氢脆的本质
硫化氢腐蚀的机理及影响因素.
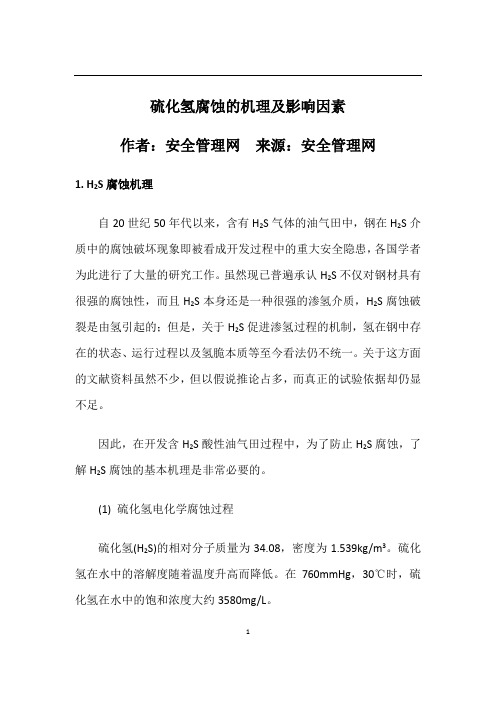
硫化氢腐蚀的机理及影响因素作者:安全管理网来源:安全管理网1. H2S腐蚀机理自20世纪50年代以来,含有H2S气体的油气田中,钢在H2S介质中的腐蚀破坏现象即被看成开发过程中的重大安全隐患,各国学者为此进行了大量的研究工作。
虽然现已普遍承认H2S不仅对钢材具有很强的腐蚀性,而且H2S本身还是一种很强的渗氢介质,H2S腐蚀破裂是由氢引起的;但是,关于H2S促进渗氢过程的机制,氢在钢中存在的状态、运行过程以及氢脆本质等至今看法仍不统一。
关于这方面的文献资料虽然不少,但以假说推论占多,而真正的试验依据却仍显不足。
因此,在开发含H2S酸性油气田过程中,为了防止H2S腐蚀,了解H2S腐蚀的基本机理是非常必要的。
(1) 硫化氢电化学腐蚀过程硫化氢(H2S)的相对分子质量为34.08,密度为1.539kg/m3。
硫化氢在水中的溶解度随着温度升高而降低。
在760mmHg,30℃时,硫化氢在水中的饱和浓度大约3580mg/L。
1在油气工业中,含H2S溶液中钢材的各种腐蚀(包括硫化氢腐蚀、应力腐蚀开裂、氢致开裂)已引起了足够重视,并展开了众多的研究。
其中包括Armstrong和Henderson对电极反应分两步进行的理论描述;Keddamt等提出的H2S04中铁溶解的反应模型;Bai和Conway对一种产物到另一种产物进行的还原反应机理进行了系统的研究。
研究表明,阳极反应是铁作为离子铁进入溶液的,而阴极反应,特别是无氧环境中的阴极反应是源于H2S中的H+的还原反应。
总的腐蚀速率随着pH的降低而增加,这归于金属表面硫化铁活性的不同而产生。
Sardisco,Wright和Greco研究了30℃时H2S-C02-H20系统中碳钢的腐蚀,结果表明,在H2S分压低于0.1Pa时,金属表面会形成包括FeS2,FeS,Fe1-X S在内的具有保护性的硫化物膜。
然而,当H2S分压介于0.1~4Pa时,会形成以Fe1-X S为主的包括FeS,FeS2在内的非保护性膜。
氢脆现象发生的条件

氢脆现象发生的条件氢脆是一种在高强度钢材中发生的现象,其主要特征是在应变速率较低条件下,材料在高应力下发生断裂。
这种现象会导致材料的脆性增加,从而降低其可靠性和使用寿命。
氢脆主要发生在高强度钢材料中,而低强度钢材料通常不会发生氢脆现象。
氢脆现象的发生条件涉及多个方面,主要包括材料本身的性能、外部环境和加工工艺等因素。
下面将逐个分析这些因素。
首先,材料本身的性能对氢脆的发生具有重要影响。
高强度钢材料通常具有较高的强度和硬度,这使得其更容易受到氢脆现象的影响。
此外,材料的结构和组织也会影响氢脆的发生,部分热处理工艺会改变材料的结构,导致材料变得更容易受到氢脆的影响。
另外,材料中的存在的一些缺陷,如夹杂物、析出相等也会促进氢脆的发生。
因此,对材料的成分和性能进行合理的设计和选择是预防氢脆的关键。
其次,外部环境也是氢脆发生的重要条件之一。
氢气是引起氢脆发生的主要原因之一,外部环境中存在的氢气会进入材料内部并与材料中的碳原子结合,形成氢化碳化物,从而导致材料变脆。
因此,在一些特定环境中,如酸洗、电镀、水脱氢等工艺下,氢气会被析出并渗入材料内部,增加了氢脆发生的风险。
此外,环境中的应力和温度变化也可能加剧材料的脆性,从而促进氢脆现象的发生。
因此,在实际生产中,要注意控制好外部环境和加工工艺,避免氢脆的发生。
