轮胎计算校核
轮胎计算重量计算公式
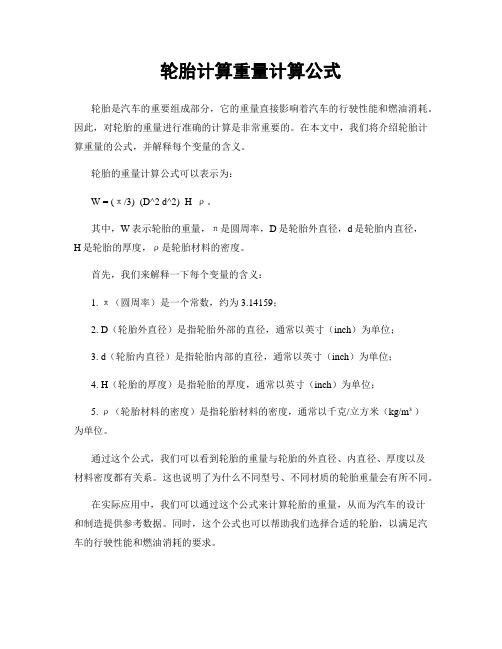
轮胎计算重量计算公式轮胎是汽车的重要组成部分,它的重量直接影响着汽车的行驶性能和燃油消耗。
因此,对轮胎的重量进行准确的计算是非常重要的。
在本文中,我们将介绍轮胎计算重量的公式,并解释每个变量的含义。
轮胎的重量计算公式可以表示为:W = (π/3) (D^2 d^2) H ρ。
其中,W表示轮胎的重量,π是圆周率,D是轮胎外直径,d是轮胎内直径,H是轮胎的厚度,ρ是轮胎材料的密度。
首先,我们来解释一下每个变量的含义:1. π(圆周率)是一个常数,约为3.14159;2. D(轮胎外直径)是指轮胎外部的直径,通常以英寸(inch)为单位;3. d(轮胎内直径)是指轮胎内部的直径,通常以英寸(inch)为单位;4. H(轮胎的厚度)是指轮胎的厚度,通常以英寸(inch)为单位;5. ρ(轮胎材料的密度)是指轮胎材料的密度,通常以千克/立方米(kg/m³)为单位。
通过这个公式,我们可以看到轮胎的重量与轮胎的外直径、内直径、厚度以及材料密度都有关系。
这也说明了为什么不同型号、不同材质的轮胎重量会有所不同。
在实际应用中,我们可以通过这个公式来计算轮胎的重量,从而为汽车的设计和制造提供参考数据。
同时,这个公式也可以帮助我们选择合适的轮胎,以满足汽车的行驶性能和燃油消耗的要求。
除了轮胎的重量计算公式外,还有一些其他因素也会影响轮胎的重量,比如轮辋的重量、轮胎的花纹设计等。
因此,在实际应用中,我们还需要综合考虑这些因素,来得到更加准确的轮胎重量。
另外,需要注意的是,轮胎的重量计算公式只是一个理论模型,实际的轮胎重量可能会受到生产工艺、材料特性等因素的影响。
因此,在实际应用中,我们还需要结合实际情况进行修正和调整。
总之,轮胎的重量计算公式为W = (π/3) (D^2 d^2) H ρ,通过这个公式,我们可以计算轮胎的重量,为汽车的设计和制造提供参考数据。
同时,我们还需要考虑其他因素的影响,来得到更加准确的轮胎重量。
轮胎的重量怎么计算公式

轮胎的重量怎么计算公式轮胎是车辆的重要组成部分,其重量不仅影响着车辆的燃油消耗和行驶性能,也直接关系到车辆的安全性能。
因此,了解轮胎的重量计算公式对于车辆制造和维护都是非常重要的。
下面将介绍轮胎的重量计算公式及其相关知识。
一、轮胎的重量计算公式。
轮胎的重量主要由轮胎胎体和轮辋组成。
轮胎胎体是由胎面、侧壁和内层组成,而轮辋是支撑轮胎的金属部分。
轮胎的重量可以通过以下公式进行计算:轮胎重量 = 胎体重量 + 轮辋重量。
其中,胎体重量可以通过以下公式进行计算:胎体重量 = 胎面重量 + 侧壁重量 + 内层重量。
轮辋重量可以通过以下公式进行计算:轮辋重量 = (轮辋外径轮辋内径) ×轮辋宽度×轮辋材料密度。
在实际应用中,轮胎的重量还受到胎面花纹、轮胎结构、胎体材料、轮辋材料和轮胎尺寸等因素的影响,因此在计算轮胎重量时需要综合考虑这些因素。
二、轮胎重量的影响因素。
1. 胎面花纹。
轮胎的胎面花纹不仅影响着车辆的抓地力和操控性能,也直接影响着轮胎的重量。
一般来说,花纹越深、越复杂的轮胎重量会越重。
因此,在设计轮胎时需要综合考虑花纹的设计和轮胎的重量。
2. 轮胎结构。
轮胎的结构分为斜交式和径向式两种,不同的结构对轮胎的重量也会产生影响。
一般来说,径向式轮胎比斜交式轮胎重量要轻。
3. 胎体材料。
