2旋压成形的基本方式分析
旋压机技术之旋压成型的基本方式拉深旋压
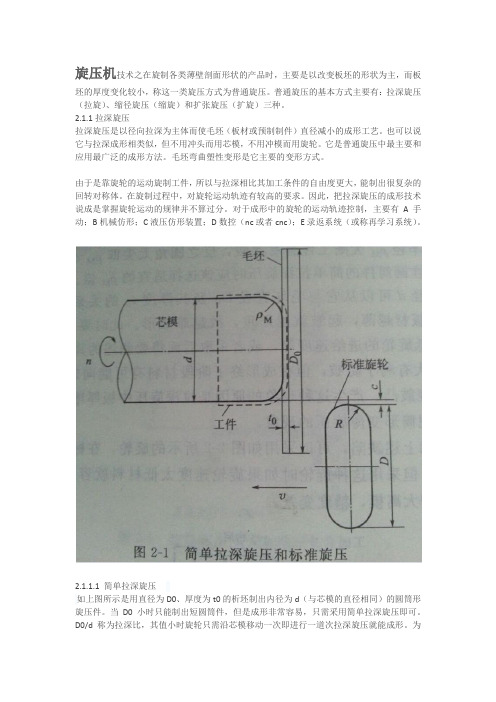
旋压机技术之在旋制各类薄壁剖面形状的产品时,主要是以改变板坯的形状为主,而板坯的厚度变化较小,称这一类旋压方式为普通旋压。
普通旋压的基本方式主要有:拉深旋压(拉旋)、缩径旋压(缩旋)和扩张旋压(扩旋)三种。
2.1.1拉深旋压拉深旋压是以径向拉深为主体而使毛坯(板材或预制制件)直径减小的成形工艺。
也可以说它与拉深成形相类似,但不用冲头而用芯模,不用冲模而用旋轮。
它是普通旋压中最主要和应用最广泛的成形方法。
毛坯弯曲塑性变形是它主要的变形方式。
由于是靠旋轮的运动旋制工件,所以与拉深相比其加工条件的自由度更大,能制出很复杂的回转对称体。
在旋制过程中,对旋轮运动轨迹有较高的要求。
因此,把拉深旋压的成形技术说成是掌握旋轮运动的规律并不算过分。
对于成形中的旋轮的运动轨迹控制,主要有A手动;B机械仿形;C液压仿形装置;D数控(nc或者cnc);E录返系统(或称再学习系统)。
2.1.1.1 简单拉深旋压如上图所示是用直径为D0、厚度为t0的析坯制出内径为d(与芯模的直径相同)的圆筒形旋压件。
当D0小时只能制出短圆筒件,但是成形非常容易,只需采用简单拉深旋压即可。
D0/d称为拉深比,其值小时旋轮只需沿芯模移动一次即进行一道次拉深旋压就能成形。
为区别于多道次拉深旋压而称它为简单拉深旋压。
旋压机旋轮只应沿芯模运动以保证它与芯模的间隙C。
在实际成形中还需考虑下面几个问题。
(1)旋轮的形状通常选用直径为D、顶端圆角半径为R的圆孤状旋轮。
将上图中所示的旋轮称为标准旋轮。
(2)旋轮的进给速度通常用拖板运动的速度u0(m/min)表示,但由于在判断成形的效果时要考虑毛坯的转速,因此毛坯每转的旋轮移动量U的大小是极为重要的因素,称其为旋轮进给量。
例如在进给速度U不变的条件下,如果毛坯转速增加一倍,则旋轮相对毛坯的运动距离变为原来的1/2,这样瞬间成形量就变小了。
(3)芯模的形状在上图中的情况下芯模是圆柱形,其直径为d,端部拐角处的圆角半径为pm。
金属旋压成形工艺

金属旋压成形工艺引言金属旋压成形是一种常见的金属成形工艺,通过将金属材料置于旋转的模具中,通过轴向压力和旋转运动对金属材料进行塑性变形,从而得到所需形状和尺寸的产品。
金属旋压成形工艺在制造行业中得到广泛应用,广泛用于制造各种金属产品,如罐体、汽车零部件、工业容器等。
本文将介绍金属旋压成形工艺的原理、应用领域和工艺参数等内容。
原理金属旋压成形的基本原理是通过旋转压力对金属材料进行塑性变形,从而得到所需形状和尺寸的产品。
其具体步骤如下: 1. 将金属材料置于旋转的模具中,并夹紧以防止材料滑动。
2. 施加轴向压力,使金属材料受到压力作用。
3. 同时进行模具的旋转运动,使金属材料在轴向压力和旋转力的作用下发生塑性变形。
4. 根据产品的形状和尺寸要求,逐渐调整模具的位置和形状,使金属材料逐步完成所需的变形。
应用领域金属旋压成形工艺广泛应用于以下领域: 1. 罐体制造:金属旋压成形工艺可用于制造各种罐体,如油罐、气罐、水罐等。
通过金属旋压成形,可以使罐体具有较高的密封性和强度。
2. 汽车零部件:金属旋压成形工艺可用于制造汽车零部件,如汽车油箱、排气管等。
