。
二、安装前的准备工作1. 确定安装位置:根据生产线的布局和工艺要求,选择合适的安装位置,并确保周围环境符合安装要求,如通风、无尘、无水等。
2. 准备所需设备和工具:根据生产线的具体要求,准备好所需的设备和工具,包括螺丝刀、扳手、电动工具等。
3. 确定安装人员:指定专业的安装人员进行安装工作,并确保其具备相关技能和经验。
三、安装流程1. 搭建基础结构:根据生产线的设计图纸,搭建好基础结构,包括支架、平台等。
2. 安装设备和机器:根据生产线的工艺流程,按照设备和机器的安装顺序,逐一进行安装。
确保设备和机器的稳固性和安全性。
3. 连接电源和信号线:根据设备和机器的要求,正确连接电源和信号线,确保电力供应和通信正常。
4. 安装传动系统:根据生产线的要求,安装传动系统,包括传动带、链条等,并进行正确的张紧和调整。
5. 安装控制系统:根据生产线的要求,安装控制系统,包括PLC、触摸屏等,并进行正确的连接和配置。
四、调试步骤1. 电气调试:按照控制系统的要求,进行电气调试,包括检查电源供应、检测信号传输、检验开关和按钮的功能等。
2. 机械调试:按照设备和机器的要求,进行机械调试,包括检查传动系统的运行情况、调整传动比例、检测运动部件的顺畅性等。
3. 功能调试:按照生产线的工艺要求,进行功能调试,包括检查各个设备和机器的功能是否正常、调整参数、测试自动化控制等。
4. 整体调试:进行整体调试,包括模拟实际生产情况,测试生产线的运行效果、检查各个部分的协调性和稳定性等。
五、测试与验证1. 运行测试:对安装和调试完成的自动化生产线进行运行测试,检查各个设备和机器的运行状态、检测生产线的生产能力等。
2. 故障排除:如果在测试过程中发现故障,及时进行排除,保证生产线的正常运行。
自动化生产线的安装与调试

自动化生产线的安装与调试引言概述:自动化生产线在现代工业中扮演着至关重要的角色。
它们能够提高生产效率、减少人力成本,并且提供更高质量的产品。
然而,为了确保自动化生产线的正常运行,正确的安装和调试是至关重要的。
本文将详细介绍自动化生产线的安装与调试过程。
一、准备工作1.1 确定生产线的布局在安装自动化生产线之前,首先需要确定生产线的布局。
这包括确定各个设备的位置、工作站的设置以及物料的流动路径。
合理的布局可以提高生产效率并减少生产线上的物料堆积和拥堵。
1.2 选购合适的设备在安装自动化生产线之前,需要选购适合生产需求的设备。
这包括机械设备、传感器、控制系统等。
选择合适的设备可以确保生产线的稳定运行和高效生产。
1.3 准备所需材料和工具在安装自动化生产线之前,需要准备所需的材料和工具。
这包括电缆、连接器、螺丝刀、扳手等。
准备充足的材料和工具可以提高安装效率,并确保安装过程的顺利进行。
二、安装设备2.1 安装机械设备首先,需要按照设备的安装说明书,将机械设备安装在指定位置。
确保设备的稳固安装可以保证设备在运行时不会浮现晃动或者倾斜的情况。
2.2 连接电气设备接下来,需要连接电气设备,包括传感器、机电、控制器等。
确保电气连接正确无误,且符合设备的电气要求。
同时,进行必要的接地和绝缘工作,以确保安全运行。
2.3 连接控制系统最后,需要连接控制系统,将各个设备与控制器进行连接。
确保控制系统能够准确地控制和监测设备的运行状态,以实现自动化生产线的正常运行。
