直接还原炼铁技术的最新发展doc
直接还原铁技术现状

冶金管理2006年第8期直接还原铁是铁矿在固态条件下直接还原为铁,可以用来作为冶炼优质钢、特殊钢的纯净原料,也可作为铸造、铁合金、粉末冶金等工艺的含铁原料。
这种工艺不用焦炭炼铁,原料也是使用冷压球团不用烧结矿,所以是一种优质、低耗、低污染的炼铁新工艺,也是全世界钢铁冶金的前沿技术之一。
直接还原炼铁工艺有气基法和煤基法两种,按主体设备可分为竖炉法、回转窑法、转底炉法、反应罐法、罐式炉法和流化床法等。
目前,世界上90%以上的直接还原铁是用气基法生产出来的。
但是天然气资源有限、价高,使生产量增长不快。
用煤作还原剂在技术上也已过关,可以用块矿、球团矿或粉矿作铁原料(如竖炉、流化床、转底炉和回转窑等)。
但是,因为要求原燃料条件高(矿石含铁品位要大于66%,含SiO2+Al2O3杂质要小于3%,煤中灰分要低等),规模小,设备寿命低,生产成本高和某些技术问题等原因,致使直接还原铁生产在全世界没有得到迅速发展。
因此,高炉炼铁生产工艺在较长时间内仍将占有主导地位。
一、直接还原铁的质量要求直接还原铁是电炉冶炼优质钢种的好原料,所以要求的质量高(包括化学成分和物理性能),且希望其产品质量均匀、稳定。
1.化学成分。
直接还原铁的含铁量应>90%,金属化率要>90%。
含SiO2每升高1%,要多加2%的石灰,渣量增加30kg/t,电炉多耗电18.5kWh。
所以,要求直接还原铁所用原料含铁品位要高:赤铁矿应>66.5%,磁铁矿>67.5%,脉石(SiO2+Al2O3)量<3%~5%。
直接还原铁的金属化率每提高1%,可以节约能耗8~10度电/t。
直接还原铁含C<0.3%,P<0.03%,S<0.03%,Pb、Sn、As、Sb、Bi等有害元素是微量。
2.物理性能。
回转窑、竖炉、旋转床等工艺生产的直接还原铁是以球团矿为原料,要求粒度在5~30mm。
隧道窑工艺生产的还原铁大多数是瓦片状或棒状,长度为250~380mm,堆密度在1.7~2.0t/m3。
炼钢工艺发展的趋势
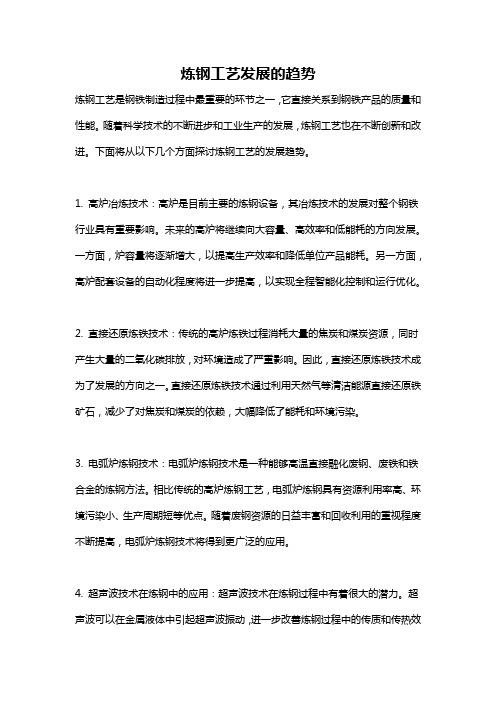
炼钢工艺发展的趋势炼钢工艺是钢铁制造过程中最重要的环节之一,它直接关系到钢铁产品的质量和性能。
随着科学技术的不断进步和工业生产的发展,炼钢工艺也在不断创新和改进。
下面将从以下几个方面探讨炼钢工艺的发展趋势。
1. 高炉冶炼技术:高炉是目前主要的炼钢设备,其冶炼技术的发展对整个钢铁行业具有重要影响。
未来的高炉将继续向大容量、高效率和低能耗的方向发展。
一方面,炉容量将逐渐增大,以提高生产效率和降低单位产品能耗。
另一方面,高炉配套设备的自动化程度将进一步提高,以实现全程智能化控制和运行优化。
2. 直接还原炼铁技术:传统的高炉炼铁过程消耗大量的焦炭和煤炭资源,同时产生大量的二氧化碳排放,对环境造成了严重影响。
因此,直接还原炼铁技术成为了发展的方向之一。
直接还原炼铁技术通过利用天然气等清洁能源直接还原铁矿石,减少了对焦炭和煤炭的依赖,大幅降低了能耗和环境污染。
3. 电弧炉炼钢技术:电弧炉炼钢技术是一种能够高温直接融化废钢、废铁和铁合金的炼钢方法。
相比传统的高炉炼钢工艺,电弧炉炼钢具有资源利用率高、环境污染小、生产周期短等优点。
随着废钢资源的日益丰富和回收利用的重视程度不断提高,电弧炉炼钢技术将得到更广泛的应用。