通过金属旋压成形,可以使零部件具有较好的耐压性和密封性。
3. 工业容器:金属旋压成形工艺可用于制造各种工业容器,如储罐、压力容器等。
通过金属旋压成形,可以使容器具有较高的耐压性和耐腐蚀性。
4. 金属管材加工:金属旋压成形工艺可用于加工金属管材,改变其形状和尺寸。
通过金属旋压成形,可以使金属管材具有较好的韧性和强度。
工艺参数金属旋压成形的工艺参数对成形效果和产品质量起着重要的影响。
常见的工艺参数包括: 1. 旋转速度:旋转速度是指旋转模具的转速,通常以每分钟转数(RPM)来表示。
旋转速度的选择要根据金属材料的性质和成形要求来确定,过高或过低的旋转速度都可能影响成形效果。
2. 压力:压力是指施加在金属材料上的轴向压力。
压力的选择要根据金属材料的硬度和成形要求来确定,过高或过低的压力都可能导致成形不良或产生内部应力。
旋压工艺

二、工艺分析1、旋压过程分析⑴劈开轮劈开轮成形分为劈开、整形二个阶段。
垂直缸快速进给,在接近零件时转为工进并压紧零件(始终保压),主轴带动上下模旋转(见图2)。
X1劈开轮沿径向快速进给,接近工件时转换为工进,当X1进给了8~10mm后,X3整形轮沿径向快速进给(此时X1停留在原地)(图2 b),接近工件时转换为工进,此时X1和X3同时工进,在速度上X3比X1稍快一点。
当X1进给到预定深度,延时0.5~1.5秒后快速退回,X3继续工进,直到零件成形(图2 c)。
图 2 劈开轮旋压过程示意图在此旋压过程中要注意的问题有:1、垂直缸在压紧工件后应始终处于保压状态下,直到零件成形,X3退回;2、X1的进给位置一定要是在毛坯的二分之一处,偏差不能大于0.1mm,否则会产生劈偏现象,造成废品;3、X1和X3工进速度的协调关系(见图3);4、成形后槽型的回弹变形与X3的延时和X3旋轮尺寸之间的关系,当成形旋轮X3进给到位后,零件槽型部分会产生冷作硬化,角度尺寸有部分回弹现象,这时的X3旋轮的最终进给尺寸和延时量可以适当调整,最终保证角度尺寸不会超差。
在设计X3旋轮时也可以将回弹因素考虑进去,X3的旋轮夹角可以在图纸要求的尺寸上增加1°至2°,使之在旋压结束时能补充回弹量。
图3 X1与X3工进速度的协调关系注:当X1的工进速度比X3快或两者相等,都会产生如图a的效果,这时会发生已经被劈开的材料边缘部分受材料内应力的作用向X1旋轮表面靠拢,最终产生相对摩擦。
这样会在X1旋轮表面留下一圈积削,而这些积削会划伤零件表面,从而影响零件表面质量。
只有当X3的进给速度比X1的进给速度稍快一点(但不能快太多,否则到最后会产生X3成了劈开轮,X1没有起到作用的情况),由X3撑开已经被劈开的材料部分,使被劈开的材料部分不会与X1产生相对摩擦。
从而保证产品质量。
⑵折叠轮折叠轮成形分为预成形、整形二个阶段。
垂直缸快速进给,在接近零件时转为工进并压紧零件(没有保压)。
旋压成形技术
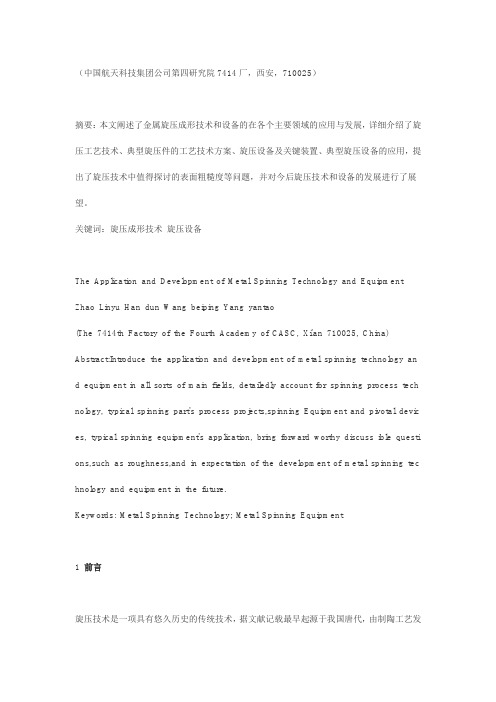
(中国航天科技集团公司第四研究院7414厂,西安,710025)摘要:本文阐述了金属旋压成形技术和设备的在各个主要领域的应用与发展,详细介绍了旋压工艺技术、典型旋压件的工艺技术方案、旋压设备及关键装置、典型旋压设备的应用,提出了旋压技术中值得探讨的表面粗糙度等问题,并对今后旋压技术和设备的发展进行了展望。
