镁合金的强化机制
双相结构的镁合金

双相结构的镁合金引言:镁合金作为一种轻质高强度材料,在航空、汽车和电子等领域具有广泛的应用前景。
而双相结构的镁合金,由于其独特的组织结构和优异的性能,成为当前研究的热点之一。
本文将从双相结构的定义、形成机制、性能特点以及应用前景等方面进行探讨。
一、双相结构的定义双相结构是指材料中同时存在两种或两种以上的组织相,其特点是相互间有明显的界面。
在镁合金中,常见的双相结构包括α-Mg相和Mg17Al12相、α-Mg相和β-Mg17Al12相等。
二、双相结构的形成机制双相结构的形成机制主要与合金元素的添加和热处理工艺有关。
在镁合金中,添加适量的合金元素如铝、锌等可以改变镁的晶体结构,形成α-Mg相和Mg17Al12相等不同的组织相。
而热处理工艺则通过控制合金的加热、保温和冷却过程,使不同相的晶粒尺寸和分布得以调控,从而形成双相结构。
三、双相结构的性能特点1. 高强度:双相结构的镁合金由于同时存在两种或两种以上的组织相,其晶界、相界和孪晶等界面对材料的强度起到了增强作用,使得合金的强度大大提高。
2. 良好的塑性:双相结构的镁合金具有良好的塑性,可以在外力作用下发生塑性变形,适应复杂的加工工艺要求。
3. 优异的耐腐蚀性:镁合金中的双相结构可以提高合金的耐腐蚀性能,降低材料的腐蚀速率,延长材料的使用寿命。
4. 良好的热稳定性:双相结构的镁合金在高温条件下具有较好的热稳定性,能够保持较高的强度和塑性。
四、双相结构的应用前景1. 航空领域:双相结构的镁合金由于其高强度和轻质特性,可用于制造飞机零部件,如发动机叶片、机身结构等,以减轻飞机的重量,提高燃油效率。
2. 汽车领域:双相结构的镁合金可以应用于汽车车身和发动机部件,以减轻汽车整体重量,提高汽车的燃油经济性和行驶性能。
3. 电子领域:双相结构的镁合金还可以用于制造电子设备的外壳和散热器等部件,以提高设备的散热效果和稳定性。
结论:双相结构的镁合金由于其独特的组织结构和优异的性能,在航空、汽车和电子等领域具有广泛的应用前景。
AZ31镁合金组织性能的影响分析

摘要挤压变形AZ31镁合金组织以绝热剪切条纹和细小的α再结晶等轴晶为基本特征。
挤压变形可显著地细化镁合金晶粒并提高镁合金的力学性能。
随挤压比的增大,晶粒细化程度增加,晶粒尺寸由铸态的d400μm减小到挤压态的d12μm(min);强度、硬度随挤压比的增大而增大,延伸率在挤压比大于16时呈单调减的趋势。
轧制变形使板材晶粒明显细化,硬度提高。
AZ31合金中添加Ce,其铸态组织中能够形成棒状Al4Ce相,并能改善合金退火态组织和力学性能;添加Ce可以改善AZ31的综合力学性能。
关键词:AZ31变形镁合金;强化机制;组织;性能绪论20世纪90年代以来,作为最轻金属结构材料的镁合金的用量急剧增长,在交通、计算机、通讯、消费类电子产品、国防军工等诸多领域的应用前景极为广阔,被誉为“21世纪绿色工程材料”,许多发达国家已将镁合金列为研究开发的重点。
大多数镁合金产品主要是通过铸造生产方式获得,变形镁合金产品则较少。
但与铸造镁合金产品相比,变形镁合金产品消除了铸造缺陷,组织细密,综合力学性能大大提高,同时生产成本更低,是未来空中运输、陆上交通和军工领域的重要结构材料。