4. 超声波技术在炼钢中的应用:超声波技术在炼钢过程中有着很大的潜力。
超声波可以在金属液体中引起超声波振动,进一步改善炼钢过程中的传质和传热效果,提高钢的纯净度和均匀性。
此外,超声波还可以用于检测和监测钢铁产品中的缺陷和杂质,提高质量控制的准确性和效率。
5. 粉煤气化技术:粉煤气化技术是一种利用煤炭资源进行炼钢的新技术。
通过对煤炭进行气化,产生合成气,再利用合成气进行炼钢,既能够提高煤炭资源的利用率,又能够减少对传统能源的依赖和环境污染。
粉煤气化技术属于绿色环保型炼钢工艺,对于改善钢铁行业的能源结构和减少碳排放具有重要意义。
总体来说,炼钢工艺的发展趋势是朝着高效、环保、智能化和资源综合利用的方向发展。
气基竖炉直接还原低碳炼铁方案(一)
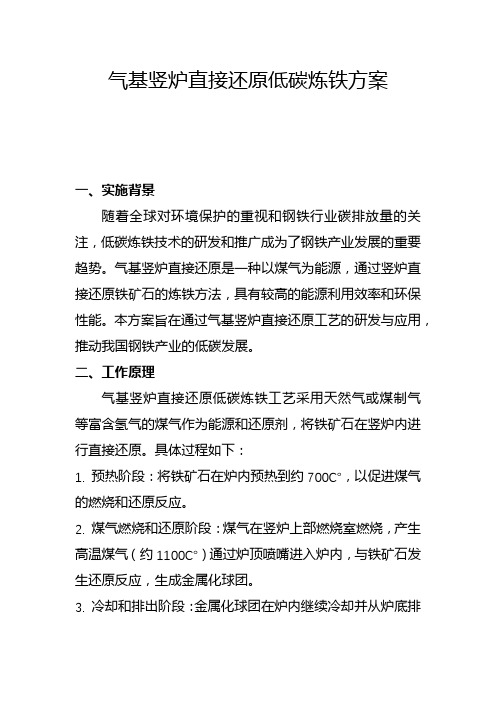
气基竖炉直接还原低碳炼铁方案一、实施背景随着全球对环境保护的重视和钢铁行业碳排放量的关注,低碳炼铁技术的研发和推广成为了钢铁产业发展的重要趋势。
气基竖炉直接还原是一种以煤气为能源,通过竖炉直接还原铁矿石的炼铁方法,具有较高的能源利用效率和环保性能。
本方案旨在通过气基竖炉直接还原工艺的研发与应用,推动我国钢铁产业的低碳发展。
二、工作原理气基竖炉直接还原低碳炼铁工艺采用天然气或煤制气等富含氢气的煤气作为能源和还原剂,将铁矿石在竖炉内进行直接还原。
具体过程如下:1. 预热阶段:将铁矿石在炉内预热到约700℃,以促进煤气的燃烧和还原反应。
2. 煤气燃烧和还原阶段:煤气在竖炉上部燃烧室燃烧,产生高温煤气(约1100℃)通过炉顶喷嘴进入炉内,与铁矿石发生还原反应,生成金属化球团。
3. 冷却和排出阶段:金属化球团在炉内继续冷却并从炉底排出。
4. 成品处理阶段:对金属化球团进行破碎、筛分、磁选等处理,得到最终产品。
三、实施计划步骤1. 研发与设计:开展气基竖炉直接还原工艺的基础研究和应用研究,设计适合我国钢铁产业的气基竖炉直接还原工艺流程和设备。
2. 设备制造与安装:根据设计要求,制造设备并在现场安装调试。
3. 工业试验:在制造和安装完成后,进行工业试验,验证工艺流程和设备的可行性和稳定性。
4. 生产调试:根据工业试验结果,对工艺流程和设备进行优化调整,逐步达到设计产能。
5. 技术服务与培训:提供相关技术服务和培训,确保企业能够自主运行和维护气基竖炉直接还原生产线。
四、适用范围本方案适用于大型钢铁企业和中小型民营钢铁企业。
特别是对于具有丰富铁矿资源和煤气资源的钢铁企业,气基竖炉直接还原低碳炼铁工艺具有较高的适用性和优势。
此外,对于地处环保要求较高地区或面临转型升级压力的钢铁企业,该工艺也具有较大的应用潜力。
五、创新要点1. 竖炉结构优化设计:通过对竖炉内部结构的优化设计,提高煤气与铁矿石的接触面积和热交换效率,降低能源消耗。
炼铁工艺的发展与创新从传统到现代

炼铁工艺的发展与创新从传统到现代炼铁工艺是铁矿石经过一系列工艺流程,将其转化为钢铁的过程。
随着科学技术的不断进步与发展,炼铁工艺也在不断创新和改进。
本文将从传统到现代的角度,探讨炼铁工艺的发展与创新。
一、传统炼铁工艺的演进传统炼铁工艺主要包括高炉法和直接还原法两种。
高炉法是将铁矿石、焦炭和石灰石等原料放入高炉中,在高温下进行还原反应,产生炼铁渣和铁水。
而直接还原法则是将铁矿石与还原剂(如氢气、甲烷等)直接反应,得到铁水。