关键词:旋压成形技术旋压设备The Application and Development of Metal Spinning Technology and Equipment Zhao Linyu Han dun Wang beiping Yang yantao(The 7414th Factory of the Fourth Academy of CASC, Xi'an 710025, China) Abstract:Introduce the application and development of metal spinning technology an d equipment in all sorts of main fields, detailedly account for spinning process tech nology, typical spinning part's process projects,spinning Equipment and pivotal devic es, typical spinning equipment's application, bring forward worthy discuss ible questi ons,such as roughness,and in expectation of the development of metal spinning tec hnology and equipment in the future.Keywords: Metal Spinning Technology; Metal Spinning Equipment1 前言旋压技术是一项具有悠久历史的传统技术,据文献记载最早起源于我国唐代,由制陶工艺发展出了金属的旋压工艺。
旋压成形工艺分析
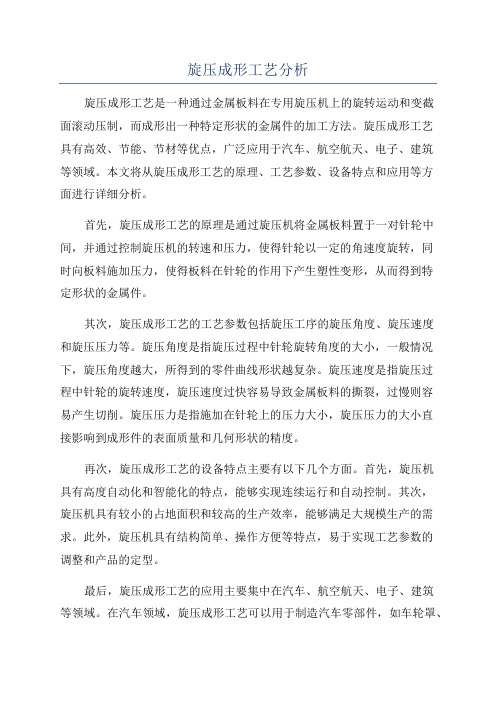
旋压成形工艺分析旋压成形工艺是一种通过金属板料在专用旋压机上的旋转运动和变截面滚动压制,而成形出一种特定形状的金属件的加工方法。
旋压成形工艺具有高效、节能、节材等优点,广泛应用于汽车、航空航天、电子、建筑等领域。
本文将从旋压成形工艺的原理、工艺参数、设备特点和应用等方面进行详细分析。
首先,旋压成形工艺的原理是通过旋压机将金属板料置于一对针轮中间,并通过控制旋压机的转速和压力,使得针轮以一定的角速度旋转,同时向板料施加压力,使得板料在针轮的作用下产生塑性变形,从而得到特定形状的金属件。
其次,旋压成形工艺的工艺参数包括旋压工序的旋压角度、旋压速度和旋压压力等。
旋压角度是指旋压过程中针轮旋转角度的大小,一般情况下,旋压角度越大,所得到的零件曲线形状越复杂。
旋压速度是指旋压过程中针轮的旋转速度,旋压速度过快容易导致金属板料的撕裂,过慢则容易产生切削。
旋压压力是指施加在针轮上的压力大小,旋压压力的大小直接影响到成形件的表面质量和几何形状的精度。
再次,旋压成形工艺的设备特点主要有以下几个方面。
首先,旋压机具有高度自动化和智能化的特点,能够实现连续运行和自动控制。
其次,旋压机具有较小的占地面积和较高的生产效率,能够满足大规模生产的需求。
此外,旋压机具有结构简单、操作方便等特点,易于实现工艺参数的调整和产品的定型。
