轧钢机主传动系统扭振故障分析
《轧机传动系统扭振智能控制方法研究》范文
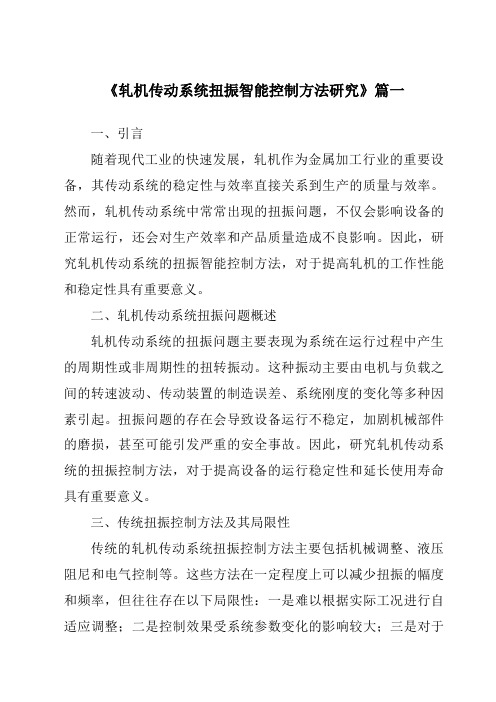
《轧机传动系统扭振智能控制方法研究》篇一一、引言随着现代工业的快速发展,轧机作为金属加工行业的重要设备,其传动系统的稳定性与效率直接关系到生产的质量与效率。
然而,轧机传动系统中常常出现的扭振问题,不仅会影响设备的正常运行,还会对生产效率和产品质量造成不良影响。
因此,研究轧机传动系统的扭振智能控制方法,对于提高轧机的工作性能和稳定性具有重要意义。
二、轧机传动系统扭振问题概述轧机传动系统的扭振问题主要表现为系统在运行过程中产生的周期性或非周期性的扭转振动。
这种振动主要由电机与负载之间的转速波动、传动装置的制造误差、系统刚度的变化等多种因素引起。
扭振问题的存在会导致设备运行不稳定,加剧机械部件的磨损,甚至可能引发严重的安全事故。
因此,研究轧机传动系统的扭振控制方法,对于提高设备的运行稳定性和延长使用寿命具有重要意义。
三、传统扭振控制方法及其局限性传统的轧机传动系统扭振控制方法主要包括机械调整、液压阻尼和电气控制等。
这些方法在一定程度上可以减少扭振的幅度和频率,但往往存在以下局限性:一是难以根据实际工况进行自适应调整;二是控制效果受系统参数变化的影响较大;三是对于复杂工况下的扭振问题,控制效果往往不理想。
因此,需要研究更加智能化的扭振控制方法。
四、智能扭振控制方法研究针对传统扭振控制方法的局限性,本研究提出了一种基于智能控制的轧机传动系统扭振控制方法。
该方法主要利用人工智能技术,通过实时监测和分析系统的运行状态,实现自适应的扭振控制。
具体包括以下几个方面:1. 智能识别与监测:通过安装传感器和监测装置,实时采集轧机传动系统的运行数据,包括转速、扭矩、振动等。
利用人工智能技术对这些数据进行处理和分析,实时识别系统的运行状态和扭振情况。
2. 智能诊断与预测:根据实时监测的数据,利用机器学习、深度学习等人工智能技术,对系统的运行状态进行诊断和预测。
通过分析系统的历史数据和运行规律,预测可能出现的扭振问题,并及时采取相应的控制措施。
《轧机传动系统扭振智能控制方法研究》范文

《轧机传动系统扭振智能控制方法研究》篇一一、引言随着现代工业的快速发展,轧机作为金属加工行业的重要设备,其传动系统的稳定性与效率显得尤为重要。
然而,轧机传动系统中扭振问题一直是影响其性能的关键因素之一。
扭振不仅会降低设备的生产效率,还可能导致设备的损坏和维修成本的增加。
因此,对轧机传动系统扭振的智能控制方法进行研究具有重要的理论价值和实践意义。
二、轧机传动系统扭振问题概述轧机传动系统的扭振问题主要源于电机与轧辊之间的力矩传递不均、系统刚度不足以及外部负载的波动等因素。
扭振会导致传动系统的动力性能下降,增加设备的维护成本,甚至可能引发安全事故。
传统的控制方法主要依靠经验丰富的操作人员和复杂的机械结构来减少扭振,但效果有限且难以适应复杂的工况。
因此,研究智能控制方法对解决轧机传动系统的扭振问题具有重要意义。
三、智能控制方法在轧机传动系统中的应用针对轧机传动系统的扭振问题,智能控制方法提供了一种有效的解决方案。
这些方法主要包括基于人工智能的预测控制、优化控制和自适应控制等。
这些方法可以实时监测和分析传动系统的运行状态,通过调整控制参数来减少扭振。
此外,智能控制方法还可以根据不同的工况和负载变化自动调整控制策略,提高系统的适应性和稳定性。
四、轧机传动系统扭振智能控制方法研究本文提出了一种基于深度学习的轧机传动系统扭振智能控制方法。
