化学镀镍金常见问题分析
化学镀镍问题及对策

化学镍故障与对策
状况 镀液分解 浴液的混浊 析出速度过快 析出速度过慢
无析出反应 析出皮膜粗糙
原因
pH 值过高
镀浴负荷过大 过多活化钯带入 镀液局部过热 亚磷酸镍的生成
pH 值偏高 镀液温度偏高 镀液不平衡 pH 值偏低
镀液温度偏低 镀液不平衡 金属或有机污染
镀液老化 pH 值偏低
镀液温度偏低 前处理不良
避免发生 分批逐次添加并修正 补充量 Nhomakorabea光泽不良
发生斑点
针孔 peeling
pH 值偏高 负载过小 pH 偏高 镀浴浓度过低 重金属混入 镀液老化 後水洗及乾燥不充份 pH 偏高 前处理不良 镀浴浓度过高 前处理不良 素材表面不良 前处理不良(脱脂不 良) 工件中途吊起 单次药液补充过量
式调整 以稀硫酸降低 pH 值 修正负载比例 以稀硫酸降低 pH 值 镀液调整 重新建浴 重新建浴 加强水洗及热水洗 以稀硫酸降低 pH 值 改善前处理 补充蒸发水份 改善前处理 检查素材表面 改善前处理
前处理不良 有不溶解物带入 氢氧化镍生成
改善对策
pH 值测量应在补充添加
彻底搅拌後进行
修正负载比例
加强水洗
充份搅拌并注意温控 镍浓度及 pH 值确认在 正常操作范围,降低液 温至 20 ~40℃後添加 适量建浴液充份搅拌 添加稀硫酸降低 pH 值 温度控制在 84~92℃ 分析添加镀液组成 以稀释 2 倍氨水调整 pH 值 温度控制在 84~92℃ 分析添加镀液组成 假镀去除金属,以活性 碳去除有机污染 重新建浴 以稀释 2 倍氨水调整 pH 值 改善浴温控制 脱脂、酸活化、活化钯 等要确认条件 加强前处理 加强过滤 注意 pH 控制及搅拌方
化金常见异常及改善
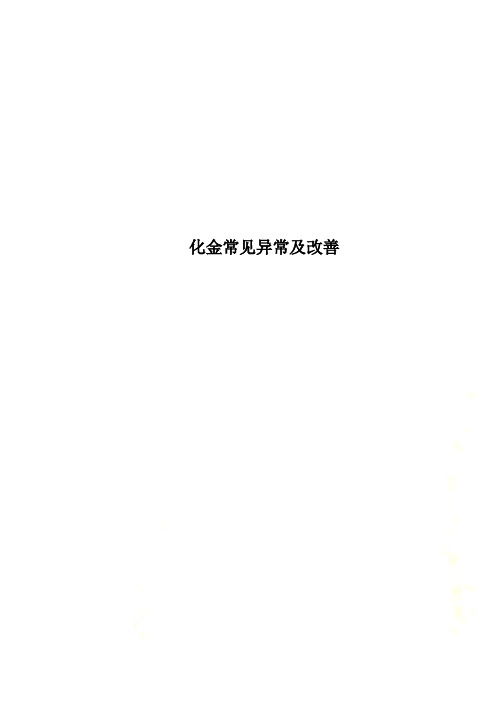
化金常见异常及改善常见问题的原因及处理方案1.漏镀产生原因及解决方案A、镍缸方面①.镍缸拖缸效果差,未能很好激发其活性:重新拖缸,拖缸时镍缸温度提升至82-85℃之间或负载加大或时间延长则可解决。
②.镍缸温度低于75℃或PH值低于4.0:检查温度和PH值,使其不脱离控制范围。
③.镍缸D剂含量过高:正确使用D剂,停产1天以上则额外补加1ml/L,平时按正常比例补加。
④.镍缸打气过强:适当调整其打气流量。
⑤.镍缸空载时间过长或负载不够:保证生产连续性,负载不足加挂拖缸板共镀。
⑥.镍缸加热管漏电:将漏电加热管换掉;B、活化方面①.活化Pd2+浓度低:添加钯水提高Pd2+浓度;②.活化温度太低(低於20℃):加强检测频率,留意温控效果。
③.活化CU2+高,已到后期:更换新活化。
④.活化处理时间过短:正确掌握活化处理时间。
C、板子方面①.线路图形设计不合理,存在电位差,生产时产生化学电池效应出现漏镀:前处理磨板时仅磨板不过微蚀,适当延长活化时间并提高镍缸的活性。
②.阻焊油塞孔未塞满填平,生产中水洗不足,造成药水污染铜面:加大水洗流量。
③.板面铜层显影不净或毒钯处理时遭硫化物污染:检查前工序,毒钯处理应当在蚀刻后退锡前进行,生产此种板需加强磨刷和水平微蚀。
④.板面铜层退锡不净:重新剥锡至铜面干净。
⑤.挠性板溢胶:检查压合工序,控制压合品质。
D、其他方面①.板子活化后在空气中裸露太久钯钝化:防止板子裸露空气中,天车故障及时将板移入对应水洗槽。
