扩散性铝化物涂层及制备工艺
扩散性铝化物涂层附制备工艺

扩散性铝化物涂层及制备工艺高温铝化物扩散涂层是在20世纪50年代发展起来的,到目前仍被广泛应用,并占整个高温防护涂层的90%。
制备铝化物涂层的扩散渗铝工艺成熟,方法多样化。
在镍基合金上应用最广的渗铝方法有:固体粉末渗铝,料浆法渗铝。
下面简要介绍固体粉末渗铝、料浆渗铝、气相渗铝三种工艺的原理。
1固体粉末渗铝[11]在耐热钢容器中,将样品包装于扩散剂之中,渗剂由金属铝粉末或富Al的FeAl合金粉末,活化物质(如卤族化合物)及填料(氧化铝)混合组成,用氢或氢气作保护气体,按规定的时间进行热扩散处理。
以钢的渗铝为例来说明渗铝的原理。
渗铝过程中发生如下系列反应:2NH4Cl=2HCl+N2+3H26HCl+2Al=2AlCl3+3H2Fe+AlCl3=FeC13+[Al]即在高温下,NH4Cl分解释放出HCl气体、HCl和铝粉或FeAl粉中的铝反应形成气态AlCl3。
AlCl3扩散向渗件表面,并和基体元素铁反应,铝原子被置换出来.反应式在通常情况下几乎不会发生,但在金属表面有催渗剂的条件是有可能发生的。
一般常见的渗铝温度为850℃~1050℃。
温度太低,渗铝速度会急剧下降;温度太高,则渗铝件的晶粒急剧长大而使材料的机械性能变差。
渗铝层的厚度可通过调整渗铝时间和温度来控制。
但是,为获得较厚的渗层,延长渗铝时间远没有提高温度那样效果显著,因为在保温一定时间后,合金表面的铝己达到饱和状态,此后渗铝层的厚度将完全取决于铝的扩散速度,即使再延长时间,渗铝层厚度也不会有很大的增加[12]。
固体粉末渗铝的优点是:设备简单,操作方便,特别适用于机械的零部件;其缺点是:渗剂容易被氧化,工件尺寸受限制,对工件表面粗糙度有一定影响。
2料桨法渗铝[13][14]料浆法(slurry process)将渗铝剂和粘结剂配制成料浆,涂在工件表面,烘干后在真空或氢气保护下进行高温扩散处理。
高温扩散处理温度一般在1000℃~1200℃。
用铝活度高的料浆得到向里扩散型涂层,铝活度低时得到向外扩散型1 / 4铝化物涂层。
不同条件下进行渗后扩散的铝硅涂层氧化行为研究

不同条件下进行渗后扩散的铝硅涂层氧化行为研究陈忠;蒙彩思;火克莉;张姚;郝粉利【摘要】目的提高铝硅涂层的抗氧化性能.方法采用料浆法在DZ417G定向凝固镍基高温合金叶片的燃气流道表面制备铝硅防护涂层,通过扫描电子显微镜(SEM)分析不同条件下进行渗后扩散的铝硅涂层表面显微组织形貌和截面显微组织形貌.结果无保护气氛下进行渗后扩散处理的铝硅涂层,在扩散过程中就已经发生了氧化,氧化过程首先形成多孔非致密结构的θ-Al2O3相,随着氧化过程的进行,θ-Al2O3相逐渐转变成致密结构的α-Al2O3相,从而起到真正的抗氧化作用.结论铝硅涂层中的Al元素提前被消耗,对铝硅涂层的使用寿命存在一定影响,因而渗后扩散须保证在真空条件下或有保护气氛条件下进行,使叶片表面渗后的铝浓度达到一定的要求,从而在使用过程中可以生成致密结构的α-Al2O3相,起到抗氧化作用,提高叶片的使用寿命.【期刊名称】《装备环境工程》【年(卷),期】2019(016)001【总页数】5页(P30-34)【关键词】铝硅涂层;氧化;SEM;EDS【作者】陈忠;蒙彩思;火克莉;张姚;郝粉利【作者单位】贵阳航发精密铸造有限公司,贵阳 550014;贵阳航发精密铸造有限公司,贵阳 550014;贵阳航发精密铸造有限公司,贵阳 550014;贵阳航发精密铸造有限公司,贵阳 550014;贵阳航发精密铸造有限公司,贵阳 550014【正文语种】中文【中图分类】TG178随着航空涡轮发动机工作温度的不断提高,对发动机关键零件所用镍基高温合金的高温力学性能也提出了更高的要求,仅靠改进涡轮叶片的制造工艺,往往难以满足安全可靠工作所需的抗高温氧化和热腐蚀能力[1-3]。
