PPAP检查表
PPAP全套表格

S = 供应商必须向世特瑞公司提交,并在适当的场所(包括制造场所)保留一份记录或文件的副本。
R = 供应商必须在适当的场所(包括制造场所)保存,并在顾客有要求时应易于得到。
* = 供应商必须在适当的场所保存,并在有要求时向世特瑞公司提交。
CH2016-16-35
CH2016-16-35
外观批准报告(AAR)
CH2016-16-35
供应商代表签字:日期:部门/职务:CH2016-16-35
供应商代表签字:日期:部门/职务:
供应商代表签字:日期:部门/职务:
CH2016-16-35
二级供应商清单
CH2016-16-35
CH2016-16-35
CH2016-16-35
CH2016-16-35
芜湖世特瑞转向系统有限公司
公司地址:芜湖经济技术开发区龙山路18号
n
生产件批准状况通知PRODUCTION PART APPROVAL STATUS NOTICE
NO:
致:
供应商名称/代码:
地址:
适用范围(车型)APPLICATION(VEHICLES)
零件号PART NUMBER
零件名称PART NAME
更改等级/更改日期CHANGE LEVEL/DATED
更改号CHANGE NUMBER
原用零件号ORIGINAL PART NUMBER
生产件批准状况如下:
Production part approval status is as follow
批准状态
CLASS
备注
世特瑞质量工程师
STL SQE 批准:
CH2016-16-35。
0、PPAP 提交清单及检查表

序号PPAP 文件种类递 交Yes1设计记录2工程变更文件(若有)3设计失效模式和后果分析 (DFMEA)4零部件特殊特性清单Yes零件号 :供应商承诺PPAP 日期:供应商名称 :零件名称 :5分供方物料清单Yes 6过程流程图Yes 7过程失效模式和后果分析 (PFMEA)Yes 8控制计划Yes 9测量系统分析(MSA)Yes 10尺寸报告Yes 11材料、性能检测计划及报告Yes 12外观批准报告(ARR)(如适用)Yes 13生产件样品Yes 14标准样品Yes15检具(含辅具)验收报告(含查基准书,如果有)16包装规范Yes 17初始过程能力研究Yes18产能分析报告Yes19零件提交保证书(PSW)Yes供应商编制: 供应商审核 :SQE 审核 : 日无要求递交N/A PPAP 阶段N/A P1阶段N/A P1阶段N/A P1阶段P1阶段DFMEA是否有技术部门会签供应商提交,SQE是否认同PPAP 实际提交日期:判断依据1.确认远特科技技术部门PDM中设计记录最新版本号与最后一次设计变更/OTT版本号一致。
2.确认设计记录签字盖章是否齐全工程变更通知是否已发布图纸号及版本(设计):PPAP的提交等级 :PPAP 提交清单及检查表项目名称 :车/机型年份 :P1阶段P1阶段P1阶段P1阶段P1阶段P2阶段P2阶段P2阶段P2阶段P2阶段N/A P1阶段P1阶段P2阶段检/辅具验收报告是否有??公司SSQE 确认签字(如果有检查基准书,基准书是否有SQE签字)包装、盛具验收报告是否有??公司SQE确认签字供应商提交,SQE是否认同供应商提交,SQE是否认同供应商提交,SQE是否认同供应商提交,SQE是否认同供应商提交,SQE是否认同供应商提交,SQE根据CA现场确认结果判断供应商是否按CA要求封样并保存供应商提交,SQE是否认同供应商提交,SQE是否认同供应商提交,SQE是否认同供应商提交,SQE是否认同P3阶段P2、P3阶段供应商提交,SQE是否认同供应商提交,SQE是否认同: 日期 : 年月 日: 日期 : 年月日SQE确认OK/NG备注///OK提交日期:设计):交等级 ::年份 :OK OK OK OK OK OK OK OK OK OK OK OK OKOK OK。
PPAP送件自我查检表