目前,AZ31镁合金的应用十分广泛,尤其用于制作3C产品外壳、汽车车身外覆盖件等冲压产品的前景被看好,正成为结构镁合金材料领域的研究热点而受到广泛重视。
第1章挤压变形对AZ31镁合金组织和性能的影响1.1 挤压变形组织特征及挤压比的影响作用图1-1为动态挤压变形过程中的组织变化。
动态变形过程大致分为3个区域:初始区、变形区和稳态区,分别对应着不同的组织。
图1-1a为初始区挤压变形前的铸态棒料组织。
由粗大的α-Mg树枝晶和分布其间的α-Mg+Mg17Al12共晶体组成,枝晶形态十分发达,具有典型的铸造组织特征。
晶粒尺寸为112~400μm。
图1-1b为变形区近稳态区组织。
图中存在大量无序流线,流线弯曲度大、方向不定且长短不一,显然这种组织特征是在挤压力作用下破碎的树枝晶晶臂(α固溶体)发生滑移、转动的结果。
镁合金的强化机制
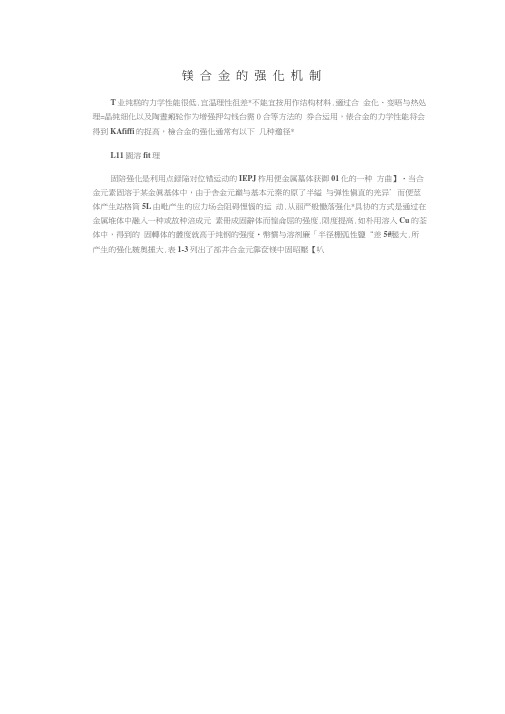
镁合金的强化机制T业纯糕的力学性能很低.宜温理性徂差*不能宜按用作结构材料.適过合金化、变晤与热处理=晶純细化以及陶晝瘢轮作为增强押勾钱台需0合等方法的券合运用,俵合金的力学性能将会得到KAfiffi的捉高,檢合金的强化通常有以下几种邀径*L11園溶fit理固陪强化是利用点録陥对位错运动的IEPJ柞用便金属墓体获御01化的一种方曲】・当合金元素固溶于某金眞基体中,由于舎金元巔与基本元秦的原了半縊与弹性愼直的羌异’而便莖体产生站格筒5L由毗产生的应力场会阻碍悝惱的运动.从丽严般慟落强化*具协的方式是通过在金属堆体中融入一种或故种涪成元素冊成固辭体而惶侖屈的强度.陨度提髙.如朴用溶入Cu的荃体中,得到的固轉体的叢度就高于纯钢的强度•幣慣与溶剂廉「半径棚弧性鹽“差5#腿大.所产生的强化皴奧捶大.表1-3列出了部井合金元靠奁镁中固昭壓【叭A IT样分合介尢素虚4中拘H)況zt*元素用溶度相系转交3处悼尔分《L%頂逼分数/%Ag 3.815,0共晶471Al11.812.7共晶437Cd100100八析■Gd 4.5323.69共晶54«Li17.0 5.5共品588Mn 1.022包晶652Nd13共品552Y 3.7512.5共晶565Zn 2.4 6.2共崩347Zr 1.0 3.3包晶65313.2第二相粒于强化页二相粒于强化可分为沉淀强化和弥散强化:沉淀强化即町效彊化•因获得第二相粒子的工艺不同,第二相粒子强化有不同的名称:①酒过相变热处理获得的,林为析出硬化、沉淀強化或时效强化:②通过粉末烧结或内氧化敬御的.称为號散强化㈢.冇时也不加区別的混称为分做强化或粒子张比.合金产生时效强化亦須满兀一•定条件.即合令元素在基体中的迥溶度下降而彼少.时效可强化的合金在a单相区长时何保温,可以使铸态合金中分称在詁界或胡内的第二相分解,合金元素原子分布于基体抽格,如果此时以较大的冷却速愷(如水冷)使合金冷却到室温,即可御到过饱和固溶体.过饱和固陷体在a十"两相区适当温度下进行长时间时效处理,过诲和固溶体将会分解成为a基体和沉淀郴"弥敢分布的沉淀相粒子阴碍位错运动从而提髙合金强度。
变形镁合金的分类、强化机制以及塑性加工
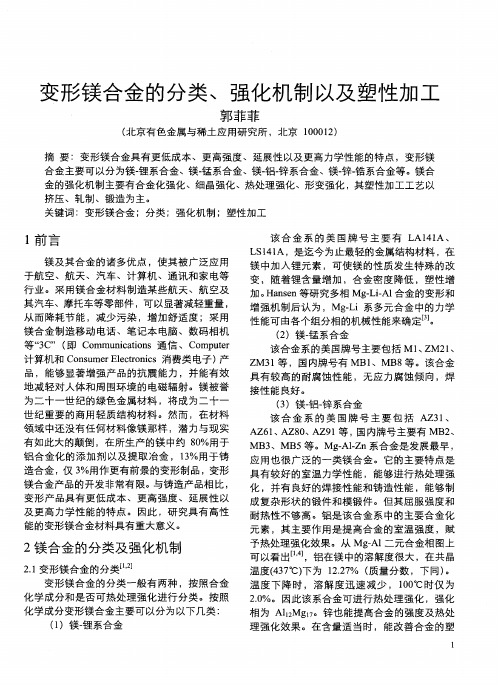
