旋风分离器结构改进的研究现状和发展趋势_王清华
旋风分离器文献综述(DOC)
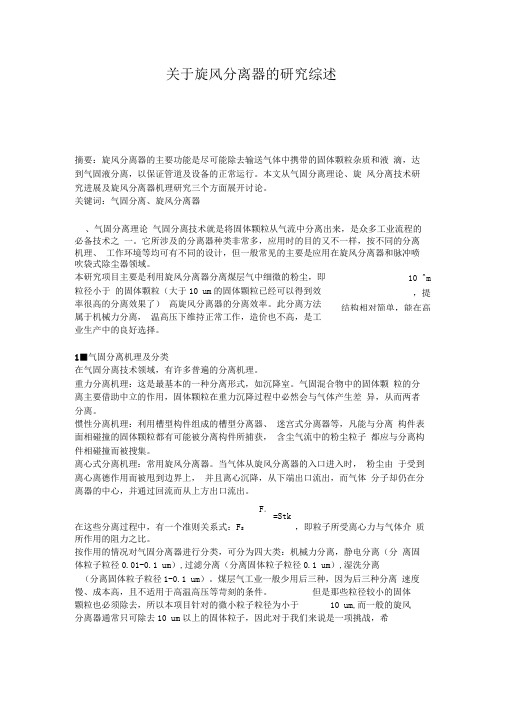
关于旋风分离器的研究综述摘要:旋风分离器的主要功能是尽可能除去输送气体中携带的固体颗粒杂质和液 滴,达到气固液分离,以保证管道及设备的正常运行。
本文从气固分离理论、旋 风分离技术研究进展及旋风分离器机理研究三个方面展开讨论。
关键词:气固分离、旋风分离器、气固分离理论 气固分离技术就是将固体颗粒从气流中分离出来,是众多工业流程的必备技术之 一。
它所涉及的分离器种类非常多,应用时的目的又不一样,按不同的分离机理、 工作环境等均可有不同的设计,但一般常见的主要是应用在旋风分离器和脉冲喷 吹袋式除尘器领域。
本研究项目主要是利用旋风分离器分离煤层气中细微的粉尘,即粒径小于 的固体颗粒(大于10 um 的固体颗粒已经可以得到效率很高的分离效果了) 高旋风分离器的分离效率。
此分离方法属于机械力分离, 温高压下维持正常工作,造价也不高,是工业生产中的良好选择。
1■气固分离机理及分类在气固分离技术领域,有许多普遍的分离机理。
重力分离机理:这是最基本的一种分离形式,如沉降室。
气固混合物中的固体颗 粒的分离主要借助中立的作用,固体颗粒在重力沉降过程中必然会与气体产生差 异,从而两者分离。
惯性分离机理:利用槽型构件组成的槽型分离器、 迷宫式分离器等,凡能与分离 构件表面相碰撞的固体颗粒都有可能被分离构件所捕获, 含尘气流中的粉尘粒子 都应与分离构件相碰撞而被搜集。
离心式分离机理:常用旋风分离器。
当气体从旋风分离器的入口进入时, 粉尘由 于受到离心离德作用而被甩到边界上, 并且离心沉降,从下端出口流出,而气体 分子却仍在分离器的中心,并通过回流而从上方出口流出。
=Stk在这些分离过程中,有一个准则关系式:F s,即粒子所受离心力与气体介 质所作用的阻力之比。
按作用的情况对气固分离器进行分类,可分为四大类:机械力分离,静电分离(分 离固体粒子粒径0.01-0.1 um ),过滤分离(分离固体粒子粒径0.1 um ),湿洗分离(分离固体粒子粒径1-0.1 um )。
循环流化床旋风分离器防变形及结构优化
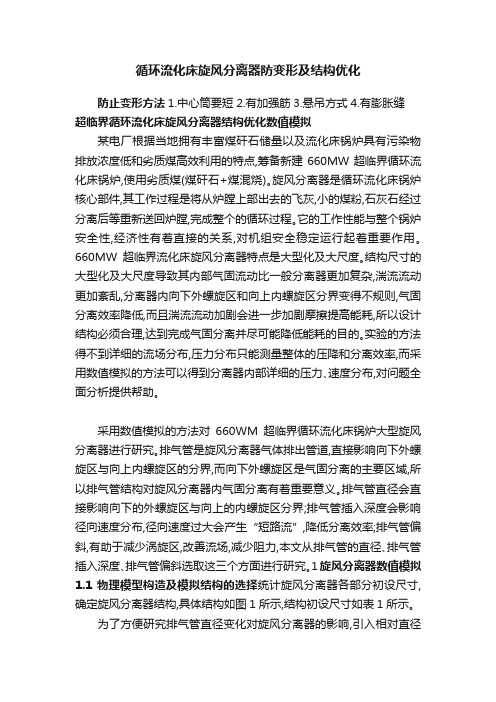
循环流化床旋风分离器防变形及结构优化防止变形方法1.中心筒要短2.有加强筋3.悬吊方式4.有膨胀缝超临界循环流化床旋风分离器结构优化数值模拟某电厂根据当地拥有丰富煤矸石储量以及流化床锅炉具有污染物排放浓度低和劣质煤高效利用的特点,筹备新建660MW超临界循环流化床锅炉,使用劣质煤(煤矸石+煤混烧)。旋风分离器是循环流化床锅炉核心部件,其工作过程是将从炉膛上部出去的飞灰,小的煤粉,石灰石经过分离后等重新送回炉膛,完成整个的循环过程。它的工作性能与整个锅炉安全性,经济性有着直接的关系,对机组安全稳定运行起着重要作用。660MW超临界流化床旋风分离器特点是大型化及大尺度。结构尺寸的大型化及大尺度导致其内部气固流动比一般分离器更加复杂,湍流流动更加紊乱,分离器内向下外螺旋区和向上内螺旋区分界变得不规则,气固分离效率降低,而且湍流流动加剧会进一步加剧摩擦提高能耗,所以设计结构必须合理,达到完成气固分离并尽可能降低能耗的目的。实验的方法得不到详细的流场分布,压力分布只能测量整体的压降和分离效率,而采用数值模拟的方法可以得到分离器内部详细的压力、速度分布,对问题全面分析提供帮助。采用数值模拟的方法对660WM超临界循环流化床锅炉大型旋风分离器进行研究。排气管是旋风分离器气体排出管道,直接影响向下外螺旋区与向上内螺旋区的分界,而向下外螺旋区是气固分离的主要区域,所以排气管结构对旋风分离器内气固分离有着重要意义。排气管直径会直接影响向下的外螺旋区与向上的内螺旋区分界;排气管插入深度会影响径向速度分布,径向速度过大会产生“短路流”,降低分离效率;排气管偏斜,有助于减少涡旋区,改善流场,减少阻力,本文从排气管的直径、排气管插入深度、排气管偏斜选取这三个方面进行研究。1旋风分离器数值模拟1.1 物理模型构造及模拟结构的选择统计旋风分离器各部分初设尺寸,确定旋风分离器结构,具体结构如图1所示,结构初设尺寸如表1所示。为了方便研究排气管直径变化对旋风分离器的影响,引入相对直径比:式中:De———排气管管径,m;D———圆柱分离段直径,m。排气管直径太大会使分离效率急剧降低,而太小会使总压差急剧上升,一般排气管相对直径比选取0.5,对于压差要求不大的可进一步缩小排气管直径来提高分离效率。选取模拟直径范围2.55m~4.25m,模拟尺寸选取2.55m~4.25m范围内典型尺寸2.55m、2.975m、3.4m、3.825m、4.25m,分别对应相对直径比0.3、0.35、0.4、0.45、0.5,其中4.25m是初设值。插入深度为3.6m,8.5m,10.1m分别对应排气管的底端在进气管底板以上,与进气管底板持平,在进气管底板以下这三种典型结构。选取这三个典型插入深度进行模拟,其中插入深度3.6m为初设值。排气管向涡旋区适量偏离,可以优化流场。旋风分离器初设排气管不进行偏置布置,为提高分离效率,降低总压差,对初设排气管结构进行设计优化。据文献,90°~180°方向紧靠排气管外壁会形成离体漩涡区。在偏置0°~180°方向之间选取典型偏置方向0°,45°,90°,145°,180°进行研究。