该方法通过在系统中安装传感器来实时监测传动系统的运行状态,包括力矩、速度、加速度等参数。
然后,利用深度学习算法对这些数据进行处理和分析,预测出传动系统的扭振情况。
接着,根据预测结果,通过优化算法调整控制参数,实现对扭振的智能控制。
具体而言,该方法包括以下几个步骤:1. 数据采集与预处理:通过传感器实时采集轧机传动系统的运行数据,包括力矩、速度、加速度等参数。
然后对这些数据进行预处理,包括去噪、滤波和归一化等操作,以便后续的深度学习算法处理。
2. 深度学习模型构建:构建深度学习模型,如循环神经网络(RNN)或长短期记忆网络(LSTM)等,用于分析和预测传动系统的扭振情况。
《考虑带材的轧机主传动系统扭振研究》范文

《考虑带材的轧机主传动系统扭振研究》篇一一、引言在带材轧制过程中,轧机主传动系统的扭振问题是一个重要的研究课题。
扭振不仅会影响轧机的正常运行,还可能对带材的质量和轧机的使用寿命产生不良影响。
因此,对轧机主传动系统扭振的研究具有重要的理论意义和实际应用价值。
本文将针对考虑带材的轧机主传动系统扭振问题进行研究,旨在深入探讨其产生原因、影响因素及相应的控制措施。
二、轧机主传动系统扭振的产生原因及影响因素1. 产生原因轧机主传动系统的扭振主要由于电机与轧辊之间的转矩波动、轧制过程中的摩擦力变化、带材的厚度、宽度及材质差异等因素引起。
此外,轧机主传动系统的结构设计、刚度及阻尼等因素也会对扭振产生影响。
2. 影响因素(1)电机与轧辊之间的转矩波动:电机转矩的波动是引起轧机主传动系统扭振的主要原因之一。
转矩波动的大小、频率及相位等因素都会对扭振产生影响。
(2)轧制过程中的摩擦力变化:轧制过程中,轧辊与带材之间的摩擦力会发生变化,从而导致轧机主传动系统的扭振。
(3)带材的厚度、宽度及材质差异:不同厚度、宽度及材质的带材在轧制过程中会产生不同的力学性能,进而影响轧机主传动系统的扭振。
三、考虑带材的轧机主传动系统扭振研究方法针对考虑带材的轧机主传动系统扭振问题,本文采用以下研究方法:1. 理论分析:通过建立轧机主传动系统的动力学模型,分析扭振的产生原因及影响因素。
结合带材的力学性能,探讨带材对轧机主传动系统扭振的影响。
2. 实验研究:通过实验测量轧机主传动系统的扭振数据,分析实际生产过程中扭振的特点及规律。
同时,通过改变带材的厚度、宽度及材质等参数,研究这些因素对扭振的影响。
3. 仿真分析:利用仿真软件对轧机主传动系统进行仿真分析,验证理论分析的正确性。
通过改变仿真参数,探讨不同因素对扭振的影响程度。
四、控制措施及优化建议针对轧机主传动系统的扭振问题,本文提出以下控制措施及优化建议:1. 优化电机与轧辊之间的转矩控制:通过优化电机的转矩控制策略,减小转矩波动,从而降低轧机主传动系统的扭振。
《2024年轧机传动系统扭振智能控制方法研究》范文

《轧机传动系统扭振智能控制方法研究》篇一一、引言随着现代工业的快速发展,轧机作为金属加工的重要设备,其传动系统的稳定性和效率对产品质量和生产效率具有重要影响。
然而,轧机传动系统中扭振问题一直是影响其性能的关键因素之一。
扭振不仅会导致设备运行的不稳定,还会对设备产生损害,影响产品的精度和表面质量。
因此,研究轧机传动系统的扭振智能控制方法具有重要的现实意义。
二、轧机传动系统扭振问题分析轧机传动系统扭振问题的产生,主要是由于电机与轧辊之间的传动不平衡、负载变化、系统刚度不足等因素引起的。
扭振不仅会降低设备的运行效率,还会对设备的寿命和产品质量产生负面影响。
传统的扭振控制方法主要依赖于经验和试错法,缺乏理论指导和智能优化,难以满足现代工业的高效、稳定、智能化的需求。