最后,加工工艺也对氢脆的发生具有重要影响。
一些加工工艺会使材料容易吸收氢气,增加氢脆的发生风险。
例如,在一些金属切削加工中,由于切削过程生成了大量的金属屑,这些金属屑本身就会带有氢气,并且在切削加工中产生的温度和压力会使得这些氢气渗入材料内部,增加了材料的氢脆风险。
另外,在焊接、热处理等加工工艺中,也会引入大量氢气,使材料发生氢脆。
因此,在选择和优化加工工艺时,要注意减少氢气的引入,避免氢脆的发生。
总之,氢脆的发生是一个综合性问题,其发生条件涉及材料本身的性能、外部环境和加工工艺等因素。
要有效预防氢脆的发生,需要从多个层面加以控制。
金属的氢损伤

氢损伤是指与氢的行为有关的金属损伤。金 属从冶炼起,经铸、轧、锻、焊、热处理、机加 工直到使用的过程中,都难免程度不同地同含氢 气氛,含氢化合物(如 H2O 、 H2S 、各种酸溶液) 乃至纯氢发生接触。于是在有些场合下就会发生 金属-氢-力三者先后或共同作用而导致金属破 坏。在航空、航天,交通运输,尤其在化工、石 油等部门都经常发生氢致损伤并都有由此导致的 事故。
依据是工作温度、氢的来源及金属的脱碳程度。
22
延迟氢脆裂纹扩展到瞬断截面时,形变速率增 大,氢的脆化作用消失,其断裂形式就同有裂纹 的无氢试样单调一次加载快速断裂相同,决定于
材料本性、零件尺寸和载荷情况。所以我们讨论
延迟氢脆断口的重点是起裂点及慢速扩展区。可
逆延迟氢脆断裂,在宏观上是很脆的,看不出塑
电解、电镀而氢活度很高,以致在内部产生的
氢气压很高,将金属膨胀起来,成为气泡。
(四)氢腐蚀 发生的温度较氢鼓泡为高,
在205℃-595℃。其本质是氢与钢中的碳结合生
成CH4而鼓泡。由于其受损的外形与氢鼓泡相似
,故早期常将这两者混为一谈。
3
(五)发纹或白点
指通常发生于大型钢锻
件中的一种缺陷。一般认为炼钢或其它工艺加
。溶解态的氢(即屏蔽的质子)能在金属中较
快地扩散。陷井中的氢要获得足以克服势陷井
的能量后,才能与其它H同样地参予扩散过程。
10
第三节 钢中氢损伤的机理
氢对钢的损伤机理,大体说来不外乎三种方式: 一是氢作为破坏力的来源之一,主要指造成内压或 内应力;二是氢使材料弱化、脆化,这里是指固溶 氢使金属的表面能、结合能下降以及形成脆弱的氢 化物MxHy,第三个方而则是氢参与并促进钢的塑性变 形(氢致塑变)和断裂。
材料力学性能名词解释部分

力学性能指标及定义:脆性材料:弹性变形,然后断裂塑性材料:弹性变形,塑性变形低塑性变形材料:无颈缩高塑性材料:有颈缩弹性:是材料的可逆变形。
本质:晶体点阵内的原子具有抵抗相互分开、接近或剪切移动的性质。
弹性模量Ε:表明材料对弹性形变的抗力,代表了材料的刚度。
(斜率)弹性极限ζe:材料发生最大弹性形变时的应力值。
弹性比功W e:材料吸收变形功而又不发生永久变形的能力。
W e=1/2ζeεe=εe2/2Ε(面积)普弹形变(高分子):应力与应变的关系符合胡克定律,变形由分子链内部键长和键角发生变化产生。
高弹形变(高分子):分子链在外力作用下,原先卷曲的链沿受力方向逐渐伸展产生,伸展长度与应力不成线性关系。
弹性的不完整性:应变滞后于应力。
本质:组织的不均匀性,使材料受应力作用时各晶粒的应变不均匀或应变明显受时间的影响。
弹性后效:加载时应变落后于应力而和时间有关的现象称为正弹性后效;反之,卸载时应变落后于应力的现象称为反弹性后效。
