铝表面前处理及化学沉积镍初期行为
铝件化学镍钯金工艺流程

铝件化学镍钯金工艺流程一、铝件的前期处理。
铝件表面可不像我们看到的那么干净哦。
在进行化学镍钯金流程之前,要先把铝件表面的油污啥的去掉。
就像我们洗脸要把脏东西洗掉一样。
一般会用专门的除油剂,把铝件泡在里面,让那些油污自己乖乖地离开铝件的表面。
然后呢,铝件表面还有一层氧化膜,这层氧化膜可有点碍事啦。
得想办法把它去掉,这时候就会用到酸性的溶液。
不过这个酸性溶液的浓度可得控制好,太浓了就像大力水手吃多了菠菜,会把铝件本身也弄坏的。
把铝件放到酸性溶液里,氧化膜就慢慢溶解掉啦,这样铝件就露出了它原本的“小脸蛋”,准备迎接下一个工序。
二、化学镍过程。
接下来就是化学镍啦。
化学镍就像是给铝件穿上一层银色的铠甲。
这个过程呢,是在含有镍离子的溶液里进行的。
溶液里的镍离子就像一个个小士兵,慢慢地在铝件表面集合起来,形成一层镍层。
这时候,溶液的温度、pH值都很关键哦。
如果温度不合适,就像我们人感觉冷或者热的时候没精神一样,镍离子也没那么活跃,就不能很好地在铝件上“安家”。
pH值要是不对,那整个化学镍的过程就像在走歪路,可能会导致镍层不均匀或者长不出来。
三、化学钯过程。
有了镍层之后,就轮到化学钯啦。
化学钯的作用可大了呢。
它就像是在镍层上面又铺了一层精致的“地毯”。
钯离子会在镍层的基础上进行沉积。
这个过程的溶液成分也很讲究,要保证钯离子有足够的量,还得有合适的还原剂。
要是钯离子不够,那这层“地毯”就会薄得可怜,要是还原剂不合适,钯离子就没办法好好地变成金属钯附着在上面。
这一步就像是给铝件的防护又加了一道保险,让它更加耐用和稳定。
四、化学金过程。
最后就是化学金啦。
化学金就像是给铝件戴上了一个金色的皇冠。
金离子在合适的条件下会沉积在钯层上面。
这时候的溶液环境同样需要严格控制。
金层不仅让铝件看起来更加高大上,还在导电性和耐腐蚀性方面有很好的表现。
就像一个人穿了一身漂亮又实用的衣服。
而且这个金层很薄很薄,但是却有着大大的作用。
化学镍的工艺流程
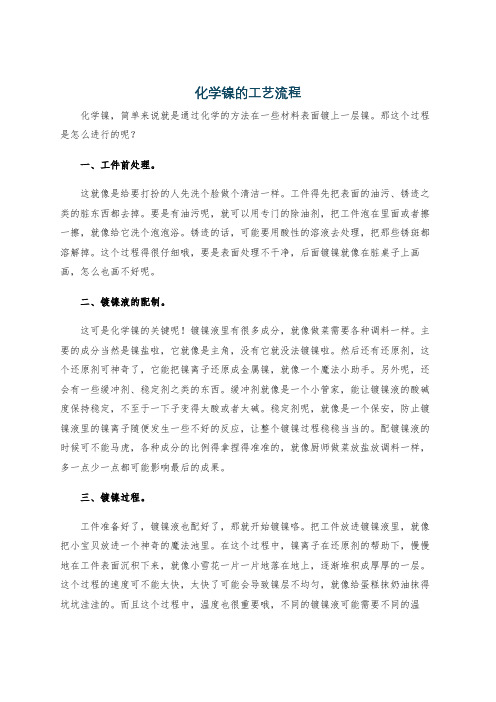
化学镍的工艺流程化学镍,简单来说就是通过化学的方法在一些材料表面镀上一层镍。
那这个过程是怎么进行的呢?一、工件前处理。
这就像是给要打扮的人先洗个脸做个清洁一样。
工件得先把表面的油污、锈迹之类的脏东西都去掉。
要是有油污呢,就可以用专门的除油剂,把工件泡在里面或者擦一擦,就像给它洗个泡泡浴。
锈迹的话,可能要用酸性的溶液去处理,把那些锈斑都溶解掉。
这个过程得很仔细哦,要是表面处理不干净,后面镀镍就像在脏桌子上画画,怎么也画不好呢。
二、镀镍液的配制。
这可是化学镍的关键呢!镀镍液里有很多成分,就像做菜需要各种调料一样。
主要的成分当然是镍盐啦,它就像是主角,没有它就没法镀镍啦。
然后还有还原剂,这个还原剂可神奇了,它能把镍离子还原成金属镍,就像一个魔法小助手。
另外呢,还会有一些缓冲剂、稳定剂之类的东西。
缓冲剂就像是一个小管家,能让镀镍液的酸碱度保持稳定,不至于一下子变得太酸或者太碱。
稳定剂呢,就像是一个保安,防止镀镍液里的镍离子随便发生一些不好的反应,让整个镀镍过程稳稳当当的。
配镀镍液的时候可不能马虎,各种成分的比例得拿捏得准准的,就像厨师做菜放盐放调料一样,多一点少一点都可能影响最后的成果。
三、镀镍过程。
工件准备好了,镀镍液也配好了,那就开始镀镍咯。
把工件放进镀镍液里,就像把小宝贝放进一个神奇的魔法池里。
在这个过程中,镍离子在还原剂的帮助下,慢慢地在工件表面沉积下来,就像小雪花一片一片地落在地上,逐渐堆积成厚厚的一层。
这个过程的速度可不能太快,太快了可能会导致镍层不均匀,就像给蛋糕抹奶油抹得坑坑洼洼的。
而且这个过程中,温度也很重要哦,不同的镀镍液可能需要不同的温度,就像不同的小动物需要不同的生活环境一样。
如果温度不合适,可能镍离子就不愿意乖乖地在工件上沉积了。
四、后处理。
镀镍完成了,还不能马上就大功告成呢。
还得给镀了镍的工件做个后处理。
比如说清洗一下,把表面可能残留的镀镍液洗干净,不然那些残留的东西可能会腐蚀镍层或者影响工件的外观。
铝合金电镀镍前处理工艺

铝合金电镀镍前处理工艺
铝合金化学镀镍前采用二次浸锌最普通,但浸锌存大的缺陷:①锌层易溶解于酸性化学镀镍溶液中;②由于基体与镍层之间夹杂锌层,在腐蚀介质中形成电偶腐蚀(Al-Zn-Ni),将导致镀层鼓泡或脱落,降低耐蚀性;③经浸锌后化学镀镍,不宜进行400oC热处理,会造成浸锌层空松。
同时铝和镍膨胀系数相差悬殊,在高温时会引起足够的应力,使镀层与铝之间产生破裂。
而以活化代替浸锌,为化学镀镍提供了一个较好的底层,镀层与在材有结合力能达到同浸锌一样好的结果,是一种很有用途的铝合金前处理新工艺。
活化处理液为:NiSO4。
6H2024~30g/L,HEDP40~50g/L,稳定剂N25~30ml/L,Ph(NaOH调整)>12,室温,1~4min。
控制活化时间至关重要,对某一具体配方,可通过实验杰确定最佳浸清时间,即当表面完全呈均匀灰色时,进行化学镀镍可得到最佳镀层质量。
铝表面前处理及化学沉积镍初期行为

铝 及 其合 金 密度 小 、比强 度 高,常 被 用 于 制 造 管 道 、汽 车化 油器 等 .但其 硬 度低 、耐 磨 和 耐腐蚀 性
Received:October 8,2011:Revised:November16,2011;PublishedonW eb:December1,2011.