三、智能控制方法研究针对轧机传动系统的扭振问题,本文提出了一种智能控制方法。
该方法基于现代控制理论、信号处理技术和人工智能技术,通过实时监测和分析传动系统的运行状态,实现对扭振的智能控制和优化。
1. 信号处理技术信号处理技术是智能控制方法的基础。
通过对传动系统中的振动信号进行采集、处理和分析,可以获取系统的运行状态和扭振特征。
利用频谱分析、小波分析等信号处理方法,可以提取出扭振信号的频率、幅度、相位等特征参数,为后续的智能控制提供依据。
2. 人工智能技术人工智能技术是实现智能控制的关键。
通过建立基于人工智能的模型,可以对传动系统的运行状态进行预测和优化。
例如,可以利用神经网络、支持向量机等机器学习算法,对历史数据进行分析和学习,建立扭振控制的模型和规则。
然后,根据实时监测的数据,对模型进行修正和优化,实现对扭振的智能控制。
3. 智能控制策略基于信号处理技术和人工智能技术,可以制定出多种智能控制策略。
例如,可以根据扭振的特征参数,制定出适应不同工况的控制策略。
通过调整电机的转速、力矩等参数,实现对扭振的有效控制。
同时,还可以利用优化算法,对控制策略进行优化和改进,提高控制的效果和效率。
《考虑带材的轧机主传动系统扭振研究》

《考虑带材的轧机主传动系统扭振研究》篇一一、引言在现代金属轧制工业中,带材轧机作为关键设备,其主传动系统的稳定性和性能直接关系到产品质量和生产效率。
然而,在实际生产过程中,主传动系统常常面临扭振问题,这会对设备造成损害,降低生产效率,甚至影响产品质量。
因此,对轧机主传动系统的扭振进行研究,提出有效的控制措施,具有重要的现实意义。
二、轧机主传动系统概述轧机主传动系统主要由电机、减速器、工作辊道和联轴器等部分组成。
在轧制过程中,由于电机转速和工作辊道转速的不一致,以及轧制力的变化等因素,容易导致主传动系统产生扭振。
这种扭振会传递到整个设备,对设备的稳定性和使用寿命造成影响。
三、扭振产生的原因及影响1. 扭振产生的原因:轧机主传动系统扭振的产生主要与电机转速、工作辊道转速、轧制力、设备刚度等因素有关。
当这些因素发生变化时,会导致传动系统内部产生扭矩波动,进而引发扭振。
2. 扭振的影响:扭振会导致设备运行不稳定,增加设备的振动和噪音,降低设备的使用寿命。
同时,扭振还会影响产品的质量和生产效率,增加生产成本。
四、考虑带材的轧机主传动系统扭振研究针对考虑带材的轧机主传动系统扭振问题,可以从以下几个方面进行研究:1. 理论分析:通过建立主传动系统的数学模型,分析扭振产生的机理和影响因素。
这包括考虑带材的厚度、宽度、材质等因素对主传动系统的影响。
2. 实验研究:通过实验测试主传动系统的动态特性,包括扭振的频率、幅度和传播规律等。
这可以通过在实验室或实际生产线上进行实验来实现。
3. 控制系统设计:根据理论分析和实验结果,设计有效的控制系统来抑制主传动系统的扭振。
这包括设计合理的控制策略和算法,以及选择合适的执行机构和传感器等。
4. 优化设计:通过优化设计主传动系统的结构参数和材料性能等,提高设备的刚度和阻尼性能,从而减小扭振的产生。
这需要综合考虑设备的成本、可靠性、维护等因素。
5. 实际应用:将研究成果应用于实际生产中,验证其有效性和可行性。
《2024年考虑带材的轧机主传动系统扭振研究》范文

《考虑带材的轧机主传动系统扭振研究》篇一一、引言在金属带材轧制过程中,轧机主传动系统的扭振问题是一个重要的研究领域。
扭振不仅影响轧机的稳定运行,还可能对带材的质量和精度造成影响。
因此,对轧机主传动系统的扭振进行深入研究具有重要的实际意义。