②.活化后酸洗或水洗太久,促使钯剥离或铜面遭氧化:活化后酸洗和水洗总时间保持在3分钟以内。
③.新配后浸酸温度太高使钯剥离:新配后浸需将温度下降到30℃以下才可生产。
2.渗镀产生原因及预防改善对策A、活化时间过长或活化水洗不足:致使镀镍时出现长胖现象,严重的则表现为跨镀。
预防及改善:①.活化时间控制在工艺范围内。
②.加大活化后水洗流量,并且活化后水洗每班更新一次。
若中途停纯水则需停止生产,待有纯水后再生产。
手把手教你化学镀镍的常见故障及解决办法

手把手教你化学镀镍的常见故障及解决办法(1)沉积速度慢(这点也是平台上最多朋友咨询的)造成这种现象的原因与解决方法:镀液pH值过低:测pH值调整,并控制pH在下限值。
虽然pH 值较高能提高沉速,但会影响镀液稳定性。
镀液温度过低:要求温度达到规范时下槽进行施镀。
新开缸第一批工件下槽时,温度应达到上限,反应开始后,正常施镀时,温度在下限为好。
溶液主成分浓度低:分析调整,如还原剂不足时,添加还原补充液;镍离子浓度偏低时,添加镍盐补充液。
对于上规模的化学镀镍,设自动分析、补给装置是必要的,可以延长连续工作时间(由30h延至56h)和镍循环周期(由6周延至11周)。
亚磷酸根过多:弃掉部分镀液。
装载量太低:增加受镀面积至1dm2/L。
稳定剂浓度偏重:倾倒部分,少量多次加浓缩液。
(2)镀液分解(镀液呈翻腾状,出现镍粉)造成这种现象的原因与解决方法:温度过高或局部过热:搅拌下加入温去离子水。
次亚磷酸钠大多:冲稀补加其它成分。
镀液的pH值过高:调整pH值至规范值。
机械杂质:过滤除去。
装载量过高:降至1dm2/L槽壁或设备上有沉淀物:滤出镀液,退镀清洗(用3HNO3溶液)。
操作温度下补加液料大多:搅拌下少量多次添加。
稳定剂带出损失:添加少量稳定剂。
催化物质带入镀液:加强镀前清洗。
镀层剥离碎片:过滤镀液。
(3)镀层结合力差或起泡造成这种现象的原因与解决方法:镀前处理不良:提高工作表面的质量,加工完成后应清除工件上所有的焊接飞溅物和焊渣。
工件表面的粗糙度应达到与精饰要求相当的粗糙义,如碳钢工件表面粗糙度Ra<>温度波动太大:控制温度在较小的范围波动。
下槽温度太低:适当提高下槽温度。
清洗不良:改进清洗工序。
金属离子污染:用大面积废件镀而除去。
有机杂质污染:活化炭1-2g/L 处理。
热处理不当:调整热处理时间和温度。
(4)镀层粗糙造成这种现象的原因与解决方法:镀液浓度过高:适当冲稀镀液。
镀液的pH值过高:降低pH值至规范值。
镀镍问题与解决方案

镀镍问题与解决方案引言概述:镀镍是一种常见的金属表面处理方法,它可以提高金属的耐腐蚀性、硬度和外观。
然而,在镀镍过程中,我们常常会遇到一些问题,如镀层不均匀、气泡、缺陷等。
为了解决这些问题,我们需要采取一些有效的解决方案。
正文内容:1. 镀层不均匀问题:1.1 控制电流密度:调整电流密度可以使镀层均匀。
在镀层不均匀的区域增加电流密度,而在均匀的区域减少电流密度。
1.2 改善搅拌条件:通过改善搅拌条件,如增加搅拌桨的数量或改变搅拌桨的位置,可以使电解液均匀分布,从而获得均匀的镀层。
2. 气泡问题:2.1 降低电流密度:气泡往往是由于过高的电流密度造成的。
降低电流密度可以减少气泡的产生。