三、调试设备3.1 验证设备的运行状态在安装完成后,需要对设备进行验证,确保其正常运行。
通过检查设备的各个部件和功能,确认其是否符合预期的运行要求。
3.2 调整设备的参数和设置根据生产需求,需要对设备的参数和设置进行调整。
这包括调整传感器的灵敏度、调整控制器的参数等。
通过合适的参数设置,可以优化设备的运行效果。
3.3 进行设备的功能测试最后,需要进行设备的功能测试。
自动化生产线安装与调试

自动化生产线安装与调试引言概述:随着科技的不断进步,自动化生产线在工业生产中扮演着越来越重要的角色。
自动化生产线的安装与调试是确保生产线正常运行的关键步骤。
本文将从安装前的准备工作、设备安装、电气连接、调试过程和调试后的验收等五个大点详细阐述自动化生产线的安装与调试过程。
正文内容:1. 准备工作1.1 现场勘察:对于自动化生产线的安装与调试,首先需要进行现场勘察,了解生产线的布局、空间限制以及设备的安装位置。
1.2 材料准备:根据勘察结果,准备所需的设备、工具和材料,确保安装与调试过程的顺利进行。
1.3 人员安排:合理安排安装与调试人员,确保每一个环节的顺利进行。
2. 设备安装2.1 机械设备安装:根据生产线的布局,按照设备安装图纸进行机械设备的安装,包括设备的固定、连接和调整等。
2.2 传动系统安装:根据生产线的要求,安装传动系统,如皮带传动、链条传动等,确保传动系统的正常运行。
2.3 机电一体化设备安装:对于机电一体化设备,需要根据设备的特点进行安装,包括电气连接、传感器的安装等。
3. 电气连接3.1 电气路线布置:根据生产线的需要,合理布置电气路线,确保各个设备之间的电气连接正确可靠。
3.2 电气设备安装:按照电气图纸,安装各个电气设备,包括机电、控制柜、传感器等。
3.3 电气连接调试:进行电气连接的调试,确保各个设备之间的信号传输正常,电气系统的稳定性和安全性。
4. 调试过程4.1 单元设备调试:对于每一个单元设备,进行独立的调试,确保设备的正常运行。
4.2 系统联调:将各个单元设备进行联调,确保设备之间的协同工作正常,达到预期的生产效果。
4.3 故障排除:在调试过程中,及时发现并解决设备故障,确保生产线的稳定运行。
5. 调试后的验收5.1 生产能力测试:对已安装调试完成的生产线进行生产能力测试,评估其生产效率和产能。
5.2 安全性检查:进行安全性检查,确保生产线符合相关的安全标准和要求。
自动化生产线安装与调试

自动化生产线安装与调试一、引言自动化生产线是现代工业生产中的重要组成部份,它能够提高生产效率、降低成本、减少人工操作错误等。
为确保自动化生产线的正常运行,需要进行安装与调试工作。
本文将详细介绍自动化生产线的安装与调试流程、所需设备和工具、安装要求、调试步骤以及常见问题解决方法。
二、安装与调试流程1. 确定安装位置:根据生产线的设计要求和工厂的实际情况,确定自动化生产线的安装位置。
安装位置应考虑到生产线的运输、维修和操作的便利性。
2. 准备所需设备和工具:根据生产线的规格和要求,准备好所需的设备和工具。
常见的设备包括输送带、机器人、传感器等,工具包括螺丝刀、扳手、电缆等。
3. 进行安装工作:a. 搭建支架:根据生产线的设计要求,搭建支架并固定好。
b. 安装设备:根据生产线的布局图,将设备安装到支架上,并进行固定和连接。
c. 连接电源和信号线:将设备的电源线和信号线连接到电源和控制系统中。
