3.6.4成型零件计算例题分析
成型零件的尺寸计算

2021年4月2日
§3.3.3 成型零件的尺寸计算
六、中心距与孔边距的计算
5.中心距尺寸计算(平均值法)
其中:
CM
(Cs
Cs
Scp
)
z 2
中心距制造公差δz=(1/3~1/6)Δ或查教材表3-5孔间距公差
6.凹模上的孔边距计算(平均值法)
此时凹模存在单边磨损,最大磨损量为δc/2。
2021年4月2日
§3.3.3 成型零件的尺寸计算
四、型腔和型芯径向尺寸计算
2.型芯径向尺寸计算
标注公差后得:
lM
(ls
lsScp
3 4
)0-z
※式中Δ前的系数可取在1/2~3/4之间
※有脱模斜度时径向尺寸确定
当脱模斜度不包括在塑件公差范围内时:
塑件上外形以大端为准,斜度取向小端; 模具型腔以大端为准,斜度取向小端。 只检验大端尺寸:LM=[Ls+LsScp–(3/4)Δ]+δz 塑件上的孔以小端为准,斜度取向大端; 模具型芯以小端为准,斜度取向大端。 只检验小端尺寸第:1l1M页=[/共ls3+4l页sScp +(3/4)Δ]-δz
⑵公制普通螺纹型芯工作尺寸计算 螺纹型芯中径尺寸 d2M-δz=(D2s+D2sScp+b)-δz 螺纹型芯大径尺寸 dM-δz=(Ds+DsScp+b)-δz 螺纹型芯小径尺寸 d1M-δz=(D1s+D1sScp+b)-δz
第17页/共34页
2021年4月2日
§3.3.3 成型零件的尺寸计算
六、中心距与孔边距的计算
第12页/共34页
2021年4月2日
§3.3.3 成型零件的尺寸计算
注塑模设计案例

2024年10月10日
三、注射模旳构造设计
3.浇注系统旳设计
⑶浇口设计 浇口形式旳选择
因为该塑件外观质量要求较高,浇口旳位置和大小应以不 影响塑件旳外观质量为前提。同步,也应尽量使模具构造 更简朴。
潜伏式浇口 浇口位置在塑件内表面,不影响其外 观质量。 但采用这种浇口形式增长了模具构造 旳复杂程度。
2024年10月10日
二、拟定成型设备选择与模塑工艺规程编制
2.拟定成型工艺参数
⑴塑件模塑成型工艺参数旳拟定 查附表9得出工艺参数见下表,试模时可根据实际 情况作适当调整。
聚碳酸脂
预热和干燥 料筒温度t/0C
喷嘴温度t/0C
温度t/0C110~120 时间τ/h8~12 后段 210~240 中段 230~280 前段 240~285
⑵塑件型腔较大,有尺寸不等旳孔,如Ф12、4-Ф10、4Ф4.5、4-Ф5它们均符合最小孔径要求。
⑶在塑件内壁有4个高2.2,长11旳内凸台。所以,塑件不 易取出。需要考虑侧抽装置。
结论:综上所述,该塑件可采用注射成型加工。
2024年10月10日
二、拟定成型设备选择与模塑工艺规程编制
1.计算塑件旳体积和重量
查有关手册得PC旳收缩率为Q=0.5%~0.7%,故平 均收缩率为:Scp=(0.5+0.7)%/2=0.6%=0.006,根 据塑件尺寸公差要求,模具旳制造公差取Z=Δ/3。
已知条件:平均收缩率SCP =0.006mm;模具旳制 造公差取Z=Δ/3。
类 零件 别 图号
模具 零件 名称
塑件尺寸
计算公式
塑料模设计及制造实例
二、拟定模具构造方案
1.拟定型腔数量及布局形式 2.选择分型面 3.拟定浇注系统与排气系统 4.选择推出方式 5.拟定侧凹部分旳处理方式 6.模具加热与冷却方式 7.拟定成型零件旳构造形式
零件的变形及强度计算

二、轴向拉伸和压缩时的内力 零件受到外力作用时,由于内部各质点之间的相对位
置的变化,材料内部会产生一种附加内力,力图使各质点
