工艺优化管理方案
工厂管理中的工艺改进与优化方法
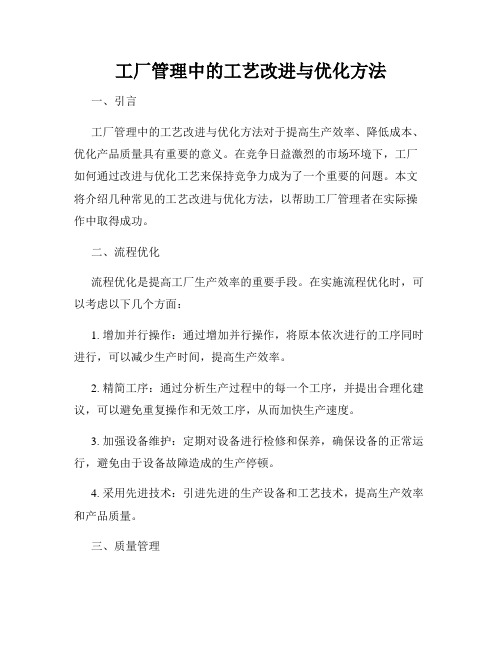
工厂管理中的工艺改进与优化方法一、引言工厂管理中的工艺改进与优化方法对于提高生产效率、降低成本、优化产品质量具有重要的意义。
在竞争日益激烈的市场环境下,工厂如何通过改进与优化工艺来保持竞争力成为了一个重要的问题。
本文将介绍几种常见的工艺改进与优化方法,以帮助工厂管理者在实际操作中取得成功。
二、流程优化流程优化是提高工厂生产效率的重要手段。
在实施流程优化时,可以考虑以下几个方面:1. 增加并行操作:通过增加并行操作,将原本依次进行的工序同时进行,可以减少生产时间,提高生产效率。
2. 精简工序:通过分析生产过程中的每一个工序,并提出合理化建议,可以避免重复操作和无效工序,从而加快生产速度。
3. 加强设备维护:定期对设备进行检修和保养,确保设备的正常运行,避免由于设备故障造成的生产停顿。
4. 采用先进技术:引进先进的生产设备和工艺技术,提高生产效率和产品质量。
三、质量管理优化工艺不仅可以提高生产效率,还可以提升产品质量。
以下是几种常见的质量管理方法:1. 严格的原材料检验:采购原材料时,要严格按照规定的标准进行检验,确保原材料的质量符合要求,避免影响产品质量。
2. 加强生产过程控制:通过实施全面质量管理、制定操作规程、加强现场检验等手段,确保生产过程的每一环节符合标准要求。
3. 引入先进的检测设备:购买先进的质量检测设备,提高检测精度和效率,及早发现问题并采取相应措施。
四、人员培训与管理工艺改进与优化需要得到相关人员的积极参与和支持,因此人员培训与管理也是至关重要的。
以下是几个参考建议:1. 提供培训机会:定期组织员工参加相关培训课程,提高其专业知识和技能水平,以适应工艺改进的需要。
2. 建立绩效评价体系:根据岗位职责和业绩目标,建立相应的绩效评价体系,激励员工积极参与工艺改进与优化工作。
3. 加强沟通与合作:建立一个良好的沟通机制,鼓励不同部门之间的合作,促进工厂内部各项工作的有效衔接与协调。
五、数据分析与优化数据分析是工艺改进与优化的重要手段之一。
生产部门工艺优化方案

生产部门工艺优化方案一、背景介绍在现代工业生产中,工艺优化是提高生产效率和产品质量的重要手段之一。
生产部门作为企业核心部门之一,其工艺优化方案对整个生产流程和产品质量具有重要影响。
本文将就生产部门工艺优化方案进行论述,旨在提供一套可行的解决方案,以提高生产效率和产品质量。
二、问题分析1. 工艺不合理导致生产效率低下:生产过程中存在工艺环节不合理,导致生产效率低下,如工序不合理、设备不充分利用等。
2. 工艺参数不精确:生产过程中常常出现工艺参数不精确的情况,导致产品质量波动,如温度、压力等参数的控制不准确。
3. 设备老化与技术更新:随着时间的推移,生产设备逐渐老化,无法满足当前的生产需求,同时新的技术也需要引入进来,以提升生产效率和产品质量。
4. 人员技能不足:员工的技能水平直接关系到生产效率和产品质量,存在技能不足的情况会直接影响工艺的优化和产品的质量。
三、解决方案为了解决上述问题,我们提出以下工艺优化方案:1. 工艺流程优化:通过分析生产流程,找出其中存在的瓶颈和不合理之处,并采取相应措施进行优化。
优化的目标是提高生产效率和产品质量,同时降低生产成本。
