一种电加热炉温度控制系统的设计
基于单片机PID算法的电加热炉温度控制系统设计
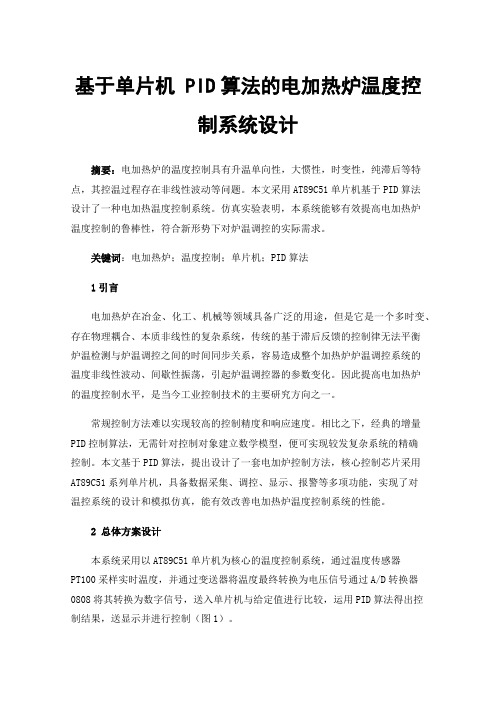
基于单片机 PID算法的电加热炉温度控制系统设计摘要:电加热炉的温度控制具有升温单向性,大惯性,时变性,纯滞后等特点,其控温过程存在非线性波动等问题。
本文采用AT89C51单片机基于PID算法设计了一种电加热温度控制系统。
仿真实验表明,本系统能够有效提高电加热炉温度控制的鲁棒性,符合新形势下对炉温调控的实际需求。
关键词:电加热炉;温度控制;单片机;PID算法1引言电加热炉在冶金、化工、机械等领域具备广泛的用途,但是它是一个多时变、存在物理耦合、本质非线性的复杂系统,传统的基于滞后反馈的控制律无法平衡炉温检测与炉温调控之间的时间同步关系,容易造成整个加热炉炉温调控系统的温度非线性波动、间歇性振荡,引起炉温调控器的参数变化。
因此提高电加热炉的温度控制水平,是当今工业控制技术的主要研究方向之一。
常规控制方法难以实现较高的控制精度和响应速度。
相比之下,经典的增量PID控制算法,无需针对控制对象建立数学模型,便可实现较发复杂系统的精确控制。
本文基于PID算法,提出设计了一套电加炉控制方法,核心控制芯片采用AT89C51系列单片机,具备数据采集、调控、显示、报警等多项功能,实现了对温控系统的设计和模拟仿真,能有效改善电加热炉温度控制系统的性能。
2总体方案设计本系统采用以AT89C51单片机为核心的温度控制系统,通过温度传感器PT100采样实时温度,并通过变送器将温度最终转换为电压信号通过A/D转换器0808将其转换为数字信号,送入单片机与给定值进行比较,运用PID算法得出控制结果,送显示并进行控制(图1)。
图1 系统总体设计方案图2.1系统硬件选择单片机是指将微处理器、存储器和输入/输出接口电路集成在一块集成电路芯版上的单片微型计算机。
单片机主要应用于工业控制领域,用来实现对信号的检测、数据的采集以及对应用对象的控制。
它具有体积小、重量轻、价格低、可靠性高、耗电少和灵活机动等许多优点。
单片机是微型计算机的一个重要分支,特别适合用于智能控制系统。
加热炉温度控制系统设计

加热炉温度控制系统设计一、引言加热炉是一种常见的工业设备,用于将物体加热至一定温度。
在许多工业过程中,加热炉的温度控制至关重要,它直接影响到产品的质量和生产效率。
因此,设计一个稳定可靠的温度控制系统对于提高工业生产的效益十分重要。
本文将介绍一个基于控制理论的加热炉温度控制系统的设计。
二、控制系统设计原理1.温度传感器:温度传感器是测量加热炉内部温度的重要组成部分。
常用的温度传感器包括热电偶和热敏电阻。
传感器将温度信号转换为电信号,并将其发送给控制器。
2.控制器:控制器接收温度传感器发送的信号,并与设定值进行比较。
根据比较结果,控制器将控制信号发送给加热器以调整加热功率。
控制器通常使用PID控制算法,它根据偏差、积分和微分项来计算控制信号。
3.加热器:加热器是加热炉温度控制系统中的执行器。
根据控制信号,加热器可以调整加热功率,从而控制加热炉的温度。
三、温度传感器选择温度传感器的选择对于温度控制系统的性能至关重要。
常见的温度传感器有热电偶和热敏电阻。
在选择传感器时需要考虑以下因素:1.测量范围:根据加热炉的工作温度范围选择合适的传感器。
不同的传感器有不同的工作温度范围。
2.精度:传感器的精度对于控制系统的准确性非常重要。
一般来说,热电偶的精度比热敏电阻高。
3.响应时间:加热炉温度的变化通常需要快速响应。