2.2 提高搅拌效果:通过增加搅拌桨的转速或改变搅拌桨的形状,可以提高搅拌效果,将气泡从电解液中排出。
3. 缺陷问题:3.1 清洗金属表面:在镀镍之前,彻底清洗金属表面是非常重要的。
通过去除污垢、油脂和氧化物,可以减少缺陷的产生。
3.2 控制镀液温度:镀液温度对镀层质量有很大影响。
在适宜的温度范围内进行镀镍,可以减少缺陷的发生。
3.3 选择合适的镀液配方:不同的金属需要不同的镀液配方。
选择合适的镀液配方可以提高镀层的质量,减少缺陷的产生。
4. 防止镀层剥落问题:4.1 提高镀层附着力:通过在金属表面进行预处理,如机械打磨、化学处理等,可以增加镀层的附着力,防止镀层剥落。
4.2 控制镀液pH值:镀液的pH值对镀层的附着力有重要影响。
在适宜的pH范围内进行镀镍,可以提高镀层的附着力。
5. 提高镀层质量问题:5.1 优化镀液配方:通过调整镀液配方中的各种成分的比例,可以提高镀层的质量。
5.2 控制镀液温度和时间:镀液的温度和镀液时间对镀层质量有很大影响。
在适宜的温度和时间范围内进行镀镍,可以获得高质量的镀层。
总结:通过控制电流密度、改善搅拌条件、降低电流密度、提高搅拌效果、清洗金属表面、控制镀液温度、选择合适的镀液配方、提高镀层附着力、控制镀液pH值、优化镀液配方、控制镀液温度和时间等方法,可以解决镀镍过程中的一些常见问题,提高镀层的质量和均匀性,从而满足不同应用领域的需求。
化金常见异常及改善
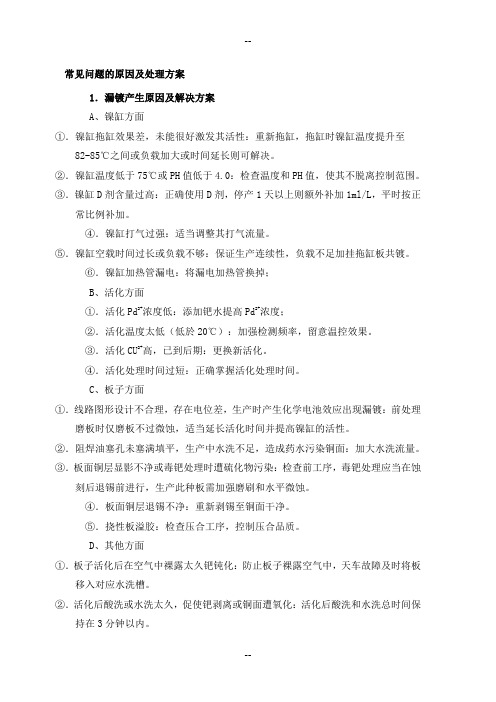
常见问题的原因及处理方案1.漏镀产生原因及解决方案A、镍缸方面①.镍缸拖缸效果差,未能很好激发其活性:重新拖缸,拖缸时镍缸温度提升至82-85℃之间或负载加大或时间延长则可解决。
②.镍缸温度低于75℃或PH值低于4.0:检查温度和PH值,使其不脱离控制范围。
③.镍缸D剂含量过高:正确使用D剂,停产1天以上则额外补加1ml/L,平时按正常比例补加。
④.镍缸打气过强:适当调整其打气流量。
⑤.镍缸空载时间过长或负载不够:保证生产连续性,负载不足加挂拖缸板共镀。
⑥.镍缸加热管漏电:将漏电加热管换掉;B、活化方面①.活化Pd2+浓度低:添加钯水提高Pd2+浓度;②.活化温度太低(低於20℃):加强检测频率,留意温控效果。
③.活化CU2+高,已到后期:更换新活化。
④.活化处理时间过短:正确掌握活化处理时间。
C、板子方面①.线路图形设计不合理,存在电位差,生产时产生化学电池效应出现漏镀:前处理磨板时仅磨板不过微蚀,适当延长活化时间并提高镍缸的活性。
②.阻焊油塞孔未塞满填平,生产中水洗不足,造成药水污染铜面:加大水洗流量。
③.板面铜层显影不净或毒钯处理时遭硫化物污染:检查前工序,毒钯处理应当在蚀刻后退锡前进行,生产此种板需加强磨刷和水平微蚀。
④.板面铜层退锡不净:重新剥锡至铜面干净。
⑤.挠性板溢胶:检查压合工序,控制压合品质。
D、其他方面①.板子活化后在空气中裸露太久钯钝化:防止板子裸露空气中,天车故障及时将板移入对应水洗槽。
②.活化后酸洗或水洗太久,促使钯剥离或铜面遭氧化:活化后酸洗和水洗总时间保持在3分钟以内。
③.新配后浸酸温度太高使钯剥离:新配后浸需将温度下降到30℃以下才可生产。
2.渗镀产生原因及预防改善对策A、活化时间过长或活化水洗不足:致使镀镍时出现长胖现象,严重的则表现为跨镀。
