最新FMEA分析报告
软件需求FMEA分析报告,1200字

软件需求FMEA分析报告软件需求FMEA分析报告一、引言软件需求FMEA(Failure Mode and Effects Analysis)是一种常用的风险分析方法,用于识别软件需求中的潜在故障模式及其对系统的影响。
本报告旨在对某软件需求进行FMEA分析,以识别潜在风险并提出相应的预防措施。
二、FMEA分析过程1. 确定需求首先,我们明确分析的软件需求是什么。
在本次分析中,为了简化,我们选取了一个简单的需求:用户登录功能。
2. 识别潜在故障模式接下来,我们识别可能存在的潜在故障模式。
对于用户登录功能,可能的潜在故障模式包括:用户无法通过用户名和密码登录、系统无反应或崩溃、登录成功但无法访问受限资源等。
3. 评估故障影响程度针对每个潜在故障模式,我们评估其对系统的影响程度。
例如,用户无法通过用户名和密码登录会导致用户无法使用系统的功能,影响程度较高;而系统无反应或崩溃可能导致用户丧失工作进度,影响程度较高。
4. 评估故障发生概率除了影响程度,我们还需要评估每个故障模式的发生概率。
这可以通过历史数据、模拟测试或专家意见等方式获取。
在本次分析中,我们假设用户登录功能的故障发生概率较低。
5. 计算风险优先级数值根据故障影响程度和发生概率的评估结果,我们可以计算每个故障模式的风险优先级数值。
通过将影响程度乘以发生概率,我们可以对故障模式进行排序,以便后续处理。
6. 提出预防措施根据故障模式的风险优先级数值,我们可以确定需要采取的预防措施。
对于风险优先级较高的故障模式,我们可能需要采取更多的预防措施,例如增加输入校验、加强系统稳定性等。
三、分析结果和预防措施经过上述分析过程,我们得到了用户登录功能的FMEA分析结果如下:1. 用户无法通过用户名和密码登录风险优先级数值:高预防措施:增加输入校验、使用强密码策略、添加登录重试机制等。
2. 系统无反应或崩溃风险优先级数值:高预防措施:加强系统稳定性、进行性能测试、增加异常处理等。
fmea报告模板

FMEA报告模板1. 引言故障模式与影响分析(Failure Mode and Effects Analysis,简称FMEA)是一种系统性的方法,用于识别和评估潜在的故障模式,并预测它们可能引起的影响。
本报告旨在提供一个FMEA报告模板,以便团队能够按照一致的结构和标准进行FMEA分析,并记录所得出的结果。
2. FMEA分析流程2.1 确定FMEA的范围在开始FMEA分析之前,需要明确定义FMEA的范围。
确定范围时,需要明确产品或过程的边界,以便团队可以集中精力进行分析。
2.2 识别故障模式在这一步骤中,团队需要列出所有可能的故障模式。
这些故障模式可以通过多种途径获得,包括过去的经验、相关文献和专家意见等。
2.3 评估故障影响对于每个故障模式,团队需要评估其可能引起的影响。
这些影响可以包括安全风险、质量降低、生产停止、客户满意度下降等。
2.4 确定故障原因在这一步骤中,团队需要分析每个故障模式的根本原因。
通过识别原因,团队可以采取相应的预防措施来减少故障的发生。
2.5 评估现有控制措施团队需要评估现有的控制措施,以确定它们对于减轻故障影响和预防故障的效果。
如果控制措施被认为不足或不可靠,团队需要考虑采取额外的措施。
2.6 制定改进措施根据之前的分析结果,团队需要制定改进措施,以降低故障模式的发生概率或减少其影响。
这些措施可以包括工艺改进、设计修改、培训和培训等。
2.7 实施改进措施在这一步骤中,团队需要实施之前制定的改进措施,并监控其效果。
必要时,可以进行调整和再次评估。