模拟尺寸选取汇总表如表2所示。1.2 网格划分使用网格划分软件对构建好的个体进行网格划分,将旋分分离器分成3个子区域,分别是进气管段,排气管段和其他区域。分别对3个子区域进行网格划分。经过网格无关性检验,最终选取201287个网格个体的模型。具体网格划分如图2所示。其中进气管段与圆柱分离段连接处含有尖端易产生质量较差网格。先采用“撒种子”方法将进气管段上表面进行划分,然后采用cooper 方法对进气管段进行网格划分,剩下的圆柱体段,圆锥体段都是规则几何体,可以直接采用cooper方式进行划分,最终生成高质量网格。图3为进气管段与圆柱体段连接处网格。1.3 湍流模型的选取旋风分离器流体为强旋湍流,湍流模型有k-ε模型,RNG模型和RSM模型。k-ε模型是基于同向性假设,这与旋风分离器的强旋性质不符,RNG模型虽然加入了时均应变率,但仍基于同向性假设,还是不能符合旋风分离器的强旋性质。RSM模型抛弃了各向同性假设,在模拟各向异性湍流方面有显著优势,许多学者采用RSM模型对旋风分离器进行研究并得到了与实际情况相近的结果,所以采用RSM湍流模型来进行模拟。表3为RSM模型控制方程组。1.4 差分格式及算法选取常用的差分格式有一阶差分格式,二阶差分格式和QUICK差分格式。一阶差分格式只有一阶精度的截差,优点在于易于收敛,但是扩散项大,误差较大;二阶差分格式在一阶差分格式基础上优化了精度截差,使模拟更加接近现实但是仍有一定的假扩散;QUICK差分格式不仅保留了稳定性而且具有更高的精度截差,假扩散被进一步减小,为提高模拟准确性采用QUICK差分格式。PRESTO压力插补格式适用于高速旋转流动,符合旋风分离器内流体高旋流动的特点,所以采用PRESTO压力插补格式。SIM-PLEC耦合方式是在SIMPLE 耦合方式基础上进行优化,对于许多问题SIMPLEC耦合方式可以快速得到收敛解,所以采用SIMPLEC压力速度耦合方式。1.5 两相流模型选取择气相湍流流动会对颗粒相产生影响,同样,颗粒相反过来也会对气相产生影响,但是颗粒之间的相互作用可以忽略不计,所以采用相间耦合的随机轨道模型来模拟分离器颗粒运动。颗粒在分离器中主要受重力作用和拽力作用,不考虑其他力。颗粒相在拉格朗日坐标系下的运动方程如式(2)、式(3):1.6边界条件设置设旋风分离器内物质为空气,温度为900℃,气体密度为0.301kg/m3,黏度μ=4.67×10-3Pa·s,并对边界条件进行设置。(1)进口:速度进口(velocityinlet),大小为20m/s;(2)出口:自由出流(outflow),流量为1;(3)颗粒捕集口:壁面(wall),在加入颗粒时设置为trap类型;(4)壁面:标准壁面函数,无滑移壁面。分级效率是评价旋风分离器分离性能的一个重要指标之一。分级效率是指某给定粒径颗粒的分离效率,与进气口颗粒粒径,浓度无关,因此可以看出,用分级效率评价旋风分离器性能更具有意义,不考虑操作条件,单独考虑旋风分离器总效率是无意义的。因为旋风分离器对大颗粒几乎可以完全分离,关键在于对小颗粒的分离,所以主要对小颗粒进行模拟,颗粒直径服从Rosin-Rammler分布,颗粒粒径0.05mm~0.1mm,平均粒径0.075mm,从颗粒质量流中任意选取2000个颗粒来计算分级效率。颗粒初始喷入位置是进气口平面,颗粒速度与进气口空气速度相同。颗粒在分离器中随气流做高旋流动,大颗粒在离心力作用下被甩出,经多次碰撞壁面后落入排尘口平面,认为颗粒被捕集;小颗粒随气相流体流动,被携带从排气管排出,认为颗粒逃逸。设进入旋风分离器颗粒数为n,被捕捉数为ni,分级效率通过式(5)计算:2数值模拟结果与分析2.1 排气管直径对旋风分离器的影响模拟排气管直径2.55m、2.975m、3.4m、3.825m、4.25m,分别对应相对直径比0.3、0.35、0.4、0.45、0.5这5种典型结构。图4为不同直径x=0截面速度等值线分布图。通过数值模拟得到各个直径下总压差变化曲线图5。从图5可知。排气管直径增大,总压差随之降低,直径从2.55m增加到2.975m,压差降低12.1%;从2.975m增加到3.4m,压差降低7.60%;从3.4m增加到3.825m,压差降低7.43%;从3.825m到4.25m,压差降低5.32%,变化幅度逐渐趋于平缓。分析图4,图5可知,排气管直径增大,会导致分离器内高旋湍流速度降低,减弱了流体内部以及流体与排气管壁面和分离器内壁面的摩擦。同时排气管直径的增大可以有效减弱排气管底端入口径缩效应。最终使总压差降低,能耗减少。通过模拟得到各个直径下分级效率变化曲线图6从图6中可以看出,排气管直径增大,分级效率先增后减,但是总体变化幅度不超过2.5%。分析图4,图6发现旋风分离器分级效率最主要是受切向速度影响,排气管直径的增大会导致切向速度的降低。直径在2.55m~3.4m之间变化时,向上内螺旋区域和向下外螺旋区域变化不大,不影响气固分离;但排气管直径增大,排气管底部区域轴向速度会减少,减弱“短路流”的影响,使分级效率得到提升。排气管直径在3.4m~4.25m之间变化时,排气管直径的增大会压缩向下外螺旋区域。向下外螺旋区域是气固分离的主要区域,分离区域被压缩导致分级效率降低。虽然排气管直径增大会进一步降低轴向速度,这对减弱“短路流”是有利的,但是排气管直径的增加,也会加剧旋风分离器分离区域的“甩尾”现象,导致颗粒返混,降低分级效率并且加剧锥形壁面的磨损。