(OCP)as a function of time(EocP—f).Scanning electron microscopy(SEM)was used to observe the surface
morphology of the pretreated specim ens.During the initial stages of the electroless nickel deposition,all pretreated and un.pretreated aluminum substrates experienced removaI of the oxide f¨m,activation,mixed control and electroless nickeI deposition.After nickelimmersion and electroless nickel pre-plating.fine nickeI particles were aRached to the surface of the aluminum .Our experimentaI results.including EocP-t and SEM .indicate that electroless nickel plating in a weak acidic bath was successfully accom plished on the aIum inum pretreated with a double treatment of electroless nickeI pre—plating in an alkaline nickeI solution containing a com plexing agent and a reductant.The nickeI coating obtained adhered to the aluminum substrate,had a granular appearance and an amorphous structure.
铝沉镍工艺

铝件喷砂沉镍工艺
一、沉镍前喷砂工艺注意事项
1、工件喷砂前用铝合金专用除油粉或除油剂+超声波清洗(50° ~60°)+清水清洗工件
上的油渍(清洗完一定要吹干孔内及表面水渍)。
2、工件喷砂时尽量把牙孔和盲孔堵住不要喷砂。
3、喷砂的砂粒使用次数不得超出1~2 次,建议使用一次保证沉镍后颜色同一。
4、工件喷砂完要用气枪把表面没喷上的沙粒吹干净。
5、工件喷砂完要用宣纸或泡沫棉或珍珠棉、气泡袋单个零件分开包装防止零件刮花或
碰伤(因为喷砂和沉镍不在同一工厂)。
二、沉镍工艺注意事项
1、沉镍池时间10~15 分钟。
2、沉镍完必须氮氧化防止变色。
3、保证沉镍完与色板一致电镀药水只能用药水的前1~3 个周期(电镀池药水的1~3 周
期,药水使用周期大概 6 个周期左右)。
4、沉镍镀层膜厚3μ m~5μ m 单边。
5、沉镍完要用泡沫棉或珍珠棉、气泡袋、宣纸单个零件分开包装防止零件刮花或碰伤。
三、喷砂、沉镍前后尺寸变化:
四、颜色对比
1~3 个周期药水沉镍4~6 个周期药水沉镍。
铝及铝合金直接化学镀镍前处理工艺研究

铝及铝合金直接化学镀镍前处理工艺研究在铝及铝合金表面形成一层均匀的氧化铝膜是非常重要的。
氧化铝膜可以提供一个良好的基底,有助于后续的化学镀镍工艺。
常用的方法有化学法、电化学法和热氧化法。
化学法通常是将铝表面浸泡在含有氧化剂的酸性溶液中,通过氧化反应形成氧化铝膜。
电化学法是利用电解池将铝表面与阳极连接,通过电流的作用形成氧化铝膜。
热氧化法是将铝加热至一定温度,在空气中进行氧化反应。
这些方法各有优缺点,可以根据具体情况选择适合的方法。
为了提高铝表面的粗糙度,常常需要进行机械处理,如研磨、抛光等。
机械处理可以去除表面的氧化物和污染物,使铝表面更加光滑,有利于氧化铝膜的形成。
为了增加铝表面的附着性,还需要进行一定的活化处理。
活化处理可以提高铝表面的亲水性,使其更容易与镀液中的镍离子发生反应。
常用的活化方法有酸洗、碱洗和活化剂处理等。
酸洗是将铝表面浸泡在含有酸性溶液中,通过酸的腐蚀作用去除表面的氧化物和污染物。
碱洗是将铝表面浸泡在含有碱性溶液中,通过碱的腐蚀作用去除表面的氧化物和污染物。
活化剂处理是将铝表面浸泡在含有活化剂的溶液中,通过活化剂的作用改善表面的性质。
为了进一步提高镀层的质量和均匀性,可以进行一些附加的处理,如表面清洁、去油脂和除尘等。
表面清洁可以去除铝表面的杂质和污染物,提高镀层的附着力。
去油脂可以去除表面的油脂和有机物,减少镀层的缺陷。
除尘可以去除表面的尘埃和颗粒,保证镀层的均匀性。
铝及铝合金直接化学镀镍前处理工艺是一个复杂的过程,需要进行多个步骤的处理。
通过合理选择和组合这些处理方法,可以有效地提高铝及铝合金的表面质量,为后续的化学镀镍过程提供良好的基础。
这对于提高铝及铝合金的耐腐蚀性、装饰性和机械性能具有重要的意义。
铝合金的前处理对Ni-Co-P化学镀层沉积特性和耐腐蚀性能的影响