然而,传统炼铁工艺存在一些问题。
首先,高炉法需要大量使用焦炭作为还原剂,导致能源消耗和环境污染问题。
其次,直接还原法虽然能够节约部分能源,但其还原效率较低,产出的铁水品质也不稳定。
二、基于传统的工艺改进为了解决传统炼铁工艺存在的问题,研究人员开始进行基于传统的工艺改进。
其中一个重要的改进是炼铁炉的结构优化。
通过改变炉膛形状、燃烧方式等,提高炼铁的效率和品质。
此外,还通过添加助熔剂、改变添加时间等方式,进一步优化炼铁工艺。
除了结构改进,工艺改进还包括了炼铁原料的优化选择。
研究人员通过对不同铁矿石的分析和试验,选择更优质的原料,以提高炼铁产品的品质。
同时,也研究了不同焦炭种类和添加量对炼铁过程的影响,为提高炼铁效率和环保性做出了贡献。
三、现代炼铁工艺的创新随着新材料和新技术的不断涌现,现代炼铁工艺得到了进一步的创新。
其中一个重要的创新是氧化还原反应的电磁过程控制技术。
通过在炼铁炉中加入电磁线圈,对炼铁过程中的温度、浓度等参数进行准确控制,提高炼铁效率和产品品质。
另外,为了降低能源消耗和环境污染,现代炼铁工艺还采用了先进的喷射燃烧技术。
该技术通过将高温燃烧产生的废气进行再循环利用,提高炼铁过程中的能量利用率。
同时,还采用了新型炉衬材料和高效能耗炉墙结构,减少了炼铁过程中的热损失。
除了这些技术创新,现代炼铁工艺还注重炼铁过程的数据采集与分析。
通过对炼铁过程中各个参数进行监测和分析,研究人员能够更好地控制和优化炼铁工艺。
直接还原铁生产工艺及发展方向

直接还原铁生产工艺及发展方向铁生产工艺的发展可以追溯到公元前2000年左右的古代。
在古代,人们首先发现了在高温条件下加热矿石可以从中提取金属。
这一过程被称为矿石冶炼,其中铜、铁和其他金属被广泛使用。
最早期的铁器使用原始的冶炼工艺,如陶瓷炉和炭火加热。
在这个时期,人们从矿石中提取铁质,并通过锻造和淬火方法制作器物。
然而,到了公元前8世纪左右,人们开始使用更高级的铁冶炼工艺。
最著名的是“低凤炉”、“高凤炉”和“方式炉”。
这些工艺的进步使得铁的生产成本大大降低,而且使得铁制品在农业、建筑和武器制造方面得到了广泛应用。
随着时间的推移,人们在铁生产工艺方面取得了更多的进步。
在18世纪,工业革命的到来带来了新的技术和设备,如高炉、转炉和开平法。
这些新技术大大提高了铁的生产效率,推动了工业化进程。
到了20世纪,铁生产工艺又迎来了一次革命。
高炉和转炉被更先进的炼铁技术所取代,如电炉和氧气顶吹转炉。
这些新技术不仅提高了生产效率,而且减少了对燃料和资源的需求。
此外,新的炼铁技术还使得对矿石种类的选择更加灵活,使得更多类型的矿石可以用于铁的生产。
在铁生产工艺的发展方向上,环保和可持续发展成为了主要的关注点。
随着环境污染和资源短缺的日益严重,铁生产已经朝着更环保和经济可行的方向发展。
一种主要的发展趋势是采用更加清洁的能源和生产方法。
例如,利用可再生能源和低碳技术来为铁生产提供能源。
此外,研究人员还在努力开发新的生产方法,如电解和高温合成气体反应,以减少对燃料的依赖和减少二氧化碳排放。
此外,优化生产效率也是一个重要的发展方向。
通过改进工艺流程、优化能源利用和降低废物产生,可以进一步提高生产效率并减少资源消耗。
金属回收和再利用也是铁生产工艺的另一个发展方向。
回收和再利用废旧金属可以减少对原始矿石的需求,降低对环境的影响。