轮胎的胎体材料一般为橡胶,不同种类的橡胶材料对轮胎的重量也会产生影响。
高性能的橡胶材料一般比普通的橡胶材料要轻。
4. 轮辋材料。
轮辋一般由铝合金或钢铁制成,不同的材料对轮胎的重量也会产生影响。
铝合金轮辋比钢铁轮辋要轻。
5. 轮胎尺寸。
轮胎的尺寸也会对其重量产生影响。
一般来说,尺寸越大的轮胎重量会越重。
三、轮胎重量的计算方法。
在实际生产中,轮胎的重量可以通过以下方法进行计算:1. 实际称重法。
将已经生产好的轮胎放在称重台上进行称重,得到轮胎的实际重量。
2. 数值模拟法。
通过计算机辅助设计软件对轮胎的结构进行模拟,然后根据材料的密度和轮胎的尺寸计算轮胎的重量。
整车法规校核(整车尺寸及质量限值)

D2=10.2m
T
D1=25m
图1-3
1.2.2. 车辆质量限值要求 1. 最大允许轴荷<=该轴轮胎数×3000kg 2. 最大允许总质量<=4900kg 3. 车辆轴荷要求:GB 车辆轴荷>=车辆最大总质量×25%,EEC(3.2.1) 车辆前轴轴荷>=车辆 最大总质量×30%
所属范围 : 总布置@ 乘员舱布置 设计指南
注:法规包括了汽车、挂车及汽车列车的要求,本指南仅针对于乘用车而言。
1.2.1. 车辆外廓尺寸要求
1. GB与EEC对乘用车车辆尺寸的限值相同,如表1-1、3) 12000mm
车宽(W103) 2900mm
车高(H100) 4000mm
表1-1
2. 后视镜单侧外伸量的限值(仅GB)为见表1-2、图1-1、图1-2
整车尺寸及质量限值
1 –车辆尺寸与质量限值
1.1输入与设定信息
做车辆尺寸/质量校核,需要的数据为:整车外表面数据整车质量/轴荷相关参数。
Page 1/90 返回目录
1. 2 法规要求与校核
➢车辆尺寸/质量校核相关法规为:GB 1589-2004,92/21/EEC,美标没有相关法规。 ➢GB 1589-2004与92/21/EEC要求基本相同。
当Δh1(外后视镜高度)
<1800mm (G.V.W.)
要求Δw (后视镜单侧外伸量)
<=200mm
>=1800mm (G.V.W.) <=290mm
表1-2
3. 天窗等开启时,要求超出车高部分Δh2<=300mm (图1-1) (仅GB)
Δw-right
Δw-left
W103
图1-1
(完整word版)驱动桥转矩校核

(完整word版)驱动桥转矩校核
驱动桥转矩校核
一、按驱动打滑转矩确定从动齿轮计算转矩
公式:T cs=G×m×ζ×R/η
字母含义:
T cs-—计算转矩(N.m)
G --满载状态下驱动桥静载荷(N),1。
6T=16000N
M -—汽车最大加速度时的后轴负荷转移系数,取1。
2
ζ——轮胎与路面的附着系数,取0.85
R ——轴轮滚动半径(m),365mm
η—-主减速器主动齿轮到车轮的传动效率,η=0.9
T cs=16000×1。
2×0.85×0.356/0。
9≈6455(N.m)
二、按发动机最大转矩和变速箱最低档传动比确定从动轮的计算转矩
公式:T ce=T e×i bs×i zj×η1
字母含义:
T ce—-计算转矩(N。
m)。
T e -—发动机最大转矩(N.m), 285 N.m
I bs --变速箱最大传动比, 5.441
i zj --主减速比, 4。
1
η1 ——发动机到万向传动轴之间的传动效率,取0。
85。
T ce=285×5。
441×4.1×0.85≈5375(N。
m).
