工厂制程
制程简介

一、洁净室一般的机械加工是不需要洁净室(clean room)的,因为加工分辨率在数十微米以上,远比日常环境的微尘颗粒为大。
但进入半导体组件或微细加工的世界,空间单位都是以微米计算,因此微尘颗粒沾附在制作半导体组件的晶圆上,便有可能影响到其上精密导线布局的样式,造成电性短路或断路的严重后果。
为此,所有半导体制程设备,都必须安置在隔绝粉尘进入的密闭空间中,这就是洁净室的来由。
洁净室的洁净等级,有一公认的标准,以class 10为例,意谓在单位立方英呎的洁净室空间内,平均只有粒径0.5微米以上的粉尘10粒。
所以class后头数字越小,洁净度越佳,当然其造价也越昂贵(参见图2-1)。
为营造洁净室的环境,有专业的建造厂家,及其相关的技术与使用管理办法如下:1、内部要保持大于一大气压的环境,以确保粉尘只出不进。
所以需要大型鼓风机,将经滤网的空气源源不绝地打入洁净室中。
2、为保持温度与湿度的恒定,大型空调设备须搭配于前述之鼓风加压系统中。
换言之,鼓风机加压多久,冷气空调也开多久。
3、所有气流方向均由上往下为主,尽量减少突兀之室内空间设计或机台摆放调配,使粉尘在洁净室内回旋停滞的机会与时间减至最低程度。
4、所有建材均以不易产生静电吸附的材质为主。
5、所有人事物进出,都必须经过空气吹浴(air shower) 的程序,将表面粉尘先行去除。
6、人体及衣物的毛屑是一项主要粉尘来源,为此务必严格要求进出使用人员穿戴无尘衣,除了眼睛部位外,均需与外界隔绝接触(在次微米制程技术的工厂内,工作人员几乎穿戴得像航天员一样。
) 当然,化妆是在禁绝之内,铅笔等也禁止使用。
7、除了空气外,水的使用也只能限用去离子水(DI water, de-ionized water)。
一则防止水中粉粒污染晶圆,二则防止水中重金属离子,如钾、钠离子污染金氧半(MOS) 晶体管结构之带电载子信道(carrier channel),影响半导体组件的工作特性。
工厂管理的IPQC制程控制

工厂管理IPQCIPQC(InPut Process Quality Control)中文意思为制程控制,是指产品从物简介(属品质保证部)1.负责首检和部分过程检查、制程中的确认,标识及统计;2.负责巡检,对整个生产过程物料使用、装配操作、机器运行、环境符合性等全方位的定时检查确认。
3.IPQC一般是首检、巡检和抽检;是制程中巡回流动检验;属品质保证部管理.生产过程检验(IPQC):一般是指对物料入仓后到成品入库前各阶段的生产活动的品质控制,即Input Process Quality Control。
而相对于该阶段的品质检验,则称为FQC(Final Quality Control)。
① 过程检验的方式主要有:a. 首件自检、互检、专检相结合;b. 过程控制与抽检、巡检相结合;c. 多道工序集中检验;d. 逐道工序进行检验;e. 产品完成后检验;f. 抽样与全检相结合;② 过程品质控制(IPQC):是对生产过程做巡回检验。
a. 首件检验;b. 材料核对;c. 巡检:保证合适的巡检时间和频率,严格按检验标准或作业指导书检验。
包括对产品质量、工艺规程、机器运行参数、物料摆放、标识、环境等的检验; d检验记录,应如实填写。
③ 过程产品品质检验(FQC):是针对产品完工后的品质验证以确定该批产品可否流入下道工序,属定点检验或验收检验。
