新能源汽车电池包关键连接技术
探析新能源汽车电池技术存在的问题及对策
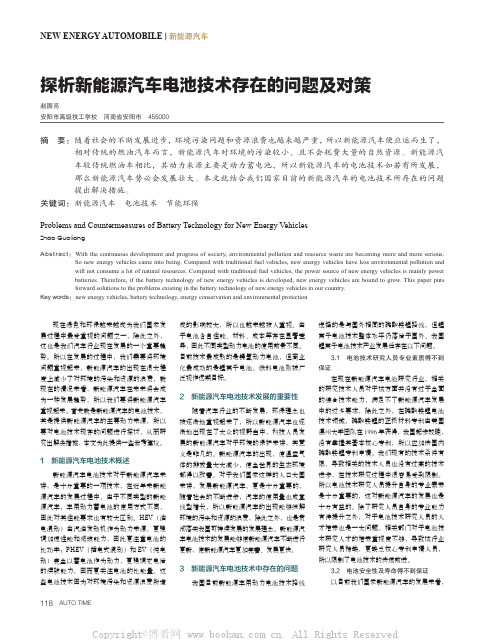
NEW ENERGY AUTOMOBILE | 新能源汽车探析新能源汽车电池技术存在的问题及对策赵国亮安阳市高级技工学校 河南省安阳市 455000摘 要: 随着社会的不断发展进步,环境污染问题和资源浪费也越来越严重,所以新能源汽车便应运而生了,相对传统的燃油汽车而言,新能源汽车对环境的污染较小、且不会耗费大量的自然资源。
新能源汽车较传统燃油车相比,其动力来源主要是动力蓄电池,所以新能源汽车的电池技术如若有所发展,那么新能源汽车势必会发展壮大。
本文就结合我们国家目前的新能源汽车的电池技术所存在的问题提出解决措施。
关键词:新能源汽车 电池技术 节能环保现在绿色和环保越来越成为我们国家发展过程中最受重视的问题之一,除此之外,这也是我们汽车行业现在发展的一个重要趋势。
所以在发展的过程中,我们需要将环境问题重视起来,新能源汽车的出现在很大程度上减少了对环境的污染和资源的浪费,就现在的情况来看,新能源汽车在未来将会成为一种发展趋势,所以我们要将新能源汽车重视起来。
首先就是新能源汽车的电池技术,其是提供新能源汽车的主要动力来源,所以要对电池技术现存的问题进行探讨,从而研究出解决措施,本文为此提供一些参考建议。
1 新能源汽车电池技术概述新能源汽车电池技术对于新能源汽车来讲,是十分重要的一项技术,在近年来新能源汽车的发展过程中,由于不同类型的新能源汽车,车用动力蓄电池的使用方式不同,因此对其性能要求也有较大区别。
HEV(油电混动)由汽油发动机作为动力来源,更强调加速性能和爬坡能力,因此更注重电池的比功率;PHEV(插电式混动)和EV(纯电动)完全以蓄电池作为动力,更强调充电后的续驶能力,因而更关注电池的比能量。
这些电池技术因为对环境污染和资源浪费所造成的影响较大,所以也越来越被人重视。
由于电池各自性能、材料、成本等存在显著差异,因此不同类型动力电池的使用前景不同。
目前技术最成熟的是镍氢动力电池,但商业化最成功的是锂离子电池,燃料电池则被广泛视作远期目标。
新能源汽车电池包内部串并联切换技术的原理

新能源汽车电池包内部串并联切换技术的原理新能源汽车电池包内部的串并联切换技术主要是为了提高电池包的性能、可靠性和灵活性。
其原理如下:1. 串联连接:在串联模式下,电池包中的各个电池单体依次连接,形成一个高电压的电池组。
电流在电池单体中依次流过,电压相加。
串联连接可以提高电池包的总电压,从而提供更高的动力输出。
2. 并联连接:在并联模式下,电池包中的各个电池单体并联连接,形成一个低电压、高电流的电池组。
电流可以同时流过多个电池单体,电流相加。
并联连接可以增加电池包的总电流容量,提供更长的续航里程。
3. 切换机制:串并联切换技术通过特定的电路和控制系统来实现电池单体之间的连接切换。
这个切换机制可以根据车辆的工作条件和需求,自动或手动地将电池单体进行串联或并联连接。
4. 优化性能:通过切换电池单体的串并联连接方式,电池包可以在不同的工况下实现最优的性能。