零件名稱﹕通用車型﹕零件編號客戶名稱﹕許瑞興(福州)交通器材有限公司PPAP 送件自我查檢表符號說明﹕“S ”----供應商(Shall)提供客戶核準﹐和保留影本記錄或文件於適當區域﹐包括製造場所。
“R ”----供應商應(Shall)保存於適當區域﹐包括製造場所﹐并隨時備妥提供給有需求之客戶。
“*”----供應商應(Shall)保存於適當區域﹐并依客戶送件。
送件層級﹕第III 級適用於所有送件。
第I 級應用於散裝(BULK)材料(除非客戶有另行指定)。
PPAP 送件時機1.3 客戶通知和送件要求﹕1.3.1 通知客戶*供應商應(Shall)通知客戶﹐針對設備機製程變更。
*客戶可(May)決定PPAP 送件核準要求(參考表1.3.1)1. 選用一種有別于先前核準過產品中使用過之結構或材料。
2. 產品來自新的或改裝過的工具﹑模具﹑模型﹑鑄模等(除非可更換行工具)﹐包括增加的或置換的工具。
3. 現存工具或設備翻新或重組后之生產。
4. 工具和設備轉移到另一產地後生產之產品或額外地生產之產品。
5. 包括零組件﹑材料或服務(如熱處理﹑電鍍)來源之變更。
6. 在工具無法大批生產連續12個月或以上之﹐又重新生產之產品。
7. 零組件之產品和製程變更﹐來自供應商內部或外部分包商﹐已影響產品之適用性﹑性能﹑機能和/或耐久性。
8. 適用於散裝(BULK)材料*來自現有分包商之新的管制特性。
HSH 核准﹕確認﹕承辦﹕日期﹕.O 提出新文件N/A 不適用←沿用舊有資料*來自現有分包商之新的管制特性。
* 産品外觀特性變更,圍影響規格。
*同一制程之參數修正。
*外部核準産品之DFMEA變更。
9. 檢驗/試驗方法變更之新技術(未影響外觀標準)送件客戶特定要求﹕II 1. 戴姆勒----克萊斯勒汽車II 2. 福特汽車II 3. 通用汽車II 4. 卡車OEM業者。
PPAP清单-项目开发准备状态检查表

Project Number 项目号 Project Name 项目名称 Date Initial Samples 初样日期 Topic
No. Element 因素 11 Process-
parameter 工艺参数
Launch Readiness Check开发准备检查表
Material Number 材料号 Material Name 材料名字
Project Number 项目号 Project Name 项目名称 Date Initial Samples 初样日期 Topic Project项目
Development Product 开发产品
Production生产 Production
(continuation)生产连续
Launch Readiness Check开发准备检查表
G绿色
x
2 Gate Report
Gate reporting for the gates "Nomination", "Testing Release", "Release of Purchasing" done and all open points closed 关键点报告是指:提名,检测发布,采购发布已完成
x
6 FMEA Design FMEA设计
FMEA finished, all actions c DVP
DVP established, all tests done with pre-production parts, all requirements fullfilled 建 立DVP, 所有试生产零件的测试已完成,满足要求。
Material Number 材料号 Material Name 材料名字
PPAP检查清单样板
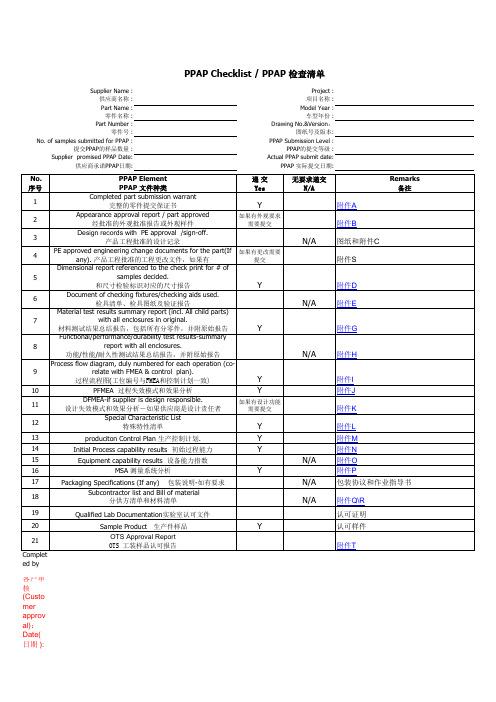
report with all enclosures. 功能/性能/耐久性测试结果总结报告,并附原始报告
Process flow diagram, duly numbered for each operation (co-
relate with FMEA & control plan).