弹性滞后:由于正反弹性后效使得应力-应变得到的封闭回线内耗:加载时消耗于材料的的变形功大于卸载时材料所放出的变形功,因而有部分变形功被材料所吸收,这被吸收的功为内耗。
(例子:①音响效果好的元件要求内耗小such as音叉、琴弦等②机件在运转时常伴有振动,需要良好的消振材料such as灰口铸铁)包申格效应:金属材料预先经少量塑性变形后再同向加载,弹性极限升高,反之降低的现象。
与位错运动所受阻力有关。
(例子:高速运转部件预先进行高速离心处理,有利于提高材料的抗变形能力。
)超弹性材料:材料在外力作用下产生远大于其弹性极限时的应变量,外力去除自动恢复其变形的现象。
脆性:弹性极限前断裂(断裂前不产生塑性变形的性质)韧性:断裂前单位体积材料所吸收的变性能和断裂能,即外力所作的功①弹性变形能②塑性变形能③断裂能塑性:材料在断裂前发生的永久型变形(不可逆变形)塑性变形:位错在外力的作用下发生滑移和孪生。
材料力学性能课后习题答案

材料力学性能课后习题答案1弹性比功:金属材料吸收弹性变形功的能力,一般用金属开始塑性变形前单位体积吸收的最大弹性变形功表示。
2.滞弹性:金属材料在弹性范围内快速加载或卸载后,随时间延长产生附加弹性应变的现象称为滞弹性,也就是应变落后于应力的现象。
3.循环韧性:金属材料在交变载荷下吸收不可逆变形功的能力称为循环韧性。
4.xx效应:金属材料经过预先加载产生少量塑性变形,卸载后再同向加载,规定残余伸长应力增加;反向加载,规定残余伸长应力降低的现象。
5.解理刻面:这种大致以晶粒大小为单位的解理面称为解理刻面。
6.塑性:金属材料断裂前发生不可逆永久(塑性)变形的能力。
韧性:指金属材料断裂前吸收塑性变形功和断裂功的能力。
7.解理台阶:当解理裂纹与螺型位错相遇时,便形成一个高度为b的台阶。
8.河流花样:解理台阶沿裂纹前端滑动而相互汇合,同号台阶相互汇合长大,当汇合台阶高度足够大时,便成为河流花样。
是解理台阶的一种标志。
9.解理面:是金属材料在一定条件下,当外加正应力达到一定数值后,以极快速率沿一定晶体学平面产生的穿晶断裂,因与大理石断裂类似,故称此种晶体学平面为解理面。
10.穿晶断裂:穿晶断裂的裂纹穿过晶内,可以是韧性断裂,也可以是脆性断裂。
沿晶断裂:裂纹沿晶界扩展,多数是脆性断裂。
11.韧脆转变:具有一定韧性的金属材料当低于某一温度点时,冲击吸收功明显下降,断裂方式由原来的韧性断裂变为脆性断裂,这种现象称为韧脆转变12.弹性不完整性:理想的弹性体是不存在的,多数工程材料弹性变形时,可能出现加载线与卸载线不重合、应变滞后于应力变化等现象,称之为弹性不完整性。
弹性不完整性现象包括包申格效应、弹性后效、弹性滞后和循环韧性等金属的弹性模量主要取决于什么因素?为什么说它是一个对组织不敏感的力学性能指标?答:主要决定于原子本性和晶格类型。
合金化、热处理、冷塑性变形等能够改变金属材料的组织形态和晶粒大小,但是不改变金属原子的本性和晶格类型。
氢脆

氢脆1.氢脆的定义:是溶于钢中的氢,聚合为氢分子,造成应力集中,超过钢的强度极限,在钢内部形成细小的裂纹,又称白点。
强度极限:材料不发生过量塑性变形甚至断裂。
2.氢脆产生的条件:氢在常温常压下不会对钢产生明显的腐蚀,但当温度超过300℃和压力高于30MPa时,会产生氢脆这种腐蚀缺陷,尤其是在高温条件下。
3.氢脆的来源:内部氢脆和环境氢脆。
①内部氢脆:是材料在使用前内部已含有足够的氢并导致了脆性,它可以是材料在冶炼、热加工、热处理、焊接、电镀、酸洗等制造过程中产生。