最后,旋压成形工艺的应用主要集中在汽车、航空航天、电子、建筑等领域。
在汽车领域,旋压成形工艺可以用于制造汽车零部件,如车轮罩、车身饰条等。
在航空航天领域,旋压成形工艺可以应用于制造薄壁管件、舵面部件等。
在电子领域,旋压成形工艺可以用于制造散热器、天线等。
在建筑领域,旋压成形工艺可以应用于制造门窗框、屋顶构件等。
总之,旋压成形工艺是一种高效、节能的金属加工方法,具有广泛的应用前景。
通过分析旋压成形工艺的原理、工艺参数、设备特点和应用等方面,可以更好地了解旋压成形工艺的特点和应用领域,为相关行业的生产和技术改进提供一定的指导和参考。
金属成形:旋压过程的分析
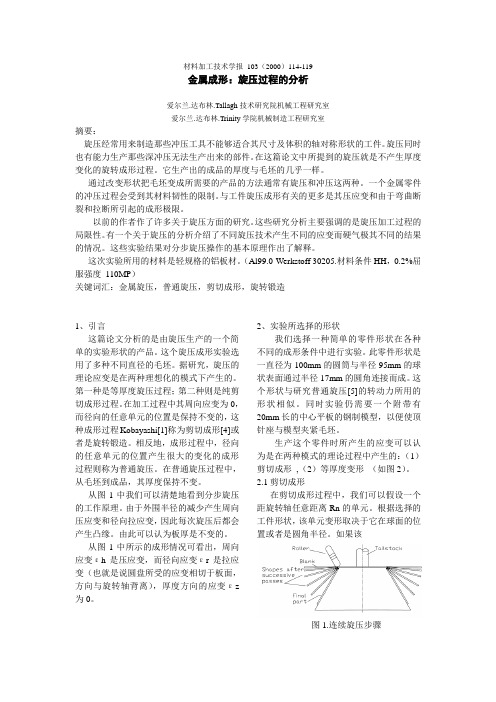
材料加工技术学报103(2000)114-119金属成形:旋压过程的分析爱尔兰.达布林.Tallagh技术研究院机械工程研究室爱尔兰.达布林.Trinity学院机械制造工程研究室摘要:旋压经常用来制造那些冲压工具不能够适合其尺寸及体积的轴对称形状的工件。
旋压同时也有能力生产那些深冲压无法生产出来的部件。
在这篇论文中所提到的旋压就是不产生厚度变化的旋转成形过程。
它生产出的成品的厚度与毛坯的几乎一样。
通过改变形状把毛坯变成所需要的产品的方法通常有旋压和冲压这两种。
一个金属零件的冲压过程会受到其材料韧性的限制。
与工件旋压成形有关的更多是其压应变和由于弯曲断裂和拉断所引起的成形极限。
以前的作者作了许多关于旋压方面的研究。
这些研究分析主要强调的是旋压加工过程的局限性。
有一个关于旋压的分析介绍了不同旋压技术产生不同的应变而硬气极其不同的结果的情况。
这些实验结果对分步旋压操作的基本原理作出了解释。
这次实验所用的材料是轻规格的铝板材。
(Al99.0-Werkstoff 30205.材料条件HH,0.2%屈服强度110MP)关键词汇:金属旋压,普通旋压,剪切成形,旋转锻造1、引言这篇论文分析的是由旋压生产的一个简单的实验形状的产品。
这个旋压成形实验选用了多种不同直径的毛坯。
据研究,旋压的理论应变是在两种理想化的模式下产生的。
第一种是等厚度旋压过程;第二种则是纯剪切成形过程。
在加工过程中其周向应变为0,而径向的任意单元的位置是保持不变的,这种成形过程Kobayashi[1]称为剪切成形[4]或者是旋转锻造。
相反地,成形过程中,径向的任意单元的位置产生很大的变化的成形过程则称为普通旋压。
在普通旋压过程中,从毛坯到成品,其厚度保持不变。
从图1中我们可以清楚地看到分步旋压的工作原理。
由于外围半径的减少产生周向压应变和径向拉应变,因此每次旋压后都会产生凸缘。
由此可以认为板厚是不变的。
从图1中所示的成形情况可看出,周向应变εh是压应变,而径向应变εr是拉应变(也就是说圆盘所受的应变相切于板面,方向与旋转轴背离),厚度方向的应变εz 为0。
旋压成形工艺分析
压技术的单位不断增加,拥有旋压设备近千台,
从事旋压技术的人员数以千计。
汇报时间
第
一1、旋压的概念、特点、分类及发展简介 1 国页外技术先进的国家,其旋压技术已日臻成熟。
国内旋压技术近年来发展迅速,随着对外引进和 自主创新能力的提高,与国外先进国家旋压技术 的差距正在缩短。
汇报时间
二、普通旋压成形技术 普通旋压成形作为发展较早的一项旋压成
