学会切削用量选用一般方法
合理选择切削用量
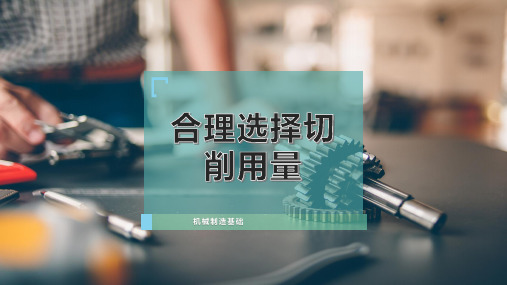
16
课堂实训——选择切削用量
机械制造基础
3)确定切削速度 vc 根据已知条件和已确定的 ap 和 f 值,由P139-140页表得切削速度 vc 130~160 m/min。由于该轴为
细长轴,应选取较小的切削速度,因此切削速度 vc 130 m/min。计算机床转速为
n 1 000vc 1 000 130 1 035 r/min πd 3.14 40
70~80
背吃刀量 ap/(mm)
2~6 进给量 f /(mm/r)
0.3~0.6
切削速度 vc /(m/min)
100~120 90~110 70~90 70~90 50~70 60~80 60~70
6~10
0.6~1
70~90 60~80 50~70 50~70 40~60 50~70 50~60
0.4~0.7 0.6~0.9
0.4~0.6
跳到 P144
5
二、进给量的选择
机械制造基础
续表
铸铁及 铜合金
16×25
20×30 25×25
40
0.4~0.5
60
0.6~0.8
0.5~0.8
0.4~0.6
100
0.8~1.2
0.7~1
0.6~0.8
0.5~0.7
400
1~1.4
1~1.2
0.8~1
0.6~0.8
寸为 46 mm×350 mm,加工尺寸为 39 mm×300 mm。在普通卧式车床CA6140上加工,使用焊接式硬
质合金YT15车刀,刀杆截面尺寸为16 mm×25 mm,刀具几何参数为
o 15,o 8,r 75, s 0,rε 1 mm,br1 0,
第七章 切削用量的选择

在选择合理切削用量时,必须考虑加工性质。 由于粗加工和精加工要完成的加工任务和追求的目 标不同,因而切削用量选择的基本原则也完全不同。
7.7.1
粗加工时切削用量选择的基本原则
粗加工时高生产效率是追求的基本目标。这个目 标常用单件机动时最少或单位时间切除金属体积最多 来表示。下面以外圆纵车为例加以说明(图7-1)。
3.确定切削速度vc 当刀具使用寿命T、背吃刀量ap与进给量f确定 后,即可按式(7.4)计算切削速度vc
(7.4) 式中 k vc——切削速度修正系数,与刀具材料和几 何参数、工件材料等有关。 Cv 、 xv 、yv 、m及K vc值见表7.3.加工其他工件 材料时的系数及指数可查切削用量手册。
由式(6.6)可知,在选择切削用量时:应首先 选择最大的ap,其次要在机床动力和刚度允许的前提 下,选用较大的f,最后再根据式(6.6)选择合理的 vc值。
当刀具使用寿命为一定值用高速钢车刀切钢时,切削用量之间有式(7.3) 关系
(7.3)
式(7.3)表明,为保证刀具合理使用寿命,
不参与优化。因此,切削用量的优化主要是指切削切 削速度vc与进给量f的优化组合。 以单件成本最低为目标的优化目标函数的建 立过程如下: 当ap一定时,由式(7.1)
式中 由式(6.5)得
式中
将tm 、T值代入式(6.14),得 式中
式( 7.9 )即为所建立的单件成本最低的目标函 数。求该函数的极值,得
合理切削用量的选择可按下列方法进行:
1.确定背吃刀量ap
ap一般根据性质与加工余量来确定。
切削加工一般分为粗加工、半精加工和精加工
粗加工时,在保留半精与精加工余量的前提下,若机 床刚度允许,加工余量应尽可能一次切掉,在中等功 率机床上采用硬质合金刀具车外圆时,粗车取ap=2 ~ 6mm,半精车去ap=0.2 ~ 3mm,精车取ap=0.1 ~ 0.3mm。
车削加工操作中切削用量的选择
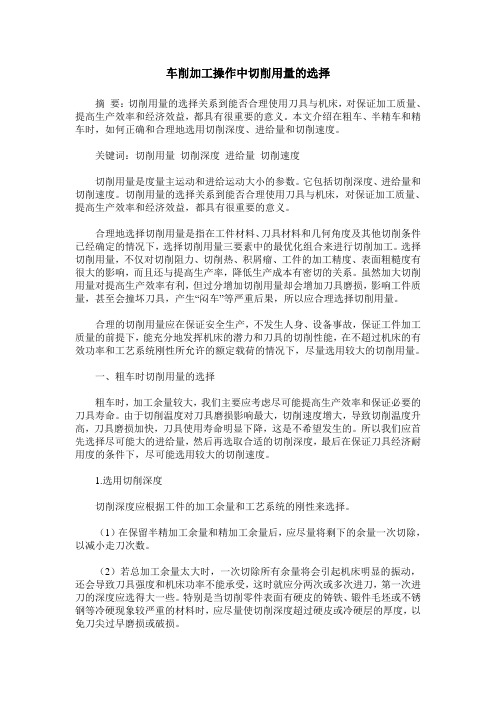
车削加工操作中切削用量的选择摘要:切削用量的选择关系到能否合理使用刀具与机床,对保证加工质量、提高生产效率和经济效益,都具有很重要的意义。
本文介绍在粗车、半精车和精车时,如何正确和合理地选用切削深度、进给量和切削速度。
关键词:切削用量切削深度进给量切削速度切削用量是度量主运动和进给运动大小的参数。
它包括切削深度、进给量和切削速度。
切削用量的选择关系到能否合理使用刀具与机床,对保证加工质量、提高生产效率和经济效益,都具有很重要的意义。
合理地选择切削用量是指在工件材料、刀具材料和几何角度及其他切削条件已经确定的情况下,选择切削用量三要素中的最优化组合来进行切削加工。
选择切削用量,不仅对切削阻力、切削热、积屑瘤、工件的加工精度、表面粗糙度有很大的影响,而且还与提高生产率,降低生产成本有密切的关系。
虽然加大切削用量对提高生产效率有利,但过分增加切削用量却会增加刀具磨损,影响工件质量,甚至会撞坏刀具,产生“闷车”等严重后果,所以应合理选择切削用量。
合理的切削用量应在保证安全生产,不发生人身、设备事故,保证工件加工质量的前提下,能充分地发挥机床的潜力和刀具的切削性能,在不超过机床的有效功率和工艺系统刚性所允许的额定载荷的情况下,尽量选用较大的切削用量。
一、粗车时切削用量的选择粗车时,加工余量较大,我们主要应考虑尽可能提高生产效率和保证必要的刀具寿命。
由于切削温度对刀具磨损影响最大,切削速度增大,导致切削温度升高,刀具磨损加快,刀具使用寿命明显下降,这是不希望发生的。
所以我们应首先选择尽可能大的进给量,然后再选取合适的切削深度,最后在保证刀具经济耐用度的条件下,尽可能选用较大的切削速度。
1.选用切削深度切削深度应根据工件的加工余量和工艺系统的刚性来选择。
(1)在保留半精加工余量和精加工余量后,应尽量将剩下的余量一次切除,以减小走刀次数。
(2)若总加工余量太大时,一次切除所有余量将会引起机床明显的振动,还会导致刀具强度和机床功率不能承受,这时就应分两次或多次进刀,第一次进刀的深度应选得大一些。
第二章第六节切削用量的选择方案

• 精加工多采用较高的切削速度,即可提高加工效率, 又要照顾到刀具使用寿命。
二、三要素的选定
1. ap的选定 • 一般根据加工性质与加工余量确定ap。切削加工一
般分为粗加工、半精加工和精加工。 (1)粗加工:考虑机床功率,系统刚度尽可能大
第六节 切削用量的选择
一、切削用量的选择原则
每次切削加工都必须选择切削速度、进给量和背吃刀量,这是 肯定的。
切削用量这三个要素与 生产效率、加工质量和加工成本都有非 常密切的关系。