d. 安装传感器和控制器:根据生产线的需要,安装传感器和控制器,并进行连接和调试。
4. 进行调试工作:a. 检查连接:检查设备之间的连接是否坚固,电源和信号线是否正确连接。
b. 进行初步测试:启动自动化生产线,观察设备的运行情况,检查是否存在异常。
c. 调整参数:根据生产线的要求,调整设备的参数,确保其正常运行。
d. 进行全面测试:进行全面测试,包括设备的运行速度、准确度、稳定性等方面的测试。
e. 解决问题:如果在测试过程中发现问题,及时解决,并进行相应的调整和修复。
5. 完成安装与调试:当自动化生产线经过全面测试且没有明显问题时,即可宣布安装与调试工作完成。
三、安装要求1. 安全要求:在进行安装与调试工作时,必须遵守相关的安全规定,佩戴好个人防护装备,确保工作人员的安全。
2. 环境要求:自动化生产线的安装位置应满足一定的环境要求,如温度、湿度、通风等。
3. 设备要求:所使用的设备必须符合相关的标准和规定,确保其质量和性能稳定。
自动化生产线安装与调试
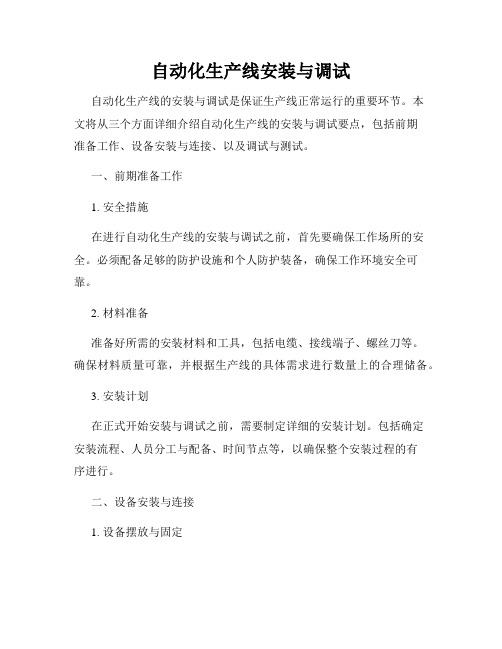
自动化生产线安装与调试自动化生产线的安装与调试是保证生产线正常运行的重要环节。
本文将从三个方面详细介绍自动化生产线的安装与调试要点,包括前期准备工作、设备安装与连接、以及调试与测试。
一、前期准备工作1. 安全措施在进行自动化生产线的安装与调试之前,首先要确保工作场所的安全。
必须配备足够的防护设施和个人防护装备,确保工作环境安全可靠。
2. 材料准备准备好所需的安装材料和工具,包括电缆、接线端子、螺丝刀等。
确保材料质量可靠,并根据生产线的具体需求进行数量上的合理储备。
3. 安装计划在正式开始安装与调试之前,需要制定详细的安装计划。
包括确定安装流程、人员分工与配备、时间节点等,以确保整个安装过程的有序进行。
二、设备安装与连接1. 设备摆放与固定根据生产线图纸和现场实际情况,确定各设备的摆放位置,并进行固定。
确保设备之间的距离和高度符合规范要求,避免可能的碰撞或交叉干扰。
2. 电源接入依据设备的电源要求,将其逐个接入到电源系统中。
注意线路的绝缘与接地,确保电源供应稳定可靠,并且符合电气安全标准。
3. 控制系统连接将各设备的控制系统通过传感器、执行器等进行有序连接,确保信号传输畅通无阻。
同时,检查关键部位的传感器精度和执行器的动作准确性,以确保设备的正常运行。
三、调试与测试1. 控制系统调试先进行控制系统的简单调试,包括对PLC程序进行验证、调整设备的启动与停止逻辑等。
确保控制系统的各项功能正常,能够准确地对设备进行控制。
2. 设备功能测试按照设备的功能要求,进行各项功能测试。
例如,对于一台装配机器人,可以测试其抓取、装配、完成周期等功能。
通过测试,验证设备的性能和运行是否符合预期。
3. 整线测试在完成各个设备的功能测试后,进行整线测试。
模拟实际生产环境,检查设备在复杂工况下的协调与协作能力。
测试过程中发现的问题及时记录,并进行相应的调整和优化。
总结:自动化生产线的安装与调试是一个复杂而重要的过程,需要细致入微地进行操作。
自动化生产线安装与调试

自动化生产线安装与调试随着科技的不断发展,自动化生产线在工业生产中扮演着越来越重要的角色。
而自动化生产线的安装与调试是确保生产线正常运行的关键步骤。