3. FMEA报告模板以下是一个FMEA报告的模板,可以根据实际情况进行调整:3.1 项目信息•项目名称:•项目编号:•项目负责人:•报告日期:3.2 FMEA范围•产品/过程边界:•分析目的和要求:3.3 FMEA分析团队•团队成员及职责:3.4 故障模式识别3.4.1 故障模式1•故障模式描述:•潜在原因:•潜在影响:•现有控制措施:•建议改进措施:3.4.2 故障模式2•故障模式描述:•潜在原因:•潜在影响:•现有控制措施:•建议改进措施:…3.5 故障影响评估•故障模式1影响评估:•故障模式2影响评估:•…3.6 故障原因分析•故障模式1原因:•故障模式2原因:•…3.7 现有控制措施评估•故障模式1现有控制措施评估:•故障模式2现有控制措施评估:•…3.8 改进措施制定•故障模式1改进措施:•故障模式2改进措施:•…3.9 改进措施实施•故障模式1改进措施实施情况:•故障模式2改进措施实施情况:•…4. 结论根据以上的FMEA分析结果,团队可以得出结论,并提出进一步的建议和行动计划。
FMEA分析报告

FMEA分析报告FMEA(Failure Mode and Effects Analysis)是一种系统性的风险评估方法,常用于分析产品或过程中的潜在问题和可能的影响。
这篇报告将介绍FMEA分析的目的,步骤和优势,并通过一个实例进行详细说明。
一、FMEA分析的目的二、FMEA分析的步骤1.确定分析的范围:明确需要分析的产品或过程的范围和目标。
2.收集团队:组建一个多学科的团队,包括设计人员、工程师、生产人员等。
3.识别潜在的故障模式:对产品或过程进行详细审查,识别可能出现的故障模式。
4.评估故障的严重程度:分析每个故障模式可能引发的后果,评估其对产品性能和安全性的影响。
5.评估故障发生的可能性:分析每个故障模式发生的概率或频率,并将其与已有的统计数据或历史记录进行比较。
6.评估故障的检测能力:评估现有的探测和防范措施对于检测和防止故障的效果。
7.计算风险优先级:根据故障的严重程度、发生可能性和检测能力计算每个故障模式的风险优先级,确定应优先处理的故障模式。
8.制定改进措施:根据风险优先级,制定相应的改进措施,减少或消除故障的可能性和后果。
9.实施改进措施:将改进措施应用到产品设计或过程中,确保其有效性和可持续性。
10.监控和追踪效果:通过定期监测和追踪,评估改进措施的效果和持续性,并根据需要进行调整和改进。
三、FMEA分析的优势1.预测潜在问题:通过系统性的分析,FMEA能够预测产品或过程中可能出现的问题,并提前采取措施避免或降低潜在的风险。
2.提高产品质量:通过识别并改进潜在问题,FMEA能够改善产品的质量和可靠性,提高顾客满意度。
3.降低故障率和维修成本:通过消除或减少故障的可能性,FMEA能够降低产品或过程的故障率和维修成本。
4.加强团队协作:FMEA需要一个多学科的团队进行分析和讨论,促进了团队成员之间的协作和沟通。
5.持续改进:FMEA是一个持续改进的过程,通过监测和追踪改进措施的效果,不断优化和改进产品或过程。
产品设计fmea报告

产品设计fmea报告一、概述本报告旨在对产品设计过程中的潜在风险进行分析和评估,以指导设计团队制定相应的风险控制措施。
通过采用FMEA(Failure Mode and Effects Analysis)方法,我们对产品设计中可能出现的失效模式、失效影响和失效严重程度进行了详细研究,以及风险优先级的排序和风险控制建议的提出。
本报告旨在为产品设计团队提供有力依据,促进产品设计过程的高质量和安全性。
二、FMEA分析过程2.1 分析团队本次FMEA分析由产品设计团队成员组成的跨职能小组进行。
小组成员包括设计工程师、品质控制专家和生产工艺专家。
