硅化物涂层电子束重熔表面改性技术
电子束表面处理

2. 5 电子束表面薄层退火
当电子束作为表面薄层退火热源使用时,所需要的功率 密度要较上述方法低很多,以此降低材料的冷却速度。对于 金属材料,此法主要应用于薄带的表面处理。另外,电子束 退火还成功地应用于半导体材料上。
3. 电子束表面处理的发展前景
近些年电子束表面处理从宏观性能的改变到微观作用 机理的研究得到了进一步的深入发展,有学者通过数值模 拟的方法分析电子束处理过程的温度场、浓度场和应力场 的分布及变化。电子束处理后改变了表层金属和合金的微 观结 构,可以获得过饱和固溶体等非平衡结构,从而达到 提高材料表面性能的目的。
2. 4 电子束表面非晶化处理
将电子束的平均功率密度提高到 106 ~ 107W/cm2,作用时 间缩短至 10-5 s左右,使金属在基体与熔化的表层之间产生很 大的温度梯度,在停止电子束照射后,金属表面快速冷却速 率(107~ 9 / s)远远超过常规制取非晶的冷却速率(103~ 6 / s),所 获非晶的组织形态致密,抗疲劳及抗腐蚀性能优良。
2. 2 电子束表面重熔处理
电子束重熔可使合金的化学元素重新分布,降低某些 元素的显微偏析程度,从而改善工件表面的性能。由于电 子束重熔是在真空条件下进行的有利于防止表面的氧化, 因此电子束重熔处理特别适用于化学活性高的镁合金、铝 合金等的表面处理。
2. 3 电子束表面合金化
一般选择 W、Ti、B、Mo 等元素及其碳化物作为合 金元素提高材料耐磨性;选择 Ni、Cr 等元素可提高材料 的抗腐蚀性能;而适当添加 Co、Ni、Si 等元素能改善合金 化效果。
通过控制电子束处理参数以及不同的处理工艺, 可以 达到不同的表面改性效果。可将目前的电子束表面改性技 术分为以下几种类型: 电子束表面相变强化、重熔处理、合金化、熔敷、电子束 表面非晶化处理、薄层退火。
大连理工大学科技成果——核主泵关键部件表面强化技术原理与工艺

Theory and Technology of Surface Modification Techniques for NCP Application
研究背景与来源
大型先进压水堆核电站核主泵,是核电站的“心脏”,也是核电技术国产化最后一
个难度最大的重大装备。核主泵驱动核岛内的高温高压水循环,将反应堆芯核裂变的热 能传递给蒸汽发生器产生蒸汽,推动汽轮机发电,设计工作压力17 MPa,流量24000 m3/h,扬程100 m,温度340 ℃,工作效率79%以上。核主泵水润滑轴承、机械密封、 转子组件等关键部件在高温高压及辐射环境中,要满足长期安全可靠使役要求,亟待研 究和解决关键部件耐磨减摩、抗蚀、抗疲劳等表面强化的难题,实现核主泵自主化制造 的突破。
硬质合金冲击强化 (减摩耐磨性能改善 )
硬质合金密封环冲击强化
等离子体源渗氮技术工艺装备
强流脉冲离子束表面工程装备
超音速喷涂硬质合金涂层装备 水润滑轴承表面强化
阶段研究成果
研究工作发表SCI学术论文32篇,授权发明专利3项,国际会议大会邀请报告2次。
(3)发展出强流脉冲离子束无约束冲击强化技术,在硬质合金上耦合形成了数微米重熔改性层和数百微米 冲击硬化层,克服了现有的载能束重熔强化易开裂、冲击效率低的局限性,解决了核级硬质合金部件表面 强化的难题。
等离子体
离子注入层 鞘层
扩散层
等离子体基低能离子注入传质机制
激光束
光吸收层
透明约束层
大面积强流脉冲离子束