变形区②的坯料与旋轮圆角Ⅱ及芯模接触,产生 扎压与弯曲变形。承受轴向拉应力,切向压应力, 厚度方向有压应力σr,呈一向拉伸、两向压缩的 体积应变状态。
已变形区③产生拉伸变形,为轴向伸长、壁厚减 薄呈平面应变状态 。
汇报时间
第
1
二、普通旋压成形技术
9
2)页坯料的制备
坯料直径按等面积原则进行计算,考虑工件适量 减薄,坯料直径应小于计算值的3%~5%。薄璧 工件拉伸旋压时,坯料应先将边缘预成形,以防 止在前期旋压道次中起皱,并提高工效。坯料外 缘光滑整齐有利于防止旋压中边缘开裂。
阴极铜150~450m/min ;
黄铜200~650 m/min ;
不锈钢250~550 m/min ;
拉伸钢300~500 m/min。
汇报时间
第
2
二、普通旋压成形技术
2
5)页 旋轮轨迹的设定
无论在哪种旋压方式下,旋轮的运动轨迹都是一 个重要的工艺要素,平板拉深旋压成形曲母线形 和筒形件时,旋轮可按渐开线轨迹运动。渐开线 的方程为:(叶山益次郎)
汇报时间
第
一4、旋压的概念、特点、分类及发展简介 页
2、旋压成形工艺的特点: 1)在旋压过程中,旋轮(或钢球)对坯料逐点施压,接
触面积小,单位压力可达250~350公斤力/毫米2以上,对 于加工高强度难变形材料,所需总变形力较小,从而使功 率消耗大大降低。 2)坯料的金属晶粒在三向变形力的作用下,沿变形区滑 移面错移,滑移面各滑移层的方向与变形方向一致,因此, 金属纤维保持连续完整。。 3)强力旋压可使制品达到较高的尺寸精度和表面光洁度。 在旋压过程中,旋轮不仅对被旋压的金属有压延的作用, 还有平整的作用,因此制品表面光洁度高,
有关旋压成形技术简介
传统旋压成形技术简介旋压成形是一种板材连续局部塑性成形的技术;是一种综合了锻造、挤压、拉伸、弯曲、环轧、横轧和滚挤等工艺特点的少无切削加工的先进工艺。
传统的旋压工艺将金属筒坯、平板毛坯或预制坯用尾顶顶紧在旋压机芯模上,由主轴带动芯棒和坯料旋转,同时旋压轮从毛坯一侧将材料挤压在旋转的芯模上,使材料产生逐点连续的塑性变形,从而获得各种母线形状的空心旋转体零件。
如图 1.2 所示为旋压工艺的加工原理。
根据不同的分类方法,可以将旋压分为以下几种:(1)根据旋压加工过程中毛坯厚度的变化情况,一般将旋压工艺分为普通旋压和强力旋压两种[36-37]。
普通旋压时,在旋压成形过程中毛坯的厚度基本不发生变化;主要有拉深旋压、缩径旋压、扩径旋压、制梗成形等。
普通旋压是加工薄壁空心回转体零件的无屑加工工艺过程。
它借助旋轮对随芯模转动的金属圆板作进给运动的同时施压,主要改变其直径尺寸使其成为所需工件。
图1.3 为封头旋压工艺过程,是典型的普通旋压。
封头旋压通常是采用板料成形,变形前后壁厚不变化或者变化极小,直径变化较大,或收缩或扩大,旋压时较易失稳或局部拉薄,有单向前进旋压和往复摆动多道次逐步旋压两种方式。
强力旋压又称变薄旋压,是指在旋压成形过程中毛坯的厚度不断在减薄。
借助旋轮对随旋压模转动的金属圆板或管坯作进给运动并施压,加工薄壁空心回转体零件的无屑成形工艺过程。
变薄旋压属体积成形范畴,在成形过程中主要是壁厚减薄而直径尺寸基本不变。
(2)按旋压产品形状的不同,普通旋压又可分为拉深旋压、收颈旋压、扩径旋压、翻边旋压、卷边旋压、切边旋压、压筋旋压及表面精整旋压等;强力旋压又可分为流动旋压(又称筒形件变薄旋压)和剪切旋压(又称锥形件变薄旋压)。