过程流程图(工位编号与FMEA和控制计划一致)
Y
PFMEA 过程失效模式和效果分析
Y
DFMEA-if supplier is design responsible. 设计失效模式和效果分析-如果供应商是设计责任者
如果有设计功能 需要提交
Special Characteristic List
特殊特性清单
Y
produciton Control Plan 生产控制计划.
7
8
9 10 11 12 13 14 15 16 17 18
PPAP Element PPAP 文件种类
递交 Yes
Completed part submission warrant
完整的零件提Biblioteka 保证书YAppearance approval report / part approved 经批准的外观批准报告或外观样件
Project : 项目名称 :
Model Year : 车型年份 :
Drawing No.&Version: 图纸号及版本:
PPAP Submission Level : PPAP的提交等级 :
Actual PPAP submit date: PPAP 实际提交日期:
No. 序号
1 2 3 4
5
6
PPAP Checklist / PPAP 检查清单
PPAP提交资料检查表
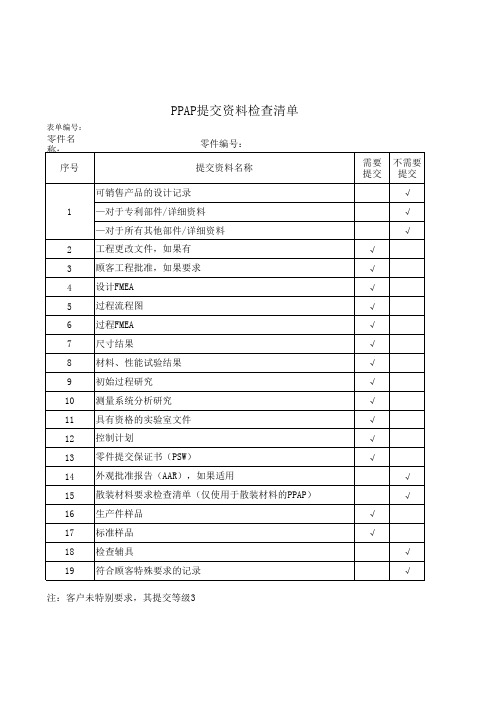
注:客户未特别要求,其提交等级3
需要 不需要 提交 提交
√ √ √ √ √ √ √ √ √ √ √ √ √ √ √ √ √ √ √ √ √
表单编号:
零件名 称:
序号
PPAP提交资料检查清单零 Nhomakorabea编号: 提交资料名称
可销售产品的设计记录 1 —对于专利部件/详细资料
—对于所有其他部件/详细资料 2 工程更改文件,如果有 3 顾客工程批准,如果要求 4 设计FMEA 5 过程流程图 6 过程FMEA 7 尺寸结果 8 材料、性能试验结果 9 初始过程研究 10 测量系统分析研究 11 具有资格的实验室文件 12 控制计划 13 零件提交保证书(PSW) 14 外观批准报告(AAR),如果适用 15 散装材料要求检查清单(仅使用于散装材料的PPAP) 16 生产件样品 17 标准样品 18 检查辅具 19 符合顾客特殊要求的记录
PPAP检查表

结果
PPAP Checklist / PPAP 检查内容清单
No. 序号
PPAP Element PPAP 文件内容
第三方材料告 10
检查内容 尺寸报告是否有检测人员的签字、检测日期? 试验机构是否是客户认可的、或者是权威机构认可的实验室?
10 供应商原材料质保书
执行的标准号及版本号是否与图纸/试验大纲相一致? 是否提交了所有分零件的原材料质保书?
PPAP Checklist / PPAP 检查内容清单
No.
PPAP Element
序号
PPAP 文件内容
1 客户正式发放的图纸
检查内容 顾客的图纸及客户发放的图纸复印件是否包括在提交的文件中?
特殊特性是否在图纸中标明?
2 工程更改文件(如果有)
图纸的版本是否为最新状态? 是否有授权的工程更改,该工程更改已发生在零件上,但还未在设计记录反映出来?