综合影响下,分级效率降低。2.2 排气管插入深度对旋风分离器的影响对排气管插入深度为3.6m、8.5m和10.1m的情况进行模拟。图7为不同插入深度的结构简图。图8为不同插入深度x=0截面速度等值线分布图。经模拟得到不同插入深度下的总压差变化折线图9。从图9可以看出,随着插入深度的增加,压差快速地升高,插入深度8.5m比3.6m压差增加42.93%;插入深度10.1m比8.5m压差增加66.39%。分析图8,图9可知这主要是因为排气管插入深度提高,加大了流体与排气管壁面的接触面积从而加大摩擦,流体能量损失增加,流速降低。而总压=静压+动压。流体流速的减小,总压中动压部分减小,使出口总压减小,在入口总压不变条件下,最终总压差增大。通过模拟得到不同插入深度的旋风分离器分级效率变化折线图10。从图10可以看出,插入深度越大,分级效率越大。分析图8,图10可知,这是因为进入旋风分离器的部分气流会直接沿壁面向上流动,到达顶端后继续贴壁流动,汇聚到排气管底部四周后,紧贴排气管内壁而不经过旋风分离器圆柱体段和锥体段部分直接从排气管流出。颗粒相中一些容易被气流携带的小颗粒就会直接从排气管排出,造成“短路流”,降低分级效率。而插入深度增加,排气管贴壁速度减小,减弱“短路流”影响,提高分级效率。2.3 排气管偏心对旋风分离器的影响模拟计算了排气管沿着0°、45°、90°、135°及180°五个偏置方向的总压差和分级效率。为了便于分析,引入相对偏心距。式中:Δx———排气管偏心的距离,mm;R———圆柱段的半径,mm;r———排气管的半径,mm。相对偏心距设为定值10%(偏心距0.425m)。图11为不偏置和偏于180°方向的示意图。图12为不同偏置方向z=18截面的速度分布等值线图。通过模拟得到不同偏置方向的总压差变化曲线图13。从图13中可以看出,当偏置方向角度增加时,总压差先增后减,在偏置于90°方向时达到最大值,比初设结构增加了17.48%。在偏置方向180°时压差最小,比初设结构减少了5.32%。通过模拟得到不同偏置方向分级效率变化曲线图14。从图14中可以看出,偏置于180°方向时分级效率最高,达到77.78%。分析图12,图14可知这是由向心力导致的,因为排气管偏置于180°方向时,正好是速度进口切向方向,切向速度阻力小,可以一直保持较高速度。流体切向速度对颗粒分离起到最主要作用,流体切向速度的高速性,保证了颗粒相可以被有效地分离。3综合性评价及结构优化总压差(Δp)和分级效率(η)是评价旋风分离器重要指标,总压差Δp代表了旋风分离器能耗的多少,分级效率η代表了旋风分离器分离固体颗粒能力,评价旋风分离器的性能必须将两者都考虑进去。而压降Δp与阻力系数ξ关系如式(7)所示:式中:ui———进口气流的速度,m/s; ρg———气体密度,kg/m。阻力系数ξ可以用来表示能耗的相对大小。引进综合性因素Y=η/ξ,因为旋风分离器分级效率越高越好,而能耗越少越好,所以Y最大结构最优。使用综合性因素Y 对某电厂排气管结构进行设计优化。表4为不同直径的综合性因素计算表。从表4中可以看出,直径为4.25m时,Y=3.17最大。表5为不同插入深度的综合性因素计算表。从表5中可以看出,插入深度为3.6m 时,Y=3.17最大。表6为不同偏置方向的综合性因素计算表。从表6中可以看出,偏置方向为180°时,Y=3.38最大,为了进一步提高分离器效率,降低能量损失,某电厂旋风分离器排气管可以偏置方向为180°布置。4结语通过数值模拟的方法对某电厂660MW超临界循环流化床旋风分离器排气管直径,插入深度,偏置方向进行研究并得到这三种结构变化对分离器压差和分级效率的影响规律。引进分析综合因素Y=η/ξ,对某电厂分离器排气管结构进行了评价和设计优化。得到了以下结论:(1)随着排气管直径的增大,总压差逐渐减小,但幅度越来越小,直径4.25m时,压差最小为1461.65Pa。而分级效率是先增加后减小,直径为3.4m时最大,达到79.4%,但是整体变化幅度较小,不超过2.5%。(2)插入深度越小,总压差越小,插入深度3.6m时,总压差最小为1461.65Pa。而对于分级效率,插入深度越大,分级效率越高,插入深度10.1m时,分级效率最高为82.6%。(3)偏置方向在0°~180°变化时,偏置方向的角度增加,压差先增后减,90°时最大,达到1717.09Pa。对于分级效率,偏置方向的角度越大,效率越大,180°时,达到77.78%。(4)通过引进综合因素Y=η/ξ来评价优化排气管初设结构。某电厂旋风分离器排气管直径4.25m,插入深度3.6m的设计是合理的。为进一步提高性能,排气管可以偏置于180°方向布置。文献信息赵立正,原奇鑫,康志忠,郭永红,孙保民. 超临界循环流化床旋风分离器结构优化数值模拟[J]. 锅炉技术,2016,03:31-37+44.来源:循环流化床发电。
旋流分离技术的现状与应用前景

旋流分离技术的现状与应用前景袁惠新X曾艺忠杨中锋(江南大学)(华北油田采油五厂)摘要在简述了液液旋流分离器的基本结构和工作原理及特点的基础上,介绍了旋流分离技术用于油污水处理、原油或其他油品脱水、液化气脱胺等方面的研究与发展现状,并展望了旋流分离技术在液液分离过程中的应用前景。
关键词旋流分离器旋流分离技术油水分离含油污水处理油品脱水中图分类号TQ05118+4文献标识码A文章编号0254-6094(2002)06-0359-05旋流分离器(简称旋流器)的发明、应用已有约一个半世纪了。