防护涂层是保护叶片具有良好抗高温和耐腐蚀性能的有效手段,通过防护涂层的使用,既能保障叶片的强度,又能提高各项性能,是目前航空发动机叶片制备生产中必不可少的工艺过程。
其中,Al-Si涂层作为一种改性的铝化物涂层,因其具有优异的抗高温氧化和热腐蚀性能而广泛应用于航空发动机涡轮叶片的高温防护中[4-5]。
铝化物涂层产品介绍

中国科学院金属研究所表面工程研究部
地址:沈阳市沈河区文化路 72 号
联系方式 hjyu11s@
部件渗铝主要通过以下三种涂层工艺实施:
包埋法 我们最常用的包埋方法是在玻璃密封或 H2 还原/Ar 惰性气氛中进行的,避免了部件的氧化。
渗铝部件被浸入在粉末中,粉末的成分包括: 渗铝源:铝粉(或铝合金) 活化剂(例如卤化物) 惰性填充剂(例如氧化铝;防止粉末烧结)
外包埋 外包埋法与包埋法很相似,唯一不同的是部件悬挂在粉末之上而不与粉末接触。
优点:消除了涂层当中的颗粒,改善了部件表面,不需要进一步的表面处理。
缺点:增加了粉末与部件的距离,因此降低了沉积速率。
气相渗铝 表面工程部自主研发气相渗铝方法,可以沉积燃气轮机叶片内腔,气相渗铝是外包埋法的改进版,不 同之处在于: 1. 每一个部件都有独立的气体发生室。 2. 从粉末中产生的卤化物气体被输送到叶片内腔当中沉积涂层。
渗铝
渗铝是一项高温化学工艺,主要利用铝元素扩散到基体表面形成一层金属铝化物涂层。金属所表面工 程研究部成功研发多种铝化物涂层,可以为客户提供多种铝化物涂层防护方案,满足工程要求。
铝化物涂层的应用和性能
铝化物扩散涂层为中高温工作环境当中的金属材料提供防护,防护内容主要包括: 热腐蚀 金属粉化/尘化 氧化 硫化 碳化
料浆法 料浆法主要用于局部涂覆或局部修复。料浆主要成分为有机粘结剂和水,其中含有少量的渗剂。渗剂 的成分决定涂层成分。不需要涂层的区域需要遮盖,防止这些区域涂覆涂层。
总结
作为集生产和研发一体的涂层供应商,我们可以根据客户的需要研发并提供可以满足不同需要的涂层。 同时,为降低客户的成本,某些已经使用的渗铝部件可以被修复。我们通过严格的质量管理流程来保 证涂层性能。每一批每一件产品在交货前都会被仔细检查,按照美国材料标准协会 ASTM B875-96 铝 化物涂层标准。同时,每一批产品都会有质量证明,并附带样品供客户检测。
钛合金高温抗氧化涂层的研究进展

钛合金高温抗氧化涂层的研究进展3李 威1,肖来荣1,2,温燕宁1,胡加瑞1,蔡圳阳1,殷傲宇1(1 中南大学材料科学与工程学院,长沙410083;2 中南大学有色金属材料科学与工程教育部重点实验室,长沙410083)摘要 高温抗氧化性差是限制钛合金作为高温结构材料在航空航天领域广泛应用的关键问题。
从涂层体系出发,综述了国内外钛合金高温抗氧化涂层的研究进展。
根据涂层的制备方法和性能,对比了各涂层的优缺点,分析了涂层研究中面临的问题,并提出了解决方法,展望了钛合金高温抗氧化涂层的发展方向。
关键词 钛合金 高温抗氧化 涂层 性能中图分类号:TB43 文献标识码:AProgress in R esearch on High T emperature Oxidation R esistantCoatings of Titanium AlloysL I Wei 1,XIAO Lairong 1,2,WEN Yanning 1,HU Jiarui 1,CA I Zhenyang 1,YIN Aoyu 1(1 School of Materials Science and Engineering ,Central South University ,Changsha 410083;2 The Key Laboratory of Non 2Ferrous Metals ,Materials Science and Engineering of Ministry of Education ,Central South University ,Changsha 410083)Abstract The use of titanium alloys as high temperature structural material in aerospace industry is restricted because of its poor oxidation resistance at high temperatures.The present status of research on high temperature oxida 2tion resistant coatings of titanium alloys is reviewed.The advantages and disadvantages of different coatings are com 2pared on the basis of preparation method and properties of the coating ,existing problems are analyzed and possible so 2lutions are suggested ,and the trend development is pointed out.K ey w ords titanium alloys ,high temperature oxidation resistant ,coatings ,properties 3材料科学与工程国家创新实验区项目 李威:男,硕士,主要从事高温防护涂层的研究 肖来荣:通讯作者,男,1968年生,教授 E 2mail :leevii @0 引言钛合金是一种新型结构材料,具有密度小、比强度高、耐高温、耐腐蚀等优点。
自蔓延工艺

在Al2O3-Fe体系燃烧合成离心铸造技术中,添加剂 主要是:SiO2、Cr2O3、Na2B4O7等。SiO2加入使 Al2O3初始结晶温度和最终结晶温度下降,显著提高陶瓷 层致密度。燃烧合成产物铁与Al2O3润湿性不良,加入 Na2B4O7后其润湿性大大改善,促进结合强度,提高压 减强度,增强复合管道耐热冲击和机械冲击的能力。
离心复合原理示意图
要成功地进行离心熔铸,应满足以下几个条件: ①可燃的SHS混合物; ②燃烧产物为高温熔体; ③燃烧温度高于基体的熔点; ④涂层和基体之间可形成冶金结合。
SHS离心铸造工艺的主要技术参数有: ①SHS混合物的燃烧温度 ②产物的熔化量 ③基体的厚度
(5)SHS焊接技术
随着现代工业和科技的发展,对耐热金属、金属间化合物、陶瓷 等材料的同种或异种材料的焊接要求越来越高,然而许多陶瓷在焊接 熔化时发生分解,从而导致焊件变脆,许多金属间化合物在焊接熔化 和重新凝固过程中,长程有序遭破坏,使其高温强度丧失,出现热裂 和脆性;而异类材料用常规方法焊接,会造成严重的不相容问题。 SHS焊接提出了一种有希望的解决办法。 SHS焊接是指利用SHS反应的放热及其产物来焊接受焊材料的 技术。根据被焊接母材来源的不同,可将SHS焊接分为一次焊接和二 次焊接。一次焊接是被焊接的母材在焊接过程中同时原位合成的焊接 工艺,而二次焊接则是焊接现存的母材。
SHS焊接可用于焊接同种和异型的难熔金属、耐热材 料、耐腐蚀氧化物陶瓷或非氧化物陶瓷和金属间化合物。 其装置如下图所示。
SHS焊接陶瓷的原理是利用活性元素在陶瓷的界面处 与陶瓷发生界面反应来改善陶瓷的表面状态,以提高焊料 反应产物与陶瓷的润湿性。例如采用Ti-C-Ni粉末作为焊料 可以实现SiC陶瓷的SHS焊接,金属镍粉的作用是为了降 低反应的激发温度和燃烧温度。 在异类材料的焊接中,目前研究得比较多且有明确 应用前景的领域是陶瓷与金属之间的焊接。
MCrAlY_金属黏结层高温失效行为研究进展