例如,在高速行驶或需要高功率输出时,采用串联连接以提供更高的电压;而在续航里程更为重要时,切换到并联连接以增加电流容量。
5. 电池管理系统:为了确保串并联切换的安全和有效性,电池管理系统(BMS)起着关键作用。
BMS 监测电池单体的状态,包括电压、电流、温度等参数,并根据这些信息来控制切换过程,以防止过充、过放、过热等问题。
6. 平衡和保护:在串并联切换过程中,还需要考虑电池单体之间的平衡和保护。
不平衡的电池单体可能会影响整个电池包的性能和寿命。
因此,BMS 通常会采用均衡充电等技术来保持电池单体之间的电量平衡,并在必要时进行保护措施,如断开故障电池单体的连接。
通过电池包内部的串并联切换技术,新能源汽车可以根据不同的行驶需求和工况,灵活调整电池组的连接方式,以实现更好的能量利用效率和性能。
这有助于提高电动汽车的续航里程、加速性能和整体可靠性。
但需要注意的是,串并联切换技术的实现需要复杂的电路设计和高效的控制系统,同时也对电池管理和保护提出了更高的要求。
新能源及三电系统紧固连接关键技术

新能源及三电系统紧固连接关键技术引言:随着新能源汽车的快速发展,三电系统作为其核心组成部分,正成为汽车行业的热门领域。
而在三电系统的构建中,紧固连接技术的重要性不可忽视。
本文将重点探讨新能源及三电系统紧固连接的关键技术,以及其在新能源汽车行业中的重要作用。
一、紧固连接的定义和作用紧固连接是通过螺栓、螺母等紧固件将两个或多个零部件连接在一起,以实现机械装配或固定的技术。
在新能源及三电系统中,紧固连接技术起到了至关重要的作用。
首先,它能够确保系统的稳定性和可靠性,避免在工作过程中发生松动或脱落现象。
其次,紧固连接还能够提高系统的密封性和防护性能,保证系统在恶劣环境下的正常工作。
因此,掌握新能源及三电系统的紧固连接关键技术对于确保整个系统的正常运行至关重要。
二、新能源及三电系统紧固连接的关键技术1. 材料选择:在新能源及三电系统的紧固连接中,材料的选择至关重要。
由于新能源汽车在工作过程中需要承受较大的载荷和振动,因此选择具有高强度和良好韧性的材料非常重要。
目前,常用的材料包括高强度钢、不锈钢和合金材料等。
2. 螺纹设计:螺纹是紧固连接的核心部分,其设计合理与否直接影响到连接件的强度和紧固性能。
在新能源及三电系统紧固连接中,需要考虑螺纹的尺寸、牙型和牙距等因素。
合理的螺纹设计能够提高连接件的紧固效果,并能够减少松动和脱落的可能。
3. 紧固力控制:在紧固连接过程中,控制紧固力的大小十分重要。
过大的紧固力可能导致连接件变形或损坏,而过小的紧固力则可能导致连接件松动。
因此,需要通过合适的紧固工具和紧固步骤来控制紧固力的大小,确保连接件的紧固效果。
4. 表面处理:新能源及三电系统在工作过程中常常需要承受恶劣的工作环境,如高温、湿度等。
为了提高连接件的耐腐蚀性和抗氧化性能,需要对连接件进行合适的表面处理,如镀锌、镀铬等。
5. 检测与质量控制:为了确保紧固连接的质量和可靠性,需要进行合适的检测与质量控制。
常用的检测方法包括力矩扳手检测、超声波检测和视觉检测等。
新能源汽车核心技术详解电池包和BMSVCUMCU