(1)发展出低温、高效等离子体基低能离子注入技术,在不锈钢部件上获得高硬高韧、单一过饱和面心立 方相γN改性层,突破了现有第二相强化表面改性方法破坏耐蚀性的局限性,解决了不锈钢部件耐磨抗蚀复 合改性的难题;
高能束表面改性技术

国内自20世纪80年代以来激光相变硬化工艺的应用开发在车辆、机械、矿山、模具等方面也有许多成功的实例并建立了生产线,例如对汽车或拖拉机汽缸套内壁进行激光相变硬化处理,使汽缸套的使用寿命成倍提高。
*
激光合金化与激光熔覆
激光合金化与熔覆是同一种类型的工艺,它们的区别仅在于,激光合金化所形成的合金层的成分是介于施加合金与基体金属之间的中间成分,即施加合金受到较大或一定的稀释。而激光熔敷则是除较窄的结合层外,施加合金基本保持原成分很少受到稀释。 这些区别可以由被施加材料、施加合金成分、施加形式及量和激光工艺参数的改变来达到。
#2022
*
电子束表面处理的特点
2.电子束表面改性工艺
1)电子束表面相变硬化
电子束表面相变硬化也称电子束表面淬火,是用高能量的电子束快速扫描工件,控制加热速度为103~105℃/s,使金属表面薄层被快速加热到相变点以上,此刻工件基体仍处于冷态。随着电子束的移开和热传导作用,表面热量迅速向工件心部或其他区域传递,高速冷却(冷却速度达108K/s~1010 K/s)产生马氏体等相变,在瞬间实现自冷淬火。
01
扫描速度太慢,会导致金属表面温度超过熔点,或者加热深度过深,不能自冷淬火。扫描速度太快,则可能使表面达不到相变温度。功率密度则受激光器功率和和光斑尺寸的影响,功率密度太小,表面得不到足够的热量,不能达到所需的相变温度。
02
*
常用的黑化处理方法有磷化法、碳素法和熔覆红外能量吸收材料(如胶体石墨、含炭黑和硅酸钠或硅酸钾的涂料等)。其中磷化法最好,其吸收率可达80%~90%,膜厚仅为5μm,具有较好的防锈性,激光处理后不用清除即可用来装配。
*
3)电子束表面合金化
电子束表面合金化与激光表面合金化有些相似,将某些具有特殊性能的合金粉末或化合物粉末如B4C、WC等粉末预涂敷在金属的表面上,然后用电子束加热,或在电子束作用的同时加入所需合金粉末使其熔融在工件表面上,在表面形成与原金属材料的成分和组织完全不同的新的合金层,从而使零件或零件的某些部位提高耐磨性、耐蚀性、耐高温氧化的特种性能。
电子束选区熔化增材制造技术研究现状分析

电子束选区熔化增材制造技术研究现状分析1. 本文概述随着现代制造业的快速发展,增材制造技术作为一种创新制造方法,在航空航天、生物医疗、汽车制造等领域展现出了巨大的应用潜力。
电子束选区熔化(Electron Beam Selective Melting, EBSM)作为增材制造技术的一种,以其高精度、高效率和优异的机械性能等特点受到广泛关注。
本文旨在对电子束选区熔化增材制造技术的研究现状进行全面分析,包括其工作原理、关键工艺参数、材料适用性、优势与挑战以及在不同领域的应用情况。
通过对现有文献的综述和案例分析,本文将深入探讨EBSM技术的发展趋势,为其未来的研究和应用提供理论指导和实践参考。
2. 电子束选区熔化增材制造技术基本原理EBSM系统首先通过电子枪产生高能电子束。
电子枪通常采用场发射或热发射的方式,产生高速电子流。
这些电子流在高压电场的作用下被加速,形成高能电子束。
电子束的能量密度通常在107至109Wcm范围内,足以熔化大多数金属和合金。
电子束在计算机控制下精确地扫描金属粉末层。
当电子束照射到粉末上时,其能量被粉末吸收并转化为热能,导致粉末局部熔化。
电子束的扫描路径和功率密度可以精确控制,以确保只有预定区域的粉末被熔化。