②环境氢脆:是指材料原先不含氢或含氢极微,但在有氢的环境与介质中产生。
这样的环境通常有(1)在纯氢气氛中(有少量的水分,甚至干氢)由分子氢造成氢脆(2)由氢化物致脆(3)由H2S致脆(4)高强钢在中性水或潮湿的大气中致脆。
总结:无论是内部氢脆还是环境氢脆,其脆化的本质都是一样的。
这个现象叫“氢脆”,不叫“氢化”,主要发生在钢铁上。
对于铜来说,氢能溶于液态铜,且其溶解度随温度的升高而升高;若吸氢较多,过饱和氢会大量析出,在铸坯上出现微小气泡和微裂纹。
另外一方面如上文所述形成水蒸气,产生极大内应力,引起所谓“氢脆”现象,严重影响铜的塑性加工性能。
但是在酸性环境中,由于铜的化学活性比氢低,通常并不会被腐蚀。
至于铝,它会把酸中的氢离子还原成氢气,相应地自己被腐蚀掉。
4.氢脆的特点①首先氢脆一经产生,就消除不了。
②氢脆只可防,治不了。
③电镀后,如产生氢脆,进行热处理是不适合的。
设备在电镀或酸洗时,钢表面被吸附的氢原子过饱和,使氢渗入钢中。
热处理的方法是将工件加热至某一温度,保温一段时间,缓冷,使氢随溶解度逐渐变小,逐渐析出。
但是加热会破坏镀层。
5.如何预防氢脆。
①控制好酸洗过程。
首先,尽量缩短酸洗时间;其次加缓蚀剂,减少产氢量。
压力容器的氢脆(或称氢损伤)是指它的器壁受到氢的侵蚀,造成材料塑性和强度降低,并因此而导致的开裂或延迟性的脆性破坏。
高温高压的氢对钢的损伤主要是因为氢以原子状态渗入金属内,并在金属内部再结合成分子,产生很高的压力,严重时会导致表面鼓包或皱折;氢与钢中的碳结合,使钢脱碳,或使钢中的硫化物与氧化物还原。
氢脆的介绍及断口形貌

氢脆断裂的失效分析1. 氢损伤的特点和分类氢损伤指在金属中发生的一些过程,这些过程导致金属的承载能力因氢的出现而下降。
氢损伤可以按照不同方式分类。
按照氢损伤敏感性与应变速度的关系分为两大类。
第一类氢损伤的敏感性随应变速度的增加而增加,其本质的是在加载前材料内部已存在某种裂纹源,故加载后在应力作用下加快了裂纹的形成和扩展。
第二类氢损伤的敏感性随应变速度的增加而降低,其本质是加载前材料内部并不存在裂纹源,加载后由于应力与氢的交互作用逐渐形成裂纹源,最终导致材料的脆性断裂。
1.1第一类氢损伤第一类氢损伤包括以下几种形式:(1)氢腐蚀由于氢在高温高压下与金属中第二相夹杂物货合金添加物发生化学反应,生成的高压气体,这些高压气体造成材料的内裂纹和鼓泡,使晶界结合力减弱,最终使金属失去强度和韧性。
(2)氢鼓泡过饱和的氢原子在缺陷位置(如夹杂)析出后,形成氢分子,在局部造成很高氢气压,引起表面鼓泡货内部裂纹。
(3)氢化物型氢脆氢与周期表中ⅣB或ⅤB族金属亲和力较大,容易生成脆性的氢化物相,这些氢化物在随后受力时成为裂纹源和扩展途径。
氢在上述三种情况下造成了金属的永久性损伤,使材料的塑性或强度降低,即使从金属中除氢,这些损伤也不能消除,塑性或强度也不能恢复,故称为不可逆损伤。
1.2第二类氢损伤第二类氢损伤包括以下几种形式:(1) 应力诱发氢化物型氢脆在稀土、碱土及某些过渡族金属中,当氢含量不高时,氢在固溶体中的过饱和度较低,尚不能自发形成氢化物。
在加载后,由于应力作用,使氢在应力集中处富集,最终形成氢化物。
这种应力应变作用诱发的氢化物相变。
只是在较低的应变速度下出现的。
然而,一旦出现氢化物,即使去载荷除氢,静止一段时间后,再高速变形,塑性也不能恢复故也属于不可逆氢脆。
(2) 可逆氢脆含氢金属在缓慢的变形中逐渐形成裂纹源,裂纹扩展后最终发生脆断。