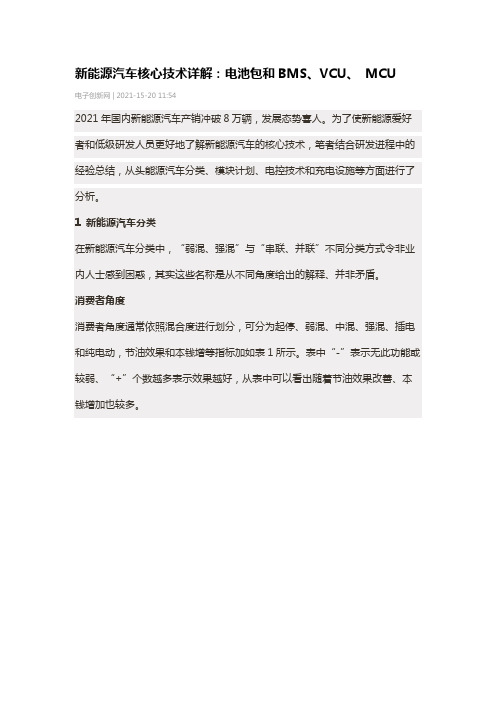
新能源汽车核心技术详解:电池包和BMS、VCU、MCU电子创新网 | 2021-15-20 11:542021年国内新能源汽车产销冲破8万辆,发展态势喜人。
为了使新能源爱好者和低级研发人员更好地了解新能源汽车的核心技术,笔者结合研发进程中的经验总结,从头能源汽车分类、模块计划、电控技术和充电设施等方面进行了分析。
1 新能源汽车分类在新能源汽车分类中,“弱混、强混”与“串联、并联”不同分类方式令非业内人士感到困惑,其实这些名称是从不同角度给出的解释、并非矛盾。
消费者角度消费者角度通常依照混合度进行划分,可分为起停、弱混、中混、强混、插电和纯电动,节油效果和本钱增等指标加如表1所示。
表中“-”表示无此功能或较弱、“+”个数越多表示效果越好,从表中可以看出随着节油效果改善、本钱增加也较多。
技术角度图1 技术角度分类技术角度由简到繁分为纯电动、串联混合动力、并联混合动力及混联混合动力,具体如图1所示。
其中P0表示BSG(Belt starter generator,带传动启停装置)系统,P1代表ISG(Integrated starter generator,启动机和发电机一体扮装置)系统、电机处于发动机和聚散器之间,P2中电机处于聚散器和变速器输入端之间,P3表示电机处于变速器输出端或布置于后轴,P03表示P0和P3的组合。
从统计表中可以看出,各类结构在国内外乘用或商用车中均取得普遍应用,相对来讲P2在欧洲比较流行,行星排结构在日系和美系车辆中占主导地位,P03等组合结构在四驱车辆中应用较为普遍、欧蓝德和标致3008均已实现量产。
新能源车型选择应综合考虑结构复杂性、节油效果和本钱增加,例如由通用、克莱斯勒和宝马联合开发的三行星排双模系统,虽然节油效果较好,但由于结构复杂且本钱较高,近十年间的市场表现不尽如人意。
2 新能源汽车模块计划虽然新能源汽车分类复杂,但其中共用的模块较多,在开发进程中可采用模块化方式,共享平台、提高开发速度。
动力电池包安装流程及注意事项

动力电池包安装流程及注意事项
动力电池包的安装流程:
导热垫、水管安装:首先安装导热垫和水管。
模组安装:然后安装电池模组。
水冷系统气密性检测:通过加压、保压检测水冷系统的气密性。
高低压线束安装:接着安装高低压线束。
高压绝缘测试:进行高压绝缘测试。
阻燃隔热防护层安装:安装阻燃隔热防护层,以进一步降低热失控风险。
上盖安装:安装电池包的上盖。
Pack气密性检测:进行Pack的气密性检测。
EOL下线测试:进行EOL下线测试。
动力电池下线:最后,动力电池下线。
在安装过程中注意事项:
所有电线的连接必须牢固,裸露的铜丝禁止相互碰接(包括交叉碰接),这样容易使控制器损坏以及出现锂离子电池保护板保护,出现不亮灯的情况。
新能源汽车电池包装配方案的研究
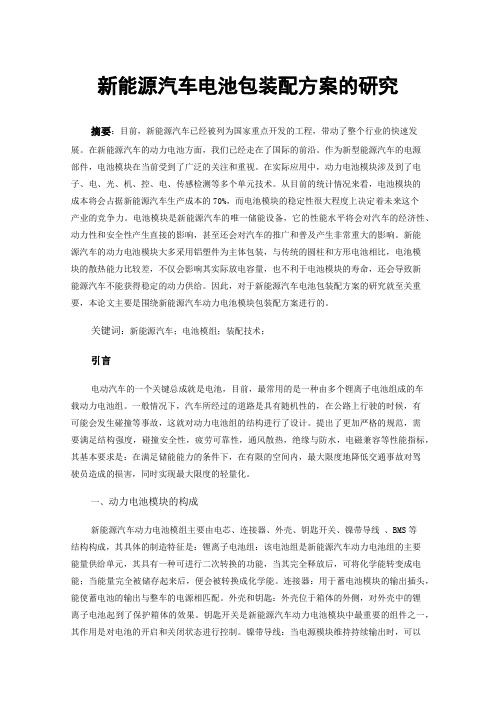
新能源汽车电池包装配方案的研究摘要:目前,新能源汽车已经被列为国家重点开发的工程,带动了整个行业的快速发展。
在新能源汽车的动力电池方面,我们已经走在了国际的前沿。