熔化的粉末在重力和表面张力的作用下保持形状,并与下层已固化的材料相结合。
随着电子束的连续扫描,熔化区域逐渐扩展,逐层构建出所需的三维结构。
这一过程中,熔化与凝固快速交替进行,要求精确控制温度,以防止热应力和变形。
EBSM过程通常在真空或保护气氛中进行,以防止熔化金属与空气中的氧气、氮气等发生反应,避免氧化和污染。
气氛控制对于保持零件质量至关重要,特别是在处理易氧化或对气氛敏感的合金时。
制造完成后,零件通常需要去除支撑结构并进行后续的热处理、机加工等,以达到最终的设计要求和使用性能。
电子束选区熔化增材制造技术因其高能量密度、高精度和良好的材料适应性,在航空航天、生物医疗、高端制造等领域展现出巨大的应用潜力。
涂层表面改性提高材料耐腐蚀性策略
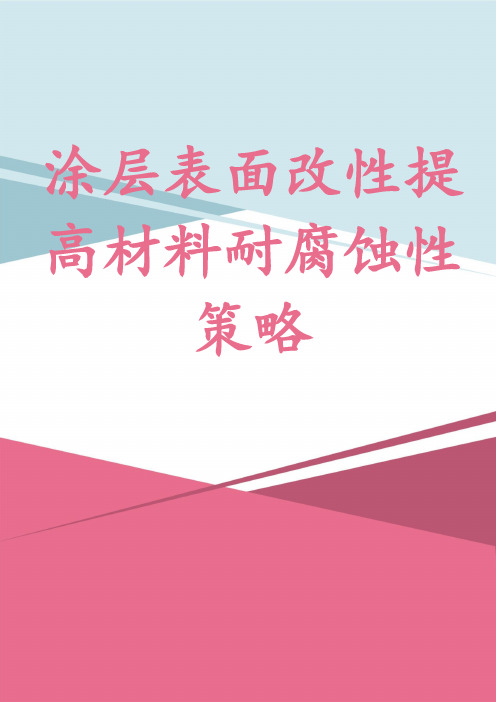
涂层表面改性提高材料耐腐蚀性策略一、涂层表面改性技术概述涂层表面改性技术是一种通过在材料表面施加涂层来提高其耐腐蚀性能的方法。
这种技术广泛应用于各种工业领域,尤其在海洋、化工、航空航天等对材料耐腐蚀性有特殊要求的行业中。
涂层不仅可以提高材料的耐腐蚀性,还能增强其耐磨性、耐高温性等其他性能。
1.1 涂层表面改性技术的核心原理涂层表面改性技术的核心原理是通过在材料表面形成一层保护膜,这层膜可以是金属的、非金属的或者有机的,其目的是隔离材料与腐蚀介质的接触,从而减缓或阻止腐蚀过程的发生。
涂层的保护作用主要体现在以下几个方面:- 物理隔离:涂层形成一层屏障,阻止腐蚀介质如氧气、水分和腐蚀性化学物质与材料基体接触。
- 化学保护:某些涂层材料含有能够与腐蚀介质反应的活性成分,通过化学反应消耗腐蚀介质,减缓腐蚀过程。
- 电化学保护:涂层可以通过形成电化学屏障,改变材料表面的电位,从而抑制腐蚀电池的形成。
1.2 涂层表面改性技术的应用领域涂层表面改性技术的应用领域非常广泛,主要包括以下几个方面:- 海洋工程:海洋环境中的高盐分和微生物活动对材料腐蚀性极强,涂层技术可以有效提高海洋工程结构的耐腐蚀性。
- 化工行业:化工设备经常接触各种腐蚀性化学品,涂层技术可以保护设备免受化学腐蚀。
- 航空航天:航空航天器在极端环境下工作,涂层技术可以提高其结构材料的耐腐蚀性和耐高温性。
二、涂层表面改性技术的种类与发展涂层表面改性技术经过多年的发展,已经形成了多种类型,每种类型都有其独特的性能和应用场景。
2.1 传统涂层技术传统涂层技术主要包括热喷涂、电镀、化学镀等方法。
这些方法通过在材料表面形成一层金属或合金涂层来提高其耐腐蚀性。
虽然这些技术成熟可靠,但存在一些局限性,如涂层与基体的结合力较弱,涂层的均匀性和致密性难以保证。
2.2 高性能涂层技术随着科技的进步,新型高性能涂层技术应运而生,如纳米涂层、复合涂层、自修复涂层等。
这些技术利用纳米材料的独特性能,或者通过复合多种材料来提高涂层的综合性能。
表面工程技术及其应用

已损伤后的船舶柴油机气缸盖
25
船舶螺旋桨
26
锅炉水冷壁现场喷涂NiCr合金防腐耐磨涂层
27
喷涂防腐耐磨涂层后的水冷壁管
28
超音速火焰喷涂制备纳米WC-12Co防腐耐磨涂层
29
HVOF制备纳米WC-12Co涂层后的浆液循环泵叶轮
30
防腐处理后的浆液循环泵叶轮
31
表面工程的概念