但在未形成裂纹前,去载荷除氢,静止一段时间后再高速变形,材料的塑性可以得到恢复,为可逆氢脆。
钛合金热氢处理技术及其应用前景_侯红亮

关键词 : 钛合金 ; 氢 ;氢致塑性 ; 氢致相变 中图分类号 : TG 146 . 2 氢是一个令人生畏的元素 , 若进入金属 , 可以 引起材料内部结构的变化 , 在绝大多数情况下 , 氢 使材料的许多性能( 如磁性 、 耐腐蚀性等) 恶化 , 而 且能导致氢脆 。因此 , 自上世纪 40 年代钛工业发展 以来 , 氢一直被视为一种有害的杂质元素 , 认为氢 在钛合金中只会产生不利影响而一直致力于氢脆的 研究 。 然 而 , 在 1959 年 , 原西 德 学者 Zwiecker 和 Schleicher 在 钛合 金 Ti-8Al , Ti-10Al , Ti-13Al 和 Ti8Al-3In 铸锭加入适量的氢 , 研究其热压力加工性能 时发现合金的热加工性能得到明显改善 , 从而提出 了氢增加钛合金热塑性的观点 , 并通过实验验证了 这种观点 。这在当时仅被作为一种例外而被忽视 , 但 Zwiecker 和 Schleicher 已揭开了钛合金中 氢作用 的新的一页[ 1 3] 。 许多学者在总结和评述氢对钢铁材料力学性能 的影响时指出 : 氢可以促进螺形位错的迁移 , 并加 快位错的运动 , 从而导致流动应力的降低 。根据对 氢脆断口的分析 , 发现裂纹前端有一个相当大的塑 性变形区 , 说明氢脆在本质上是氢致滞后塑性与开 裂 , 验证了氢致软化现象的存在 , 引发了人们对氢 致软化或氢致塑性更深层次的思考 。 氢作为可逆合金化元素在钛合金中具有很高的 吸附能力和扩散迁移能力 , 对相变过程和组织结构 的形成有着强烈的影响 , 保证能实现可逆合金化而 不改变材料的整体状态 。钛合金热氢处理技术 , 也 称氢处理或氢工艺 , 是利用氢致塑性 、 氢致相变以 1. 1 存在形式 研究表明 : 氢在钛及钛合金中间隙固溶 , 且溶 解度高 。在 600 ℃及 100 kPa 压力下纯钛可溶解的 氢达 60 % ( 摩尔分数) 。如果钛氢系统中的氢含量超 过合金的固溶度时 , 则可形成氢化物 , 主要有面心 立方结构的 δ 氢化物 、 面心四方结构的 ε 氢化物和 [4 6 ] γ 氢化物 。 氢的溶解及其反应具有可逆性 。通过真空退火 的方法可以将氢从钛合金中去除 , 使钛结构在服役 之前的氢含量恢复到安全水平 , 保证在服役时不发 生氢脆 。钛氢系统的吸放氢特点有可能使氢作为临 时合金化元素在钛合金中得到应用 , 这正是钛合金 热氢加工技术的重要基础 。 1. 2 氢对相变的影响 1)氢是 β 相稳定元素 , 可以有效地降低 ( α + β) / β 转变温度 , 相应增加了退火和淬火合金中 β 相数量 。如渗氢后纯钛的 β 相转变温度由 860 ℃ 降 文献标识码 : A 及钛合金中氢的可逆合金化作用以实现钛氢系统最 佳组织结构 、 改善加工性能的一种新体系 、 新方法 和新手段 。利用该技术可以达到改善钛合金的加工 性能 、 提高钛制件的使用性能 、 降低钛产品的制造 成本 、 提高钛合金的加工效率的目的 。
- 1、下载文档前请自行甄别文档内容的完整性,平台不提供额外的编辑、内容补充、找答案等附加服务。
- 2、"仅部分预览"的文档,不可在线预览部分如存在完整性等问题,可反馈申请退款(可完整预览的文档不适用该条件!)。
- 3、如文档侵犯您的权益,请联系客服反馈,我们会尽快为您处理(人工客服工作时间:9:00-18:30)。
