丰田的7种浪费分析及消除浪费的步骤和对策
七大浪费识别与解决
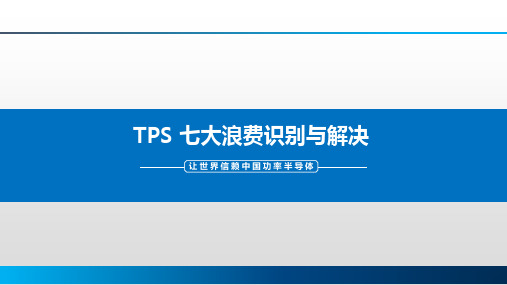
一生的时间 睡眠时间
在企业的 工作时间
如何降低成本,增加利润?
什么是实质性劳动?
取笔帽 1“
步行1“
取笔芯 1“
组装 1“
放下 1“
步行1“
请问创造实质性劳动的环节在哪里? 所谓实质性劳动,就是指具有产品价值和客户价值,并为公司创造利润 的劳动。除此之外一切劳动都是浪费!
如何降低成本,增加利润? 追求实质性劳动
过度加工 浪费
如何产生 加工浪费: 设计产品问题; 加工顺序不合理 作业内容不合理 模夹治具不良 标准化不彻底 材料存在不足
思维方式必须转变
不良品浪费
生产不合格品 造成的浪费
不良品 需要 再生产或维修
造成增加 成本
结束语
不以善小而不为
让世界信赖中国功率半导体
Thanks
感谢您的聆听
搬运 浪费
搬运本身不产生附加价值,所有的搬运都是浪费
思维方式必须转变
搬运的浪费 非必要的搬运距离; 临时堆积(落地次数),倒手&搬运; 搬运车辆的空车行走; 台车上的空间浪费(装载率); 搬运造成破损、刮痕的发生(防护)
搬运 浪费
常见原因 ➢ 布局不合理(孤岛) ➢ 过多暂存区(货架) ➢ 物流线路不合理 ➢ 批量生产(WIP) ➢ 工位间有障碍物 ➢ 线外检验
七大浪费的认识
过剩生产 浪费导致&掩盖其他浪费(万恶之首)
物
搬运 浪费
库存 浪费(万恶之源)
过度加工 浪费(最难察觉)
人
等待 浪费
(有形)改善关键
动作 浪费
质
不良品 浪费
七大浪费---便于记忆的方式
TIMWOOD
① Transportation-搬运 浪费 ② Inventory-库存 浪费 ③ Motion-动作 浪费 ④ Wait-等待 浪费 ⑤ Over-process 过度加工 浪费 ⑥ Over-production 过度生产 浪费 ⑦ Defect-不良品 浪费
丰田管理-现场的7种浪费

现场工作的“七种浪费"在工业生产中,凡是不能直接创造出价值的一切活动,均视为浪费。
文中结合精益生产论述生产现场的七种浪费和如何消除。
20世纪50年代后期诞生于日本丰田汽车公司的精益生产方式,在80年得以发展完善,而且逐步在中国的企业里得到实施,并取得了较为丰硕的成果:生产周期缩短,在制品减少,生产效率提高,废品减少,库存大幅度降低……在本文中,将结合大连三洋制冷推行精益生产方式的实际情况,重点论述生产现场的七种浪费和如何有效消除。
精益生产方式中所指出的浪费,和大家日常生活中所提到的浪费有着截然不同的含义,即:在工业生产中,凡是不能直接创造出价值的一切活动,均视为浪费。
精益生产方式将所有浪费归纳成七种:(1)等待的浪费;(2)搬运的浪费;(3)不良品的浪费;(4)动作的浪费;(5)加工的浪费;(6)库存的浪费;(7)制造过多(早)的浪费.一、七种浪费之一:等待的浪费等待就是闲着没事,等着下一个动作的来临,这种浪费是无庸置疑的。
造成等待的原因通常有:作业不平衡、安排作业不当、停工待料、品质不良等。
以制造部性能试验课等待电控盘为例,由于电控盘不能按要求及时入厂,有可能无法按期交货,而当电控盘入厂后,又需要抢进度,可能会出现加班、质量问题等。
另有一种就是“监视机器”的浪费,有些工厂买了一些速度快、价格高的自动化机器,为了使其能正常运转或其他原因,例如:排除小故障、补充材料等等,通常还会另外安排人员站在旁边监视.所以,虽然是自动设备,但仍需人员在旁照顾,特称之为“闲视”的浪费.例如在产品检测过程中,调试人员和氦检人员站在产品旁边等待,这种情况是否还有?除了在直接生产过程中有等待外,其他管理工作中就没有等待这种浪费发生吗?当制造部在生产新产品发生一些问题时,技术部和品质保证部是否能立即解决而不需要现场人员长时间等待?如何减少这种等待?二、七种浪费之二:搬运的浪费大部分人皆会认同搬运是一种无效的动作,也有人会认为搬运是必须的动作,因为没有搬运,如何做下一个动作?很多人都有这种想法。