1. 表面工程的概念: 它是指将固体材料表面预处理后,通过表面涂覆、 表面改性或多种表面技术复合处理,改变固体材料表面的形态、化 学成分和组织结构,以获得所需要的表面性能的系统工程。 2. 表面工程的学科体内容: 表面工程基础理论; 表面工程技术及复合表面技术; 表面加工技术; 表面质量检测与控制; 表面工程技术设计等。 3. 表面工程基础理论:表面失效分析、表面摩擦与磨损、表面腐蚀与 防护、表面界面结合与复合。
37
表面工程技术的发展
1. 传统的表面工程技术:表面热处理、表面渗碳及油漆技术。
1) 秦兵马俑宝剑表面是采用铬盐氧化工艺处理;“唐三彩”及 “景泰蓝”的处理工艺。 2) 高分子涂装技术:50年代油性涂料、天然树脂涂料→合成树 脂→水系涂料。 3) 传统的表面淬火:火焰加热→高频加热→激光束、电子束淬 火。 4) 渗碳工艺:自动控制、离子渗碳改善渗碳质量和速度。 5) 电镀及电刷镀技术:纯金属镀Zn、Cr、Ni、Cu(Cu-NiCr)→镀覆多种合金→复合金属陶瓷镀层→纳米刷镀层。 6) 热喷涂技术:装饰性和防护性涂层到制备各种功能性涂层, 如:气阀涂层、活塞环涂层等。
44
表面工程技术的分类
6. 按表面改性的机制分类:
1) 表面合金化:离子轰击热处理、化学热处理、 激光化学热处理、离子注入、离子混合或重熔。
电子束表面改性技术的研究及应用探讨
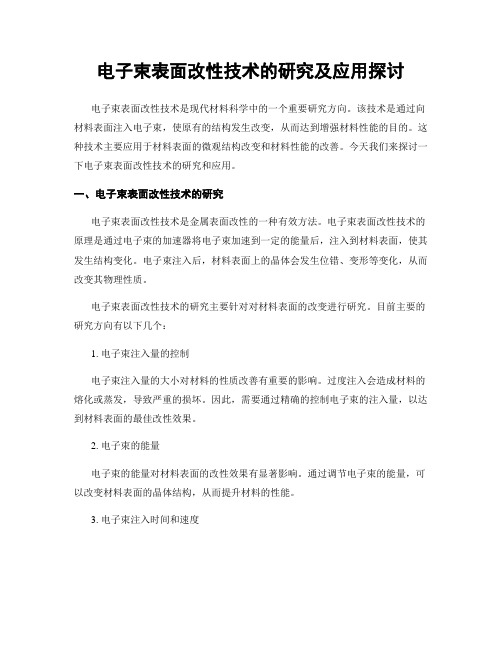
电子束表面改性技术的研究及应用探讨电子束表面改性技术是现代材料科学中的一个重要研究方向。
该技术是通过向材料表面注入电子束,使原有的结构发生改变,从而达到增强材料性能的目的。
这种技术主要应用于材料表面的微观结构改变和材料性能的改善。
今天我们来探讨一下电子束表面改性技术的研究和应用。
一、电子束表面改性技术的研究电子束表面改性技术是金属表面改性的一种有效方法。
电子束表面改性技术的原理是通过电子束的加速器将电子束加速到一定的能量后,注入到材料表面,使其发生结构变化。
电子束注入后,材料表面上的晶体会发生位错、变形等变化,从而改变其物理性质。
电子束表面改性技术的研究主要针对对材料表面的改变进行研究。
目前主要的研究方向有以下几个:1. 电子束注入量的控制电子束注入量的大小对材料的性质改善有重要的影响。
过度注入会造成材料的熔化或蒸发,导致严重的损坏。
因此,需要通过精确的控制电子束的注入量,以达到材料表面的最佳改性效果。
2. 电子束的能量电子束的能量对材料表面的改性效果有显著影响。
通过调节电子束的能量,可以改变材料表面的晶体结构,从而提升材料的性能。
3. 电子束注入时间和速度电子束注入时间和速度也对电子束表面改性技术的效果有重要的影响。
一般来说,注入时间和速度都需要控制在合适的范围内,以避免材料表面的熔化、蒸发或其他形变等问题。
二、电子束表面改性技术的应用电子束表面改性技术的应用不仅局限于材料改性,还可以应用于其他领域。
以下是其主要应用领域:1. 电子束表面改性技术在航空航天领域的应用电子束表面改性技术在航空航天领域的应用越来越广泛。
它可以用于制造各种支架、引擎和其他重要部件。
电子束表面改性技术可以提升这些材料的性能,降低摩擦系数和阻力等,大大提高了安全性和寿命。
2. 电子束表面改性技术在医学领域的应用电子束表面改性技术在医学领域的应用也很广泛。
它可以用于制造人造骨骼植入物、心脏支架和其他医疗器械。
电子束表面改性技术还可以增强这些材料的生物相容性,从而减少排异反应的几率。
电子束熔覆改性技术扫描波形设计

Ke r Elcr n b a r — h n Elcr n b a s a n n g r S ra e metn n o i f ai n, o r y wo ds e to e m eme i g, e to e m c n i g f u e, u c l g a d s l i to P we i f i di c