综上所述,铁生产工艺经历了漫长的发展历程,并不断向更加环保、经济可行和高效率方向发展。
随着技术的不断更新和创新,铁生产工艺有望进一步完善,为社会的可持续发展做出更大的贡献。
直接还原炼铁的现状及发展趋势

气基还原 , 产 厂主要集 中在南 美、 东 、 生 中 东 南 亚 等地 区 , 委 内瑞 拉 、 如 墨西 哥 、 非 、 南 印度
维普资讯
攀 钢 技 术 似烧 结 的环冷 机 , 近 年才 开 发 的还 原设 备 。 是
2 12 燃 料 . .
・5 ・
Arx是 M irx 的 一 种 改 进 形 式 , 取 e de 它
目前 使 用 最 广 泛 的 是 天 然 气 , 用 天 然 使
消 了天 然 气 的 重 整 炉 , 天 然 气 部 分 氧 化 后 将 入炉 , 炉 内 热 海 绵 铁 催 化 裂 解 【 。HYL一 靠 3 J Ⅲ也 在 尝试 采 取 这 种 工 艺 , 消 重 整 炉 【J 取 4。
之一 。
生产 工 艺 主 要 集 中 在 竖 炉 气 基 还 原 的
Mirx HYLⅢ 、 de 、 HYLI三 种 工 艺 , 原 块 状 还
矿 石 , 图 2所 示 ; 如 回转 窑 S / R 工 艺 占有 L N
一
1 世 界 直 接 还 原 铁 生 产 简 况
定 比例 ; 外 , oe 另 C rx工 艺 近 年发 展 迅 速 。
世 界 直接 还 原 铁 产 量 增 长 迅 速 , 2 0 到 05 年 , 接 还 原 铁 产 量 将 达 到 70 0万 t1 】如 直 0 _l , 2
图 1所 示 。
。
年 份
’
0 o
o 0
图 2 直 接 还 原 炼 铁 工 艺 的种 类
一 。
图 1 世 界 直 接 还 原 铁 年 产 量
典 型 的 竖炉 还 原 工 艺 有 米 德 雷 克 斯 直 接 还 原公 司 ( 户 钢铁 公 司 子公 司 ) Mir ( 神—I ( 4 、 e l 图 ) Arx l
直接还原铁生产技术及现状

直接还原铁生产技术及现状铁生产技术的发展历史可以追溯到公元前2000年左右,最初的铁制品是通过在炭火中烧烤铁矿石来获得的。
这种烧烤技术被称为古老的冶金学,也被认为是人类历史上最早的冶金技术之一古代的铁生产技术在公元前1000年左右经历了重大的革新,这是由于铁矿石的高温还原反应被发现。
这种高温反应是通过将铁矿石与木炭或石炭混合,并在高温环境下加热来进行的。
这项技术的发现使得铁成为了当时最重要的金属之一,但其生产量仍然相对较小。
在一些古代文明中,如中国、印度等,铁的制造和使用逐渐扩大,为社会的农业、战争和工艺生产做出了重要贡献。
到了公元前300年左右,铁生产技术再次得到了改进。
在罗马时代,一种称为“减氧法”的技术被发明,这个技术将铁矿石与木炭放入特殊的炉子中,并且通过控制加热和供氧来获取较高纯度的铁。
这项技术极大地提高了铁的生产效率,使得罗马帝国在铁材料的生产和使用方面取得了巨大的进展。
这种技术的使用也标志着对铁生产的进一步工业化,奠定了现代铁产业的基础。
到了中世纪,铁生产技术进一步发展,很大程度上得益于对炼铁炉的改进。
这些改进包括提高炉子的结构、使用更多供氧装置以及改进燃烧气体的预热系统等。
这些改进使得炼铁过程更为高效,并且提高了产量和纯度。