本文将重点研究考虑带材因素的轧机主传动系统扭振问题,分析其产生的原因及影响因素,提出相应的控制策略,以期为实际生产提供理论支持。
二、轧机主传动系统扭振的产生原因及影响因素1. 产生原因轧机主传动系统的扭振主要由电机与轧机之间的转速波动、轧制力的变化、带材的物理特性等因素引起。
在轧制过程中,由于电机与轧机之间的转速差异、轧制力的不稳定以及带材的弹性变形等因素,使得传动系统产生扭振。
2. 影响因素(1)电机与轧机之间的匹配程度:电机与轧机之间的转速差异是导致扭振的主要原因之一。
因此,电机与轧机的匹配程度对扭振的影响较大。
(2)轧制力:轧制力的变化会引起带材的变形,进而影响传动系统的稳定性,导致扭振的产生。
(3)带材的物理特性:带材的厚度、宽度、硬度等物理特性对轧机主传动系统的扭振也有一定影响。
例如,硬度较高的带材在轧制过程中更容易引起扭振。
三、考虑带材因素的轧机主传动系统扭振分析1. 带材厚度对扭振的影响带材厚度越大,其抵抗变形的能力越强,从而对传动系统的扭振产生一定的影响。
较厚的带材在轧制过程中需要更大的轧制力,容易使传动系统产生更大的扭振。
2. 带材宽度对扭振的影响带材宽度对扭振的影响主要表现在宽度方向上的力矩变化。
较宽的带材在轧制过程中需要更大的力矩来保持稳定,这可能导致传动系统产生更大的扭振。
3. 带材硬度对扭振的影响带材硬度越高,其抵抗变形的能力越强,从而使得轧制过程中产生的力矩变化更大,容易导致传动系统产生扭振。
四、控制策略及措施1. 优化电机与轧机的匹配程度:通过改进电机与轧机的匹配程度,减小转速差异,从而降低扭振的产生。
2. 调整轧制力:通过调整轧制力的大小和分布,使带材在轧制过程中保持稳定,从而减小扭振的产生。
《考虑带材的轧机主传动系统扭振研究》范文

《考虑带材的轧机主传动系统扭振研究》篇一一、引言在现代金属轧制工业中,带材轧机主传动系统的扭振问题已经成为一个亟待解决的技术难题。
由于轧制过程中涉及到的多种复杂因素,如轧制力、轧制速度、带材张力等,这些因素都会对主传动系统的扭振产生影响。
本文将就考虑带材的轧机主传动系统扭振进行研究,以期为相关领域的技术人员提供有益的参考。
二、带材轧机主传动系统扭振问题的重要性扭振问题在带材轧机主传动系统中具有显著的影响。
首先,扭振会导致传动系统的振动和噪声,影响设备的正常运行和寿命。
其次,扭振还会影响带材的轧制质量,如产生皱纹、波浪等表面缺陷。
最后,扭振问题还可能引发设备故障,增加生产成本和维修成本。
因此,对带材轧机主传动系统扭振的研究具有重要的实际意义。
三、带材对主传动系统扭振的影响带材对轧机主传动系统扭振的影响主要体现在以下几个方面:1. 带材的物理特性(如厚度、宽度、强度等)会直接影响轧制过程中的力传递和扭矩分布,从而影响主传动系统的扭振。
2. 带材的张力是影响扭振的重要因素。
当带材张力过大或过小时,都会导致主传动系统的扭振加剧。
3. 轧制速度和轧制力的变化也会对主传动系统的扭振产生影响。
当这些参数发生波动时,会引发主传动系统的动态响应,从而导致扭振的产生。
四、轧机主传动系统扭振的研究方法针对轧机主传动系统的扭振问题,可以采用以下研究方法:1. 理论分析:通过建立主传动系统的动力学模型,分析其扭振产生的机理和影响因素。
2. 实验研究:通过实际轧制过程中的数据采集和分析,研究主传动系统的扭振特性和规律。
3. 数值模拟:利用有限元分析等方法,对主传动系统的扭振进行数值模拟和预测。
五、研究内容及结果本研究以某带材轧机为研究对象,通过理论分析、实验研究和数值模拟等方法,对主传动系统的扭振进行了深入研究。
