厚度自动控制系统
带材冷轧机厚度自动控制(AGC)方式及恒体积流控制系统

带材冷轧机厚度自动控制(AGC)方式及恒体积流控制系统李铁【摘要】The paper discussed several control modes and the corresponding characteristics of AGC system of cold strip mil;it presented the composition of the control system and the mathematical model of the constant volume flow;it demonstrated the hardware component of control system of the constant volume flow based on IPC and PLC,respectively;it described the signal acquisition and working principle of constant volume flow in the gauge control system.%文章论述了带材冷轧机厚度自动控制系统AGC(automatic gap control)的几种控制方式和特点,着重论述了恒体积流的控制系统组成和数学模型,阐述了以工控机和PLC为核心的两种恒体积流控制系统的硬件组成,主要强调了恒体积流在厚度控制系统中的信号采集以及工作原理。
【期刊名称】《有色金属加工》【年(卷),期】2014(000)005【总页数】5页(P60-64)【关键词】恒体积流控制;厚度自动控制;AGC【作者】李铁【作者单位】中铝洛阳铜业有限公司,河南洛阳471039【正文语种】中文【中图分类】TG334.9+3冷轧带材纵向厚度精度是衡量产品质量的重要技术指标。
为了提高厚度控制精度,厚度液压自动控制系统应运而生。
目前,冷轧厚度控制已实现对稳态、加减速、动态变化过程中控制,其中,恒体积流控制模式的实现更具重要意义。
AGC控制

液压AGC控制技术的分析与应用摘要:综述板带轧钢厚度控制技术的发展和产生厚差的原因(主要有:温度、轧制力等)。
着重介绍了液压厚度自动控制的概念、原理、应用等。
关键词:液压AGC;原理;应用第一章液压AGC概念与原理1.1 液压AGC的概念厚度自动控制是通过测厚仪或传感器(如辊缝仪和压头等)对带钢实际轧出厚度进行连续地测量(或估算),并根据实测值与给定值相比较后的偏差信号,借助于控制回路和装置或计算机的功能程序,改变压下位置、轧制压力、张力、轧制速度等,把厚度控制在允许偏差范围之内的方法。
特制品的厚度自动控制在一定尺寸范围内的系统称为厚度自动控制系统,简称为AGC。
液压AGC就是借助于轧机的液压系统,通过液压伺服阀调节液压缸的油量和压力来控制轧辊的位置,对带钢进行厚度自动控制的系统。