三、后桥储备系数ξ
ξ=(T CS-T CE)/ T C=(6455-5375)/5375×100%=20.09%。
总布置中后轮跳动校核
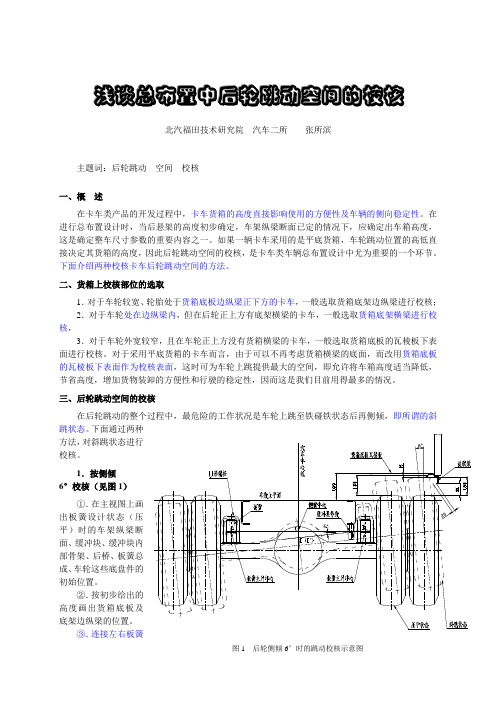
浅谈总布置中后轮跳动空间的校核北汽福田技术研究院汽车二所张所滨主题词:后轮跳动空间校核一、概述在卡车类产品的开发过程中,卡车货箱的高度直接影响使用的方便性及车辆的侧向稳定性。
在进行总布置设计时,当后悬架的高度初步确定,车架纵梁断面已定的情况下,应确定出车箱高度,这是确定整车尺寸参数的重要内容之一。
如果一辆卡车采用的是平底货箱,车轮跳动位置的高低直接决定其货箱的高度,因此后轮跳动空间的校核,是卡车类车辆总布置设计中尤为重要的一个环节。
下面介绍两种校核卡车后轮跳动空间的方法。
二、货箱上校核部位的选取1.对于车轮较宽、轮胎处于货箱底板边纵梁正下方的卡车,一般选取货箱底架边纵梁进行校核;2.对于车轮处在边纵梁内,但在后轮正上方有底架横梁的卡车,一般选取货箱底架横梁进行校核,3.对于车轮外宽较窄,且在车轮正上方没有货箱横梁的卡车,一般选取货箱底板的瓦棱板下表面进行校核。
对于采用平底货箱的卡车而言,由于可以不再考虑货箱横梁的底面,而改用货箱底板的瓦棱板下表面作为校核表面,这时可为车轮上跳提供最大的空间,即允许将车箱高度适当降低,节省高度,增加货物装卸的方便性和行驶的稳定性,因而这是我们目前用得最多的情况。
三、后轮跳动空间的校核在后轮跳动的整个过程中,最危险的工作状况是车轮上跳至铁碰铁状态后再侧倾,即所谓的斜跳状态。
下面通过两种方法,对斜跳状态进行校核。
1.按侧倾6°校核(见图1)①.在主视图上画出板簧设计状态(压平)时的车架纵梁断面、缓冲块、缓冲块内部骨架、后桥、板簧总成、车轮这些底盘件的初始位置。
②.按初步给出的高度画出货箱底板及底架边纵梁的位置。
③.连接左右板簧主片中心A、B两点,与汽车中心线交于C点,则C点为汽车的侧倾中心。
④.过右侧缓冲块骨架中点D,向左作一下倾6°的斜线⑤.过C点作6°斜线的垂线,与之交于E点⑥.重绘一后桥(带车轮),作出其桥上平面中点E’点⑦.将新桥旋转6°,使其与斜线平行。
车轮跳动与轮罩设计校核规范标准

上海同济同捷科技有限公司企业标准TJI/YJY车轮跳动与轮罩设计校核规范标准2005-XX-XX发布2005-XX-XX实施上海同济同捷科技有限公司发布TJI/YJY前言防止车轮转向及跳动时与车体发生运动干涉,特制定此校核标准。
本标准的附录A为规范性附录。
本标准由上海同济同捷科技有限公司提出。
本标准由上海同济同捷科技有限公司质量与项目管理中心负责归口管理。
本标准主要起草人:梅禹目录一、概述 ............................................. 错误!未定义书签。
二、某车转向轮跳动校核........................ 错误!未定义书签。
2.1 前轮内外转向角 ........................................ 错误!未定义书签。
2.2 车轮跳动量 ............................................... 错误!未定义书签。
2.3 某车转向轮跳动校核 ................................. 错误!未定义书签。
三、某车后轮跳动校核 ........................... 错误!未定义书签。
3.1 车轮跳动量 ............................................... 错误!未定义书签。
3.2某车后轮跳动校核.................................... 错误!未定义书签。
四、结论............................................... 错误!未定义书签。