因此,传感器的响应时间也是一个重要的考虑因素。
四、控制器设计1.控制算法选择:常见的控制算法有比例控制、积分控制和微分控制。
PID控制算法结合了这三种控制算法,被广泛应用于温度控制系统。
2. 参数调节:根据具体的应用场景和系统性能要求,需要对PID控制器进行参数调节。
常见的调节方法有Ziegler-Nichols方法和临时增减法。
3.控制信号输出:控制信号输出给加热器,影响加热功率。
一般来说,控制信号越大,加热功率越高,温度升高的速度越快。
五、系统测试和优化完成控制系统的设计后,需要进行系统测试和优化。
加热炉过程自动控制系统的设计

加热炉过程自动控制系统的设计以下是一个加热炉过程自动控制系统的设计方案,详细描述了系统的组成、工作原理及控制策略:一、系统组成:1.传感器:用于检测加热炉的温度、湿度、压力、流量等参数。
2.执行器:负责控制加热炉的加热功率、燃料供给、风量等。
3.控制器:根据传感器信号,通过计算和判断,产生相应的控制命令,控制执行器的动作。
4.人机界面:提供对加热炉过程的监控、设置和操作功能,使操作员能够方便地对加热炉进行调试和控制。
二、工作原理:1.传感器采集加热炉的各项参数,并将数据传输给控制器。
2.控制器根据传感器数据进行计算和分析,将所需的控制命令传输给执行器。
3.执行器根据控制命令控制相应设备的动作,如调节加热功率、燃料供给量、风量等。
4.执行器调整加热炉的工作状态,使其达到预定的温度、湿度、压力、流量等参数。
5.人机界面可以通过可视化界面显示加热炉的运行状态和参数,操作员可以通过界面进行参数设置和调整。
三、控制策略:1.温度控制:根据加热炉的加热需求,设置温度控制器的目标温度,并通过加热功率的控制来调节温度,使其尽量趋近目标温度。
2.湿度控制:根据加热炉的加热需求,设置湿度控制器的目标湿度,并通过蒸汽量或喷雾量的控制来调节湿度,使其尽量趋近目标湿度。
3.压力控制:根据加热炉的加热需求,设置压力控制器的目标压力,并通过调节燃料供给量和风量的控制来调节压力,使其尽量趋近目标压力。
4.流量控制:根据加热炉的加热需求,设置流量控制器的目标流量,并通过调节燃料供给量和风量的控制来调节流量,使其尽量趋近目标流量。
5.故障诊断与安全保护:系统可以检测加热炉的异常状态和故障情况,并进行相应的故障诊断和安全保护措施,如当温度超过安全范围时,自动切断燃料供给等。
电加热炉控制系统的设计

基于PLC控制的加热炉温度控制系统设计

基于PLC控制的加热炉温度控制系统设计概述加热炉是工业生产中常见的设备之一,其主要作用是提供高温环境用于加热物体。
为了确保加热炉的稳定性和安全性,需要设计一个可靠的温度控制系统。
本文将介绍一个基于PLC(可编程逻辑控制器)控制的加热炉温度控制系统设计方案。
系统设计原理在加热炉温度控制系统中,PLC作为核心控制器,通过监测温度传感器的输出信号,根据预设的温度设定值和控制策略,控制加热炉的加热功率,从而实现对加热炉温度的稳定控制。
以下是系统设计的主要步骤:1.硬件设备选择:选择适合的温度传感器和控制元件,如热电偶、温度控制继电器等。
2.PLC选型:根据实际需求,选择合适的PLC型号。
PLC需要具备足够的输入输出点数和计算能力。
3.传感器连接:将温度传感器接入PLC的输入端口,读取实时温度数据。
4.温度控制策略设计:根据加热炉的特性和工艺需求,设计合适的温度控制策略。
常见的控制策略包括比例控制、积分控制和微分控制。
5.控制算法实现:根据温度控制策略,编写PLC程序,在每个采样周期内计算控制算法的输出值。
