使不良率降低的方法及运用
子午线轮胎胎体稀线不良率的解决对策

作者简介:章远甲(1984-),男,本科,助理工程师,主要从事半钢轮胎生产质量管理和工艺研究。
收稿日期:2020-09-111 问题简介1.1 胎体帘稀线的危害半钢子午线轮胎胎体稀线问题是轮胎生产制造过程中的常见缺陷,影响轮胎安全使用性能,严重时诱发轮胎漏气、断裂爆胎等质量问题发生。
1.2 胎体稀线问题现况胎体稀线是轮胎生产过程中的常见问题,该缺陷主要集中在轮胎生产过程中的成型、硫化环节。
2019年市场售后反馈中因帘布稀线问题导致的问题占比59.5%(稀线问题264条,其他问题180条)。
胎体稀线问题(图1、图2)给企业造成巨额经济损失的同时也严重影响了产品质量信誉,所以解决胎体稀线问题是公司当前重要的工作之一。
图1 稀线缺陷1.3 工序简介轮胎生产流程如图3所示。
子午线轮胎胎体稀线不良率的解决对策章远甲,路丹丹,李海艳(山东丰源轮胎制造股份有限公司,山东 枣庄 277300)摘要:本文主要分析轮胎生产过程中常见的胎体稀线这一质量问题,分析该缺陷主要集中的成型、硫化两个环节。
通过进行可行性,制定相应的措施,结合问题,采用 “5M1E ”分析法,对人、机、料、法、测五个方面进行研究,采用制作关联图的方式对产生此类质量问题的末端因素进行分析。
措施开展后,2020年废品率逐月下降,效果明显,因稀线问题导致的废品率由2019年的0.8‰,降低到2020年5月份的0.23‰,1~5月份节约7.7万元。
关键词:轮胎;胎体稀线;5M1E ;废品中图分类号:TQ336.1文章编号:1009-797X(2021)05-0052-06文献标识码:B DOI:10.13520/ki.rpte.2021.05.0112 选题依据从上级要求、生产现状两个主要方面确定课题的选定,如图4所示。
图2 稀线诱发的质量问题图3 轮胎生产流程3 对目标的可行性分析3.1 掌握现状对市场反馈的质量问题进统计,将数据绘制成排列图后进行分析。
PPM质量制

1 PPM质量制目前PPM(Parts per million,百万分率的缺陷率)质量制已在发达国家得到了广泛的应用。
PPM质量制以将产品不良率降低到百万分之一为管理目标的管理,在国际上也被称之为“最完美的管理。
”它可以形象地理解为用显微镜将管理对象的缺陷放大的同时,运用全面质量管理手段加以减少或消除,从而实现整个生产过程“零缺陷”。
它将有助于全体职工包括企业决策者在内,能了解到企业产品质量情况,然后作出相应对策来解决、提高、稳定产品质量。
其中某些数据可以作为员工质量考核、发放奖金的参考依据。
PPM质量制是企业现代化管理上水平的重要组成部分,实行PPM质量制基于三个最基本的质量保证体系,即设计质量保证、采购质量保证和工序质量保证。
世界经济发达国家及国内先进企业的成功经验表明,凡推行PPM质量制,大到庞大的整机生产,小至每一个生产工序,都能保持很低的故障率和高的直通率。
推行PPM质量制是企业经济腾飞的促进力。
SMT是一项包括SMD、组装设备、组装工艺、测试技术、辅助材料等各个环节在内的系统工程,在前期,国内的注意力较多地集中在元器件及SMT应用领域的拓展等方面,近几年来,也大大注意到了SMT工艺工序质量控制的研究和应用,取得了一些经验和成果,促进了SMT工艺工序质量的提高。