试述氢脆的本质
我认为位错井捕氢学说比较合理的解释了氢脆的本质。
实际金属材料内部存在大量的缺陷,它们都是氢的陷阱,陷阱增大材料的吸氢量,减慢氢的扩散速度,使氢发生偏聚,从而降低该处的界面结合力。
而且氢促进了位错的平面滑移,阻碍了交滑移。
从而加剧位错塞积。
导致位错分布和塑性变形的不均匀性。
如果在应力作用下形变速率较小,形变温度又不太低的话,那么氢原子的运动速度与位错运动速度是相适应的,这时不会产生氢或位错的大量堆积,也就不会发生氢脆;当在应力作用下移动着的位错及氢气团运动至晶界或其他障碍物时,会产生位错的堆积,同时必然造成氢在晶界或解理面的富集,在位错堆积的端部形成较大的应力集中,从而形成裂纹,富集的氢原子不仅易导致裂纹形成,而且有使其发生扩展的趋势,最后造成脆性断裂。
也就是说,由于氢的存在使得位错的堆积更加严重,更加快速,从而在较低的载荷下就发生脆断。
以上观点是参考相关文献后我个人对氢脆的理解
举例分析由氢引起的金属失效问题
某型机翼盖板用30CrMnSiNi2A钢螺钉规格为M6,采用氯化铵镀镉工艺在螺钉表面镀镉后再经(190±10)℃×23 h除氢。
在装配后的存放期间该螺钉发生了断裂,具有明显的延迟特征,断裂位置位于螺杆与钉头转接处(螺纹退刀槽)处,初步分析为氢脆断裂。
作者对此进行了进一步失效分析,并对其进行了生产工艺改进,以确定该螺钉的失效模式及主要原因。
1理化检验与结果
1.1化学成分
用ICP-AES型电感耦合等离子体原子发射光谱仪分析试样的化学成分(质量分数,%)为
0.29C,1.12Si,1.18Mn,1.08Cr,1.76Ni,0.012P,0.000 8S;
满足GJB 1951-1994的要求。
1.2断口形貌
从宏观断口形貌可见,该螺钉断裂于钉头与螺杆转接处, 断口洁净且较平齐,无明显的塑性变形;断口表面呈结晶颗粒状,在光镜下呈闪光小刻面特征;断口表面无明显的放射棱线特征,上侧边缘存在微小的剪切唇边。
由宏观断口形貌可见,断裂起源于螺钉断口次表面,源区微观上为典型的沿晶特征,表面洁净未见冶金和加工缺陷;断口的扩展区亦以沿晶特征为主,瞬断区为韧窝特征,沿晶和沿晶与韧窝混合特征区域面积占断口90%以上。
另在源区和扩展区均可见二次裂纹,扩展区局部位置存在沿晶与韧窝的混合特征。
对断口各区域进行能谱分析,没有发现硫、氯等腐蚀性元素,也未见镉等其它外来元素。
1.3显微组织
在螺钉断口附近取样,经抛光腐蚀后用光学显微镜下观察。
螺钉组织为马氏体组织,组织均匀,未见异常。
1.4拉伸性能
对与断裂螺钉同批次的螺钉进行拉伸试验,检测螺钉的实际断裂载荷。
结果表明,断裂螺钉的
实际破断力约为32 kN。
螺钉在拉伸试验中断裂于退刀槽底部,槽底处直径为4.5 mm,计算出螺钉材料的抗拉强度约为2 010 MPa(缺口强度),强度偏高。
螺钉拉伸断口微观上为典型的韧窝特征。
对与断裂螺钉同工艺、同批次的螺钉进行了冲击试验,冲击试验断口同为韧窝特征。
1.5 显微硬度
螺栓显微硬度测试结果为520.6,495.9,506.1,518.5,525.6HV0.3,平均值为513.3HV0.3,相当
于49.8 HRC。
正常螺栓为45 HRC。
螺栓的实际硬度均高于设计要求的36~40 HRC。
测试结
果显示失效螺栓硬度比正常螺栓高4~5 HRC。
1.6氢含量
由于断裂螺钉剩余部分质量不足,无法进行含量的测试,因此对与断裂螺钉同工艺、同批次螺钉的螺杆和螺纹部位的氢含量进行检测。
