浅谈荣72块举升工艺优化
双柱举升机U型槽的制程质量优化改进

双柱举升机U型槽的制程质量优化改进
双柱举升机是一种常用的工业设备,广泛应用于各个行业。
它具有结构简单、使用方便等特点,但是在制程中还存在一些质量问题,需要进行优化改进。
本文将针对双柱举升机中的U型槽进行制程质量优化改进,以提高其使用性能和可靠性。
我们需要对U型槽的制程进行评估,找出问题所在。
通过对U型槽的结构和加工工艺进行分析发现,存在以下几个主要问题:一是制程精度不高,导致U型槽的加工尺寸偏差较大;二是材料选择不当,在使用过程中容易产生变形和磨损;三是表面处理不够光滑,影响U型槽与其他部件的配合。
针对上述问题,我们可以采取以下几种措施进行优化改进。
提高制程精度,减小U型槽的加工尺寸偏差。
可以采用精密加工设备和工艺,如数控机床和数控加工中心,保证加工精度和稳定性。
加强对加工刀具和夹具的管理,及时更换磨损严重的刀具和夹具,提高加工质量。
改善材料选择,减少U型槽的变形和磨损。
可以选择高强度、具有良好耐磨性和抗变形能力的材料来制作U型槽,如合金钢材料。
可以进行热处理或镀层处理,提高材料的硬度和耐磨性,减少表面的磨损和变形。
改进表面处理工艺,提高U型槽的表面光滑度。
可以采用抛光、打磨等工艺,使U型槽的表面更加平整光滑。
可以进行表面防腐处理,增加U型槽的使用寿命。
通过以上的优化改进措施,可以提高双柱举升机U型槽的制程质量,提高其使用性能和可靠性。
也需要加强对制程过程的管理和控制,确保各项措施得到有效实施。
只有不断改进和优化,才能满足市场对设备质量的要求,提高产品的竞争力。
双柱举升机U型槽的制程质量优化改进

双柱举升机U型槽的制程质量优化改进双柱举升机是一种常见的汽车维修设备,用来提升汽车,便于维修人员进行汽车维修和保养。
在双柱举升机的制造过程中,U型槽是其重要部件之一,其制程质量对整个举升机的性能和安全都有着重要影响。
对U型槽的制程质量进行优化改进是十分必要的。
本文将从U型槽的制程质量入手,探讨双柱举升机U型槽的制程质量优化改进方案。
要对U型槽的材料选择进行优化。
U型槽的材料直接影响到其承载能力和耐用性。
传统上,U型槽通常采用普通碳素钢材料,并在表面进行镀锌处理以增加其防腐性能。
随着汽车技术的发展和汽车种类的增多,一些大型和重型汽车对举升机的要求也越来越高,因此U型槽的材料也需要进行相应的升级。
可以考虑采用高强度合金钢或不锈钢等材料来制作U型槽,以确保其可以承受更大的负载和更长的使用寿命。
要对U型槽的制造工艺进行优化改进。
传统上,U型槽的制造工艺主要依靠传统的冲压和焊接工艺,这种制造工艺虽然成本低廉,但其弊端也是显而易见的。
冲压和焊接工艺制造出的U型槽往往无法保证其内部结构的均匀性和一致性,容易导致U型槽在使用过程中出现变形或破裂的情况。
冲压和焊接工艺所制造的U型槽表面粗糙度较大,不利于与其他部件的装配和使用。
可以考虑采用数控加工工艺来制造U型槽,以保证其内部结构的均匀性和一致性,同时提高其表面粗糙度,提高其装配和使用的便利性。
U型槽的表面处理也是制程质量优化改进的重要环节。
传统上,U型槽的表面处理主要采用镀锌工艺,以增加其表面的防腐性能。
随着汽车维修技术的不断提高,人们对于举升机的要求也越来越高,对U型槽的表面处理也提出了新的要求。