恢复其原来位置。附加内力的大小随外力的增加而增加, 当附加内力增加到一定限度时,零件就会破坏。因此,在
研究零件承受载荷的能力时,需要讨论附加内力。后面的 讨论中所述的内力,都是指这种附加内力。
通过对低碳钢的
曲线分析可知,试样在拉伸过程
中经历了弹性变形(oab段)、塑性变形(bcde段)和断 裂(e点)三个阶段。 弹性变形阶段,试样的变形与应力始终呈线性关系。 应力σp称为比例极限。图中直线oa的斜率就是材料的弹性 模量E。 塑性变形阶段,试样产生的变形是不可恢复的永久变 形。该阶段又分屈服阶段(bc-塑性变形迅速增加)、强 化阶段(cd-材料恢复抵抗能力)和颈缩阶段(de-试样局 部出现颈缩)。应力σs称为屈服点,当零件实际应力达到 屈服点时,将会引起显著的塑性变形。应力σb称为抗拉强
强度校核
设计截面 确定许可载荷
例2-2某车间自制一台简易吊车(图a)。已知在铰接点B 处吊起重物最大为FP=20kN,杆AB与BC均用圆钢制作,且
dBC=20mm,材料的许用应力[σ]=58Mpa。试校核BC杆的
强度,并确定AB杆的直径dAB(不计杆自重)。
第二节 零件的剪切和挤压
一、剪切和挤压的概念 如图b所示,在外力FP的作用下,截面发生相对错动 的变形称为剪切变形。产生相对错动的截面m—m称为剪切
强度储备,为此用极限应力除以一个大于1的系数(安全 系数)所得商作为材料的许用应力[σ]。
对于塑性材料,当应力达到屈服点时,零件将发生显
著的塑性变形而失效。考虑到其拉压时的屈服点相同,故
拉、压许用应力同为 式中,nS是塑性材料的屈服安全系数。 对于脆性材料,在无明显塑性变形下即出现断裂而失 效(如铸铁)。考虑到其拉伸与压缩时的强度极限值一般 不同,故有
成型零部件尺寸及力学计算
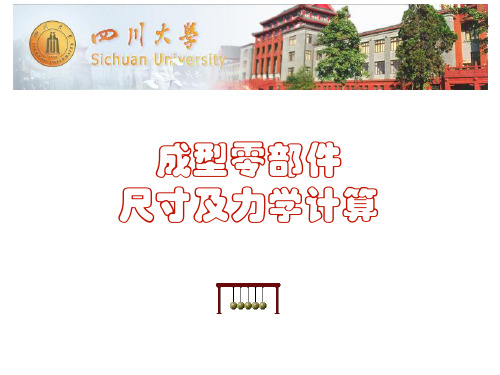
塑料成型模具成型零部件尺寸及力学计算塑料成型模具重点、难点•重点:•收缩的定义和重要性•计算型腔尺寸的方法•理解按极限尺寸计算和按平均收缩率计算的差别•模具常用的修模方法•难点:•按极限尺寸计算型腔尺寸的方法塑料成型模具塑料制品精度塑料原料收缩δS估算收缩率不准确δSS 模具零件制造误差δm 模具零件磨损δw 配合与安装误差δq影响因素制品公差Δ≥δS +δSS +δm +δw +δq因此,塑料制品的精度往往较低,应尽量选用低精度。
否则制品精度的提高会使模具的制造费用成指数幂增加。
制品公差标准GB/T14486-1993塑料成型模具成型零件制造误差在0~500mm 内。
、、、、,、IT 、IT 、IT 、IT IT a i m m D 。
D D a i a m m 160100644025 12111098,:: ,::)001.045.0(3其值分别对应常用精度系数公差单位型腔零件尺寸型腔零件制造公差δδ+=⋅=组合式型腔的制造公差要用尺寸链来决定制造误差约与成正比。
当制品尺寸较小时,型腔零件的制造误差约占制品公差的三分之一。
3D塑料成型模具塑料原料收缩理论收缩指的是在高温高压下注射入模腔中的塑料所成型出来的制品比模腔尺寸要小的现象。
常以mm/mm 或%来表示每种塑料的收缩或膨胀或压缩率可能不同原则1:塑料的压力、体积和温度之间有一种联系。
影响压力、温度和时间的因素都将影响收缩。
原则2:塑料受热时会膨胀,当冷却到原来的温度时又会收缩到原来的体积。
原则3:塑料受压时其体积会缩小,当压力恢复时又会膨胀到原来的体积。