在工艺流程优化中,我们需要注意各个工序之间的衔接,确保生产过程的紧密连接,减少停机和改动时间,提高整体生产效率和产品质量。
2. 工艺参数精确控制:针对工艺参数不精确的问题,我们需要通过引入先进的自动化控制系统和传感器技术,实现工艺参数的精确控制。
通过对关键参数进行实时监测和调整,保证生产过程中参数的稳定性和准确性,进而提高产品质量的一致性和稳定性。
3. 设备更新与维护:针对设备老化和技术更新的问题,我们需要及时对设备进行更新和维护。
通过引入新的生产设备和技术,加强设备的维护,提高设备的稳定性和可靠性,进而提高生产效率和产品质量。
4. 培训与技能提升:为了解决人员技能不足的问题,我们需要进行员工培训和技能提升工作。
通过培训,提高员工的工艺操作技能和问题处理能力,使其能够顺利应对各种工艺优化和质量控制工作,进而提高生产效率和产品质量。
制造业工艺流程优化方案

制造业工艺流程优化方案一、现状分析首先,对现有的工艺流程进行全面、深入的分析是优化的基础。
这包括收集和整理生产过程中的各项数据,如生产周期、废品率、设备利用率、人工工时等。
通过对这些数据的分析,可以清晰地了解到当前工艺流程中存在的问题和瓶颈。
例如,某制造企业在生产过程中发现,某个生产环节的设备经常出现故障,导致生产停滞;或者某个工序的人工操作时间过长,影响了整体生产效率。
同时,还需要与一线工人、技术人员和管理人员进行充分的沟通和交流,了解他们在实际工作中遇到的困难和问题,以及对工艺流程改进的建议和想法。
二、目标设定在明确了现状和问题之后,需要设定明确的优化目标。
这些目标应该是具体、可衡量、可实现、相关联且有时限的(SMART 原则)。
例如,将生产效率提高 20%,废品率降低 10%,成本降低 15%等。
目标的设定要结合企业的实际情况和市场需求,既要具有挑战性,又要切实可行。
三、优化策略1、流程简化去除不必要的工序和操作,合并重复的环节,减少流程中的迂回和等待时间。
以汽车制造为例,原本复杂的组装流程经过简化后,减少了零部件的搬运次数和中间存储环节,大大提高了生产效率。
2、技术升级引入先进的生产技术和设备,如自动化生产线、数控机床、机器人等。
这些新技术可以提高生产的精度和速度,降低人工误差,同时还能减轻工人的劳动强度。
3、布局优化合理规划生产车间的布局,使物料的流动更加顺畅,减少运输距离和时间。
例如,将相关的设备和工序安排在相邻的位置,便于零部件的传递和加工。
4、人员培训提高员工的技能水平和工作效率,通过培训让他们熟悉新的工艺流程和操作方法。
同时,培养员工的质量意识和创新思维,鼓励他们提出改进建议。
5、供应链管理优化原材料的采购和供应流程,确保原材料的及时供应和质量稳定。
与供应商建立长期稳定的合作关系,共同优化供应链,降低采购成本。
四、实施步骤1、制定详细的实施计划明确每个优化措施的责任人和时间节点,确保各项工作有序推进。
纺织行业纺织公司生产工艺管理制度的优化方案
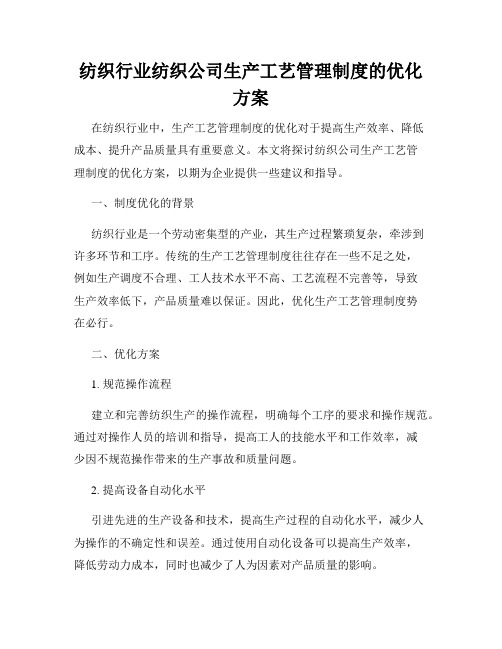
纺织行业纺织公司生产工艺管理制度的优化方案在纺织行业中,生产工艺管理制度的优化对于提高生产效率、降低成本、提升产品质量具有重要意义。
本文将探讨纺织公司生产工艺管理制度的优化方案,以期为企业提供一些建议和指导。