作为新型能源汽车的电源部件,电池模块在当前受到了广泛的关注和重视。
在实际应用中,动力电池模块涉及到了电子、电、光、机、控、电、传感检测等多个单元技术。
从目前的统计情况来看,电池模块的成本将会占据新能源汽车生产成本的70%,而电池模块的稳定性很大程度上决定着未来这个产业的竞争力。
电池模块是新能源汽车的唯一储能设备,它的性能水平将会对汽车的经济性、动力性和安全性产生直接的影响,甚至还会对汽车的推广和普及产生非常重大的影响。
新能源汽车的动力电池模块大多采用铝塑件为主体包装,与传统的圆柱和方形电池相比,电池模块的散热能力比较差,不仅会影响其实际放电容量,也不利于电池模块的寿命,还会导致新能源汽车不能获得稳定的动力供给。
因此,对于新能源汽车电池包装配方案的研究就至关重要,本论文主要是围绕新能源汽车动力电池模块包装配方案进行的。
关键词:新能源汽车;电池模组;装配技术;引言电动汽车的一个关键总成就是电池,目前,最常用的是一种由多个锂离子电池组成的车载动力电池组。
一般情况下,汽车所经过的道路是具有随机性的,在公路上行驶的时候,有可能会发生碰撞等事故,这就对动力电池组的结构进行了设计。
提出了更加严格的规范,需要满足结构强度,碰撞安全性,疲劳可靠性,通风散热,绝缘与防水,电磁兼容等性能指标,其基本要求是:在满足储能能力的条件下,在有限的空间内,最大限度地降低交通事故对驾驶员造成的损害,同时实现最大限度的轻量化。
一、动力电池模块的构成新能源汽车动力电池模组主要由电芯、连接器、外壳、钥匙开关、镍带导线、BMS等结构构成,其具体的制造特征是:锂离子电池组:该电池组是新能源汽车动力电池组的主要能量供给单元,其具有一种可进行二次转换的功能,当其完全释放后,可将化学能转变成电能;当能量完全被储存起来后,便会被转换成化学能。
新能源汽车技术路线及关键技术

项目一
项目二
项目三
项目四
项目五
项目六
任务一 任务二 任务三
小型纯电动汽车方面,针对大规模商业化示范需求, 开发系列化特色纯电驱动车型及其能源供给系统,并探 索新型商业化模式。实现小型纯电动汽车(含增程式) 关键技术突破,重点掌握电气系统集成、动力系统匹配 和整车热-电综合管理等技术。开发出舒适、安全、性价 比高的小型纯电动轿车系列产品。
项目一
项目二
项目三
项目四
项目五
项目六
任务一 任务二 任务三
5 混合动力电动汽车 针对常规混合动力电动汽车大规模产业化需求,开展系
列化混合动力系统总成开发,协调控制、能量管理等关键技 术攻关和整车产品的产业化技术研发,将节能环保发动机开 发与电动化技术有机结合,重点突破产品性价比,形成市场 竞争优势;突破混合动力电动汽车产业化关键技术,构建混 合动力电动汽车零部件配套保障体系,开展批量化生产装备 与工艺、质量管理体系及配套的维修检测设备开发,建成混 合动力电动汽车专用的装配、检测、检验生产线。
小结
一、新能源汽车技术路线 二、新能源汽车关键技术
后测
TtronClass 畅课
作业
P40 任务练习问答题1、2
第二类
动力电池容量较 小,大部分工况下 要由内燃机提供驱 动功率的电动汽车 (称为常规混合动 力电动汽车)。
项目一
项目二
