特种加工结课论文
特种加工技术论文.(优选)
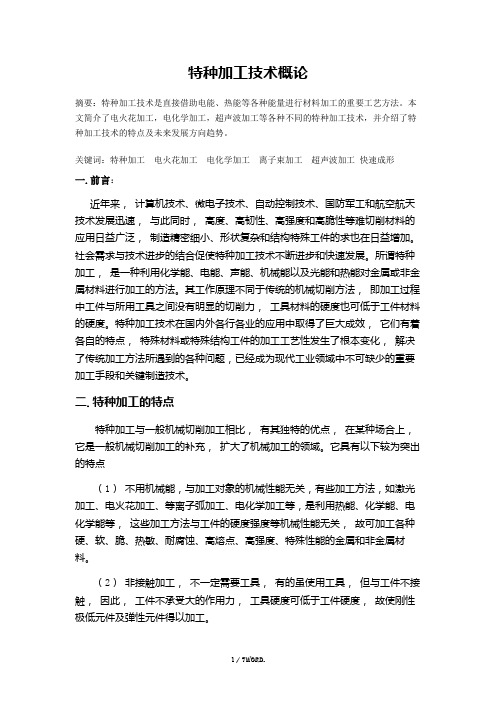
特种加工技术概论摘要:特种加工技术是直接借助电能、热能等各种能量进行材料加工的重要工艺方法。
本文简介了电火花加工,电化学加工,超声波加工等各种不同的特种加工技术,并介绍了特种加工技术的特点及未来发展方向趋势。
关键词:特种加工电火花加工电化学加工离子束加工超声波加工快速成形一.前言:近年来,计算机技术、微电子技术、自动控制技术、国防军工和航空航天技术发展迅速,与此同时,高度、高韧性、高强度和高脆性等难切削材料的应用日益广泛,制造精密细小、形状复杂和结构特殊工件的求也在日益增加。
社会需求与技术进步的结合促使特种加工技术不断进步和快速发展。
所谓特种加工,是一种利用化学能、电能、声能、机械能以及光能和热能对金属或非金属材料进行加工的方法。
其工作原理不同于传统的机械切削方法,即加工过程中工件与所用工具之间没有明显的切削力,工具材料的硬度也可低于工件材料的硬度。
特种加工技术在国内外各行各业的应用中取得了巨大成效,它们有着各自的特点,特殊材料或特殊结构工件的加工工艺性发生了根本变化,解决了传统加工方法所遇到的各种问题,已经成为现代工业领域中不可缺少的重要加工手段和关键制造技术。
二.特种加工的特点特种加工与一般机械切削加工相比,有其独特的优点,在某种场合上,它是一般机械切削加工的补充,扩大了机械加工的领域。
它具有以下较为突出的特点(1)不用机械能,与加工对象的机械性能无关,有些加工方法,如激光加工、电火花加工、等离子弧加工、电化学加工等,是利用热能、化学能、电化学能等,这些加工方法与工件的硬度强度等机械性能无关,故可加工各种硬、软、脆、热敏、耐腐蚀、高熔点、高强度、特殊性能的金属和非金属材料。
(2)非接触加工,不一定需要工具,有的虽使用工具,但与工件不接触,因此,工件不承受大的作用力,工具硬度可低于工件硬度,故使刚性极低元件及弹性元件得以加工。
(3)微细加工,工件表面质量高,有些特种加工,如超声、电化学、水喷射、磨料流等,加工余量都是微细进行,故不仅可加工尺寸微小的孔或狭缝,还能获得高精度、极低粗糙度的加工表面。
特种加工技术论文(2)
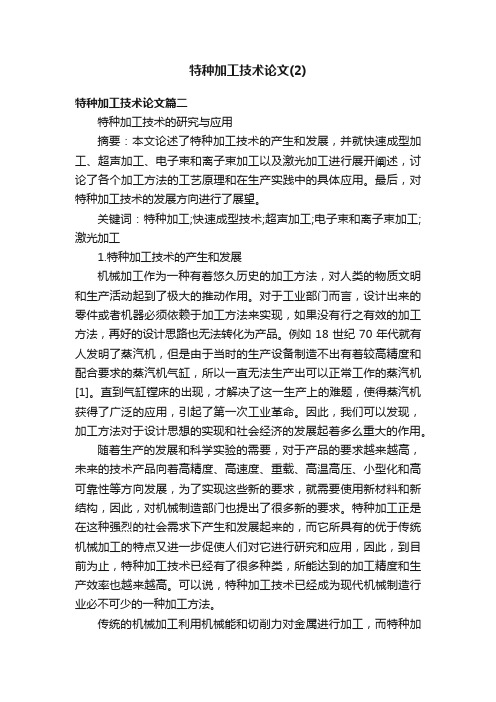
特种加工技术论文(2)特种加工技术论文篇二特种加工技术的研究与应用摘要:本文论述了特种加工技术的产生和发展,并就快速成型加工、超声加工、电子束和离子束加工以及激光加工进行展开阐述,讨论了各个加工方法的工艺原理和在生产实践中的具体应用。
最后,对特种加工技术的发展方向进行了展望。
关键词:特种加工;快速成型技术;超声加工;电子束和离子束加工;激光加工1.特种加工技术的产生和发展机械加工作为一种有着悠久历史的加工方法,对人类的物质文明和生产活动起到了极大的推动作用。
对于工业部门而言,设计出来的零件或者机器必须依赖于加工方法来实现,如果没有行之有效的加工方法,再好的设计思路也无法转化为产品。
例如18世纪70年代就有人发明了蒸汽机,但是由于当时的生产设备制造不出有着较高精度和配合要求的蒸汽机气缸,所以一直无法生产出可以正常工作的蒸汽机[1]。
直到气缸镗床的出现,才解决了这一生产上的难题,使得蒸汽机获得了广泛的应用,引起了第一次工业革命。