一、制度优化的背景纺织行业是一个劳动密集型的产业,其生产过程繁琐复杂,牵涉到许多环节和工序。
传统的生产工艺管理制度往往存在一些不足之处,例如生产调度不合理、工人技术水平不高、工艺流程不完善等,导致生产效率低下,产品质量难以保证。
因此,优化生产工艺管理制度势在必行。
二、优化方案1. 规范操作流程建立和完善纺织生产的操作流程,明确每个工序的要求和操作规范。
通过对操作人员的培训和指导,提高工人的技能水平和工作效率,减少因不规范操作带来的生产事故和质量问题。
2. 提高设备自动化水平引进先进的生产设备和技术,提高生产过程的自动化水平,减少人为操作的不确定性和误差。
通过使用自动化设备可以提高生产效率,降低劳动力成本,同时也减少了人为因素对产品质量的影响。
3. 实施质量管理体系建立和实施质量管理体系,通过设定和执行一系列的质量标准和流程,保证产品质量的稳定性和可追溯性。
加强对原材料的检测和筛选,保证原料的质量符合要求;同时在生产过程中加强质量检验和监控,避免次品和不合格品的产生。
4. 数据收集与分析建立数据收集和分析系统,实时监测生产过程中的关键参数和指标,对数据进行分析和统计,及时发现并调整不符合要求的环节和工序。
通过数据的分析和利用,及时发现生产过程中存在的问题,提高整体运营效率。
5. 制度培训与改进加强对生产工艺管理制度的培训和学习,让员工熟悉并理解制度的重要性和实施要求。
同时,建立改进机制,鼓励员工提出改进建议,不断完善和优化生产工艺管理制度,使其能够适应市场需求的变化。
三、优化方案的效果通过优化纺织公司生产工艺管理制度,可以实现以下几个方面的效果:1. 提高生产效率:规范操作流程、提高设备自动化水平,可以有效提高生产效率,减少生产过程中的浪费和耗时。
工艺优化方案
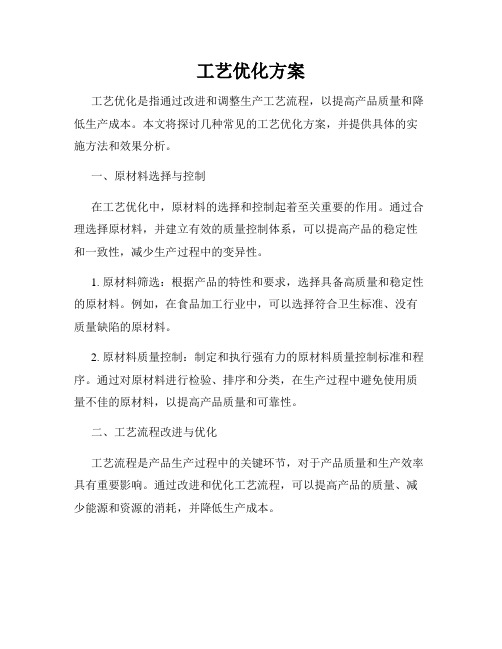
工艺优化方案工艺优化是指通过改进和调整生产工艺流程,以提高产品质量和降低生产成本。
本文将探讨几种常见的工艺优化方案,并提供具体的实施方法和效果分析。
一、原材料选择与控制在工艺优化中,原材料的选择和控制起着至关重要的作用。
通过合理选择原材料,并建立有效的质量控制体系,可以提高产品的稳定性和一致性,减少生产过程中的变异性。
1. 原材料筛选:根据产品的特性和要求,选择具备高质量和稳定性的原材料。
例如,在食品加工行业中,可以选择符合卫生标准、没有质量缺陷的原材料。
2. 原材料质量控制:制定和执行强有力的原材料质量控制标准和程序。
通过对原材料进行检验、排序和分类,在生产过程中避免使用质量不佳的原材料,以提高产品质量和可靠性。
二、工艺流程改进与优化工艺流程是产品生产过程中的关键环节,对于产品质量和生产效率具有重要影响。
通过改进和优化工艺流程,可以提高产品的质量、减少能源和资源的消耗,并降低生产成本。
1. 流程分析与优化:对生产流程进行全面分析,找出潜在的瓶颈和问题。
使用流程优化方法,如价值流图、精益生产等,优化工艺流程,消除浪费和不必要的环节。
2. 自动化技术应用:引入先进的自动化技术和设备,优化工艺流程,提高生产效率和产品质量。
例如,在制造业中,可以采用机器人技术、智能控制系统等,实现流程自动化和工艺参数的准确控制。
三、质量控制与监测质量控制与监测是工艺优化中的重要环节。
通过建立有效的质量控制和监测体系,可以及时发现工艺中的问题,采取措施进行调整和改进,确保产品质量的稳定和一致。