预防及改善:①.活化时间控制在工艺范围内。
②.加大活化后水洗流量,并且活化后水洗每班更新一次。
若中途停纯水则需停止生产,待有纯水后再生产。
镀镍问题与解决方案

镀镍问题与解决方案一、问题描述镀镍是一种常见的表面处理方法,用于提高金属制品的耐腐蚀性、硬度和美观度。
然而,在镀镍过程中可能会出现一些问题,如镀层不均匀、起泡、脱落等,影响了产品的质量和性能。
因此,寻找解决方案是至关重要的。
二、问题分析1. 镀层不均匀:镀层不均匀可能是由于镀液中金属离子分布不均匀、工件表面准备不良或电流密度不均等原因引起的。
2. 起泡:起泡问题可能是由于镀液中存在杂质、工件表面有油脂或气体等引起的。
3. 脱落:脱落问题可能是由于工件表面准备不良、镀液中含有杂质或电流密度过高等原因引起的。
三、解决方案1. 镀层不均匀的解决方案:a. 检查镀液中金属离子的浓度和分布情况,确保它们均匀分布。
b. 对工件进行充分的表面处理,包括清洗、除油、打磨等,以确保表面平整。
c. 调整电流密度,使其在工件表面均匀分布,避免出现过高或过低的电流密度区域。
2. 起泡的解决方案:a. 检查镀液中是否存在杂质,如有必要,进行滤液处理或更换新的镀液。
b. 在镀液中加入抗起泡剂,以减少气泡的形成。
c. 在工件表面进行充分的清洗和除油处理,以消除油脂和气体的影响。
3. 脱落的解决方案:a. 提高工件表面的粗糙度,以增加镀层与基材的附着力。
b. 检查镀液中是否含有杂质,如有必要,进行滤液处理或更换新的镀液。
c. 调整电流密度,避免过高的电流密度导致镀层与基材的结合不牢固。
四、实施效果评估在实施上述解决方案后,可以进行以下评估措施:1. 对镀层进行质量检测,包括镀层厚度、硬度、附着力等指标的测试,以确保镀层质量达到要求。
2. 对产品进行性能测试,如耐腐蚀性、耐磨性等,以评估解决方案的有效性。
3. 监测生产过程中的镀液情况,包括金属离子浓度、杂质含量等,以确保解决方案的持续有效性。
通过以上解决方案的实施和评估,可以有效解决镀镍过程中的问题,提高产品质量和性能,满足客户的需求。
同时,定期维护和监测镀液的状态,及时调整和改进解决方案,可以进一步提高镀镍过程的稳定性和可靠性。
化学镀镍过程常见疑难问题及解决方法
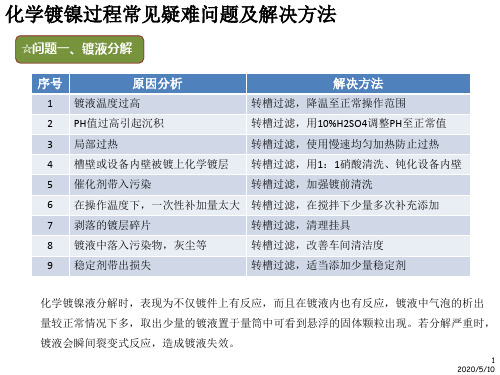
6 2014/6/3
化学镀镍过程常见疑难问题及解决方法
☆问题八、镀速低 序号
1 2 3 4 5
原因分析
镀液温度偏低 镀液PH值偏低 镍离子或还原剂浓度偏低 金属离子稳定剂浓度太高 镀液老化
解决方法
升高温度至正常范围 用稀NaOH(或NH4OH)调整PH值至正常范围 分析镀液,分别补充调整镍离子或还原剂浓度 至正常值 大面积假镀除去或者更换部分镀液 更换部分镀液
5 2014/6/3
化学镀镍过程常见疑难问题及解决方法
☆问题七、无镀速 序号
1 2
原因分析
稳定剂过高 表面未活化 更换部分镀液
解决方法
增强前处理酸化、活化方式
3 4
5
基体本身并非催化剂 镀液PH值,温度太低
金属离子污染
镀前表面催化处理,闪镀镍,浸胶体钯活化等 用稀NaOH(NH4OH)调整,升温至正常范围
解决方法
改进搅拌强度或方式
3 4
5
金属离子污染 工件表面残留物