a. 检验项目:外观、尺寸、理化特性等;b. 检验方式:一般采用抽样检验;c.不合格处理;d.记录;④ 依据的标准:《作业指导书》、《工序检验标准》、《过程检验和试验程序》等等。
品质检验方法1、全数检验:将送检批的产品或物料全部加以检验而不遗漏的检验方法。
适用于以下情形:① 批量较小,检验简单且费用较低;② 产品必须是合格;③ 产品中如有少量的不合格,可能导致该产品产生致命性影响。
2、抽样检验:从一批产品的所有个体中抽取部分个体进行检验,并根据样本的检验结果来判断整批产品是否合格的活动,是一种典型的统计推断工作。
浅谈晶圆代工厂制程节点和应用

浅谈晶圆代工厂制程节点和应用显示驱动芯片(DDIC)是显示面板制造中的一个关键部件。
通常,无晶圆厂IC设计公司(如联咏科技、奇景光电和LX Semicon)设计DDIC,在半导体晶圆代工厂中采用不同的制程节点(以微米[µm]或纳米[nm]为单位)制造IC芯片。
晶圆代工厂作为原始设备制造商(OEM)与IC公司合作,或为分包商制造关系。
之后,IC封装和测试公司完成DDIC的后道工序。
然后,DDIC被交付给显示面板厂商,将IC粘合在面板上,实现显示信号驱动功能。
DDIC通常以带载封装(TCP)形式包装和运输。
图1显示了LCD面板和DDIC之间的关系。
图1:LCD面板和DDICSource: ChipMos显示面板的分辨率通常以像素和子像素的形式出现。
例如,FHD面板意味着分辨率为1920×1080,而4K或超高清(UHD)面板意味着分辨率为3840×2160。
3840表示X轴,而2160表示Y轴。
3840×2160分辨率表示面板有3840×2160(8,294,400)个像素。
每个像素有三个子像素(红、绿、蓝)。
因此,面板总共有3840xRGBx2160(2490万)个子像素。
像素和子像素构成了分辨率。
DDIC的功能是驱动这些子像素的显示信号。
因此,分辨率和每颗DDIC的信道数(pin)决定了每片面板中DDIC的数量,而不一定由面板尺寸决定。
当涉及到DDIC规格时,面板的分辨率是最关键的因素。
在制造DDIC时,晶圆代工厂的制程节点是最关键的因素。
DDIC通过不同的粘合技术被粘合在面板边缘,如COG (chip-on-glass)和COF (chip-on-film)。
柔性OLED面板也采用COP (chip-on-plastic)方式,如图2所示。
图2:DDIC的COG、COF和COP粘合Source: Omdia由于分辨率是以X轴和Y轴形式出现的,所以有几种驱动IC:源极驱动芯片(Source driver IC):它驱动X轴上的信号,也被称为source端或column端。
如何建立工厂建厂九大流程

如何建立工厂(建厂九大流程)在中国,工厂建设项目主要细分为以下阶段和步骤,需要说明的是,其中不少步骤往往是同步进行的,项目成功的关键因素之一就是项目管理和协调。
1\前置审批主要包括:工厂项目立项备案、用地、选址及环境评审、获取土地使用证及规划审批等这几项内容其中部分是可以同步进行的,大部分地区的具体操作流程基本大同小异,部分地区可能会在具体细节上顺序及操作方式会有所不同。