1.2板带轧钢产生厚差的原因带钢厚度精度可分为一批同规格带钢的厚度异板差和每一条带钢的厚度同板差。
为此可将厚度精度分解为带钢头部厚度命中率和带钢全长厚度偏差。
从厚差分布特征来看,产生厚差的原因有以下几种: (1)头尾温差,这主要是由于粗轧末出口速度一般比精轧机入口速度要高,因而造成了带钢头部和尾部在空气中停留时间的不同。
( 2)加热炉内导轨在钢胚表面造成的低温段称为水印,由于此段温度变化率大,厚度变动比较“陡”。
(3)活套起套过猛,对带钢产生冲击,使颈部厚度变薄。
( 4 )咬钢时,由于速度设定不协调加上动态速降造成钢套过大,起套并投入高速控制后由于纠偏过快造成带钢拉钢,这一松一紧使厚度减薄,宽度拉窄。
(5)温度波动造成轧制力以及厚度波动。
(6)油膜轴承的油膜厚度发生变化使实际辊缝变化,从而影响轧件厚度。
(7)轧辊偏心将直接使实际辊缝产生高频周期变化。
为了克服或减轻这些干扰因素对成品厚度的影响,除了改进AGC 系统的结构外,还可以将它与各种先进的智能算法相结合,以提高其精度。
1.3液压AGC基本原理1.3.1液压AGC 的设备及其与工作液压AGC技术是将机械、液压、自动控制以及轧制工艺等专业紧密联系在一起的综合先进技术。
铝冷轧机液压厚度自动控制(AGC)系统
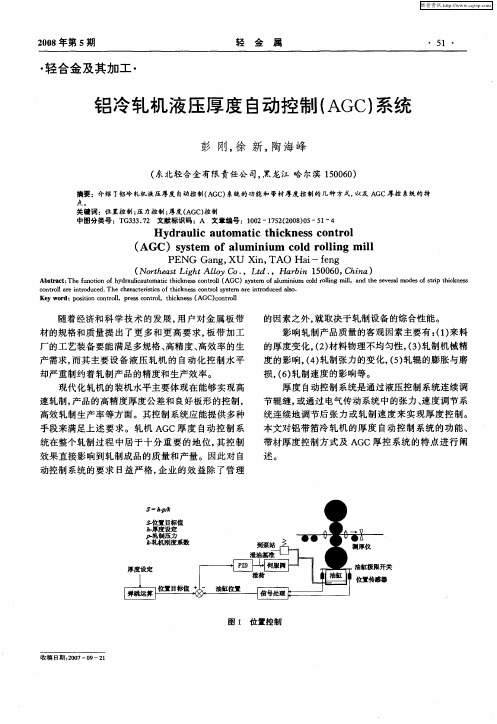
油缸 内或专 门设计 的检 测支座上 。在 轧机 的操 作侧
出 口厚度 相应 的辊 缝 。当给定 了 出 口厚度及 预期 负
载后通 过弹跳 方程 即 可计 算 出 一个 给 定 辊 缝, 并通
和传动 分 别有 两 个 或两 组 传 感 器 获 取 位 置 反 馈 信
号, 然后 把这 两个 信号 加 以平 均 产 生一 个 代表 中央
K yw r : oio nrU rs nrl hcn s AG cnrl e od ps i c t ,pesc t ,ti es( C)o t l t no o o o k o
ri 5 0 0 C ia 6n 1 0 6 , hn )
A s a tT efn t n o y r u cuo t i n s o t l A C)sse o lmi u c l ln b t c : h u o i f da l a tmai t c es n r l( G r o h i ch k c o y tm f u n m dr l g mm,a d tesv rl d s f t pt i n s a i o oi n ea e r c es h e mo o s i h k
厚 度 自动 控制 系统 是通过 液 压控制 系统连 续调 节辊缝, 或通过 电气传动 系统 中 的张力 、 度调 节系 速
产需 求 , 其主 要设 备 液 压 轧机 的 自动 化 控制 水 平 而
厚度控制-AGC

AGC控制系统的原理数学模型及应用综述摘要:本文介绍了AGC在上生产过程中的控制原理,AGC的分类及数学模型,AGC控制系统在生产中的应用和AGC控制技术的发展过程及趋势。
