塑料收缩率和模具尺寸计算要点
塑料收缩率计算公式

塑料的收缩率是指在塑料制品冷却过程中,由于塑料分子结构重新排列和凝固收缩而导致的尺寸缩小的比例。
塑料的收缩率与塑料材料的种类、成分、工艺条件等因素有关,因此具体的计算公式会有所差异。
以下是一种常用的简化计算收缩率的公式:
收缩率(%)= [(原始尺寸-最终尺寸) / 原始尺寸] ×100
其中,原始尺寸是制品在热态时的尺寸,最终尺寸是制品在冷却后的尺寸。
这个公式假设塑料材料在冷却过程中是等向收缩的,即各个方向的收缩率相同。
需要注意的是,具体的塑料材料和工艺条件会影响收缩率的大小和方向,因此在实际生产中,为了得到更准确的收缩率,通常需要进行实验和测试。
此外,一些塑料制品在设计时会考虑到收缩率,通过调整模具尺寸等方式来补偿收缩,以获得所需的最终尺寸。
模具相关尺寸的计算:

模腔尺寸的计算: (1)、型腔的径向尺寸确定:按平均值计算,塑件的平均收缩率S为0.6% 7级精度模具最大磨损量取塑件公差的1/6;模具的制造公差£z=△/3取x=0.75。
LM1 5.98O+0.48 →6.26O-0.48 (LM1)o+£z=〔(1+s)Ls1-X△〕o+£z =〔(1+0.006)×0.26-0.75×0.48〕0+0.18=5.930+0.16 ②LM2 48O+0.48 →5.28O-0.48 (LM2)o+£z=〔(1+S) ×5.28-0.75×0.48〕o+£z =4.950+0.16 ③LM3 5.15O+0.48 →5.63O-0.48 (LM3)o+£z=〔(1+S) ×5.63-0.75×0.48〕o+£z =5.300+0.16 ④LM4 1O+0.48→1.38O-0.38 (LM4)o+£z=〔(1+S) ×1.38-0.75×0.38〕o+£z=1.100+0.12 ⑤LM5 18.89O+0.88→19.77O-0.88 (LM5)o+£z=〔(1+S)×19.77-0.75×0.88〕o+£z =19.230+0.29 ⑥LM60.96O+0.38→1.34O-0.38 (LM6)o+£z=〔(1+S) ×1.34-0.75×0.38〕o+£z =1.060+0.12 ⑦LM7∮2O+0.38 →∮2.38O-0.38 (LM7)o+£z=〔(1+S) ×2.38-0.75×0.38〕o+£z =2.100+0.12 ⑧LM8 ∮6.1O+0.58 →∮6.68O-0.38 (LM7)o+£z=〔(1+S) ×6.68-0.75×0.38〕o+£z =6.290+0.19 ⑨LM9 ∮0.77→1.05 (LM9) =〔(1+S)*1.05-0.75*0.38〕=0.86 o+0.13 ⑩LM10 10.5 →11.18 (LM10) =〔(1+S)*11.18-0.75*0.68〕 =10.74 (2)、型芯高度尺寸① H 4.7 →5.18 HM1 =〔(1+S)*5.18-0.75*0.48] =[(1+0.006)*4.7+0.5*0.48]=4.97 ② H 8.9 →9.48 HM2 =〔(1+S)*9.48-0.75*0.58〕 =[(1+0.006)*8.9+0.5*0.58] = 9.25 (3)、型芯的径向尺寸:① LM1=5.98 →5.98 LM1 =[(1+s)*Ls+x△] =[(1+0.006)*5.98+0.75*0.48]= 6.37 ②LM2=2.12 →2.12 LM2 =[(1+s)*Ls+X△] =[(1+0.006)*2.12+0.75*0.38] =2.42 (4)、型腔的深度尺寸① H m1 0.77 →1.15 Hm1 =〔(1+s)Hs1-x 〕 =〔(1+0.006)*1.15-0.5*0.38〕=0.97 Hm2 10.5 →11.18 Hm1 =〔(1+s)Hs2-x 〕 =〔(1+0.006)*11.18-0.5*0.68〕 =10.9 (5)斜导柱侧抽芯机构的设计与计算①:抽芯距(S) S=S1+(2→3)㎜ = +(2→3)㎜= +(2→3)㎜ =2.93+2.5㎜ =5.43㎜②:抽芯力(Fc) Fc=chp( cos -sin ) =[2*3.14*(3.1+1)∕2*10 ]*3.5*10 *1*10 *(0.15*cos30-sin30) =60.38N ③: 斜导柱倾斜角()斜导柱倾角是侧抽心机构的主要技术数据之一,它与塑件成型后能否顺利取出以及推出力、推出距离有直接关系。
塑料注塑成型尺寸公差来源

6Y.F/}B~R]3{
设计塑料模时,确定了模具结构之後即可对模具的各部分进行详细设计,即确定各模 板和零件的尺寸,型腔和型芯尺寸等。这时将涉及有关材料收缩率等主要的设计参 数。因而只有具体地掌握成形塑料的收缩率才能确定型腔各部分的尺寸。即使所选模 具结构正确,但所用参数不当,就不可能生产出品质合格的塑件。
浇口形式对收缩率也有影响。用小浇口时,因保压结束之前浇口即固化而使塑件 的收缩率增大。注塑模中的冷却回路结构也是模具设计中的一个关键。冷却回路设计 得不适当,则因塑件各处温度不均衡而产生收缩差,其结果是使塑件尺寸超差或变 形。在薄壁部分,模具温度分布对收缩率的影响则更为明显。
iAx开C思论坛O TR vK-i e6a$N
CAD,EMIXiesn模dg具,设计,招聘,培训[e$L0WcG
w.iAxcnP3W"`j)kC `}x;bn6\
补料:在成形条件中,尽量减少补料以使塑件尺寸保持稳定。但补料不足则无法 保持压力,也会使收缩率增大。
iAx开C思论坛H^p ovd1b8hU bs.iaxcnfqk ]_ `A;i pn
注射压力:注射压力是对收缩率影响较大的因素,特别是充填结束後的保压页号 335 压力。在一般情况下,压力较大的时因材料的密度大,收缩率就较小。
CAD,EMIXiesn模dg具,设计,招聘,培训U.v%K4TC(l CAD,EMIXiesn模dg具,设计,招聘,培训H0[*Ee1L5gv:zD w.iAxcnlh\er|Id9XUC-
注射速度:注射速度对收缩率的影响较小。但对於薄壁塑件或浇口非常小,以及 使用强化材料时,注射速度加快则收缩率小。
塑料模塑件尺寸公差的相关知识

塑料模塑件尺寸公差的相关知识1 引言 (2)2 应用范围 (2)3 概念 (2)4 公差 (3)4.1 一般公差(未注公差尺寸) (3)4.2标注公差尺寸 (3)4.3 模具相关尺寸 (3)4.4 模具无关尺寸 (3)4.5公差的缩减 (4)4.6脱模斜度 (4)4.7形状公差与尺寸公差 (5)4.8排屑加工产品的尺寸公差 (5)4.9 螺纹公差 (5)5 检验条件 (5)1 引言塑料模塑件在制造过程中不可避免的会产生尺寸误差,在生产中产生的尺寸误差通常由下列原因引起:a) 成型工艺:——模塑材料的均一性——成型设备的设定——模具温度——模具在成型压力下的弹性变形b) 模具条件:——模具尺寸的制造公差(参造DIN 16749)——模具的磨损——模具可动部件间的配合误差本标准中的公差是基于上述考虑,同时根据对于大量实际应用的测试结果而确定出来的。