买地建厂投资流程:签订投资意向或合资合作意向书、工商注册(工商行政管理局)、企业名称预先核准申请表、公司具体名称、股东名称、出资总额、出资比例(如股东是法人,需带营业执照副本复印件)、验资证明、环保证明、房产证明项目备案(计划局、发改委):编制项目简介、填写项目申请备案表、项目备案请示、企业法人营业执照正副本复印件、组织机构代码证复印件相关手续办理(环保局、建设局、土地局):环保评审∕审批、选址意见书、建设用地规划许可证、地质灾害评估报告、土地评估、建设用地勘测定界报告、建设用地预审办理土地证(土地局):地籍调查表、用地申请及法人身份证复印件、公司章程及营业执照、国土资源局规划股出图意见、建设部门一证一书、环保证明、一书四方案、土地评估工厂选址在全球范围内对许多制造业企业所作的调查表明,企业认为下列因素是进行设施选址时必须考虑的:1、地理位置、当地各项成本及原材料和成品运输成本;2、劳动力的获取条件及雇员生活环境质量;3、与市场或客户的接近程度及服务的便利程度;4、与供应商和生产制造资源的接近程度和便利程度;5、政策优势及当地其它软环境。
6、越来越多的投资者关注风水和运势工厂风水工厂是商业用,以商为用当然要以财为主,如果你找的厂房财不旺,如何能发财?不旺财还劫财那你可就惨了从年年出口的外贸顺差,到中国惊人的外汇储备。
从世界产品中国造,到全世界国家都说中国强大起来了。
支撑这一切繁荣的是几千万家大大小小的工厂。
这种繁荣的景象无疑催生了更多的工厂,每天有上千家的工厂开业,也有几百家工厂倒闭关门,有几百家在苦苦支撑,到现在,能从激烈的市场竟争中走出来的工厂是幸运的,随着中国产品对国外市场所占的比例越来越高,一些国外商家与媒体对中国产品的反面炒作,抓住一些问题产品大做文章,使进口国加强了对中国产品的检验,国内相关部门也加强了对生产产品的质量监管,使中小企业的生存发展空间变小,市场竟争越来越激烈。
工厂产品制程异常处理及改善--课件
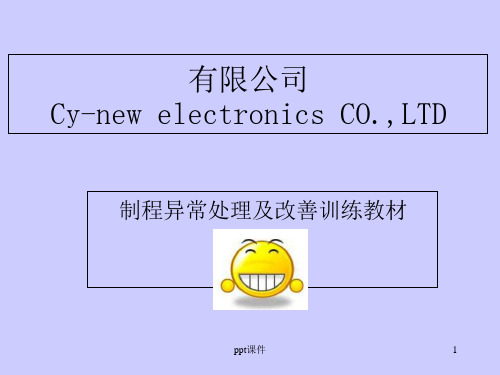
首先,要有稳定的人员
人员的流动高低,往往可以反映员工对企业的认同程度,尤 其高人员流动率的企业,一切成长的条件都会随着人员的流动而 流失。品质也是如此。
新进的员工
工作熟练度低
对机器,工具不了解
对材料不了解
造成太多变因存在
对作业方法不熟练
对品质 p求t课不件认识
8
其次,要有良好的教育训练
现代的企业管理讲究的是多元的专业化,每一项工作均有它的 专业知识及理论基础,如何将这此专业知识及理论基础演化为实 用的技巧,则需要由具有理论基础及专业经验的人来进行,也才 能尽快地填补企业内成员工作经验的不足及理念上的差异造成的 沟通协调的困难。
c,进料不良,前工 程之不良品纳入本工程 中。
3
第二部分:制程异常来源及分类
1,制程异常的来源
任何一个与产品有关的因素变动,产品也就随之 变动,因素变动的大小,产品的特性也随之大小而变 动。总体来讲,影响产品制程异常出现的因素有人, 机器,材料,方法,环境与管理六个方面。
以下,分别举例讲述:
a,异常来源之一
• 材料 (Material) 今品级对吗? 今数量对吗? 今品牌对吗? 今有杂质吗? 今存货适当吗? 今有浪费吗?
• 方法 (Method) 今标准适当吗? 今标准有修订吗? 今安全吗? 今能确保品质吗? 今工作程序适当吗? 今温度、湿度、照明适当吗?
今存放方式适当吗?
今前后工程协良好吗?