参考文献.......................................... 错误!未定义书签。
一、概述此校核的目的是确定车轮上跳至极限位置时占用的空间,进而确定车轮与轮罩之间的运动间隙是否足够,并由此决定前后轮罩设计的最小尺寸边界,指导轮罩的进一步设计。
汽车总布置设计指南(轮胎布置校核)

版本:01
6、轮胎型号及尺寸的确认 6.1、确定车型所选用的轮胎型号 6.2、进行轮胎运动校核时,所选用的轮胎数模必须是厂家提供的该型号轮胎的 标准尺寸数模。 6.3、若某个车型配置有多个可选轮胎型号,需对每个轮胎的断面宽度和外直径 进行对比分析,选择最大尺寸的轮胎进行轮胎包络校核。 7、校核中对防滑链的要求 7.1、驱动轮必须配备防滑链,非驱动轮可不配备防滑链 7.2、防滑链的厚度H按12mm计算,若车型明确选定了某厂家提供的防滑链,则按 该厂家提供的尺寸进行校核。 8、轮胎运动范围 8.1、转向轮:转向轮运动时,配备防滑链与不配备防滑链的运动条件设置不同, 需分别进行校核。
图1
图2
第 1页 共4页
版本:01
3.10、径向间隙:胎冠与周边零部件间隙。 3.11、侧面间隙:胎肩及胎侧与周边零部件间隙。 3,12、面接触:面接触指可能存在的干涉是周边零部件的面型结构(如轮罩表面、 纵梁侧面等)与轮胎产生干涉,这种干涉不会对轮胎造成致命损坏,不会对行驶 安全性造成严重影响。 3.13、边接触:边接触指可能存在的干涉是周边零部件的边型结构(如纵梁翻边、 侧围翻边等)与轮胎产生干涉,这种干涉会导致轮胎被划破、割裂或刺穿等,会 对轮胎造成致命损坏,会对行驶安全性造成严重影响。 3.14、标准尺寸数模:与GB/T2978中提及的新胎尺寸一致的轮胎数模。 4、轮胎与周边零部件的关系:车辆行驶过程中,轮胎存在前后旋转、转向及遇 到路面不平而产生的跳动等多种运动状态,轮胎在运动过程中,周边存在两种状 态零部件,在校核时需要区别对待。 4.1、轮胎运动时,随轮胎一起运动的零部件:这些零部件通常是随着轮胎一起 运动的零部件,包括摆臂、减振器、转向横拉杆等。由于这些件无法通过运动包络 校核间隙关系,因此需要动态地分析与车轮的间隙。 4.2、轮胎运动时,不随轮胎一起运动的零部件:这些零部件通常不随轮胎运动 而运动,主要是车身件或安装固定在车身上的零部件,包括副车架、纵梁、保 险杠、轮罩装饰件等。这些件与轮胎的运动间隙关系可以通过测量与轮胎运动包 络的间隙获得。 5、校核过程
矿车车轮结构设计,强度校核

矿车车轮结构设计,强度校核一、引言矿车作为矿山运输的主要工具,其轮子的结构设计和强度校核对于提高矿车的运输效率、延长矿车的使用寿命至关重要。
本文将从矿车车轮的结构设计和强度校核方面入手,探究如何设计出更加稳定、坚固的矿车。
二、矿车车轮结构设计矿车车轮一般由轮辋和车轮轮缘两部分组成,轮辋负责承受车轮轮缘的载荷,轮缘则负责与轨道接触,传递车轮的力和扭矩。
矿车车轮的结构设计需要考虑以下几个方面:1. 轮辋的设计轮辋是矿车车轮结构的关键部分,其主要作用是承受车轮轮缘的载荷并传递给车轮轴。
轮辋的设计需要考虑到承载能力、强度和刚度等因素。
一般采用钢板冲压成型的方式来制造轮辋,其设计参数需要考虑车轮负载和工作条件等因素。
2. 车轮轮缘的设计车轮轮缘是矿车车轮的另一个关键部分,其主要作用是与轨道接触,传递车轮的力和扭矩。
车轮轮缘的设计需要考虑到磨损、强度和刚度等因素。
在磨损方面,车轮轮缘需要使用高强度的材料来提高其耐磨性。
在强度和刚度方面,设计参数需要考虑车轮负载和工作条件等因素。
3. 配合设计的优化车轮轮缘与轮辋之间的配合是矿车车轮设计中不可忽视的方面。
过松或过紧的配合都会对矿车的安全以及轮子的使用寿命造成影响。
需要通过优化设计轮辋和轮缘的尺寸和间隙,实现最佳的配合。
三、矿车车轮强度校核矿车车轮在工作中承受的荷载方式比较复杂,其强度校核需要考虑到静态荷载、动态荷载、冲击荷载、转矩荷载等多种荷载方式。