因此,我们可以发现,加工方法对于设计思想的实现和社会经济的发展起着多么重大的作用。
随着生产的发展和科学实验的需要,对于产品的要求越来越高,未来的技术产品向着高精度、高速度、重载、高温高压、小型化和高可靠性等方向发展,为了实现这些新的要求,就需要使用新材料和新结构,因此,对机械制造部门也提出了很多新的要求。
特种加工正是在这种强烈的社会需求下产生和发展起来的,而它所具有的优于传统机械加工的特点又进一步促使人们对它进行研究和应用,因此,到目前为止,特种加工技术已经有了很多种类,所能达到的加工精度和生产效率也越来越高。
可以说,特种加工技术已经成为现代机械制造行业必不可少的一种加工方法。
传统的机械加工利用机械能和切削力对金属进行加工,而特种加工主要利用电能、化学能、光能、声能和热能等能量来去除金属,因此特种加工技术可以用来加工各种高硬度、高强度、高脆性和高韧性的金属或者非金属材料。
由于特种加工采用广义上的刀具,例如激光、超声波、电子束和离子束等,所以易于实现加工过程的全自动化,这对于现代化生产的组织和管理有着很重要的意义。
特种加工技术论文

特种加工技术论文特种加工技术及其应用研究摘要:本文简述了特种加工技术的概念、分类,重点阐述了其领域的实际应用与研究发展方向。
关键词:特种加工;特点;应用;研究方向1特种加工涵义特种加工是相对传统切削加工而言,本质上是直接或复合利用电能、电化学能、化学能、光能、物质动能等对工件进行加工的工艺方法总称。
目前常用的有电火花加工、超声波加工、激光加工,除此之外还有电化学加工、电子束加工等。
它与传统切削加工相比具有:加工过程不再主要依靠机械能,而是直接或复合利用其它能量完成工件的加工;加工所用工具材料的硬度可大大低于被加工材料硬度,有时甚至无需使用工具即可完成对工件的加工;加工过程工具与工件间不存在显著的机械切削力;加工方法日新月异等特点。
2 特种加工分类、方法及应用电火花成形(穿孔)加工:该法可加工任何导电材料。
它是利用火花放电腐蚀金属原理,用工具电极(纯铜或石墨)对工件进行复制加工的工艺方法,可用于加工型腔模(锻模、压铸模、注塑模等)和型腔零件;加工冲模、粉末冶金模、挤压模、型孔零件、小异型孔、小深孔等。
其中最为典型的应用是在YG8(硬质合金)工件上,加工一个直径1mm深80mm的孔,只需12分钟;电火花双轴回转展成法加工凹凸球面、球头;电火花共轭同步回转可加工精密螺纹、齿轮等复杂表面;目前已能加工出0.005mm的短微细轴和0.008mm的浅微细孔,以及直径小于1mm的齿轮。
电火花线切割加工:它是利用移动的细金属丝(铜丝或钼丝)作电极,对工件进行脉冲火花放电腐蚀,实现切割成形的加工方法。
它同样可以加工任何导电材料;加工各种形状的冲模、切割电火花成形加工用的电极、切割零件等。
典型的应用例如:试制切割特殊微电机硅钢片定转子铁心芯;切割斜度锥面、上下异形面工件;工件倾斜数控回转切割加工双曲面零件;数控三轴联动加分度切割加工扭转四方锥台。
超声波加工:它是利用加工工具的超声频振动,通过磨料悬浮液加工硬脆材料的一种成形方法。
特种加工论文

精密加工技术姓名:潘培福班级:08机械二班学号:200800606219摘要:目前,精密加工是指加工精度为1~0.1µm,表面粗糙度为Ra0.1~0.01µm的加工技术,但这个界限是随着加工技术的进步不断变化的,今天的精密加工可能就是明天的一般加工。
