冷冲压工艺与模具设计教学课件
合集下载
冷冲压工艺与模具设计教学课件

F KLt b
对在曲柄压力机上用薄料(t<1.5mm)对小 工件(面积 <2000mm2)压肋或压肋兼有校形工 序时的变形力按式计算。
F KAt2
K-系数,取0.7~1; L-加强肋长度(mm); t-材料料厚(mm); b —材料的抗拉强度(Mpa); A-局部成形面积;
二、压凸包
D 4 dp
握胀形模的结构及工作原理。
教学要求: 掌握常见胀形模的工作过程,能够根据模具
设计手册,进行胀形模的设计。
胀形:利用模具使坯料局部塑性变形,材料变薄, 表面积增大的冲压方法。
5.1.1 胀形成形的特点和分类 外部材料不进入变形区,变形区材料受双向
拉应力,产生拉伸变形,材料变薄。
当坯料外径与成形直径的比值D/d>3时, 其成形完全依赖于直径为d的圆周以内金属厚度 的变薄实现表面积的增大而成形。
(4)翻边力的计算
翻边力一般不大,非圆孔翻边力比圆孔翻边力小
圆柱形凸模:
F=1.1 (D-d0 )ts
圆锥形(球形)凸模:
F=1.2 tDms
(m=0.05~0.25)
5.2.2 外缘翻边 沿毛坯的曲边,使材料的拉伸或压缩,形成
高度不大的竖边。
1.分类 (1)外凸外缘翻边:属压缩类翻边,近似于局
课后思考
1、胀形的变形特点怎样?为什么采用胀形 工序加工的零件表面质量好?
2、什么叫胀形?胀形方法一般有哪几种? 各有什么特点?
3、胀形模的主要结构特点是什么?
5.2 翻边
学习目标: 能够掌握翻边的概念、成形特点及分类,掌
握翻边模的结构及工作原理。
教学要求: 掌握常见翻边模的工作过程,能够根据模具
胀形和液压胀形。
冷冲压工艺与模具设计绪论课件

学习目的与要求:
1.掌握冲压和冲模概念、冲压工序和冲模分类; 2.了解冷冲模的发展方向。
《冷冲压工艺与模具设计》
第一次课 冷冲压工艺与模具设计概述
重点:
冲压成形基本概念、冲模工序分类。
难点:
冲压成形基本规律、冲模工序分类。
《冷冲压工艺与模具设计》
第一次课 冷冲压工艺与模具设计概述
俗话说:“没有规矩不成方圆”世界上的许许多多东西 都 是从他们各具特色的“规矩”中诞生出来得。东西-----产品, 规矩-------模具。
《冷冲压工艺与模具设计》
第一次课 冷冲压工艺与模具设计概述
二、冲压工序的分类如图(续)
成形工序:冲压成形时,变形材料内部应力超过屈服极限σ , s 但未达到强度极限σb,使材料产生塑性变形,从而 成形零件。成形工序主要有弯曲、拉深、翻边等。 (如图)
《冷冲压工艺与模具设计》
第一次课 冷冲压工艺与模具设计概述
1.基本概念(续) 加工对象:主要金属板材 加工依据:板材冲压成形性能(主要是塑性) 加工设备:主要是压力机 加工工艺装备:冲压模具
冲压模具:在冲压加工中,将材料加工成零件(或半成品)
的一种特殊工艺装备,称为冲压模具(俗称冲 模)。
《冷冲压工艺与模具设计》
第一次课 冷冲压工艺与模具设计概述
一、冲压与冲模概念
片面追求生产效率、模具精度和使用寿命必然导致成本的 增加,只顾降低成本和缩短制造周期而忽视模具精度和使用寿 命必然导致质量的下降。
《冷冲压工艺与模具设计》
第一次课 冷冲压工艺与模具设计概述
六、冲压技术现状与发展方向
1.我国冲压技术现状 技术落后、经济效益低。 主要原因:①冲压基础理论与成形工艺落后;
包括:工作零件、定位零件、卸料与压料零件等;
1.掌握冲压和冲模概念、冲压工序和冲模分类; 2.了解冷冲模的发展方向。