项目三
项目四
项目五
项目六
任务一 任务二 任务三
从培育战略性新兴产业角度看,发展电气化程度比较高 的“纯电驱动”电动汽车是我国新能源汽车技术的发展方 向和重中之重。
要在坚持节能与新能源汽车“过渡与转型”并行互动、 共同发展的总体原则指导下,规划电动汽车技术发展战略 。
基于大数据分析的电动汽车动力电池包关键技术研究及应用(高明裕)
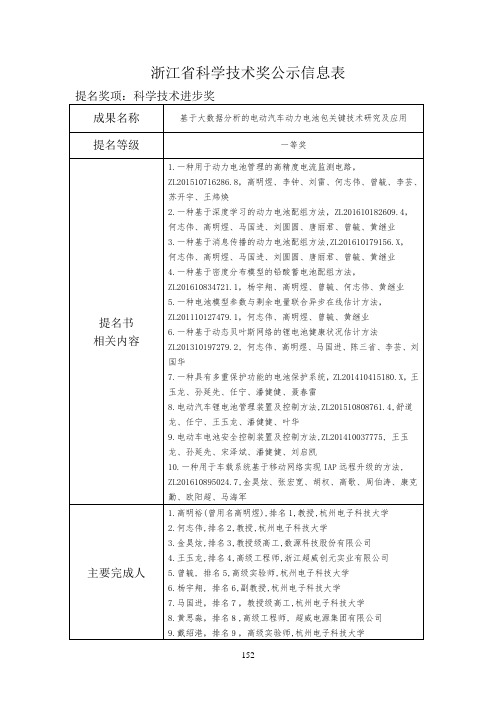
9.电动车电池安全控制装置及控制方法,ZL201410037775,王玉龙、孙延先、宋泽斌、潘健健、刘启凯
10.一种用于车载系统基于移动网络实现IAP远程升级的方法,ZL201610895024.7,金昊炫、张宏宽、胡权、高歌、周伯涛、康克勤、欧阳超、马海军
主要完成人
1.高明裕(曾用名高明煜),排名1,教授,杭州电子科技大学
浙江省科学技术奖公示信息表
提名奖项:科学技术进步奖
成果名称
基于大数据分析的电动汽车动力电池包关键技术研究及应用
提名等级
一等奖
提名书
相关内容
1.一种用于动力电池管理的高精度电流监测电路,ZL201510716286.8,高明煜、李钟、刘雷、何志伟、曾毓、李芸、苏开宇、王炜焕
2.一种基于深度学习的动力电池配组方法,ZL201610182609.4,何志伟、高明煜、马国进、刘圆圆、唐丽君、曾毓、黄继业
9.戴绍港,排名9,高级实验师,杭州电子科技大学
10.张宏宽,排名10,教授级高工,数源科技股份有限公司
11.李芸, 排名11,高级实验师,杭州电子科技大学
12.蒋力放,排名12,教授级高工,数源科技股份有限公司
13.丁毅,排名13,高级工程师,数源科技股份有限公司
主要完成位
1.单位名称:杭州电子科技大学
6.一种基于动态贝叶斯网络的锂电池健康状况估计方法ZL201310197279.2,何志伟、高明煜、马国进、陈三省、李芸、刘国华
7.一种具有多重保护功能的电池保护系统,ZL201410415180.X,王玉龙、孙延先、任宁、潘健健、聂春雷
8.电动汽车锂电池管理装置及控制方法,ZL201510808761.4,舒道龙、任宁、王玉龙、潘健健、叶华
- 1、下载文档前请自行甄别文档内容的完整性,平台不提供额外的编辑、内容补充、找答案等附加服务。
- 2、"仅部分预览"的文档,不可在线预览部分如存在完整性等问题,可反馈申请退款(可完整预览的文档不适用该条件!)。
- 3、如文档侵犯您的权益,请联系客服反馈,我们会尽快为您处理(人工客服工作时间:9:00-18:30)。
新能源汽车电池包关键连接技术
1 序言
近年来,受益于国家优惠政策,新能源汽车行业得到了蓬勃发展,其销量也在逐年递增。
为了适应并扩大市场需求,解决“里程焦虑”的问题,新能源汽车正不断地追求着轻量化。
电池包作为新能源汽车开发中十分重要的部件,其趋同的技术与生产水平备受人们的关注[1]。
目前,行业内普遍使用的电池包箱体有:铝型材电池包箱体、铸铝电池包箱体和钣金电池包箱体等。
钣金电池包箱体安全性、可靠性高,多数使用在公共交通工具上,如公交车。
对于小型轿车而言,多数使用的是铝制电池包箱体。