2.2 分析范围本次FMEA分析的范围涵盖了产品设计阶段的所有活动,包括需求分析、概念设计、详细设计和设计验证。
2.3 FMEA工具我们采用了FMEA表格进行分析,表格的内容包括失效模式、失效影响、失效严重程度(S)、发生概率(O)、探测能力(D)、风险优先级(RPN)和风险控制建议。
2.4 分析方法我们按照以下步骤进行FMEA分析:1. 识别失效模式:团队成员通过头脑风暴和借鉴类似产品的经验来识别可能的失效模式。
2. 评估失效影响:团队成员评估每个失效模式对产品性能、客户满意度和安全性等方面的影响。
3. 评估失效严重程度(S):根据失效影响的严重程度,我们对每个失效模式进行了权重评分。
4. 评估发生概率(O):团队成员根据经验和数据,评估每个失效模式的发生概率。
5. 评估探测能力(D):团队成员评估探测到失效模式的概率,并考虑到各种测试和检查方法的可靠性。
6. 计算风险优先级(RPN):根据S、O和D的评估结果,计算每个失效模式的RPN值。
7. 提出风险控制建议:根据RPN值和团队的专业知识,提出相应的风险控制建议。
2.5 分析结果经过团队的共同努力,我们完成了FMEA分析,并得到了以下结果:失效模式失效影响S O D RPN 风险控制建议模块失效导致整个产品无法工作产品无法正常工作10 5 8 400 设计冗余措施,提高模块可靠性设计尺寸偏差超出允许范围产品无法装配或安装8 6 9 432设计合理的公差,严格控制生产过程产品设计不符合安全标准安全隐患,可能导致事故发生9 4 7 252 与安全专家合作,确保产品符合相关安全标准... ... ... ... ... ... ...三、风险控制建议基于上述FMEA分析结果,我们提出了以下风险控制建议:1. 设计冗余措施:在产品设计中引入冗余,通过多个模块的备份实现高可靠性,即使一个模块失效,其他模块仍然能继续工作。
FMEA潜在的失效模式与后果分析报告
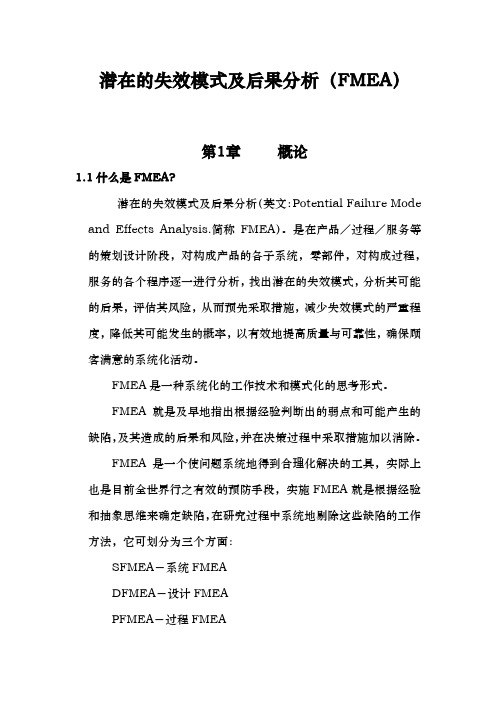
潜在的失效模式及后果分析(FMEA)第1章概论1.1什么是FMEA?潜在的失效模式及后果分析(英文:Potential Failure Mode and Effects Analysis.简称FMEA)。
是在产品/过程/服务等的策划设计阶段,对构成产品的各子系统,零部件,对构成过程,服务的各个程序逐一进行分析,找出潜在的失效模式,分析其可能的后果,评估其风险,从而预先采取措施,减少失效模式的严重程度,降低其可能发生的概率,以有效地提高质量与可靠性,确保顾客满意的系统化活动。
FMEA是一种系统化的工作技术和模式化的思考形式。
FMEA就是及早地指出根据经验判断出的弱点和可能产生的缺陷,及其造成的后果和风险,并在决策过程中采取措施加以消除。
FMEA是一个使问题系统地得到合理化解决的工具,实际上也是目前全世界行之有效的预防手段,实施FMEA就是根据经验和抽象思维来确定缺陷,在研究过程中系统地剔除这些缺陷的工作方法,它可划分为三个方面:SFMEA-系统FMEADFMEA-设计FMEAPFMEA-过程FMEA1.2 FMEA的历史世界上首次采用FMEA这种概念与方法的是在20世纪60年代中期美国的航天工业。
进入70年代,美国的海军和国防部相继应用推广这项技术,并制订了有关的标准。
70年代后期,FMEA被美国汽车工业界所引用,作为设计评审的一种工具。
1993年2月美国三大公司联合编写了FMEA手册,并正式出版作为QS9000质量体系要求文件的参考手册之一,该手册于1995年2月出版了第2版。
1994年,美国汽车工程师学会SAE发布了SAE J1739-潜在失效模式及后果分析标准。