《冷冲压工艺与模具设计》
第一次课 冷冲压工艺与模具设计概述
重点:
冲压成形基本概念、冲模工序分类。
难点:
冲压成形基本规律、冲模工序分类。
《冷冲压工艺与模具设计》
第一次课 冷冲压工艺与模具设计概述
俗话说:“没有规矩不成方圆”世界上的许许多多东西 都 是从他们各具特色的“规矩”中诞生出来得。东西-----产品, 规矩-------模具。
《冷冲压工艺与模具设计》
第一次课 冷冲压工艺与模具设计概述
二、冲压工序的分类如图(续)
成形工序:冲压成形时,变形材料内部应力超过屈服极限σ , s 但未达到强度极限σb,使材料产生塑性变形,从而 成形零件。成形工序主要有弯曲、拉深、翻边等。 (如图)
《冷冲压工艺与模具设计》
第一次课 冷冲压工艺与模具设计概述
1.基本概念(续) 加工对象:主要金属板材 加工依据:板材冲压成形性能(主要是塑性) 加工设备:主要是压力机 加工工艺装备:冲压模具
冲压模具:在冲压加工中,将材料加工成零件(或半成品)
的一种特殊工艺装备,称为冲压模具(俗称冲 模)。
《冷冲压工艺与模具设计》
第一次课 冷冲压工艺与模具设计概述
一、冲压与冲模概念
片面追求生产效率、模具精度和使用寿命必然导致成本的 增加,只顾降低成本和缩短制造周期而忽视模具精度和使用寿 命必然导致质量的下降。
《冷冲压工艺与模具设计》
第一次课 冷冲压工艺与模具设计概述
六、冲压技术现状与发展方向
1.我国冲压技术现状 技术落后、经济效益低。 主要原因:①冲压基础理论与成形工艺落后;
包括:工作零件、定位零件、卸料与压料零件等;
冷冲压工艺与模具设计课件第4章
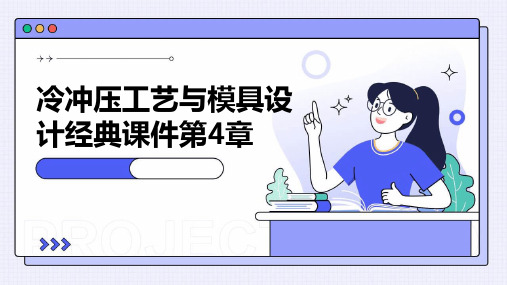
冷冲压工艺与模具设 计经典课件第4章
目录
CONTENTS
• 冷冲压工艺概述 • 模具设计基础 • 模具结构设计 • 模具制造工艺 • 模具使用与维护
01 冷冲压工艺概述
冷冲压工艺的定义与特点
定义
冷冲压工艺是一种金属加工方法 ,通过施加外力将金属板料或坯 料制成所需形状和尺寸的零件。
特点
冷冲压工艺具有高生产效率、低 成本、高质量、可加工复杂形状 零件等优势,广泛应用于汽车、 家电、电子、航空航天等领域。
表面处理技术
对模具表面进行涂层、渗碳淬 火等处理,以提高模具的耐磨
性和抗腐蚀性。
模具制造的质量控制
测量技术
采用高精度的测量设备 和方法,对模具零件进 行检测,确保加工精度
。
统计过程控制
通过统计方法对制造过 程进行监控,及时发现
和消除异常因素。
预防性维护
定期对设备进行检查和 维护,确保设备的稳定
性和可靠性。
04 模具制造工艺
模具制造的工艺流程
材料准备
根据模具设计要求,选择合适的材料 ,并进行材料预处理,如切割、矫直 、预热等。
装配与调试
将各零件组装成完整的模具,并进行 调试,确保模具工作正常。
01
02
粗加工
对材料进行初步加工,包括粗铣、粗 刨、粗车等,以去除大部分余量。
03
半精加工
进一步加工模具零件,包括半精铣、 半精刨、半精车等,以满足模具零件 的形状和尺寸要求。
根据冲压工艺和生产要求 ,进行模具的结构设计, 确定模具的基本结构和零 部件组成。
对模具的各个零件进行详 细设计,包括工作零件、 定位零件、压料零件、导 向零件等。
根据模具设计和零件设计 的结果,绘制装配图和零 件图,以供制造和使用。
目录
CONTENTS
• 冷冲压工艺概述 • 模具设计基础 • 模具结构设计 • 模具制造工艺 • 模具使用与维护
01 冷冲压工艺概述