结果表明:1. 带材的物理特性、张力、轧制速度和轧制力等因素都会对主传动系统的扭振产生影响。
2. 通过优化带材的物理特性和张力控制,可以有效降低主传动系统的扭振。
轧机主传动电机振动故障处理_wgjs详述

一起轧钢主传动电机振动故障处理经过的回顾丁学杰1陶桂林(武汉钢铁集团公司热轧厂430083 武汉)摘要振动是电机的常见故障之一,本文结合我厂一起轧钢主传动电机振动故障的处理经过,对电机振动故障的分析方法和处理经验进行了总结。
关键词轧钢电机振动故障轧钢主传动电机是钢铁企业的关键动力设备,其运行状态的好坏不仅关系到产品质量的好坏,还关系到钢铁企业的生产效益能否实现。
随着冶金自动化水平的提高,钢铁企业对生产的连续性和设备的稳定性都提出了很高的要求。
作为钢厂核心设备的的轧机出现任何非正常停机都将造成重大的经济损失。
我厂的R2初轧机是一台由双电机驱动的可逆轧机,上下轧辊电机的容量和驱动控制结构完全相同。
××年7月,R2轧机的上辊电机出现异常振动和巨大响声,同时伴有整流子打火等异常现象。
本文将介绍这起电机振动故障的特点,以及故障分析和处理的前后经过。
1电机基本情况与振动故障的特点R2轧机的两台驱动电机均由日本东芝公司于1975年制造,故障出现前电机一直正常运行。
该电机设计容量5000kW,电枢额定电压:750V,额定电流:7250A,励磁电压:500V,励磁电流:307A,额定转矩:122kN.m,额定转速:40r/min,最大转速65 r/min,电机极数:18,轧机的传动系统如图1所示。
图1 电机与轧辊联接示意图××年7月在电机日常巡检时发现,R2轧机在轧钢时上辊传动系统出现异常的振动和巨大的响声。
进一步观察还发现,电机转子存在较明显的轴向窜动、同时伴随整流子打火等异常现象。
凭经验,这是轧机系统出现的较为严重的振动故障。
由于电机与轧辊之间的传动机构较多,故障出在轧机传动机构还是电机本身一时难以判断。
为迅速找到振动根源,我们多方面入手,对引起轧机系统振动的因素进行了排查。
1作者简介:丁学杰,1961~,湖北武汉人,高级工程师2轧机系统振动故障的排查引起轧机系统振动的原因很多,文献[1~3]显示轧机本身的机械系统、电机的机械结构的、电机的电磁性能改变、以及电机基础性状的变化都有可能造成轧机系统的振动。
- 1、下载文档前请自行甄别文档内容的完整性,平台不提供额外的编辑、内容补充、找答案等附加服务。
- 2、"仅部分预览"的文档,不可在线预览部分如存在完整性等问题,可反馈申请退款(可完整预览的文档不适用该条件!)。
- 3、如文档侵犯您的权益,请联系客服反馈,我们会尽快为您处理(人工客服工作时间:9:00-18:30)。
!" 上 辊 电 动 机 轴 扭 矩 ; #" 上 辊 电动机电流 ( $) ;," 下辊电动机 轴扭矩;%" 下辊电动机电流($) ; (’ ( )*+) &" 转速
轧制过程中产生的冲击载荷激起的主传动系统的动态响应 取决于结构特性, 即主传动系统的惯性分布和弹性分布、 系统的 衰减特性和间隙等; 同时也取决与轧制条件, 如轧件材料、 轧件 与轧辊的速度差和轧件的粗糙度等。一般情况下,热轧带钢精 轧机不发生异常扭矩, 厚板轧机有异常扭矩, 初轧机常因各种原 因发生特别大的扭矩。
++++++++++++++++++++++++++++++++++++++++, +++++++++++++++++++++++++++++++++++++++++++++++++++++++++++++++++++++++++++++++++++++++++++++, ++++++++++++++++++++++++++++++++++++++++,