铝合金的前处理对Ni-Co-P化学镀层沉积特性和耐腐蚀性能的影响胡永俊;熊玲;蒙继龙;李风;成晓玲【期刊名称】《腐蚀科学与防护技术》【年(卷),期】2009(21)2【摘要】通过扫描电镜(SEM)、能谱仪(EDS)和电化学站等技术研究了铝合金化学镀Ni-Co-P的"浸锌-闪镀法"和"预植法"两种前处理工艺对镀层的成分、表面形貌和耐腐蚀性能的影响.结果表明,铝合金化学镀Ni-Co-P前处理工艺决定Ni-Co-P 镀层的形貌和耐腐蚀性能,对镀层的成分影响不明显;铝合金经"浸锌-闪镀法"前处理工艺处理后化学镀Ni-Co-P所得镀层的镀层耐腐蚀性能下降,并用原子氢-电化学联合理论解释了不同前处理对镀层形貌和耐腐蚀性能影响的原因.【总页数】3页(P194-196)【关键词】铝合金;化学镀;Ni—Co—P;前处理【作者】胡永俊;熊玲;蒙继龙;李风;成晓玲【作者单位】广东工业大学材料与能源学院;华南理工大学研究生院;华南理工大学材料与能源学院;广东工业大学轻工与化工学院【正文语种】中文【中图分类】TG174.44【相关文献】1.铝合金上化学镀Ni-Co-P合金工艺及镀层性能的初步研究 [J], 胡佳;方亮;唐安琼;李赟2.铝合金表面催化活性对化学镀镍-铜-磷合金镀层化学组成及耐腐蚀性能的影响[J], 胡永俊;成晓玲;胡光辉;蒙继龙;熊玲;张海燕3.新的铝合金表面化学镀镍磷合金前处理工艺及镀层性能的研究续完 [J], 张刚;邓真红4.热处理对化学沉积Ni-P、Ni-Co-P合金组织及耐蚀性能的影响 [J], 顾正彬;李延祥;李恒杰5.铝合金表面化学镀Ni-Co-P/SiC复合镀层的组织与性能研究 [J], 钟佩文;方亮;胡佳;杨有利因版权原因,仅展示原文概要,查看原文内容请购买。
铝材化学浸镍工艺操作流程
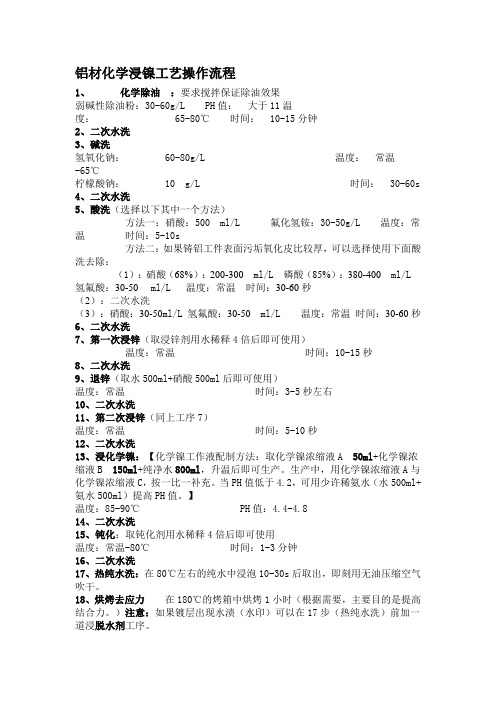
铝材化学浸镍工艺操作流程1、化学除油:要求搅拌保证除油效果弱碱性除油粉:30-60g/L PH值:大于11温度:65-80℃时间:10-15分钟2、二次水洗3、碱洗氢氧化钠:60-80g/L 温度:常温-65℃柠檬酸钠:10 g/L 时间:30-60s4、二次水洗5、酸洗(选择以下其中一个方法)方法一:硝酸:500 ml/L 氟化氢铵:30-50g/L 温度:常温时间:5-10s方法二:如果铸铝工件表面污垢氧化皮比较厚,可以选择使用下面酸洗去除:(1):硝酸(68%):200-300ml/L 磷酸(85%):380-400ml/L 氢氟酸:30-50 ml/L 温度:常温时间:30-60秒(2):二次水洗(3):硝酸:30-50ml/L氢氟酸:30-50ml/L 温度:常温时间:30-60秒6、二次水洗7、第一次浸锌(取浸锌剂用水稀释4倍后即可使用)温度:常温时间:10-15秒8、二次水洗9、退锌(取水500ml+硝酸500ml后即可使用)温度:常温时间:3-5秒左右10、二次水洗11、第二次浸锌(同上工序7)温度:常温时间:5-10秒12、二次水洗13、浸化学镍:【化学镍工作液配制方法:取化学镍浓缩液A 50ml+化学镍浓缩液B 150ml+纯净水800ml,升温后即可生产。
生产中,用化学镍浓缩液A与化学镍浓缩液C,按一比一补充。
当PH值低于4.2,可用少许稀氨水(水500ml+氨水500ml)提高PH值。
】温度:85-90℃PH值:4.4-4.814、二次水洗15、钝化:取钝化剂用水稀释4倍后即可使用温度:常温-80℃时间:1-3分钟16、二次水洗17、热纯水洗:在80℃左右的纯水中浸泡10-30s后取出,即刻用无油压缩空气吹干。
18、烘烤去应力在180℃的烤箱中烘烤1小时(根据需要,主要目的是提高结合力。
)注意:如果镀层出现水渍(水印)可以在17步(热纯水洗)前加一道浸脱水剂工序。
- 1、下载文档前请自行甄别文档内容的完整性,平台不提供额外的编辑、内容补充、找答案等附加服务。
- 2、"仅部分预览"的文档,不可在线预览部分如存在完整性等问题,可反馈申请退款(可完整预览的文档不适用该条件!)。
- 3、如文档侵犯您的权益,请联系客服反馈,我们会尽快为您处理(人工客服工作时间:9:00-18:30)。
铝表面前处理及化学沉积镍初期行为杨丽坤杨防祖*田中群周绍民(厦门大学化学化工学院,固体表面物理化学国家重点实验室,福建厦门361005)摘要:利用开路电位-时间(E OCP -t )曲线,研究铝表面经浸镍和化学预镀镍前处理后,化学沉积镍的初期行为;通过扫描电子显微镜(SEM)观察铝表面经前处理后的表面形貌.结果表明:未经及经前处理的铝表面,化学沉积镍的初期行为都经历去氧化膜、活化、混合控制以及化学沉积过程.经过浸镍和化学预镀镍前处理后的铝表面附着细小的镍颗粒.依据E OCP -t 和SEM 的最佳实验结果,在含有络合剂和还原剂的碱性预镀镍溶液中,经二次化学预镀镍前处理,成功实现铝基底弱酸性化学镀镍.所获得的化学镀镍层与铝基底结合牢固,呈团颗粒状形貌和非晶态结构.关键词:化学镀镍;铝;浸镍;化学预镀镍;开路电位中图分类号:O646Initial Behavior of the Electroless Nickel Deposition on PretreatedAluminumYANG Li-KunYANG Fang-Zu *TIAN Zhong-QunZHOU Shao-Min(State Key Laboratory of Physical Chemistry of Solid Surfaces,College of Chemistry and Chemical Engineering,Xiamen University,Xiamen 361005,Fujian Province,P .R.China )Abstract:The initial behavior of electroless nickel deposition