(3)根据旋压过程中金属材料的流动方向不同,流动旋压可分为正旋和反旋。
正旋是指旋压过程中金属材料的流动方向与旋轮的进给方向相同;反旋是指旋压过程中金属材料的流动方向与旋轮的进给方向相反。
旋压详细资料
旋压的基本原理和加工工艺详解利用旋压工具(旋轮或擀棒)和芯模使毛坯边旋转边成形,生产金属空心回转体件的一种回转成形工艺。
旋压时,金属毛坯随芯模旋转或旋压工具绕毛坯和芯模旋转,旋压工具相对芯模作进给运动,从而使毛坯受压并产生连续局部变形以获得空心回转体零件,如图所示。
旋压时,旋压工具与毛坯接触面积小,毛坯只局部产生塑性变形,所需变形力小,可用小吨位的设备加工大型空心回转体制品。
旋压产品具有较高的尺寸精度和较低的表面粗糙度,力学性能好。
旋压工具制造简单,更换容易。
但旋压产量较低,品种受到一定限制,多适用于小批量多品种的产品。
旋压是一种古老的加工方法。
早在10世纪初,中谚藤:国就使用旋压方法把银锡等金属板旋压成各种器皿。
20世纪以来,旋压工艺在工业上得到广泛应用。
目前旋压工艺不仅用于加工铝、铜及其合金,而且越来越多地用于加工钢铁和稀有金属。
旋压的产品有日常生活用具、化工容器、各种形状的机器零件,航天器、航空器和火箭导弹的各种壳体部件等。
旋压按加工温度分为冷旋压、温旋压和热旋压。
一般多采用冷旋压。
旋压按金属变形特征分为普通旋压和强力旋压。
普通旋压改变毛坯的形状,扩大或缩小直径而基本不改变厚度的旋压方法。
这种旋压多用于成形各种薄壁的铝、铜、不锈钢等生活用具,如灯罩、炊具及手工艺品等。
普通旋压包括缩径旋压(缩旋)和扩径旋压(扩旋)。
此外,还可以完成一些切割、搭接等工作。
普通旋压有手工旋压、半自动旋压和自动旋压等。
缩径旋压使毛坯产生径向收缩的一种普通旋压。
缩旋除在旋压工具作用下使整体旋压成形外,还可以进行收口、收颈、压槽和收边等局部变形。
扩径旋压使毛坯产生径向胀大的一种普通旋压。
它除了整体扩旋成形外,还可以翻边、扩颈、扩口和压槽等局部成形。
扩颈旋压采用芯模在毛坯之外而旋轮在毛坯之内的内旋压法。
普通旋压工艺参数主要考虑坯料的尺寸和性能、旋轮进给量、仿形板的型面、道次间距及旋轮形状等。
普通旋压坯料一般用板坯。
旋轮进给量厂是芯模每转一圈时,旋压工具沿芯模母线移动的距离;常选,f=0.3~3m/r,f过大时制品易起皱,过小时制品易拉薄。
旋压制造工艺
中国兵器工业集团第五五研究所
汇报时间 2013-11-7
第 13 页
二、普通旋压成形技术
2、普通旋压的工艺优点: 1)模具制造周期较短,模具费用低于整套冲压模具50 %~80%左右。 2)近似为点变形,旋压力比冲压力低。 3)可在一次装卡中完成成形、切边、制梗、咬接等多 道工序。 4)可以成形其他成形方法难以成形或不能成形的钛、 钨等稀有金属,并且旋压时实现加热较其它工艺加热成 形方便。 5)制品范围广。普通旋压可以成形出球形、椭球形、 曲母线形、杯形、锥形及变截面带台阶的异形薄壁回转 体零件。
中国兵器工业集团第五五研究所
汇报时间 2013-11-7
第9页
一、旋压的概念、特点、分类及发展简介