7大浪费的产生原因和消除方法

7大浪费的产生原因和消除方法丰田的7种浪费丰田生产方式认为,不产生附加价值的一切作业都是浪费,它把浪费分为以下7种。
1、生产过剩的浪费:一心想要多销售而大量生产,结果在人员、设备、原材料方面都产生浪费。
在没有需求的时候提前生产而产生浪费。
2、不合格产品的浪费:在生产过程中出现废品、次品,会在原材料、零部件、返修所需工时数、生产这些不合格产品所消耗的资源方面产生浪费。
3、待工的浪费:在进行机械加工时,机器发生故障不能正常作业,或因缺乏零部件而停工等活等,在这样的状态下所产生的浪费都是停工等活的浪费。
4、动作上的浪费:不产生附加价值的动作、不合理的操作、效率不高的姿势和动作都是浪费。
5、搬运的浪费:除去准时化生产所必需的搬运,其他任何搬运都是一种浪费。
比如在不同仓库间移动、转运、长距离运输、运输次数过多等。
6、加工本身的浪费:把与工程的进展状况和产品质量没有任何关系的加工当做是必要的加工而进行操作,此种状况下所产生的浪费。
7、库存的浪费:因为原材料、零部件、各道工序的半成品过多而产生的浪费。
这些东西过度积压还会引起库存管理费用的增加。
消除7种浪费的步骤从哪里开始消除这7种浪费为好呢?在像丰田一样积累了50年以上的改善经验和没有这些改善经验的企业中,在生产体制上存在着很大差异。
在此让我们以问题比较多的企业为对象,来思考一下处理7种浪费的基本顺序。
步骤①:在需要的时候适时生产需要的产品可以排除生产过剩的浪费,这需要具备严格管理的思想。
步骤②:如果经常产生不合格产品,抑制生产过剩是很困难的。
我们要消除不合格产品,消除制造不合格产品的浪费。
步骤③:对于停工等活,只要明白其要点就很容易改善。
消除停工等活的浪费,有效利用人力资源。
步骤④~⑥可以根据消除浪费的着眼点从可以实施的部分开始实施。
步骤④:对于动作的浪费,如果减少工时数(人数×时间)将会对消除浪费产生很大影响。
但是,即使是进行动作分析,清除了一些细小的浪费,也会被其他的问题所掩盖,所以必须注意。
详解车间生产的七大浪费及解决方案

详解车间生产的七大浪费及解决方案丰田精益生产方式认为,不产生附加价值的一切作业都是浪费,它把浪费分为以下7种。
01库存浪费“库存是万恶之源”,过多的库存不仅占用空间和资金,产生大量不必要的搬运、堆积和寻找,而且还掩盖了企业内部的各种问题。
例如,生产周期不合理、设备故障太多、不良品太多等。
其产生的原因主要是:企业认为如果有了充足的库存,出现问题时可以有库存先顶上,问题就可以慢慢解决甚至不用解决,最起码不必现在急需解决。
久而久之,就埋下了隐患的种子。
解决方法主要是:提振需求、减少差异源。
具体就是深入联系需求方,做好订单提前量、创造可预知性,联系供应方缩短供应周期、小批量、多批次,调整生产减少瓶颈使其均衡;通过设备专有化,将离岛式车间转变成流水线或虚拟流水线等。
02等待的浪费在加工、搬运、检查过程中,随处可见等待的现象。
例如,前工序来料不及时、设备发生故障、自动机器工作、生产负荷不平衡等,都是等待浪费发生的高危时段。
解决方法:做好提前量,加强协同,扩大销售量,出租厂房、代工,加强资本运作等。
03动作的浪费在生产过程中,人和设备的动作中只要不产生附加价值,都可称为动作浪费。