关键词:AGC;控制原理;数学模型;监控1 概述AGC是Automatic Gauge Control System的简称,即所谓的轧机自动厚度控制系统。
是轧机自动化系统中不可缺少的一部分,它控制金属带材厚度精度,使金属带材厚差在限定的标准内,提高金属带材的成品率。
AGC系统的作用有两个:一是辊缝的计算,二是根据产品尺寸结合机架的形变量来调整实际的辊缝值,使之轧制的产品尺寸符合既定要求[1]。
1.1 我国厚度控制技术的发展概况目前我国已经应用的厚度控制系统,可大致分为3种基本类型[2]。
(1) 用测厚仪信号反馈控制轧机压下或轧机入口侧带钢张力的AGC(Automatic Gauge Control)系统。
上个世纪70年代,厚度控制系统大多是这类系统,而且是模拟线路。
按轧机出口侧测厚仪测出的带钢实际偏差信号反馈控制,大偏差或被轧带钢厚度大于0.4mm时,按偏差信号大小去移动压下位置,改变辊缝间距,以减小厚度偏差,即所谓粗调;在小偏差或被轧带钢厚度小于0.4mm时,则调节轧机入口侧带钢张力,进一步减小厚度偏差,即所谓精调。
我国早期的AGC系统调节压下装置的执行机构是电动的,因电动压下响应慢和非线性的缺点,逐渐被液压压下机构代替睁[3]。
(2) 采用前馈控制和测厚仪信号反馈控制轧机压下或轧机入口侧带钢张力的AGC系统。
将上述AGC系统数字化,并增加前馈控制回路就构成这类AGC系统。
前馈控制是当轧机入口侧有厚度偏差的带钢进入轧辊时,立即调节被控机架压下位置,将入口带钢厚度偏差消除的一种控制策略。
方法是将轧机入口侧测厚仪至轧辊中心的距离分成若干整数段,把经过入口侧测厚仪的每段带钢厚度顺序存入移位寄存器中,寄存器按FIFO方式工作,当寄存器输出的带钢段进入轧辊时,系统按该段厚度偏差值调整压下,以消除进入轧机的带钢厚度偏差。
轧机液压自动厚度控制系统要素和构成分析
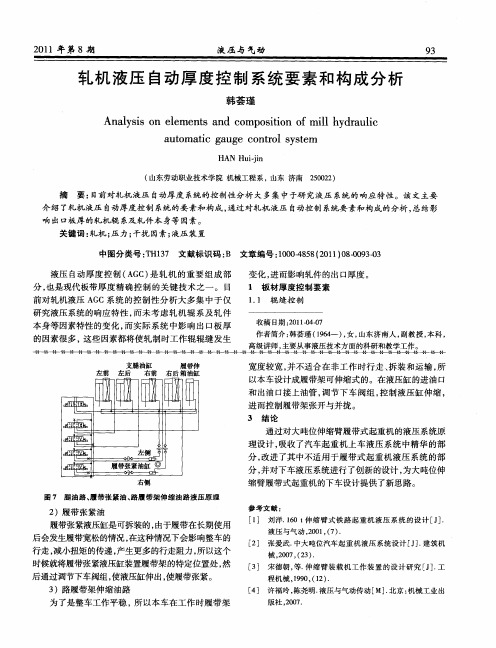
液压与 气动
9 3
轧机 液 压 自动厚 度控 制 系统 要 素 和构 成 分 析
韩荟瑾
An lsso lme t n o o i o fmi y ru i ay i n ee n sa d c mp st n o l h d a l i l c
a t mai a g o to y t m u o tc g u e c n r ls se
1 板 材厚 度控 制 要素
1 1 辊 缝 控 制 . 收稿 日期 :0 10 - 21- 0 47
分, 也是现代板带厚度精 确控制 的关键技术之一。 目 前对轧机液压 A C系统的控制性分析大多集 中于仅 G 研 究 液压 系统 的响 应 特性 , 未 考 虑轧 机 辊 系及 轧 件 而 本身等因素特性 的变化 , 而实际系统 中影 响出 口板厚 的因素很多 , 这些因素都将使轧制时工作辊辊缝发生
I6 秒 流 量 控 制 .