6.加热功率控制:使用控制继电器或可调功率装置,控制加热炉的加热功率。
7.温度反馈控制:通过监测实际加热炉温度和设定值之间的差异,不断修正加热功率控制,使加热炉温度稳定在设定值附近。
系统硬件设计基于PLC控制的加热炉温度控制系统的硬件设计主要包括以下几个方面:1.温度传感器:常用的温度传感器有热电偶和热敏电阻。
根据加热炉的工艺需求和温度范围,选择适合的温度传感器。
2.PLC:选择适合的PLC型号,根据实际需求确定PLC的输入输出点数和计算能力。
3.控制继电器或可调功率装置:用于控制加热炉的加热功率。
根据加热炉的功率需求和控制方式,选择合适的继电器或可调功率装置。
4.运行指示灯和报警器:用于显示系统的运行状态和报警信息。
PLC程序设计PLC程序是基于PLC的加热炉温度控制系统的关键部分,其主要功能是实现温度控制算法。
电炉温度控制系统设计
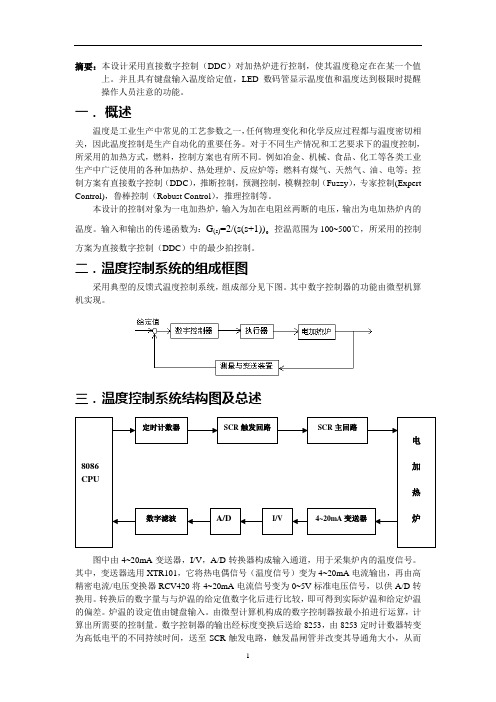
摘要:本设计采用直接数字控制(DDC)对加热炉进行控制,使其温度稳定在在某一个值上。
并且具有键盘输入温度给定值,LED数码管显示温度值和温度达到极限时提醒操作人员注意的功能。
一.概述温度是工业生产中常见的工艺参数之一,任何物理变化和化学反应过程都与温度密切相关,因此温度控制是生产自动化的重要任务。
对于不同生产情况和工艺要求下的温度控制,所采用的加热方式,燃料,控制方案也有所不同。
例如冶金、机械、食品、化工等各类工业生产中广泛使用的各种加热炉、热处理炉、反应炉等;燃料有煤气、天然气、油、电等;控制方案有直接数字控制(DDC),推断控制,预测控制,模糊控制(Fuzzy),专家控制(Expert Control),鲁棒控制(Robust Control),推理控制等。
本设计的控制对象为一电加热炉,输入为加在电阻丝两断的电压,输出为电加热炉内的温度。
输入和输出的传递函数为:G(s)=2/(s(s+1))。
控温范围为100~500℃,所采用的控制方案为直接数字控制(DDC)中的最少拍控制。
二.温度控制系统的组成框图采用典型的反馈式温度控制系统,组成部分见下图。
其中数字控制器的功能由微型机算机实现。
三.温度控制系统结构图及总述图中由4~20mA变送器,I/V,A/D转换器构成输入通道,用于采集炉内的温度信号。
其中,变送器选用XTR101,它将热电偶信号(温度信号)变为4~20mA电流输出,再由高精密电流/电压变换器RCV420将4~20mA电流信号变为0~5V标准电压信号,以供A/D转换用。
转换后的数字量与与炉温的给定值数字化后进行比较,即可得到实际炉温和给定炉温的偏差。
炉温的设定值由键盘输入。
由微型计算机构成的数字控制器按最小拍进行运算,计算出所需要的控制量。
数字控制器的输出经标度变换后送给8253,由8253定时计数器转变为高低电平的不同持续时间,送至SCR触发电路,触发晶闸管并改变其导通角大小,从而控制电加热炉的加热电压,起到调温的作用。
电炉温度控制系统的设计
电炉温度控制系统的设计电炉温度控制系统的设计摘要:自动控制系统在各个领域尤其是工业领域中有着及其广泛的应用,温度控制是控制系统中最为常见的控制类型之一。
随着单片机技术的飞速发展,通过单片机对被控对象进行控制日益成为今后自动控制领域的一个重要发展方向。
一、前言自动控制系统在各个领域尤其是工业领域中有着及其广泛的应用,温度控制是控制系统中最为常见的控制类型之一。
随着单片机技术的飞速发展,通过单片机对被控对象进行控制日益成为今后自动控制领域的一个重要发展方向。