我们在追求最高的生产效率、最好的加工质量和最低的加工成 本时如何选择切削用量三个要素呢?怎样选择才算合理呢? 下面让我们来分析一下切削用量三要素与生产效率、加工质 量和加工成本的关系。
• (2)工件材料强度、硬度高时,应选较低的vc。 • (3)切削合金钢比切削中碳钢切削速度降低20%~30%;切削
调质状态的钢比切削正火、退火状态钢要降低切削速度 20%~30%;切削有色金属比切削中碳钢的切削速度可提高 100%~300%。
• (4)刀具材料的切削性能愈好,切削速度也选得愈高,如硬质 合金钢的切削速度比高速钢刀具可高几倍,涂层刀具的切削 速度比未涂层刀具要高,陶瓷、金刚石和CBN刀具可采用更 高的切削速度。
f ↑ → 残留面积↑ Ra↑
v c → 通过积屑瘤来影响
2.切削用量与生产率 (1) 生产率
1 w
tw
tw
tm
tct
tm T
tot
tm ( ----- 机动时间)基本工艺时间 tct ----- (安装、调整、换刀)辅助工艺时间 tot ----- 其他辅助时间
切削用量及切削时间的确定

切削用量及切削时间的确定在机械加工过程中,切削用量和切削时间的确定是非常重要的。
合理的切削用量和切削时间可以提高加工效率、保证加工质量,并延长刀具的使用寿命。
本文将从切削用量和切削时间的概念、确定方法以及影响因素等方面进行探讨。
一、切削用量的概念和确定方法切削用量是指单位时间内切削刃具所切削的工件材料的量。
切削用量的大小直接影响着加工效率和刀具寿命。
切削用量的确定需要综合考虑工件材料的性质、刀具的材料和结构、机床的刚性以及切削液的冷却性能等因素。
确定切削用量的方法有以下几种:1. 经验法:根据以往的经验和实践,通过试切、试验等方式来确定切削用量。
这种方法简单直观,但需要经验丰富的操作人员。
2. 切削力法:通过测量切削过程中的切削力来确定切削用量。
一般情况下,切削力越大,切削用量也越大。
3. 切削功率法:通过测量切削过程中的切削功率来确定切削用量。
切削功率与切削用量呈正比关系,可以通过监测电机的功率来间接测量切削功率。
4. 数值模拟法:利用数值仿真软件对切削过程进行建模和模拟,通过模拟结果来确定切削用量。
这种方法可以较准确地预测切削过程中的切削力、切削温度等参数,从而确定合适的切削用量。
二、切削时间的概念和确定方法切削时间是指完成一道工序所需的时间,也可以理解为单位工件的加工时间。
切削时间的长短直接影响着加工效率和生产能力。
切削时间的确定需要考虑工件的尺寸和形状、切削速度、进给速度以及切削用量等因素。
确定切削时间的方法有以下几种:1. 经验法:根据以往的经验和实践,通过试切、试验等方式来确定切削时间。
这种方法简单直观,但需要经验丰富的操作人员。
2. 切削速度法:通过调整切削速度来控制切削时间。
一般情况下,切削速度越快,切削时间越短。
3. 进给速度法:通过调整进给速度来控制切削时间。
进给速度越大,切削时间越短。
4. 数值模拟法:利用数值仿真软件对切削过程进行建模和模拟,通过模拟结果来确定切削时间。
这种方法可以较准确地预测切削过程中的加工时间,从而确定合适的切削时间。
4.4切削用量的选择数控车削加工中的切削用量包括背吃刀量
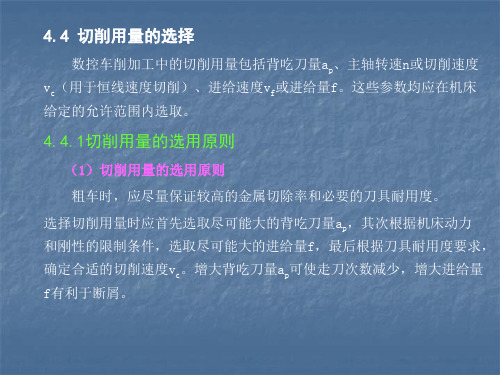