对保留和去除表面镀镉层后的氢含量进行测量,每种状态测量3个取平均值。
可见螺钉中氢含量较高,且保留镀镉层的氢含量要高于去除镀镉层后的氢含量,螺纹处的氢含量要高于螺杆处的。
2断裂原因分析
根据以上试验结果,首先,螺栓的显微组织为回火马氏体,由文献[1]在各种不同的显微组织中,对氢脆敏感性从大到小的一般顺序为马氏体、上贝氏体(粗大贝氏体)、下贝氏体(细贝氏体)、索氏体、珠光体、奥氏体,因而螺栓的组织是氢脆敏感组织。
其次,一般地,钢中氢的质量分数超过5×10-4时,即存在氢脆裂纹的危险。
而对于30CrMnSiNi2A这种超高强度钢,氢的质量分数超过1×10-4时即已经是危险的,而表1中的试验结果表明该螺钉中氢的质量分数远大于1×10-4;而该螺钉的强度高达2010MPa,强度偏高。
而且,虽然正常螺栓的氢含量也很高高,但并没有发生氢脆断裂,这是由于失效螺栓因热处理不当而导致强度过高,从而对氢的敏感性增加。
最后,根据断口的形貌及能谱分析结果,螺钉断口宏观上无明显的塑性变形,断口表面清洁, 无腐蚀产物, ,有放射花样,呈结晶颗粒特征,光镜下为闪光的小刻面特征;断裂起源于螺钉次表面,源区为典型的沿晶特征; 晶界上伴有变形线(发纹线或鸡爪痕), 这是氢脆的典型特征。
断口扩展区为沿晶特征或沿晶与韧窝混合特征,占断口面积的90%以上,为典型的沿晶断裂。
所以判定失效螺栓应属于氢脆断裂
3预防措施
通过在热处理过程中控制工艺参数,使螺钉获得不同的强度级别,经镀镉并根据标准严格执行除氢工艺后,对螺钉中的氢含量进行测定。
由表2可见,不同工艺批次螺钉的氢含量差别较小;拉伸断裂载荷超过32 kN的3组螺钉均未通过氢脆验证试验,而拉伸断裂载荷较低的5组螺钉均获通过。
实际上,氢的扩散和聚集导致材料局部氢浓度偏高是导致氢致开裂的直接原因。
氢通常会聚集在存在缺陷或应力集中的次表面,聚集位置的氢浓度达到一定值后,氢致附加应力与外加应力共同作用,导致形成氢脆裂纹或断裂。
也就是说,在钢中存在氢的前提下,局部的氢浓度偏高
才是导致氢致裂纹的原因。
由于所测得的氢含量值为所取试样的平均值,不能反映裂纹尖端真实的氢浓度;而且在进行氢含量测定时,所取试样是否包含镀层对于氢含量测试的影响很大,带镀层试样的氢含量可能超出不带镀层试样5倍甚至更多(见表2),因此,在进行氢含量测定时如何选取试样亦需进一步探讨。
文献和实践经验均表明,超高强度钢中氢含量低于1×10-6(测得的平均值)也可能发生氢脆,但氢含量更高时未必发生氢脆。
这表明,氢含量只能作为一个参考指标,不能将氢含量的测定值作为材料或制件是否会发生氢脆的直接判据。
而且,实际批量生产时,将螺钉中的氢含量控制在极低的水平(质量分数为1×10-4)是很困难的,但通过改善热处理工艺来控制螺钉的强度则相对容易。
从表2可以看出,当螺钉的最大断裂载荷降低至30 kN时,各组螺钉均通过了氢脆验证试验,也就是说,即使螺钉中的氢含量较高,将螺钉强度控制在相对较低的水平可以保证螺钉在一定应力范围内使用而不发生氢脆。
因此,在生产高强度钢和超高强度钢螺纹紧固件时,在根据标准严格执行除氢工艺的基础上,在螺钉强度满足标准规定的前提下,尽量控制螺钉的强度至下限,这对于预防和控制该螺钉的氢脆是非常有效的。
4结论
(1)机翼盖板用30CrMnSiNi2A钢螺钉装配后的失效为氢脆断裂。
(2)在根据标准规定除氢的工艺基础上,将螺钉的强度降低到合适的水平,是预防和控制高强度螺钉氢脆的有效措施。