本文将介绍自动化生产线安装与调试的相关内容。
一、前期准备1.1 确定生产线的布局和设计方案。
在安装之前,需要根据生产需求确定生产线的布局和设计方案,包括设备的摆放位置、输送带的长度和宽度等。
1.2 准备所需的设备和零部件。
在安装过程中,需要准备好所需的设备和零部件,确保安装过程顺利进行。
1.3 确保安装人员熟悉设备操作规程。
在安装之前,需要确保安装人员熟悉设备的操作规程,以便进行正确的安装和调试。
二、安装设备2.1 按照设计方案进行设备的安装。
根据前期确定的布局和设计方案,按照要求对设备进行安装,确保设备摆放位置准确。
2.2 连接设备和输送带。
在安装过程中,需要将设备与输送带连接起来,确保设备能够正常运行。
2.3 调整设备的高度和角度。
在安装过程中,需要调整设备的高度和角度,确保设备能够正常运行并符合生产需求。
三、电气连接3.1 连接电源和控制系统。
在安装过程中,需要将设备连接到电源和控制系统,确保设备能够正常供电和控制。
3.2 进行电气线路的检查和调试。
在连接电源和控制系统之后,需要对电气线路进行检查和调试,确保线路连接正确并能够正常工作。
3.3 调整控制系统的参数。
在连接电源和控制系统之后,需要调整控制系统的参数,确保设备能够按照要求运行。
四、机械调试4.1 进行设备的空载测试。
在安装和连接设备之后,需要进行设备的空载测试,确保设备能够正常运转。
4.2 进行设备的负载测试。
在空载测试通过之后,需要进行设备的负载测试,确保设备能够正常运行并符合生产需求。
4.3 调整设备的速度和运行方式。
在进行负载测试之后,需要调整设备的速度和运行方式,确保设备能够按照要求运行。
五、最终调试5.1 进行整体联调测试。
在完成机械调试之后,需要进行整体联调测试,确保设备各部分协调运行。
自动化生产线安装与调试
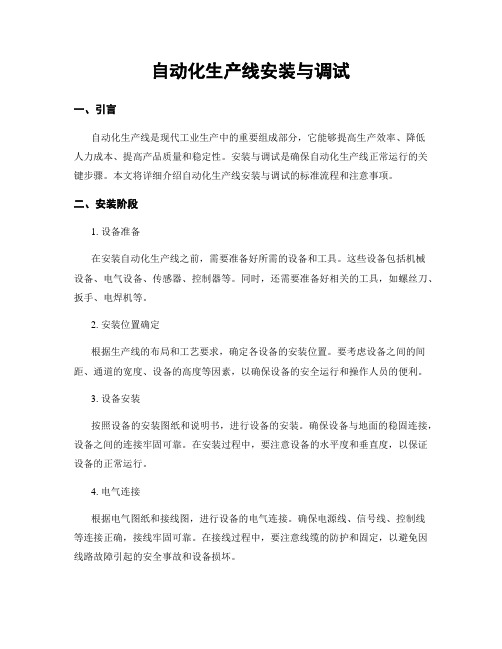
自动化生产线安装与调试一、引言自动化生产线是现代工业生产中的重要组成部分,它能够提高生产效率、降低人力成本、提高产品质量和稳定性。
安装与调试是确保自动化生产线正常运行的关键步骤。
本文将详细介绍自动化生产线安装与调试的标准流程和注意事项。
二、安装阶段1. 设备准备在安装自动化生产线之前,需要准备好所需的设备和工具。
这些设备包括机械设备、电气设备、传感器、控制器等。
同时,还需要准备好相关的工具,如螺丝刀、扳手、电焊机等。
2. 安装位置确定根据生产线的布局和工艺要求,确定各设备的安装位置。
要考虑设备之间的间距、通道的宽度、设备的高度等因素,以确保设备的安全运行和操作人员的便利。
3. 设备安装按照设备的安装图纸和说明书,进行设备的安装。
确保设备与地面的稳固连接,设备之间的连接牢固可靠。
在安装过程中,要注意设备的水平度和垂直度,以保证设备的正常运行。
4. 电气连接根据电气图纸和接线图,进行设备的电气连接。
确保电源线、信号线、控制线等连接正确,接线牢固可靠。
在接线过程中,要注意线缆的防护和固定,以避免因线路故障引起的安全事故和设备损坏。
5. 传感器和控制器安装根据传感器和控制器的安装图纸和说明书,进行传感器和控制器的安装。
确保传感器与被测物体的接触良好,控制器与设备的连接正确。
在安装过程中,要注意传感器的定位和校准,以确保传感器的准确性和稳定性。