on aluminum pretreated by nickel immersion and electroless nickel pre-plating processes was studied measuring the open circuit potential (OCP)as a function of time (E OCP -t ).Scanning electron microscopy (SEM)was used to observe the surface morphology of the pretreated specimens.During the initial stages of the electroless nickel deposition,all pretreated and un-pretreated aluminum substrates experienced removal of the oxide film,activation,mixed control and electroless nickel deposition.After nickel immersion and electroless nickel pre-plating,fine nickel particles were attached to the surface of the aluminum.Our experimental results,including E OCP -t and SEM,indicate that electroless nickel plating in a weak acidic bath was successfully accomplished on the aluminum pretreated with a double treatment of electroless nickel pre-plating in an alkaline nickel solution containing a complexing agent and a reductant.The nickel coating obtained adhered to the aluminum substrate,had a granular appearance and an amorphous structure.Key Words:Electroless nickel plating;Aluminum;Nickel immersion;Electroless nickel pre-plating;Open circuit potential[Article]doi:10.3866/PKU.WHXB201112011物理化学学报(Wuli Huaxue Xuebao )Acta Phys.-Chim.Sin .2012,28(2),414-420FebruaryReceived:October 8,2011;Revised:November 16,2011;Published on Web:December 1,2011.∗Corresponding author.Email:fzyang@;Tel:+86-592-2185957;Fax:+86-592-2181436.The project was supported by the National Natural Science Foundation of China (20873114,20833005,21021002),National Key Basic Research Program of China (973)(2009CB930703),and Science and Technology Project of Fujian Province,China (2009H4020).国家自然科学基金(20873114,20833005,21021002),国家重点基础研究发展规划项目(973)(2009CB930703)和福建省科技计划项目(2009H4020)资助ⒸEditorial office of Acta Physico-Chimica Sinica1引言铝及其合金密度小、比强度高,常被用于制造医疗器械、冷冻装置、石油精炼装置、石油和天然气管道、汽车化油器等.但其硬度低、耐磨和耐腐蚀性414杨丽坤等:铝表面前处理及化学沉积镍初期行为No.2差,已越来越不能满足其应用要求.铝及其合金化学镀镍1-3后可显著提高表面硬度、耐磨和耐腐蚀性,并赋予表面钎焊性、可抛光性等功能特性.4-6相对于铝合金,铝的化学性质更加活泼.铝为两性金属,标准电极电位为-1.66V,在酸、碱溶液中都不稳定.在应用最为广泛的弱酸性化学镀镍中,铝基体直接浸入化学镀镍液时,易发生铝与镍络合离子的置换反应和析氢反应,在其表面形成疏松粗糙的接触性镀层或表面结构缺陷,从而严重影响镀层与基体间的结合强度.7因此,铝及其合金进行弱酸性化学镀镍前,通常进行复杂的前处理.目前常用的是二次浸锌法.8通过浸锌处理,可以在一定程度上避免产生对镀层与基体间结合力有严重影响的接触性镀层.但这种工艺的缺点是,在潮湿的腐蚀环境下,锌层相对镍镀层是阳极,将受到横向腐蚀,最终导致化学镀镍层剥落.此外,过渡锌层熔点较低,限制了镀件的应用范围.浸锌处理后的铝(合金)镀件置于酸性化学镀镍镀液中时,锌层可能溶解,从而对化学镀镍液造成污染,导致酸性化学镀镍液不稳定和容易分解,并造成镀层结合力差.