2 应用范围本标准的公差适用于热塑性材料和热固性材料通过模压、传递、压塑和注塑成型的塑料模塑件,而不适用于挤出、吹塑、发泡、烧结,深冲和排屑机加工工艺(pengding)成型的模塑件。
表1 给出了应用于各种模塑材料的推荐公差等级。
3 概念模塑收缩率 VS模塑收缩率是指23±2℃时模腔尺寸L W和模塑件尺寸L F之差,模塑件在成型后应置于标准气氛(DIN 50 014-23/50-2)中16h后立即测量其尺寸。
VS= (1-LW/ LF )*100%流向收缩率 VSR流向收缩率是指成型时注射方向的模塑收缩率。
横向收缩率 VST横向收缩率是指成型时与注射方向相垂直方向的模塑收缩率。
模塑收缩率差∆VS模塑收缩率差是指流向收缩率和横向收缩率之差。
∆VS=VSR-VST更多概念请参考:DIN 7708 part 1 模塑件、压塑件、注塑件、模塑材料DIN 16700 压塑件、传递成型件、挤出、注塑成型件DIN 7182 part 1 & DIN 7168 part 1 公差、偏差、一般公差DIN 7184 part 1 & DIN 7168 part 2 形状公差和位置公差DIN 7724 标准中涉及的高聚物概念4 公差在模塑件检验时应使用本公差,详见第5节。
塑封模具常用计算公式及方法

集成电路塑封模具常用计算公式及方法1 引言随着电子信息产业的迅速发展,集成电路封装产业在国内也随之迅猛发展,但集成电路封装设备--塑封模具却成为制约封装产业发展的瓶颈,长期依靠进口。
本文通过我公司长期制造塑封模具的经验,详细介绍了封装模具常用的计算公式及方法。
2 塑封模具的常用计算公式及方法塑料模具的常用计算公式及方法主要涉及以下几个方面:原材料线涨系数的测量计算;成型型腔尺寸的计算;型腔镶件的线涨匹配;上料框架线涨尺寸的计算。
2.1 原材料线涨系数的测量计算在这里原材料线涨系数的计算,主要针对引线框架的线涨计算,也可适用于其他材料的计算(如铝、钢等)。
在此,只提供计算方法以便灵活应用。
线涨系数指原材料温度每升高1℃,单位长度内所增加的长度。
(1)式中:a为原材料的线涨系数/℃-1;Lt为原材料在t温度时的长度(一般指高温时的长度)/mm;L0为原材料在常温时的的长度/mm;t指高温(一般我们根据封装工艺的特点测试时取175℃/℃:to指常温(一般取20℃)/℃。
例:一种材料在20℃时长150mm,升温到175℃时长度为150.3mm,求线涨系数a为多少?解:a=(150.3-150)/[150×(175-20)]=12.9 X 10-6℃-1。
2.2 成型型腔尺寸的计算(2)式中:L为型腔尺寸/mm;L'为塑件尺寸/mm;S为树脂成型收缩率。
该公式为基本简化公式,具体计算时,根据塑封体外形偏差的大小,适当调整,在此不作累述。
S一般取0.2%~0.4%,在实际使用时根据用户提供的树脂型号选取。
例:塑件外形尺寸为18mm,计算型腔尺寸L,树脂收缩率S为0.35%。
解:L=18x(1+0.35%)=18.063mm2.3 型腔镶件的线涨匹配公式:(3)式中:L模为模具型腔经线涨匹配后的尺寸/mm;L产为引线框架的实测长度尺寸/mm;a产为引线框架的线涨系数/℃-1;a钢为模具型腔所选钢材的线涨系数/℃-1;t工作为模具正常工作时的温度(一般取175℃/℃;t常温为模具室温时的温度(一般取20℃)/℃。
1-4模具内模镶件尺寸的确定