ca dng p o e s EB s a nig fg r s a pv tlfc o f ci g t e t mp rt r e d o e me t g s ra e i h ld i r c s . c n n ue i ioa a traf tn h e e au e f l ft r — l n u c n te i e i he i f prc s fEB mo i c to o e so d f ain. i
A s a t h cn igf uew s ei e -r S f h l t nb a E bt c T esann gr a d s nd i t r — eee r em( B)c aat i i . i nu l y r i g f ef o t i co hrce sc Tt im al rts a o
的 关键 因素 :
关键词 电子 束重熔 , 扫描 波形 , 面熔凝 , 表 能量 分布 , 温度场 ,熔化深度
S a n n iu e De in o e to a c n i g F g r sg fEl cr n Be m
C a dn d f ai n Te h i u ld i g Mo i c t c n q e i o
化物涂层 重熔试验 , 研究 了扫描 波形对 电子束 单道 熔覆 能量输入 均 匀性的影响 。 结果表 明 , 电子束 熔覆过 程 中 熔池表 面温度场 均 匀性是 扫描波形 、 电子束束斑 品质 、 描 频 率和 工 艺参数综 合影 响 的结 果 , 设 计 波形 可用 扫 所 于电子柬熔覆表 面改性技 术 , 改性层厚度 均匀一致 , 扫描 波形是 影 响 电子束 熔覆过程 中熔池表 面温度 场 均 匀性
- 1、下载文档前请自行甄别文档内容的完整性,平台不提供额外的编辑、内容补充、找答案等附加服务。
- 2、"仅部分预览"的文档,不可在线预览部分如存在完整性等问题,可反馈申请退款(可完整预览的文档不适用该条件!)。
- 3、如文档侵犯您的权益,请联系客服反馈,我们会尽快为您处理(人工客服工作时间:9:00-18:30)。
中国空间科学技术 2010年10月 Chinese Space Science and T echnology 第 5 期硅化物涂层电子束重熔表面改性技术于斌 靳庆臣 刘志栋 何俊(兰州物理研究所,兰州730000)摘要在Nb521铌合金表面采用料浆烧结法制备硅化物涂层,利用高频扫描电子束对硅化物涂层进行重熔处理,通过扫描电子显微镜对处理样品表面形貌进行组织结构分析。
研究表明,经过电子束重熔处理,硅化物涂层表面陶瓷晶粒粒度降低,表面粗糙度降低,陶瓷颗粒之间烧结作用增强,重熔区域与未处理区域具有明显的边界,电子束能量分布较均匀,电子束重熔提高了硅化物涂层的抗氧化性能和抗热震性能。
关键词电子束重熔 表面粗糙度抗氧化性能 形貌 硅化物涂层 卫星1 引言铌是一种难熔金属,由于其在高温下有较好的力学性能而被广泛地应用于航空、航天等领域,但是铌合金的氧化行为使其应用受到限制[1]。
硅化物涂层作为铌合金的高温保护涂层,在高温氧化时,涂层表面形成一层玻璃态氧化物膜,延长涂层的高温使用寿命,在高温氧化过程中,熔融态硅化物可以封闭涂层中的裂纹。
这一现象受到学者们的广泛关注,并开展了进一步提高硅化物涂层的抗氧化性能的研究[2]。