精密加工所要解决的问题,一是加工精度,包括形位公差、尺寸精度及表面状况,有时有无表面缺陷也是这一问题的核心;二是加工效率,有些加工可以取得较好的加工精度,却难以取得高的加工效率。
精密加工应该包括微细加工和超微细加工、光整加工等加工技术。
关键词:精密加工、精密、切削、磨削。
几种常用的精密加工方法传统的精密加工方法有布轮抛光、砂带磨削、超精细切削、精细磨削、珩磨、研磨、超精研抛技术、磁粒光整等。
砂带磨削是用粘有磨料的混纺布为磨具对工件进行加工,属于涂附磨具磨削加工的范畴,有生产率高、表面质量好、使用范围广等特点。
国外在砂带材料及制作工艺上取得了很大的成就,有了适应于不同场合的砂带系列,生产出通用和专用的砂带磨床,而且自动化程度不断提高(已有全自动和自适应控制的砂带磨床),但国内砂带品种少,质量也有待提高,对机床还处于改造阶段。
精密切削也称金刚石刀具切削(SPDT),用高精密的机床和单晶金刚石刀具进行切削加工,主要用于铜、铝等不宜磨削加工的软金属的精密加工,如计算机用的磁鼓、磁盘及大功率激光用的金属反光镜等,比一般切削加工精度要高1~2个等级。
例如用精密车削加工的液压马达转子柱塞孔圆柱度为0.5~1µm,尺寸精度1~2µm;红外反光镜的表面粗糙度Ra0.01~0.02µm,还具有较好的光学性质。
从成本上看,用精密切削加工的光学反射镜,与过去用镀铬经磨削加工的产品相比,成本大约是后者的一半或几分之一。
但许多因素对精密切削的效果有影响,所以要达到预期的效果很不容易。
同时,金刚石刀具切削较硬的材料时磨损较快,如切削黑色金属时磨损速度比切削铜快104倍,而且加工出的工件的表面粗糙度和几何形状精度均不理想。
特种加工技术论文

特种加工技术论文特种加工作为一种有着悠久历史的加工方法,对人类的物质文明和生产活动起到了极大的推动作用。
下面是店铺整理的特种加工技术论文,希望你能从中得到感悟!特种加工技术论文篇一特种机械加工技术摘要:太阳能级多线切割技术是一种特殊的机械加工技术,它是在传统的机械加工的基础上建立起来的。
随着太阳能市场的启动和发展,作为晶体硅太阳能电池制造过程的主要环节,越来越受到人们的重视。
本文介绍了硅片切割的发展史,并从硅片切割的设备、工艺、生产流程和新技术等方面进行了较详细的阐述。
关键词:多线切割技术;硅片生产流程;硅片切割工艺;硅片切割新技术中图分类号: TU74 文献标识码: A太阳能级硅片切割的历史在上世纪80年代以前,人们在切割超硬材料的时候一般采用涂有金刚石粉的内圆切割机进行切割。
然而随着半导体行业的飞速发展,人们对已有的生产效率难以满足,同时由于内圆切割的才来损失非常大,在半导体行业成本的摩尔定律的作用下,人们对于降低切割陈本,提高效率的要求欧越来越高。
多线切割技术因此而逐步发展起来。
多线切割机由于其更高效、更小的切割损失以及更高精度的优势,对于切割贵重、超硬材料有着巨大的优势,近十年来已取代传统的内圆切割成为硅片切割加工的主要方式。
在2003年以前,多线切割主要满足于半导体行业的需求,切割技术主要掌握在欧、美、日、台等国家和地区,国内半导体业务以封装业务为主,上游的晶圆切割技术远远落后于发达国家和地区,相关的设备制造研发也难有进展。