到了18世纪,随着燃烧技术和冶金科学的进展,铁生产技术又迈上了一个新的台阶。
在这个时候,由于煤炭的大量使用,炼铁工艺发生了革命性的变化。
在这种现代炼铁法中,矿石和煤炭被放入高炉中,在高温环境下进行化学反应。
通过这个工艺,大量的铁矿石可以得到还原,得到高质量的生铁。
这种先进的炼铁法被广泛应用于欧洲的工业革命中,推动了工业化的进程。
随着时间的推移,各种现代技术和创新被应用于铁的生产过程中,这些技术包括用电解法提纯铁、高炉法等。
现代大规模铁生产以高炉和电炉为主,这些炉子能够生成高品质的铁,用于制造各种铁制品。
此外,利用再生铁和废钢再生技术也成为现代铁产业的重要组成部分,以提高资源利用效率和减少环境影响。
-=-周渝生 中国直接还原铁技术发展及市场供需分析 (终稿)
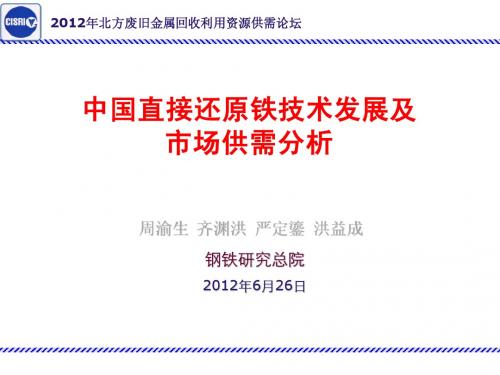
天然气
非焦煤 煤/天然气 天然气 煤/天然气 焦炭/煤粉 块煤/焦炭 煤 煤
竖炉
竖炉 转底炉 流化床 转底炉 高炉 预还原炉-熔 化气化炉 回转窑 隧道窑
10
12 12 13 15 16 16.5 20 25-30
190
190 14-40 150 14-30 400 120 15 1-4
TFe≥90% DRI
2012年北方废旧金属回收利用资源供需论坛
中国直接还原铁技术发展及 市场供需分析
周渝生 齐渊洪 严定鎏 洪益成 钢铁研究总院
2012年6月26日
内 容 提 要
1.中国近几年铁产量及直接还原铁的产量和比例 2.废钢比提高将推动我国直接还原的发展 中国目前DRI发展及 市场需求 3.低品质难选含铁原料用转底炉炼粒铁是煤基DRI的创新方向 4.气基竖炉直接还原工艺技术是我国直接还原的主要发展方向 5.加压煤制气工艺是我国发展直接还原新工艺的基础和条件
2.废钢比提高将推动我国直接还原的发展 中国目前DRI发展
及市场需求
煤基隧道窑本来是利用高品位铁精矿粉生产粉末冶 金原料的初级还原工序,尽管国家三令五申严禁建设, 但它迎合了资金少的短线投资者赌一把的心理,近几 年建成约400万吨产能,产量仅20-30万吨低品质的炼 钢用DRI。隧道窑单机产能小(最大仅2万吨/年),煤 耗高达1t/t DRI以上,生产周期长达48-70h,废弃的 还原罐、煤灰、烟尘造成的环境污染严重,隧道窑不 是我国直接还原技术的发展方向。
炉法的显著优点是单套设备产量大、能耗、排放最低
(见表1),是直接还原无焦炼铁技术的主流。表1的
数据表明,竖炉法直接还原炼铁生产技术是大型化、低
能耗、低CO2排放、产品质量优良的先进炼铁技术,应
- 1、下载文档前请自行甄别文档内容的完整性,平台不提供额外的编辑、内容补充、找答案等附加服务。
- 2、"仅部分预览"的文档,不可在线预览部分如存在完整性等问题,可反馈申请退款(可完整预览的文档不适用该条件!)。
- 3、如文档侵犯您的权益,请联系客服反馈,我们会尽快为您处理(人工客服工作时间:9:00-18:30)。
直接还原炼铁技术的最新发展作者: 胡俊鸽,吴美庆,毛艳丽, 钢铁研究摘要撰写人TsingHua出版日期:2006年4月30日直接还原铁可以作为电炉、高炉和转炉的炉料。
DRI代替优质废钢更适合于生产对氮和有害元素有严格要求的钢种,如用于石油套管、钢丝绳、电缆线等的钢种。
近年,由于钢铁市场升温,废钢资源呈现世界性紧缺。