冷冲压工艺的定义与特点
定义
冷冲压工艺是一种金属加工方法 ,通过施加外力将金属板料或坯 料制成所需形状和尺寸的零件。
特点
冷冲压工艺具有高生产效率、低 成本、高质量、可加工复杂形状 零件等优势,广泛应用于汽车、 家电、电子、航空航天等领域。
表面处理技术
对模具表面进行涂层、渗碳淬 火等处理,以提高模具的耐磨
性和抗腐蚀性。
模具制造的质量控制
测量技术
采用高精度的测量设备 和方法,对模具零件进 行检测,确保加工精度
。
统计过程控制
通过统计方法对制造过 程进行监控,及时发现
和消除异常因素。
预防性维护
定期对设备进行检查和 维护,确保设备的稳定
性和可靠性。
04 模具制造工艺
模具制造的工艺流程
材料准备
根据模具设计要求,选择合适的材料 ,并进行材料预处理,如切割、矫直 、预热等。
装配与调试
将各零件组装成完整的模具,并进行 调试,确保模具工作正常。
01
02
粗加工
对材料进行初步加工,包括粗铣、粗 刨、粗车等,以去除大部分余量。
03
半精加工
进一步加工模具零件,包括半精铣、 半精刨、半精车等,以满足模具零件 的形状和尺寸要求。
根据冲压工艺和生产要求 ,进行模具的结构设计, 确定模具的基本结构和零 部件组成。
对模具的各个零件进行详 细设计,包括工作零件、 定位零件、压料零件、导 向零件等。
根据模具设计和零件设计 的结果,绘制装配图和零 件图,以供制造和使用。
冷冲压工艺及模具设计说课稿ppt

冷冲压工艺及模具设计说课稿 ppt
xx年xx月xx日
contents
目录
• 引言 • 冷冲压工艺基本知识 • 冷冲压模具设计基础 • 冷冲压工艺及模具设计的实际应用 • 说课稿总结与展望
01
引言
说课稿的目的和意义
本次说课稿旨在让学生了解和掌握冷冲压工艺及模具设计的 基本概念、原理和技能,为后续的专业课程和实践环节打下 坚实的基础。
冷冲压工艺的分类和应用
冲孔工艺
Hale Waihona Puke 落料工艺弯曲工艺拉伸工艺
修整工艺
用于加工各种金属板材 和带材,广泛应用于汽 车、家电、电子、仪器 仪表等领域。
将金属板材或带材加工 成各种形状的零件,如 垫圈、齿轮、法兰等。
将金属板材或带材加工 成各种形状的零件,如 角钢、槽钢、钢管等。
将金属板材或带材加工 成各种形状的零件,如 圆筒形件、盒形件、球 形件等。
加强教学方法的改进
教师应积极探索新的教学方法,如引入多媒体教学、网 络教学等,提高教学效果和学生学习兴趣,更好地帮助 学生掌握知识要点。
促进师生互动交流
教师应加强与学生的互动交流,及时了解学生的学习情 况和反馈意见,不断改进教学环节和方法,提高教学质 量。
THANKS
谢谢您的观看
对已成形的零件进行修 整和精加工,以提高其 质量和精度。
冷冲压工艺的基本原理
1
冷冲压工艺的基本原理是利用模具和冲压设备 的压力,将金属板材或带材变形并加工成所需 形状和尺寸。
2
冷冲压工艺需要考虑到材料、模具、设备、润 滑等多种因素,以及各种工艺参数对加工质量 和生产效率的影响。
3
在实际生产中,需要根据具体情况选择合适的 冷冲压工艺和模具设计,以满足生产要求和提 高生产效率。
xx年xx月xx日
contents
目录
• 引言 • 冷冲压工艺基本知识 • 冷冲压模具设计基础 • 冷冲压工艺及模具设计的实际应用 • 说课稿总结与展望
01
引言
说课稿的目的和意义
本次说课稿旨在让学生了解和掌握冷冲压工艺及模具设计的 基本概念、原理和技能,为后续的专业课程和实践环节打下 坚实的基础。