黄晓梅等9研究出一种无氰浸锌工艺,所得的锌合金层颗粒细小、均匀、结合力好;尹国光10尝试采用预浸镍前处理工艺代替传统浸锌工艺,通过观察活化膜和预镀镍层的表面形貌,分析镀层结合力、孔隙率和耐蚀性能,得出最佳pH值在9-10之间,预镀镍层最佳厚度约为0.6μm 的实验条件;李新跃等11对化学镀镍工艺进行改进,尝试采用直接化学镀镍方法以得到性能良好的镍镀层;Takács等12以次磷酸钠和乳酸溶液对铝合金进行前处理,在前处理过程中形成一种次磷酸盐吸附层后再进行化学镀镍.铝表面化学镍沉积初期行为复杂.通过测定化学镀过程的开路电位与时间(E OCP-t)曲线,可以鉴别金属对化学镀反应的催化活性、实验条件对化学镀诱发反应的影响,尚可解释化学镀初期过程中电极/溶液界面状态,13-17从而,揭示化学沉积初期的实质. Niwa等4通过测定经前处理后的单晶硅片碱性化学镀镍的E OCP-t曲线,研究前处理对硅片上化学镀镍的影响.Elsentriecy等18-20通过测定AZ91D镁合金表面锡酸盐转化膜、钼酸盐转化膜形成过程的E OCP-t 曲线,以确定最适宜的处理时间.谷新等21测定了铜基和陶瓷基化学镀铜过程混合电位与时间曲线,研究化学镀诱发过程.王桂香等22报道了塑料化学镀镍过程的E OCP-t曲线,结果显示,初期阶段电位负移,最终电位值基本不变,体系达到稳定的时间约为100s.然而,根据这些实验结果尚无法全面深入了解活泼金属表面化学镍沉积初期的实质过程.本实验以铝为研究对象,采用预浸镍和化学预镀镍技术,结合无铅镉弱酸性化学镀镍工艺,23通过E OCP-t曲线和扫描电子显微镜(SEM),研究预处理后金属铝表面镍的生长状况和化学镀诱发过程.利用SEM、X射线衍射(XRD)等研究方法,研究铝基底经二次化学预镀镍处理后,镀层的外观形貌、结合力和结构.2实验条件2.1铝前处理流程电化学实验用铝电极的前处理过程:铝片(2 cm2)→打磨抛光→除油(碳酸钠40g·L-1,磷酸钠35 g·L-1,洗涤剂5mL·L-1,温度70-80°C,时间5 min)→表面活化处理(氨水250mL·L-1,柠檬酸三钠6g·L-1,室温约20°C,时间1min)→浸镍或化学预镀镍.铝片(10cm2)经相同前处理后,进行二次化学预镀镍处理(浸68%浓硝酸5s→表面活化处理1min→化学预镀镍3min),随后进行弱酸性化学镀镍40 min,获得的样品进行外观形貌、结合力和结构表征.2.2化学镀镍液、前处理液的组成及条件2.2.1化学镀镍液组成及条件弱酸性化学镀镍液组成及条件与前文23的相同,主要试剂为硫酸镍27g·L-1,次磷酸钠30g·L-1,醋酸钠20g·L-1,乳酸31mL·L-1,丙酸3.7mL·L-1,柠檬酸钠1.2g·L-1,稳定剂1.5mL·L-1(Sn2+、Se4+、Mo6+、Sb3+和Bi3+的混合物溶液).化学镀镍在(91±1)°C条件下进行,用NH3·H2O调节镀液pH为4.8-5.2.2.2.2前处理液浸镍前处理液A:柠檬酸钠6g·L-1,醋酸镍2g·L-1,乳酸10mL·L-1,三乙醇胺10mL·L-1,用NH3·H2O调节pH为10-11,温度20°C.化学预镀镍前处理液B:硫酸镍13g·L-1,次磷酸钠30g·L-1,柠檬酸三钠40g·L-1,氯化铵30g·L-1,用NH3·H2O调节pH为9.0-9.5,温度40°C.所有溶液均采用化学纯试剂(国药集团化学试剂有限公司生产)与去离子水配制.2.3电化学实验采用两电极体系(参比电极与辅助电极串联)测量化学镀镍过程开路电位与时间(E OCP-t)曲线;经前415Acta Phys.-Chim.Sin.2012Vol.28处理的铝片为工作电极,饱和甘汞电极(SCE)为参比电极(文中电位值均相对于此电极).电化学实验时,接通仪器使其处于工作状态,同时快速将研究电极浸入化学镀镍液((91±1)°C)中,记录E OCP -t 关系曲线.所用仪器为电化学综合测试仪(荷兰Auto-lab PGSTAT30).实验中,每隔0.1s 记录一个数据.实验过程中所用水均为二次去离子水.2.4镀层表征镀层结合力:铝片经二次化学预镀镍3min 及化学镀镍40min 后,在200°C 下热处理1h,取出,快速置于冷水中,观察镀层是否脱落、鼓泡或起皮.镀层形貌:选用扫描电子显微镜(Hitachi S-4800,日本日立公司)观察镀层形貌,10kV ,真空度优于10-3Pa.采用随机附带的能量色散谱(EDS)测定镀层组成.镀层结构:用多晶转靶X 射线衍射仪(X ʹpert PRO,荷兰帕纳科公司)测定.采用Cu 靶K α射线,λ为0.15406nm,管电流30mA,管电压40kV ,以石墨单色器滤波,扫描速率为6(°)·min -1.3结果与讨论3.1铝及其前处理后化学沉积镍初期行为图1为铝基底(曲线a)、前处理液A 浸镍处理1min(曲线b)和前处理液B 化学预镀镍3min(曲线c)后,化学镀镍过程的E OCP -t 曲线.由图1曲线a 可知,电位首先出现一个平台区,接着迅速负移,达到一个极小值;随后电位正移,最终达到另一个平台区,此时电位值基本不随时间变化,体系处于稳态.铝基底非常活泼,易被空气中的氧气氧化生成氧化膜.因此,化学沉积最初出现的电位平台区可理解为,电极浸入弱酸性的化学镀镍液后,氧化膜化学溶解破坏.此时,电位值主要表现为附着氧化膜的铝电极相对于SCE 的电位;电位平台的长短表现为氧化膜化学溶解破坏的时间,也就是氧化膜的厚度.