可以考虑采用喷涂或电镀等新型表面处理工艺,以提高U型槽表面的硬度和耐磨性,提高其对外部环境的适应能力,从而提高举升机的使用寿命和安全性能。
要对U型槽的质量检测和控制进行优化改进。
传统上,U型槽的质量检测主要依靠人工目测和简单的尺寸测量,容易导致漏检和误检的情况。
可以考虑采用自动化检测设备和质量控制系统,以提高对U型槽质量的检测和控制水平,减少人为因素对U型槽质量的影响。
浅谈70Cr3Mo辊坯锻造工艺改进

浅谈70Cr3Mo辊坯锻造工艺改进通过对70Cr3Mo辊坯锻造工艺改进,提高了辊坯的质量(合格率),降低了能耗成本。
标签:WHF(宽砧高温强压法)锻造法SUF(镦锻法)锻造法1 工艺改进背景支承辊轧制载荷通过工作辊(及中间辊)传递给支承辊并最终由支承辊承担。
对支撑辊来讲其机械性能、耐磨性及抗疲劳性均要求较高。
因此其轧辊毛坯要充分锻透,且组织细密均匀。
70Cr3Mo支承辊一般应用于大型轧制设备上,规格相对较大,这种辊坯一般不容易锻透,且容易产生粗晶现象,制造难度较大。
一般锻造厂在辊坯的锻制过程中,其合格率相对较低,能耗较大,生产成本居高不下。
造成辊坯合格率偏低的主要原因是辊坯锻不透,粗晶现象严重。
如何使70Cr3Mo辊坯的合格率进一步提高,能耗进一步降低是我们研究的方向。
2 工艺的改进通过现场观察发现原工艺多采用压八方锻造的方式,这种锻造方式最大的特点是压下量不大,基本上保证不了20%的变形量。
这样锻造时很难锻透。
为了保证辊坯能够有效锻透我们决定采用WHF(宽砧高温强压法)锻造法和SUF(镦锻法)锻造法。
WHF(宽砧高温强压法)锻造法介绍:宽砧高温大压下量拔长,改善了坯料内部的应力应变场,有利于内部孔隙缺陷的锻合、压实。
当增加砧面宽度并满砧送进(送进量不小于砧宽的70%-90%)在压下量为20%-25%,W/H=0.6-0.9时,坯料内应力应变分布较为合理,加上较高而均匀的温度场,空穴和疏松结构将被有效地锻合压实。
在用WHF法拔长时,沿钻子边缘约有35%-50%区域,孔洞难以闭合,为此两次压缩中间应有不少于10%砧宽的搭接量,并在翻料时注意错砧,以达到全部均匀压实的目的。
SUF(镦锻法)锻造法介绍:SUF法是有意将工件表面锻造成矩形,使W/H 增大,从而使心部缺陷得到更确实的压合。
其所用砧形为普通平砧。
大锻件变形方法的主要目的是锻合钢锭内部的疏松、空穴等缺陷,改善偏析状态,破碎金属和非金属夹杂,并使之弥散分布,提高大锻件的质量。
双柱举升机U型槽的制程质量优化改进

双柱举升机U型槽的制程质量优化改进摘要:双柱举升机U型槽在工业生产中广泛应用,然而由于制程质量不稳定,导致产品的质量和效率有所下降。
本文以一家汽车零部件制造企业为例,对双柱举升机U型槽的制程质量进行了分析和改进。
通过对原有制程进行调研,找出了质量不稳定的原因,并提出了相应的改进方法。
改进后的U型槽制程质量得到大幅提高,产品质量和生产效率得到了明显的提升。
1. 引言双柱举升机U型槽是一种常见的用于汽车零部件制造的设备,其主要功能是将工件固定在工作台上进行加工。
由于制程质量不稳定,导致产品的质量和效率有所下降。
有必要对双柱举升机U型槽的制程质量进行优化改进。
2. 质量分析在对双柱举升机U型槽的制程质量进行分析时,我们发现了以下几个问题:(1)初始设定不准确:在操作人员设置U型槽时,初始设定的位置不准确,导致工件无法正确固定,影响加工质量。