冷冲压工艺的分类和应用
冲孔工艺
Hale Waihona Puke 落料工艺弯曲工艺拉伸工艺
修整工艺
用于加工各种金属板材 和带材,广泛应用于汽 车、家电、电子、仪器 仪表等领域。
将金属板材或带材加工 成各种形状的零件,如 垫圈、齿轮、法兰等。
将金属板材或带材加工 成各种形状的零件,如 角钢、槽钢、钢管等。
将金属板材或带材加工 成各种形状的零件,如 圆筒形件、盒形件、球 形件等。
加强教学方法的改进
教师应积极探索新的教学方法,如引入多媒体教学、网 络教学等,提高教学效果和学生学习兴趣,更好地帮助 学生掌握知识要点。
促进师生互动交流
教师应加强与学生的互动交流,及时了解学生的学习情 况和反馈意见,不断改进教学环节和方法,提高教学质 量。
THANKS
谢谢您的观看
对已成形的零件进行修 整和精加工,以提高其 质量和精度。
冷冲压工艺的基本原理
1
冷冲压工艺的基本原理是利用模具和冲压设备 的压力,将金属板材或带材变形并加工成所需 形状和尺寸。
2
冷冲压工艺需要考虑到材料、模具、设备、润 滑等多种因素,以及各种工艺参数对加工质量 和生产效率的影响。
3
在实际生产中,需要根据具体情况选择合适的 冷冲压工艺和模具设计,以满足生产要求和提 高生产效率。
冷冲压工艺与模具设计培训课程(ppt 155页)
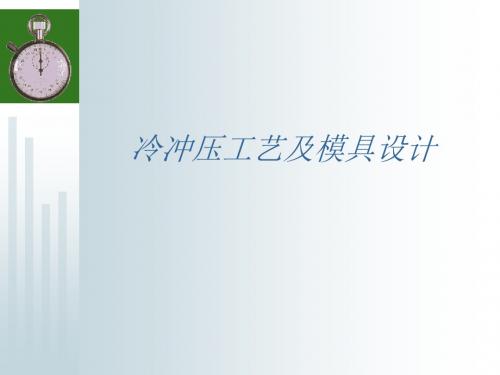
金属受外力作用就会发生变形,表现为形状、尺寸、 体积等的变化。变形力去除后,能恢复原状的变形称为弹 性变形;不能恢复原状的永久变形称为塑性变形。除脆性 材料外,大部分固体材料变形时都呈现出明显的弹性变形 阶段和塑性变形阶段。
弹性变形时,金属内原子的位置发生变化,表现为原 子间距有微小的改变,从而引起了体积的变化。此时,原 子的稳定平衡状态遭到破坏,作用在物体上的外力和企图 使原子恢复到最小势能位置的原子间反作用力相平衡,这 种反作用力称为内力,单位面积上的内力就称为应力。
分离工序是将冲压件或毛坯沿一定的轮廓进行断裂分 离加工,以获得所需要的零件形状和尺寸,又称为冲裁工 序。
分离工序种类:落料、冲孔、切断、切边、剖切、切
舌等。
1.1.2.2 成形工序 成形工序是在材料不发生破坏的前提下使毛坯发生塑
性变形,以获得所需要的零件形状和尺寸。 成形工序种类:弯曲、拉深、翻边、胀形、起伏成形
2、模具设计制造现代化 大力开展模具CAD/CAM技术的研究和应用,已有许多成熟的模 具CAD/CAM一体化软件应用于模具的设计及制造,使设计者尽 可能将时间和精力用于创新开发。
3、冷冲压生产的机械化和自动化 大力推进冲压工艺中的送料、冲压、取件甚至装配等生产环
节的机械化和自动化研究和应用,使生产率得到极大的提高。
3、操纵系统 由空气分配系统、制动器、离合器和电气控制 箱等组成。压力机的工作是通过操纵机构进行控制的。
4、支承部件 包括床身、工作台、拉紧螺栓等部分。床身是 压力机的基础,保证设备所要求的精度、强度和刚度。床 身上固定有工作台,用于安装冲模的下模。
5、辅助系统 包括气路系统和润滑系统。
6、附属装置 包括过载保护、气垫、滑块平衡装置、移动工 作台、快速换模和监控装置等。
弹性变形时,金属内原子的位置发生变化,表现为原 子间距有微小的改变,从而引起了体积的变化。此时,原 子的稳定平衡状态遭到破坏,作用在物体上的外力和企图 使原子恢复到最小势能位置的原子间反作用力相平衡,这 种反作用力称为内力,单位面积上的内力就称为应力。