开始,只用于选矿过程中的固液分离和固固分离-分级,后来发展到固气分离,液气分离等。
到20世纪80年代末,这种旋流分离器被用于石油工业中的产出水除油,取得了满意的效果。
在液液分离研究过程中,先是轻分散相液体的分离(如油污水脱油),再是重分散相液体的分离(如油品脱水)。
虽然旋流分离技术在液液分离方面的应用要晚得多,但已显示出了其体积小、快速、高效、连续操作等方面的优越性,特别是用于轻分散相液体的分离,其牛顿效率非固液分离能比。
1简介1.1液液旋流器的基本结构及工作原理旋流器是一种利用离心沉降原理将非均相混合物中具有不同密度的相的机械分离设备。
旋流分离器的基本构造为一个分离腔、一到两个入口和两个出口(图1)。
分离腔主要有圆柱形、圆锥形和柱-锥形3种基本形式。
柱-锥形又有单锥形和双锥形两种。
入口有单入口和多入口几种,但在实践中,一般只有单入口和双入口两种。
就入口与分离腔的连接形式来分,入口又有切向入口和渐开线入口两种。
出口一般为两个,而且多为轴向出口,分布在旋流分离器的两端。
靠近进料端的为溢流口,远离进料端的为底流口。
在互不相溶、且具有密度差的液体混合物以一定的方式及速度从入口进入旋流分离器后,在离心力场的作用下,密度大的相被甩向四周,并顺着壁面向下运动,作为底流排出;密度小的相向中间迁移,并向上运动,最后作为溢流排出。
这样就达到了液-液分离的目的。
如何提高旋风分离效率的措施

如何提高旋风分离效率的措施旋风分离器是一种常用的固体颗粒分离设备,它通过旋转气流产生离心力,将固体颗粒从气流中分离出来。
在许多工业领域,旋风分离器被广泛应用于颗粒物料的分离和回收。
然而,旋风分离器的效率受到许多因素的影响,如颗粒物料的性质、气流速度、旋风分离器的结构等。
为了提高旋风分离效率,我们可以采取一些措施来优化设备的运行和设计。
首先,要选择合适的旋风分离器结构。
旋风分离器的结构对其分离效率有着重要的影响。
一般来说,旋风分离器的结构包括进气口、旋风管、排气口和收集器。
进气口的设计应该能够使气流均匀进入旋风管,而旋风管的设计应该能够使气流产生旋转运动,从而产生离心力将固体颗粒分离出来。
排气口的设计应该能够使气流和固体颗粒有效分离,而收集器的设计应该能够方便固体颗粒的收集和回收。
因此,选择合适的旋风分离器结构对提高分离效率至关重要。
其次,要优化气流速度。
气流速度是影响旋风分离效率的重要因素之一。
一般来说,气流速度越大,离心力越大,分离效率越高。
然而,气流速度过大也会导致能耗增加和设备磨损加剧。
因此,要根据具体的颗粒物料性质和分离要求,合理选择气流速度,以达到最佳的分离效果。
另外,要加强颗粒物料的预处理。
颗粒物料的性质对旋风分离效率有着重要的影响。
一般来说,颗粒物料的大小、密度和形状都会影响其在旋风分离器中的分离效果。
因此,在使用旋风分离器之前,可以对颗粒物料进行预处理,如粉碎、筛分等,以使其符合旋风分离器的分离要求。
这样可以有效提高分离效率,并减少设备的磨损。
此外,要加强设备的维护和管理。
设备的维护和管理对于提高旋风分离效率至关重要。
定期对设备进行检查和维护,及时清理和更换磨损部件,可以保证设备的正常运行,提高分离效率。
此外,合理管理设备的运行参数,如气流速度、进料量等,也可以有效提高分离效率。
最后,要加强技术研发和创新。
随着科技的不断进步,新型的旋风分离器结构和材料不断涌现,可以更好地满足工业生产对于分离效率的要求。
重油催化装置旋风分离器问题分析及改进措施
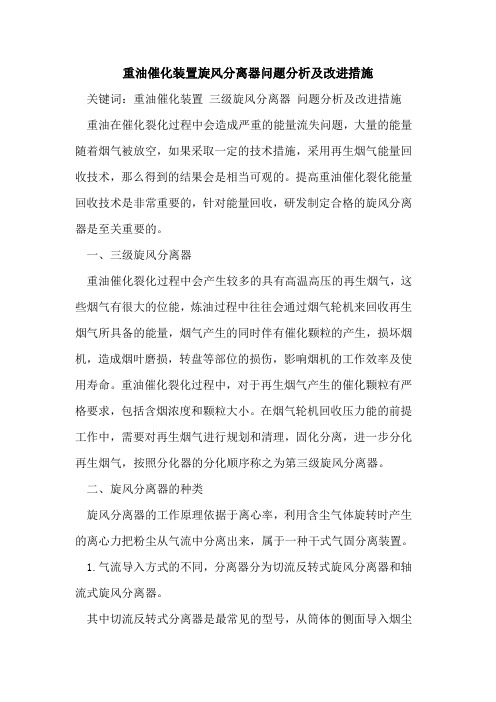
重油催化装置旋风分离器问题分析及改进措施关键词:重油催化装置三级旋风分离器问题分析及改进措施重油在催化裂化过程中会造成严重的能量流失问题,大量的能量随着烟气被放空,如果采取一定的技术措施,采用再生烟气能量回收技术,那么得到的结果会是相当可观的。
提高重油催化裂化能量回收技术是非常重要的,针对能量回收,研发制定合格的旋风分离器是至关重要的。
一、三级旋风分离器重油催化裂化过程中会产生较多的具有高温高压的再生烟气,这些烟气有很大的位能,炼油过程中往往会通过烟气轮机来回收再生烟气所具备的能量,烟气产生的同时伴有催化颗粒的产生,损坏烟机,造成烟叶磨损,转盘等部位的损伤,影响烟机的工作效率及使用寿命。
重油催化裂化过程中,对于再生烟气产生的催化颗粒有严格要求,包括含烟浓度和颗粒大小。
在烟气轮机回收压力能的前提工作中,需要对再生烟气进行规划和清理,固化分离,进一步分化再生烟气,按照分化器的分化顺序称之为第三级旋风分离器。
二、旋风分离器的种类旋风分离器的工作原理依据于离心率,利用含尘气体旋转时产生的离心力把粉尘从气流中分离出来,属于一种干式气固分离装置。
1.气流导入方式的不同,分离器分为切流反转式旋风分离器和轴流式旋风分离器。
其中切流反转式分离器是最常见的型号,从筒体的侧面导入烟尘气体,气流旋转向下进入椎体,到达端点之后反转向上,通过排气管排出清洁气体。
轴流式旋风器利用气流旋转原理,尘烟进入筒体之后,呈圆周运动,气流向下向锥体移动,呈螺旋形。
通过重力和离心力的作用,粉尘顺着器壁落入锥体中,轴流式旋风器旋转的切向速度随着锥体的半径变化而变化,切向速度到达临界点的同时气流会由向下螺旋运动变为向上螺旋运动,称之为内旋气流。