2003年随着太阳能光伏行业的爆发式增长,国内民营企业的硅片切割业务迅速发展起来。
大量引进了瑞士和日本的先进的数控多线切割设备。
这才使切割太阳能级硅片的多线切割机的数量开始在国内爆发式增长,相关的技术交流也开始在国内广泛兴起。
当前国内使用的硅片切割机的种类及特点目前国内各个硅片切割厂家基本使用国际3大多线切割机的设备。
也就是,瑞士的HCT、M+B、日本的NTC,另外近两年日本的TMC(东京制纲)线锯也开始打入国内市场,并取得了不错的销量。
《特种加工论文特种加工技术的发展及其对制造技术的影响》

特种加工技术的开展及其对制造技术的影响摘要:特种加工是传统加工工艺方法的重要补充和开展,已成为航空,航天,电子仪表,家用电器以及通讯,汽车,轻工业等各个机械制造行业,随着科技的进步,特种加工的种类也越来越多,本文介绍了电火花加工、电火花线切割加工、电化学加工、激光加工、电子束加工、离子束加工的特点及应用。
关键字:特种加工特点应用开展一、引言特种加工技术一个响亮的名词已在21世纪迅速崛起,特种加工技术在制造业具有重要的地位以及开展意义,显示了其在国家根底工业现代化中的战略性作用。
在一些尖端科学技术部门和新型的工业领域中,以越来越多地使用特殊物理,机械性能的新材料,如高强度、高硬度、高熔点、高脆性、高粘性、磁性材料等,有的硬度已接近甚至超过现有刀具材料的硬度,同时,有的零件加工尺寸及其微小,加工形状极其复杂,或者有的加工外表有特殊严格的外表质量要求等,使用常规的加工技术无法进行或达不到加工要求。
从而产生了多种有别于传统机械加工的新加工方法,这些加工方法广泛定义为特种加工技术。
特种加工不使用刀具,磨具等切除金属,而是采用电、磁、声、光等物理能量及化学能量或组合施加在被加工部位上,从而去除材料,或改变材料的性能,到达加工要求。
特种加工技术采用电磁声光等无形的能量,是科技的进步的最大表现,在未来的开展中,我们要不断认识特种加工的优缺点,更好的利用好特种加工技术,为未来的生产做出更大的奉献。
二、特种加工及其开展特种加工是除了单独利用机械能加工以外的所有加工方法的总称,它可以利用电能,热能,流体能,光能,声能,化学能及特殊机械能等多种能量或其复合施加在工件的被加工部位以实现材料切除的加工方法[1]。
1.特种加工的特点:特种加工在加工机理和加工形式上与传统切削和成形加工有着本质的区别,主要表现在:①不能只用机械能,与加工对象的力学性能无关。
有些加工方法如激光加工,电火花加工,等离子弧加工,电化学加工等,是利用热能,化学能,电化学能等,这些加工方法与工件的硬度,强度等力学性能无关,故可加工各种硬、软、脆、热敏、耐腐蚀、高熔点、高强度、特殊性能的金属和非金属材料。
李晓峰特种加工论文
特种加工的认识起源:直到1943年,前苏联拉扎林可夫妇研究开关触点遭受护花放电腐蚀损坏的现象和原因,发现电火花的瞬间高温可使局部的金属熔化、气化而被蚀除掉,开创和发明了电火花加工方法切削加工的本质和特点:1刀具材料比工件更硬2靠机械能把工件上多余的材料切除特种加工:应用物理、化学的方法,对有特殊要求及特殊加工对象进行加工的一种手段特种加工特点:1道具的硬度低预备加工件的硬度2靠机械能以外的能量3加工过程工具和工件之间不存在显著的切削力4可以用简单的运动加工复杂的零件特种加工对材料可加工型和结构工艺的影响:1提