从 而 降耗 节 能 ,减 少 污 染 ,增 加舒 适 度 ;采用 镁 合 金 制造 移 动 电话 、笔 记 本 电脑 、数码 相 机 等“ 3 C ”( 即 C o mmu n i c a t i o n s通 信 、 C o m p u t e r 计 算机 和 C o n s u me r E l e c t r o n i c s消 费类 电子 ) 产 品 ,能够 显 著 增 强产 品的抗 震 能 力 ,并 能有 效 地 减 轻对 人 体 和周 围环境 的 电磁辐 射 。镁 被 誉
MB 3 、MB5等 。Mg — A1 一 Z n系合 金是 发展 最早 , 应 用 也 很 广泛 的一 类镁 合 金 。它 的主 要 特点 是 具 有 较好 的室 温 力学 性 能 ,能 够进 行 热 处理 强 化 ,并有 良好 的焊 接 性 能和 铸造 性 能 ,能够 制 成 复 杂 形状 的锻 件 和 模锻 件 。但 其 屈 服 强度 和 耐 热性 不 够 高 。铝 是 该合 金 系 中 的主 要合 金 化 元 素 ,其 主 要作 用 是 提 高合 金 的 室温 强 度 ,赋 予 热处 理 强化效 果 。从 Mg — A1 二元 合金相 图上 可 以看 出¨ J ,铝 在镁 中的 溶解 度很 大 ,在 共 晶
变形镁 合金 的分类 \强化机 制 以及塑性加工
郭菲菲
( 北 京有 色金 属与稀 土 应 用研 究所 ,北 京 1 0 0 0 1 2 )
摘 要 :变形 镁合 金 具有 更低 成 本 、更 高强 度 、延 展性 以及 更 高 力学性 能 的特 点 ,变形 镁 合金主要可以分为镁- 锂系合金、镁- 锰系合金、镁一 铝一 锌系合金、镁一 锌一 锆系合金等。 镁合
高强度镁合金研发生产方案(二)
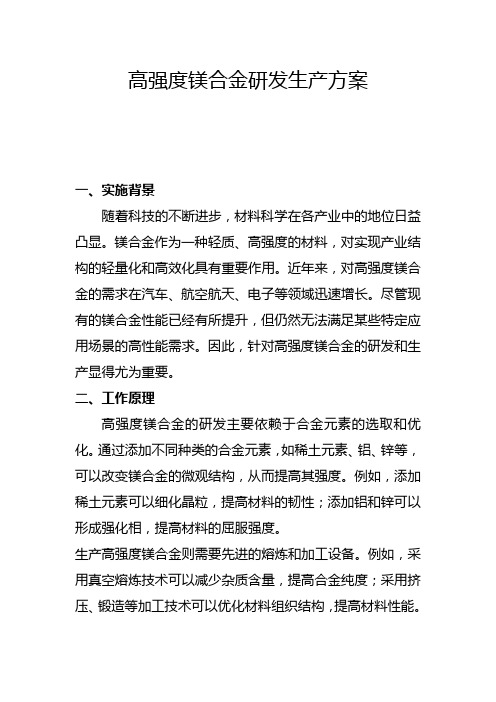
高强度镁合金研发生产方案一、实施背景随着科技的不断进步,材料科学在各产业中的地位日益凸显。
镁合金作为一种轻质、高强度的材料,对实现产业结构的轻量化和高效化具有重要作用。
近年来,对高强度镁合金的需求在汽车、航空航天、电子等领域迅速增长。
尽管现有的镁合金性能已经有所提升,但仍然无法满足某些特定应用场景的高性能需求。
因此,针对高强度镁合金的研发和生产显得尤为重要。
二、工作原理高强度镁合金的研发主要依赖于合金元素的选取和优化。
通过添加不同种类的合金元素,如稀土元素、铝、锌等,可以改变镁合金的微观结构,从而提高其强度。
例如,添加稀土元素可以细化晶粒,提高材料的韧性;添加铝和锌可以形成强化相,提高材料的屈服强度。
生产高强度镁合金则需要先进的熔炼和加工设备。
例如,采用真空熔炼技术可以减少杂质含量,提高合金纯度;采用挤压、锻造等加工技术可以优化材料组织结构,提高材料性能。
三、实施计划步骤1.合金元素选择与优化:选取不同的合金元素,进行配比实验,通过力学性能测试,确定最佳的合金成分。
2.熔炼与加工工艺研究:研究并优化真空熔炼、挤压、锻造等工艺,以获得理想的材料组织结构。
3.热处理工艺研究:研究并优化热处理工艺,以获得最佳的力学性能。
4.产品制备与性能检测:制备不同规格的高强度镁合金产品,进行力学性能、耐腐蚀性等方面的检测。
5.产业化推广:将研发的高强度镁合金应用于实际生产中,结合产业需求进行持续优化。