FMEA还被广泛应用于其他行业,如粮食、卫生、运输、燃气等部门。
1.3 为什么要进行FMEA?工程中大量的事实证明,由于策划设计阶段疏忽,分析不足,措施不够,以至造成产品/过程/服务等投入运行时严重程度不同的失效,给顾客带来损失,甚至产生诸如“挑战者”号航天飞机爆炸的惨痛事故。
fame潜在风险分析报告

fame潜在风险分析报告
FMEA可以描述为一组系统化的活动,其目的是:
(a)认可并评价产品过程中的潜在失效以及失效的后果:
(b)确定能够消除或减少潜在失效发生机会的措施;
(c)将全部过程形成文件。
FMEA是对确定设计或过程必须做那些事情才能使顾客满意这一过程的补充。
所有的FMEA都关注设计,无论是产品设计或者是过程设计。
在进行FMEA时有三种基本的情形,每一种都有其不同的范围或关注焦点:
情形1:新设计、新技术或新过程。
FMEA的范围是全部设计、技术或过程。
情形2:对现有设计或过程的修改(假设对现有设计或过程已有FMEA)。
FMEA的范围应集中于对设计或过程的修改、由于修改可能产生的相互影响以及现场的历史情况。
情形3:将现有的设计或过程用于新的环境、场所或应用(假设对现有设计或过程已有FMEA)1>.FMEA的范围是新环境或场所对现有设计或过程的影响。
失效模式分析(FMEA)心得报告

失效模式分析(FMEA)心得報告----報告人紀志龍一、FMEA導入的步驟:1.研究PROCESS/PRODUCT2.BRAINSTORM可能失效模3.列出每一失效模式潛在結果4.Assign嚴重度分數5.鑑定每一失效模式之原因6.Assign發生度分數7.鑑定目前偵測失效模式8.Assign難檢度分數9.計算RPN(先其風險評估)10.決定失效模式優先順序11.採取矯正行動12.重新計算RPN二、FMEA製作時機1.原型樣品前2.試產前3.產品製程變異4.製程不穩定/或能力不足三、FEMA用途1.是一種分析技術2.認明產品設計或製程上可能不良模式3.評估缺點對客戶的可能影響4.認明缺點對客戶的可能影響5.認明產生該不良模式之可能原因6.認明有關之重要製程變數7.研訂改善措施8.建立預防管制方法四、FMEA表格(上課實習內容、主要針對加油站的設立所產生的FEMA並加以預防)※R PN直愈大表示潛在風險愈高,第10項計畫之後也是回歸到矯正行動,一直到RPN 值降到最低為止。
五、結論課程中談到我們可以透過RPN、製定行動方案、降低失效模式;但QS-9000認證系統可能停止運作,改由ISO/TS 16949替代,目前是台積電最早申請通過,未來所有汔車零件相關產業都會要求通過此認證,因此他們也建議若要申請QS-9000系統倒不如直接申請ISO/TS 16949,因為ISO/TS 16949是由QS-9000(APQP、SPC、MSA、PPAP、FMEA、QSA)加上生產者特定要求及歐洲VDA-VOLUMES所組成,其內容較QS-9000更完整更詳細,也由於FEMA 太深還有許多地方不能詳盡敘述,可能須導入試RUN才能了解,未來公司也不排除申請ISO/TS 169469 ,若要實際導入建議須有專案專責負責人才行。
--完畢。
FMEA学习心得及报告

F M E A 学习报告及心得一、 FMEA 学习报告:●FMEA 可分为 DFMEA,PMFEA 等等● FMEA 实行的必需条件:需要管理者的支持与督查.由于 FMEA 实行是一个多方谈论的活动并要大批时间与资源。