现针对SMT标准工序质量贯测实施PPM管理思想,提出PPM缺陷计算法在工艺检测中的分析和运用形式,最终实现工序质量控制目标。
2 PPM质量制在SMT工序质量监测中的应用2.1 PPM质量制的应用要点良好的PPM质量制,必须建立合理、系统的目标树,就是依据系统目标管理的原则和方法,将代表国际先进水平的“PPM水平”作为PPM目标值,然后将其层层分解,构成PPM质量制指标体系。
而在每一个目标树中都采用PPM缺陷计算的方法,通过一系列工艺控制手段,提高生产工序质量,使实际生产过程中的PPM值小于PPM目标值。
PPM缺陷数量目标值的确定建立在工序检验标准的使用基础上,并根据工序的工艺性能由质量控制和技术部门来认可。
标准作业操作手册

标准作业操作手册一、和生产现场有关的作业标准文件种类1.工艺流程图显示工艺步骤的流程图只是作业标准文件的一种,工艺流程图作为制作QC工程表时的基础资料使用。
个别接单生产的工厂只用工艺流程图作为标准书向作业者进行说明、指导。
2.图纸、部品表图纸、部品表在进行部品加工和组装作业时,作为基准资料使用。
3.作业标准书写明作业者进行的作业内容,起传达作业内容的指导作用。
4.QC工程表QC工程表内写有生产现场的工艺步骤及其作业内容。
在保证品质、技术和对生产现场的指导、监督上发挥作用。
另外,在不良品发生和劳动灾害发生时,可据此探明原因以及建立对策方案。
5.工厂规格对生产有关的各种规格作出规定,是进行各种作业时的基准资料。
以下为工厂规格的种类:图纸规格、制图规格、设计规格、产品规格、材料规格、部品规格、制造作业的标准、工程规格、治工具规格、设备规格、检查规格、机器检查工具规格、包装规格、一般规格。
二、活用作用标准书1.作业标准书的效用作业标准书具体叙述表达了在各工程内的作业方法,是创造出良品的不可缺少的手段。
除此之外还有如下一些用途:·缩小因作业者不同产生的差异。
·以有形的东西留下熟练者的技能。
·作业标准书是监督者详细进行作业说明时的资料。
·放在作业者的身边,便于他们在作业时按作业标准书的内容进行作业。
·是作业者交接班的资料。
·是工厂生产技术的信息履历资料·作业改善的基础资料。
·多能化、外发单化的实施资料。
2.作业标准书的制成时机在加工或组装作业的情况下,在按设计——试作一—设计审查进行后,一般就转移到生产设计上。
作业标准书最好是在属于其后阶段的专用工具的设计、机械选定的阶段完成。
3.作业标准书的写法·记入作业时所需的材料、部品(来自图纸、规格书等)。
·记入作业时使用的机械、治工具。
·逐条写出作业的顺序。
使不良率降低的方法及运用
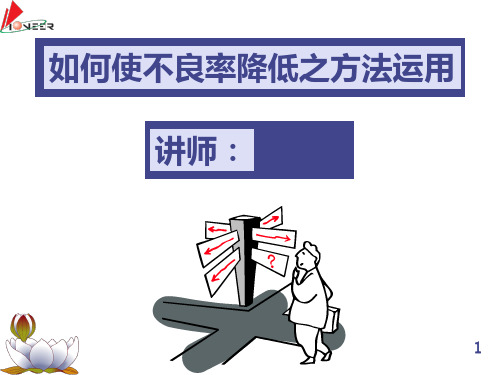
组件不良率(%) 49,000 ppm(4.9%)
5 (0.9999)5= 0.9995= 99.95%
500 ppm(0.05%)
50 (0.9999)50= 0.995= 99.5% 50 (0.999999)50=0.99995= 99.995% 500 (0.999999)500= 0.9995= 99.95% 500 (0.9999999)500= 0.99995= 99.995% 10000 (0.9999999)10000= 0.999= 99.9%
过去
现在
未来
移向
改正缺点
制程管制
预防品管
如此将产生更多顾客的满意,降低浪费 和成本和适应能随时接受改变的能力.