分离工序是将冲压件或毛坯沿一定的轮廓进行断裂分 离加工,以获得所需要的零件形状和尺寸,又称为冲裁工 序。
分离工序种类:落料、冲孔、切断、切边、剖切、切
舌等。
1.1.2.2 成形工序 成形工序是在材料不发生破坏的前提下使毛坯发生塑
性变形,以获得所需要的零件形状和尺寸。 成形工序种类:弯曲、拉深、翻边、胀形、起伏成形
2、模具设计制造现代化 大力开展模具CAD/CAM技术的研究和应用,已有许多成熟的模 具CAD/CAM一体化软件应用于模具的设计及制造,使设计者尽 可能将时间和精力用于创新开发。
3、冷冲压生产的机械化和自动化 大力推进冲压工艺中的送料、冲压、取件甚至装配等生产环
节的机械化和自动化研究和应用,使生产率得到极大的提高。
3、操纵系统 由空气分配系统、制动器、离合器和电气控制 箱等组成。压力机的工作是通过操纵机构进行控制的。
4、支承部件 包括床身、工作台、拉紧螺栓等部分。床身是 压力机的基础,保证设备所要求的精度、强度和刚度。床 身上固定有工作台,用于安装冲模的下模。
5、辅助系统 包括气路系统和润滑系统。
6、附属装置 包括过载保护、气垫、滑块平衡装置、移动工 作台、快速换模和监控装置等。
- 1、下载文档前请自行甄别文档内容的完整性,平台不提供额外的编辑、内容补充、找答案等附加服务。
- 2、"仅部分预览"的文档,不可在线预览部分如存在完整性等问题,可反馈申请退款(可完整预览的文档不适用该条件!)。
- 3、如文档侵犯您的权益,请联系客服反馈,我们会尽快为您处理(人工客服工作时间:9:00-18:30)。
2.胀形毛坯的计算
L0 = L [1+(0.3~0.4) ]+h
h—修边余量,一般取b=10~20mm; —制件切向最大伸长率; L —制件母线长度。
3.胀形力
软模胀形圆柱空心件的单位压力p
两端不固定
p
2t dmax
b
两端固定
p
2 b
t
d
max
t
2R
钢模胀形所需压力的计算公式,可根据力的
平衡方程式推导得到,其表达式为:
需凸起曲面的冲压方法。 根据模具的不同,可分为钢性胀形、橡胶模
胀形和液压胀形。
1—凸模 2—凹模 3—毛坯 4—软体介质 5—外套
1-上模 2-轴头 3-下模 4-管坯 加轴向压缩的液体胀形
1.胀形变形程度 胀形系数
K=dmax /d0
K-材料的胀形系数; Dmax–胀形后所能达到的最大直径; d–胀形前毛坯的直径;
拉应力,产生拉伸变形,材料变薄。
当坯料外径与成形直径的比值D/d>3时, 其成形完全依赖于直径为d的圆周以内金属厚度 的变薄实现表面积的增大而成形。
胀形主要有起伏成形和空心毛坯胀形两类。
5.1.2 起伏成形 通过材料局部拉深变形,形成凹进或凸起,
用于腹板类板料零件压制加强肋(加强工件刚 度)或压制凸包、凹坑、花纹图案及标记等。
生压缩变形,易起皱而破坏。
5.1 胀形
学习目标: 能够掌握胀形的概念、成形特点及分类,掌
握胀形模的结构及工作原理。
教学要求: 掌握常见胀形模的工作过程,能够根据模具
设计手册,进行胀形模的设计。
胀形:利用模具使坯料局部塑性变形,材料变薄, 表面积增大的冲压方法。
5.1.1 胀形成形的特点和分类 外部材料不进入变形区,变形区材料受双向
2
式中 D—翻边直径; r—翻边件半径; t—材料厚度。
(3)非圆孔翻边 变形特点: I部分视为圆孔翻边; II视为弯曲 变形;III部分视为拉深。
最小圆角部分进行允许 变形程度的校核。 翻边系数:
Kf =(0.85~0.9)K0 预制孔:分别按弯曲,翻边,拉深展开;圆弧处 宽度比直线部分宽5~10%,再光滑连结。