检查内容
外观认可报告是否按照要求格式进行填写(如有客户格式,按客户格式填写)? 是否有颜色、皮纹、光泽的标准样块? 表面纹理加工的供应商是否经过认可(若有此要求)? 是否有客户工程师确认的认可样件? 是否提交全尺寸测量的样件?(提交的PPAP样品与全尺寸测量的样品一一对应,并编号) 每个/箱样件上是否悬挂/粘贴了客户规定的样品标识? 样品代号与尺寸检验报告相对应。 是否提交了每一付模具的每一个模腔的产品,并保留了每一模具、模腔的样件? 是否有客户认可签字 是否包括检具清单? 是否包含客户特殊要求且满足? 客户批准的偏差申请 分供方清单是否获得采购的批准? 分供方清单中是否包含贸易商?(必须体现原材料的生产方) PSW是否已经获得签字批准 签字盖章 针对每道工序都提交了产能分析么? 潜在产能百分比是否>120% ? 表格是否填写完整?
供应商PPAP审核检查表--示例
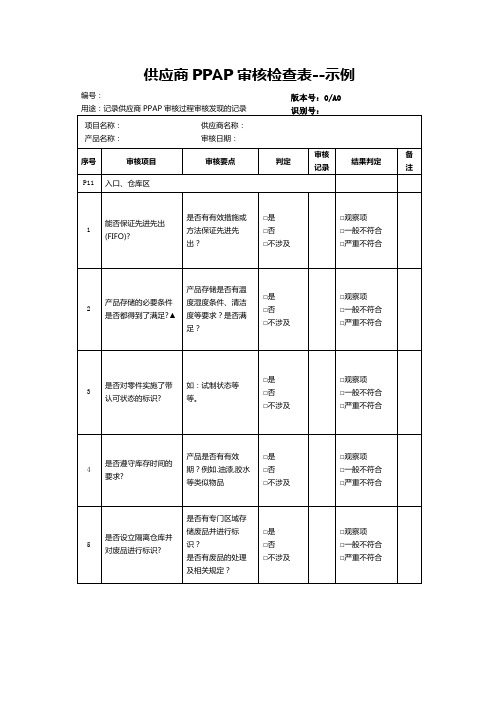
□一般不符合
□严重不符合
11
数据采集和可评价性是否开展?
数据采集和可评价性是否开展(利用测量和检验设备有效监控质量要求)?
□是
□否
□不涉及
□观察项
□一般不符合
□严重不符合
12
过程检验的有效性?
□是
□否
□不涉及
□观察项
□一般不符合
□严重不符合
13
成品检验的有效性?
□是
□否
□不涉及
□观察项
□一般不符合
□是
□否
□不涉及
□观察项
□一般不符合
□严重不符合
P2
产品状态的认可
6
设计记录的确认?▲
抽查零部件的详细的设计记录。
自制件状态是否已经得到批量认可?
对于总成件是否考虑了组装可行性分析、状态判定,顾客的认可?
□是
□否
□不涉及
□观察项
□一般不符合
□严重不符合
7
全尺寸测量结果是否满足顾客要求?
是否进行了全尺寸测量工作?
供应商PPAP审核检查表--示例
编号:
用途:记录供应商PPAP审核过程审核发现的记录
项目名称: 供应商名称:
产品名称: 审核日期:
序号
审核项目
审核要点
判定
审核记录
结果判定
备注
P11
入口、仓库区
1
能否保证先进先出(FIFO)?
是否有有效措施或方法保证先进先出?
□是
□否
□不涉及
□观察项
□一般不符合
□严重不符合
16
存放区域的设定和标识的区分?▲
现场是否进行了不合格品区域的划分?