设计可分为产品设计与过程设计,FMEA 都关注这两设计,它是一组系统化的活动,FMEA目的:①发现和谈论产品与过程(制造过程,装置过程)潜伏的功能无效及其可能发生的结果;②找寻除掉和减少潜伏的功能无效发生的机遇;③将整个子系统(定议顾客的产品为系统)设计过程与设计过程文件化,满足系统过程的增补; DFMEA● DFMEA是一种解析技术,是一个解析小组(不是个人)是要在设计的先期阶段发生的,在产品图纸发放从前完成,最后作为产品的评审标准.如整个产品开发各个阶段若有改正时要及时更正.以致产品无效的基本要素:①内部系统/子系统/零件间互相干涉;②内部系统/子系统/零件与环境互相作用;③使用一段时间后零零件的磨损;④制造差异;⑤顾客使用;●DFMEA 的作用:①鉴别潜伏或现存的功能失郊模式并评估影响的严重等级;②帮助鉴别功能无效模式,并基于无效结果严重度的排序,优先关注严重高的无效模式;③帮助鉴别功能无效的体系和原由;●DFMEA 前的输入:在准备 DFMEA从前需要采集表述设计企图的文件:①顾客要求-------QFD(质量功能睁开);②整个产品要求,将顾客感性的描述转变为技术指标,确认设计要求;③已知的产品要求;④制造、装置、服务和回收再利用的要求●DFMEA 输出 ;①设计考据计划(DVP ) ;②列出潜伏的要点特征和重要特征;③列出“预防设计错误”与“探测设计错误”的设计控制,此中预防是一种方法,探测是一个动作;●DFMEA 规则: (重要 )①DFMEA 时要假设所有零零件可以依照图纸和规范制造出来的。
侧重在设计过程的控制。
,②DFMEA只考虑设计和资料规范相关的问题。
制造过程相关问题或资料错误平时在PFMEA 中考虑如零零件来料不良不是DFMEA考虑的.③特别要点的是,所选定系统的每个零件一定被完全解析。
- 1、下载文档前请自行甄别文档内容的完整性,平台不提供额外的编辑、内容补充、找答案等附加服务。
- 2、"仅部分预览"的文档,不可在线预览部分如存在完整性等问题,可反馈申请退款(可完整预览的文档不适用该条件!)。
- 3、如文档侵犯您的权益,请联系客服反馈,我们会尽快为您处理(人工客服工作时间:9:00-18:30)。
潜在失效模式和效应分析(FMEA)☐系统☐设计☐过程
系统/ 子系统/ 零部件/ 项目名称:责任者:编号:
生效日期:页码:第页/ 共页型号/类型:编制者:
核心小组:FMEA日期(制定) 修订
专业文档
严重度(Severity)
专业文档
频度(Occurrence)
专业文档
专业文档
探测度(Detection)
专业文档
专业 文档
1、最困难的事就是认识自己。
20.11.311.3.202012:0312:03:04Nov-2012:03
2、自知之明是最难得的知识。
二〇二〇年十一月三日2020年11月3日星期二
3、越是无能的人,越喜欢挑剔别人。
12:0311.3.202012:0311.3.202012:0312:03:0411.3.202012:0311.3.2020
4、与肝胆人共事,无字句处读书。
11.3.202011.3.202012:0312:0312:03:0412:03:04
5、三军可夺帅也。
Tuesday, November 3, 2020November 20Tuesday, November 3, 202011/3/2020
6、最大的骄傲于最大的自卑都表示心灵的最软弱无力。
12时3分12时3分3-Nov-2011.3.2020
7、人生就是学校。
20.11.320.11.320.11.3。
2020
年11月3日星期二二〇二〇年十一月三日 8、你让爱生命吗,那么不要浪费时间。
12:0312:03:0411.3.2020Tuesday, November 3, 2020
亲爱的用户: 烟雨江南,画屏如展。
在那桃花盛开的地方,在这醉
人芬芳的季节,愿你生活像春天一样阳光,心情像桃花一样美丽,感谢你的阅读。