金属切削加工中的振动分析及控制途径
机床切削时的振动分析
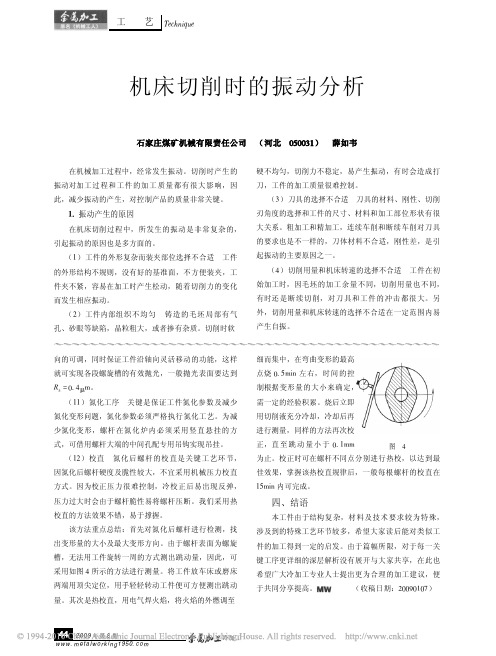
#" 防止和减小振动的措施
由于振动产生的原因是多方面的,要依据具体情况 分析,判断振动产生的原因和性质,采取有效措施,避 免和减少振动的产生。 ( $ ) 工件要正确装夹! 工件夹紧时,夹紧点要选在 工件刚性好,且变形小的部位。以减小接触变形,并且 距工件承受切削力的位置越近越好。如果是车床,注意 降低高速旋转时因工件偏心而引起的振动。如果是镗、 铣、刨及钻床等,则注意增大工件和工作台的接触面 积,提高稳定性。 ( % ) 合理选择刀具的材料 ! 如钨钴类 ()* 和钨钛 钴类 (+" ,抗振性强,分别适用于铸铁、有色金属和钢 件的粗加工;而 ()& 和 (+$" 则适用于精加工。制造刀
杆时,要选择合适的材料,调质处理,以增加刀杆自身 的刚性。在保证顺畅排屑的情况下,尽量选择直径 较 大、长度适宜的刀杆。 ( & ) 合理选择刀杆的几何角度! 在金属切削中,对 产生振动影响最大的刀具角度是主偏角和前角。减少主 偏角,会使切削截面宽度增加,厚度减小,径向切削力 增大,振动也随之增大;减小前角,或采用负前角,切 屑会增大,切屑与刀具前面的摩擦力使切削加工硬化提 高,振动增强;刀尖圆弧半径的变化,对切削振动的影 响也比较明显,由于刀尖圆弧的增大,刀具切削的 阻 力、径向力及加工表面的摩擦力和挤压力也随之增大, 振动也增大。 所以,选择刀具的几何角度时,一般注意以下几个 方面:!工件系统刚性较弱时,应采用较大的主偏角, 在 ,"- . /0- 时,可有效减小径向切削分力。 " 适当增大 前角,使切削刃光滑锐利,有较低的表面粗糙度值,减 小切屑和刀具前面的摩擦力,可同时抑制和排除切屑瘤 产生,降低径向切削分力。 # 尽量不采用负前角,尽量 选用较小的刀尖圆弧半径。 ( ’ ) 合理选用切削用量 ! 在车削中,切削速度 ) 1 "0 . #02 3 245 时,稳 定 性 最 低,最 容 易 产 振幅越小;背吃刀量越小,振幅越小。在工件表面粗糙 度值允许的前提下,应选择较大的进给量和较小的背吃 刀量。 ( " ) 提高机床自身的抗振性 ! 可以从改善机床刚 性,提高机床零件加工和装配质量方面合理保养机床。 机床各移动部件之间和各轴承安装的间隙应按照规定的 技术要求来调整,使其处于最佳工作状态。应锁紧的零 件必须锁紧可靠无松动,保持工作面平整、光滑,使工 件和工作台面有很好的接触性。 ( # ) 工作环境的选择! 精密机床要尽量同粗加工机 床分开布置,远离锻造等工序的工作场地,远离有重型 车辆行驶的公路等,尽量减少环境对机床的影响。
车削过程中振动与控制
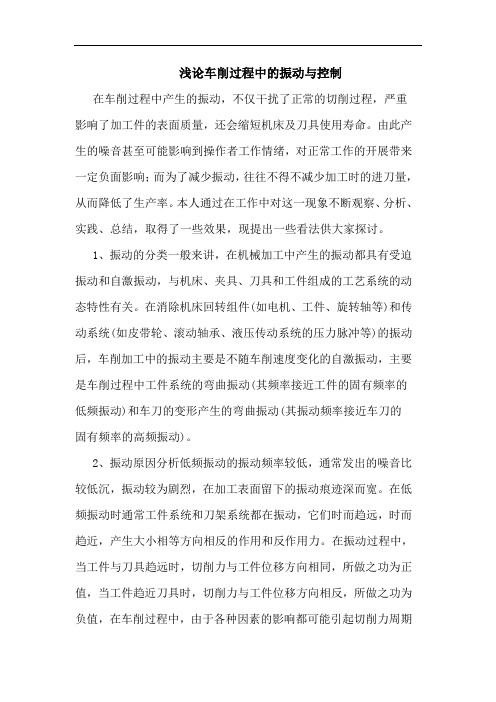
浅论车削过程中的振动与控制在车削过程中产生的振动,不仅干扰了正常的切削过程,严重影响了加工件的表面质量,还会缩短机床及刀具使用寿命。
由此产生的噪音甚至可能影响到操作者工作情绪,对正常工作的开展带来一定负面影响;而为了减少振动,往往不得不减少加工时的进刀量,从而降低了生产率。