涂层的电子束重熔可以改善涂层组织及提高性能[3]。
Weisenbur ge对镍基合金表面CoNiCrAlY 涂层进行了电子束重熔研究,处理后超音速火焰喷涂涂层和真空等离子喷涂涂层表面粗糙度分别由62 m和47 m下降至3 7 m和8 m,近表层30~40 m厚度范围内气孔被彻底消除,高温氧化试验涂层氧化膜增长速率降低[4]。
H am atani对CoCrW合金表面应用高速火焰热喷涂法制备的NiCrFeSi涂层进行电子束重熔研究,指出涂层气孔数量、表面粗糙度和涂层/基体界面粘结强度是优化电子束改性工艺参数的标准[5]。
U tu研究了电子束重熔对高速火焰热喷涂方法制备的CoNiCrAlY涂层耐腐蚀性能的影响,电子束重熔技术可以显著降低涂层气孔和氧化物含量,涂层耐腐蚀性能有较大程度的提高[6]。
目前,星用发动机材料多为以硅化物体为抗氧化涂层的铌合金,因此,延长硅化物涂层的抗氧化寿命是卫星长寿命发展的需求,为此作者研究了电子束重熔对铌合金表面硅化物涂层的表面形貌和性能的影响。
2 试验方法试验用基体材料为铌合金,利用烧结方法制备硅化物涂层,涂层试样尺寸为50mm 12m m 3m m,试验设备是法国T ECH M ET A公司生产的6kW电子束焊机。
首先进行电子束扫描波形的设计,然后利用该波形的电子束对硅化物涂层进行重熔处理;通过工作台的移动实现电子束对试验样品表面的垂直辐照,在真空条件下,利用优化的工艺参数进行涂层单道电子束重熔改性处理。
工艺参数见表1。
利用JSM 5500扫描电镜分析重熔涂层表面组织形貌。
收稿日期:2009 11 03。
收修改稿日期:2010 03 16表1 硅化物涂层电子束重熔工艺参数工艺参数电压/kV电流/mA 重熔速率/(mm/min)扫描频率/H z 规范3093002003电子束扫描波形设计电子束扫描能量输入均匀性是开展电子束表面改性技术前提,电子束扫描波形直接影响电子束熔覆涂层表面熔池的温度场,进而影响熔池表面温度及熔体的粘度、熔体密度、合金元素的扩散、熔覆改性层组织结构均匀性、表面平整度、气孔或裂纹。
Knyazeva 指出电子束扫描频率大于50H z 时在波形范围内产生的热输入等同于一个有效热源[7]。
电子束扫描控制系统研究表明,频率至少在500H z 以上时,平面加热才可以认为是面热源,此时所获得温度场的温度起伏较小,当扫描的频率达到1000H z 时几乎可以认为没有温度的波动。
图1 扫描波形轨迹电子束几乎没有质量和惯性,可以通过电磁场的控制实现电子束的偏转扫描。
通过前期大量试验验证,按照以下要求设计波形,可以保证电子束扫描波形范围内能量输入较均匀:1)扫描波形左右对称;2)扫描波形由光滑曲线构成;3)扫描波形上轨迹和下轨迹曲率相近,即包含的离散化数据点相近;4)扫描波形中不出现尖锐拐点;5)扫描波形高频扫描时无畸变现象;6)扫描波形纵向幅值小于横向幅值,纵向即为电子束重熔时工件运动方向。
获取能量输入较均匀的扫描波形参数和形状分别如表2和图1(a)所示。
电子束扫描波形轨迹见图1,其中所设计扫描波形轨迹如图1(a),电子束扫描等效热源近似形状如图1(b)。
表2 电子束扫描波形参数波形参数波形幅值/mm 束斑直径/mm 扫描方式扫描波形轨迹设计112 6线扫描见图14 试验结果与讨论图2左侧和右侧分别为同一试样铌合金硅化物涂层重熔后表面形貌和原涂层表面形貌,电子束图2 硅化物涂层电子束重熔表面形貌重熔快速熔化和凝固过程导致涂层表面晶粒粒度降低,增强了硅化物金属陶瓷涂层的烧结作用,涂层表面大晶粒被电子束打碎熔化,凝结为小颗粒并烧结在一起,重熔层表面和原涂层表面界面分明说明电子束能量输入较均匀。