模具内模镶件尺寸的确定二、确定内模镶件外形尺寸确定内模镶件尺寸的方法有两种:经验法和计算法。
在实际工作中常常采用经验确定法而不是计算法。
但对于大型模具、重要模具,为安全起见,最好再用计算法校核其强度和刚度。
确定内模镶件尺寸总体原则是:必须保证模具具有足够的强度和刚度,使模具在使用寿命内不致变形。
1. 内模镶件经验确定法( 1 )确定内模镶件的长、宽尺寸第一步:按上面的排位原则,确定各型腔的摆放位置。
第二步:按下面的经验数据,确定各型腔的相互位置尺寸。
一模多腔的模具,各型腔之间的钢厚B 可根据型腔深度取12 一25mm ,型腔越深,型腔壁应越厚,见图6 。
特殊情况下,型腔之间的钢厚可以取30mm 左右。
特殊情况包括以下几方面。
图 6 图7①当采用潜伏式浇口时,应有足够的潜伏式浇口位置及布置推杆的位置。
②塑料制品尺寸较大,型腔较深(≧ 50mm )时。
③塑料制品尺寸较大,内模镶件固定型芯的孔为通孔。
此时的镶件成框架结构,刚性不好,应加厚型腔壁以提高刚性(见图7)。
图6排位确定镶件大小图7 动模镶件做通孔④型腔之间要通冷却水时,型腔之间距离要大一些。
第三步:确定内模镶件的长、宽尺寸:型腔至内模镶件边之间的钢厚A 可取15 ~50mm 。
制品至内模镶件的边距也与型腔的深度有关,一般制品可参考表1 所列经验数值选定。
表1 型腔至内膜镶件边经验数值型腔深度型腔至内膜镶件边数值/mm 型腔深度型腔至内膜镶件边数值/mm ≦20mm 15~20 30~40 30~3520~30mm 25~30 ﹥40 35~50 注:1 .凸模和凹模的长度和宽度尺寸通常是一样的。
2 .内模镶件的长、宽尺寸应取整数,宽度应尽量和标准模架的推杆板宽度相等。
( 2 )内模镶件高度尺寸的确定内模镶件包括凹模和凸模,厚度与制品高度及制品在分型面上的投影面积有关,一般制品可参考下述经验数值选定。
①凹模厚度A 一般在型腔深度基础上加Wa=15 ~20mm ,当制品在分型面上的投影面积大于200cm2时,W 。
ABS注塑成型收缩率的几点关系

来源于:注塑塑料网/ABS注塑成型收缩率的几点关系塑料收缩率直接关系到制品的形状和尺寸精度。
塑料制品特性、模具设计、工艺条件控制等影响成型收缩率和后收缩的各因素,对注塑制品及其稳定性影响极大[门。
目前模具尺寸的设计通常运用公差带或平均收缩率的方法计算,模具在试模后,根据试制出的制品尺寸来修正模具,然而一些高硬度。
低粗糙度模具的表面尺寸修正起来相当困难,且费工费时,有时甚至无法修正,造成巨大的损失。
所以,要得到所需尺寸的精密注塑件,同时又能尽量减少对模具的修正,就需要充分了解成型收缩率随工艺条件的变化规律,预先精确测定成型收缩率。
(丙烯膨丁二惭苯乙烯)三元共聚物(ABS)塑料综合了丙烯睛的耐化学药品性、耐油性、刚度和硬度,丁二烯的韧性和耐寒性及苯乙烯的电性能,被广泛应用于汽车、电器仪表和机械工业中,是目前通用工程塑料中应用最广泛的品种之一[z]。
国外对塑料成型收缩率的研究开始得较早,且取得了比较丰富的研究成果「3-7],国内专门从事塑料成型收缩率研究的并不多[8-11]。
因此,笔者采用xsrn n oss-so标准测定了^ss塑料在不同工艺条件下注射模塑的成型收缩率,得出了ABS塑料的成型收缩率随工艺条件的变化规律,为制订合理的工艺条件进行正确的工艺控制和模具设计从而生产出合格尺寸的制品提供了重要依据。
一、实验部分(一)主要原材料ABS:IH-100,上海高桥石化公司。