5、旋压成形技术国内外的发展 我国旋压技术发展始于20世纪60年代初期,先 后有北京有色金属研究总院、北京航空工程研究 所、中国兵器工业第五五研究所等单位率先开展 旋压技术工艺和设备的研究。随后,兵器、航空、 航天、核工业、汽车等行业也陆续开展了旋压技 术研究与开发。据不完全统计,当前全国从事旋 压技术的单位不断增加,拥有旋压设备近千台, 从事旋压技术的人员数以千计。
中国兵器工业集团第五五研究所
汇报时间 2013-11-7
第 10 页
一、旋压的概念、特点、分类及发展简介
国外技术先进的国家,其旋压技术已日臻成熟。 国内旋压技术近年来发展迅速,随着对外引进和 自主创新能力的提高,与国外先进国家旋压技术 的差距正在缩短。
中国兵器工业集团第五五研究所
汇报时间 2013-11-7
中国兵器工业集团第五五研究所
汇报时间 201
4)拉旋转速 拉旋时工件转速适度增大有助于增加变形的稳定 性,工件的转速与材料、壁厚、直径、及设备的 刚度有关,常用圆周速度表示。常用材料圆周速 度选择的参考数据如下: 纯铝200~750m/min ; 阴极铜150~450m/min ; 黄铜200~650 m/min ; 不锈钢250~550 m/min ; 拉伸钢300~500 m/min。
- 1、下载文档前请自行甄别文档内容的完整性,平台不提供额外的编辑、内容补充、找答案等附加服务。
- 2、"仅部分预览"的文档,不可在线预览部分如存在完整性等问题,可反馈申请退款(可完整预览的文档不适用该条件!)。
- 3、如文档侵犯您的权益,请联系客服反馈,我们会尽快为您处理(人工客服工作时间:9:00-18:30)。
▪ (2)卷边成形
▪ (3)压沟和滚筋成形
▪ (4)擀光成形
▪ (5)剪切加工
2.2 强力旋压和基本方式
▪ 根据旋压件的类型和金属变形机理的差异, 强力旋压可分为锥形件强力旋压(或称为 剪切旋压)和筒形件强力旋压(或称为流 动旋压)两种,前者用于加工锥形,抛物 线形,和半球形等异型件,而后者则用于 筒形件和管形件的加工。有时这两种方法 联合运用,加工各种复合形零件。
图3-1 短芯头卧式旋压原理图
1旋压成品 2短芯头3凹模 4滚珠 5管坯 6送料装置 7连杆 8支座 9调节螺母
图 3-2 短芯头立式旋压原理图
1拉杆固定 2拉杆 3进给丝杠 4管坯 5卡爪 6滚珠 7凹模2.2.2 筒形变薄旋压
▪ 按照旋压时金属流动的方向与旋轮运动方向一致 与否,可分为正旋压和反旋压两种。前者指相互 方向一致,后者则方向相反。在实际筒形件变薄 旋压中,两种方法都得到了很好的运用,有时也 可联合使用。
▪ 正旋压主要优点如下: ▪ (1)旋压力能参数小。 ▪ (2)工件贴模性能好,产生扩径和金属堆积也较小。 ▪ (3)在相同条件下,正旋压的极限减薄率较反旋的高,因
2.3.3 张力旋压
▪ 所谓张力旋压法,即在强力旋压过程中,对被旋压的工 件端部施加以轴向力,恒定的张力(推力),此张力引起 的拉应力应低于材料的屈服极限,一般为(0.2—0.5) σs。
2.3.4 多旋轮的错距旋压法
▪ 采用两个旋轮或三个旋轮并使其布置于不 同的平面内,即沿着轴向旋轮彼此相隔一 定距离,即产生轴向错距C。同时又在径 向彼此间距为一定值,即径向错距△t,为 使各个旋轮承担各自规定的旋压工作量, 这就是所谓的多旋轮错位旋压法
旋压成形技术
▪ 在实际成形中还需考虑下面几个问题: ▪ (1)旋轮的形状 ▪ (2)旋轮的进给速度 ▪ (3)芯模的形状 ▪ (4)毛坯的转速 ▪ (5)毛坯的尺寸和性质