第 3 期第 22-32 页材料工程Vol.52Mar. 2024Journal of Materials EngineeringNo.3pp.22-32第 52 卷2024 年 3 月M CrAlY 金属黏结层高温失效行为研究进展Research progress in high -temperature failure behavior of M CrAlY metal bond -coat刘佳琪1,2,王超会1,2*,林蔚1,2,由园1,2,程伟东1,2,董美伶1,2,王铀3,王宇航1,2,朱忠宇1,2,刘金泉1,2(1 齐齐哈尔大学 材料科学与工程学院,黑龙江 齐齐哈尔 161006;2 黑龙江省聚合物基复合材料重点实验室,黑龙江 齐齐哈尔 161006;3 哈尔滨工业大学 材料科学与工程学院,哈尔滨 150001)LIU Jiaqi 1,2,WANG Chaohui 1,2*,LIN Wei 1,2,YOU Yuan 1,2,CHENG Weidong 1,2,DONG Meiling 1,2,WANG You 3,WANG Yuhang 1,2,ZHU Zhongyu 1,2,LIU Jinquan 1,2(1 College of Materials Science and Engineering ,Qiqihar University ,Qiqihar 161006,Heilongjiang ,China ;2 Heilongjiang Provincial KeyLaboratory of Polymeric Composite Materials ,Qiqihar 161006,Heilongjiang ,China ;3 College of Materials Science andEngineering ,Harbin Institute of Technology ,Harbin 150001,China )摘要:随着航空发动机与燃气轮机涡轮进口温度的不断提高,M CrAlY (M =Ni ,Co 或NiCo )包覆型涂层因具有抗高温氧化以及高的热膨胀系数等优点,成为广泛应用的热障涂层金属黏结层材料。
Nb-Ti-Al合金及其硅化物涂层的高温氧化行为

Nb-Ti-Al合金及其硅化物涂层的高温氧化行为蔡圳阳;肖来荣;余宸旭;刘赛男;毛海军;曾德露【摘要】The Nb-40Ti-7Al (mass fraction,%) alloy was prepared by electron beam melting and vacuum self-consuming arc melting, and then prepared the Si-Cr-Ti coating on the surface of the alloy in the way of stuff paste melting. Oxidation behavior of the alloy matrix and coating at 1 400℃were studied, including the change of morphology and composition during the oxidation process, by means of XRD, SEM, EDS, and EPMA. The results show that the oxidation products of the alloy are mostly TiNb2O7, TiO2 and Al2O3 during the oxidation time of 1h-11h at 1 400℃. The coating is mainly composed of the subject layer of (Nb, Ti, Cr, Al)Si2 and transition