下面从轮辋和车轮轮缘两个方面介绍矿车车轮的强度校核。
1. 轮辋的强度校核轮辋的强度校核需要考虑到轮辋在轮轴上的弯曲应力、剪切应力和挤压应力等。
计算时还需要考虑轮辋的变形和塑性应变等因素。
一般采用有限元分析法进行轮辋的强度校核,通过对轮辋进行模拟荷载的分析,确定其结构是否合理、强度是否足够。
还需要进行现场测试和检验,确保轮辋的强度和刚度等参数符合要求。
2. 车轮轮缘的强度校核车轮轮缘的强度校核需要考虑到轴向力、径向力、剪切力、扭矩等荷载形式对轮缘的影响。
- 1、下载文档前请自行甄别文档内容的完整性,平台不提供额外的编辑、内容补充、找答案等附加服务。
- 2、"仅部分预览"的文档,不可在线预览部分如存在完整性等问题,可反馈申请退款(可完整预览的文档不适用该条件!)。
- 3、如文档侵犯您的权益,请联系客服反馈,我们会尽快为您处理(人工客服工作时间:9:00-18:30)。
第 2 页,共 2 页
前轮最小胎压
后轮最小胎压
3、对于车辆最高行驶速度超过一定数值的轮胎,其满载条件下所承受的最大轮荷不 应超过该车速条件下所对应负荷能力的百分比
第 1 页,共 2பைடு நூலகம்页
轮胎计算与校核
(ETRTO 2010)
车辆最高时速 200 kph 速度符号对应最高车速
——
DATE
注:以下 部分需要填写
≤270
kph
344.000 416.250 522.900
1、满载条件下的最大轮荷,不超过所选轮胎的最大负荷能力
❈不同胎压下轮胎负荷能力(kg) 负荷指数 180kPa 96 小结1 545 190kPa 570 200kPa 595 180 210kPa 620 kPa 220kPa 640 230kPa 665 240kPa 685 180 250kPa 710 kPa
R
mm mm mm mm mm mm ——
17
最大使用高度 最大使用外径 最大使用宽度 最大负荷能力 理论轮辋宽度
96
129 690 242 710 157.5 0.7 7.0 J
W
mm mm mm kg mm —— ——
理论轮辋宽度系数 选用轮辋规格
# 能力校核
车型 载荷工况
整备质量 设计载荷 满载载荷
整车重 量 (kg)
1600 1850 2100
前轴分 配 (%)
57.0% 55.0% 50.2%
前轴荷 (kg)
912.000 1017.500 1054.200
后轴荷 (kg)
688.000 832.500 1045.800
前轮荷 (kg)
456.000 508.750 527.100
后轮荷 (kg)
轮胎计算与校核
(ETRTO 2010) # 轮胎规格
断面宽 高宽比 结构代号 轮辋直径
DATE
注:以下 部分需要填写
负荷指数
速度符号
225 # 基本参数
静力半径 滚动半径 设计断面高度 新胎设计外径 新胎设计断面宽度 轮辋名义直径 标准轮辋规格
55
312.72 330.09 124 680 233 432 7.0J
最高车速对应轮胎负荷能力的百分比 ❈不同胎压下轮胎负荷能力(kg) 负荷指数 180kPa 96 小结3 —— 190kPa —— 200kPa —— 0
210kPa —— kPa
220kPa ——
230kPa ——
240kPa —— 0
250kPa —— kPa
前轮最小胎压
后轮最小胎压
结论
1、轮胎承载能力 2、最小胎压设定值 车轮 胎压 前轮 200 后轮 180
前轮最小胎压
后轮最小胎压
2、设计载荷条件下的最大轮荷,不超过所选轮胎负荷指数对应负荷能力的88%
❈不同胎压下轮胎负荷能力(kg) 负荷指数 180kPa 96 小结2 479.6 190kPa 501.6 200kPa 523.6 200 210kPa 545.6 kPa 220kPa 563.2 230kPa 585.2 240kPa 602.8 180 250kPa 624.8 kPa