本人通过在工作中对这一现象不断观察、分析、实践、总结,取得了一些效果,现提出一些看法供大家探讨。
1、振动的分类一般来讲,在机械加工中产生的振动都具有受迫振动和自激振动,与机床、夹具、刀具和工件组成的工艺系统的动态特性有关。
在消除机床回转组件(如电机、工件、旋转轴等)和传动系统(如皮带轮、滚动轴承、液压传动系统的压力脉冲等)的振动后,车削加工中的振动主要是不随车削速度变化的自激振动,主要是车削过程中工件系统的弯曲振动(其频率接近工件的固有频率的低频振动)和车刀的变形产生的弯曲振动(其振动频率接近车刀的固有频率的高频振动)。
2、振动原因分析低频振动的振动频率较低,通常发出的噪音比较低沉,振动较为剧烈,在加工表面留下的振动痕迹深而宽。
在低频振动时通常工件系统和刀架系统都在振动,它们时而趋远,时而趋近,产生大小相等方向相反的作用和反作用力。
在振动过程中,当工件与刀具趋远时,切削力与工件位移方向相同,所做之功为正值,当工件趋近刀具时,切削力与工件位移方向相反,所做之功为负值,在车削过程中,由于各种因素的影响都可能引起切削力周期性的变化,使在每一振动周期中,切削力对工件(或刀具)所做之正功总是大于它对工件(或刀具)所做之负功,从而使工件(或刀具)获得能量补充产生自激振动。
在车削过程中,影响切削力周期性地变化,并使退出时切削力大于切人时切削力的情况有以下几个因素: 2.1切削与刀具相对运动产生的摩擦力。
在加工韧性钢材时径向切削分力开始随切削速度的增加而增大,自某一速度开始,随切削速度的增加而下降。
据切削原理可知,径向切削分力主要取决于切削与刀具相对运动产生的摩擦力,即切削与刀具前刀面的摩擦力。
切削加工中振动产生的原因及消减措施
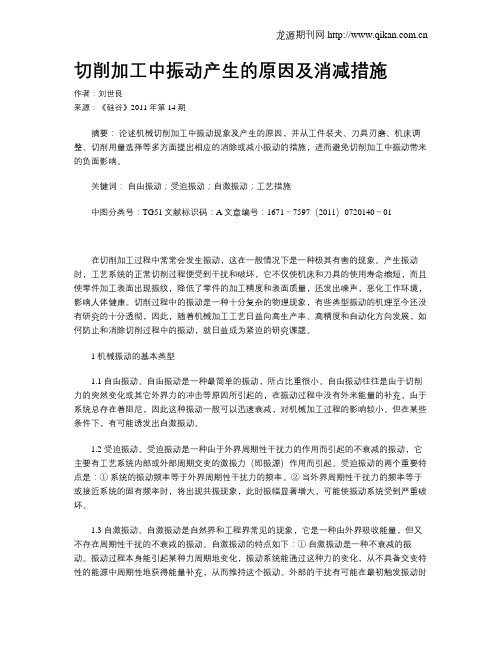
切削加工中振动产生的原因及消减措施作者:刘世良来源:《硅谷》2011年第14期摘要:论述机械切削加工中振动现象及产生的原因,并从工件装夹、刀具刃磨、机床调整、切削用量选择等多方面提出相应的消除或减小振动的措施,进而避免切削加工中振动带来的负面影响。
关键词:自由振动;受迫振动;自激振动;工艺措施中图分类号:TG51文献标识码:A文章编号:1671-7597(2011)0720140-01在切削加工过程中常常会发生振动,这在一般情况下是一种极其有害的现象。
产生振动时,工艺系统的正常切削过程便受到干扰和破坏,它不仅使机床和刀具的使用寿命缩短,而且使零件加工表面出现振纹,降低了零件的加工精度和表面质量,还发出噪声,恶化工作环境,影响人体健康。
切削过程中的振动是一种十分复杂的物理现象,有些类型振动的机理至今还没有研究的十分透彻,因此,随着机械加工工艺日益向高生产率、高精度和自动化方向发展,如何防止和消除切削过程中的振动,就日益成为紧迫的研究课题。
1 机械振动的基本类型1.1 自由振动。
自由振动是一种最简单的振动,所占比重很小。