2003年,我国钢铁企业生产回收的废钢铁和非生产回收废钢铁合计为1502万t;而全年炼钢消耗废钢与辅助炼钢消耗废钢之和为4 750万t。
显然,国内的废钢缺口很大。
未来几年,随着国际市场废钢资源的短缺,世界对废钢的需求量将不断增长。
当今,在废钢资源全球性紧缺、国际市场价格频频上扬的情况下,对于我国来说,寻找废钢替代品已迫在眉捷。
直接还原铁和热压块铁是最好的废钢替代品。
1直接还原炼铁技术发展状况2003年世界直接还原铁总量为4900万t。
比2002年增加了10%,不同工艺所生产直接还原铁所占份额如下:Midrex 为64.6%,HyLⅢ为18.4%,HyLⅠ为1.3%,Finmet为5.2%,其他气基为0.4%,煤基为10.2%。
直接还原工艺根据还原剂不同可分为气基和煤基。
气基直接还原工艺中,竖炉Midrex、Arex(Midrex改进型)和HyLⅢ工艺、反应罐法Hy LⅠ、流化床法Fior和Finmet工艺,都已获得了工业应用,流化床法Fior、Cir cored和碳化铁法在工业上应用不久就停产了。
煤基直接还原法中,获得工业应用的有回转窑法和转底炉法(Inmet-co、Fastmet、Sidcomet、DRylron),新开发的多层转底炉Primus工艺已于2003年2月投产。
1.1气基直接还原工艺气基还原工艺可分为使用球团矿或者块矿的工艺和使用铁矿粉的工艺。
各种气基直接还原铁工艺发展状况如表1所示。
表1各种气基直接还原铁工艺发展状况工艺装备工艺特点所用原料目前状况研究发展F ior(委内瑞拉)4个流化床反应器生产能耗高于竖炉Midrex和HyLⅢ铁矿粉Side tur厂于1976年投产,1985年开始,年产量达到35万t~41万t。
由于市场原因于2000年停产。
由委内瑞拉和奥钢联进一步发展成FinmetFinmet(奥钢联和委内瑞拉)4个流化床反应器铁矿靠重力从较高反应器流向较低反应器直接使用矿粉,是Fior 的进一步改进,比Fior能耗低、人员需求少。
与Fior相比,其还原气体中H2含量少,CO没被氧化去。
在Finmet工艺中,矿粉在流化床第一段被还原过程产生的热气体预热,其较高的CO含量可以提高热平衡,并使HBI的w(C)达3%。
铁矿粉:<12mm现已有两个厂投产澳大利亚的BoodarieIron和委内瑞拉的Orinoco Iron 目前已生产了650万tHBI目前,V AI正在开发新一代Finmet工艺:Finm etmegatrain,能力为110万t,是当前反应装置的2倍。
Midrex(美国米德兰公司)竖炉、天然气重整炉、热压块机竖炉炉顶气与天然气混合,共同进入重整炉制取还原气, 还原竖炉和制气设备是相互联系、相互影响的。
对铁矿含硫量有一定限制,否则含硫炉顶气进入重整炉将造成裂解催化剂失效。
含碳球团、块矿在世界各地获得非常广泛应用,直接还原铁产量在各种工艺中占第1位,2003年比例为66.6%。
已获得工业广泛应用,在墨西哥、印度尼西亚、委内瑞拉、巴西、印度有多家生产厂,2003年在各种直接还原法产量中,占第二位,产量比例为18.4%。
HyLⅢ(墨西哥希尔萨公司)竖炉、天然气重整炉、热压块机可分为两部分, 制气部分和还原部分,这两部分可以相互独立。
这点与Midrex不同。
另,温度和压力比Mi drex高。
可以处理含硫量较高的铁矿。
这也与Midrex不同。