三、调试阶段1. 电气调试进行设备的电气调试,包括电源的接通、电气元件的检查和测试等。
确保电气系统的正常运行,各设备的电气连接正确,电气信号的传输稳定。
2. 机械调试进行设备的机械调试,包括设备的运行测试、传动系统的检查和调整等。
确保设备的机械部分能够正常运转,各部件的协调配合良好,设备的运行平稳。
3. 传感器和控制器调试进行传感器和控制器的调试,包括传感器的校准、控制器的参数设置等。
确保传感器能够准确感知被测物体的状态,控制器能够正确地对设备进行控制和调节。
4. 整体调试对整个自动化生产线进行综合调试,包括设备的协调运行、工艺流程的测试和优化等。
自动化生产线的安装与调试

自动化生产线的安装与调试一、引言自动化生产线是现代工业生产中的重要组成部分,它能够提高生产效率、降低成本、提高产品质量和稳定性。
本文旨在详细介绍自动化生产线的安装与调试过程,包括设备准备、安装步骤、调试方法以及常见问题解决等内容。
二、设备准备1. 确定生产线的布局和工艺流程,包括设备的位置、物料输送方式、工作站设置等。
2. 根据生产线的需求,选择合适的自动化设备,包括机械设备、传感器、控制系统等。
3. 配置所需的工具和设备,如螺丝刀、扳手、电缆等。
三、安装步骤1. 搭建机械结构:根据设备布局图和工艺流程,安装机械设备,包括传送带、机械臂、装配机等。
确保设备安装牢固、平稳。
2. 连接电气系统:根据设备的电气图纸,连接电源线、传感器、执行器等。
确保电气连接正确、稳定。
3. 安装控制系统:根据设备的控制系统图纸,安装控制器、PLC等设备,并进行线缆连接。
确保控制系统安装正确、可靠。
4. 连接通信网络:如果生产线需要与其他设备或系统进行通信,需要配置网络设备,并进行网络连接。
5. 安装并调试软件:根据生产线的需求,安装相应的软件,并进行调试。
确保软件运行稳定、功能正常。
四、调试方法1. 确认设备连接:检查设备的电气连接和通信连接是否正常,确保设备能够正常接收和发送信号。
2. 验证传感器:通过模拟输入信号或实际物料,验证传感器的工作状态和灵敏度。
3. 调整机械设备:根据工艺要求,调整机械设备的位置、速度、力度等参数,确保设备能够准确执行工艺动作。
4. 配置控制系统:根据生产线的工艺流程,配置控制系统的参数和逻辑,确保设备能够按照预定的工艺要求进行操作。
5. 测试运行:进行设备的试运行,模拟生产线的实际工作环境,检查设备的运行状态和性能。
6. 优化调整:根据试运行的结果,对设备进行优化调整,如调整控制系统的参数、修正机械设备的位置等,以达到最佳的生产效果。
五、常见问题解决1. 设备无法启动:检查电源线是否连接正确,电源是否正常供电,控制系统是否配置正确。
- 1、下载文档前请自行甄别文档内容的完整性,平台不提供额外的编辑、内容补充、找答案等附加服务。
- 2、"仅部分预览"的文档,不可在线预览部分如存在完整性等问题,可反馈申请退款(可完整预览的文档不适用该条件!)。
- 3、如文档侵犯您的权益,请联系客服反馈,我们会尽快为您处理(人工客服工作时间:9:00-18:30)。