自由振动往往是由于切削力的突然变化或其它外界力的冲击等原因所引起的,在振动过程中没有外来能量的补充,由于系统总存在着阻尼,因此这种振动一般可以迅速衰减,对机械加工过程的影响较小。
但在某些条件下,有可能诱发出自激振动。
1.2 受迫振动。
受迫振动是一种由于外界周期性干扰力的作用而引起的不衰减的振动,它主要有工艺系统内部或外部周期交变的激振力(即振源)作用而引起。
受迫振动的两个重要特点是:①系统的振动频率等于外界周期性干扰力的频率。
②当外界周期性干扰力的频率等于或接近系统的固有频率时,将出现共振现象,此时振幅显著增大,可能使振动系统受到严重破坏。
1.3 自激振动。
自激振动是自然界和工程界常见的现象,它是一种由外界吸收能量,但又不存在周期性干扰的不衰减的振动。
自激振动的特点如下:①自激振动是一种不衰减的振动。
金属加工机械的振动与噪声分析与控制

金属加工机械的振动与噪声分析与控制金属加工机械在生产过程中起着至关重要的作用。
然而,这些机械在运行过程中产生的振动与噪声问题也给生产环境和操作人员带来了许多不便。
本文将重点分析金属加工机械振动与噪声的产生原因,并提出相应的控制措施。
1. 振动与噪声的产生原因金属加工机械在运行过程中,振动与噪声的产生主要可以归结为以下几个方面:1.1 机械结构设计不合理机械结构设计不合理是导致振动与噪声的一个重要原因。
例如,机架的结构刚度不足、零部件之间的配合间隙不当等都会导致机械运行过程中的振动与噪声。
1.2 加工过程中产生的高频振动金属加工过程中,如车削、铣削、磨削等操作产生的高频振动也是振动与噪声的一个重要来源。
这些振动会传播到整个机械结构中,导致噪声的产生。
1.3 机械零件的磨损与故障机械零件在长时间运行过程中,由于磨损和故障,会导致振动与噪声的产生。
例如,轴承磨损、齿轮损坏等都会导致机械运行过程中的振动与噪声。
针对上述振动与噪声的产生原因,可以采取以下控制措施:2.1 优化机械结构设计通过优化机架的结构刚度、合理设置零部件之间的配合间隙等方法,可以有效降低机械运行过程中的振动与噪声。
2.2 采用减振材料和隔振措施在金属加工过程中,采用减振材料和隔振措施可以有效降低高频振动对整个机械结构的影响。
例如,在机械结构中加入橡胶减振垫、采用隔振支架等。
2.3 定期维护和检查通过定期对机械零件进行维护和检查,及时发现并解决磨损和故障问题,可以有效降低振动与噪声的产生。
3. 结论金属加工机械振动与噪声的产生原因复杂多样,需要从多个方面进行分析和控制。
通过优化机械结构设计、采用减振材料和隔振措施以及定期维护和检查,可以有效降低振动与噪声问题,提高生产环境和操作人员的舒适度。
以上内容为金属加工机械振动与噪声分析与控制左右。
后续内容将详细介绍振动与噪声的测量方法、分析手段以及具体的控制方案等。
为了有效地分析和控制金属加工机械的振动与噪声,首先需要对其进行准确的测量。
切削振动产生原因和解决

细长杆立铣刀铣削深型腔时 常采用插铣方法