四、适用范围高强度镁合金适用于对材料轻量化和高性能要求较高的领域,如:•汽车制造业:作为替代钢铁和铝合金的轻量化材料,可提高车辆燃油效率和动力性能。
•航空航天:用于制造飞机零部件和卫星结构件,提高性能并降低重量。
•电子产品:用于制造轻薄、高性能的电子产品外壳和内部结构件。
•建筑行业:作为轻质、高强度的建筑材料,可提高建筑物的抗震性能和节能效果。
五、创新要点1.研究新型的合金元素配比,提高镁合金的强度和韧性。
2.探索先进的熔炼和加工工艺,获得理想的材料组织结构。
镁合金的热处理

镁合金的热处理热处理是改善或调整镁合金力学性能和加工性能的重要手段。
镁合金的常规热处理工艺有退火和固溶时效两大类。
部分热处理工艺可以降低镁合金铸件的铸造内应力或淬火应力,从而提高工件的尺寸稳定性。
镁合金能否进行热处理强化完全取决于合金元素的固溶度是否随温度变化。
当合金元素的固溶度随温度变化时,镁合金可以进行热处理强化。
可热处理强化镁合金 铸造镁合金 Mg-A1-Mn 系(如AM100A )Mg-A1-Zn 系(如AZ63A 、AZ81A 、AZ91C 和AZ92C等) Mg-Zn-Zr 系(如ZK51A 和ZK61A 等) Mg-RE-Zn-Zr 系(如EZ33A 和ZE41A )Mg-Ag-RE-Zr 系(如QE22A )Mg-Zn-Cu 系(如ZC63A )变形镁合金 Mg-Al-Zn 系(如AZ80A ) Mg-Zn-Zr 系(如ZK60A ) Mg-Zn-Cu 系(如ZC71A )某些热处理强化效果不显著的镁合金通常选择退火作为最终热处理工艺。
镁合金热处理的最主要特点是固溶和时效处理时间较长,其原因是因为合金元素的扩散和合金相的分解过程极其缓慢。
由于同样的原因,镁合金淬火时不需要进行快速冷却,通常在静止的空气中或者人工强制流动的气流中冷却。
一、 热处理类型和选择符号意义 符号 意义 F加工状态 T4 固溶处理(然后自然时效) O完全退火 T5 人工时效 H1加工硬化 T6 固溶处理后人工时效 H2加工硬化后退火 T7 固溶处理后稳定化处理 T2去应力退火 T8 固溶处理后冷加工、人工时效 T3 固溶处理后冷加工 T9固溶处理、人工时效后冷加工 铸造镁合金和变形镁合金都可以进行退火(O )、人工时效(T5)、固溶(T4)以及固溶加人工时效(T6、T61)处理,其热处理规范和应用范围与铸造铝合金的基本相同。
镁合金的扩散速度小,淬火敏感性低,从而可以在空气中淬火;个别情况下也可以采用热水淬火(如T61),其强度比空冷T6态的高。
镁合金力学性能强化的几种途径

镁合金力学性能强化的几种途径摘要对近几年镁合金力学性能强化的研究进行了总结,主要途径归纳为三个方面,一是热处理,二是合金化,三是加工工艺。
关键词:镁合金力学性能热处理合金化加工工艺镁及镁合金是目前最轻的金属结构材料,具有密度低、比强度和比刚度高的特点,而且还具有优良的阻尼性能、较好的尺寸稳定性和机械加工性能及较低的铸造成本。
广泛应用于航空航天、汽车和电子等行业。
但是,镁合金密排六方的晶体结构及较少的滑移系决定了其塑性变形能力较差,所以应该用一些方法来提高其力学性能,本文就近几年镁合金力学性能方面的研究进行总结,并提出建议。