高了材料的可加工型2改变了零件的典型工艺路线3改变了试制新产品的模式4对产品零件的结构设计带来了很大的影响5对结构工艺性评价需新衡量6微细纳米加工手段电火花加工的原理:实际与工具和零件(正负电极)之间脉冲性火花放电时的电腐蚀现象来时除多余的金属,已达到对工件的尺寸、形状及表面质量预定的加工要求电火花加工机理:1极间介质的电离、击穿,形成放电通道2介质液分解、电极材料融化、气化热膨胀3电极材料的抛出4极间介质的消电离电火花加工条件:1必须使工件电极和工件被加工表面之间经常保持移动的放电间隙2电火花放电必须是瞬时的脉冲性放电3电火花必须在有一定绝缘性能的液体介质中进行(煤油、皂化液、去离子水)电火花教工工艺方法分类:有电火花穿孔成型加工、电火花线切割、电火花磨削和镗削、电火花同步共轭回转加工、电火花高速小孔加工、电火花表面强化与刻字电火花加工中基本规律:影响电蚀量因素:电极效应,电参数,金属材料热血常数,工作液,其他因素(加工过程稳定性,加工面积,电极材料,炭黑墨)极性效应:单纯由于正负极性不同而彼此电蚀不一样的现象。
电子轰击和离子轰击是影响极性效应重要因素正极加工:工件接脉冲电源的正极的加工在工厂中如何选择极性进行加工:当采用窄脉冲精加工时,应选用正极性加工;当采用长脉冲粗加工时,应采用负离子极性加工,可以得到较高的蚀除速度和较低的电极损耗。
《特种加工》课程论文
特种加工技术的发展及其应用————学院专业名称:机械设计制造及其自动化班级:学生学号:学生姓名:摘要:现阶段,先进制造技术不断发展,作为先进制造技术中的重要的一部分,特种加工对制造业的作用日益突显。
对什么是特种加工、特种加工的特点、种类以及发展趋势等作了描述。
阐述了特种加工在现代社会发展过程中的重要地位,大力发展特种加工的必要性。
关键词:特种加工技术、特点、变革、发展趋势1. 前言传统的机械加工技术对推动人类的进步和社会的发展起到了重大的作用。
随着科学技术的迅速发展,新型工程材料不断涌现和被采用,工件的复杂程度以及加工精度的要求越来越高,对机械制造工艺技术提出了更高的要求。
由于受刀具材料性能、结构、设备加工能力的限制,使用传统的切削加工方法很难完成对高强度、高韧性、高硬度、高脆性、耐高温和磁性等新材料,以及精密复杂、微细构件或难以处理的形状的加工。
为了解决这些加工的难题,人们不断开发研究并成功采用“传统的切削加工以外的新的加工方法——特种加工方法”解决了很多工艺问题,在生产上发挥了很大的作用,引起了机械制造工艺技术领域的许多变革。
特种加工是相对于传统的切削加工而言的,实质上是直接或复合利用电能、电化学能、化学能、光能、声能、热能、磁能、物质动能、甚至爆炸能等对工件进行加工的工艺方法的总称。
2. 正文2.1特种加工技术的特点2.1.1加工范围上不受材料强度、硬度等限制。
特种加工技术主要不依靠机械力和机械能去除材料,而是主要用其他能量(如电、化学、光、声、热等)去除金属和非金属材料,完成工件的加工。
故可以加工各种超强硬材料、高脆性及热敏材料以及特殊的金属和非金属材料。
2.1.2以柔克刚。
特种加工不一定需要工具,有的虽使用工具,但与工件并不接触,加工过程中工具和工件间不存在明显的强大机械切削力,所以加工时不受工件的强度和硬度的制约,在加工超硬脆材料和精密微细零件、薄壁元件、弹性元件时,工具硬度可以低于被加工材料的硬度。