铝制电池包箱体承载结构主要分为两种:底板承载式结构和框架承载式结构。
大众公司在研究中发现框架承载式结构更容易实现轻量化以及满足不同结构下的强度要求,并将此结构应用于奥迪A6EV车型上[2]。
依据承载结构的不同,其对应的生产工艺流程、方法也存在一定的差别。
本文针对电池包箱体制造的关键连接技术:钨极氩弧焊、熔化极气体保护焊、搅拌摩擦焊、激光焊以及新兴的螺栓自拧紧技术(FDS)和胶接技术等分别进行介绍。
2 传统熔化焊
2.1交流钨极氩弧焊
钨极氩弧焊(TIG焊)属于非熔化极惰性气体保护焊的一种,是在惰性气体的保护下,利用钨极与焊件间产生的电弧热熔化母材和填充焊丝(也可以不加焊丝),从而形成优质焊缝的焊接方法[3]。
交流TIG焊在焊接时具
有电弧与熔池的可见性好、操作简单、焊缝外观无焊灰及不需清洁等优点,并且具有清理氧化膜的作用,因此非常适合铝制电池包箱体的焊接。
此外,对于空间狭小的短焊缝焊接以及密封性要求高的焊缝也尤为合适。
例如,比亚迪和吉利旗下多款混动车型的电池包箱体,在生产制造过程中均大量采用交流TIG焊,实现壳体的连接,保证工件气密性,其TIG焊缝约占箱体总焊缝量的80%。
某车型电池包下箱体焊缝如图1所示,箱体结构紧凑,型材刚度大,可以选择交流TIG焊。
然而,随着箱体结构的演变,箱体尺寸在变大、型材结构在变薄、焊接结构在优化以及焊后尺寸精度要求在提高,因此交流TIG焊的优势并不凸显。
相反,其缺点:焊接速度慢、焊接热输入大、焊后变形大、不易控制等,限制了箱体的高效生产。
因此,热输入小、变形小、工作效率高的熔化极气体保护焊开始渐渐取代TIG焊。
图1 某车型电池包下箱体焊缝
2.2CMT焊
CMT(Cold Metal Transfer)是一种全新的MIG/MAG焊接工艺,它是利用一个较大的脉冲电流使得焊丝顺利起弧,并在焊丝端部熔化长大,在熔滴即将发生脱落的时刻,电流急剧衰减至几乎为零,利用熔滴与熔池的表面张力、熔滴自身重力和焊丝的机械回抽作用,实现熔滴的完美过渡,从而形成连续的焊缝[4]。
相比传统MIG焊,CMT技术具有热输入小、无飞溅、电弧稳定以及焊接速度快等优点,可用于多种材料的焊接,在铝制电池托盘的生产制造中占据着举足轻重的地位。
例如,比亚迪、北汽旗下多款车型所使用的电池包下箱体结构,多采用CMT焊接技术,其焊缝约占箱体焊缝的70%。
箱体简易结构如图2所示,边框与底板(采用间断
焊或整圈满焊)以及横梁与底板之间的焊接均采用CMT焊接工艺,只有底板背部为搅拌摩擦焊。
多数电池包箱体供应商在生产制造过程中,为了保证焊接质量(见图3),引用机器手自动化焊接取代人工焊接,提高了生产效率,保证了焊缝的一致性及工件精度。
图2 电池包下箱体熔化焊简易结构
图3 铝制电池包箱体CMT焊缝
虽然随着自动化程度的提高,MIG焊在电池包箱体焊接中占据的比重越来越高,但是其仍难摆脱铝合金传统熔化焊的焊接问题,如热输入大引起的变形、气孔、焊接接头系数低等。
因此,高效绿色、焊接质量更高的搅拌摩擦焊技术走进了人们的视野。
3 搅拌摩擦焊
搅拌摩擦焊(FSW)是英国剑桥焊接研究所发明的一种固相连接技术。