显然,铝表面虽然进行了除油和活化前处理,但氧化膜仍然存在;化学沉积镍初期必然经历去氧化膜的过程;通过电位平台的长短可以了解氧化膜的厚度.电位平台达到m 点后,电位开始显著下降并达到一极小值(n 点).这说明,电位平台达到m 点时,氧化膜被破坏而裸露出铝基底.此时,电极电位主要表现为金属铝相对于SCE 的电位.由于铝的标准电极电位为-1.66V ,所以E OCP -t 曲线中的电位值迅速下降.电极电位的迅速下降,导致铝和镍络合离子发生置换反应(2Al+3Ni 2+=3Ni+2Al 3+)和可能的析氢反应(2Al+6H +=2Al 3++3H 2↑).结果是,铝表面上附着的、具有催化活性的微小镍置换产物,触发化学镀镍反应发生.因此,从m 点至n 点的电位变化,表现为铝表面化学镀镍的活化过程.m 点至n 点的电位变化时间越短,说明活化速率越快;n 点的电位越负,说明裸露的铝表面面积越大.由图1曲线a 的m 点至n 点的电位变化时间可知,铝上化学镀镍的活化过程迅速.超过n 点时,电位出现一相对缓慢的正移.这表明,化学镀镍处于混合控制期,表现为裸露铝、铝表面和镍络合离子发生置换反应和可能的析氢反应、以及铝表面化学镀镍反应复杂的混合控制.随着铝表面逐渐被化学镀镍层所覆盖,混合电位中金属铝相对于SCE 的电极电位所占的比例降低,E OCP -t 曲线中的电位值逐渐正移.直至图1曲线a 中的p 点时,基底铝的影响作用恒定或消失,电位趋于稳定.n 点和p 点电位变化幅度越小,时间越短,说明基底铝对化学镀镍过程的影响作用越弱.电位平台超过p 点时,E OCP -t 曲线中的电位值归因于化学沉积镍的混合电位.显然,p 点对应的时间,反映了铝上实现化学沉积镍稳定开始的时间.时间越短,基底铝的影响越小、化学镀镍越容易进行.实验结果表明,化学镀镍时间延长至10min 时,E OCP -t 曲线中的电位值与p 点的基本一致.谷新21和王桂香22等针对E OCP -t 曲线的实验综合解释为,化学镍沉积初期,双电层尚未形成,这一段时间可以称为电极的活化时间.随后反应开始进行,Ni 2+和大量负电性的配位离子吸附到电极表面使电位负移,次磷酸根离图1铝基底(a)、溶液A 浸镍处理1min (b)和溶液B 化学预镀镍处理3min (c)后化学沉积镍过程的E OCP -t 曲线Fig.1E OCP -t curves for the electroless nickel deposition on Al base (a),pretreated in the nickel immersion solution A for 1min (b),and pretreated in the electroless nickelpre-plating solution B for 3min(c)杨丽坤等:铝表面前处理及化学沉积镍初期行为No.2子开始被氧化,Ni 2+被还原,同时Ni 2+与铝基底还会发生置换反应,本体溶液中的Ni 2+来不及补充,电位继续负移,最后达到极小值.随着铝基底逐渐被新生镍覆盖,电位逐渐变正,最终电位到达一个平台区.显然,本文工作可以进一步清晰理解化学沉积镍的初期行为.Takács 等12测定了铝合金基底浸镍后化学镀镍的E OCP -t 曲线,结果显示,曲线一开始就出现电位正移(类似于图1曲线a 电位从极小值n 点开始).显然,这一实验结果也无法充分说明化学镍沉积的初期行为.铝经过溶液A 浸镍前处理1min 和溶液B 化学预镀镍前处理3min 后,化学镍沉积初期行为也经历了去氧化膜、活化、混合控制和化学沉积过程.比较图1曲线a 、b 和c 可知,m 点之前的电位平台电位值及去氧化膜的时间不同,说明前处理后的铝表面物质组成、状态及膜厚度已发生变化.虽然经过溶液A 浸镍前处理1min 后(曲线b),铝表面去氧化膜时间更短,但其n 点电位与曲线a 的基本相同,且明显存在混合控制过程.而经过溶液B 化学预镀镍前处理3min 后(曲线c),n 点电位最正,且几乎没有经历混合控制过程.显然,不同的前处理工艺,直接影响着化学镍沉积的初期行为.3.2前处理时间的影响铝在溶液A 浸镍处理过程中,将发生铝与镍络合离子的置换反应、析氢反应;在溶液B 化学预镀镍处理过程中,还将发生次磷酸根氧化、镍络合离子还原的化学镍还原反应.因此,反应过程中,一方面,置换及化学还原的镍原子附着于铝表面并逐渐增多和团聚;另一方面,析氢反应则导致镍颗粒脱落.处理时间显然影响着化学镀镍层的质量.铝基底分别经溶液A 浸镍处理1、2、3和5min 后的E OCP -t 曲线示于图2,表面形貌SEM 图示于图3.对比图2中各曲线可知,经溶液A 不同时间浸镍处理后,达到化学镍沉积过程控制的p 点时间基本相似;虽然浸镍处理1min 后的n 点电位较负,但其去氧化膜时间最短.通过观察不同浸镍时间处理后的SEM 图,可以更好地了解预浸时间的影响.图3结果显示,浸镍处理1min 后,铝表面附着大量的镍细小颗粒,颗粒未能全部覆盖于铝表面.随着浸镍时间增加,镍颗粒图2铝基底经溶液A 浸镍不同处理时间后的化学镀镍的E OCP -t 曲线Fig.2E OCP -t curves for the electroless nickel deposition on Al base pretreated in the nickel immersion solution Afor different timet /min:(a)1,(b)2,(c)3,(d)53铝基底经溶液A 不同浸镍时间处理后的SEM 图Fig.3SEM images of Al base pretreated in solution A for different timet /min:(a)1,(b)2,(c)3,(d)5417Acta Phys.