“彗尾”,气带
大面积假镀除去或者更换部分镀液 改进镀前清洗工序,使用不含硅酸盐的清洗剂
重新安排槽内工作吊挂位置,改进搅拌方式
4 2014/6/3
化学镀镍过程常见疑难问题及解决方法
☆问题六、镀层晦暗失光 序号
1 2
原因分析
镀后清洗水污染 表面前处理不当
7 2014/6/3
化学镀镍过程常见疑难问题及解决方法
☆问题九、镍离子消耗过快 序号
1 2
原因分析
槽壁或设备上镀上化学镍层 槽负载过大 减少槽装载量
解决方法
转槽过滤,用1:1硝酸清洗,钝化槽壁或设备
3 4
镀镍问题与解决方案

镀镍问题与解决方案一、问题描述镀镍是一种常见的表面处理方法,用于提高金属制品的耐腐蚀性和装饰性。
然而,在镀镍过程中,可能会出现一些问题,如镀层不均匀、气泡、孔洞等。
这些问题会影响产品的质量和外观,因此需要找到相应的解决方案。
二、镀镍问题及解决方案1. 镀层不均匀问题描述:镀层在部分区域厚度不均匀,出现明显的颜色差异。
解决方案:- 检查电流密度:确保电流在整个镀镍过程中均匀分布,可以通过调整电流密度来解决问题。
- 检查镀液浓度:镀液浓度不均匀可能导致镀层不均匀,应确保镀液浓度均匀。
- 检查搅拌装置:搅拌装置的运行状况会影响镀液的流动性,进而影响镀层的均匀性,应确保搅拌装置正常运转。
2. 气泡问题问题描述:镀层表面出现气泡,影响镀层的光洁度和质量。
解决方案:- 检查镀液温度:镀液温度过高可能导致气泡产生,应控制镀液温度在适宜范围内。
- 检查镀液中的杂质:镀液中的杂质会促使气泡的形成,应定期清理镀液中的杂质。
- 检查镀液搅拌:充分搅拌镀液可以减少气泡的产生。
3. 孔洞问题问题描述:镀层表面出现孔洞,影响镀层的紧密性和耐腐蚀性。
解决方案:- 检查镀液成分:镀液成分不当可能导致孔洞的产生,应调整镀液成分以提高镀层的质量。
- 检查镀液pH值:镀液pH值过高或过低都会导致孔洞的产生,应保持镀液pH值在适宜范围内。
- 检查镀液搅拌:充分搅拌镀液可以减少孔洞的产生。
4. 其他问题除了上述常见的问题,镀镍过程中还可能出现其他问题,如黑斑、脱落等。
针对不同问题,可以采取以下解决方案:- 检查镀液中的杂质:杂质可能导致黑斑或脱落,应定期清理镀液中的杂质。
- 检查镀液温度和时间:温度和时间的控制可能影响镀层的质量,应确保镀液温度和时间在适宜范围内。
- 检查镀液pH值:pH值的不当可能导致镀层问题,应保持镀液pH值在适宜范围内。
三、总结镀镍过程中可能出现的问题包括镀层不均匀、气泡、孔洞等,这些问题会影响产品的质量和外观。
针对不同问题,可以采取相应的解决方案,如调整电流密度、镀液浓度、镀液温度和时间,清理镀液中的杂质等。
- 1、下载文档前请自行甄别文档内容的完整性,平台不提供额外的编辑、内容补充、找答案等附加服务。
- 2、"仅部分预览"的文档,不可在线预览部分如存在完整性等问题,可反馈申请退款(可完整预览的文档不适用该条件!)。
- 3、如文档侵犯您的权益,请联系客服反馈,我们会尽快为您处理(人工客服工作时间:9:00-18:30)。
化学镀镍/金常见问题分析
由于化学镍/金制程敏感,化学镍/金板的用途多种多样,且对表观要求极严,因此化学镀镍/金生产中所遇到的问题很多。
其中常见的一些问题及解决方法参见下表2。
问题
原因
解决方法