图4-24为车圆弧的阶梯走刀路线。
图4-25(a)为车圆弧的同心圆弧走刀路线。
图4-24 阶梯走刀路线车圆弧
图4-25
同心圆弧走刀路线车圆弧
图4-27为车圆弧的车锥法切削路线
即先车一个圆锥,再车圆弧。
图4-27 车锥法走刀路线车圆弧
(2)车圆锥的走刀路线分析
图4-26 车圆锥走刀路线
(3)车螺纹时轴向进给距离的分析
(4)按安装次数划分工序 以一次安装完成的那一部分工艺过程为一道工序。这种方法适
用于工件的加工内容不多的工件,加工完成后就能达到待检状态。
如图4-21所示工件,工序一:以毛坯的粗基准定位加工左端轮廓; 工序二:以加工好的外圆表面定位加工右端轮廓。
图4-21 轴类零件分析
4.5.3加工顺序的确定
在对零件图进行认真和仔细的分析后,制定加工方案应遵循以 下基本原则——先粗后精,先近后远,内外交叉,程序段最少,走
表4-4 常用切削用量推荐表
工件材料
加工内容
背吃刀量 ap/mm 5-7
切削速度 vc/m· min-1 60~80
进给量 f/mm· r-lσb>600MPa
粗加工
精加工 钻中心孔
2-3
2-6
80~120
120~150 500~800r· min-1
0.2~0.4
表4-3 硬质合金刀具切削用量推荐表
粗 加 工 刀具 材料 工件材料 切削速度 (m/min) 220 180 120 80 80 40 120 100 1600 进给量 (mm/r) 0.2 0.2 0.2 0.2 0.2 0.2 0.2 背吃刀量 mm 3 3 3 3 3 3 2 切削速度 (m/min) 260 220 220 160 140 · 140 120 精 加 工 进给量 (mm/r) 0.l 0.l 0.1 0.l 0.l 0.1 0.l 背吃刀量 mm 0.4 0.4 0.4 0.4 0.4 0.4 0.5 0.5 0.5
切削 用量的合理选择
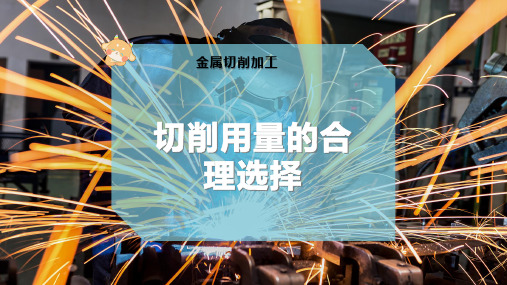
2)根据机床说明书,取机床实际进给量 =0.51mm/r。 3)检验机床进给机构允许的进给量。参考CA6140车床说 明书,查出机床进给机构允许的最大进给抗力为:FMfmax= 3528N。 计算切削时进给力为:
统、工件刚度以及精加工时表面粗糙度要求,确定进给量。
3)根据刀具寿命,确定切削速度。 4)所选定的切削用量应该是机床功率所允许的。
1.2切削用量的合理选择方法
1.背吃刀量的合理选择
背吃刀量一般是根据加工余量来确定。 粗加工(表面粗糙度Ra=50~12.5μm)时,尽可能一 次走刀即切除全部余量,在中等功率的机床上加工,取 ap=8~10mm;加工余量太大或余量不均匀、工艺系统刚性 不足或者断续切削时,可分几次走刀。 半精加工(Ra=6.3~3.2μm)时,取ap=0.5~2mm。 精加工(Ra=1.6~0.8μm)时,取ap=0.1~0.4mm。
1.5切削用量的优化概念
切削用量的优化是指在一定的预定目标及约束条件下, 选择最佳的切削用量。
在实际生产中,由于各种条件(加工零件、机床、刀 具、夹具等)都在变化,很难确定出一组最合理的切削用 量数值。