-Chim.Sin.2012Vol.28逐渐团聚、絮状增长并脱离铝表面.因此,适宜浸镍时间为1min.铝基底分别经溶液B 化学预镀镍处理1、2、3、4min 后的E OCP -t 曲线示于图4,表面形貌的SEM 图示于图5.由图4可知,经溶液B 化学预镀镍不同时间处理后,化学镍沉积的初期行为的变化趋势基本相同.不同的是,化学预镀镍处理2和3min 后,去氧化膜时间相对较短.由图5可知,化学预镀镍1min 后,铝基底表面上还原出的镍晶粒细小但量较少;化学预镀镍2min 后,铝表面附着大量的、粒径相对较大的镍颗粒.化学预镀镍超过3min 时,镍的覆盖率又逐渐减小.根据图1、图2和图4化学镍沉积初期的E OCP -t 曲线分析,结合图3和图5的形貌观察可见,铝基底较合适的前处理方式为2-3min 化学预镀镍.3.3二次化学预镀镍的影响图5结果显示,一次化学预镀镍处理后,铝表面附着的镍颗粒较为粗大且分布较不均匀,镍颗粒未能全部覆盖于铝表面.因此,有必要进一步考察二图4铝基底经溶液B 化学预镀镍不同时间处理后的化学镀镍E OCP -t 曲线Fig.4E OCP -t curves for the electroless nickel deposition on Al base pretreated in the electroless nickel pre-platingsolution B for different timet /min :(a)1,(b)2,(c)3,(d)45铝基底经溶液B 化学预镀镍不同时间处理后的SEM 图Fig.5SEM images of Al base pre-plated in solution B for different timet /min:(a)1,(b)2,(c)3,(d)4图6铝基底进行一次(a)和二次(b)化学预镀镍后的SEM 图Fig.6SEM images of Al base pretreated by the single (a)and double (b)treatments of electroless nickelpre-plating418杨丽坤等:铝表面前处理及化学沉积镍初期行为No.2次化学预镀镍的效果.铝片经过一次化学预镀镍、浸硝酸和表面活化处理后,附着于铝表面上的较为粗大的镍颗粒溶解,同时进一步活化铝表面.经过二次化学预镀镍处理,附着于铝表面的镍颗粒有望更加细小、分布均匀和全面覆盖.铝表面一次和二次化学预镀镍处理3min 后的SEM 图见图6.图6表明,经过二次化学预镀镍处理,附着于铝表面的镍颗粒更加细小、分布均匀和覆盖度更高.根据图7铝基底(曲线a)、一次(曲线b)和二次(曲线c)化学预镀镍处理后的E OCP -t 曲线结果可知,经二次化学预镀镍处理后,去氧化膜时间更短,说明膜厚更小;去氧化膜平台电位更正,说明铝表面的电化学活性更低,不易于腐蚀破坏.3.4化学镀镍层形貌与结构铝经过系列前处理、二次化学预镀镍、弱酸性化学镀镍后的SEM 和XRD 图见图8.由图可见,经过二次化学预镀镍后,可成功实现弱酸性化学镀镍.化学镀镍后,铝表面已完全被镀层覆盖;镀层呈胞颗粒状,结构致密,颗粒间存在晶界,与前文23铁件上化学镀镍的结果基本一致.Elsentriecy 、19沟引宁、24和贺忠臣25等得到的胞状物大小分别约为10、12和5μm.本文中,胞状物的大小约为3μm.与前文23和文献26结果相似.XRD 谱仅在2θ为45°附近出现一个漫散射峰,说明镀层为非晶态结构.经能量色散谱测定,镀层中P 的质量分数为9.0%.此外,热处理后(200°C,1h),镀层外观基本无变化,并未发现起皮、鼓泡现象,说明化学镀镍层与铝基底结合力良好.4结论开路电位-时间关系曲线结合形貌观察,可以揭示镍化学沉积初期的反应历程和反应实质,并对活泼金属(合金)上实现化学镀镍有理论指导意义.研究表明,化学沉积镍的初期行为经历了去氧化膜、活化、混合控制以及化学沉积过程.铝基底化学浸镍和化学预镀镍前处理,较适宜的时间分别为1min 和2-3min.在开路电位-时间关系曲线的理论指导和形貌观察的基础上,采用二次预镀镍方法,铝表面一次和二次化学预镀镍各处理3min 后,成功实现铝基底弱酸性化学镀镍.所获得的化学镀镍层与铝基底结合牢固,呈团颗粒胞状形貌和非晶态结构.本文工作可为铝上化学镀镍提供理论和技术借鉴.References(1)Chen,C.Y .;Lin,K.Y .;Tsai,W.T.;Chang,J.K.;Tseng,C.M.Int.J.Hydrog.Energy 2010,35(11),5490.(2)Kar,K.K.;Sathiyamoorthy,D.J.Mater.Process.Technol.2009,209(6),3022.(3)Lee,C.K.Material Chemistry and Physics 2009,114(1),125.(4)Niwa,D.;Takano,N.;Yamada,T.;Osaka,T.Electrochimi.Acta2003,48(9),1295.(5)Gu,C.D.;Lian,J.S.;Li,G.Y .;Niu,L.Y .;Jiao,Z.H.Surf.Coat.