- 1、下载文档前请自行甄别文档内容的完整性,平台不提供额外的编辑、内容补充、找答案等附加服务。
- 2、"仅部分预览"的文档,不可在线预览部分如存在完整性等问题,可反馈申请退款(可完整预览的文档不适用该条件!)。
- 3、如文档侵犯您的权益,请联系客服反馈,我们会尽快为您处理(人工客服工作时间:9:00-18:30)。
c 产能分析(识别瓶颈工序)
d 特殊特性清单 e 追溯性 f 安全启动计划 g 包装规范
检查内容
是否提交了所有分零件的原材料质保书? 质保书上的原材料是否与图纸/材料替代申请上要求的材料一致? 报告中是否包括标准值和实测值及判定结果? 报告是否有实验室或质量部的批准(盖章)? 试验报告是否标明了所执行的标准? 执行的标准号及版本号是否与图纸/试验大纲相一致? 试验报告是否有试验人员的签字、试验日期? 能力分析是否包含了图纸上标注的所有特殊特性?(全检除外) 是否按照至少125个零件、25个子组来进行能力研究?(破坏性实验按照客户要求) 是否所有特殊特性的Ppk大于或等于1.67?(或按照客户要求) 是否所有试验应在有资质的试验室进行? 提交资料中是否有该实验室资质证明复印件? 资质证明的日期是否还在有效期内? 该零件是否有外观认可要求? 每次递交是否在供应商处保留一个标准样本(或控制计划中标明的数量)? 样品是否贴上标签并标明最新的工程水平? 外观认可报告是否按照要求格式进行填写(如有客户格式,按客户格式填写)? 是否有颜色、皮纹、光泽的标准样块? 表面纹理加工的供应商是否经过认可(若有此要求)? 是否有客户工程师确认的认可样件? 是否提交全尺寸测量的样件?(提交的PPAP样品与全尺寸测量的样品一一对应,并编号) 每个/箱样件上是否悬挂/粘贴了客户规定的样品标识? 样品代号与尺寸检验报告相对应。 是否提交了每一付模具的每一个模腔的产品,并保留了每一模具、模腔的样件? 是否有客户认可签字 是否包括检具清单?
生产控制计划.
MSA 测量系统分析 尺寸检验标识对应的尺寸报告 (气泡图附此处)
第三方材料报告
检查内容
顾客的图纸及客户发放的图纸复印件是否包括在提交的文件中? 特殊特性是否在图纸中标明? 图纸的版本是否为最新状态? 是否有授权的工程更改,该工程更改已发生在零件上,但还未在设计记录反映出来? 工程更改记录是否有客户相关工程师或者客户的手写签字? 工程批准上是否有客户相关工程师或者客户的手写签字?
客户批准的偏差申请 分供方清单是否获得采购的批准? 分供方清单中是否包含贸易商?(必须体现原材料的生产方) PSW是否已经获得签字批准 签字盖章 针对每道工序都提交了产能分析么? 潜在产能百分比是否>120% ? 表格是否填写完整? “SUMMARY OF RESULTS”是否确认状态为"Ready" 包含传递特性(针对客户的客户项目) 是否包含了图纸中要求的所有特殊特性、关键特性 是否明确的表示出追溯方式 F2表格是否已经签字确认? 包装规范是否已经获得客户包装工程师批准?(提交已经获得客户批准的包装规范)
2
结果
No.
PPAP Element
序号
PPAP 文件内容
18 完整的零件提交保证书
PPAP Checklist / PPAP 检查内容清单
检查内容
保证书是否标明正确的零件号、零件名、正确的版本? 客户名称是否正确? 零件的重量是否在保证书上注明?重量是否以Kg为单位并精确到小数点后四位? 提示-随机抽取10个零件,取平均值作为零件重量 每一个零件号是否有一张完整的保证书?(除非客户同意放弃) 责任人是否在保证书上签字并注明职位、电话、签字日期?(责任人一般为质量部经理或者是公司 总经理) 供应商名称是否完整,供应商代码是否正确? 是否注明多付模具或者多形腔的状态? PSW中声明产能与产能分析中的产能是否能做到一致? IMDS号码是否填写? 提交等级是否正确?(一般情况为等级3) 如果提交等级为“其它”,是否注明了适当的理由?
1
结果
PPAP Checklist / PPAP 检查内容清单
No.
PPAP Element
序号
PPAP 文件内容
10 供应商原材料质保书
10 功能/性能/耐久性测试结果总结报告,并附 原始报告
11 初始过程能力
12 实验室认可文件
13 经批准的外观批准报告和外观样件 (需要时)
14 生产件样品
15 标准样品 16 检具清单、检具图纸及验证报告 17 客户特殊要求 a 偏差申请(如果有) b 分供方清单 & 所有分零件PS PPAP 检查内容清单
No. 序号
1 2 3 4 5 6
7
8 9
10
PPAP Element PPAP 文件内容 客户正式发放的图纸 工程更改文件(如果有) 产品的工程批准(如果有) 设计失效模式和效果分析-如果供应商是设 计责任者 过程流程图
PFMEA 过程失效模式和效果分析