21 0 1年第 8期
辊缝控制是 A C控制的基本内环 , G 它与其他 A C G 模式一起发挥控制作用。辊缝位置的检测有若干种选 择方式及其检测元器件的安装位置 , 位移传感 器可安 装在轧机液压缸上 、 轧机弯辊液压缸 内或专门设计 的 检测支座上 , 还可以将位移传感器安装于缸体中间 , 不
量 和压 力 的调节来 控 制 液压 缸 上 、 移 动 的行 程 来 调 下 节轧辊 辊缝 值 。
压 力控 制是 A C控 制 的第二 个基 本 内环 , G 它也 需 与其他 A C模式一起发挥其控制作用 。具体安装位 G 置在 液压 缸 阀组上 , 压力 传感 器检 测液 压缸 内的压 力 , 经 转 换得 到轧 机轧 制力 反 馈 信 号 , 个 信 号 和压 力 给 这
液压AGC自动厚度控制系统介绍

一、液压AGC自动厚度控制系统简介液压AGC自动厚度控制系统是现代化轧机提高轧制精度必不可少的技术装备,是生产厂家在未来激烈市场竞争中取得优势的重要保证。
公司致力于液压AGC成套技术与装备的研发、推广。
公司建立了多学科相配套的AGC专业体系,可以集液压AGC自动厚度控制系统的设计、开发、制造、安装、调试于一体,为用户提供优质服务。
目前为止,本公司所推出的液压AGC自动厚度控制系统已经应用在国内外上百条冷轧、热轧带钢生产线上,完全可以满足带钢产品厚度的精确控制。
为了保证带钢产品的厚度精度和良好板型,本系统具有液压压下辊缝控制(AGC)、恒轧制压力控制(AFC)、测厚仪监控,对薄规格产品还可采用张力厚度控制等功能。
本系统工作可靠、操作方便、自我保护功能完备,并具有轧制工艺数据库,在轧制不同规格的带材时,只需要调出相应的轧制工艺即可在每次开始轧制以前设置轧制状态。
应用该系统后,冷轧带钢的厚控精度可以达到:0.15±0.003mm、0.3±0.006mm(纵向厚度偏差)二、系统主要控制功能1、辊缝位置闭环控制(APC);2、带钢厚度闭环控制(监控AGC、张力AGC、秒流量AGC、予控AGC);3、辊缝压靠压力设定及辊缝拨零操作;4、轧辊两侧压/抬同步控制;5、辊缝差设定与钢带纠偏控制;6、轧制力设定与报警;7、各项轧制工艺参数的采集、记录、显示和打印为轧制规程的优化提供参数。
三、主要技术性能指标1、辊缝(厚度)设定精度优于0.001mm2、带材厚度控制精度:±1.5~3%h(带钢厚度)本指标与测厚仪以及来料和轧机精度水平有关。
3、系统响应时间: 30-50 ms四、主要设备介绍1、液压泵站液压泵站主要由主液压泵、蓄能器、油箱,司服阀组,减压稳压阀组、循环过滤机构等组成。
2、压下油缸压下油缸采用优质锻造合金钢制作,经过三次无损探伤,以保证缸体的质量;结构采用特殊设计,油封采用进口产品;装有高分辨率的位移传感器以检测油缸的位移。
第9章-轧钢厚度自动控制

材料与冶金学院李振亮课程名称:《材料成型控制工程基础》(第9章,共11章)编写时间:2010 年9月1日内 蒙 古 科 技 大 学 教 案连铸坯 液芯压下顶弯、 拉矫液压摆式切头均热炉高压水除磷 立辊轧边 F1- F6精轧内蒙古科技大学教案内蒙古科技大学教案图9-14 测厚仪型反馈式厚度自动控制系统 图9-15 δh 与δS 的关系曲线h 实—实测厚度;h 给—给定厚度 “压下有效系数”的概念? 由前式可知,当轧机的空载辊缝S0改变δS 时,所引起的轧件出口厚度变化量δS ,δh 与δS 之间的比值C=δh/δS 称为“压下有效系数”,表示压下螺丝位置改变量能造成多大的轧件出口厚度变化量。