特种加工论文范文
特种加工论文范文特种加工是一门重要的制造技术,广泛应用于飞机、船舶、汽车等行业。
本文通过对特种加工的概念、分类、应用以及发展趋势等方面的探讨,旨在深入了解特种加工的相关知识。
特种加工是指通过特殊的工艺方法,对材料进行加工和处理,以达到特定要求的一种加工方式。
它可以改变材料的组织结构和性能,使其适应特定的工作环境和使用要求。
特种加工包括表面处理、热处理、化学加工等多种形式,其技术要求较高,需要经过专门的培训和实践经验才能掌握。
特种加工按照加工目的和方法可以分为不同的分类。
例如,表面处理可以分为电镀、电泳涂装、喷涂等几种形式;热处理可以分为淬火、回火、正火等多种方式。
每种分类都有各自的特点和适用范围,在不同的工程中发挥着重要的作用。
特种加工被广泛应用于航空、汽车、军事和制造业等领域。
在航空领域,特种加工可以提高飞机零部件的耐热、耐腐蚀性能,增加其使用寿命。
在汽车领域,特种加工可以改善汽车材料的硬度和强度,提高车辆的安全性能。
在军事领域,特种加工可以改善武器装备的性能和精度,提高其作战效能。
在制造业领域,特种加工可以改善产品的外观质量,提高其市场竞争力。
特种加工在国内外都存在一定的发展趋势。
随着科技的不断进步和需求的增加,特种加工的技术水平也在不断提高。
一方面,特种加工逐渐向多功能、多种材料发展,以满足日益复杂的工程需求。
另一方面,特种加工也向绿色、环保的方向发展,以适应现代社会对环境保护的要求。
在特种加工的发展过程中,也存在一些问题和挑战。
一方面,特种加工技术的不断革新和变革,需要企业不断进行技术研发和创新,以提高核心竞争力。
另一方面,特种加工技术的应用范围广泛,需要加强行业标准和规范,以确保产品的质量和安全。
总之,特种加工是一门重要的制造技术,对于提高材料的性能和质量具有重要意义。
通过对特种加工的了解和研究,可以不断提高工程设备和产品的质量水平,满足日益增长的市场需求。
在特种加工的发展过程中,需要不断进行技术创新和标准规范,以推动特种加工技术的进一步提升和发展。
特种加工技术论文
特种加工技术摘要特种加工是指那些不属于传统加工工艺范畴的加工方法,它不同于使用刀具、磨具等直接利用机械能切除多余材料的传统加工方法。
特种加工是近几十年发展起来的新工艺,是对传统加工工艺方法的重要补充与发展,目前仍在继续研究开发和改进。
直接利用电能、热能、声能、光能、化学能和电化学能或几种复合形式直接施加在被加工的部位,从而使工件改变形状、去除材料、改变性能等。
有时也结合机械能对工件进行的加工。
特种加工中以采用电能为主的电火花加工和电解加工应用较广,泛称电加工。
特种加工亦称“非传统加工”或“现代加工方法”,泛指用电能、热能、光能、电化学能、化学能、声能及特殊机械能等能量达到去除或增加材料的加工方法,从而实现材料被去除、变形、改变性能或被镀覆等。
关键词:特种加工电火花加工激光加工技术电化学加工引言采用自动化技术,充分利用计算机技术对特种加工设备的控制系统,电源系统进行优化,加大对特种加工的基本原理,加工机理,工艺规律,加工稳定性等深入研究的力度,建立综合工艺参数自适应控制装置,数据库等,进而建立特种加工的CAD/CAM与FMS系统,使加工设备向自动化,柔性化方向发展,这是当前特种加工技术的主要发展方向。