河南机电高等专科学校自动控制系《自动化生产线安装与调试》课程大作业班级:姓名:学号:成绩:2014年12月25日目录目录1供料站系统 (1)1.1 供料站电气原理图 (1)1.2 供料站程序流程图 (2)2加工站系统 (3)2.1 加工站电气原理图 (3)2.2 加工站程序流程图 (4)3装配站系统 (6)3.1 装配站电气原理图 (6)3.2 装配站程序流程图 (7)4分拣站系统 (9)4.1 分拣站电气原理图 (9)4.2 分拣站程序流程图 (10)5输送站系统 (11)5.1 输送站电气原理图 (11)5.2 输送站程序流程图 (12)6学习心得 (14)1 供料站系统1.1供料站电气原理图图1.1 供料粘电气原理图工作原理:工件垂直叠放在料仓中,推料缸处于料仓的底层并且其活塞杆可从料仓的底部通过。
当活塞杆在退回位置时,它与最下层工件处于同一水平位置,而夹紧气缸则与次下层工件处于同一水平位置。
在需要将工件推出到物料台上时,首先使夹紧气缸的活塞杆推出,压住次下层工件;然后使推料气缸活塞杆推0V 顶料电磁阀0V 0V 推料电磁阀黄色指示灯绿色指示灯红色指示灯来自电源配电箱外部电源P L C 直流电源输出24V24V 顶料到位检测顶料复位检测推料到位检测推料复位检测物料台物料检测物料不够检测物料有无检测金属传感器检测24V 停止按钮启动按钮急停按钮单机/联机出,从而把最下层工件推到物料台上。
在推料气缸返回并从料仓底部抽出后,再使夹紧气缸返回,松开次下层工件。
这样,料仓中的工件在重力的作用下,就自动向下移动一个工件,为下一次推出工件做好准备。
在底座和管形料仓第4层工件位置,分别安装一个漫射式光电开关。
它们的功能是检测料仓中有无储料或储料是否足够。
若该部分机构内没有工件,则处于底层和第4层位置的两个漫射式光电接近开关均处于常态;若仅在底层起有3个工件,则底层处光电接近开关动作而第4层处光电接近开关常态,表明工件已经快用完了。
这样,料仓中有无储料或储料是否足够,就可用这两个光电接近开关的信号状态反映出来。
推料缸把工件推出到出料台上。
出料台面开有小孔,出料台下面设有一个园柱形漫射式光电接近开关,工作时向上发出光线,从而透过小孔检测是否有工件存在,以便向系统提供本单元出料台有无工件的信号。
在输送单元的控制程序中,就可以利用该信号状态来判断是否需要驱动机械手装置来抓取此工件。
1.2供料站程序流程图图1.2 供料粘程序流程图2 加工站系统2.1加工站电气原理图图2.1 加工站电气原理图滑动加工台的工作原理:滑动加工台在系统正常工作后的初始状态为伸缩气缸伸出,加工台气动手指张开的状态,当输送机构把物料送到料台上,物料检测0V 夹紧电磁阀0V 0V 黄色指示灯绿色指示灯红色指示灯来自电源配电箱外部电源P L C 直流电源输出24V24V 物料台物料检测料台夹紧检测料台伸出到位检测料台缩回到位检测加工压头上限检测加工压头下限检测光纤传感器检测24V 停止按钮启动按钮急停按钮单机/联机料台伸缩电磁阀加工压头电磁阀传感器检测到工件后,PLC控制程序驱动气动手指将工件夹紧→加工台回到加工区域冲压气缸下方→冲压气缸活塞杆向下伸出冲压工件→完成冲压动作后向上缩回→加工台重新伸出→到位后气动手指松开的顺序完成工件加工工序,并向系统发出加工完成信号。
为下一次工件到来加工做准备。
在移动料台上安装一个漫射式光电开关。
若加工台上没有工件,则漫射式光电开关均处于常态;若加工台上有工件,则光电接近开关动作,表明加工台上已有工件。
该光电传感器的输出信号送到加工单元PLC的输入端,用以判别加工台上是否有工件需进行加工;当加工过程结束,加工台伸出到初始位置。