插铣就是刀具象钻头一样轴向 进刀,当铣削深的型腔时,通 常长杆的悬伸大于3倍的刀杆 直径,我们推荐使用轴向进刀 的插铣方法,但是立铣刀刀片 刃口有一定的径向切削刃,刀 具供应商有技术资料证明此刀 具在插铣时的最大吃刀宽度 PlungeMill是专门用于模具和 航空工业的大直径插铣刀,它 最大的特点是高效率和超大切 宽,通常用于大型深腔模具的 开粗。
切削振动的原因
刀具在切削工件时发生振动需要有下面三 个条件同时存在: 第一是包括刀具在内的工艺系统刚性不足 导致其固有频率低, 第二是切削产生了一个足够大的外激力, 第三是这个外激力的频率与工艺系统的固 有频率相同随即产生共振
分清自激振动和强迫振动
。
刀具振动实际应该叫“切削振动,通常发生在长悬臂刀杆的镗削和铣削,薄 壁件的切削加工,细长杆的车削等等。当环保做为车间考核的标准时,高速 钻削产生的高频啸叫也和振动噪音一起列为技术公害。 切削振动顾名思义只有在刀具进行切削时才产生,如果振动来自非切削因素 如不稳定的机床地基,机床丝杠的间隙,主轴轴承的损坏甚至几百米以外火 车的经过而产生的震动我们叫做强迫振动,这种振动不伴随噪音而非我们讨 论的话题。 切削振动产生噪音,但噪音并不是全由切削振动引起发生,机夹刀片铣刀在 100米以上的切削速度每齿走刀在0.1毫米以上铣削3毫米的切深,即便是铣削 灰口铸铁也会产生接近90分贝的噪音,而低频切削振动噪音常低于此值。 切削振动是自激振动是一种正弦波振动,除了用专业仪器测量振频与波长外 ,最明显的是工件被加工表面有振纹。
薄壁工件的铣削加工
薄壁工件铣削发生振动的原因完全来自于工件,这种工件被叫做箱式或者 碗式零件(box like or bowl like shape workpiece),由于振动来自于工件本身 ,那么技术人员各显神通,国外在处理这类零件的铣削加工主要以改善工 件夹持为主,例如增加合适的辅助支撑点,在夹具和机床工作台面之间加 装一层木板,用粗大的橡皮条或者弹簧勒在壳体的外面,在箱体内部充满 湿沙子等等,奇思妙想不一而足。在铣削薄腹板时,推荐使用90度面铣刀 以减小对腹板的轴向切削力。
剖析金属切削加工中的振动及其抑制措施

剖析金属切削加工中的振动及其抑制措施摘要:金属切削加工中普遍存在振动现象,也是一种无法忽视的有害现象。
如果金属切削加工中出现振动现象,会导致刀具与工件之间产生航相对位移,则会造成加工表面出现振动痕迹,对零件的质量和性能容易造成不良影响。
其振动产生噪音会对人体听力造成损害,对于这些情况则需要对金属切削加工中的振动现象给予重视。
本文主要是对金属切削加工中的振动现象进行了分析,并提出科学合理的抑制措施。
关键词:金属切削加工;振动;抑制措施;引言:在金属切削加工中产生振动是非常普遍的现象,容易对工艺系统的正常切削过程造成不良影响,发生振动现象的原因比较多,一般是因为各种因素的影响所造成的。
但是对其产生原因进行排查和分析,根据分析结果采用具有针对性的抑制措施,便可以在一定程度上抑制振动的产生,同时还能控制振动造成的破坏影响,从而有效提升工件的加工质量,以及延长刀具的使用期限。
1.金属切削加工中振动现象的产生原因比如说在车削加工中也会产生振动,在车床安装的过程中通过加设隔振地基、且保障传动系统并不存在缺陷的情况下,在进行加工的过程中依旧还是会产生一定程度上的振动。