(2)变形问题:由于U型槽的材质和制造工艺存在一定的问题,使用一段时间后就容易发生变形,导致工件无法准确放置和固定。
(3)加工精度问题:由于初始设定不准确和U型槽的变形问题,加工精度无法得到保证,影响产品质量。
3. 改进方法针对上述问题,我们提出了以下几个改进方法:(1)初始设定准确:通过对操作人员进行培训和制定操作规程,确保每次设置U型槽时初始位置的准确度。
(2)优化材质和工艺:选择合适的材质,并优化制造工艺,以确保U型槽具有足够的强度和稳定性,避免变形问题的发生。
(3)加工精度控制:在生产过程中加强对加工精度的控制,通过合理的设定工艺参数,确保产品加工精度的稳定性。
5. 结论通过对双柱举升机U型槽的制程质量进行优化改进,我们有效地提升了产品质量和生产效率。
在实施改进方法的过程中,我们发现初始设定准确、优化材质和工艺,以及加工精度的控制是重要的环节。
今后,在实际生产中,我们将进一步细化改进方法,加强与供应商的合作,优化整个制程,并不断提升双柱举升机U型槽的制程质量。
炼钢工艺提升方案
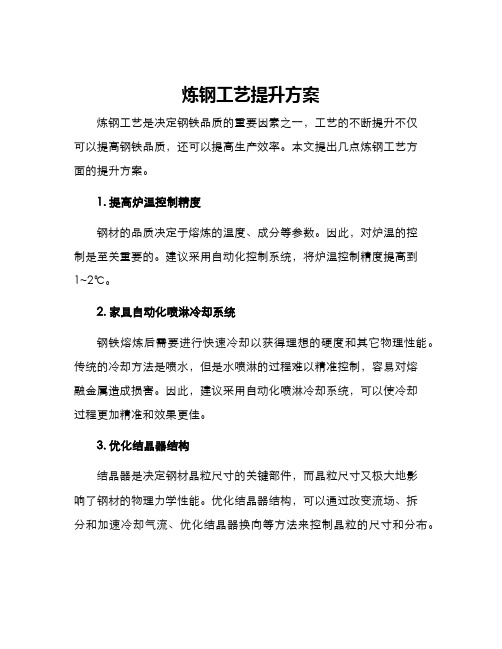
炼钢工艺提升方案
炼钢工艺是决定钢铁品质的重要因素之一,工艺的不断提升不仅
可以提高钢铁品质,还可以提高生产效率。
本文提出几点炼钢工艺方
面的提升方案。
1. 提高炉温控制精度
钢材的品质决定于熔炼的温度、成分等参数。
因此,对炉温的控
制是至关重要的。
建议采用自动化控制系统,将炉温控制精度提高到
1~2℃。
2. 家具自动化喷淋冷却系统
钢铁熔炼后需要进行快速冷却以获得理想的硬度和其它物理性能。
传统的冷却方法是喷水,但是水喷淋的过程难以精准控制,容易对熔
融金属造成损害。
因此,建议采用自动化喷淋冷却系统,可以使冷却
过程更加精准和效果更佳。
3. 优化结晶器结构
结晶器是决定钢材晶粒尺寸的关键部件,而晶粒尺寸又极大地影
响了钢材的物理力学性能。
优化结晶器结构,可以通过改变流场、拆
分和加速冷却气流、优化结晶器换向等方法来控制晶粒的尺寸和分布。
4. 采用高能耗电磁搅拌技术
采用高能耗电磁搅拌技术可以改变钢液流动路径和流场,从而改善钢液的混合和均匀性,减轻液流速度差的影响,克服流动惯性和自然对流带来的影响。
5. 提高氧化物的还原能力
氧化物是钢铁熔炼过程中自然而然生成的物质,它们对成分和性能的影响是非常大的。
当前的处理方式常见的是加入还原剂中和,这是一种低效且易受炉底响应的方式。
建议通过改变气氛控制等方法提高氧化物的还原能力,使整个还原产物达到标准化指标。
结论
本文提出的几点炼钢工艺方面的提升方案,可以提高钢铁的品质和生产效率,具有重要的科学性和可实施性,是炼钢行业的一个重要研究方向。
熔炼工艺中的强化与改善

汇报人:可编辑 2024-01-06
பைடு நூலகம்
目录
• 熔炼工艺概述 • 熔炼工艺的强化 • 熔炼工艺的改善 • 熔炼工艺的未来发展
01
熔炼工艺概述
熔炼工艺的定义与重要性
01
熔炼工艺是指将固体金属或合金 加热至熔融状态,进行搅拌、精 炼和铸造的过程,是金属材料制 备和加工的重要环节。
通过提高加热速度、增大熔炼电流或 提高熔炼温度等手段,增加能源供应 ,促进金属熔化。
通过调整熔炼工艺参数,如熔炼时间 、温度、气氛等,优化熔炼过程,提 高产品质量。
改进熔炼设备