可焊性差
1)金层太厚或太薄;
2)沉金后受多次热冲击;
3)最终水洗不干净;
4)镍槽生产超过6MTO。
1)调整参数,使厚度在:0.05~0.15μm;
2)出板前用酸及DI水清洗;
3)更换水洗槽;
4)保持4~5MTO生产量。
Ni/Cu结合力差
1)前处理效果差;
2)一次加入镍成分太高1)检查微蚀量及更换除油槽;
2)用光板拖缸20~30min
Au/Ni结合力差
1)金层腐蚀;
2)金槽、镍槽之间水洗PH>8
3)镍面钝化1)升高金槽PH值;
2)检查水的质量;
3)控制镀镍后沉金前打气及停留时间
漏镀
1)活化时间不足;
2)镍槽活性不足1)提高活化时间;
2)使用校正液,提高镍槽活性
渗镀
1)蚀刻后残铜;
2)活化后镍槽前水洗不足;
3)活化剂温度过高;
4)钯浓度太高;
5)活化时间过长;
6)镍槽活性太强1)反馈前工序解决;
2)延时水洗或加大空气搅拌;
3)降低温度至控制范围;
4)降低浓度至控制范围;
5)降低活化时间;
6)适当使用稳定剂
镍厚偏低
1)PH 太低;
2)温度太低;
3)拖缸不足;
4)镍槽生产超6MTO 1)调高PH值;
2)调高温度;
3)用光板拖缸20~30min;
4)更换镍槽
金厚偏低
1)镍层磷含量高;
2)金槽温度太低;
3)金槽PH值太高;
4)开新槽时起始剂不足1)提高镍槽活性;
2)提高温度;
3)降低PH值;
4)适当加入起始剂
渗镀问题改善办法
随着电子产业的高速发展,PCB布线越来越精密,多数PCB厂家都采用干膜来完成图形转移,干膜的使用也越来越普及,但我在售后服务的过程中,仍遇到很多客户在使用干膜时产生很多误区,现总结出来,以便借鉴。
一,干膜掩孔出现破孔
很多厂家认为,出现破孔后,应当加大贴膜温度和压力,以增强其结合力,其实这种观点是不正确的,因为温度和压力过高后,抗蚀层的溶剂过度挥发,使干膜变脆变薄,显影时极易被冲破孔,我们始终要保持干膜的韧性,所以,出现破孔后,我们可以从以下几点做改善:
1,降低贴膜温度及压力
2,改善钻孔披锋
3,提高曝光能量
4,降低显影压力
5,贴膜后停放时间不能太长,以免导致拐角部位半流体状的药膜在压力的作用下扩散变薄
6,贴膜过程中干膜不要张得太紧
二,干膜电镀时出现渗镀
之所以渗镀,说明干膜与覆铜箔板粘结不牢,使镀液深入,而造成“负相”部分镀层变厚,多数PCB厂家发生渗镀都是由以下几点造成:
1,曝光能量偏高或偏低
在紫外光照射下,吸收了光能量的光引发剂分解成游离基引发单体进行光聚合反应,形成不溶于稀碱的溶液的体型分子。
曝光不足时,由于聚合不彻底,在显影过程中,胶膜溶胀变软,导致线条不清晰甚至膜层脱落,造成膜与铜结合不良;若曝光过度,会造成显影困
难,也会在电镀过程中产生起翘剥离,形成渗镀。
所以控制好曝光能量很重要。
2,贴膜温度偏高或偏低
如贴膜温度过低,由于抗蚀膜得不到充分的软化和适当的流动,导致干膜与覆铜箔层压板表面结合力差;若温度过高由于抗蚀剂中的溶剂和其它挥发性物质的迅速挥发而产生气泡,而且干膜变脆,在电镀电击时形成起翘剥离,造成渗镀。
3,贴膜压力偏高或偏低
贴膜压力过低时,可能会造成贴膜面不均匀或干膜与铜板间产生间隙而达不到结合力的要求;贴膜压力如果过高,抗蚀层的溶剂及可挥发成份过多挥发,致使干膜变脆,电镀电击后就会起翘剥离。