图 ! $"" 轧机列传动示意图 !A 主电机;@A 主传动轴;#A 齿轮箱;BA 三辊轧机
@ 扭矩的测量及计算
以抚顺特殊钢公司的 $"" 轧机为例进行扭矩的测量 -@., 图 ! 为 $"" 轧机列传动示意图。
@A ! 轧制力矩的测量
监测轧钢机的轧制力矩时需要使用力矩传感器, 而一般的
% 来稿日期: @""# G !@ G @H
诊断与控制系统 % 扭振故障监测、
轧钢机的状态监测、 故障诊断和控制系统中, 状态监测是前 提, 故障诊断是结果, 故障预防与控制是目的, 各系统间关系如 图 > 所示。 扭振的控制应在设计轧钢机时就加以考虑,要进行结构的 (质量 ) 动力优化设计, 以控制扭振为目标选择最佳的惯性 和弹 (刚度 ) 簧 的配置。在强度设计中要确定各部件的最合理的安全 系数。特别是要处理好整个主传动系统的共振问题。对正在使 用的轧钢机要控制能够产生扭振的各种因素,合理控制压下量 和咬入速度, 减轻咬入冲击, 加强轧件的温度管理及主传动系统 的反冲击问题。在轧钢机上安装轧制力矩在线监测系统,实现 扭矩超限报警是扭振监控的前提。
+ ,+
《机械设计与制造 》 @A+" #--%
42" ,
/BCD*+E’F
GEH*I+
J
/B+AKBCLA’E
测试了三个钢种, 两种规格十根轧件。 其中 #-.’/+0* 三根, 坯 !&- )),成品 !1&))" %-.’/+/2 二根,坯 !&- )),成品
# #
9 ! ; 设计上的冲击和过载荷因素。它包括两个方面, 一是机 (属于扭转刚性分布上的因素 ) 械构造上的过载荷因素 ; 二是由 主电动机速度控制造成的冲击因素。 9 # ; 维修上的冲击和过载荷因素。它包括由主传动系统间 隙、造成的过载荷因素及由上下轧辊扭矩不平衡造成的过载荷 因素。 9 , ; 操作上的冲击和过载荷因素。它包括的因素较多, 主要 (咬入速度因素及轧件头部形状 有: 由咬入速度造成的冲击因素 (咬入前, 因素 ) ; 由咬入时的轧辊和轧制速度差造成的冲击因素 轧件速度不适当造成的因素及咬入前,轧辊圆周速度不适当造 成的因素 ) ; 由轧件头部温度降低造成的过载荷; 由上下轧辊扭 (由轧件上下面温度差造成的过载荷、 矩不平衡造成的过载荷 由 轧件的弯曲造成的过载荷以及在立辊轧机上由于侧导板未对准 轧制中心线造成的过载荷 ) ; 误操作产生的压下量设定过大。 轧制时各种轧钢机在发生扭振时的扭矩曲线图形如图 % 、 其中图 % 是咬钢时发生的异常扭矩, 图 & 是轧制过程 图 & 所示。 中发生的异常扭矩。
* 是轧辊直径, * 取 !&%-)), ’ 为轧辊轴颈直径, ’ 7 ,--))," 为轧辊轴承摩擦系数,取 -" -# ,$( 是驱动一个轧辊 的力矩。扭矩 $ 的计算结果见表 ! 。 利用上述原理及方法,计算出的数据与力矩传感器测量出 的数据接近, 所以公式 9 ! ; 可作为轧制力矩的数学模型, 实际上 完全可以达到扭振长期在线监测轧制力矩的目的。
表 ! 扭矩的计算和测量结果
(< ) 压下量 ())) 道次 钢温 计算扭矩 $ 9 =4・ ) ; 测量扭矩 # 9 =4・ ) ; 误差 ! !-&!1" & &#&" 1 &&3" , >? # !-&!-" & &-!" % &,>" 5 1? , !-!3" %1#" # %15" & !? % !--1" %13" > &--" 5 &? & 531" # &!-" 3 &,&" & &? > 5,%" 3 >-5" 5 >#5" 1 ,? 1 5,#" > ,,-" > ,%1" & &?