例如,单手空闲、作业动作突然停止、作业动作过大、左右手交换、步行过多、转身的角度太大、移动中变换“状态”、伸背弯腰动作以及重复动作等,这些不合理的动作造成了时间和体力上的不必要消耗,都是动作浪费。
消除动作浪费的三个主要改善方向为:①取消不必要的动作;②组合两个以上的动作;③放置物品时遵循先进先出原则。
解决办法:根据人体工程学进行动作研究,合理摆放设备,生产标准化,制作工具,对设备进行必要的改造。
04生产过剩的浪费生产过剩包括生产过多和生产过早两个方面。
生产过多主要是由生产不均衡所造成的。
出现了不均衡情况,本应停线追溯其原因,以便及时发现问题,但过量生产有可能使原因无从查起。
生产大量没有卖出去的产品,不仅占用资金、生产空间和仓储空间,增加搬运和库存的浪费,而且还会掩盖生产过程已经出现的各种偏差、浪费和不合理,白白丢掉了改善的突破口。
丰田生产方式消除浪费、降低成本过程总结
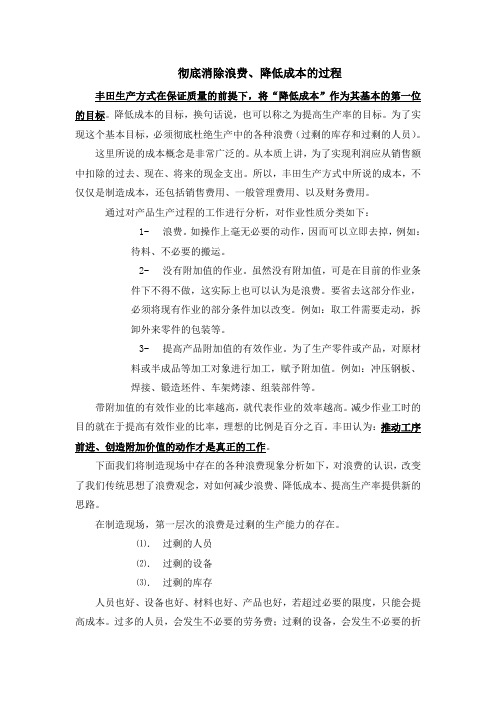
彻底消除浪费、降低成本的过程丰田生产方式在保证质量的前提下,将“降低成本”作为其基本的第一位的目标。
降低成本的目标,换句话说,也可以称之为提高生产率的目标。
为了实现这个基本目标,必须彻底杜绝生产中的各种浪费(过剩的库存和过剩的人员)。
这里所说的成本概念是非常广泛的。
从本质上讲,为了实现利润应从销售额中扣除的过去、现在、将来的现金支出。
所以,丰田生产方式中所说的成本,不仅仅是制造成本,还包括销售费用、一般管理费用、以及财务费用。
通过对产品生产过程的工作进行分析,对作业性质分类如下:1-浪费。
如操作上毫无必要的动作,因而可以立即去掉,例如:待料、不必要的搬运。
2-没有附加值的作业。
虽然没有附加值,可是在目前的作业条件下不得不做,这实际上也可以认为是浪费。
要省去这部分作业,必须将现有作业的部分条件加以改变。
例如:取工件需要走动,拆卸外来零件的包装等。
3-提高产品附加值的有效作业。
为了生产零件或产品,对原材料或半成品等加工对象进行加工,赋予附加值。
例如:冲压钢板、焊接、锻造坯件、车架烤漆、组装部件等。
带附加值的有效作业的比率越高,就代表作业的效率越高。
减少作业工时的目的就在于提高有效作业的比率,理想的比例是百分之百。
丰田认为:推动工序前进、创造附加价值的动作才是真正的工作。
下面我们将制造现场中存在的各种浪费现象分析如下,对浪费的认识,改变了我们传统思想了浪费观念,对如何减少浪费、降低成本、提高生产率提供新的思路。
在制造现场,第一层次的浪费是过剩的生产能力的存在。
⑴.过剩的人员⑵.过剩的设备⑶.过剩的库存人员也好、设备也好、材料也好、产品也好,若超过必要的限度,只能会提高成本。
过多的人员,会发生不必要的劳务费;过剩的设备,会发生不必要的折旧费;过剩的库存,会发生不必要的资金占用、利息支出和机会成本的增加。
由于这些浪费的存在,会产生第二层次的浪费。
特别在工序中人员过多的情况下,每个生产循环中本来就经常或多或少出现闲暇时间(等待时间),为了避免等待就生产出了多余的产品。
丰田内部培训系列教材—7大浪费(15页)

7大浪费--不良、返修的浪费
定义: 是指工厂内发生不良品,需要进行处置的时间· 人力· 物力上的浪费,以及由此造成的相关浪费。
特征:
额外增加人手去检查、修复和 重工
交货延误
较差的顾客/供应商关系
由于重工、报废和额外空运导 致利润降低
组织的反作用(如救火式补救 活动、速递来代替事前预防)
原因: 流程能力不足 作业员控制错误 训练不足 工具/设备不适当 库存水平高
前工程
7大浪费--库存浪费
定义:
原因:
任何超过及时满足顾客所需的产品和 流程能力不足
服务。
存在没有控制的瓶颈
特征: 反应速度慢 库存周转率低 额外的收货空间
更换时间长 供应商能力不足 管理层决策失误 局部利益优化 预测系统不准确
存储场所大
先进后出代替先进先出 问题出现时产生大量重工 原材料超过保质期 供远过于求
净作业:
增加附加价值的作业 (装配,焊接,etc)
无附加价值的作业:
在现有的条件下必须要 做的
(去取部品,etc)
浪 费:
作业方面某些没有必 要的
(等待,返修,etc)
净
作
作
业
技能员 的动作
浪
费
业
没有附加价值的 付随,附带作业
造成成本上升的最大原因-7大浪费
搬运的浪费
生产必要数量以外的搬运 (最小必要量以外的搬运)
[临时放置].[转载]. [零星取出]等的浪费
空手等待的浪费
等待前工程的部品,要取出 工件而等待设备卷帘的打开
的浪费
最恶 劣
制造过剩的浪费
过早地生产因预测会发生 不良,提前生产出必要数量
以上的产品,这样一来 就隐藏了改善的需要 同时会产生等待或
七大浪费(丰田)PPT幻灯片课件
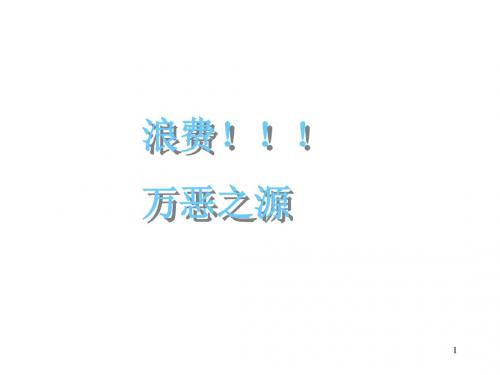
表现形式:
•不良品存在库房内待修
库存是万恶的根源
•设备能力不足所造成的安全库存
•换线时间太长造成次大批量生产的浪费
•采购过多的物料变库存
16
5.库存的浪费
过多的库存会造成的浪费:
•产生不必要的搬运、堆积、放置、找寻、防 护处理等浪费的动作 •使先进先出的作业困难 •损失利息及管理费用 •物品之价值会减低,变成呆滞品 •占用厂房、造成多余的工作场所、仓库建设 投资的浪费 •造成无形的浪费
表现形式:
•自动机器操作中,人员的“闲视”等待
•作业充实度不够的等待
•设备故障、材料不良的等待
•生产安排不当的人员等待
•上下工程间未衍接好造成的工程间的等待
10
2.等待的浪费
原因:
•生产线布置不当,物流混乱 •设备配置、保养不当 •生产计划安排不当 •工序生产能力不平衡 •材料未及时到位 •管理控制点数过多 •品质不良
•搬运距离很远的地方,小批量的运输 •主副线中的搬运 •出入库次数多的搬运 •破损、刮痕的发生
12
3.搬运的浪费
原因:
•生产线配置不当 •未均衡化生产 •坐姿作业 •设立了固定的半成品放置区 •生产计划安排不当
对策:
•U型设备配置 •一个流生产方式 •站立作业 •避免重新堆积、重新包装
注意:
•工作预置的废除 •生产线直接化 •观念上不能有半成品放置区 •人性考虑并非坐姿才可13 以
?
7
对策:
1.制造过多的浪费 •顾客为中心的弹性生产系统
Hale Waihona Puke •单件流动—一个流生产线•看板管理的贯彻
•快速换线换模
•少人化的作业方式
•均衡化生产
丰田生产方式之七大浪费
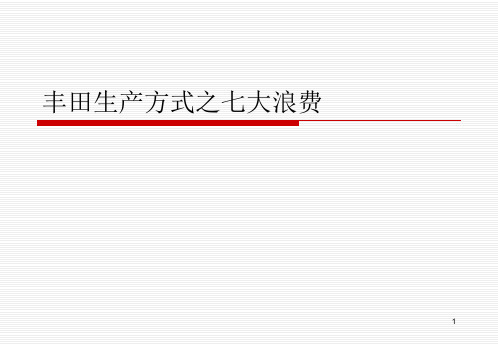
7、等待的浪费
总停线时间 17%
总走线时间 83%
总停线时间 总走线时间
上午8:30至下午17:30的时间描述
42
7、等待的浪费
生产线的暗灯布局 暗灯看板
工位指示灯
急停按钮及 停线指示灯
报警喇叭
FPS点 暗灯拉索
FPS点
FPS点 一个工位
典型的暗灯区域
FPS点 关键检查
完成按钮
43
七大浪费
剪床
冲床 冲床
压床 压床
剪床
冲床
压床
14
1、过量生产的浪费
短底梁过量剪料
15
1、过量生产的浪费
流程式布局
剪床
冲床1
冲床2
剪床
冲床1
冲床2
压床
前后
角柱
门横 梁
16
1、过量生产-措施应用事例
实施流线化布局,工序间采用滑轨传递产品:
后桥焊接工段 孤岛作业严重, 在制品积压多!