如加强肋与边缘的距离小于(3~5t) 时,在 成形中由于边缘的收缩,需考虑增加切边余量。
2.压筋力
F KLt b
对在曲柄压力机上用薄料(t<1.5mm)对小 工件(面积 <2000mm2)压肋或压肋兼有校形工 序时的变形力按式计算。
F KAt 2
K-系数,取0.7~1; L-加强肋长度(mm); t-材料料厚(mm);
H D d 0.43r 0.72t 2
内孔的翻边极限高度:
H max
D 2
(1
Kmin )
0.43r
0.72t
(2)在拉深件的底部冲孔翻边
允许的翻边高度:
h
D 2
(1
K0 )
0.57(r
t) 2
拉深高度: h` H h r
预孔直径: d K0D
或
d D 1.14(r t ) 2h
式中:
tan F 2 Ht b 1 2 2 tan
F 所需胀形力t 材料厚度
H 胀形后高度
t 材料厚度
摩擦系数,一般 0.15 ~ 0.20
芯
0
,12
0
,150
.
5.1.4 胀形模结构
1-凹模 2-分瓣凸模 3-拉簧 4-锥形芯块 斜块胀形模
墩压胀形模 1-上模板;2-上凹模;3-下凹模; 4-下模板;5-凸轮;6-轴承钉;7-手把;8-凸模
冷冲压工艺与模具设计教学课件 下载-样章.ppt
成形工艺与模具设计
概述 5.1 胀形 5.2 翻边 5.3 缩口 5.4 校平与整形
返回目录
概述 成形:用不同性质的局部变形来改变毛坯或半
成品形状和尺寸的冲压工序。 伸长类成形:如胀形和内缘翻边,受拉应力而产
生伸长变形,易被拉裂而破坏;
压缩类成形:如缩口和外缘翻边,受压应力而产
(4)翻边力的计算
翻边力一般不大,非圆孔翻边力比圆孔翻边力小
圆柱形凸模:
F=1.1 (D-d0 )ts
圆锥形(球形)凸模:
F=1.2 tDms
(m=0.05~0.25)
5.2.2 外缘翻边 沿毛坯的曲边,使材料的拉伸或压缩,形成
高度不大的竖边。
1.分类 (1)外凸外缘翻边:属压缩类翻边,近似于局
b —材料的抗拉强度(Mpa);
A-局部成形面积;
二、压凸包
D—拉深件凸缘直径;
D 4 dp
dp—拉深件筒身外径;
当局部鼓凸的变形量较大时,应先成形加强 鼓凸肚部分,后成形其他周围部分。
如果工件要求的鼓凸深度超过许用成形高度, 则需先预成形球形到一定深度后,再冲压凸包到 设计深度。
5.1.3 圆柱形空心毛坯胀形 将空心件或管状坯料径向向外扩张,胀出所
成球形或抛物面形。(以避免成为拉深)凹模圆 角半径影响不大,一般取工件圆角半径(但应大 于翻边圆角半径)。
部浅拉深,易起皱。 (2)内凹外缘翻边:属伸长类翻边,近似于局
部孔翻边,易开裂。
2.变形程度 内凹外缘翻边的变形程度用翻边系数Es表示:
ES
b Rb
外凸外缘翻边的变形程度用翻边系数Ec表示:
Ec b Rb
3.外缘翻边力
k=0.2~0.3
F 1.25Ltk b
5.2.3 翻边模结构
1.结构 与拉深模相似,但凸模圆角半径较大,常做
设计手册,进行翻边模的设计。
翻边: 利用模具,将工件的孔边缘或外缘边缘翻成
竖立直边的成形方法。
5.2.1 内孔翻边 1.变形特点及变形系数
坯料受切向和径向拉伸,接近预孔边缘变形 大,易拉裂。
翻边系数
d K0 D
2.工艺计算与翻边力 (1)平板毛坯内孔翻边时预孔直径及翻边高度
d D 2(H 0.43r 0.72t)
课后思考
1、胀形的变形特点怎样?为什么采用胀形 工序加工的零件表面质量好?
