非常好的DFMEA学习资料
DFMEA培训资料PPT可编辑

效應 度
失 效 度 管制
現行檢 難 風險 建議 負責
執行結果
測設計 管制
檢 度
優先 數
措施
人與 日期
采行 措施
S
O
D RPN
设计FMEA填写说明
(1)FMEA编号:填入FMEA文件编号,以便可以追踪使用。 (2)系统、子系统及零组件:指示合适的分析等级,并填入系统、子系统或零件名称或零件名称
和编号。 (3)设计责任者:填入OEM、部门和小组,也包括供货商名称。 (4)准备者:填入准备FMEA责任工程师的姓名、电话号码、公司。 A.系统FMEA范围:
3.必要之处采用可靠性高之零组件
2.开发阶段
1.明确把握失效原因,并实施适当的改善
2.零件安全之宽放确认
3.寿命、性能、强度等之确认
3.制造阶段
1.活用工程设计,进而改善制程上之弱点
2.利用FMEA之过程制订必要之制程标准
4.客户抱怨阶段 1.不同之环境产生之失效,以FMEA克服
2.不同之使用法产生之失效,以FMEA克服
FMEA之演变
1.FMECA为FMEA之前身,系在1950由格鲁曼飞机提出,用在飞机主控系统的失效分 析。
2.波音与马丁公司在1957年正式编订FMEA的作业程序,列在其工程手册中。 3.60年代初期,美太空总署将FMECA成功的应用于太控计划。美军同时也开始应用
FMECA技术,并于1974年出版MIL-STD-1629 FMECA作业程序。 4.1980年修改为MIL-STD-1629A,延用至今 5.1985由国际电工委员会(IEC)出版之FMECA国际标准(IEC812),即参考MIL-STD-1629A
设计FMEA之目的
1.帮助设计需求与设计方案的评估。 2.帮助初始设计对制造和装配的需求。 3.在设计发展阶段,增加失效模式和系统效应分析的次数。 4.提供另一项分析信息,帮助设计验证之规划。 5.根据对顾客需求的影响性,列出失效模式的排序,并按序改善。 6.提供一项改善方案,可以减少矫正与追查的活动。 7.提供更好的参考数据,协助现场解决问题,评估设计变更和发展更进一步的设计。
《DFMEA培训资料》课件OK

在明确分析对象后,需要确定分析的目标,包括识别潜在的故障模式、评估故障对系统的影响等。
收集相关资料和信息
收集相关资料
在进行DFMEA分析前,需要收集与对象 相关的各种资料,包括技术文档、设计图 纸、流程图等。
VS
收集相关信息
除了对象本身的资料,还需要收集与对象 相关的其他信息,如用户反馈、行业标准 等。
03
结合其他工具和方法
DFMEA可以结合其他工具和方法,如DOE、FMEA、田口方法等,形
成更加全面和系统的质量管理体系,提高产品质量和生产效率。
06
参考文献和附录
参考文献
参考文献1
作者1,书名1,出版社1,出 版年份1
参考文献2
作者2,书名2,出版社2,出版年 份2
参考文献3
作者3,书名3,出版社3,出版年 份3
4. 识别潜在失效模式
根据收集的信息,识别出可能导致产品失效的各种模式。
5. 分析失效影响
分析每个潜在失效模式对产品功能和使用的影响。
DFMEA的流程
6. 评估风险优先级:根据失效影响 的重要性、发生的频率和可检测性 ,确定潜在失效模式的优先级。
8. 形成报告:将分析结果整理成报 告,包括潜在失效模式、失效影响 、优先级和改进措施等。
《dfmea培训资料》课件 ok
2023-10-31
contents
目录
• 什么是DFMEA? • DFMEA的流程和工具 • 如何进行DFMEA分析 • DFMEA的案例分析 • DFMEA的总结和展望 • 参考文献和附录
01
什么是DFMEA?
DFMEA的定义
DFMEA是Design Failure Mode and Effects Analysis的缩 写,中文意思是设计失效模式与影响分析。
DFMEA学习资料