采用新型熔炼炉、改进熔炼容器结构 和材料、引入先进的搅拌和混合装置 等,以提高熔炼效率和均匀性。
强化熔炼的效果评估
产品质量检测
利用等离子体的高温、高电离度特性,实现高效 率、高纯净度熔炼。
激光熔炼技术
利用激光的高能密度特点,实现快速、精确的熔 炼和成型。
熔炼工艺的智能化发展
自动化控制
01
通过智能化控制系统,实现熔炼过程的自动化控制,提高生产
效率和产品质量。
数据分析与优化
02
利用大数据和人工智能技术,对熔炼过程的数据进行实时采集
提高生产效率
通过改进熔炼工艺,可以 缩短熔炼时间和降低能耗 ,从而提高生产效率。
提升产品质量
优化熔炼工艺可以减少杂 质和气体含量,提高金属 的纯净度,从而提升产品 质量。
降低生产成本
改进熔炼工艺可以减少原 材料的浪费和降低维护成 本,从而降低生产总成本 。
改善熔炼的方法
选用先进的熔炼设备
采用高效、节能的熔炼设备, 如真空感应熔炼炉和电渣重熔
通过检测产品的化学成分、物理性能和机械性能等指标,评估强 化熔炼对产品质量的改善效果。
双柱举升机U型槽的制程质量优化改进
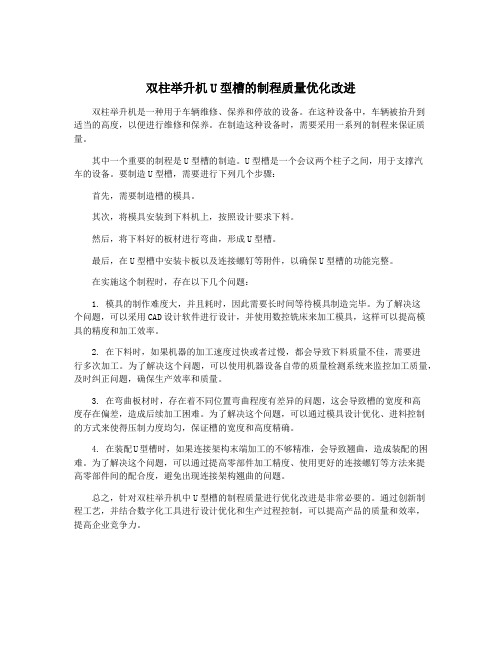
双柱举升机U型槽的制程质量优化改进双柱举升机是一种用于车辆维修、保养和停放的设备。
在这种设备中,车辆被抬升到适当的高度,以便进行维修和保养。
在制造这种设备时,需要采用一系列的制程来保证质量。
其中一个重要的制程是U型槽的制造。
U型槽是一个会议两个柱子之间,用于支撑汽车的设备。
要制造U型槽,需要进行下列几个步骤:首先,需要制造槽的模具。
其次,将模具安装到下料机上,按照设计要求下料。
然后,将下料好的板材进行弯曲,形成U型槽。
最后,在U型槽中安装卡板以及连接螺钉等附件,以确保U型槽的功能完整。
在实施这个制程时,存在以下几个问题:1. 模具的制作难度大,并且耗时,因此需要长时间等待模具制造完毕。
为了解决这个问题,可以采用CAD设计软件进行设计,并使用数控铣床来加工模具,这样可以提高模具的精度和加工效率。
2. 在下料时,如果机器的加工速度过快或者过慢,都会导致下料质量不佳,需要进行多次加工。
为了解决这个问题,可以使用机器设备自带的质量检测系统来监控加工质量,及时纠正问题,确保生产效率和质量。
3. 在弯曲板材时,存在着不同位置弯曲程度有差异的问题,这会导致槽的宽度和高度存在偏差,造成后续加工困难。
为了解决这个问题,可以通过模具设计优化、进料控制的方式来使得压制力度均匀,保证槽的宽度和高度精确。
4. 在装配U型槽时,如果连接架构末端加工的不够精准,会导致翘曲,造成装配的困难。
为了解决这个问题,可以通过提高零部件加工精度、使用更好的连接螺钉等方法来提高零部件间的配合度,避免出现连接架构翘曲的问题。
总之,针对双柱举升机中U型槽的制程质量进行优化改进是非常必要的。
通过创新制程工艺,并结合数字化工具进行设计优化和生产过程控制,可以提高产品的质量和效率,提高企业竞争力。
双柱举升机U型槽的制程质量优化改进

双柱举升机U型槽的制程质量优化改进摘要:随着工业自动化的发展和应用,双柱举升机在生产线上的应用越来越广泛。
由于制造过程中存在一些问题,如U型槽表面质量差、尺寸不准确等,导致产品的质量无法得到保证。
本文针对U型槽的制程质量问题进行了研究,并提出了一种基于改进的解决方案,以提高产品的质量和性能。