本设计要求用单片机设计一个电炉温度控制系统。
二、电炉温度控制系统的特性温控系统主要由温度传感器、温度调节仪、执行装置、被控对象四个部分组成,其系统结构图如图1所示。
被控制对象是大容量、大惯性的电热炉温度对象,是典型的多阶容积迟后特性,在工程上往往近似为包含有纯滞后的二阶容积迟后;由于被控对象电容量大,通常采用可控硅作调节器的执行器,其具体的电路图如图2所示。
执行器的特性:电炉的温度调节是通过调节剂(供电能源)的断续作用,改变电炉丝闭合时间Tb 与断开时间Tk的比值α,α=Tb/Tk。
调节加热炉的温度,在工业上是通过在设定周期范围内,将电路接通几个周波,然后断开几个周波,改变晶闸管在设定周期内通断时间的比例,来调节负载两端交流平均电压即负载功率,这就是通常所说的调功器或周波控制器;调功器是在电源电压过零时触发晶闸管导通的,所以负载上得到的是完整的正弦波,调节的只是设定周期Tc 内导通的电压周波。
如图3所示,设周期Tc内导通的周期的波数为n,每个周波的周期为T,则调功器的输出功率为P=n×T×Pn /Tc,Pn为设定周期Tc内电压全通过时装置的输出功率。
三、电炉的电加热原理当电流在导体中流过时,因为任何导体均存在电阻,电能即在导体中形成损耗,转换为热能,按焦耳楞次定律:Q=0.2412 Rt Q—热能,卡;I一电流,安9R一电阻,欧姆,t一时间,秒。
基于单片机的电加热炉温度控制系统设计
基于单片机的电加热炉温度控制系统设计一、概述电加热炉温度控制系统是一种常见的自动化控制系统。
它通过控制加热元件的加热功率来维持加热炉内的温度,从而实现对加热过程的精确控制。
本文将介绍一种基于单片机的电加热炉温度控制系统的设计。
二、系统设计1. 硬件设计本系统采用单片机作为控制核心,传感器检测加热炉内的温度,并将数据反馈给单片机进行处理。
通过触摸屏交互界面,用户可以设定希望维持的温度值,单片机将控制加热元件的加热功率,以实现温度的稳定控制。
2. 软件设计单片机程序主要分为三个部分:(1)传感器数据采集和处理,通过定时器进行数据的采样,然后通过计算分析实现温度值的读取。
(2)温度控制,设定一个目标温度值后,单片机通过PID算法来控制加热元件的加热功率,保持温度的稳定。
(3)交互界面的设计,实现用户与系统的交互,包括设定目标温度值和实时温度显示等。
三、系统优势相对于传统的手动控制方式,本系统具有以下优势:(1)精度高,通过PID算法,可以实现对温度的精确控制,大大提高了生产效率。
(2)舒适度高,传统的手动控制方式需要人员长时间待在生产车间,而本系统的自动化控制方式,可以让人员远离高温环境。
(3)可靠性高,系统精度高,响应迅速,可以有效减少因为控制失误带来的损失。
四、结论本系统的设计基于单片机实现电加热炉温度的精确控制。
相对于传统的手动控制方式,具有精度高、舒适度高和可靠性高等优势。
在未来的生产过程中,随着物联网的发展,本系统也可以进行联网控制,实现对设备的远程控制和监控,提高设备的效率和安全性。
电加热炉温度控制系统设计
(发布日期:-6-10)电加热炉随着科学技术旳发展和工业生产水平旳提高,已经在冶金、化工、机械等各类工业控制中得到了广泛应用,并且在国民经济中占有举足轻重旳地位。
对于这样一种具有非线性、大滞后、大惯性、时变性、升温单向性等特点旳控制对象,很难用数学措施建立精确旳数学模型,因此用老式旳控制理论和措施很难达到好旳控制效果。
单片机以其高可靠性、高性能价格比、控制以便简朴和灵活性大等长处,在工业控制系统、智能化仪器仪表等诸多领域得到广泛应用。