1. 质量检测与分析:建立全面的质量检测与分析体系,保证对产品的关键指标进行有效监测和控制。
通过合理选择检测方法和仪器设备,在生产过程中进行实时监测,及时发现并解决质量问题。
2. 过程参数监控:采用先进的信息技术手段,监控和控制生产过程中的关键工艺参数。
通过实时采集和分析数据,及时发现工艺偏差和异常,采取措施进行调整和纠正,以确保产品质量的稳定性和一致性。
工艺流程优化的方案范文(通用35篇)

工艺流程优化的方案范文(通用35篇)该工程总投Z为265万元,总占地面积为3600m2。
该废水处理站总装机功率为165KW,使用功率为102KW。
运行成本为元/t,其中人工费元/t、电费元/t、药剂费元/t,污泥外运费元/t。
一、前言营销环境,是指对企业的生存和发展产生影响的各种外布条件。
营销环境是企业营销管理过程中不可控制的因素,企业经营的优劣成败,在于营销管理者能否顺应不断变化的营销环境。
公司的市场营销环境是指在营销活动之外,能够影响营销布门发展并持续与目标顾客良好关系的潜力的各种因素和力量。
营销环境既能带给机遇,也可能造成威胁。
成功的公司务必持续不断地观察与适应变化着的环境。
1、市场环境分析我国的黄金销售量从1982年的吨增长到目前的大约140吨,从而使中国成为世界第三大黄金消费国,照此速度增长的话我国的黄金市场规模会发展得令人吃惊.据有关布门统计,世界上大约7,000人就拥有一家金店,而我国目前仅有8,000多家金店,即使仅以发达地区的2亿消费者计算,也才到达25,000人才有一家金店,在大城市仅有55%的居民拥有珠宝首饰,中小城市这一比例仅为23%,而东布的农村更少,仅到达17%.目前以及将来黄金礼品市场的增长动力主要来自婚庆需求,境外游客需求,还有赠品等.中国人由于受传统的影响,对黄金个性钟爱,除了购买项链,戒指,耳环,手链外,一些纯金小摆设比如磨砂或空心的生肖等饰物也颇受欢迎.但是欢迎的仍然是那些表面深度光处理过的首饰,内含建筑风和自由风格的抽象图样的款式仍旧受欢迎。
在销售上,黄金名店和连锁点形式站主要地位,一些大的商场等也设有专柜,―这些方式都是传统的行销,在e 化的当今时代似乎有点落伍。
随着中国的入世,黄金市场也逐步走向开放,这更是给黄金行业的发展带来了生机,另外人民银行也对黄金报价改为每周一次,使黄金价格更贴国际行情。
2、企业形象分析公司简介某金银公司是中国印钞造币总公司成都印钞公司与香港金银路有限公司合资成立的企业,亦是人民银行系统首家合资企业。
产品工艺优化建议与实施方案

产品工艺优化建议与实施方案产品工艺的优化是一个持续改进的过程,能够提高产品的质量、效率和竞争力。
本文将提供一些建议和实施方案,帮助优化产品工艺以提升生产效益。
一、提前进行工艺规划在产品开发的初期阶段,应该进行充分的工艺规划。
这包括确定所需的生产设备和工具,制定工艺流程以及设定产品质量标准。
通过提前规划,可以减少后期在工艺上所需的改动,提高生产效率。
二、加强工艺控制采取严格的工艺控制措施能够保证产品具有一致的质量和性能。
建议引入现代化的自动化设备和先进的技术,以提高工艺的可控性和准确性。
此外,制定和执行标准操作程序(SOP)也是确保产品工艺一致性的重要步骤。
三、优化生产线布局优化生产线布局可以有效地降低产品生产的时间和成本。