含碳球团或者块矿HyL- ZR是HyL Ⅲ的进一步改进,没有重整装置。
该工艺目前只在墨西哥Monterrey得以实施。
Arex(委内瑞拉奥里诺科黑色冶金公司开发)竖炉是Midrex的改进型,无重整装置,竖炉集气体重整与矿石还原于一体球团矿或者块矿Megamod-Midrex直径为7.5 m的竖炉、较大的重整炉年产量超过200万t的Midrex工艺1.1.1使用球团矿或块矿的气基直接还原工艺使用球团矿或者块矿的有竖炉法Midrex、HyLⅢ、Arex和罐式炉HyLⅠ。
目前,Midrex和HyLⅢ是成熟的工艺,在委内瑞拉、印度、加拿大、美国、伊朗、沙特阿拉伯等已获得了广泛应用。
Midrex主要生产厂有33座。
1994年以来投产的生产厂逐步大型化,每套年产能大都在100万t左右。
如表2所示。
HyLⅢ是希尔萨公司在H yLⅠ基础上开发出的高压逆流式移动床工艺,20世纪80年代开始在工业上应用。
世界上主要生产厂有12座。
近年新投产的设备年产能都约为100万t。
如表3所示。
表21994年以来投产的Midrex生产厂生产厂年生产能力/万t产品投产年印度Ispat工业公司100DRI1994埃及ANSDKⅡ80DRI1997墨西哥IMEXSA120DRI1997美国AmericanIronReduction120DRI1997委内瑞拉COMSIGV A100HBI1998rinidad&Tobago,Ispat DR3136DRI1999南非撒旦哈(Saldanha)80.4DRI1999埃及ANSDKⅢ80DRI2000 HyL-ZR是新开发的无重整装置的直接还原工艺,目前为止该工艺只在墨西哥蒙特雷(Mont errey)得以实施。
其天然气在竖炉内发生部分燃烧,通过控制而产生合乎要求的还原气体,从而对铁矿石进行还原;而传统HyLⅢ工艺一般在添加蒸汽条件下使天然气在催化重整器中裂表31999年以来投产的HyLⅢ生产厂生产厂年生产能力/万t产品投产年墨西哥蒙特雷Hylsa 4M67.5DRI1998沙特阿拉伯HadeedⅢ110DRI1999俄罗斯LebedinskyGOK90HBI1999委内瑞拉DOSVEN150(两套设备)HBI2000解。
为了获得w(H2)达80%的还原气体,通过洗涤去除CO2。
Megamod厂的Midrex设备是大型的Midrex设备,如今直接还原铁年产量超过170万t,生产率超过220t/h。
直径为8m的竖炉年产直接还原铁能力270万t。
1.1.2气基粉矿直接还原工艺在直接还原生产中,采用细矿粉的直接入炉与块矿和球团矿相比其原料成本具有明显优势。
气基粉矿直接还原一般都采用化床工艺。
很长时间以来,获得商业应用的粉矿直接还原铁工艺只有Fior工艺(如表1所示)。
Finmet工艺是Fior工艺的进一步发展<1>,是基于粒度小于12mm的粉矿的气体直接还原工艺。
已经有两个工业厂投产,年设计产能都超过200万t热压块铁。
两个厂2003年共产163万tHBI。
1.1.3气基直接还原工艺工业生产结果表4中汇总了气基直接还原的一些工业生产数据<2>。
Midrext和HyLⅢ工艺的天然气消耗为9.7~10.7GJ/t,而Finm et为13.3GJ/t。
对这些工艺来说重要的是天然气的价格。
而Finmet工艺使用更便宜的粉矿,补偿了较高的天然气消耗。