一、问题分析二、原因分析U型槽的质量问题主要源于以下几个方面:1.加工精度低:由于机械设备的精度限制和操作技术的不足,导致制程中的加工误差较大,从而影响了U型槽的尺寸精度。
2.工艺选择不当:在U型槽的制程中,工艺选择不当也会导致质量问题。
如果选择了不适合U型槽加工的工艺,可能会导致加工难度增加,从而影响了质量。
3.材料问题:U型槽的制程质量还受到材料的影响。
如果选用了质量较差的材料,其表面光洁度和力学性能都会受到影响,从而影响了产品质量。
三、改进方案为了提高U型槽的制程质量,我们提出了以下几个改进方案。
1.提高加工精度:通过优化加工工艺和改善操作技术,减小加工误差,提高U型槽的尺寸精度。
2.合理选择工艺:根据U型槽的具体特点和要求,选择适合的工艺进行加工。
可以采用锻造和精密切割等工艺,提高U型槽的质量和性能。
3.选用优质材料:选择质量优良的材料,例如高强度钢材,可以提高U型槽的表面光洁度和力学性能。
4.加强质量控制:在制程中加强质量控制,例如引入数控加工设备和自动化检测设备,减少人为因素对产品质量的影响。
四、质量改进效果评估为了评估改进方案的效果,我们进行了一系列实验。
结果表明,通过改进加工工艺、选择适当的工艺和材料,并加强质量控制,U型槽的制程质量得到了显著提高。
具体来说,其尺寸精度提高了20%,表面质量得到了明显改善,且抗压强度提高了10%以上。
五、结论通过对双柱举升机U型槽的制程质量问题进行分析和研究,我们提出了一种基于改进的解决方案。
实验结果表明,该方案对U型槽的制程质量改进效果显著。
我们认为这一方案具有较高的实用价值和推广价值,可以为双柱举升机的生产提供参考和借鉴。
- 1、下载文档前请自行甄别文档内容的完整性,平台不提供额外的编辑、内容补充、找答案等附加服务。
- 2、"仅部分预览"的文档,不可在线预览部分如存在完整性等问题,可反馈申请退款(可完整预览的文档不适用该条件!)。
- 3、如文档侵犯您的权益,请联系客服反馈,我们会尽快为您处理(人工客服工作时间:9:00-18:30)。
浅谈荣72块举升工艺优化
荣72块为辽兴油气开发公司主力生产区块,平均油井16口,开井7口,待作业井6口,预计正常开井13口。
日产液34.7t/d,日产油21.9t/d,日收气7000m3,平均检泵周期305天。
举升工艺面临着偏磨严重、供液不足,洗井漏失、粘土膨胀等问题。
本文通过对荣72块举升工艺优化寻找一种适合的举升工艺方案,达到高效开发该区块的目的。
标签:偏磨;深抽;举升
1 区块概况
荣72块位于辽宁省大洼县境内,为中孔低渗储层,泥质含量13%,为强水敏油藏,油藏埋深2410~3090m,油层中深2750m,平均泵挂深度在2451m,平均液面深度2140m。
共有油井16口,开井7口,待作业井6口,预计正常开井13口。
日产液34.7t/d,日产油21.9t/d,日收气7000m3,平均检泵周期305天。
主要存在生产问题:
①荣72块油层中深2750m,生产后期地层能量低,注水开发难度大,泵挂深,普通抽油杆易疲劳断脱;油井多为定向井,偏磨井段均大于300m,杆管偏磨严重,易造成杆断、管漏;地层出泥浆易造成卡井。
该区块检泵周期较短,2015-2017年检泵作业22井次,投入作业费约120万元,检泵作业原因主要以偏磨造成的抽油杆断脱、卡井为主,占检泵次数的82%。