开发新工艺方法及复合工艺。
为适应产品高技术性能要求与新型材料的加工要求,需要不断开发新工艺方法,包括微细加工和复合加工,尤其是高质量,高效率,经济型的复合加工。
1 电火花加工电火花加工主要是基于工具和工件(正、负电极)之间脉冲性火花放电时的电腐蚀现象来蚀除多余的金属。
用以达到对零件的尺寸、形状及表面质量预定的加工要求。
研究发现点火放电时火花通道中瞬时产生大量的热,达到很高的温度,足以使任何金属材料局部熔化、气化而被蚀除,形成放电凹坑。
如图1所示:图1,电火花加工原理示意图1-工件 2-脉冲电源 3-自动进给调节装置 4-工具 5-工作液 6-过滤器 7-工作液泵2 电火花加工过程及参数选择一般认为,点火加工可分为以下四个连续过程:极间介质的电离、击穿,形成放电通道;介质热分解、电极材料熔化、气化热膨胀;电极材料的抛处;极间介质的消电离。
- 1、下载文档前请自行甄别文档内容的完整性,平台不提供额外的编辑、内容补充、找答案等附加服务。
- 2、"仅部分预览"的文档,不可在线预览部分如存在完整性等问题,可反馈申请退款(可完整预览的文档不适用该条件!)。
- 3、如文档侵犯您的权益,请联系客服反馈,我们会尽快为您处理(人工客服工作时间:9:00-18:30)。
工作液在线切割加工中的应用
电火花线切割机床专用工作液伴随着线切割机床的发展至今在我国已有近50 年的历史。
在这漫长的发展过程中,随着电火花线切割机床加工性能的提高、功能设计及技术进步的演变,为适应不同时期的需求,经过几代技术人员的艰辛努力,线切割机床专用工作液从早期单一油剂型产品发展到今天的多品种多种类。
电火花线切割加工是电火花加工中的一种,是用移动着的金属丝(钼丝或钨丝)作工具电极,按预定的轨迹作进给运动电火花放电是在电极丝进给方向的周边与工件之间进行,当两者按照规定的轨迹作进给运动时,便形成了成形切割放电部位的电极丝必须用流动的工作液充分包围起来,将电极上的热量和电腐蚀物随电极丝的移动和工作液的流动被带出放电部位。
电火花线切割加工是模具加工的重要手段之一。
在模具制造技术迅速发展的今天, 对模具加工质量和效率要求越来越高, 深入了解合理选用电火花线切割加工液, 对提高电火花线切割加工的质量和加工效率起着重要作用。
1 工作液的作用与特点
电火花线切割加工原理大致分为4个阶段:极间介质的电离、击穿; 电极材料的熔化、气化膨胀; 电极材料的抛出; 极间介质的消电离。
由电火花线切割加工的原理可知道,工作液在线切割加工过程中充当着放电介质的作用, 同时还有冷却和洗涤的作用。
在实际的加工生产中, 工作液对加工工艺指标影响很大, 如切割速度、表面粗糙度、加工精度等。
快走丝电火花线切割使用的工作液一般是专用的乳化液( 目前市面上供应的乳化液有多种, 各有特点) 。
根据线切割的加工工艺特点, 它们都应该具有以下性能。
1 . 1 一定的绝缘性能
火花放电必须在具有一定的绝缘性能的液体介质中进行。
工作液的绝缘性能可使击穿后的放电通道压缩, 从而局限在较小的通道半径内火花放电, 形成瞬时和局部高温来熔化并气化金属, 放电结束后又迅速恢复放电间隙成为绝缘状态。
绝缘性能要适中, 绝缘性能太低, 则工作液成了导电体, 而不能形成火花放电; 绝缘性能太高, 则放电间隙小, 排屑难,切割速度降低。
1 .