1 镁及其合金的力学性能镁是一种二价的碱金属元素,属于密排六方晶系,这种密排六方结构使之在力学和物理性能方面表现出强烈的各向异性。
纯镁象其他纯金属一样,表现出相对低的强度。
其弹性模量E=45GPa,切变模量K=17GPa,比弹性模量E/ρ=25GPa。
因此必须用其他元素进行合金化以获得所需要的性能。
目前主合金元素是Al、Zn 和Re等,这些合金元素使镁合金得到不同程度的强化。
变形镁合金主要通过热变形和冷变形来提高强度。
热处理是提高镁合金力学性能的重要途径。
另外其他一些工艺或处理也能有效提高镁合金的力学性能,如颗粒增强复合材料、半固态铸造和熔体热速处理、表面处理等。
2强化途径2.1 热处理2.1.1铸造镁合金的热处理铸造镁合金的室温和高温力学性能强化途径有固溶处理和失效处理[1]。
对某高锌镁合金Mg-Zn-Al-RE进行热处理[2],固溶处理温度340℃,保护剂为硫铁矿石,保温时间20 h,热水淬火,淬火介质采用70~75℃热水;时效处理温度180℃,保温时间10 h,出炉空冷。
经固溶及时效处理后,合金的相成分主要为α-Mg,还有含微量稀土的其它固溶强化三元相。
其中比较典型的固溶强化相有Ф相Al2Mg5Zn2和τ相Mg32(Al,Zn)49。
这些强化相的弥散存在可以提高基体的力学性能[3]。
高强度镁合金研发生产方案(一)

高强度镁合金研发生产方案一、实施背景随着科技的不断进步,材料科学在各产业中的地位日益提升。
镁合金作为一种轻质、高强度的材料,对提升产业效率、降低能耗具有重要作用。
近年来,汽车、航空航天、电子等产业对镁合金的需求持续增长,带动了镁合金研发生产的热潮。
二、工作原理镁合金的研发与生产主要依赖于镁的特性及其合金化过程。
镁合金的工作原理主要是通过添加不同的合金元素,改变镁合金的显微组织,从而提高其强度、韧性、耐腐蚀性等性能。
常见的合金元素有铝、锌、锰等,这些元素的添加可以有效地提高镁合金的各项性能。
三、实施计划步骤1.材料选择与设计:根据应用需求,选择合适的镁合金成分,并设计合金的显微组织。
2.熔炼与铸造:将选定的镁合金成分在高温下熔炼,然后倒入模具中铸造。
3.热处理:通过控制加热和冷却速度,改变镁合金的显微组织,提高其性能。
4.加工与成型:将热处理后的镁合金进行机加工、挤压、锻造等操作,以满足各种形状和尺寸的需求。
5.质量检测:对镁合金成品进行各项性能检测,确保满足应用要求。
四、适用范围高强度镁合金适用于汽车、航空航天、电子、通讯等产业。
特别是在汽车轻量化趋势下,高强度镁合金可以用于制造汽车零部件,如发动机气缸体、变速器壳体等,以实现轻量化、降低油耗和提高动力性能。
五、创新要点1.成分优化:通过创新合金元素配比,开发出具有更高强度和良好韧性相结合的镁合金。
2.冶炼技术改进:引入先进的冶炼技术,如真空熔炼、电磁搅拌等,以提高镁合金的质量和性能。
3.热处理工艺优化:通过研究热处理工艺对镁合金显微组织和性能的影响,制定出更为合理的热处理制度。
4.加工成型技术提升:引入先进的加工成型技术,如精密铸造、挤压锻造等,以制造出更为复杂和精细的镁合金零部件。
5.环保考量:在冶炼和加工过程中,采取环保措施,减少废弃物产生和能源消耗。
六、预期效果通过以上创新措施的实施,预期能够实现以下效果:1.提高镁合金的强度和韧性,以满足各产业对高性能镁合金的需求。