2.我国使用的三旋器主要是多管式三旋,有两种类型分别是立管式三旋和卧管式三旋。
多管式三旋的优势是拥有共同的进气室,集气室和集尘室。
再生烟气进入室管后流向各个并联的分气单管。
由单管净化后放入集气室,再经排气管进入烟气轮机。
环流式旋风分离器结构改进及其在煅后焦装置的应用

环流式旋风分离器结构改进及其在煅后焦装置的应用杨志毅【摘要】中海油惠州石化有限公司400Kt/a煅后焦装置采用DⅢ型旋风分离器进行烟气除尘,存在烟气除尘率低,管路和设备积灰严重、磨损大,装置检维修频次高等问题.该公司对环流式旋风分离器结构进行了改进并将其应用于煅后焦装置烟气除尘.与DⅢ型旋风分离器相比,烟气除尘率由43.22%提高了93.12%,引风机电耗下降6.4%,旋风分离器出口管路及后序设备积灰严重、磨损大的问题得到有效解决,延长了装置运行周期,每年节省装置检维修及运行费用210万元.【期刊名称】《化工中间体》【年(卷),期】2018(000)010【总页数】3页(P144-146)【关键词】环流式旋风分离器;结构改进;煅后焦装置;应用【作者】杨志毅【作者单位】中海油惠州石化有限公司广东 516082【正文语种】中文【中图分类】T中海油惠州石化有限公司(以下简称惠州石化)采用美国Metso Minerals的回转窑煅烧技术于2010年5月建成投产了400Kt/a煅后焦装置,该装置采用2台DⅢ型旋风分离器回收冷却机烟气中夹带的煅后焦颗粒。
该装置自投产以来,一直存在烟气除尘率低,管路和设备积灰严重、磨损大,装置检维修频次高等问题,严重影响了装置的安全、清洁生产和经济效益。
为了改变这种状况,惠州石化先后采用由青岛科技大学化学工程研究所开发研制并进行内部结构改进的2台环流式旋风除尘器替代原有的2台DⅢ型旋风分离器,烟气除尘率大幅度提高,管路和设备堵塞严重、磨损大的问题得到有效解决,装置检维修及运行费用降低。
1.旋风分离器烟气除尘工况(1)旋风分离器进口烟气操作条件及烟气组成旋风分离器进口烟气操作条件及组成见表1。
表1 旋风分离器进口烟气操作条件及组成旋风分离器进口烟气组成旋风分离器进口烟气操作条件流量/(m3•h-1)压力/Pa温度/℃H2O/%N2/%O2/%CO2及其他/%煅后焦颗粒/(mg•m-3)50000-70000-180--400 160-250 25-36 40-54 12-17 3-7 220-530(2)旋风分离器进口烟气煅后焦颗粒粒度分布通过MASTERSIZER2000激光测定仪对旋风分离器进口烟气中的煅后焦颗粒样品进行粒径分析,其粒径分布见表2。
催化裂化第三级旋风分离器的现状和发展方向
催化裂化第三级旋风分离器的现状和发展方向通过分析我国目前所采用的多管式三旋分离器在运行过程中的问题,并对烟气轮机正常运转的影响进行研究,分析导致问题出现的原因,结合国外常用的一种旋风式三旋方案进行解决,提高催化裂化第三级旋风分离器的运行状态,并且介绍旋风式三旋分离器的主要结构特点。
标签:催化裂化;第三级旋风分离器;现状催化裂化第三级旋风分离器的正常运行可以确保催化裂化装置的长期运行,并且帮助装置实现节能降耗。
通过对催化裂化第三级旋风分离器技术的现状进行分析,并提出相应的改进措,有助于提高我国催化裂化三级旋风分离器技术的进步。
1我国多管式三旋的现状和存在的问题第三级旋风分离器是催化裂化装置中最为关键的设备之一,第三级旋风分离器的结构形式主要包括:多管立式三旋、多管卧式三旋、布埃尔式三旋以及旋流式三选。
与我国对于多管式三旋的引用胶为频繁,并且从20世纪70年代后期就开始研究催化炼化能量回收系统多管式第三级旋风分离器,通过不断引进西方的技术结合自主研发技术,我国已经开发出了具有独自特点和自主知识产权的多管三旋技术,并且在旋风分离器的应用水平较为广泛,因此多管第三级旋风分离器的应用,可以确保催化裂化装置的安全运行和节能降耗。
经过我国广大科研人员的不懈努力,我国催化裂化装置第三级旋风分离器已经达到了比较先进的水平,可以有效提高单管的抗返混能力和多管式三旋的整体效率,但是从实际使用情况来看,多管式三旋的使用也存在一些问题。
近几年以来,我国的催化裂化装置技术发展迅速,催化裂化装置的大型化原料的掺渣比例不断增加,烧焦温度呈明显上升趋势,装置的操作因此会变得十分不稳定,因此有些炼油厂的第三级旋风分离器会出现一些问题,其中主要包括以下几种问题:(1)单管在进行冷态试验时分离效率较高,但是在实际工业生产过程中单管并不能单独使用,需要进行并联使用,在并联使用过程中,提高整体的分离效率才是最终的目标。
但是在实际应用过程中单管并联后的整体分离效率并不理想,出现这种情况的原因在于单管抗返混能力较差,将单管组合以后,单管内的压降不均匀,造成部分单管不能够正常运作,从而导致组合效率出现下降。
下排气旋风分离器的结构改造及效果分析
4 2
柬工案 技术
工 业 技 术
空分 水循 环 系统改造
王 文 乐 ( 山东兖矿集 团国际焦化有 限公 司 , 山东 兖州 2 7 2 1 o o )
( ℃ )
4 9 49
( ℃)
5 5 5 9
E 8 0 0 2
管程 :循环水 :3 2~ 4 o ℃ ;0 . 5~O . 4 M P a ( A ) ( 操作)
二段气体
冷却器
设计参数 :5 0 ℃ :O . 6 MP a( G)
壳程 :空气:1 3 0~ 4 0  ̄ C: 0 . 4 3 6 MP a ( A ) ( 操作 ) 设计参数 :2 0 0 ℃: O . 6 MP a( G)