与传统熔化焊焊接原理不同,FSW是以旋转的搅拌针以及轴肩与母材摩擦产生的热为热源,通过搅拌针的旋转搅拌和轴肩的轴向力实现对母材的塑化流动,最终得到区别于熔化焊铸造组织的精细锻造组织的焊接接头[5]。
FSW具有焊接变形小、无裂纹及气孔等缺陷,且焊接接头强度高、密封性好等优点,被广泛应用于电池包箱体焊接领域。
例如,吉利、小鹏旗下多款车型的电池包箱体均采用双面搅拌摩擦焊结构。
其简易结构如图4所示,此结构主体部分使用FSW,只有边梁以及小件等少量焊缝采用熔化焊,提高了生产效率以及箱体的整体安全性能。
常规的单轴肩FSW后会产生飞边,增加了焊缝打磨的工作量(见图5)。
为了减少甚至解决飞边问题,催生了恒压力FSW、静止轴肩FSW等技术。
图4 电池包箱体FSW简易结构
图5 铝制电池包箱体FSW焊缝
常规电池包箱体生产工艺流程为边框与底板的独立焊接,之后进行组装焊接。
单独的底板模块进行单轴肩FSW,其焊接作业效率低,底板变形调控较难。
目前,国内外均开始研究该结构的双机头焊接(见图6),通过双面同时焊接,降低底板变形量,同时缩短单工序作业时间。
图7所示为双机头FSW焊接打样产品,其整体平面度控制在2mm以内。
图6 双机头FSW模拟
图7 双机头FSW焊接产品
4 激光焊
激光焊是属于高能束焊的一种,是利用能量密度极高的激光束照射在待焊材料表面,使材料熔化并形成可靠的连接接头[6]。
随着激光技术的成熟,激光焊接在车身制造中被广泛应用(见图8),主要用于汽车车门、前后盖、顶盖、流水槽和侧围外板等零部件的焊接[7,8]。
在新能源汽车电池包领域,激光焊也有应用实例,如2018年上海凌云科技股份有限公司为大众汽车制造的一款电池包,已经顺利交付生产。
但是,由于激光焊设备前期投资成本高、回报周期长,以及铝合金激光焊接困难等原因,激光焊并没有得到广泛应用。
图8 激光焊接铝合金焊缝
5 其他焊接工艺
随着新能源汽车电池包箱体结构的演变,其相应的生产制造技术也在不断地更新。
为了缓解焊接变形对箱体尺寸精度的影响,出现了螺栓自拧紧技术(FDS)和胶接技术等,其中比较出名的企业有德国WEBER公司和美国3M公司。
5.1螺栓自拧紧技术(FDS)
FDS连接技术是一种通过设备中心拧紧轴将电动机的高速旋转传导至待连接板料摩擦生热产生塑性形变后,自攻螺丝并螺栓连接的冷成形工艺[9],如图9所示。
通常配合机器人使用,自动化程度高。
在新能源电池包制造领域,该工艺主要应用于框架式结构箱体,配合胶接工艺,在保证足够连接强度的同时实现箱体的密封性能。
例如,蔚来某款车型的电池包箱体就采用了FDS技术,并已经量化生产。
虽然FDS技术优势明显,但是也有其缺点:设备成本高、焊后凸起以及螺钉造价昂贵等,另外使用工况也限制了自身的应用。
图9 FDS技术连接效果
5.2胶接技术
胶接技术是一种利用胶粘剂在连接面上产生机械结合力、物理吸附力和化学键合力而使材料连接起来的工艺方法[10]。
胶接技术不需要高温高压环境,因此它具有不易变形、结合应力分布均匀的优点。
据3M公司介绍,胶接技术在新能源汽车电池包上已经开始应用,如底板的拼接使用胶接技术,其结构胶的最大抗剪力可以达到40MPa。
综合分析,胶接技术可以。