layer of (Ti, Nb, Al)5Si3 before oxidation, and then the barrier layer ofAl2O3, SiO2 and TiO2 formed on the surface of the coating after oxidation. The oxidation behavior of alloy and coating follows the law of parabola. After coating, the mass gain of the matrix decreased from 161.98 mg·cm−3 to 9.56 mg·cm−2, and the coati ng was complete, showing that it has good anti-oxidation ability at high temperature.% 采用电子束和真空自耗电弧熔炼法制备Nb-40Ti-7Al(质量分数,%)合金,利用料浆熔烧法在合金表面制备Si-Cr-Ti涂层,研究在1400℃下合金与涂层的氧化行为。
钴基合金铝化物涂层高温氧化及退化规律的数学表征
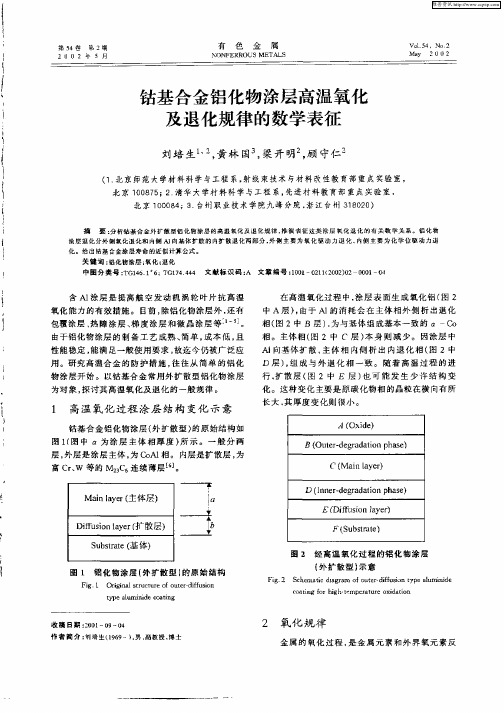
1 高温 氧化 过 程 涂层 结构 变化 示意
钻基 台 金铝化物 涂层 ( 扩散型 ) 外 的原 始结 构如 图 1 图 中 n为 涂 层 主 体 相 厚 度 ) 示 。一 般 分 两 ( 所 层, 外层 是涂 层主体 , C Al 。 内层 是扩散 层 , 为 o 相 为 富 c 、 等的 M2 6 续薄层 ¨ 。 rw 3 连 c J
化 。这种变 化 主要是 原碳化 物 相 的晶粒在横 向有 所 长太 , 其厚度 变 化则很 小 。 A( xd ) O ie
B( tr e rdt np ae Oue・ ga ai h s) d o C( i l e) Ma y r na D (n e-e rd t np ae In r ga ai h s) d o
摘 要 : 分析钻基台金外扩散型铝化铷潦层的高温氧化厦退化规律 , 推演表 征逭娄潦层 氧化迅化 的有关数 学关系。铝化物
棘 层 退化 分 外 恻 氧化 退 化 和 内侧 AI 基 体 扩 散的 内扩 散 退 化 两部 分 , 侧 主 要为 氧 化 驱 动 力 退 忧 , 向 外 内伽 主 要 为 化 学 位 驱 动 力 退 化 蛤 出 钴 基 合 金涂 屡 寿 命 的 近 似 计算 甚 式 。
关键词 : 铝化物涂层 氧化; 退化 中 图分 类 号 : G 4 6 T 7 4 文 献 标 识码 : 文章 编 号 :0 1 0 1 (0 2 0 0 0 一 4 T 16 1 ; G14 4 4 A i0 — 2 1 20 )2 0 1 O
含 A1 涂层 是 提高 航 空 发动 机 涡轮 叶 片抗 高 温 氧化 能力 的有 效措施 。 目前 , 除铝化物涂 层外 , 有 还
Fi S h ma i da rm f u e- i u in t p lmi ie g2 c e t ig a o tr df s y eau n d c o o c a ig { r hg —e e a u e o ia in o tn o i h t mp r t r x d t o
- 1、下载文档前请自行甄别文档内容的完整性,平台不提供额外的编辑、内容补充、找答案等附加服务。
- 2、"仅部分预览"的文档,不可在线预览部分如存在完整性等问题,可反馈申请退款(可完整预览的文档不适用该条件!)。
- 3、如文档侵犯您的权益,请联系客服反馈,我们会尽快为您处理(人工客服工作时间:9:00-18:30)。
扩散性铝化物涂层及制备工艺
高温铝化物扩散涂层是在20世纪50年代发展起来的,到目前仍被广泛应用,并占整个高温防护涂层的90%。