表4气基直接还原工艺的操作结果矿石或球团矿/(kg·t-1)块矿/(kg·t-1)粉矿/(kg·t-1)天然气/(GJ·t-1)电功率/(kW·t-1)氧/(m3·t-1)产品Midrex1200 300-9.7 93.0 30DRI/HBIHyLⅢ1 181 295-10.7 98 34DRI/HBIFinmet--1 500 13.3 165-HBI1.2煤基直接还原在煤基直接还原工艺中,已获得工业应用的有回转窑和转底炉工艺。
表5表示主要煤基直接还原工艺的发展现状<3~6>。
转底炉由于反应速度快、原料适应性强等特点,近年来得到了快速发展。
转底炉工艺有许多种,包括Inmeto、Fastmet、Comet、Sidcomet、IDI(IronDynamics Inc)I、TMK3、DRyIron等。
表5主要煤基直接还原工艺的发展现状工艺装备工艺特点所用原料目前状况研究发展Primus(卢森堡PaulWurth)多层转底炉、熔融炉两段式工艺,除了转底炉外,还有熔融炉,能直接生产出铁水煤粉与矿粉在炉内混合,该工艺能把Z n、Pb、碱金属等与铁分开铁矿粉、煤粉铁屑、钢铁厂粉尘已完成工业试验目前卢森堡Diff erdange已投产8.2万t/a的装置,处理含铁废料。
直径8.3m,8层RedSme lt(德国和意大利)造球装置、转底炉装置和埋弧炉熔融还原装置这是三段工艺的直接还原,造球和转底炉装置相当于转底炉技术,埋弧炉可把热态DRI熔融成铁水和渣,产能大于30万t铁精矿粉,或者含铁废料制成的球团,专门为处理金属废料开发Ellwood厂于1978年投产年处理废料2.5万t的工厂。
SMSDemag目前正在开发RedSmeltNST工艺,即用氧/煤基熔融装置代替埋弧炉,降低成本。
DRyIron转底炉、干压块机、DRI冷却机无粘结剂的矿煤干压块、转底炉单层装料和温度控制在1288℃的高温辐射加热。
常规铁矿粉或者含铁废料、焦粉第一个DRyIron设备是新日铁在光厂建设以处理残渣的Fastmet(美国和神户合作开发)转底炉、球团装置使用冷固结球团, 取消了高温氧化球团环节。
反应速度快,生产效率高。
产品质量差,全铁含量低,脉石含量高,脱硫能力较差,所以产品硫含量过高。
粒度为8~12mm的自还原球团2000年新日铁在广畑厂投产了一条年产能达19万t的Fastmet工艺来处理残渣。
2000年以来,又在君津厂投产了两座转底炉,一座处理低锌灰尘,另一座处理高炉瓦斯灰和转炉尘。
其年处理循环料的能力均为18万t。
2001年又在神户的和歌山厂投产一年产能14万t的转底炉设备来处理富锌冶金炉尘。
Inmetco(美国开发)转底炉、造HYL工艺注重钢铁生产的环保(3-13)上世纪50年代中期兴建的第一个工业规模直接还原铁厂为电炉提供优质的纯铁原料,并导致全世界直接还原铁工业迅速发展。
目前,由于此项技术减少了钢铁生产的排放量,从而获得“绿色”证书。
在希尔萨直接还原厂投入运行时,对环境问题并未给予过多的考虑。
经过长期的不断改进,HYL工艺已可以称作绿色的、现代化的工艺。
不仅该工艺本身最符合环境友好要求,而且其新的附带工艺,如HYLHytemp系统也使炼钢生产更高效。
该工艺通过全封闭气动系统给现代化电炉热装直接还原铁。
这些工艺可使钢铁生产的效率和成本效率得到空前的提高。
1、还原气体还原气体的生产有两种方法:一是外部蒸汽重整器;二是通过“原地重整”反应直接在竖炉反应器内进行。