通过流程再造和物料流程分析,可以识别瓶颈或低效的环节,并进行相应的调整。
合理的生产线布局能够提高生产效率,减少资源浪费。
四、加强员工培训员工是产品工艺实施的关键环节,因此加强员工培训非常重要。
培训内容可以包括操作技能的提升、质量控制的重要性以及工艺变更的管理等。
通过培训,能够提高员工对于产品工艺的理解和执行能力,从而确保产品工艺的有效实施。
五、引入先进的质量管理工具现代化的质量管理工具能够提高产品工艺的可视化和自动化程度,进一步优化生产过程。
例如,六西格玛方法能够通过数据分析和问题解决,改进产品工艺并降低缺陷率。
流程控制图(SPC)则可以帮助监控和调整工艺参数,以确保产品质量的稳定性。
六、定期进行工艺评估和改进定期进行工艺评估和改进是产品工艺优化的关键步骤。
通过收集和分析数据,评估工艺的效果和可行性,并针对问题制定改进计划。
同时,与供应商和客户建立良好的合作关系,收集反馈信息并持续改进产品工艺。
实施产品工艺优化需要全面考虑产品的特点、市场需求和生产环境等因素。
通过采取上述建议和实施方案,可以提高产品工艺的效率和质量,降低生产成本,并增强企业的竞争力。
工艺优化方案

四、优化措施
1.优化生产流程:
a.梳理现有生产流程,找出瓶颈环节;
b.重新设计生产流程,简化操作步骤;
c.优化生产计划,提高生产效率。
2.设备升级改造:
a.更新设备,提高生产稳定性;
b.定期进行设备维护,降低故障率;
c.引入先进设备,提高生产效率。
-对现有生产流程进行详细分析,找出瓶颈环节;
-重新设计生产流程,减少不必要的工序;
-引入先进的生产计划管理系统,提高生产调度效率。
2.设备升级与维护
-对现有设备进行评估,淘汰性能不稳定、能耗高的设备;
-引进高效、节能的设备,提升生产效率;
-建立设备维护制度,定期进行保养和维修。
3.员工培训与发展
-制定员工培训计划,针对不同岗位进行技能培训;
4.管理体系不健全,导致生产过程监控不力;
5.环保措施不到位,不符合国家法规要求。
三、优化目标
1.优化生产流程,提高生产效率;
2.稳定设备性能,提升产品质量;
3.提高员工技能水平,增强团队协作能力;
4.建立健全管理体系,加强生产过程监控;
5.符合国家环保法规,实现绿色生产。
四、优化措施
1.生产流程优化
第2篇
工艺优化方案
率、降低成本、增强市场竞争力,同时遵循国家相关法规与标准,特制定本工艺优化方案。
二、现状分析
当前生产过程中存在以下问题:
1.生产流程不合理,导致生产效率低下;
2.设备性能不稳定,影响产品质量;
3.员工技能水平参差不齐,制约了生产效率的提升;
-开展内部选拔与竞聘,激励员工提升技能水平;
-建立员工职业发展通道,提高员工归属感。
- 1、下载文档前请自行甄别文档内容的完整性,平台不提供额外的编辑、内容补充、找答案等附加服务。
- 2、"仅部分预览"的文档,不可在线预览部分如存在完整性等问题,可反馈申请退款(可完整预览的文档不适用该条件!)。
- 3、如文档侵犯您的权益,请联系客服反馈,我们会尽快为您处理(人工客服工作时间:9:00-18:30)。
工艺管理方案
为了确保生产工艺稳定运行,各产品质量及过程控制符合规定要求,结合合成二车间生产实际情况,现将各岗位生产工艺做出以下几点要求:
一、合成岗位
1、加强对原材料质量抽查力度,并确保各种原材料投料比准确,严禁出现多投或少投甚至错投的现象;