图7铝基底(a)、一次(b)和二次(c)化学预镀镍溶液B 处理3min 后的E OCP -t 曲线Fig.7E OCP -t curves for the electroless nickel deposition on Al base (a),single (b),and double (c)treatments in theelectroless nickel pre-plating solution B for 3min8铝表面化学镀镍层的SEM 图(a)与XRD 谱图(b)Fig.8SEM image (a)and XRD pattern (b)of the electroless nickel deposition coating on Alsurface419Acta Phys.-Chim.Sin.2012Vol.28Technol.2005,197(1),61.(6)Jia,F.;Wang,Z.C.Acta Phys.-Chim.Sin.2011,27(3),633.[贾飞,王周成.物理化学学报,2011,27(3),633.](7)Gao,Y.;Zheng,Z.J.;Cao,D.H.Electroplating and PollutionControl2005,25(2),21.[高岩,郑志军,曹达华.电镀与环保,2005,25(2),21.](8)Zhao,M.J.;Cai,C.;Wang,L.;Zhang,Z.;Zhang,J.Q.Surf.Coat.Technol.2010,205(7),2160.(9)Huang,X.M.;Jiang,L.M.;Li,N.;Li,D.Y.Corrosion Scienceand Protection Technology2006,18(2),107.[黄晓梅,蒋丽敏,李宁,黎德育.腐蚀科学与防护技术,2006,18(2),107.] (10)Yin,G.G.Surface Technology2004,33(2),43.[尹国光.表面技术,2004,33(2),43.](11)Li,X.Y.;Zeng,X.G.;Zheng,X.W.;Liang,W.Plating&Finishing2011,33(8),38.[李新跃,曾宪光,郑兴文,梁伟.电镀与精饰,2011,33(8),38.](12)Takács,D.;Sziráki,L.;Török,T.I.;Sólyom,J.;Gácsi,Z.;Gál-Solymos,K.Surf.Coat.Technol.2007,201(8),4526. (13)Kou,S.C.;Hung,A.Plating&Surface Finishing2003,90(3),44.(14)Kou,S.C.;Hung,A.Plating&Surface Finishing2002,89(2),48.(15)Tong,H.;Wang,C.M.Acta Chim.Sin.2002,60(11),1923.[佟浩,王春明.化学学报,2002,60(11),1923.](16)Ma,M.R.;Deng,S.T.;Wang,G.X.;Li,N.Electroplating&Pollution Control2006,26(4),26.[马梅容,邓舒太,王桂香,李宁.电镀与环保,2006,26(4),26.](17)Ger,M.D.;Sung,Y.;Ou,J.L.Materials Chemistry and Physics2005,89(2-3),383.(18)Elsentriecy,H.H.;Azumi,K.;Konno,H.Electrochimi Acta2007,53(2),1006.(19)Elsentriecy,H.H.;Azumi,K.J.Electrochem.Soc.2009,156(2),70.(20)Elsentriecy,H.H.;Azumi,K.;Konno,H.Surf.Coat.Technol.2007,202(3),532.(21)Gu,X.;Hu,G.H.;Wang,Z.C.;Lin,C.J.Acta Phys.-Chim.Sin.2004,20(2),113.[谷新,胡光辉,王周成,林昌健.物理化学学报,2004,20(2),113.](22)Wang,G.X.;Li,N.;Tu,Z.M.Materials Protection2005,38(5),1.[王桂香,李宁,屠振密.材料保护,2005,38(5),1.] (23)Yang,F.Z.;Chen,M.H.;Huang,X.J.;Tian,Z.Q.;Zhou,S.M.Electrochemistry2010,16(4),1.[杨防祖,陈明辉,黄夏菁,田中群,周绍民.电化学,2010,16(4),1.](24)Gou,Y.N.;Huang,W.J.;Chen,W.B.;Tan,G.F.;Xue,Y.Corrosion and Protection2010,31(3),225.[沟引宁,黄伟九,陈文彬,谈国峰,薛燕.腐蚀与防护,2010,31(3),225.] (25)He,Z.C.;Qin,T.N.;Ding,Y.;Ma,L.Q.Light AlloyFabrication Technology2009,37(3),44.[贺忠臣,秦铁男,丁毅,马立群.轻合金加工技术,2009,37(3),44.](26)Gu,C.D.;Lian,J.S.;Li,G.Y.;Niu,L.Y.;Jiao,Z.H.J.Alloy.Compd.2005,391(1-2),104.420。