制备铝化物涂层的扩散渗铝工艺成熟,方法多样化。
在镍基合金上应用最广的渗铝方法有:固体粉末渗铝,料浆法渗铝。
下面简要介绍固体粉末渗铝、料浆渗铝、气相渗铝三种工艺的原理。
1固体粉末渗铝[11]
在耐热钢容器中,将样品包装于扩散剂之中,渗剂由金属铝粉末或富Al的FeAl合金粉末,活化物质(如卤族化合物)及填料(氧化铝)混合组成,用氢或氢气作保护气体,按规定的时间进行热扩散处理。
以钢的渗铝为例来说明渗铝的原理。
渗铝过程中发生如下系列反应:
2NH4Cl=2HCl+N2+3H2
6HCl+2Al=2AlCl3+3H2
Fe+AlCl3=FeC13+[Al]
即在高温下,NH4Cl分解释放出HCl气体、HCl和铝粉或FeAl粉中的铝反应形成气态AlCl3。
AlCl3扩散向渗件表面,并和基体元素铁反应,铝原子被置换出来.反应式在通常情况下几乎不会发生,但在金属表面有催渗剂的条件是有可能发生的。
一般常见的渗铝温度为850℃~1050℃。
温度太低,渗铝速度会急剧下降;温度太高,则渗铝件的晶粒急剧长大而使材料的机械性能变差。
渗铝层的厚度可通过调整渗铝时间和温度来控制。
但是,为获得较厚的渗层,延长渗铝时间远没有提高温度那样效果显著,因为在保温一定时间后,合金表面的铝己达到饱和状态,此后渗铝层的厚度将完全取决于铝的扩散速度,即使再延长时间,渗铝层厚度也不会有很大的增加[12]。
固体粉末渗铝的优点是:设备简单,操作方便,特别适用于机械的零部件;其缺点是:渗剂容易被氧化,工件尺寸受限制,对工件表面粗糙度有一定影响。
2料桨法渗铝[13][14]
料浆法(slurry process)将渗铝剂和粘结剂配制成料浆,涂在工件表面,烘干后在真空或氢气保护下进行高温扩散处理。
高温扩散处理温度一般在1000℃~1200℃。
用铝活度高的料浆得到向里扩散型涂层,铝活度低时得到向外扩散型
铝化物涂层。
机理与固体粉末法类似,但因其有不受工件尺寸限制,可以在形状复杂的工件表面涂覆铝化物涂层.根据渗层形成的原理,料浆渗铝可分为熔烧型和扩散型两种。
熔烧型的料浆只用铝粉作渗剂,不加活化剂,其渗铝原理与液体法相同。
扩散型的渗铝剂中需有氧化铝粉及活化剂,其渗铝原理与固体法相同。
此次在K4l7合金表面制备的渗Al涂层属于无机盐料浆涂层,属于熔烧型,渗剂中无活化剂.无机盐料浆涂层是二十世纪七十年代发展起来的一种较新型涂层,它具有优越的耐腐蚀性能,而且工艺简便,成本低廉.我国制备此涂层一般工艺流程是:
待渗工件除油→称量或测厚→涂覆→烘干→固化→称量或测厚→扩散处理→清理→称量或测厚→成品
在按上述流程操作时,首先必须保证除油的质量,还可以用120~220目Al203砂轻吹,除去工件表面污物和造成一定的粗糙度,以增强料浆与工件表面的结合力.对料浆的厚度以称量法较为准确,用测厚法也可行。
料浆层的厚度以采用反复喷涂的方法来达到要求为好。
与一次喷涂达到厚度要求相比,多次喷涂可以改善料浆的均匀度及致密性。
采用反复喷涂的方法时,在每次喷涂后应予以烘干,烘干温度80℃。
如料浆层过厚,可用碱的水溶液除去后再重新喷涂。
固化在370℃左右进行,在扩散处理后应进行清理。
清理后的工件表面呈黑色;用轻吹砂的方法清理后,表面为带玫瑰红的乳白色。
影响工件质量工艺参数:
(1)粘结剂成分的影响粘结剂成分的变化,直接影响涂层的表面光洁度和渗入量。
(2)金属粉末的影响料浆中的铝粉含量一般控制在50%(质量百分数)。
含量过高会使料浆太稠而不易涂覆均匀,影响表面质量和涂层均匀性,含量过低涂覆时容易流淌,导致渗层铝浓度低。
(3)不同料浆量对渗入量的影响根据实践经验,一般来说,渗入量随料浆量的增加而增加,因此,正确地选择喷涂料浆量是控制渗层厚度的关键。
(4)扩散温度对渗入量的影响根据有关测试表明,扩散温度对渗入量的影响小。