利用切削用量优化的方法,在确定加工条件下,综合 考虑各个因素,通过计算机辅助设计,能找出满足高效、 低成本、高利润和达到表面质量要求的一组最佳的切削用 量参数。实际切削用量的优化过程就是建立优化目标的数 学模型,用计算机求极值。主要目标函数有三个。
床功率是否允许。 在实际生产中,切削用量的合理选择,既可参照有关 手册的推荐数据,也可凭经验根据选择原则确定。
1.3车削用量的合理选择例题
切削用量的合理选择
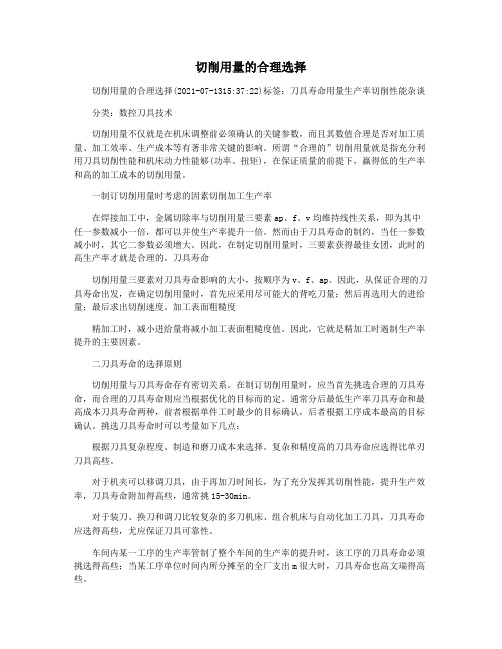
切削用量的合理选择切削用量的合理选择(2021-07-1315:37:22)标签:刀具寿命用量生产率切削性能杂谈分类:数控刀具技术切削用量不仅就是在机床调整前必须确认的关键参数,而且其数值合理是否对加工质量、加工效率、生产成本等有著非常关键的影响。
所谓“合理的”切削用量就是指充分利用刀具切削性能和机床动力性能够(功率、扭矩),在保证质量的前提下,赢得低的生产率和高的加工成本的切削用量。
一制订切削用量时考虑的因素切削加工生产率在焊接加工中,金属切除率与切削用量三要素ap、f、v均维持线性关系,即为其中任一参数减小一倍,都可以并使生产率提升一倍。
然而由于刀具寿命的制约,当任一参数减小时,其它二参数必须增大。
因此,在制定切削用量时,三要素获得最佳女团,此时的高生产率才就是合理的。
刀具寿命切削用量三要素对刀具寿命影响的大小,按顺序为v、f、ap。
因此,从保证合理的刀具寿命出发,在确定切削用量时,首先应采用尽可能大的背吃刀量;然后再选用大的进给量;最后求出切削速度。
加工表面粗糙度精加工时,减小进给量将减小加工表面粗糙度值。
因此,它就是精加工时遏制生产率提升的主要因素。
二刀具寿命的选择原则切削用量与刀具寿命存有密切关系。
在制订切削用量时,应当首先挑选合理的刀具寿命,而合理的刀具寿命则应当根据优化的目标而的定。
通常分后最低生产率刀具寿命和最高成本刀具寿命两种,前者根据单件工时最少的目标确认,后者根据工序成本最高的目标确认。
挑选刀具寿命时可以考量如下几点:根据刀具复杂程度、制造和磨刀成本来选择。
复杂和精度高的刀具寿命应选得比单刃刀具高些。
对于机夹可以移调刀具,由于再加刀时间长,为了充分发挥其切削性能,提升生产效率,刀具寿命附加得高些,通常挑15-30min。
对于装刀、换刀和调刀比较复杂的多刀机床、组合机床与自动化加工刀具,刀具寿命应选得高些,尤应保证刀具可靠性。
车间内某一工序的生产率管制了整个车间的生产率的提升时,该工序的刀具寿命必须挑选得高些;当某工序单位时间内所分摊至的全厂支出m很大时,刀具寿命也高文瑞得高些。
- 1、下载文档前请自行甄别文档内容的完整性,平台不提供额外的编辑、内容补充、找答案等附加服务。
- 2、"仅部分预览"的文档,不可在线预览部分如存在完整性等问题,可反馈申请退款(可完整预览的文档不适用该条件!)。
- 3、如文档侵犯您的权益,请联系客服反馈,我们会尽快为您处理(人工客服工作时间:9:00-18:30)。
任务3 学会切削用量选用一般方法1.3.1刀具切削用量的概念切削用量表示主运动及进给运动参数大小的数量,是切深、进给量和切削速度三要素的总称,用来描述切削加工运动量。