h K Mh K M K S mm δδδ)1(+=+= 内 蒙 古 科 技 大 学 教 案GM-AGC工作原理图前馈式厚度自控系统原理”和“厚度计”测厚的反馈式AGC,都无法避免信号传递的滞后,因而限制了控制精度内蒙古科技大学教案图9-21 前馈AGC 控制示意图 图9-22 δh 、δS 、δH 之间的关系曲线H K M H M M mδδ=+) (9-10) 内 蒙 古 科 技 大 学 教 案内蒙古科技大学教案图9-25 入口和出口断面形状内蒙古科技大学教案内蒙古科技大学教案内蒙古科技大学教案图9-31 四辊钢板轧机的受力和变形[40]内蒙古科技大学教案图9-33 带钢良好板形线簇[40]众所周知,轧制压力波动对带钢板形的影响不是太敏感的,带钢愈厚,影响愈为迟钝。
其原因是带钢是一个整体,只要带钢宽度上各点的不均匀纵向延伸产生的内应力不超过一定限度,带钢就不会失去它维持自身平直的稳定状态,带钢愈薄,维持自身平直的能力愈差。
所以保证轧制带钢板形良好的条件,图上表现出来的不是一条直线,而是一个区间,这个区域随板厚增大而变得愈宽,见图图9-34 带钢板形良好区间[40]与区间上限AE的交点E是不产生边部浪形的临界点;塑性线是不产生中部浪形的临界点。
AGC

新型轧机系统是机、电、液、气、仪一体化的大型复杂系统,其结构与功能的复杂性决定了故障机理的复杂性以及故障诊断的困难度。轧机系统高精度与高可靠性要求使故障诊断任务更加艰巨。
这一章根据作者在轧机液压系统设计分析、故障诊断与维修领域的长期实践与积累,对现代新型轧机液压故障的症状、原因,以及故障分析的过程和方法等进行总结与提炼。主要是概括轧机控制系统(AGC系统、CVC系统、弯辊系统、活套系统)的常见故障,整理故障分析的基本思路与程序、列出故障树,并总结出故障症状与原因的关系。同时,也对轧机液压控制故障与产品质量的关系进行分析。上述内容是轧机智能诊断与监测系统的主要专家知识。
4、油缸卡死,驱动电流不为零
5、电气断线,驱动电流为零
3.2 CVC液压故障与分析
3.2.1 CVC液压故障概述
CVC主要故障有:
1) 位置传感器故障。BA给定位置设定信号,CVC油缸位移不到位,主要有:单个位置传感器测量值>极限位,或控制过程中位置传感器输出信号不变,即可能位置传感器故障;同一个辊两个位置传感器位置差|E-A|>5mm,报警;上、下两辊||UP|-|DOWN||>2mm,封锁。可能故障:液压伺服系统零点漂移、油缸卡滞等。分析位移偏差量的变化趋势。
伺服阀寿命性故障 伺服阀零偏电流趋势增大,对零偏电流I趋势分析
伺服阀突发性故障 油缸位置无法控制或偏向某一端,零偏电流突然增大
溢流阀调压力过高 当伺服系统发生故障时,可能引起油缸压力过高
溢流阀调压力过低 当伺服系统发生故障时,可能引起油缸压力过低
溢流阀损坏 压力建立不起,或起不到溢流作用
机械与电气零点不一致 伺服系统驱动零偏电流增大
6) 调节器封锁:系统应符合CVC功能投入条件,如:硬件好,传感器没有故障;开关自动状态;BA硬件好(油库准备好)等。否则调节器封锁。
- 1、下载文档前请自行甄别文档内容的完整性,平台不提供额外的编辑、内容补充、找答案等附加服务。
- 2、"仅部分预览"的文档,不可在线预览部分如存在完整性等问题,可反馈申请退款(可完整预览的文档不适用该条件!)。
- 3、如文档侵犯您的权益,请联系客服反馈,我们会尽快为您处理(人工客服工作时间:9:00-18:30)。