同时,PLC通过通信网络,把加工完成信号回馈给系统,以协调控制。
移动料台上安装的漫射式光电开关仍选用E3Z-L61型放大器内置型光电开关(细小光束型),该光电开关的原理和结构以及调试方法在前面已经介绍过了。
移动料台伸出和返回到位的位置是通过调整伸缩气缸上两个磁性开关位置来定位的。
要求缩回位置位于加工冲头正下方;伸出位置应与输送单元的抓取机械手装置配合,确保输送单元的抓取机械手能顺利地把待加工工件放到料台上。
冲压台的工作原理是:当工件到达冲压位置既伸缩气缸活塞杆缩回到位,冲压缸伸出对工件进行加工,完成加工动作后冲压缸缩回,为下一次冲压做准备。
冲头根据工件的要求对工件进行冲压加工,冲头安装在冲压缸头部。
安装板用于安装冲压缸,对冲压缸进行固定。
2.2加工站程序流程图图2.2 加工粘程序流程图3 装配站系统3.1装配站电气原理图图3.1 装配站电气原理图管形料仓用来存储装配用的金属、黑色和白色小园柱零件。
它由塑料圆管和中空底座构成。
塑料圆管顶端放置加强金属环,以防止破损。
工件竖直放入料仓的空心圆管内,由于二者之间有一定的间隙,使其能在重力作用下自由下落。
为了能对料仓供料不足和缺料时报警,在塑料圆管底部和底座处分别安装了2个漫反射光电传感器(E3Z-L 型),并在料仓塑料圆柱上纵向铣槽,以使光电传感器的红外光斑能可靠照射到被检测的物料上。
光电传感器的灵敏度调整应以能24V 手爪下降电磁阀多层警示灯-绿色黄色指示灯绿色指示灯红色指示灯来自电源配电箱24V 多层警示灯-黄色多层警示灯-红色手爪伸出电磁阀24V 挡料电磁阀顶料电磁阀回转电磁阀手爪夹紧电磁阀顶料到位检测顶料复位检测旋转缸右限位检测手爪伸出到位检测手爪夹紧检测旋转缸左限位检测落料状态检测挡料状态检测物料不足检测物料有无检测物料左检测物料右检测物料台检测停止按钮启动按钮急停按钮单机/联机手爪缩回到位检测手爪上升到位检测24V 手爪下降到位检测24V 外部电源P L C 直流电源输出24V检测到黑色物料为准则。
落料机构料仓底座的背面安装了两个直线气缸。
上面的气缸称为顶料气缸,下面的气缸称为挡料气缸。
系统气源接通后,顶料气缸的初始位置在缩回状态,挡料气缸的初始位置在伸出状态。
这样,当从料仓上面放下工件时,工件将被挡料气缸活塞杆终端的挡块阻挡而不能落下。
需要进行落料操作时,首先使顶料气缸伸出,把次下层的工件夹紧,然后挡料气缸缩回,工件掉入廻转物料台的料盘中。
之后挡料气缸复位伸出,顶料气缸缩回,次下层工件跌落到挡料气缸终端挡块上,为再一次供料作准备。
回转物料台机构由气动摆台和两个料盘组成,气动摆台能驱动料盘旋转180度,从而实现把从供料机构落下到料盘的工件移动到装配机械手正下方的功能。
装配机械手的运行过程如下:PLC驱动与竖直移动气缸相连的电磁换向阀动作,由竖直移动带导杆气缸驱动气动手指向下移动,到位后,气动手指驱动手爪夹紧物料,并将夹紧信号通过磁性开关传送给PLC,在PLC控制下,竖直移动气缸复位,被夹紧的物料随气动手指一并提起,离开当廻转物料台的料盘,提升到最高位后,水平移动气缸在与之对应的换向阀的驱动下,活塞杆伸出,移动到气缸前端位置后,竖直移动气缸再次被驱动下移,移动到最下端位置,气动手指松开,经短暂延时,竖直移动气缸和水平移动气缸缩回,机械手恢复初始状态。
本工作单元上安装有红、橙、绿三色警示灯,它是作为整个系统警示用的。