铣削加工的切深分背吃刀量和侧吃刀量。
1.切削深度(1)车削时的背吃刀量背吃刀量是在与主运动和进给运动方向相垂直的方向上测量的已加工表面与待加工表面之间的距离,单位为mm 。
如图1-3-1(a ),外圆车削时,其背吃刀量(a p )可由下式计算:2m w p d d a -= 式中 : d w w ——工件待加工表面直径,单位为mm ;d m ——工件已加工表面直径,单位为mm 。
(2)铣削吃刀量如图1-3-1(b )(c ),铣削加工的背吃刀量(a p )为平行于铣刀轴线测量的切削层尺寸,单位为㎜。
端铣时,背吃刀量为切削层深度;而圆周铣削时,为被加工表面的宽度。
侧吃刀量(a e )为垂直于铣刀轴线测量的切削层尺寸,单位为㎜。
端铣时,a e 为被加工表面宽度;而圆周铣削时,侧吃刀量为切削层深度。
(3)切削深度的选用切削深度的选取主要由加工余量和对表面质量的要求决定:(a)车削用量 (b)周铣切削用量 (C)端铣切削用量图1-3-1切削用量示意图余量不大,力求粗加工一次进给完成,但是在余量较大,或工艺系统刚性较差或机床动力不足时,可多次分层切削完成。
当工件表面粗糙度值要求不高时,粗加工,或分粗、半精加工两步加工;当工件表面粗糙度值要求较高,宜分粗、半精、精加工三步进行。
2.进给量(1)车削时的进给量如图1-3-1(a ),车削刀具在进给运动方向上相对于工件的位移量,可用刀具或工件每转(主运动为旋转运动时)的位移量来表达和测量,单位为mm /r(2)铣削时的进给量如图1-3-1(b )(c ),铣削加工的进给量f (㎜/r )是指刀具转一周,工件与刀具沿进给运动方向的相对位移量;对于多齿刀具(如钻头、铣刀),每转中每齿相对于工件在进给运动方向上的位移量称为每齿进给量f Z 。
,单位为mm /z 。
显然:f Z =zf (式中,z 为刀齿数) 进给速度F (㎜/min )是单位时间内工件与铣刀沿进给方向的相对位移量。
进给速度与进给量的关系为:z nf nf F z ==。
(n 为铣刀转速,单位r /min )(3) 进给量的选用进给量的选取主要依据工件材料的力学性能、刀具材料、工件表面粗糙度等因素。
工件材料强度和硬度越高,切削力越大,每齿进给量宜选得小些;刀具强度、韧性越高,可承受的切削力越大,每齿进给量可选得大一些;工件表面粗糙度要求越高,每齿进给量选小些;工艺系统刚性差,每齿进给量应取较小值。
3.切削速度如图1-3-1(a )(b )(c ),切削刃上选定点相对于工件的主运动的瞬时速度,单位为m /min 。
当主运动为旋转运动时,其计算公式为c v =1000n d π式中: d ——切削刃上选定点所对应的工件或刀具的直径,单位为mm 。
n ——主运动的转速,单位为r /min 。
选择切削速度时,不可忽视以下几点:①刀具材料硬度高,耐磨、耐热性好时,可取较高的切削速度。
②工件材料的切削加工性差时,如强度、硬度高、塑性太大或太小,切削速度应取低些。
③工艺系统(机床、夹具、工件、刀具)刚度较差时,应适当降低切削速度以防止振动。
④切削速度的选用应与切深、进给量的选择相适应,当切深、进给量增大时,刀刃负荷增加,使切削热增加,刀具磨损加快,从而限制了切削速度的提高;当切深、进给量均小时,可选择较高的切削速度。