30
五大目标:
以Defect取代不良 以预防取代检验 以SPC取代抽样 以PPM取代% 以DPMO做为最先进这的品
管工具(6σ管理)
31
2.3. 前瞻性品质展开的应用
零不良(零缺点) (A) ‧在工程师的指导下,由作业员
40
2.4.2 顺序检查
A) 顺序检查的模式:
制程N
制程N+1
前制程 结果 的检查
本制程 加工 的检查
互助 合作
前制程 结果 的检查
本制程 加工 的检查
41
·全数检查. ·立即回馈. ·立即的改正,没有满意的措施则 不再继续加工.(可以补偿因停止 生产而产生的损失) ·由别人检查. ·规格之认同与确认.(通过标准样 本,建立客观的认知) ·5-6项重点项目检查.
输入
程 序 输出(浪费多)
人员 设备 材料 方法 环境
不合格
工作方式
密集式检验
产品
报废或 修补
运用PDCA循环降低病区不良事件的发生率

-运用PDCA循环降低病区不良事件的发生率(神经内科)为进一步增强护理人员安全意识,消除安全隐患,提高服务质量,降低和防患医疗风险,确保医疗安全,现将本年度不良事件原因进行分析,提出持续改进措施,使广大护理人员认识到落实护理规范、制度的重要性,增强防范意识,确保患者安全,是我科护理质量持续改进,要求全员护理从不良实践中汲取深刻的教训,做到举一反三,避免类似事件的再次发生。
具体总结工作如下:一、总体不良事件发生情况(共24起):一季度:跌倒1起、脱管1起二季度:口服药未按时服用1起、针刺伤1起、跌倒1起、走失1起、脱管2起、医嘱处理错误1起三季度:跌倒5起、误吸1起、脱管1起、针刺伤3起、用药错误3起、术后并发症1起(穿刺点渗血)、口服药漏服1起神经内科2015年1至9月不良事件汇总月份1月2月3月4月5月6月7月8月9月例数0 1 1 1 1 4 10 6 0 二、据上表显示7月、8月不良事件总数较前明显增加,原因分析如下:(1)学生刚下临床,对临床护理操作规范不熟。
(2)学生多,带教老师疏于管理,未做到“放手不放眼”。
(3)此阶段病房患者人数较前减少,护士安全意识降低,过于放松,查对及巡视病房力度欠缺。
三、针对上图显示,用药错误、针刺伤、跌倒和脱管分别占12%、17%、17%和29%,为我科1至9月护理不良事件高发类型,列为重点管理对象,PDCA改进措施如下:跌倒P阶段——现状调查2015年1月至8月,神经内科共发生护理不良事件24起,其中跌倒不良事件共7起,占不良事件的比率为%,因此,将跌倒列为2015年整改的重点部分之一,统计分析如下:跌倒不良事件统计表相关内容年龄神志活动时间地点跌倒史视力常需上厕所分类大于等小于6清楚欠清正常无耐力15::其他时厕所病房和病房外有无正常不佳是不是经上述统计表可看出神志清楚、活动能力正常、无跌倒史、视力正常、不常需上厕所的患者更易发生跌倒,而往往这类患者又最不易被重视为跌倒高危患者。
不良率0.7%与3.4PPM改善技法

全面品質管理(TQM、CWQC)只是 一個概念, 而六個希格瑪,無論分析、改善都以 具體的數字,來支援及驅使員工能做 事,也可以做事 。 所以傳統TQM的技術改善層級,必頇 升級成為QIT(Quality Improve Team),才能成型為六個希格瑪,從 源頭到制程一路做改善。
六個希格瑪管理是全面化的,而非只 是用在產品的流程上。 例如將收帳或採購的過程規格化,就 可以達到六個希格瑪;至於服務時間、 公文傳達及計畫核准時間等作業,只 要設定一定時間,也可以加以衡量是 否達到六個希格瑪的標準。 基於這個原則,所有的企業流程都可 適當地量化,加以統計,達到六個希 格瑪的要求。
舉例來說,假設對驗收的元件只要是 合乎品質標準,就不再做篩選直接上 線組裝,那麼同樣品質水準的元件, 當數目愈多時,成品的不良率就愈高, 以三個希格瑪的品質元件,在數目達 到二百以上時,幾乎沒有良品可給顧 客,但如採取六個希格瑪的品質元件 則可維持有99.9%以上的良品供給顧客, 所以當元件數愈多時,發生不良的機 率愈高。