2 较好的冷却性能
电火花放电的局部瞬时温度极高, 为防止电极丝烧断和工件表面局部退火, 必须使切削部位充分冷却, 以带走火花放电时产生的热量。
1 . 3 较好的洗涤性能
洗涤性能好的工作液, 切割时的排屑效果好, 切削速度高, 切削后表面光亮清洁,
割缝中没有油污黏糊。
1 . 4 较好的防锈性能
在加工的过程中不应产生有害气体, 不应对操作人员的皮肤、呼吸道产生刺激, 不应锈蚀工件、夹具和机床。
2 正确使用工作液
快走丝线切割机一般采用乳化油与水配制而成的工作液。
加工前要根据不同的工艺条件选择不同型号的乳化液, 检查加工液的液量及赃污程度, 保证加工液的绝缘性能、洗涤性能、冷却性能达到要求。
在配制时, 以下几点经验可供参考:
( 1)工作液的配制比例一般在 5% ~20% 范围内( 乳化油5% ~20% , 水95% ~80% ) 。
一般均按质量比例配制。
在称量不方便或要求不太严时, 也可以大致按体积比例配制。
(2) 从工件厚度来看,厚度小于30mm的薄型工件, 工作液浓度在 10% ~15% 之间 ; 30~l00mm的中厚型工件, 浓度大约在 5% ~10% 之间; 大于100mm 的厚型工件, 浓度大约在 3% ~5% 之间。
(3) 从加工精度来看,工作液浓度高时,放电间隙小,工件表面粗糙度较好, 但不利于排屑 , 易造成短路。
工作液浓度低时, 工件表面粗糙度较差, 但利于排屑。
(4) 从工件材质来看,易于蚀除的材料, 如铜、铝等材料, 可以适当提高工作液浓度, 以充分利用放电能量, 提高加工效率, 但同时也应选较大直径的电极丝进行切割, 以利于排屑充分。
(5) 在工作液中加入少量的洗涤剂、皂片等, 切割速度可以大大提高。
这是因为工作液中加入洗涤剂或皂片后, 工作液洗涤性能变好了, 有利于排屑,改善了间隙状态。
(6) 新配置的工作液加工效果并非良好, 而是要经过一段时间切割后, 加工效果才能达到最佳。
纯净的工作液不容易形成放电通道, 经过一段时间放电后, 工作液中有一些悬浮的放电产物, 容易形成放电通道, 有较好的加工效果。
但工作液不能太脏, 否者容易引起电弧放电。
在其他工艺条件相同时,改变工作液种类,配比浓度,选取不同的水质,添加不同的添加剂等,都将对加工效果产生一定的影响。
3 正确判断工作液的状态
根据工作的实际条件配制了合适的工作液, 但随着加工的时间延长, 工作液会越来越脏。
工作液太脏, 会使间隙消电离变差, 且容易发生二次放电 , 对放电加工不利, 应及时更换。
如何判断工作液的使用情况, 也有几点经验供参考:
( 1) 绕上新钼丝 , 在工件上试割约1h , 观察钼丝工件部位的颜色, 若呈灰白色, 工
作液可继续切割较薄工件, 如灰白色中夹杂黑色斑点或黑条, 黑条处直径明显变细, 用力一拉, 此处就断,需要更换新的工作液。
( 2) 有时钼丝也呈灰白色,但在切割厚工件时, 无论怎样调整加工规程, 切割电流总是不稳定,这时工作液需要更换。
( 3) 工作液变黑后综合性能就会变差,极易造成断丝。
因此要经常观其色, 嗅其味, 发现异常及时更换。
要保证工作液不能太脏, 电蚀物浓度不能太高, 使工作液保持一定的介电能力。
通过对电火花线切割工作液的分析, 科学合理地选择工作液及配比, 正确地判断工作液的使用状况, 配合其他加工参数, 可以有效地提高电火花线切割加工的加工质量和加工效率。
参考文献:
[1] 张晓燕, 魏引焕, 任威. 高速走丝线切割加工中工作液性能对加工质量的影响[ J] .
模具制造, 2004( 9) : 63- 65.
[2]刘志东. 基于复合工作液的电火花线切割加工技术研究[ J] .电加工与模具, 2008(增
刊) : 24- 30.
[3]林穗贤, 于兆勤, 郭钟宁, 等. 电火花线切割加工工作液电解质对伏安特性与丝损的影响[ J] . 电加工与模具, 2010( 3) : 48- 50.
[4]叶军. 数控低速走丝电火花线切割加工技术及市场分析[ J] .电加工与模具, 2005(增
刊) : 13- 16.
[5]步丰林, 李明辉. 超大厚度电火花线切割工艺研究[ J ] . 上海交通大学学报, 1996,
30( 9) : 122- 126.
[ 6]周东. 线切割加工中电极丝的选用[ J/ OL ] . [ 2006- 03 -07]。