塑料成型模具塑料制品收缩过程刚开始注塑时,压力小,但与模腔壁接触的塑料凝固后马上收缩模腔充满后,压力升高,塑料被压缩,但可补料以补偿收缩保持压力直到浇口冻结和阀式浇口关闭,补料停止继续收缩,压力持续下降,直至顶出,收缩还将继续重要因素:注射压力和浇口封闭时间塑料成型模具塑料原料收缩率影响收缩率的因素有:从理论上计算收缩率是不大可能的左边大部分是模具设计者或制造者控制不了的导致收缩率的波动•材料规格•加入回收塑料•加入填充剂•顶出时制品的温度•注射压力及保压压力•制品壁厚和流动阻力•制品形状•模具设计多数塑料在顶出后几小时会达到总收缩量的90%,其余的10%在10天内完成,少数塑料要几个月时间在高于室温下退火,可加速松驰,终止收缩,但吸湿塑料还会有尺寸变化m mL m m L 。
钣金冲压成型例题讲解I
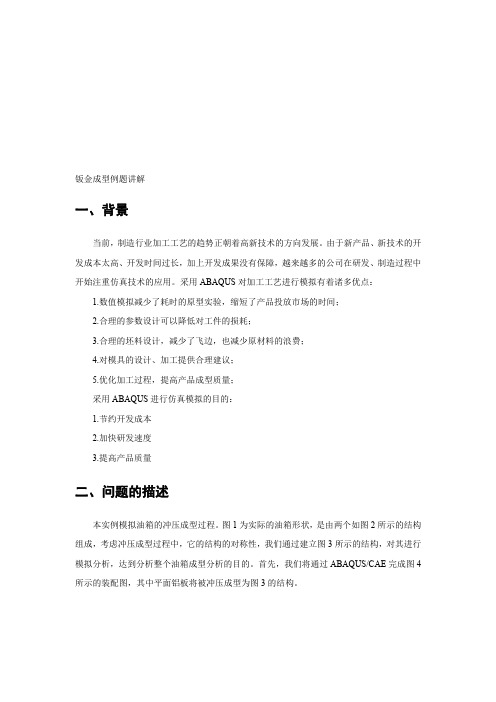
钣金成型例题讲解一、背景当前,制造行业加工工艺的趋势正朝着高新技术的方向发展。
由于新产品、新技术的开发成本太高、开发时间过长,加上开发成果没有保障,越来越多的公司在研发、制造过程中开始注重仿真技术的应用。
采用ABAQUS对加工工艺进行模拟有着诸多优点:1.数值模拟减少了耗时的原型实验,缩短了产品投放市场的时间;2.合理的参数设计可以降低对工件的损耗;3.合理的坯料设计,减少了飞边,也减少原材料的浪费;4.对模具的设计、加工提供合理建议;5.优化加工过程,提高产品成型质量;采用ABAQUS进行仿真模拟的目的:1.节约开发成本2.加快研发速度3.提高产品质量二、问题的描述本实例模拟油箱的冲压成型过程。
图1为实际的油箱形状,是由两个如图2所示的结构组成,考虑冲压成型过程中,它的结构的对称性,我们通过建立图3所示的结构,对其进行模拟分析,达到分析整个油箱成型分析的目的。
首先,我们将通过ABAQUS/CAE完成图4所示的装配图,其中平面铝板将被冲压成型为图3的结构。
三、建立模型3.1创建成型模具-阳模1、首先运行ABAQUS/CAE ,在出现的对话框内选择Create Model Database 。
2、在主菜单model 中命名新建模型为Forming example ,并保存文件为examle_forming.cae 。
3、从Module 列表中选择Part ,进入Part 模块。
4、选择Part→Create 来创建一个新的零件。
在提示区域会出现这样一个信息。
5、CAE 弹出一个如图5的对话框。
将这个零件命名为punch ,确认Modeling Space 、Type 和BaseFeature 的选项如下图。
输入300作为Approximate size 的值。
点击Continue 。
图 1图2成型模具-阳模金属板压边条成型模具-阴模图4图3图5ABAQUS/CAE 初始化草图,并显示格子。
6、在左侧工具条上点击 ,在提示栏中依次输入下表的坐标点,采用图标 连接1和2点、6和7点,采用 连接图中2、3、4点和4、5、6点。
《塑料模设计指导》电子教案 塑料模设计指导3
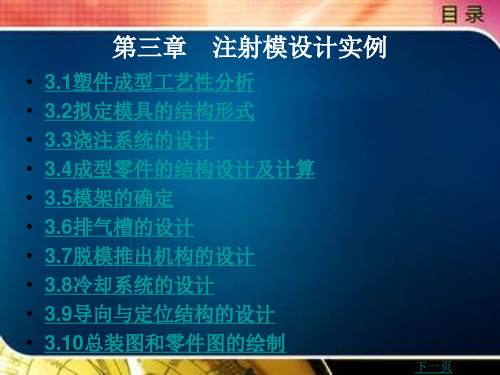
多型腔模具尽可能采用平衡式排列布置,且力求紧凑,并与浇口开设的 部位对称。由于该设计选择的是一模两腔,故采用直线对称排列,如图 3-3所示。
(3)模具结构形式的确定
从上面的分析可知,本模具设计为一模两腔,呈直线对称排列,根据塑 件结构形状,推出机构拟采用脱模板推出的推出形式。浇注系统设计时 ,流道采用对称平衡式,浇口采用侧浇口,且开设在分型面上。因此, 定模部分不需要单独开设分型面取出凝料,动模部分需要添加型芯固定 板、支撑板和脱模板。由以上综合分析可确定选用带脱模板的单分型面 注射模。