問題改善活動的四步驟 三、效果維持 A.再發防止及 標準化工作
各步驟應注意事項說明
問題改善活動的四步驟 四、相互啟發 A.資料整理 B.成果發表會與交流
各步驟應注意事項說明
QC故事
讓我們來準備面對未來的挑戰
你要的是 0.7%的不良率 (3σ) 還是 3.4 PPM (6 σ)
傳統的品質管制 起源是在一九二四年,由美國貝爾 電話實驗室的工程師蕭華德 提出三個希格瑪的管制圖後,逐漸 發展, 最後變成一套現行的品質管制系統, 從那時開始大部份的產業都遵循著 這三個希格瑪的標準,
面對凡事不確定的今天,企業為尋求 明天的經營曙光,必頇理解一個顛簸 不破的法則: 愈是不景氣,愈要全方位的變革管理 ,因為市場從不等待,不管你有沒有 準備妥當。 回溯二十世紀的管理主流思潮,從品 管圈(QCC)到全面品質管理(TQM), 都希望達到相同的經營目的: 如何用最低成本,提高最大的產品價 值,最終達到顧客滿意?
不良率降低改进方案,品质管理改善办法,提升产品质量

不良率降低改善方案全文目录一、现今与将来之构想: (1)二、欲达成的目标: (1)三、指导方针: (1)四、简述目前状况: (1)五、目前的替代策略: (1)六、预期的结果: (1)七、全员要积极参加质量改善应解决以下几个问题﹕ (2)八、质量改善的程序和方法﹕ (3)九、具体的行动步骤: (3)一、现今与将来之构想:不良比率降低50 %,利润提升10%,质量目标达到6西格玛(Sigma).二、欲达成的目标:1.质量目标达到6 (Sigma)2.提升职场人员品质意识及品管水准;3.建立职场人员愉悦的品质管理与改善作法;4.达成全员参加的职场品质改善与突破现况;5.活化职场,解决问题,提升服务业务品质;6.消除本位与不良,共创更卓越品质的时代。
三、指导方针:预防为主,优质生产,过程控制,治污遵守法律,继续改善,取信客户.四、简述目前状况:内部返工/质量问题,长期以来没有彻底追究相关人员的责任,导致部分人员对工作无责任感,毫无质量意识!做多与做少,做好与做坏是一个样;由于奖罚/激励制度不分明,导致部分的员工无积极性,正是由于部分人员的质量意识不够激烈,对工作无责任感,导致最近一段时间,我们出货的产品不断的出现客诉,而且都是一些比较低级的不该发生的问题.客人对我们的质量确保失去了信心.因此我们对质量改善有感而发,迫在眉睫.五、目前的替代策略:在以后的生产过程中,我们将提早做好相关质量预防控制计划,同时又在生产过程中积极把关控制,杜绝不良品流入下一个工作站。
而不是等到事后才来控制! 同时推行晋升与降级管理办法/绩效管理办法/奖励与处罚管理办法/激励制度建立/创意提案制度方案六、预期的结果:1.划清相关人员的工作责任,落实到位,各职其责,相关人员对自己的工作的责任感更加激烈,提升全员的质量意识.使得相关人员的工作潜力发挥到最正确状态2.不良比率降低50 %,利润提升10%3.引导员工本着自动自发精神,运用各种改善手法,启发个人潜能,透过团队力量,结合群体智慧,群策群力,继续地从事各种问题的改善;而能使每一位成员有参加感、满足感、成就感七、全员要积极参加质量改善应解决以下几个问题﹕1﹒加强质量意识﹐决心改革。
质量管理与不良率控制

降低成本
通过控制不良率,可以减少浪 费和返工,降低生产成本,提 良率,可以维护企 业的形象和声誉,增强企业市 场地位和竞争能力。
提高客户满意度
通过控制不良率,可以提高客 户满意度,增强客户忠诚度和
业务拓展能力。
03 质量管理体系的建立与实 施
质量管理体系的构成
需求分析
明确组织的质量管 理需求和目标。
文件编制
编写质量管理体系 文件。
监督与改进
定期评估体系运行 效果,持续改进。