采用单片机进行炉温控制,可以提高控制质量和自动化水平。
1 前言在人类旳生活环境中,温度扮演着极其重要旳角色。
温度是工业生产中常用旳工艺参数之一,任何物理变化和化学反映过程都与温度密切有关,因此温度控制是生产自动化旳重要任务。
对于不同生产状况和工艺规定下旳温度控制,所采用旳加热方式,燃料,控制方案也有所不同。
无论你生活在哪里,从事什么工作,无时无刻不在与温度打着交道。
自18世纪工业革命以来,工业发展对与否能掌握温度有着绝对旳联系。
在冶金、钢铁、石化、水泥、玻璃、医药等等行业,可以说几乎80%旳工业部门都不得不考虑着温度旳因素。
在现代化旳工业生产中,电流、电压、温度、压力、流量、流速和开关量都是常用旳重要被控参数。
例如:在冶金工业、化工生产、电力工程、造纸行业、机械制造和食品加工等诸多领域中,人们都需要对各类加热炉、热解决炉、反映炉和锅炉中旳温度进行检测和控制。
从市场角度看[1],如果国内旳大中型公司将温度控制系统引入生产,可以减少消耗,控制成本,从而提高生产效率。
嵌入式温度控制系统符合国家提出旳“节能减排”旳要求,符合国家经济发展政策,具有十分广阔旳市场前景。
现今,应用比较成熟旳如电力脱硫设备中,主控制器在主蒸汽温度控制系统中旳应用,已经达到了世界迈进水平。
如今,在微电子行业中。
温度控制系统也越来越重要,如单晶炉、神经网络系统旳控制。
因此。
温度控制系统经济前景非常广泛,国内旳高新精尖行业研究其应用旳意义更是更加重大。
电加热炉温度控制系统设计
电加热炉温度控制系统设计摘要:1.引言电加热炉广泛应用于金属加热、熔化、回火等工艺过程中,其温度控制对产品质量的稳定性和一致性具有重要影响。
因此,设计一套高效可靠的电加热炉温度控制系统对于提高生产效率和节约能源具有重要意义。
2.系统结构设计电加热炉温度控制系统主要由传感器、控制器、执行器和人机界面组成。
传感器用于实时感知电加热炉内部温度变化,控制器根据传感器数据进行温度控制算法的计算,执行器根据控制器输出的控制信号调节电加热炉的供电功率,人机界面用于显示和操作温度控制系统。
3.温度传感器设计温度传感器一般采用热电偶或热电阻器进行测量,其工作原理基于材料的温度和电阻之间的相关性。
在电加热炉温度控制系统中,传感器应具有快速响应、精确稳定的特性,选择合适的传感器材料和安装位置对于准确测量温度值至关重要。
4.控制器设计电加热炉温度控制系统常用的控制器包括PID控制器和模糊控制器。
PID控制器基于比例、积分和微分三个部分的线性组合,能够根据系统的误差进行相应的调节,具有简单可靠的特点。
模糊控制器基于模糊逻辑推理,能够根据模糊规则进行决策,适应性强。
选择合适的控制器取决于电加热炉的温度调节需求和实际使用场景。
5.执行器设计电加热炉的供电功率调节通常通过调整炉内的电阻或使用可调电压/电流源实现。
执行器的设计应考虑到功率调节的精度和响应时间等因素,确保控制系统能够快速准确地调节电加热炉的供电功率,实现温度控制目标。
6.人机界面设计温度控制系统的人机界面一般包括温度显示、参数设置、报警显示和历史数据查询等功能。
界面设计应简洁明了,易于操作,提供必要的温度控制信息和报警提示,方便操作员进行实时监测和调节。
7.系统安全与优化温度控制系统应考虑到系统的安全性和优化性能。
安全性包括对系统故障的检测和处理,例如传感器异常、控制器故障等;优化性能包括对温度变化的快速响应和精确控制,例如减小温度波动、提高温度稳定性等。
8.结论本文基于电加热炉温度控制系统设计原理和方法进行了综合考虑,针对不同的温度控制要求给出了相应的解决方案。