一般来说在金属切削加工中的振动类型分别是:自激振动、强迫振动[1]。
通常在机床中强迫振动的产生频率达到50%~60%,自激振动的产生频率占有40%左右。
1.强迫振动。
其产生原因主要在于在存在不平衡的情况下则会造成离心惯性力,当设备在运行的过程中,其质量存在偏心问题,当机床在运转的时候则会产生离心惯性力,也就是导致机床产生振动的原因。
2.机床传动机构存在缺陷。
一般来说在机床传动系统中的旋转零件,由于在制造的过程中存在误差问题,导致在转动的过程中会形成下干扰力,并且具有周期性的特点,进一步会产生出现强迫振动的激振力。
比如在制造齿轮的时候没有准确把握齿形的制造质量,以及没有精准控制啮合刚度,从而导致齿轮的轴向、切向等产生振动现象,甚至还能通过轴承、轴对其他零部件造成振动影响。
切削振动的产生及解决

使用锋利的刀片来降低切削力
非涂层刀片通常比涂层刀片 要锋利 即便是涂层刀片,物理涂层 (PVD))也比化学涂层( CVD或MTCVD)刃口要锋利 判断刃口的锋利度可以从它 在指甲盖上是否划出成形的 屑来判断
刃口的钝化半径通 常在35u到75u之间
切深一定时使用小的刀尖圆弧半径
比如刀片的刀尖角为0.8mm不变时 ,随着刀片切深的增加,细长的镗 刀或铣刀杆振动倾向在切深ap和刀 尖圆弧半径(r=0.8mm)相等时最 大,当切深ap大于刀尖半径r后, 刀杆的振动反而被抑制 图中的∆R代表镗杆的弹变,可以 看出当切深ap与等于刀尖圆弧半径 时弹变最大,而且随着切深增加弹 变不会再增加反而开始减小,因为 径向切削力FCN在ap=r时最大,ap 再增加只会增加轴向抗力,而轴向 抗力不是细长刀杆产生振动弹变的 原因,反过来还会使刀杆保持稳定 。
使用正前角和大后角的刀片 配以轻快的断屑槽。 配以轻快的断屑槽。 pos. neg..
这样的刀片在镗削或铣削中的切削楔入角最小,切 削当然轻快。在车削与镗削中,7度和11度后角是 最常见的刀片,刀片为螺钉夹持的最多,在20毫米 以下的孔镗削中,即便不存在振动问题大家也通常 选择11度后角的刀片,例如山特维克可乐满的 TPMT,DPMT,VCEX的刀片(V型刀片后角为7度或 11度)。后角以7或11度后角刀片为主要推荐,因 为它们是ISO标准刀片,不同厂家的刀片可以互换 车刀片适用于镗削加工,现代机夹车刀片按照粗精 加工分为不同的短屑槽槽型,比如像可乐满刀片槽 型PF,KM,MF,KR等,其中的第二位表示刀片适合的 加工,F表示Finishing为精加工,这是适合做减振 镗削的刀片,当然刀片应该配以刃口耐冲击的材质 才可以,比如PF-4025,PF-4035,WK-4025等等。
金属切削加工的颤振及避振分析

的摩擦阻力,因此, 凡影响变形和摩擦 的因素都要影响切 削力。:实验表明【8】,。 背吃刀量%、进给量 厂增大,均使切削力 增大,但两者的影响, 程度不同,背吃刀量
3250
妻3000
-R 2750
蠢2500
刚
。Ⅵ 硝 \
L J.