规 格 : ̄ 1 8 0 0 ×7 8 0 0 F = 2 3 3 5 m
E 8 o 0 1
一
管程 :循环水 :3 2~ 4 0  ̄ C;0 . 5 ~0 . 4 MP a ( A ) ( 操作)
设计参数 :5 0 ℃:0 . 6 0 MP a 壳程 :空气 :1 2 0~ 4 o ℃ :O . 2 0 9 MP a ( A ) ( 操作) 设计参数 : 2 0 0 ℃:0 . 6 0 M P a 规格 : ̄1 8 0 0 ×7 8 0 0 ;F = 2 3 3 5 m
E8 0 01 E8 O O2
8 6 2 8 6 2
两 台换热器 用水约 4 5 1 m , / h , 距离初步设计值 3 0 8 + 2 9 0 = 5 9 8 m / h 最大设 计值 8 0 0 m / h差距较大。
旋风分离器的发展与理论研究现状
旋风分离器的发展与理论研究现状刘金红(南通职业大学化工系,南通市226007) 摘 要 综述了旋风分离器的发展概况,并从气体、粉尘运动的研究和结构改进两个方面介绍了旋风分离器的理论研究现状。
关键词 旋风分离器 除尘 气固分离 旋风分离器是一种使含有固体颗粒的气体旋转,并依靠离心力达到气固分离的装置。
由于它具有对10L m以上的粉体分离效率高、结构简单紧凑、操作维护方便等优点,故在石油化工、冶金、采矿、轻工等领域得到广泛应用。
随着工业发展的需要,为使旋风分离器达到高效低阻的目的,自1886年Mo rse的第一台圆锥形旋风分离器问世以来百余年里,国内外众多学者对分离器的结构、尺寸、流场特性等进行了大量的研究,出现了许多不同用途的旋风分离器,现从两个方面来进行概述。
1 气体、粉尘运动的研究 旋风分离器内颗粒流体的流动属于稀浓度颗粒流体力学,故可先分析纯气体流场,再计及颗粒在其中的运动。
在1949年,T er Linden[1]对旋风分离器内三维流场用球形毕托管作了比较出色的实验测试研究并得出:切向速度轴对称分布,在同一断面随其与轴心的距离减小而增大,达到最大值后又逐渐减小;径向速度在中心区方向朝外,在外围区方向朝内,形成源汇流;轴向速度在外部区域气流向下,在轴心区域气流向上;压力分布是壁面处大于中心处。
他的测试结果,无论切向、径向、轴向都有一定的规律性,轴对称性也相当好。
在国内,中科院力学研究所[2]、上海化工研究院[3]在Á400及Á830旋风分离器模型上,用五孔球形探针及热线风速仪进行了测试。
许宏庆[4]在Á288模型上,用双色激光多普勒测速仪进行了测试。
这些流场测试图呈现出的规律大致与T er Linden所得结果相同,但他们都认为非对称的切向进口造成了旋涡中心与几何中心不一致,径向速度分布呈现非轴对称性等现象,同时还证实了上涡流的存在。
至于气体运动的理论计算研究,由于流动的复杂性,一般均假定为轴对称流动,早期曾进一步假定为层流流动,近年来才考虑湍流的影响。
旋风分离器的新结构和新构件的研究进展
旋风分离器的新结构和新构件的研究进展吴凯;段继海;张自生【摘要】综述了近几年国内外学者对提高选分离器性能结构方面的研究进展,研究表明:多种新型旋风分离器的应用完全能够捕获1~5μm 的微米和亚微米级颗粒,通过安装导流件等内构件措施能够降低湍动耗散能,降低能耗,降低旋风分离器的压降。
新型旋风结构和内构件是提高传统分离器性能的重要手段。
%The research progress of improving the performance of cyclone separators at home and abroad was reviewed. The new experimental results show that: a variety of new cyclone separators can fully capture 1~5μm micron and sub micron particles, to install diversion parts and other inner components in cyclone separators can reduce the turbulent dissipation energy and energy consumption. The new structure of cyclone and inner component is an important means to improve the performance of traditional separators.【期刊名称】《当代化工》【年(卷),期】2015(000)010【总页数】3页(P2355-2356,2359)【关键词】旋风分离器;结构优化;研究进展【作者】吴凯;段继海;张自生【作者单位】青岛科技大学化工学院,山东青岛 266000;青岛科技大学化工学院,山东青岛 266000; 生态化工国家重点实验室,山东青岛 266000;青岛科技大学化工学院,山东青岛 266000; 生态化工国家重点实验室,山东青岛 266000【正文语种】中文【中图分类】TQ052旋风分离器是一种常见的气固分离设备,由于其结构简单,操作方便,被广泛应用于煤粉流态化燃烧、石油催化裂化催化剂回收等装置中。
- 1、下载文档前请自行甄别文档内容的完整性,平台不提供额外的编辑、内容补充、找答案等附加服务。