旋压成形技术
旋压成形技术
旋压成形技术
旋压成形技术
2.1.2 缩径旋压
▪ 利用旋压工具使回转体空心件或管状毛坯进行径向局部 旋转压缩以减小其直径的成形方法。
2 旋压成形的基本方式
普通旋压的基本方式主要有:拉深旋压(拉 旋)、缩径旋压(缩旋)和扩径旋压(扩旋) 等三种。
2.1.1 拉深旋压 拉深旋压是以径向拉深为主体而使毛坯(板材 或预制件)直径减小的成形工艺。也可以说它 与拉深成形相类似,但不用冲头而用芯模, 不用冲模而用旋轮。它是普通旋压中最主要 和应用最广泛的成形方法。毛坯弯曲塑性变 形是它主要的变形方式。
2.3.5 劈开旋压法
▪ 利用具有硬质尖角的轮子,对旋转着圆形毛坯的矩形截 面边缘作逐渐径向进给挤入,以使之劈开成为“Y”形的 两个部分,然后再使用1~3个成形旋轮对其进行成形和 整形旋压,得到所需的形状和尺寸零件,这种成形方法 称为劈开旋压法。
2.3.6 钢球(滚珠)旋压法
▪ 为制造特薄壁回转体空心件,可采用有效地钢球为变形 工具的钢球旋压法。
而旋轮接触角和进给量的选择范围就比较大。
▪ (4)正旋压不仅可旋制带底的直筒形(管形)件,而且易成 形带底(或底部凸台)的凸、凹筋和各种变壁厚的零件。
▪ 正旋压有如下缺点: ▪ (1)由于正旋压时旋轮需走完成品件的全长,因此工件长
度受芯模长度和旋轮的纵向行程的限制。要旋出多长的 成品件就必须有多长的芯模和旋轮行程。从而降低了设 备的生产率和造成设备庞大。此外,为了保证工件的精 度,通常要求芯模长工件略长一些,一般长出10~20% 。 ▪ (2)固定毛坯用的夹具较为复杂。 ▪ 反旋法的优缺点,正好与正旋压相反。
▪ (3)滚动模的缩旋
▪ 对于工件尺寸很大的旋压件的缩径,由于有足够 的空间,可以用滚动模进行收缩旋压,滚动模在 筒形毛坯的内侧起芯模的作用,要求有很好的刚 度,结构上保证成形尺寸及进退、调整方便。
▪ 影响工件缩旋质量的主要工艺因素如下: ▪ 1)主轴转速 ▪ 2)旋轮进给量 ▪ 3)缩旋工艺装置设计 ▪ 4)缩径时的操作
2.1.3 扩径旋压
▪ 利用旋压工具使空心回转体容器或管状毛 坯进行局部(中部或端部)直径增大的旋压 成形方法,称为扩径旋压(扩旋)。
2.1.4 普通旋压中的辅助成形
▪ 普通旋压除了上述基本成形方式外,还包 括:翻边、卷边、、压筋,修剪和擀光等 局部成形或辅助成形方法。
▪ (1)翻边(弯边)成形
2.3 其它旋压法
▪ 2.3.1 内旋压法 ▪ 所谓内旋压法则是将芯模与旋轮两者的位
置倒过来,即旋轮放在管坯的里侧而芯模 被内侧与需成形件的形状和尺寸相一致的 空心模所取代。
1-环形模 2-异形旋轮 3-环形坯料 4-空心件 5-轴
2.3.2 斜轧式旋压法
▪ 当把旋轮和芯模轴线设置成一个交错角-送进角, 便成为类似于斜轧方式的斜轧旋压法。
▪ 根据工件的形状,材料和质量要求不同,可采用 不同的生产方法
▪ (1)无芯模(又称空气模)的缩旋
▪ 主要制成开口端直径很小、缩径量很大及端部封 闭的旋压件。典型的产品如气瓶的收径和封口成 形。
▪ (2)内芯模的缩旋
▪ 针对筒形毛坯一端收口而另一端尺寸不变,或者 对有一定长度的管材进行中间缩径时,可采用内 芯模保证成形件的尺寸要求。芯模设计时根据需 要,可制成整体芯模也可制成组合芯模。