T
O
l
2
3
4
切削速度,Ⅲ·一
图1切削速度对切削力的影响
YTl5车刀,工件材料45钢
时刀具的振动速度为互,则相对切削速度为Vc----勘一孟,刀具
有振动时的实际切削速度是相对切削速度。 由式(2)知,有振动时的切削力表达式为
F。=coTsap,哳魄广(cI移水妒州2妒。3)
(4)
式(4)右边的第二项可以看作是速度型的动态力。因此速
度型的动态切削力以t)表示为
以£)可魄广(clt,。+c征+c积)
相对稳定的条件是
3c3v2+2c2v+cl=0
(9)
这是个关于公称切削速度口的二次方程,当、/ci一3c。c,≥o
钆F墨型唾匾 时,其实数解为
(10)
.,C3
由此可以推断。以式(10)所示的公称切削速度为中心的
were interpreted by analyzing velocity type dynamic cutting force.The essential and sufficient conditions of chatter
vibration occurred and developed were advanced.There is one or two stable parts of cutting velocity for preventing
- 1、下载文档前请自行甄别文档内容的完整性,平台不提供额外的编辑、内容补充、找答案等附加服务。
- 2、"仅部分预览"的文档,不可在线预览部分如存在完整性等问题,可反馈申请退款(可完整预览的文档不适用该条件!)。
- 3、如文档侵犯您的权益,请联系客服反馈,我们会尽快为您处理(人工客服工作时间:9:00-18:30)。
金属切削加工中的振动分析及控制途径
摘要:在金属切削加工过程中,如果产生振动,会造成很多不良的影响,不仅严重影响机器和零部件本身的性能和工艺,而且振动中产生的噪音还会对操作者本身的身体健康产生有害的影响。
本文将通过分析金属切削加工中产生振动的原因、主要类型和特点,重点提出控制甚至消除振动的有效途径,以促进金属切削加工技术的发展。
关键词:切削加工振动原因振动类型振动特点控制途径
引言:
近些年来,随着机械制造行业的不断发展,各种先进的制造技术也不断被研发出来,金属切削加工则是这些技术中的佼佼者,已经被应用到各个领域的机械制造和生产中。
在设计机床和刀具、制订机器零件的切削工艺及其定额、合理地使用刀具和机床以及控制切削过程时,都要利用金属切削原理的研究成果,使机器零件的加工达到经济、优质和高效率的目的。
金属切削加工过程中,刀具与工件之间相互作用和各自的变化规律现已经成为了一门学科。
在金属切削加工过程中,如果产生振动,会造成很多不良的影响,不仅严重影响机器和零部件本身的性能和工艺,而且振动中产生的噪音还会对操作者本身的身体健康产生有害的影响。
下面本文将通过分析金属切削加工中产生振动的原因、主要类型和特点,重点提出控制甚至消除振动的有效途径。
一、振动的基本类型
从一般情况而言,在金属切削加工过程中所产生的振动大致可以分为两种类型,即:自激振动和强迫振动。
相比较而言,这两种振动中自激振动的概论一般低于40%,而强迫振动则占主要方面,大约为60%。
二、产生振动的主要原因
通过统计分析我们可以清晰的看出,金属切削加工过程中产生振动的类型基本分为两种:自激振动和受迫振动。
因此,在机械制造过程中,根据这两种不同类型的振动,可以通过机床不同的运行状态来分析振动产生的原因。
(一)空转时存在的振动及原因分析
当机床在空转时也有可能产生一定的振动。
造成振动的主要原因可能是床鞍导轨之间的爬行,也可能是是由于外部传来的振动,例如:地基周期或者非周期的干扰力。
此外,机床内部振源也会使机床强迫振动,例如:机床主轴、电机等各种旋转体的不平衡等式。
(二)切削过程中产生的振动及原因分析