- 2、"仅部分预览"的文档,不可在线预览部分如存在完整性等问题,可反馈申请退款(可完整预览的文档不适用该条件!)。
- 3、如文档侵犯您的权益,请联系客服反馈,我们会尽快为您处理(人工客服工作时间:9:00-18:30)。
第38卷第2期2007年3月 锅 炉 技 术BOIL ER TECHNOLO GYVol.38,No.2Mar.,2007收稿日期:20061010作者简介:王清华(1971),男,内蒙古呼和浩特人,讲师,硕士,主要从事热能工程专业方面的教学和研究。
文章编号: CN311508(2007)02000505旋风分离器结构改进的研究现状和发展趋势王清华(内蒙古工业大学电力学院,内蒙古呼和浩特010080)关键词: 旋风分离器;结构改进;研究现状;发展趋势摘 要: 对工业上普遍应用的颗粒分离设备———旋风分离器结构改进(包括进口、出口、锥体及排尘结构)的研究现状进行了回顾。
在此基础上,提出了旋风分离器结构改进的发展趋势,即:由于进口区域和排尘结构对于颗粒的分离至关重要,因此有必要对这部分结构进行深入研究;为了进一步改善旋风分离器的分离性能,除了利用离心力外还需结合其它的除尘机理;为了降低研究成本可以采用计算流体动力学技术来优化旋风分离器结构。
中图分类号: T K 223.4 文献标识码: A1 前 言 旋风分离器应用于工业生产以来,已有百余年的历史,对于捕集、分离5~10μm 以上的颗粒效率较高。
由于能耗相对比较小,结构简单可靠,广泛地应用于冶金、化工、石油、建筑、机械、电力、轻纺、食品等工业部门。
旋风分离器中颗粒分离的机理是:颗粒由于离心力的作用克服气流的阻力向壁面运动,到达壁面附近后,由于边界层内较小的湍流,颗粒会沿着壁面进入灰斗中,从而得到分离。
对于微细颗粒(粒径小于5μm ),由于其所受到的离心力小于气流对其的阻力,因此,一般来说,这一类颗粒很难得到分离。
随着工业装置生产规模的提高以及操作条件变得更为苛刻,对旋风分离器性能的要求也不断提高。
一方面要求旋风分离器有更强的捕集细粉的能力;另一方面要求旋风分离器的压降进一步减少,以降低能耗。
所以,迫切需要研究出高效能且低能耗的新型旋风分离器。
而通常是采用有针对性地开发新结构或优化各部分尺寸的匹配关系的方法来减少不利因素的影响,以达到高效的目的。
国内外已有许多学者在这方面做出了大量试验研究,也提出了很多可行的措施和设计方案并已应用于实际工程中。
本文在回顾前人研究现状的基础上,提出今后旋风分离器的发展趋势。
2 旋风分离器结构优化的研究现状与发展方向2.1旋风分离器进口结构的研究现状 普通旋风分离器单体大多采用了单切向进口或蜗向的进口结构形式,气固两相流进入旋风分离器后,随着远离旋风分离器排气芯管入口截面,平衡尘粒逐渐减小,即空间点上颗粒分离能力逐渐增强。
因此,优化改进位于旋风分离器上部的进口结构形式是旋风分离器技术改进的可行措施。
但是采用切向或蜗向单进口结构形式易造成旋风分离器内部气流场的轴不对称(涡核偏向270°一侧),不但增大了旋风分离器的阻力,而且增加了排气芯管短路流。
所以赵兵涛等[1]提出优化改进旋风分离器进口结构,首先增设了进口回转通道(图1),通过试验得出所有增设回转通道的旋风分离器分离效率均大于无回转通道的效率。
因为阻力系数的变化可影响进口速度的变化,进口速度的大小反映出旋风分离器分离能力的强弱。
当阻力系数较小时,进口速度较大,表明旋风分离器分离能力强,由于回转通道的增设,使颗粒在进入旋风分离器腔体前进行预分离,从而使分离效率增大,但随着回转角度的继续增大,二次返混影响增大,这就使得分离效率在90°甚至270°以后有所减小,但总体仍高于0°的分离效率。
所以改变其回转角度,就改变了锅 炉 技 术 第38卷两相流含尘浓度分布,使含尘浓度外浓内淡,从而减少短路流的携尘量。
图1 单双进口回转通道 同时若采用双进口回转通道形式,则有利于降阻增效,由于进气口面积增大为原来的2倍,使进口气流速度减半,从而降低了阻力;由于采用渐缩的回转结构,减小了颗粒到达捕集壁面的距离,从而提高了分离效率;进一步的流场测定结果表明,双进口结构由于采用在旋风分离器内多点对称进气,增强了旋风分离器内部流场的轴对称性,使短路流携尘量减少,同时实现了降阻增效,又增强了气流场轴对称性,以降低旋风分离器阻力。
具体试验结果表明,将旋风分离器常规进口结构优化改进为采用单进口等宽通道进口结构时,旋风分离器回转角度为90°时性能较优,比0°(无回转通道)时的阻力降低14.73%,效率提高2.48%。
采用双进口渐缩通道进口结构时,旋风分离器性能优于所有单进口,比0°(无回转通道)时的阻力降低33.06%,效率提高3.95%。
2.2旋风分离器出口结构的研究现状 在旋风分离器内部的旋转气流中,颗粒物受离心力作用作径向向外(朝向筒锥壁)运动,运动速度可由颗粒物所受的离心力及气流阻力的运动方程求得。
显然旋风分离器分离的目的就是使颗粒物尽快到达筒锥体边壁。
因此,延长颗粒物在旋风分离器中的运动时间,在气流作用下提高颗粒物与筒锥体壁相撞的概率,可以提高旋风分离器除尘效率。
Y.Zhu [2]提出的旋风分离器结构如图2所示,在普通旋风分离器中增加一个筒壁,这一筒壁将旋风分离器内部空间划分为2个环形区域,同时,排气芯管被移到了下方,排气芯管中的上升气流也变成了下降气流,颗粒物在内外2个环形区域内都得到了分离,事实上,这种旋风分离器相当于将2个旋风子结合到了一起。