⑤在机床功率较小的机床上,限制切削速度的因素也可能是机床功率。
在一般情况下,可以先按刀具耐用度来求出切削速度,然后再校验机床功率是否超载。
1.3.2 切削用量选择原则合理的切削用量应满足以下要求:在保证安全生产,不发生人身、设备事故,保证工件加工质量的前提下,能充分地发挥机床的潜力和刀具的切削性能,在不超过机床的有效功率和工艺系统刚性所允许的额定负荷的情况下,尽量选用较大的切削用量。
一般情况下我们对切削用量选择时应考虑到下列问题:1.保证加工质量:主要是保证加工表面的精度和表面粗糙度达到工件图样的要求。
2.保证切削用量的选择在工艺系统的能力范围内:要保证切削用量的选择在工艺系统的能力范围内,不应超过机床允许的动力和转矩的范围,不应超过工艺系统(铣床、刀具、工件)的刚度和强度范围,同时又能充分发挥它们的潜力。
3.保证刀具有合理的使用寿命:在追求较高的生产效率的同时,保证刀具有合理的使用寿命,并考虑较低的制造成本。
以上三条,要根据具体情况有所侧重。
一般在粗加工时,应尽可能地发挥刀具、机床的潜力和保证合理的刀具使用寿命。
精加工时,则应首先要保证切削加工精度和表面粗糙度,同时兼顾合理的刀具的使用寿命。
1.3.3 制订切削用量的一般方法在工件材料、刀具材料、刀具几何参数以及其他切削条件已确定的条件下,切削时切削用量选择得正确与否,将直接关系到工件的加工质量、生产效率和加工成本。
合理的切削用量应该是在充分发挥机床效能、刀具切削性能和保证加工质量的前提下,能够获得高的生产率和低的加工成本。
1.兼顾切削效率和刀具耐用度,注意切削用量选用顺序为了能够获得高的生产率和低的加工成本。
吃刀量、进给量、切削速度不仅不可随意确定,并且其选择顺序也不能颠倒。
切削用量三要素与生产率均保持正比关系,提高切削速度v c,增大进给量f和背吃刀量a p,都能“同等地”提高生产率。
但吃刀量、进给量、切削速度三者对刀具耐用度的影响差别甚大,切削速度的影响最大,进给量次之,吃刀量的影响最小。
因此,要在保证一定刀具耐用度的条件下,取得最高的生产效率,必须使吃刀量、进给量、切削速度三者乘积值最大才能达到。
选取切削用量的合理顺序应是:首先选取尽可能大的吃刀量;其次根据机床动力与刚性限制条件或加工表面粗糙度的要求,选择尽可能大的进给量;最后在保证刀具耐用度的前提下,选取尽可能大的切削速度,以达到吃刀量、进给量、切削速度三者乘积值最大,这一顺序不能颠倒。
2.兼顾加工质量和切削效率,分粗精加工选切削用量考虑各种条件的限制,分粗、精加工并选择合适的切削用量。
(1)粗加工切削用量选择粗加工切削时,可以优先考虑如何提高切削效率尽量选用较大的切削用量。
在工艺系统刚度、强度的允许下取最大的切削深度和进给量。
在不超过机床有效功率、保证一定刀具耐用度的前提下取最大的切削速度。
粗加工的切削深度选定以后,应进一步尽量选择较大的进给量,其合理数值应当保证机床、刀具不致因切削力太大而损坏;切削力所造成的工件挠度不致超出工件精度允许的数值;表面粗糙度参数值不致太大。
粗加工时,限制切深、进给量的因素主要是切削力,主要考虑切削力大小、工艺系统刚度,刀具因素等。