板带箔轧制的厚度自动控制系统金属加工产品广泛应用于建筑业、容器包装业、交通运输业、电气电子工业、机械制造业、航空航天和石油化工等各工业民用部门,其生产和消费水平已成为衡量一个国家工业发达程度的重要标志之一。
作为有色金属加工行业的设计研究单位,洛阳有色金属加工设计研究院早在1989年就自行设计研制出1400mm、1200mm、1300mm、1450mm、800mm 等各型全液压不可逆铝带箔冷轧机,1300mm 可逆铝带坯热轧机,560mm、850mm 全液压可逆铜带冷轧机,以及可逆钢带冷轧机的自动厚度控制配套系统,并积极开展铝板带箔厚度自动控制系统的开发研制工作,在吸收消化国外同类产品先进技术的基础上,先后开发出AGC-Ⅲ型到AGC-Ⅶ型厚度自动控制系统,厚控精度高,系统稳定。
广泛用于铝、铜加工及钢铁加工行业的各类板带箔轧机上,深得用户好评(参见厚控系统用户表)。
板带材在轧制过程中的厚度变化,既与轧件的塑性变形抗力、厚度等因素有关,也与轧制工艺规程及轧机机架的刚度有关,下面对板带材轧制厚度自动控制原理作一简述。
1.弹跳方程和P-H 图 板带轧制过程中轧件作用于轧辊辊系的反作用力使机架发生弹性变形,遵循弹跳方程的规律:K P S h 0+=式中:h — 轧件出口厚度,mm0S — 原始辊缝,mmP — 轧制压力,tK — 轧机刚性系数,t/mm作用于轧件的轧制力,使轧件发生塑性变形,轧件的塑性曲线虽然实际上不是直线,但在板带材轧制过程中塑性曲线处在微量变化情况下,可视为直线,轧件的塑性系数M 则可表示为:M=ΔP/Δh式中:M — 轧件塑性系数ΔP — 轧制力变化量Δh — 轧件的厚度变化利用弹性变形曲线和塑性变形曲线所构成的P-H图(图1-1),可以很方便地用来分析轧件厚度变化原因。
图1-1 弹性塑性变形的P-H图2.影响厚度变化的因素2.1 轧件的尺寸及性能的影响在其他条件不发生变化的情况下,轧件出口厚度的变化与其入口厚度的波动是成正比的,如图2-1所示,如果轧件入口厚度由0HH→,则会产生厚度波动h∆。
入口厚度变化1h∆。
图2-2 轧件性能发生变化时的影响2.2轧机刚度的影响轧制过程中,轧机刚度是会变化的。
轧机刚度的变化(即轧机刚性系数的变化),反映为弹性曲线斜率的变化,如图2-3所示:冷轧带卷时引起轧机刚度变化的主要原因有:(1) 轧件宽度的变化;(2) 轧辊直径和凸度的变化;2.3 辊缝设定原始值变化的影响在轧制过程中,由于轧件尺寸及性能的影响、轧机刚度的变化等一系列因素,需要调整辊缝设定原始值,以实现厚度控制。
如图2-4,辊缝原始值增大,使B 线向右移动,在轧制力1P 点达到轧机平衡状态,从而产生偏差h ∆。
图2-4 辊缝原始值变化的影响空载时,辊缝变化原因如下:(1) 轧辊偏心和不圆;(2) 轧辊热膨胀或收缩;(3) 轧辊磨损;(4) 轧辊弯曲;(5) 上下轧辊中心线交叉;(6) 轧辊轴承油膜厚度的变化;(7) 轧制中润滑膜的变化。
2.4轧制工艺条件的影响前后张力、轧制速度及润滑等轧制工艺条件的变化,将影响轧制压力的大小,从而引起厚度偏差。
张力是以影响变形区的应力状态,改变轧件的塑性变形抗力而起作用的,如图2-2所示,张力增大轧出厚度减小,反之厚度增加,且后张力比前张力影响大。
在生产中,稳定的前张力是卷取的必要条件,为防止断带现象后张力也只能在一定范围内波动。
轧制速度是通过影响摩擦系数、变形抗力及轴承油膜厚度,从而改变轧制压力或辊缝影响出口厚度的。
在冷轧中随着速度的提高使摩擦系数减小,作用于轧件上的应力增大,出口厚度减小。