图3(a)和(c)所示为硅化物涂层重熔前表面形貌。
铌合金表面料浆烧结制备硅化物涂层是通过固液反应扩散形成的,涂层表面粗糙度较大,绝大部分由熔融的岛屿状表面相连接。
在烧结后期冷却过程中,涂层中金属硅化物冷却收缩,表面颗粒之间有较大的应力存在,涂层表面表现为粗糙的岛屿状相连,并形成微小孔洞,孔洞为氧提供了扩散通道,可见硅化物通过烧结不能完全抑制空洞的产生[8]。
此外由于孔洞的存在,在氧化的过程中,在此处造成氧的积累和氧浓度的提高,促进氧向涂层和铌合金基体扩散,使涂层寿命降低。
金属陶瓷涂层电子束重熔过程相当对涂层进行二次烧结作用,电子束重熔后的涂层表面仍较粗糙,但表面陶瓷颗粒形态及分布较均匀,涂层/基体的冶金结合增强。
文献[9]研究表明,二次熔烧的涂层比加涂一次的涂层表面组织均匀、致密,具有更宽的过渡层。
过渡层可有效阻止裂纹的进一步扩展,从而提高涂层的高温抗氧化性能。
如图3(b)和(d)所示,电子束重熔处理后,涂层表面陶瓷颗粒的烧结作用增强,较大颗粒被电子束击碎熔化冷却成为小颗粒烧结在一起,表面熔化较均匀,表面粗糙度降低。
由于涂层表面凸起颗粒熔化填补孔隙,重熔后涂层表面空洞密度降低。
本文采用高频扫描电子束进行重熔,高频扫描电子束在波形范围内等同于一个等效热源[7],涂层在电子束加热熔化情况下,经过电子束扫描搅拌涂层表面熔池,使涂层表面熔化金属流向空隙的倾向增强,从而使涂层更致密,空隙率降低。
电子束重熔促进涂层/基体之间的元素扩散,增强涂层元素的渗透深度,过渡层宽化,提高涂层/基体的粘结强度,电子束能量输入均匀性保证了涂层/基体熔化连续,且增强了涂层的致密度,降低孔隙率,能够有效地阻止氧向基体扩散,起到对铌合金基体的保护作用。
图3 硅化物涂层重熔前后表面形貌对比由图3(d)可见,电子束重熔处理后,在表面产生了若干裂纹,这是由于电子束重熔过程中,涂层中高熔点的铌硅金属间化合物快速熔化和冷却收缩,在热应力作用下,表面颗粒之间产生很大的应力,尤其是形状不规则的颗粒的一些曲率半径较小的尖角处,存在应力集中,很容易使这些区域萌生裂纹。
在涂层快速凝固过程中,涂层、涂层和基体的结合界面及基体发生了不同程度的凝固收缩,由此引发的应力也促使裂纹进一步扩展。
裂纹附近陶瓷颗粒几乎未产生塑性变形,涂层对裂纹扩展的阻碍作用很小,硅化物涂层韧性较差,说明热应力较大,远远高于陶瓷颗粒界面间的断裂强度。
电子束重熔的裂纹防治问题是电子束表面改性技术开展的前提,前期研究表明,硅化物涂层电子束重熔裂纹产生的倾向很大,在能量密度相同的前提下,采用小束流、慢速、大扫描半径、高频扫描进行重熔,可以获取无裂纹的重熔涂层。
电子束重熔处理后涂层表面粗糙度显著降低,表面陶瓷颗粒粒度降低,这与SEM得到的分析结果一致。
扫描电子束使涂层快速熔化凝固,涂层表面凸起陶瓷颗粒首先被熔化而凝固为细小颗粒,熔化金属由于重力作用填补颗粒之间的空隙,使得凸起颗粒消除和凹陷部位生长。
电子束的高频扫描使扫描波形范围内能量输入均匀,表面熔池各区域温度梯度小,熔池液态金属均匀流动,金属元素扩散均匀。
电子在波形范围内高频扫描对涂层表面熔池起到搅拌作用,提高了涂层表面熔池的流动性,液态金属流向凹陷部位的能力增强。
上述原因导致重熔后涂层表面粗糙度降低。
重熔涂层经过高温氧化试验及热震试验表明,涂层抗热震能力显著提高,这是因为电子束重熔增强了涂层/基体的冶金结合,提高了涂层/基体的粘结强度。