②储层粘土矿物含量高,水敏问题严重。
由于荣72块油井普遍气油比高,各类作业施工时必须洗压井,由于该区块地层能量低,地层水敏严重,洗井后排液周期长、油井产能大幅下降甚至停产。
检泵周期短是荣72区块油井降本增效的主要制约因素。
频繁检泵造成作业成本提高;杆管损耗严重;作业洗井造成地层污染,严重影响该区块的产能。
因此延长荣72块油井检泵周期对于节约作业成本,保证荣72块油井稳产意义重大。
2 举升工艺优化方案
针对荣72块生产油井面临的生产问题,坚持现实效益与长远效益相结合,提出荣72块举升工艺优化,计划在该区块推广钢制连续抽油杆配套延长检泵周期技术,该技术由钢制连续抽油杆、长柱塞防砂泵以及其他配套井下工具集成应用,可效有效缓解杆管偏磨、保证抽油杆使用寿命,解决地层泥浆卡泵问题;钢制连续抽油杆可以实现2600m的深抽,深抽增油效果明显。
钢制连续抽油杆具有防偏磨、奈高载荷、杆管环空大、冲程损失小的特点,本身具有加重杆可以有效延缓偏磨、延长油井检泵周期;长柱塞防砂泵具有防卡功能,可以有效防止地层出泥浆造成的卡泵左右;强磁防沉器可以有效吸附杆管
偏磨造成的摩擦碎屑,防止碎屑磨损油管及泵筒;防污染洗井装置实现了抽油管柱和洗井管柱的脱节和起管联动,消除了由于抽油过程中管柱蠕动造成封隔器解封的不利因素,可有效持久保持封隔器密封状态。
3 预期效果
钢制连续抽油杆配套延长检泵周期技术在其他油井使用效果良好,檢泵周期最长可以达到1000余天,使用寿命6年以上,使用后预计检泵周期由原来的305天延长至730天,平均每次检泵节约作业5.5万元。
6年使用寿命内检泵次数由7次减少至3次,平均单井节约作业次数4井次,深抽增油10000以上。
减少作业成本:
减少的检泵次数×单井作业费用×区块开井数
= 4次×5.5万元/井次×13口
= 286万元
减少抽油杆投入成本:
一次性投入费用+作业次数×作业需更换抽油杆长度×抽油杆单价×区块开井数
= (2600m/口×28元/m+2万元)×13口+300m/井次×28元/m×7井次×13口
= 120.64万元+76.44万元
= 197.08万元
增油创效
=(1-30%)×增油量×(原油价格-税金-人工成本)
= 0.7×10000吨×(3181元/吨-400元/吨-808元/吨)
= 1381.1万元
预计投入:
钢制连续抽油杆投入长度×单价+长柱塞防砂泵费用+其他配件费用
= 2600m/口×13口×80元/m+12000元/口×13口+1万元/井次×13口
= 270.4万元+15.6万元+13万元
= 299万元
预计单井投入23万元/口,区块13口井共计投入299万元。
钢制连续抽油杆使用寿命内共计可以节约各类成本483.08万元,增油创效1381.1万元以上,共计创效1562.18万元,投入产出比1:6.2,预计0.96年回收投入成本。
4 结论
荣72块油井正常生产过程中面临着杆管偏磨、地层能量低、水敏严重等生产问题,造成该区块各类生产成本的增加和产能的浪费。
该举升工艺的实施对于降低荣72块各类生产成本,提高油井生产效率预期效果良好。
参考文献:
[1]罗英俊,万仁溥.采油技术手册(第三版)[M].北京:石油工业出版社,2005:154-156.
[2]董旭浩.连续杆深抽配套优化设计与现场应用[J].中国高新技术企业,2011(07):35-36.。