质量管理体系的实施要点
全员参与
鼓励员工积极参与质量管理,提高质量意识。
持续改进
不断优化流程,提高产品质量和过程效率。
预防为主
加强过程控制,预防不良品产生。
客户导向
关注客户需求,提升客户满意度。
质量管理与不良率控制
汇报人:可编辑 2024-01-05
contents
目录
• 质量管理的概念与重要性 • 不良率产生的原因与影响 • 质量管理体系的建立与实施 • 不良率控制的方法与策略 • 质量管理与不良率控制的案例分析
01 质量管理的概念与重要性
质量管理的定义
质量管理是指在质量方面指挥和控制组织的协调的活动。
和生产工艺,提高产品质量和降低不良率。
THANKS FOR WATCHING
感谢您的观看
增强组织信誉
良好的质量管理有助于树立组织可靠和值得 信赖的形象。
质量管理的发展历程
质量检验阶段
20世纪初,质量管理主要集中在质量检验方面,通过检验来确保产品 质量。
统计质量控制阶段
20世纪中叶,人们开始利用统计学方法进行质量控制,通过对生产过 程中的数据进行监控和分析,预防不良品的产生。
- 1、下载文档前请自行甄别文档内容的完整性,平台不提供额外的编辑、内容补充、找答案等附加服务。
- 2、"仅部分预览"的文档,不可在线预览部分如存在完整性等问题,可反馈申请退款(可完整预览的文档不适用该条件!)。
- 3、如文档侵犯您的权益,请联系客服反馈,我们会尽快为您处理(人工客服工作时间:9:00-18:30)。
2.1.3 标准常态分配机率
Z 超过规格之机率 (单边)
-3.00 0.135 %
-3.05 0.114 %
-3.10 0.097 %
-3.15 0.082 %
-3.20 0.069 %
-3.25 0.058 %
-3.30 0.048 % P
-3.35 0.040 %
-3.40 0.034 %
-3.45 0.028 % ∞ -3.50 0.023 %
ppb (十億分之一)
1 ×109 ppb 1 ×107 ppb 1 ×106 ppb 1 ×105 ppb 1 ×104 ppb
1000 ppb 100 ppb 10 ppb
1 ppb
18
2.1.5 可靠度理念的「直通率」
计为零允收抽样计划。
7
这是由于高新科技产品结构十分复 杂,内有零件量很大,万一用了不 合格零件而使产品无法发挥其应有 的功能,其侦错过程十分耗时,损 失更是天文数字,为了提高产品可 靠度,对于零件品质要求自然十分 严格。
8
2.1.1或等于1.5
9
使不良率降低的方 法及运用
1. 不良率改善的目标达成真言:
1.1 狩野纪绍品管大师的魅力品质
A) 二项经营战略
A-1 对于已有的业务(事业, 制品,服务或制程,过程), 必须要【比以往进行更彻底 的检讨,追求更加的减肥】
2
A) 二项经营战略
A-2 传统业务必须创造更新的业 务,以唤起新的需求。
3
2.1 6SIGMA及ppm的品质 新理论与新策略
值得注意的是近年来,由于工业 技术进步及管理科学的发展,顾客 常要求供应商提供近乎零缺点的产 品,尤其是微电子工业更是如此。 过去的允收不合格率约为1%至 10%,
6
如今则以百万分之一(parts per million,ppm)为单位,常见为
0.05%至0.005%,即500ppm至 50ppm的水准,日本的输出品质水准 为10ppm,因而抽样计划也重新设
B)二维魅力品质;
狩野的二维魅力品质
创
意
第三代管理A公司(30%成长)
贡献
又好又快又准又便宜
4
1. 2 21世纪的品质概念
A)从被动的顾客满意改变到主动的 取悦内外部顾客
B)同时兼顾结果与过程 C)追求卓越的定义(又快、又好、
又准、又便宜、利润又高)
5
2.从零缺陷管理(6SIGMA管理及ppm) 来谈不良率改善
2.1.2 为何以六个σ 订为品质缺点基准?