从理论上讲,这种结构改进提高了颗粒物被收集的概率。
Zhu 型旋风分离器试验结果(气流流量范围为10~40L/min ,粒径范围为0.6~8.8μm颗粒图2 加内筒壁的旋风分离器物)与Stairmand 高效旋风分离器进行了比较,改进后的旋风分离器,除尘效率得到提高,并且随气流流量的增大而增大;同时,对于相同无因次尺寸的旋风分离器来说,前者的阻力也小于后者。
Y.Zhu 考虑各方面因素给出相应优化综合指标,得出改进后的旋风分离器性能优于传统的旋风分离器。
但这种改动后的旋风分离器较原有传统旋风分离器结构稍为复杂。
由于旋风分离器对微细颗粒物效率较低,尤其对粉尘粒径小于10μm 的颗粒的除尘效率随着颗粒直径减小逐渐降低。
也就是说,在旋风分离器的运行过程中,绝大部分微细粉尘穿透了分离区域,导致对微细粉尘效率下降。
Plomp 等[3]提出在顶部增加二次分离附件POC 的方法(图3)。
POC 二次分离利用排气芯管强旋流作用,使微细粉尘受离心力作用向边壁运动,并与挡板相撞后通过缝隙掉入挡板下部的壳体中,另一部分即使在一开始没有与边壁相撞,但由于始终受到离心力的作用,在到达POC 顶部时,其中也会有很大一部分通过缝隙处而进入挡板与壳体之间的空间,随后由于POC 中主气流的约10%通过缝隙形成渗透流。
在渗透流的推动下,颗粒物被吹出壳体。
研究结果得知,在特定结构尺寸和运行条件下总效率比改进前提高了2%~20%,POC 的阻力约为旋风分离器本体10%,该阻力与渗透气流量无关图3 POC 结构(Post Cyclone )6第2期王清华:旋风分离器结构改进的研究现状和发展趋势(在所给参数范围内)对于直径较大的旋风分离器,尤其在原旋风分离器性能不是很高的情祝下,加装POC的办法能提高旋风分离器的性能,特别是对3μm以上粉尘分离很有效。
2.3旋风分离器锥体结构的研究现状 Xiang Rongbiao等[4]研究了锥体尺寸对用于大气采样的小型旋风分离器的影响情况,以颗粒大小和气流流速为变化参数,对3个具有不同下部直径锥体的旋风分离器测出了效率。
测定结果得知:锥体下部直径大小对旋风分离采样器的效率影响显著,但是并不显著影响不同粒径颗粒物效率之间的变化程度。
当锥体下部开口部分直径大于排气芯管直径时,该锥体参数的减小,在不明显增加阻力的前提下,采样效率会随之提高;由阻力测试结果还可看出锥体开口部分直径不宜小于排气芯管直径。
从理论上讲,锥体下部直径减小能引起切向速度的提高,从而离心力增大;对于具有相同筒体直径的旋风分离器,若锥体开口小,则最大切向速度靠近锥壁,这使得颗粒能够更好地分离,同时,如果锥体开口较小,涡流将触及锥壁,使颗粒又有可能重新进入出气气流,但是后者与前者相比对旋风采样器影响较小。
所以,适当减小锥体下部直径有利于效率的提高。
已有分析得出,排气管下口直径比(D e/D)的变化对旋风分离器的效率及压降有显著影响,流场测试结果表示直径比减小,内旋流区缩小,离心力场增强,故分离效率提高,但压降也急剧上升,因此为了解决上述矛盾。
陈建义等[5]提出在减小径比同时,在排气管上沿环向开若干条纵向的狭缝。
该狭缝一方面增加了气流出口的通流面积,从而有效地降低了压降。
另外,由于开缝方向和环向成一定角度且顺着气流方向,所以气流是急剧改变方向后才进人缝隙的。
这样气流中所夹带的颗粒则由于惯性大而难以进入狭缝而逃逸,从而确保了旋风分离器效率不致下降。
并通过试验测出,这样不但使效率提高,压降也比用常规的排气管低,同时还可以有效改善“顶灰环”和“短路流”等不利影响。
同时,在一定处理气量下,分离空间高度增加后,一方面含尘气流在旋风分离器内平均停留时间延长,可促进气固进一步分离;另一方面,从灰斗及排尘口返混上来的颗粒获得二次分离的机会增多,因而可有效抑制返混对分离的不利影响,并且分离空间高度的改变几乎不会对压降产生影响。
针对循环流化床锅炉飞灰分离器必须具有的特点(即必须具有足够高的分离效率,提供足够多的物料进行循环,以满足炉内燃烧、脱硫和传热等方面的需要),华中科技大学[6]、浙江大学[7]提出了一种新型的旋风分离器———下排气式旋风分离器(图4)。
此种新型旋风分离器一般垂直布置,它同样是利用旋转含尘气流产生的离心力,将粉尘从气流中分离出来的一种气固分离装置。
其基本结构类同于上排气旋风分离器,只是其排气方式为顺流,即于分离器下方采用排气管引出空气,气流入口可采用直切式或蜗壳式等型式。
含尘气流内筒体侧面沿切向导入,气流在筒体内旋转向下,大部分气流至排气管排出,另有小部分气流则继续下旋,到达底板时折转流动方向,逆着排气管向上运动到排气口排出,分离出来的粉尘则进入锥体灰斗排出。
华中科技大学、浙江大学、西安交通大学以及清华大学[6~8]等单位对这类旋风分离器进行了详尽的试验及理论研究。
结果表明,该旋风分离器能明显改善锅炉的结构布置,而且还可以提高分离效率,特别适合于循环床锅炉,现已应用于各种容量循环床锅炉的设计。
图4 下排气旋风分离器2.4旋风分离器排尘结构的研究现状 纵观过去的100多年,旋风分离器的主要研究方向还是集中在进出口状况,涡流检测和筒体上,相对于排尘结构部分则很少有人注意。
国内外只有极少数学者进行过相关的研究。
1982年Mot hes[9]发现沿筒壁下降的下旋流与从灰斗上升的气流在锥体底部位置交换特别频繁,于是他提出在此加一防混锥的方法。