重熔使涂层/基体元素扩散作用增强,由于Nb的渗透使硅化物涂层韧性提高,过渡层宽化,涂层/基体在快速升温和降温过程中的应变协调性提高,涂层和基体界面裂纹产生倾向降低。
涂层表面粗糙度降低,在表面陶瓷颗粒之间由于凝固收缩产生了应力减小,应力集中的倾向减小,在这些区域萌生裂纹的可能性降低。
涂层空隙率降低,涂层进一步烧结,组织细化致密,提高了对氧原子渗透的阻碍作用。
上述诸多因素导致硅化物涂层的高温抗氧化性能和抗热震性能提高。
5 结束语电子束重熔处理后,硅化物涂层表面陶瓷晶粒粒度降低,表面粗糙度降低,组织结构更加均匀,表面层孔隙率降低,表面组织更加致密。
电子束重熔对硅化物涂层的二次烧结使涂层表面陶瓷颗粒烧结作用增强,增强了涂层/基体之间的元素渗透,提高了涂层致密度、组织均匀性和涂层/基体的粘结强度。
硅化物重熔处理后,涂层/基体获得了更好的冶金结合,使涂层/基体变形协调性增强,涂层/基体的界面裂纹产生的倾向降低,涂层组织更加致密,裂纹萌生倾向减小,对裂纹扩展的阻碍作用进一步增强,涂层的高温抗氧化性能和抗热震性能提高。
参 考 文 献[1] 白新德,邱钦伦,甘东文,等.铌在空气中的氧化动力学及成膜机制的研究[J].清华大学学报,1998,38(6):71-73.[2] 王禹,陈旻,郜嘉平,等.T i Cr Si硅化物涂层结构及裂纹扩展[J].稀有金属材料与工程,2000,29(5):315-320.[3] 何俊,于斌,张涛,等.预置涂层电子束熔覆改性技术研究[J].航天制造技术,2008,25(6):1-5.[4] WEISENBU RG ER A,R IZZI G,SCRIV A N I A,et al.P ulsed electro n beam tr eatment of M Cr AlY bondcoats forEB PV D T BC systems par t1of2:coat ing pr oduction[J].Sur face&Coating s T echnolog y,2007,202: 704-708.[5] HI DEK I H AM AT A NI,Y A SU N OBU M I YA ZA K I.Optimization o f an electro n beam r emelting o f H V OFspray ed allo ys and carbides[J].Surface and Coating s T echnolog y,2002,154:176-181.[6] U T U D,BRA NDL W,M AR GIN EA N G,et al.M or pho log y and phase modificat ion of H V OF spr ayedM Cr A lY coating s r emelted by electro n beam ir radiation[J].Vacuum,2005,77:451-455.[7] 郭光耀,刘方军,韩瑞清.电子束扫描控制系统[J].焊接学报,2003,24(1):91-93.[8] 肖来荣,蔡志刚,宋成.M o(Si,A l)2高温抗氧化涂层的形貌与结构研究[J].兵器材料科学与工程,2006,29(3):50-53.[9] 肖来荣,蔡志刚,殷磊,等.料浆烧结法制备改性Si Cr F e高温抗氧化涂层的研究[J].稀有金属与硬质合金,2006,34(2):16-20.作者简介于 斌 1983年生,2008年获兰州理工大学材料学专业硕士学位,工程师,从事航天压力容器设计工作。