2、什么叫胀形?胀形方法一般有哪几种? 各有什么特点?
3、胀形模的主要结构特点是什么?
5.2 翻边
学习目标: 能够掌握翻边的概念、成形特点及分类,掌
握翻边模的结构及工作原理。
教学要求: 掌握常见翻边模的工作过程,能够根据模具
a)加强肋 b)凸包
一、加强肋
1.变形部位受双向拉应力,其极限变形程度
式中极
极
l1
l l
100%
k
一起伏成形的极限变形程度
kl,l1一 一材胀料形单变向形拉区伸变的形延 前伸 后率 截面的长度
一形状系数,加强肋在0.7~0.75
(半圆肋取最大值,梯形肋取最小)
若加强肋不能一次成形,则应先压制半球形 过渡形状,再压出工件所需形状。
L0 = L [1+(0.3~0.4) ]+h
h—修边余量,一般取b=10~20mm; —制件切向最大伸长率; L —制件母线长度。
3.胀形力
软模胀形圆柱空心件的单位压力p
两端不固定
p
2t dmax
b
两端固定
p
2 b
t
d
max
t
2R
钢模胀形所需压力的计算公式,可根据力的
平衡方程式推导得到,其表达式为:
需凸起曲面的冲压方法。 根据模具的不同,可分为钢性胀形、橡胶模
胀形和液压胀形。
1—凸模 2—凹模 3—毛坯 4—软体介质 5—外套
1-上模 2-轴头 3-下模 4-管坯 加轴向压缩的液体胀形
1.胀形变形程度 胀形系数
K=dmax /d0
K-材料的胀形系数; Dmax–胀形后所能达到的最大直径; d–胀形前毛坯的直径;
拉应力,产生拉伸变形,材料变薄。
当坯料外径与成形直径的比值D/d>3时, 其成形完全依赖于直径为d的圆周以内金属厚度 的变薄实现表面积的增大而成形。
胀形主要有起伏成形和空心毛坯胀形两类。
5.1.2 起伏成形 通过材料局部拉深变形,形成凹进或凸起,
用于腹板类板料零件压制加强肋(加强工件刚 度)或压制凸包、凹坑、花纹图案及标记等。
生压缩变形,易起皱而破坏。
5.1 胀形
学习目标: 能够掌握胀形的概念、成形特点及分类,掌
握胀形模的结构及工作原理。
教学要求: 掌握常见胀形模的工作过程,能够根据模具
设计手册,进行胀形模的设计。
胀形:利用模具使坯料局部塑性变形,材料变薄, 表面积增大的冲压方法。
5.1.1 胀形成形的特点和分类 外部材料不进入变形区,变形区材料受双向
2
式中 D—翻边直径; r—翻边件半径; t—材料厚度。
(3)非圆孔翻边 变形特点: I部分视为圆孔翻边; II视为弯曲 变形;III部分视为拉深。
最小圆角部分进行允许 变形程度的校核。 翻边系数:
Kf =(0.85~0.9)K0 预制孔:分别按弯曲,翻边,拉深展开;圆弧处 宽度比直线部分宽5~10%,再光滑连结。
如加强肋与边缘的距离小于(3~5t) 时,在 成形中由于边缘的收缩,需考虑增加切边余量。
2.压筋力
F KLt b
对在曲柄压力机上用薄料(t<1.5mm)对小 工件(面积 <2000mm2)压肋或压肋兼有校形工 序时的变形力按式计算。
F KAt 2
K-系数,取0.7~1; L-加强肋长度(mm); t-材料料厚(mm);
H D d 0.43r 0.72t 2
内孔的翻边极限高度:
H max
D 2
(1
Kmin )
0.43r
0.72t
(2)在拉深件的底部冲孔翻边
允许的翻边高度:
h
D 2
(1
K0 )
0.57(r
t) 2
拉深高度: h` H h r
预孔直径: d K0D
或
d D 1.14(r t ) 2h
式中:
tan F 2 Ht b 1 2 2 tan
F 所需胀形力t 材料厚度
H 胀形后高度
t 材料厚度
摩擦系数,一般 0.15 ~ 0.20
芯
0
,12
0
,150
.