ppt课 件
b.不良情报立即回馈并采取改善行动:当发现不良时,应 立即要求前一制程的作业者注意,请其确认不良事实,并请其立 即改善。若前一制程的作业者不改善加工方法,则不良绝不会消 失,则生产线不可再继续生产,否则顺次检查将失效。生产线的 停止,可使管理人员及时发现制程的问题,并采取有效措施处理, 同时可警惕作业者,增强责任感。
制程检验管制程序009(工厂类文件)

2
OF
程初件检验记录》表上,经品保主管核定后方可大批量生产. 5.1.2 现场作业员依“作业指导书”对自已作业的产品进行自主检查。 5.1.3 生产线对电测工站和终检工站设立 100%全检并将结果记录于《电气不良 SPC 表》和《外观 P-管制表》上,由制程品管对不良品进行原因分析,要求产线改善。 5.1.4 IPQC 每节依《测试仪器功能查检表》对测试机功能进行查检,并将结果记录于《测试仪器 功能查检表》上,有异常及时通知工务维修。 5.1.5 制程品管依“制程检验规范” “工程蓝图”对制程每一工站每 2H 巡回一次,并将结果记录 于《制程品管日报表》上。 5.1.6 IPQC 将《电气不良 SPC 表》和《外观 P-管制表》一周内汇总于《线每周不良汇总表》上, 并针对不良率最高的项目或同一问量题点连续出现三次时由负责人进行原因分析及改善对策。 5.2 制程异常处理 5.2.1 现场作业员在自主检查时发现异常应立即通知线长或 IPQC 或相关人员处理. 5.2.2 制程巡检员 IPQC 在巡检中发现品质异常时应立即通知现场作业员停止作业,并将不良情 况告知线长,若为重大异常或批量不良时,则要求产线立即停止生产并填写“纠正及预防措施” 单交主管审核后再交生产主管签认后由责任单位在 72 小时内回复, 待引发不良因素彻底排除后 方可继续生产,若为批量性不良或不良率超过 5%以上, “纠正及预防措施”单则须经经理核准, 具体办法依《纠正与预防措施管制程序》中之作业。 5.2.3 现场作业员及 IPQC 检验出之不良品依《不合格品管制程序》处理。 6.0 记录: 制程初件检验记录 测试仪器功能查检表 制程品管日报表 线每周不良汇总表
XXX 电子有限公司
文件发放/更改审批表 DOCUMENT ISSUE/CHANGE APPROVAL SHEET
外协SMT工厂制程稽核报告
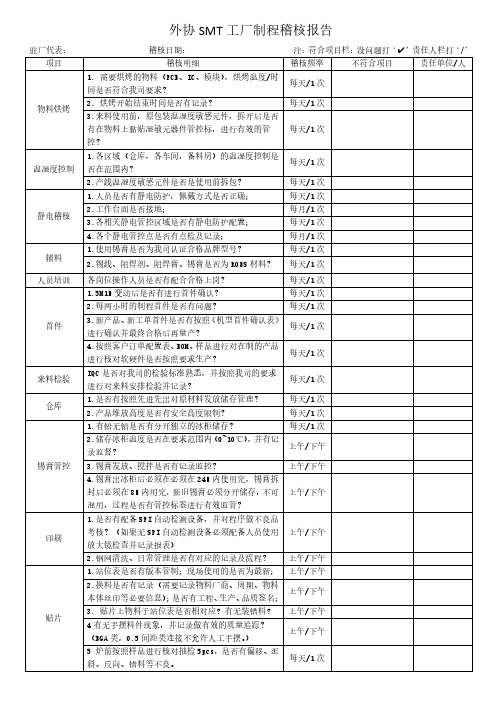
每天/1 次
每月/1 次 每天/1 次 每天/1 次 每天/1 次 上午/下午 上午/下午 上午/下午
上午/下午
上午/下午
上午/下午 上午/下午 上午/下午 上午/下午
上午/下午
上午/下午
上午/下午
每天/1 次
每天/1 次 每天/1 次 每天/1 次 每天/1 次
每月/1 次
每月/1 次 每天/1 次 首件确认 每周/1 次 上午/下午
4 有无手摆料件现象,并记录做有效的质量追踪? (BGA 类,0.5 间距类连接不允许人工手摆。)
上午/下午
5 炉前按照样品进行核对抽检 5pcs,是否有偏移、歪 每天/1 次
斜、反向、错料等不良。
回流焊 AOI/QC
分扳 条码/喷码 下载/烧录
校准 后焊接
测试 维修 出货