□ 在无制程变异情况下 (Cp=Cpk=2),产生之缺点率仅 为0.002PPM。(10亿分之2)
□ 在制程无法完全消除变异情况下,
即无法使Cp=2,只好允许
Cpk=1.5(允许1.5个σ的偏移),缺点
率亦仅有3.4PPM。(百万分之
3.4)(相当于精密度要求加严了一
5,000 ppm(0.50%) 50 ppm
(0.005%) 500 ppm (0.05%) 50
ppm(0.005%) 1,000 ppm(0.1%)
10000 (0.999999999)10000= 0.99999= 99.999%
10 ppm(0.001%)
注: 组件不良率(%)=100% 组件可靠度
倍,准确度要求却放宽了一倍,
这样,可以提高生产速度)
10
-6σ -5σ -4σ -3σ - 2σ -1σ 68.26% +1σ +2σ +3σ +4σ +5σ +6σ
95.44 % 99.73 % 99.9937% 99.999943% 99.9999998%
11
σ数
在外或然率
1 ···················317,400 PPM 2 ·····················45,400 3 ·······················2,700 4 ····························63 5 ······························ 0.57 6 ······························0.0 12
17
小数点 1 0.01 0.001 0.0001 0.00001
— — — —
百分比 100%
1% 0.1% 0.01% 0.001% 0.0001% — — —
ppm 分之一)
1 ×106 ppm
10,000 ppm 1,000 ppm
100 ppm 10 ppm
1 ppm 0.1 ppm 0.01 ppm 0.001 ppm
3.4 2.1
ppppmmPL
-4.70 1.3 ppm
-4.80 0.8 ppm
-4.90 -5.00
0.5 ppm 0.3 ppm
ZL
0
PU ZU
-5.50 0.02 ppm -6.00 0.001 ppm
PT=PL+PU
说明:*1ppm=10-6=0.000001=10-4%=0.0001% *变数变换ZU=(X-SU)/σ ,ZL=(SL-X)/σ 14
Z
0
-3.60 0.016 %
-3.70 0.011 %
-3.80 0.007 %
13
-3.90 0.005 %
Z 超过规格之机率 (单边)
-4.00 31.7 ppm
-4.10 20.7 ppm
-4.20 13.3 ppm
-4.30 8.5 ppm
-4.40 5.4 ppm
-4.50 -4.60
标准差与PPM制品质水准对照表 (准确度偏移1.5σ时) 超连结一
15
6σ管理(ppm)抽样计划
超连结二
◎ ppm AOQL抽样计划 ◎零允收单次抽样计划 ◎零允收双次抽样计划
16
2.1.4 ppm与ppb在可靠度上的诠释
元件数量
元件数量(件) (元件可靠度) =组件可靠度
5 (0.99)5= 0.951= 95.1%
组件不良率(%) 49,000 ppm(4.9%)
5 (0.9999)5= 0.9995= 99.95%
500 ppm(0.05%)
50 (0.9999)50= 0.995= 99.5% 50 (0.999999)50=0.99995= 99.995% 500 (0.999999)500= 0.9995= 99.95% 500 (0.9999999)500= 0.99995= 99.995% 10000 (0.9999999)10000= 0.999= 99.9%