②吸湿性强。水的质量分数应小于0.3%,必须充分干燥,要求表面光 泽的塑件应要求长时间预热干燥。
③流动性中等。溢边料0. 04 mm左右。
④模具设计时要注意浇注系统,选择好进料口的位置、进料形式。当 推出力过大或机械加工时塑件表面易呈现白色痕迹。
(3) AIDS的主要性能指标
其性能指标见表3-2
上一页 下一页 返回
第三章 注射模设计实例
• 3.1塑件成型工艺性分析 • 3.2拟定模具的结构形式 • 3.3浇注系统的设计 • 3.4成型零件的结构设计及计算 • 3.5模架的确定 • 3.6排气槽的设计 • 3.7脱模推出机构的设计 • 3.8冷却系统的设计 • 3.9导向与定位结构的设计 • 3.10总装图和零件图的绘制
(1)外形尺寸 该塑件壁厚为3 mm塑件外形尺寸不大,塑料熔体流程不太长,适合 于注射成型,如图3-1所示。
(2)精度等级 每个尺寸的公差不一样,有的属于一般精度,有的属于高精度,就按 实际公差进行计算。
(3)脱模斜度 ABS属无定型塑料,成型收缩率较小,参考表3-1选择该塑件上型芯 和凹模的统一模斜度为1°。
压弯成型工艺分析与计算

PPT文档演模板
2023/5/26
压弯成型工艺分析与计算
•第一章 板料压弯工作原理
•第一节、压弯曲概述 •第二节、 弯曲件的质量分析
•第二章、管子弯曲 •第一节、管子弯曲概述
•第二节、管材弯曲形式
•第三节、管子弯曲工艺分析 •第四节、管子弯曲产生的椭圆度分析 •第五节、管子最小弯曲圆角半径
•B、当弯曲角不是900时,其回弹角则用公式计算
PPT文档演模板
压弯成型工艺分析与计算
• 2)按纯塑性弯曲计算,凸模圆角半径及角度按下式计算。 • 当板料相对弯曲半径r/t>5 ~ 8时,凸模圆角半径和中心 角可按下式计算,在试模时再修正。
• 式中 r——工件的圆角半径(mm);
•
rp——凸模的圆角半径(mm);
PPT文档演模板
压弯成型工艺分析与计算
v 由于位于弯曲变形区最外侧和最内侧的材料所受的切向应力 最大,故其管壁的厚度变化也最大。因此,外侧管壁会过量 减薄。当变形程度过大时,最外侧管壁会产生裂纹,最内侧 管壁会出现失稳而起皱。同时,由于弯曲内、外侧管壁上切 向应力在法向的合力(外侧切向拉应力的合力N,向下,内侧 切向压应力的合力N2向上)的作用,使弯曲变形区的圆管横 截面在法向受压而产生畸变,即法向直径减小,横向直径增 大,从而成为近似椭圆形(见图2-2.23)。变形程度越大,则 畸变现象越严重。另外,由于从拉应力过渡到压应力的弹性 阶段的存在,卸载时外层纤维因弹性恢复而缩短,内层纤维 因弹性恢复而伸长,结果使工件弯曲的曲率和角度发生显著 变化,与模具的形状和设计要求的形状不一致,造成弯曲回 弹现象,降低了弯曲件的工艺精度。
•第六节、管子弯曲工艺方法 •第七节、弯曲回弹
3.6.4成型零件计算例题资料

LM=[50.32+50.32×0.006-(3/4)×0.64]+0.64/3=50+0.21
HM=[21.22+21.22×0.006-(2/3)×0.44]+0.44/3=21+0.15
⑷大型芯尺寸计算(45+0.36 18+0.2)
lM=[45+45×0.006+(3/4)×0.36]-0.36/3=45.5-0.12
二、成型零件的加工方法
3.常用加工方法
2023/10/14
§3.5成型零件的设计及制造案例分析
二、成型零件的加工方法
3.常用加工方法
2023/10/14
§3.5成型零件的设计及制造案例分析
二、成型零件的加工方法
3.常用加工方法 ⑷模具内工作型孔的加工
分类: 圆孔 (钻 .铣 .镗.磨) 非圆孔(钻 .铣 .锯.气割)