5.1.4 胀形模结构
1-凹模 2-分瓣凸模 3-拉簧 4-锥形芯块 斜块胀形模
墩压胀形模 1-上模板;2-上凹模;3-下凹模; 4-下模板;5-凸轮;6-轴承钉;7-手把;8-凸模
冷冲压工艺与模具设计教学课件 下载-样章.ppt
成形工艺与模具设计
概述 5.1 胀形 5.2 翻边 5.3 缩口 5.4 校平与整形
返回目录
概述 成形:用不同性质的局部变形来改变毛坯或半
成品形状和尺寸的冲压工序。 伸长类成形:如胀形和内缘翻边,受拉应力而产
生伸长变形,易被拉裂而破坏;
压缩类成形:如缩口和外缘翻边,受压应力而产
(4)翻边力的计算
翻边力一般不大,非圆孔翻边力比圆孔翻边力小
圆柱形凸模:
F=1.1 (D-d0 )ts
圆锥形(球形)凸模:
F=1.2 tDms
(m=0.05~0.25)
5.2.2 外缘翻边 沿毛坯的曲边,使材料的拉伸或压缩,形成
高度不大的竖边。
1.分类 (1)外凸外缘翻边:属压缩类翻边,近似于局
b —材料的抗拉强度(Mpa);
A-局部成形面积;
二、压凸包
D—拉深件凸缘直径;
D 4 dp
dp—拉深件筒身外径;
当局部鼓凸的变形量较大时,应先成形加强 鼓凸肚部分,后成形其他周围部分。
如果工件要求的鼓凸深度超过许用成形高度, 则需先预成形球形到一定深度后,再冲压凸包到 设计深度。
5.1.3 圆柱形空心毛坯胀形 将空心件或管状坯料径向向外扩张,胀出所
成球形或抛物面形。(以避免成为拉深)凹模圆 角半径影响不大,一般取工件圆角半径(但应大 于翻边圆角半径)。
部浅拉深,易起皱。 (2)内凹外缘翻边:属伸长类翻边,近似于局
部孔翻边,易开裂。
2.变形程度 内凹外缘翻边的变形程度用翻边系数Es表示:
ES
b Rb
外凸外缘翻边的变形程度用翻边系数Ec表示:
Ec b Rb
3.外缘翻边力
k=0.2~0.3
F 1.25Ltk b
5.2.3 翻边模结构
1.结构 与拉深模相似,但凸模圆角半径较大,常做
设计手册,进行翻边模的设计。
翻边: 利用模具,将工件的孔边缘或外缘边缘翻成
竖立直边的成形方法。
5.2.1 内孔翻边 1.变形特点及变形系数
坯料受切向和径向拉伸,接近预孔边缘变形 大,易拉裂。
翻边系数
d K0 D
2.工艺计算与翻边力 (1)平板毛坯内孔翻边时预孔直径及翻边高度
d D 2(H 0.43r 0.72t)
课后思考
1、胀形的变形特点怎样?为什么采用胀形 工序加工的零件表面质量好?
2、什么叫胀形?胀形方法一般有哪几种? 各有什么特点?
3、胀形模的主要结构特点是什么?
5.2 翻边
学习目标: 能够掌握翻边的概念、成形特点及分类,掌
握翻边模的结构及工作原理。
教学要求: 掌握常见翻边模的工作过程,能够根据模具
a)加强肋 b)凸包
一、加强肋
1.变形部位受双向拉应力,其极限变形程度
式中极
极
l1
l l
100%
k
一起伏成形的极限变形程度
kl,l1一 一材胀料形单变向形拉区伸变的形延 前伸 后率 截面的长度
一形状系数,加强肋在0.7~0.75
(半圆肋取最大值,梯形肋取最小)
若加强肋不能一次成形,则应先压制半球形 过渡形状,再压出工件所需形状。