(二)主要设备干燥料斗:FNH-A型,日本日永化工株式会社;模温调节机:NT-55型,日本日永化工株式会社;注塑机:PS40SESASE型,日本日精树脂l业株式会社;模具:按ASTM D 955-89制造,长条模、圆片模,自制。
(三)测试方法试样分别为长条门27.045 mm x 10•000 mm X3.200 mm)和圆片(o101.975 mm)。
测试时运用带百分表的靠模,精度为0.of mm,测试长条形试样在平行于流动方向及圆片形试样在平行和垂直于流动方向上的尺寸变化。
注塑计算公式范文
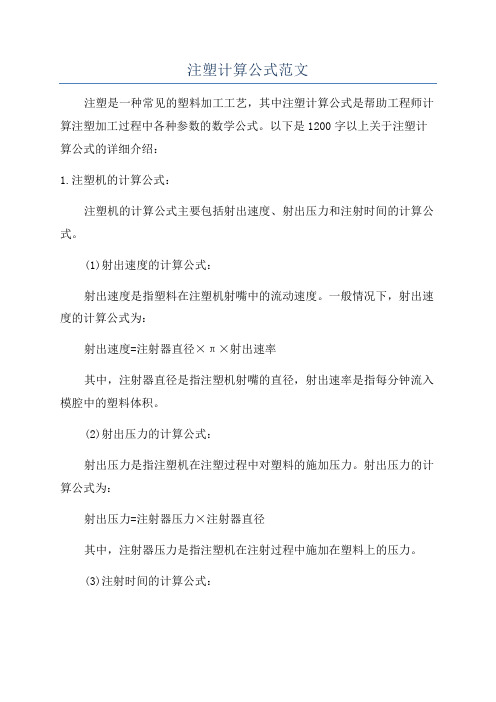
注塑计算公式范文注塑是一种常见的塑料加工工艺,其中注塑计算公式是帮助工程师计算注塑加工过程中各种参数的数学公式。
以下是1200字以上关于注塑计算公式的详细介绍:1.注塑机的计算公式:注塑机的计算公式主要包括射出速度、射出压力和注射时间的计算公式。
(1)射出速度的计算公式:射出速度是指塑料在注塑机射嘴中的流动速度。
一般情况下,射出速度的计算公式为:射出速度=注射器直径×π×射出速率其中,注射器直径是指注塑机射嘴的直径,射出速率是指每分钟流入模腔中的塑料体积。
(2)射出压力的计算公式:射出压力是指注塑机在注塑过程中对塑料的施加压力。
射出压力的计算公式为:射出压力=注射器压力×注射器直径其中,注射器压力是指注塑机在注射过程中施加在塑料上的压力。
(3)注射时间的计算公式:注射时间是指注塑机注射塑料的时间,也就是注射器的运转周期。
注射时间的计算公式为:注射时间=注射器容积/注射速度其中,注射器容积是指注塑机射嘴的容积,注射速度是指塑料从注射器流入模具的速度。
2.模具的计算公式:模具在注塑加工过程中起到了至关重要的作用,模具的计算公式主要包括模具尺寸、模腔容积和模具开合力的计算公式。
(1)模具尺寸的计算公式:模具尺寸是指模具的长度、宽度和高度。
模具尺寸的计算公式由产品设计要求和模具样品的尺寸决定。
(2)模腔容积的计算公式:模腔容积是指模具中可以容纳的塑料体积。
模腔容积的计算公式为:模腔容积=产品体积+塑料收缩率×产品体积其中,产品体积是指注塑产品的体积,塑料收缩率是指塑料在冷却过程中的体积收缩比例。
(3)模具开合力的计算公式:模具开合力是指模具在注塑加工过程中需要施加的开合力量。
模具开合力的计算公式为:模具开合力=施力面积×施力压力其中,施力面积是指模具中需要施加开合力的面积,施力压力是指每平方米需要施加在模具上的压力。
3.注塑产品的计算公式:注塑产品的计算公式主要包括产品尺寸、产品质量和产品收缩率的计算公式。
- 1、下载文档前请自行甄别文档内容的完整性,平台不提供额外的编辑、内容补充、找答案等附加服务。
- 2、"仅部分预览"的文档,不可在线预览部分如存在完整性等问题,可反馈申请退款(可完整预览的文档不适用该条件!)。
- 3、如文档侵犯您的权益,请联系客服反馈,我们会尽快为您处理(人工客服工作时间:9:00-18:30)。
塑料收缩率和模具尺寸计算要点
设计塑料模时,确定了模具结构之后即可对模具的各部分进行详细设计,即确定各模板和零件的尺寸,型腔和型芯尺寸等。
这时将涉及有关材料收缩率等主要的设计参数。
因而只有具体地掌握成形塑料的收缩率才能确定型腔各部分的尺寸。
即使所选模具结构正确,但所用参数不当,就不可能生产出品质合格的塑件。
塑料收缩率及其影响因素
热塑性塑料的特性是在加热后膨胀,冷却后收缩,当然加压以后体积也将缩小。