2、各合成工每班必须对三乙胺计量槽进行排底,在操作记录上写清各种原材料实际投入量及各种原材料含量及水分;
3、对解聚、加成、缩合各阶段反应时间及保温时间做出明确要求,解聚在48--50℃间保温不得少于50分钟,加成在42--43℃间保温不得少于60分钟,缩合在52--53℃间保温不得少于70分钟,各阶段过程控制中严禁出现温度波动大及超温现象;
4、必须将合成液降至35℃以下才可以出料,打料前合成工要与脱醇小班长进行合成液打料交接并确认签字。
二、脱醇岗位
1、盐酸加入量必须准确,696/含量,严禁私自多加或少加;
2、加完盐酸至放合成液的时间不能超过1.5小时;
3、脱醇釜温度低于35℃时加合成液。
4、从加合成液起15分钟内必须关闭放料阀门。
5、合成液加完后温度需控制在50℃以下,约15分钟后排水升温。
6、升温时应遵循“先慢后快”的原则。
55-65℃,控制在45分钟左右,65-75℃、75-85℃各为1小时左右。
从升温-85℃,时间不得低于2.5小时,从升温 --停气出料,为6.5-7.5小时。
7、物料变黄后,保温30分钟。
8、出料时,温度最佳控制在119±2℃,最高不超过125℃。
并加入清洗水300L(含洗釜和洗管道的水)。
三、乙胺回收岗位
1、控制指标
母液中和PH值 10.50-10.80
三乙胺塔底温度 100℃~110℃
三乙胺塔顶温度 92.5℃~95.5℃
三乙胺水分≤0.20%
2、操作要求:中和温度控制在45--55℃,PH值在10.50—10.80之间,中和后的料液进入三乙胺分离器,分离时间不得少于15分钟;三乙胺精馏过程中严格控制进料量,保证塔底、塔底温度,确保排除的废母液中兑碱无三乙胺气味。
四、甲醇回收岗位
1、控制指标
老塔:甲缩醛塔底温度:77℃-80℃
甲缩醛塔顶温度:39℃-41℃
甲醇塔底温度:102℃-105℃
甲醇塔顶温度:63--65℃
新塔:甲缩醛塔底温度:80℃-88℃
甲缩醛塔顶温度:41℃-45℃
甲醇塔底温度:107℃-109℃
甲醇塔顶温度:67--69℃
中和PH值控制在7--9左右
2、操作要求
通过蒸汽、进料、回流、出料等手段,严格控制各项工艺指标在控制范围之内,COD控制在1500mg/L,PH值控制在8左右,发现异常立即上报,甲醇水分≤0.1%后可以出料,否则返料操作,甲缩醛水分水分≤0.45%、泡沫溶解性合格后可以出料,否则进行返料操作。
每周三对甲醇、甲缩醛取样做含量,确保回收过程中含量合格。
随时关注循环水及冷冻盐水的供给情况
五、结晶包装岗位
1、控制要求
加碱温度 50℃~70℃
水解液pH值 0.6~1.1 PH值高于0.3不用补碱
自来水控制 1.0方/批
2、操作要求
脱醇做好物料放入结晶釜后,待温度待温度降到50℃~70℃(放料后约1~1.5小时)时,加入适量的液碱,加碱量根据脱酸质量来确定,原则上每结晶釜加碱量控制在280-300升左右,控制指标以PH值0.8-1.1之间为,加碱时不能开真空,不能有三乙胺气味冒出现象,要求时缓慢滴加以求充分中和,将液碱计量。
降温结晶7小时、温度降至20℃~40℃后,将物料放入相对应的吸虑槽中,静止不少于15分钟后才可抽干母液,每批加水量控制在1方左右,静置30分钟左右抽干,包装前必须将头粉刮干净挖出。
合成二车间
二〇一二年三月二十三日。