警示灯有五根引出线,其中黄绿交叉线为”地线”;红色线:红色灯控制线;黄色线:橙色灯控制线、绿色线:绿色灯控制线;黑色线:信号灯公共控制线。
3.2装配站程序流程图图3.2 装配粘程序流程图4 分拣站系统4.1分拣站电气原理图图4.1 分拣站电气原理图传送和分拣的工作原理:当输送站送来工件放到传送带上并为入料口漫射式光电传感器检测到时,将信号传输给PLC ,通过PLC 的程序启动变频器,电机运转驱动传送带工作,把工件带进分拣区,如果进入分拣区工件为白色,则检测白色物料的光纤传感器动作,作为1号槽推料气缸启动信号,将白色料推到1号槽里,如果进入分拣区工件为黑色,检测黑色的光纤传感器作为2号槽推料气缸启外部电源P L C 直流电源输出24V24V 编码器B相编码器A相编码器Z相物料口检测传感器光纤检测传感器金属检测传感器24V 停止按钮启动按钮急停按钮单机/联机推杆3到位检测推杆2到位检测推杆1到位检测动信号,将黑色料推到2号槽里。
自动生产线的加工结束。
4.2分拣站程序流程图图4.2 分拣粘程序流程图5 输送站系统5.1输送站电气原理图图5.1输送站电气原理图抓取机械手装置是一个能实现四自由度运动(即升降、伸缩、气动手指夹紧/松开和沿垂直轴旋转的四维运动)的工作单元,该装置整体安装在直线运动传动组件的滑动溜板上,在传动组件带动下整体作直线往复运动,定位到其他各工作单元的物料台,然后完成抓取和放下工件的功能。
传动组件由直线导轨底板、伺服电机及伺服放大器、同步轮、同步带、直线导轨、滑动溜板、拖链和原点接近开关、左、右极限开关组成。
伺服报警手指夹紧检测原点传感器停止按钮启动按钮急停按钮单机/联机+24V+24V 右限位左限位极限开关下限上限左限右限伸出到位缩回到位升降台摆动气缸机械手臂备 用伺服电机由伺服电机放大器驱动,通过同步轮和同步带带动滑动溜板沿直线导轨作往复直线运动。
从而带动固定在滑动溜板上的抓取机械手装置作往复直线运动。
抓取机械手装置上所有气管和导线沿拖链敷设,进入线槽后分别连接到电磁阀组和接线端口上。
左、右极限开关均是有触点的微动开关,用来提供越程故障时的保护信号:当滑动溜板在运动中越过左或右极限位置时,极限开关会动作,从而向系统发出越程故障信号。
5.2输送站程序流程图图5.2 输送粘程序流程图6学习心得在科技日益发达的今天,传统的生产已经代替不了工业生产的要求,自动化已经成为许多企业的核心。
而身为一名学习自动化的学生,我们更应该对自动化生产线有一定的了解和认识。
通过这次课程设计,我的知识领域得到进一步扩展,专业技能得到进一步提高,同时锻炼了自己独立完成任务的能力,另外,我还认识到无论做什么工作,都需要踏实,勤奋,严谨的态度,我深深懂得了要不断把所学知识学以致用,也发现了自己的知识薄弱,还需通过自身不断努力,不断提高自己的分析问题、解决问题的能力,同时也提高了我的专业技能,拓展了我的专业知识面,使我更加体会到要想完成一件事必须认真、踏实、勤于思考、和谨慎稳重。
这对我以后的工作将会产生深远的影响。
同时,也培养了自己认真的科学态度和严谨的工作作风,为将来能更好的适应工作岗位打下了良好的基础。
此外,每天上班制的工作时间,使即将步入社会的我们打下了良好的基础。
对自己严格要求是一种态度。
这对我们以后的工作是有很好的帮助的。
虽然在整个过程中,也遭遇了挫折,但是,在老师和同组人员的帮助下,最终都能圆满的解决。