回流焊炉温曲线是否每天都有测量(实板测试,炉温 实际测试必须有 5 个以上的测试点数据)?线别?生 产机型? 炉温测试仪器的外校期限是否在有效范围? 1. AOI 程序是否与投产机种及版本相符? 2.良品与不良品是否有区分/标识? 3. AOI 是否能覆盖全部组件? 4.报表记录是否真实准确? 1.分板程序是否与机型一致? 2.工厂每天是否有对分板后的 PCBA 质量进行确认? 3.确认实际的分板质量,分板治具设计是否对 PCBA 上的零件有干涉?分板后是否有毛边及露铜不良? 1.条码/喷码内容、格式、位置是否按照我司要求及订 单要求执行? 2.条码内容及发放使用的正确性是否有记录并监管? 1.工厂是否有对生产使用的软件做有效的监控记录? 2.确认实际使用的软件是否正确? 3.工位是否有对应 SOP 文件? 1.平台勾选项目是否按照我司要求文件勾选?校准配 置文件是否正确并有记录? 2.电脑、校准仪器、测试夹具是否有进行编码,并按 照我司要求写入到每片 PCBA 中以便异常追朔? 3.使用万用表实际测试实际输出电压是否与要求一 致? 1.后焊物料位置与用料是否与 BOM 要求一致,并有上 料确认记录? 2.焊接后的焊剂残留是否有进行清洁? 3.焊接上锡情况是否按照我司的外观检验标准执行? 1.测试工位是否有功能测试指导书? 2.是否有进入系统抽检岗位?异常是否有及时解决? 3.室内 GPS 放大器是否有对实际的频率进行按照室外 信号值进行点检? 4.仪器、电源、测试架是否有进行保养点检及校准? 5.RF 焊接点是否有使用万用表进行测试并记录? 6.副板是否有测试? 1.烙铁作业温度是否符合规定 2.维修记录是否真实,工厂是否有异常反馈机制? 1.外箱标签是否完善,与实物是否相符? 2.包装方式是否符合我司要求? 3.有工程变更的产品是否与工程变更一致; 4.特殊出货要求如 SKD、CKD 包装是否按照文件执行? 5.包装内是否附有出货检验合格报告,产品生产工艺 流程、外观、功能抽检合格?
家具工厂制程铣型标准-铣型质量检验标准

玻璃槽位不精确误差超过位置、大小、深度误差超过±0.2mm,槽内有明显刀痕(按开发部部件图)
5
加工板件的正面部分有钉眼、加厚接缝
6
棱角、圆弧处有缺口
7
造型部位有明显刀痕
8
加工板件的边、棱、角未达到均匀一致
9
铣刀底部不平整、板件平面有锤印、毛刺
10
有挂伤、撞伤、划伤、饰面板保护膜划烂
制程检验标准
文件编号
版本号
A/0
铣型质量检验标准
页/次
1/1
目的:为了使所有员工明确、统一质量要求
范围:木工车间铣型工序
检验方法:目视、手摸、量具测量
抽样标准及允收水准参考《抽样作业指导书》
检验项目
检验内容及标准
缺陷等级
CR
MA
MI
1
造型不圆滑自然,尺寸误差超过±0.5mm(按开发部部件图)
2
线条不清晰、流畅、均匀、对称、有损伤
11
造型面有崩茬、刀痕、砂痕
12
弧形板件弧度误差超过1毫米
13
14
批准
审核
制订
生效时间:
- 1、下载文档前请自行甄别文档内容的完整性,平台不提供额外的编辑、内容补充、找答案等附加服务。
- 2、"仅部分预览"的文档,不可在线预览部分如存在完整性等问题,可反馈申请退款(可完整预览的文档不适用该条件!)。
- 3、如文档侵犯您的权益,请联系客服反馈,我们会尽快为您处理(人工客服工作时间:9:00-18:30)。
2008年02月16日星期六 10:42
制程检验又称IPQC,能够在早期的加工阶段发现不合格产品,避免在以后的不合格产品上浪费资源。
在实施半成品制程控制时要做好以下工作:
1.明确IPQC的控制范围
IPQC控制环节为:物料入库后至半成品入库前的控制。
主要为半成品制造现场各部门的品质控制。
2.设置控制点
控制点设在何处,主要考虑该在制品不稳定因素而设计。
(1)该产品以前生产有异常,有较高不良品的记录。
(2)使用的生产设备不稳定。
(3)工装夹具、模具有不良情况。
(4)得到IPQC对不良物料的信息反馈。
(5)新员工操作。
(6)新产品、新材料、新设备的投入。