反之,轧制速度减小,出口厚度增加。
当速度提高时,对于油膜轴承,油膜变厚导致上下轧辊接近,出口厚度变薄。
相反,轧制速度减小,油膜变薄,出口厚度变厚。
油膜厚度与轧制速度的关系,如图2-5所示:2— 3机架连轧机最后机架Φ400/1000×1000mm图2-5 油膜厚度与轧制速度的关系润滑条件的影响,表现在轧制时摩擦系数的变化对出口厚度的影响。
3.厚度自动控制3.1 液压执行机构的闭环控制(内环)位置控制方式和轧制力控制方式是两种最常用厚度自动控制方式,如图3-1所示:选择位置控制方式时,液压缸位置基准信号与位置传感器提供的反馈信号进行比较。
偏差信号经放大等处理后,输入伺服阀,从而控制进入或流出液压缸的流量。
根据传感器的安装位置不同,又可分为油缸位置控制(位置传感器安装于油缸上)和辊缝位置控制(位置传感器安装于工作辊轴承座之间),后者轧机刚度要远远大于前者。
压力控制方式,是由压力基准值与压力传感器或负荷元件提供的反馈信号比较形成压力闭环,如图3-1。
3.2刚度调节系数GMTR在理想状态下轧机机架有无限大的刚度,辊缝将不随来料的厚度或硬度变化而变化,轧件的出口厚度也必然较为均一,但实际轧制时,轧机存在弹跳,。
厚控系统可以通过补偿机架延伸量,达到增加刚度使其超过轧机自然刚度。
下面利用弹跳方程进行分析。
当轧件来料有ΔH的变化,引起轧制压力变化ΔP,不进行补偿时,出口厚度将有如下变化:K P h ∆=∆进行补偿,使出口厚度没有波动Δh=0即 0KP S =∆+∆ 有 GMTR K P S •∆−=°∆式中:GMTR—刚度调节系数辊缝调节量—、°∆∆S S当GMTR=1时,满足Δh=0,但是在实际应用中,因轧辊存在偏心,GMTR 补偿是压力变化的ΔP正补偿,补偿效果使偏心加重,一般通过设置压力死区消除轧辊偏心的影响,GMTR 取小于1的值。
3.3 反馈式自动控制在轧机出口侧安装测厚仪,组成反馈式厚度自动控制系统,简称反馈式AGC 或监控AGC,控制原理如图3-2所示。
图3-2 反馈式自动控制系统在轧件出口侧由测厚仪实际测出厚度h ,并与给定厚度0h 相比较,得到厚度偏差0h h h −=∆如果不为零,AGC 系统有信号输出,去调节压下改变辊缝,或者调节张力、轧机速度直到输出量为零,从而消除了板厚偏差,即所谓的压力AGC、位置AGC 调节、张力AGC 和速度AGC 系统。
由于测厚仪安装在离辊缝一定距离的地方,这样厚度偏差的检测与厚度调节不是在同一时间发生,所以实际轧出厚度的波动不能得到及时反映。
即测量的对象不是辊缝中的板厚,而是到达测厚仪处的板厚,结果使整个调节有一定滞后时间,即hV L t =式中:L—轧辊中心线到测厚仪的距离−h v 轧件的出口速度将测厚仪安装在距离轧辊尽量近的位置,以缩短滞后时间,达到较好的控制效果。
3.4 多级AGC 控制为解决单级AGC 控制时,控制调节器负担过重或饱和的现象,须综合运用各种AGC 控制方式。
一般采用两种方式构成两级控制,即一个作为初级控制器,另一个作为二级控制器,如张力—速度AGC 中,张力为初级控制器,速度为二级控制器。
图3-3 二级AGC 控制结构框图如图3-3所示,二级AGC控制系统工作情况如下:初级控制器是一个厚度偏差反馈控制器,利用比例积分实现,出口厚度偏差信号作为输入信号,根据轧制速度调节增益。
二级控制器同初级控制器类似,也是一个利用比例积分实现的厚度偏差反馈控制器,不同的是以初级控制器输出的溢出部分作为偏差输入信号。
当初级控制器的输出没有超出限幅,二级控制器不被启动,该初级控制器等同于一般的单级AGC控制。