! 前言
随着轧钢设备的发展,轧制速度不断提高,主电机容量不 断增大,轧钢机安全可靠地运行在生产中占有极为重要的地 位。从结构动力学角度来看,主电机拖动轧钢机一般都通过电 动机的输出轴、 联轴器、 中间轴及齿轮座驱动轧辊的方式, 这个 主传动传统可以看成是由刚性圆盘和弹性体相结合的传动系 统,是一个扭振系统。在咬钢时受到冲击力作用或在轧制过程 中发生打滑等,因此从轧辊到主电机的轧机主传动系统经常发 生扭转振动, 剧烈的扭振导致轧钢设备的各种故障发生-!.。 由剧烈扭振造成的轧钢机故障在国内外许多钢铁企业都 发生过, 这些故障主要有轧辊断裂、 万向轴的扁头和虎口断裂、 联轴器损坏、 大人字齿轮断齿、 主电机生高片断裂、 电动机转轴 轴向串动使轴承座螺栓松动,甚至因万向轴断裂落下引起从电 动机到万向轴的主传动系统的严重破坏等。 轧制力矩是反映机器运行工况、进行扭振故障诊断的重要 参数之一,如对轧钢机工作状态和工艺状态进行长期的在线监 测,就必须对轧制力矩进行测量和计算。而国内目前还没有这 种大型的扭矩传感器,只有通过建立数学模型来实现对力能参 数进行在线监测。
图 , 引电装置示意图
#" # 轧制力矩的计算
轧机轧制过程相当于简单轧制。略去空转力矩及动力矩。 实测处的扭矩为轧制力矩与摩擦力矩之和。 即 $ 7 # $( 7 ) 9 * ( # : "’ ; (! )
图 % 咬钢时产生的异常扭矩
!" 上辊电动机轴扭矩;#" 上辊电 动机电流 ($) ;#" 下辊电动机轴 扭 矩 ;%" 下 辊 电 动 机 电 流 ( $ ) ; (’ ( )*+) &" 转速
+++++++++++++++++++++++++++++++++++++++++++++++++++++++++++++++++++++++++++++++++++++++++++++,
力矩传感器都要解体主传动系统的连接轴,这往往是现场所不 允许的。因而采用间接监测方法,建立适合于轧钢机的数学模 型, 以达到间接监测轧制力矩而不改变轧机内部和外部结构。 这 是以微电子技术对传统轧钢工业的改进和创新,利用电参数来 长期监测轧制力矩, 并适合多种类型轧机 C # D 。 轧机轧制力矩测试点选在齿轮座与减速机之间, 具有转速较 低, 转动平稳, 信号引出滑环易于安装, 输出力矩大, 测试信号比 较灵敏等特点。 采用由电阻应变片作为敏感元件构成力矩传感器 来测量轧制力矩, 贴片位置和接桥 E 全桥 F 方式如图 ! 所示。 由于被测对象是旋转体,贴好的应变片无法与信号的传输 电缆直接相连。 为此, 设计一套能够传送电阻应变片的电阻变化 滑环由绝缘性能好的材料制成。 滑环 率的引电装置如图 @ 所示。 将滑环固结在旋转轴上随其转动, 应变片组 B 条槽内镶有铜环, 桥后的 B 条线与铜环相连, 铜编线与支架上绝缘弹簧相连, 用一 根四芯屏蔽电缆与铜编线相连,另一端接入动态电阻应变仪的 接线柱上。安装方便, 信号明确。