在金属切削加工过程中,一般分为自由震动、自激振动和强迫振动。
自由震动主要是受到外界传来的冲击力,机械系统本身产生周期性或者非周期性的冲击力,如:间隙、凸轮与杠杆的冲击,材料不均匀的硬点引起的冲击。
自激振动大部分情况下是受再生效应和振动耦合等方面的影响形成的。
强迫振动主要是切屑形成的周期性、断续切削的交变力等原因造成的。
三、振动的特点分析
强迫振动与自激振动作为振动的两种不同类型,分别具有不同的特点:
(一)强迫振动的特点
振动频率与外界干扰力的频率相同是强迫振动最主要的特点。
强迫振动的振幅与系统刚度、阻尼系数以及干扰力的大小均有关系。
阻尼系数越小时振幅越大,干扰力越大时系统刚度越小。
如果系统的自然频率与干扰力的频率比值接近或者等于1时,振幅将达到非常大的程度,甚至会给机器造成相当大的损害。
(二)自激振动的特点
自激振动通常被看作是一种不衰减的振动,其振动频率接近于或者等于系统的自然频率。
在这种振动过程中,其本身就能够引起某种外力周期性的变化,并且能够从不交变的特性能源中周期性的获得能量,以此来维持振动。
自激振动的产生与否以及振幅大小取决于每一次振动的周期内,系统补充得到的能量于消耗的能量的对比。
倘若所补充的能量小于所消耗的能量,那么振幅便会逐渐减小;所补充能量大于所消耗的能量时,振幅会不断增大。
当振幅达到某一数值时,获得的能量小于消耗的能量时,自激振动也会随之消失。
三、控制振动的主要途径
针对不同的振动类型具有不同的控制振动的途径,下面本文将透过强迫振动和自激振动两种不同类型的振动分别分析控制振动的
主要途径。
1、自激振动的控制途径
控制自激振动主要有一下几个途径,即:选择合理的切削宽度、选择合适的切削深度、选择合适的切削速度和选择合适的进给量。
在切削过程中应该控制切削的宽度、深度、速度和进给量,不仅能够有效减少振动,而且能够提高工作效率,维持系统的稳定。
要特别注意的时,在金属切削加工中,还需要合理选择刀具的几何参数,积极进行故障检查和系统维护。
2、强迫振动的控制途径
(一)注重制造精度的提升。
特别是在齿轮传动的过程中,提高齿轮的制造精度和配备质量有助于减小齿轮振动,可以将夹布胶木或者尼龙等材料运用到齿轮制作过程中。
(二)提高刚性,增加阻尼。
这样可以有效提高系统的抗振能力,减小系统振动。
(三)减振与隔振并用。
一般情况下,可以采用液压缓冲结构或者装置,以此来设法减少工作台换向时的冲击。
(四)合理安排,避开共振。
在结构设计中考虑系统工艺各部件的固有频率,远离干扰振源的频率,避开共振区域,使工艺系统各部件在准静态区域或者惯性区运行。
(五)消除零件的不平衡性。
例如:在机床与电机的连接处用橡皮或者其它材料来隔离振动。
另外,保证砂轮主轴部件的平衡也十分重要。
结语:
在金属切削加工中,振动会产生极为消极的影响,不仅影响机器
的使用寿命,而且对操作人员的身体健康也会产生不良影响。
因此,在实际操作过程中,操作人员应该根据自激振动和强迫振动的不同特点及其产生的原因,积极采用各种不同的控制途径,从切削的宽度、深度、速度和进给量入手,逐渐提升精度、刚性,合理安排频率,减振与隔振并用,从而有效抑制振动的产生,促进生产安全有效进行。
参考文献:
[1]李玉平;;陈萍;;晏志勇;机械加工中的振动分析及控制措施[j];金属加工(冷加工);2008;(24):15-16
[2]张悦;;李启东;;由颖;;孙泰礼;;郑鹏;;张希川;变频器在切削力测量实验中的应用[j];实验技术与管理;2011;(01):33-34
[3]殷显东;金属切削加工中的振动分析及控制途径[j];黑龙江科技信息;2008;(28):12-13
[4]陈宏钧;金属切削常用材料及热处理手册[m];机械工业出版社;2006:26-29
[5]迟彩芬;;刘艳梅;涂层刀具技术的发展前景及应用[j] ;中国科技信息;2009;(04):43-44。