3.确定lPQC的作业步骤
(1)确认首件检验。
在每款产品、每台机器正确生产前,IPQC要确认作业员送检的首件产品,并将检验结果记录于制程首件检验记录表中。
(2)核对生产资料。
在每款产品、每台机器正式生产时,IPQC应对领用的物料、设备状态、使用的工模具、作业指导书的版本进行核对。
(3)实施IPQC巡检。
①巡检时间频率。
IPQC在进行巡检时,要不间断地按机台、工位逐次巡检,在生产高峰期,应保持1-15小时巡检一次。
特别时间,可向有关部门申请人员求援,以保证巡检密度。
②按产品质量标准检验。
外观检测:目视、手感及参照生产样板验证。
尺寸:运用量具检测。
功能特性:可用检测仪器进行验证,必要时取样给QE工程师做试验。
机器运行参数:将实际参数与产品工艺指导单上的数据对比。
产品物料摆放:检查产品、物料、边角废料、不合格品是否摆放在规定的区域。
环境:检查环境是否清洁,是否有产品、物料散落在地面上。
员工作业方法:员工是否按规定制度操作机器,更换产品生产时是否通知IPQC到场验证(包括修机、修模、换料)。
检查物料、产品、机器标识状态。
(4)制作IPQC巡检记录。
IPQC在每次检验后,要将检验结果如实记录在制程IPQC 巡检记录表上。
(5)质量异常的反馈与处理。
IPQC在巡检过程中,若发现有质量异常现象时,做如下行动:
①可判定时,填制IPQC检验问题报告,经主管审核签名后,交生产部进行改善。
②若自己不可判定时,则持不良品样板交主管确认后,制单交生产部进行改善。
③对生产部回复的改善措施进行确认,并追踪改善效果。
④对产生的不合格品进行隔离、标识。
⑤将己改善的IPQC检验问题报告的"品检联"交回品质部。
总之,进行IPQC检验时应该具体规定检验项目、检验方法、检验频率,如果在检验中发现了不合格产品,那么在它转入下一道工序之前必须进行处理,以保证最终产品的质量。
五、如何实施半成品的质量检验
当产品复杂时,检验活动会被策划成与生产同步进行,这样有助于最终检验的迅
速完成。
因此,当把各种零部件组装成半成品时,有必要把半成品作为最终产品来对待,因为它们有时在装配后往往不能再进行单独的检验。
1.设置验证点
FQC主要是针对完工产品的质量验证,以确定该批产品可否流入下一道工序,属于定点检验。
所以FQC的控制点一般都设在工序终点。
2.确定FQC的检验项目
FQC除重复IPQC对产品的外观、尺寸、用料的质量验证外,还特别注重以下几方面的验证:
(1)结构性验证:按工艺图及质量标准验证。
(2)功能性试装:公差测量,保证产品在装配阶段不受影响。
(3)特性验证。
(4)装箱数量准确性验证。
3.确定检验方式
FQC在质量验证时,一般采用抽样计划进行验货,按AQL值来判定检验批次是否允收。
抽样检验中认为可以接收的连续提交检查批的过程平均上限值,称为合格质量水平,也可称作可接收质量水平(AQL)。
AQL一般用每百单位产品不合格品数或不合格数表示。
4.质量异常的反馈与处理
(1)FQC可判定情况。
根据不合格程度,对不合格批产品做出返工、重检、退料、挑选、报废等处理决定。
(2)FQC不可判定情况。
对各种不合格品,根据情况做出判定意见,并按判定意见予以标识,监督相关部门进行隔离存放。
5.做好验货记录FQC根据当班的验货结果,填制FQC半成品抽查日报表,经被检部门签认后,一联交质检部门存档,另一联交被检部门保存。
在企业生产要求和条件的允许下,应该对半成品进行线上最终检验,更好地保证最终产品的质量。
六、如何实施产品装配与包装制程控制
产品的装配和包装是产品生产的最后环节,对它的制程控制将使产品的装配和包装工作顺利进行,对产品最后的货号、包装等进行检验。