需要根据加工条件的薄弱环节,如,工艺系统刚度差或刀片强度小,选择适当切深、进给量。
当切深、进给量选定后,应当在此基础上再选最大的切削速度,切削速度主要受刀具耐用度的限制,增大切削速度可以有效地提高生产率。
但是,在正常的生产条件下,不允许用牺牲刀具耐用度的方法来增大切削速度。
(2)精加工切削用量选择精加工时则主要按表面粗糙度和加工精度确定切削用量。
选择合理的切削用量,可提高加工表面的质量和加工精度。
精加工的合理切削用量选择应注意以下几点:①进给量与表面质量要求相适应:进给量的大小影响加工表面残留面积的大小,因而,适当地减小进给量将使表面粗糙度Ra值减小。
②选择适当的切削速度;塑性材料切削时,一般切削速度在低速或高速切削时不会产生积屑瘤,加工后表面粗糙度值较小;在中等切削速度时,刀刃上易出现积屑瘤,它将使加工的表面粗糙度值增大。
用较高的切削速度,既可使生产率提高,又可使表面粗糙度值变小。
所以不断地创造条件以提高切削速度,一直是提高工艺水平的重要方向。
其中发展新刀具材料和采用先进刀具结构,常可使切削速度大为提高。
③选择适当的背吃刀量ap;一般地说,背吃刀量对加工表面粗糙度的影响并不明显。
但当ap小到一定数值以下时,由于刀刃不可能刃磨得绝对尖锐而具有一定的刃口半径,正常切削就不能维持,常出现挤压、打滑和周期性地切入加工表面的现象,从而使表面粗糙度值增大。
为减小加工表面粗糙度值,应根据刀具刃口刃磨的锋利情况选取相应的背吃刀量。
④减小工艺系统受力变形,提高尺寸加工精度;一般来说,工艺系统的刚度越好,工艺系统受力变形小,加工误差就越小,加工精度越高。
有时工艺系统在某些敏感方向上刚度不好,受力变形会引起工件的尺寸误差和形状误差。
生产实际中,应选择适当的工艺参数(如切削用量的切深、进给量等)使切削力引起的误差敏感方向上的变形在允许的误差范围内,以保证工件的加工精度。
但有时还应考虑检验工艺系统某薄弱环节的受力变形。
如:当刀杆刚度不足时,则应减少进给量。
3.借助经验表格的刀具切削参数选择数控加工的多样性、复杂性以及日益丰富的数控刀具,决定了选择刀具时不能再主要依靠经验。
借助经验表格对刀具切削参数进行选择是实践中常用的、有效的简便方法。
有关刀具切削参数选择的经验表格,其格式、内容多种多样。
有的是刀具制造厂在开发每一种刀具时,通过做了大量的试验,在向用户提供刀具的同时,提供了详细的刀具的使用说明和经验表格,针对性较强;有的经验表格则属于通用的技术资料,针对性一般。
编程者应对自己常用牌号的刀具,能够熟练地使用刀具厂商提供的技术手册,或通用的技术资料,通过经验表格选择合适的刀具,并根据手册提供的参数合理选择刀具的切削参数。
但不管多么详细的经验表格,它不可能完全吻合于具体的切削加工情况。
经验表格是选择刀具的切削参数的重要的依据,但不是完全的依据。
应知道:与切削用量的选用的相关因素是多种多样的,每一个相关因素都可能对切削用量的选用的合理性产生影响,因此在选择刀具的切削参数时,把经验表格为重要的依据,并具体分析切削加工的条件、要求、各种限制因素,全面考量,并在实践中验证、修改调整,才是得到具体应用的、合理的刀具切削参数的有效的途径。