因此,可在较宽的温度范围内选择扩散温度。
3气相渗铝[10]
气相渗铝(vapour phase Aluminizing)与粉末包装法相似,故也称非接触包装
渗铝(out-of-contact Aluminizing),或者称为over Aluminizing或above pack。
工艺步骤:在密封的反应器中,将样品悬挂于盛渗剂的浅盘之上,通入氢气。
当加热到预定温度,渗剂中含欲渗元素如Al或Cr的合金(Me)与活化剂卤族元素(X)
的化合物AX
X (A为NH
4
、Y、Zr或Hf)反应,生成挥发性金属卤化物MeXx: Me(合金)十AXx=MeXx(g)+A
当渗铝时,铝源用FeAl合金与Cl反应,可形成AlCl、AlCl
2和AlCl
3
,它
们以气态扩散到镍基合金工件表面进行反应,扩散形成涂层,从而避免渗剂颗粒镶人涂层表层,便于做面罩,使工件局部如叶片根部不渗铝,并使叶片冷却孔内部渗铝。
4渗铝涂层相与结构
以镍基合金为例来说明渗铝层的相与结构。
在Ni-Al二元体系中(见图1.1),随铝含量升高可形成4种化合物相:γ′-Ni3Al、β-NiAl、δ-Ni2Al3以及NiAl3。
其中,NiAl
3
熔点仅为854℃,通常情况下涂层中不形成该相。
图1.1 Ni-Al二元相图
γ′-Ni3Al:铝的质量分数为13.2%~14.9%,属面心立方结构。
它的熔点为1400℃,是镍基高温合金的强化相。
β-NiAl:铝的质量分数为23.5%~36%,属体心立方结构。
符合化学计量的β相的熔点为1638℃。
当铝的原子分数大于50%时,为富铝的β相;当镍的原子分数大于50%时,为富镍的β相。
δ-Ni2Al3:铝的质量分数为55%~60%,晶胞呈棱方点阵。
它的熔点为855℃-1133℃。
常温下,该相组成的涂层极脆,受外力时易碎。
因而在使用中不希望
涂层中存在Ni
2Al
3
相。
采用高温扩散,可将其转变为NiAl相。
当铝含量很低时,铝固溶到镍中,形成γ-Ni的固溶体。
在所有Ni-Al形成的固溶体和化合物相中,β-NiAl抗氧化性最好。
γ′-Ni3Al抗氧化性能介于β-NiAl 和γ固溶体之间。
铝化物涂层的结构[15]取决于渗剂中铝的活度、渗铝温度、基体合金成分、涂层厚度、涂层中其他元素的浓度及后处理工艺。
根据扩散方式可将渗铝分为向外生长型与向内生长型两种工艺[16]。
Goward等人将这两种工艺称为低活度渗铝和高活度渗铝,这种分法在概念上是含混不清的。
渗铝徐层的类型与多种因素有关,当渗剂中的铝活度固定时,改变活性剂的含量就可获得不同类型的涂层。
以涂层的生长方式来分类则可避免种种误解。
(1)向内生长型。
在较低温度(700~850℃)下进行,反应扩散形成富Al的Ni2Al3相组成的涂层,因为Ni2Al3相很脆,需经渗后退火(1000~1100℃)后处理。
涂层的生长机制为渗剂中铝向内扩散。
Ni2Al3层中Al向基体扩散,由于Al在Ni2Al3相中互扩散系数较高,Ni2Al3最终完全转变为β-NiAl,并形成外层,外层保留了Ni2Al3相中原有碳化物及富合金元素析出相质点;中间层为纯净的β-NiAl 相;内层又复含有基体中的沉淀相。
高活度渗铝需要两次加热,不仅操作步骤多,成本高,而且表层含碳化物,相对抗高温氧化不利。
因为碳化物氧化有气态氧化物,加速氧化膜的破坏。
(2)向外生长型。
在较高温度(1000~1100℃)下进行Al与Ni反应生成NiAl 相涂层,涂层长大由Ni向外扩散。
同时NiAl层下合金中Ni浓度降低而合金元素富集;因镍基高温合金通常含3%~6%(质量)Al,故在原始表面下形成富Ni的NiAl层,其中含有基体合金元素和析出相(如碳化物和σ相)。
而原始表面以上
富Al的NiAl外层表面区镶入渗剂的颗粒,成为徐层的夹杂物(如Al
2O
3
)。
为解
决渗层表面镶入夹杂,发展了气相渗铝工艺。