二、成型零件的加工方法
3.常用加工方法
通用机床加工
数控机床加工
特种加工
外工作型面的加工
内工作型孔的加工
2023/10/14
§3.5成型零件的设计及制造案例分析
二、成型零件的加工方法
3.常用加工方法 ⑴通用机床加工
粗加工与半精加工:铣,工具铣,车
精加工:钳工修正,研磨,抛光
特点:
主要靠工人的熟练技术,效率低,质量不易保证
只能加工导电材料、加工速度慢 有电极损耗、最小角部R有限制
2023/10/14
§3.5成型零件的设计及制造案例分析
三、型腔的加工
2.型腔电加工
型腔工具电极加工
电极设计 结构形式: 整体 镶拼 组合 电极尺寸 技术要求
2023/10/14
- 1、下载文档前请自行甄别文档内容的完整性,平台不提供额外的编辑、内容补充、找答案等附加服务。
- 2、"仅部分预览"的文档,不可在线预览部分如存在完整性等问题,可反馈申请退款(可完整预览的文档不适用该条件!)。
- 3、如文档侵犯您的权益,请联系客服反馈,我们会尽快为您处理(人工客服工作时间:9:00-18:30)。
2020年10月18日
§3.5成型零件的设计及制造案例分析
三、型腔的加工
2.型腔电加工
型腔工具电极加工
电极设计 结构形式: 整体 镶拼 组合 电极尺寸 技术要求
2020年10月18日
§3.5成型零件的设计及制造案例分析
三、型腔的加工
3.型腔磨削加工
⑷大型芯尺寸计算(45+0.36 18+0.2)
lM=[45+45×0.006+(3/4)×0.36]-0.36/3=45.5-0.12 hM=[18+18×0.006+(2/3)×0.2]-0.2/3 =18.2-0.07 ⑸小型芯尺寸计算(Φ7.86+0.28 hM) lM=[7.86+7.86×0.006+(3/4)×0.28]-0.28/3=8-0.09 ⑹中心距尺寸计算(30±0.14 )
2020年10月18日
§3.5成型零件的设计及制造案例分析
一、成型零件尺寸计算实例
零件图如下图所示
材料:ABS
试确定凹模径向尺寸与深度、型芯直径和高度、孔心距、 小型芯直径。
1.分析塑件尺寸公差
2020年10月18日
⑴确定塑件的收缩率查附录C,ABS的收缩率为0.4%~0.7%,取平均收缩率Scp=0.6。 ⑵确定塑件尺寸公差,对塑件尺寸进行合理标注。
外工作型面的分类:圆形 非圆形
圆形表面的加工 车削——热处理——磨削
非圆形表面的加工 铣削 刨削 压印锉修
常规工艺规程
下料–锻造–热处理-粗加工(六面)-粗磨(六面)-钳(划线)工作型面粗加工(单面留余量0.2)-钳修-工作型面精加工(留 研磨量)-螺孔、销孔加工-热处理-研磨、抛光
2020年10月18日
成形砂轮磨削
2020年10月18日
§3.5成型零件的设计及制造案例分析
三、型腔的加工
3.型腔磨削加工
光学曲线磨床成形磨削
2020年10月18日
§3.5成型零件的设计及制造案例分析
三、型腔的加工
3.型腔磨削加工
2020年10月18日
§3.5成型零件的设计及制造案例分析
三、型腔的加工
4.型腔加工案例 模具零件的加工中,最重要的是对型腔的加工,
型腔的形状不同所采用的加工方法也不相同。
CM=(30+30×0.006)=30.2±0.01(孔间距公差查表3-5)
一、成型零件尺寸计算实例
3.工作尺寸的标注
2020年10月18日
2020年10月18日
2020年10月18日
§3.5成型零件的设计及制造案例分析
二、成型零件的加工方法
1.成型零件的工作型面的形状 外工作型面:型芯和凸模 内工作型面:型腔和型孔
精加工:钳工修正,研磨,抛光