在注塑成形过程中,首先将熔融塑料注射入模具型腔内,充填结束后熔料冷却固化,从模具中取出塑件时即出现收缩,此收缩称为成型收缩。
塑件从模具取出到稳定这一段时间内,尺寸仍会出现微小的变化,一种变化是继续收缩,此收缩称为后收缩。
另一种变化是某些吸湿性塑料因吸湿而出现膨胀。
例如尼龙610含水量为3%时,尺寸增加量为2%;玻璃纤维增强尼龙66的含水量为40%时尺寸增加量为0.3%。
但其中起主要作用的是成型收缩。
目前确定各种塑料收缩率(成形收缩+后收缩)的方法,一般都推荐德国国家标准中DIN16901的规定。
即以23℃±0.1℃时模具型腔尺寸与成型后放置24小时,在温度为23℃,相对湿度为50±5%条件下测量出的相应塑件尺寸之差算出。
收缩率S由下式表示:
S={(D-M)/D}×100% (1)
其中:
S-收缩率;
D-模具尺寸;
M-塑件尺寸。
如果按已知塑件尺寸和材料收缩率计算模具型腔则为 D=M/(1-S)。
在模具设计中为了简化计算,一般使用下式求模具尺寸:
D=M MS (2)
如果需实施较为精确的计算,则应用下式:
D=M MS MS2 (3)
但在确定收缩率时,由于实际的收缩率要受众多因素的影响也只能使用近似值,因而用式(2)计算型腔尺寸也基本上满足要求。
在制造模具时,型腔则按照下偏差加工,型芯则按上偏差加工,便于必要时可作适当的修整。
难于精确确定收缩率的主要原因,首先是因各种塑料的收缩率不是一个定值,而是一个范围。
因为不同工厂生产的同种材料的收缩率不相同,即使是一个工厂生产的不同批号同种材料的收缩率也不一样。
因而各厂只能为用户提供该厂所生产塑料的收缩率范围。
其次,在成形过程中的实际收缩率还受到塑件形状,模具结构和成形条件等因素的影响。
下面对这些因素的影响作一介绍。
塑件形状
对于成型件壁厚来说,一般由于厚壁的冷却时间较长,因而收缩率也较大。
对一般塑件来说,当熔料流动方向L尺寸与垂直于熔料流方向W尺寸的差异较大时,则收缩率差异也较大。
从熔料流动距离来看,远离浇口部分的压力损失大,因而该处的收缩率也比靠近浇口部位大。
因加强筋、孔、凸台和雕刻等形状具有收缩抗力,因而这些部位的收缩率较小。
模具结构
浇口形式对收缩率也有影响。
用小浇口时,因保压结束之前浇口即固化而使塑件的收缩率增大。
注塑模中的冷却回路结构也是模具设计中的一个关键。
冷却回路设计得不适当,则因塑件各处温度不均衡而产生收缩差,其结果是使塑件尺寸超差或变形。
在薄壁部分,模具温度分布对收缩率的影响则更为明显。
成型条件
料筒温度:料筒温度(塑料温度)较高时,压力传递较好而使收缩力减小。
但用小浇口时,因浇口固化早而使收缩率仍较大。
对于厚壁塑件来说,即使料筒温度较高,其收缩仍较大。
补料:在成型条件中,尽量减少补料以使塑件尺寸保持稳定。
但补料不足则无法保持压力,也会使收缩率增大。
注射压力:注射压力是对收缩率影响较大的因素,特别是充填结束后的保压压力。
在一般情况下,压力较大时,因材料的密度大,收缩率就较小。
注射速度:注射速度对收缩率的影响较小。
但对于薄壁塑件或浇口非常小,以及使用强化材料时,注射速度加快则收缩率小。
模具温度:通常模具温度较高时收缩率也较大。
但对于薄壁塑件,模具温度高则熔料的流动阻抗小,而收缩率反而较小。
成型周期:成型周期与收缩率无直接关系。
但需注意,当加快成型周期时,模具温度、熔料温度等必然也发生变化,从而也影响收缩率的变化。
在做材料试验时,应按照由所需产量决定的成型周期进行成型,并对塑件尺寸进行检验。