1.设置控制点
FQA同FQC一样,都是属于定点检验,其控制点均设在关键工序和产品终端。
2.确定FQA作业内容
(1)确定检验批的构成。
(2)确定抽样类型。
(3)确定AQL值。
(4)明确检验项目与验证方法。
(5)不合格品的处理。
(6)验货的记录。
3.确定FQA检验项目
(1)待装产品的验证,包括外观、尺寸、结构、功能、特性等。
(2)纸箱、标签的验证。
(3)成品的验证。
(4)包装效果的验证。
(5)纸箱标记的填制规范。
(6)成品装箱数量。
4.确定FQA作业程序
(1)检验前的准备工作
①检验前,要求装配部将所有成品整齐摆放于拉(line,生产线)头或拉尾,对于产品批量不足四箱的,等该批全部生产完成;对于批量大于或等于四箱的,须待生产够四箱然后由该拉班长挂上“待检品”牌。
②对挂有“待检品”牌的成品进行检验。
(2)检验
①依据工单、产品BOM等检验资料,首先核对产品货号、装箱数量和标签等,若发现实际情况与资料有异时,立即通知装配助拉、领班,并要求及时更正。
②根据MIL-STD-105EⅡ标准抽样,依照FQA检验标准样板及其他相关资料,对产品的外观、性能、包装进行全面检验。
③根据AQL主要缺陷为2.5、次要缺陷为4.0以及样品检验的内容和结果对每批成品做出判定。
合格:在箱盖旁加盖QA PASSED印,并挂上合格品牌,然后通知装配部搬运、封箱。
不合格:填写成品检验报告,并选出具有代表性的不良样板,根据最终判定结果做出以下处理:偏差接收。
按合格品处理。
返工:填写返工通知单,经QA部的主管审核后,交装配部的主管签名认可,装配部按返工程序执行返工,负责跟踪返工过程,对于返工后的成品,按检验程序重检,直至合格。
(3)存档。
在检验过程当中所采用的一切报告、报表及单据由QA进行编号存档,作为质量记录以供查阅。
在进行产品装配与包装制程控制时要明确其目的、内容和方法,这样才能达到预期的目的。
七、如何实施产品装配与包装品质检验
产品装配与包装品质检验可称为IPQA,IPQA的检验阶段是半制品经装配工序到成品入库前的检验,主要指装配部(或称包装部)的生产作业。
在进行IPQA检验时要了解以下内容:
1.设置lPQA检验点
(1)确认开拉首件产品。
(2)检查拉头工单资料。
(3)确认包装配件、标签、纸箱。
(4)确定生产、包装过程中的不稳定因素。
(5)得到IPQC和IQC或其他途径的不良信息反馈。
2.明确lPQA的作业步骤
(1)核对生产资料。
包括:装配生产通知单,包装规范,物料、零件规格(BOM),箱盒资料,标签资料,设备操作规范等。
(2)包装样板的签收,即首件确认。
(3)验证材料、配件、纸箱。
(4)进行过程巡检。
①确定巡检时间、频率。
②确定核查项目与验证方法。
黯争产品外观:运用目视、手感检测,并与样板核对。
产品尺寸:运用量具检测,并与产品检验标准核对。
产品结构:与产品包装规范核对。
产品功能:如扭力、拉力、压力等物料特'性.按产品检验标准进行检验。
纸箱、标签纸:按箱盒资料,标签资料等核对。
模拟测试:按产品检验标准的相应要求进行测试。
(5)制作IPQA的巡检记录。
IPQA根据当班的实际巡检结果,将具体情况按类别及时填写在包装IPQA巡检日报表相应栏目上。
(6)品质异常的反馈与处理。
IPQA在巡检中发现有不合格品的现象,需及时填制成品检验报告,经审核后交装配部改善,同时跟踪改善结果,直至合格为止。
产品装配与包装品质检验要合理设置IPQA的检验点,做好生产资料的核对和过程的巡检工作,这样才能把握好成品入库前的质量。