而当初级控制器的输出超限,启动二级控制器,开始二级调节。
两级控制器同时工作,有效地解决了单级的饱和现象,同时缩短了系统调节周期。
常用的多级AGC控制器有张力—压力AGC、压力—张力AGC、张力—速度AGC和速度—张力AGC。
3.5前馈式自动控制反馈式自动控制存在滞后,因而限制了控制精度的进一步提高,特别是轧件来料厚度变化较大时,更会影响轧出厚度的AGC、预控AGC。
控制原理如图3-4所示,在轧件未进入本机架前,利用测厚仪或前一机架测量出其实际入口厚度H,并与给定入口厚度值H相比较,当有厚度偏差H∆,∆时,便估算出可能产生的轧出厚度偏差h∆,从而确定为消除h∆所需要的辊缝调节量S 然后根据该检测点进入本机架的时间和移动S∆所需时间,提前对本机架进行厚度控制,使得厚度的控制点正好就在H∆的检测点上。
H ∆、h ∆和S ∆之间的关系,可以用P-H图进行分析,如图3-5所示。
图3-5 前馈控制P-H分析图该原理实现的关键是如何使调节点和检测点是同一点,如图3-3所示,测厚装置与机架中心线的距离L不变,入口速度也可实时检测,那么轧件从测量点到机架的时间(一般用脉冲数表示)可以确定如下:HV L p = 式中:L—测厚仪到轧辊中心线的脉冲距离—H v 轧件的入口速度,一般根据入口侧偏导辊所加脉冲电机每秒所发出的脉冲数表示因此,可以保证测量点和调节点的一致性。
由于前馈式厚度控制属于开环控制系统,因此其控制效果不能单独地进行检测。
一般将前馈式和反馈式控制系统结合使用。
3.6 质量流控制这一控制方式是根据轧制过程中的运动学特点提出的。
单位时间内通过变形区任一轧件横断面的金属秒流量(体积)相等,即hh X X H H V F V F V F ==一横断面的面积入口、出口、变形区任—、、X h H F F F运动速度一横断面上金属的水平入口、出口、变形区任—、、X h H V V V在实际应用中,轧件横向变形小,通常忽略不计,这样可由上面的等式得出:h H hV HV = H、h— 入口、出口任一横断面得厚度可推出 h V HV h hH −=∆H、h— 入口、出口测厚仪测量的轧件厚度H V 、h V — 入口、出口的速度该式为零时,没有偏差输出信号,不为零时,h ∆为偏差信号,参与厚度控制。
质量流的原理如图3-6所示:3.7张力厚度自动控制系统张力的变化可显著改变轧制压力,从而改变出口厚度。
用调整张力的方法控制厚度,惯性小、反应快且易稳定。
张力AGC是根据精轧机出口侧测厚仪测出的厚度偏差来调节机架间的张力,借以消除厚度偏差的自动控制系统。
张力调节可由两个途径实现:一是根据厚度偏差,调节精轧机的速度:二是调节活套机构的给定转矩,其控制原理如图3-7。
由于张力变化范围小,所以调节范围有限,用于微调。
在轧制过程中,常常采用调节张力和调节压下量配合使用。
3.8偏心补偿轧辊偏心描述的是较复杂的轧机设备缺陷,包括:(1) 工作辊不圆;(2) 支承辊偏心;轧辊偏心引起的轧制力变化,影响带材的纵向公差。
对于轧机刚度小的轧机偏心影响较小,而刚度大的轧机反而影响大。
基本上有以下三种方法减小轧辊偏心的影响:(1) 用轧制力方式控制辊缝;(2) 引入一个死区,在该范围内的辊缝控制不受轧制力变化的影响;(3) 利用傅立叶分析法补偿偏心,如图3-8所示。
图3-8傅立叶分析的轧辊偏心补偿系统由支承辊偏心引起的轧制负荷的变化与支承辊角度的旋转同步发生,后者由安装在支承辊端部的接近开关和工作辊上的脉冲发生器检测。