特点:
主要靠工人的熟练技术,效率低,质量不易保证
成本低,投资少,通用性好
2020年10月18日
§3.5成型零件的设计及制造案例分析
二、成型零件的加工方法
3.常用加工方法 ⑵数控机床加工
粗加工与半精加工:数控铣、加工中心 热处理后的精加工:高精度成型磨床、坐标磨床 检验:三坐标测量机 特点:
主要精加工方法: 锉修加工 坐标磨床磨削
2020年10月18日
§3.5成型零件的设计及制造案例分析
二、成型零件的加工方法
3.常用加工方法 ⑷模具内工作型孔的加工
2020年10月18日
§3.5成型零件的设计及制造案例分析
二、成型零件的加工方法
3.常用加工方法 ⑷模具内工作型孔的加工
2020年10月18日
§3.5成型零件的设计及制造案例分析
三、型腔的加工
型腔的分类: 旋转体 非旋转体
加工方法: ⑴车削加工: 旋转体 ⑵铣削加工: 非旋转体 ⑶电加工: 旋转体、非旋转体 ⑷磨削加工: 旋转体、非旋转体
2020年10月18日
§3.5成型零件的设计及制造案例分析
三、型腔的加工
1.型腔铣削加工
立铣加工: 利用不同形状和尺寸的指状铣刀按照划线尺寸进 行加工。
2020年10月18日
§3.5成型零件的设计及制造案例分析
三、型腔的加工
1.型腔铣削加工
仿形铣
数控铣
2020年10月18日
§3.5成型零件的设计及制造案例分析
三、型腔的加工
2.型腔电加工
电火花加工的基本原理 基于工具与工件(正.负极)之间的脉冲放电的电腐蚀现象来蚀
除多余金属。
条件:放电间隙 脉冲电源(瞬时放电) 液体介质 电火花加工的特点及适用范围 ⑴难切削材料 ⑵形状复杂的工件 ⑶易加工过程自动化 局限:
2.模具制造的一般程序
2020年10月18日
§3.5成型零件的设计及制造案例分析
二、成型零件的加工方法
3.常用加工方法
通用机床加工
数控机床加工
特种加工
外工作型面的加工
内工作型孔的加工
2020年10月18日
§3.5成型零件的设计及制造案例分析
二、成型零件的加工方法
3.常用加工方法 ⑴通用机床加工
粗加工与半精加工:铣,工具铣,车
对熟练工人的依赖少,效率高,质量好,可加 工形状复杂的型腔.
一次性投资大
2020年10月18日
§3.5成型零件的设计及制造案例分析
二、成型零件的加工方法
3.常用加工方法 ⑶特种加工
电火花、电解、挤压、精密铸造等
2020年10月18日
§3.5成型零件的设计及制造案例分析
二、成型零件的加工方法
3.常用加工方法 ⑶模具外工作型面的加工
30±0.14、Φ45+0.36、18+0.2均为MT3级,对ABS而言属一般精度; Φ50±0.32、Φ8±0.14、21±0.22属MT5级。
故模塑容易达到塑件的尺寸精度要求,取:δz=Δ/4。
2020年10月18日
2.成型零件的尺寸计算
2020年10月18日
⑶型腔尺寸计算(Φ50.32-0.64 21.22-0.44) LM=[50.32+50.32×0.006-(3/4)×0.64]+0.64/3=50+0.21 HM=[21.22+21.22×0.006-(2/3)×0.44]+0.44/3=21+0.15
§3.5成型零件的设计及制造案例分析
二、成型零件的加工方法
3.常用加工方法
2020年10月18日
§3.5成型零件的设计及制造案例分析
二、成型零件的加工方法
3.常用加工方法
2020年10月18日
§3.5成型零件的设计及制造案例分析
二、成型零件的加工方法
3.常用加工方法 ⑷模具内工作型孔的加工
分类: 圆孔 (钻 .铣 .镗.磨) 非圆孔(钻 .铣 .锯.气割)