用一模具进行塑料收缩率试验的实例如下。
注射机:锁模力70t,螺杆直径Φ35mm,螺杆转速80rpm;
成型条件:最高注射压力178MPa,料筒温度230(225-230-220-210)℃、
240(235-240-230-220)℃、250(245-250-240-230)℃、260(225-260-250-240)℃,注射速度57cm3/s,注射时间0.44~0.52s,保压时间6.0s,冷却时间15.0s。
模具尺寸和制造公差
模具型腔和型芯的加工尺寸除了通过D=M(1 S)公式计算基本尺寸之外,还有一个加工公差的问题。
按照惯例,模具的加工公差为塑件公差的1/3。
但由于塑料收缩率范围和稳定性各有差异,首先必须合理化确定不同塑料所成形塑件的尺寸公差。
即由收缩率范围较大或收缩率稳定较差塑料成形塑件的尺寸公差应取得大一些。
否则就可能出现大量尺寸超差的废品。
为此,各国对塑料件的尺寸公差专门制订了国家标准或行业标准。
中国也曾制订了部级专业标准。
但大都无相应的模具型腔的尺寸公差。
德国国家标准中专门制订了塑件尺寸公差的DIN16901标准及相应的模具型腔尺寸公差的DIN16749标准。
此标准在世界上具有较大的影响,因而可供塑料模具行业参考。
关于塑件的尺寸公差和允许偏差
为了合理地确定不同收缩特性材料所成形塑件的尺寸公差,让标准引入了成形收缩差△VS这一概念。
△VS=VSR-VST (4)
式中:
△VS-成形收缩差;
VSR-熔料流动方向的成形收缩率;
VST-与熔料流动垂直方向的成形收缩率。
根据塑料△VS值,将各种塑料的收缩特性分为4个组。
△VS值最小的组是高精度组,以此类推,△VS值最大的组为低精度组。
并按照基本尺寸编制了精密技术、110、120、130、140、150和160公差组。
并规定,用收缩特性最稳定的塑料成形塑件的尺寸公差可选用110、120和130组。
用收缩特性中等稳定的塑料成形塑件的尺寸公差选用120、130和140。
如果用这类塑料成形塑件的尺寸公差选用110组时,即可能出大量尺寸超差塑件。
用收缩特性较差的塑料成形塑件的尺寸公差选用130、140和150组。
用收缩特性最差的塑料成形塑件的尺寸公差选用140、150和160组。
在使用此公差表时,还需注意以下各点。
表中的一般公差用于不注明公差的尺寸公差。
直接标注偏差的公差是用于对塑件尺寸标注公差的公差带。
其上、下偏差可设计人员自行确定。
例如公差带为0.8mm,则可以选用以下各种上、下偏差构成。
0.0、-0.8、±0.4、-0.2、-0.5等。
每一公差组中均有A、B两组公差值。
其中A是由模具零件组合形成的尺寸,增加了模具零件对合处不密合所形成的错差。
此增加值为0.2mm。
其中B是直接由模具零件所决定的尺寸。
精密技术是专门设立的一组公差值,供具有高精度要求塑件使用。
在此用塑件公差之前,首先必须知道所使用的塑料适用哪几个公差组。
模具的制造公差
德国国家标准针对塑件公差制订了相应模具制造公差的标准DIN16749。
该表中共设4种公差。
不论何种材料的塑件,其中不注明尺寸公差尺寸的模具制造公差均使用序号1的公差。
具体公差值由基本尺寸范围确定。
不论何种材料塑件中等精度尺寸的模具制造公差为序号2的公差。
不论何种材料塑件较高精度尺寸的模具制造公差为序号3的公差。
精密技术相应的模具制造公差为序号4的公差。
可以合理地确定各种材料塑件的合理公差和相应的模具制造公差,这不仅给模具制造带来方便,还可以减少废品,提高经济效期益。