流动是我们 价值流分析
精细化 60-70% 人机工程 定点摄影法 60-120
38 20-30 私营企业
6、多余动作的浪费
1.两手空闲的浪费 2.单手空闲的浪费 3.作业动作停止的浪费 4.作业动作太大的浪费 5.拿的动作交替的浪费 6.步行的浪费
7. 转身角度太大的浪费 8. 动作之间没有配合好的浪费 9. 不了解作业技巧的浪费 10.伸背动作的浪费 11.弯腰动作的浪费 12.重复动作的浪费
料
料
机
机
机
人
人
人
5S
安全/健康
SOS
……
目视化管理
产品质量标准现场管理
过程控制
- 1、下载文档前请自行甄别文档内容的完整性,平台不提供额外的编辑、内容补充、找答案等附加服务。
- 2、"仅部分预览"的文档,不可在线预览部分如存在完整性等问题,可反馈申请退款(可完整预览的文档不适用该条件!)。
- 3、如文档侵犯您的权益,请联系客服反馈,我们会尽快为您处理(人工客服工作时间:9:00-18:30)。
当前,整个制造业表现的不是很景气,但细细观察,我们会发现工厂、车间到处充满了浪费现象,如果这种浪费能够得到改进的话,制造业的利润指标肯定也会提升。
本文指出了丰田所说的7种浪费以及消除浪费的步骤和对策,值得制造业同仁学习。
丰田的7种浪费
丰田生产方式认为,不产生附加价值的一切作业都是浪费,它把浪费分为以下7种。
1.生产过剩的浪费
一心想要多销售而大量生产,结果在人员、设备、原材料方面都产生浪费。
在没有需求的时候提前生产而产生浪费。
2.不合格产品的浪费
在生产过程中出现废品、次品,会在原材料、零部件、返修所需工时数、生产这些不合格产品所消耗的资源方面产生浪费。
3.待工的浪费
在进行机械加工时,机器发生故障不能正常作业,或因缺乏零部件而停工等活等,在这样的状态下所产生的浪费都是停工等活的浪费。
4.动作上的浪费
不产生附加价值的动作、不合理的操作、效率不高的姿势和动作都是浪费。
5.搬运的浪费
除去准时化生产所必需的搬运,其他任何搬运都是一种浪费。
比如在不同仓库间移动、转运、长距离运输、运输次数过多等。
6.加工本身的浪费
把与工程的进展状况和产品质量没有任何关系的加工当做是必要的加工而进行操作,此种状况下所产生的浪费。
7.库存的浪费
因为原材料、零部件、各道工序的半成品过多而产生的浪费。
这些东西过度积压还会引起库存管理费用的增加。
消除7种浪费的步骤
从哪里开始消除这7种浪费为好呢?在像丰田一样积累了50年以上的改善经验和没有这些改善经验的企业中,在生产体制上存在着很大差异。
在此让我们以问题比较多的企业为对象,来思考一下处理7种浪费的基本顺序。
步骤①:
在需要的时候适时生产需要的产品可以排除生产过剩的浪费,这需要具备严格管理的思想。
步骤②:
如果经常产生不合格产品,抑制生产过剩是很困难的。
我们要消除不合格产品,消除制造不合格产品的浪费。
步骤③:
对于停工等活,只要明白其要点就很容易改善。
消除停工等活的浪费,有效利用人力资源。
步骤④~⑥可以根据消除浪费的着眼点从可以实施的部分开始实施。
步骤④:
对于动作的浪费,如果减少工时数(人数×时间)将会对消除浪费产生很大影响。
但是,即使是进行动作分析,清除了一些细小的浪费,也会被其他的问题所掩盖,所以必须注意。
步骤⑤:
要消除搬运的浪费,就要在搬运距离和搬运次数等方面加以改进。
步骤⑥:
对于加工过程中本身的浪费,要认识到不产生附加价值的一切东西都是浪费。
步骤⑦:
如果按照①~⑥步骤操作,库存必然会减少。
虽然这些问题堆积如山,但是如果追求库存为零将会产生许多问题。
根据企业的水平,最好在最后阶段消除库存的浪费。