DFMEA学习资料第三版前⾔FMEA第三版(QS-9000)戴姆勒克莱斯勒、福特和通⽤汽车公司供⽅使⽤的参考⼿册,将其作为指南,在进⾏设计FMEA和过程FMEA开发中提供帮助。
本参考⼿册旨在澄清与FMEA开发相关的技术问题。
本参考⼿册考⼿册与供⽅质量要求特别⼯作组的约定相⼀致,即将戴姆勒克莱斯勒、福特和通⽤汽车公司供⽅使⽤的参考⼿册、程序、报告格式及技术术语标准化。
因此,FMEA第三版是为供⽅提供指南⽽编写的。
⼿册中未规定要求,⽽是对覆盖设计阶段或过程分析阶段进⾏FMEA时通常出现的各种情形提供了通⽤性指南。
本⼿册在技术上等效于SAE J1739关于设计FMEA和过程FMEA的标准,但不包括设备FMEA的应⽤。
对设备FMEA感兴趣者可以参考SAE J1739的有关⽰例。
供⽅质量要求特别⼯作组感谢以下各位及其所在的公司。
在FMEA⼿册第三版或以前各版的编写过程中,他们倾注了⼤量的时间和精⼒。
第三版Kevin A. Lange - 戴姆勒克莱斯勒Steven C. Leggett - 通⽤Beth Baker – AIAG以前各版Howard Riley - 戴姆勒克莱斯勒 Mark T. Wrobbel - 戴姆勒克莱斯勒George R. Baumgartner - 福特 Rebecca French - 通⽤Lawrence R. Mccullen - 通⽤ Mary Ann Raymond - BoschRobert A. May – Goodyear William Ireland –Kelsey-Hayes Tripp Martin – Peterson Spring此外,供⽅质量要求特别⼯作组还要感谢以下SAE J1739⼯作组的各位,他们在此版⼿册的技术变更和改进⽅⾯提供的⼤⼒⽀持。
William D. Carlson -戴姆勒克莱斯勒Glen R. Vallance -福特Carl S. Carlson -通⽤本⼿册的版权归戴姆勒克莱斯勒、福特和通⽤汽车公司所有。
DFMEA培训资料
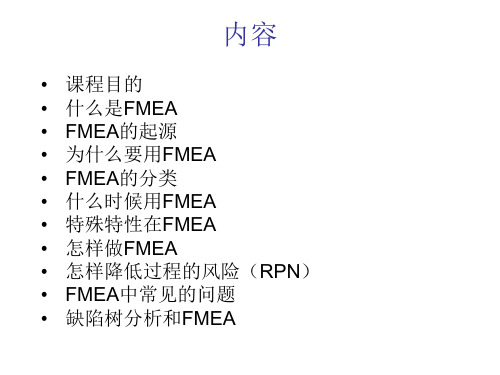
怎样用FMEA评估过程的风险?
• 失效模式的不可探测度 (D)
•用 D(不可探测度 )来表示产品的缺陷 的被发现的可能性。 D最小为1, 最大是 10。D越大,产品的缺陷越难以被探测到 的可能性越小。
怎样做PFMEA?
1. 成立一个跨部门的小组
• 制造(工艺)工程师
一般是组长
• 设备工程师
• 设计工程师
• 品质工程师
• 生产工程师/主管
• 可靠性工程师
• 工业工程师
• 等。。。
在开始FMEA前,把小组的人员先写 在FMEA表格的上边。
怎样做PFMEA?
2. 定义所涉及的产品的特殊特性:
•客户图纸 •规格书 •等。。
必要时应与客户沟通,以确保领会客户的 要求。
练习 1
– 一般通过FMEA评估产生,由制造商自己指定。
• 产品和过程的特殊特性都应当包含在控制 计划中。
Characteristics I
Characteristics II
Characteristics III
Characteristics IV
Characteristics V
怎样用FMEA评估过程的风险?
来自DFMEA中的 与DFMEA相同的后 对过程失效
问题的原因
果
模式的特定
的根本原因
三种 FMEA之间的关系
DFMEA工具培训学习课件

培养专业的DFMEA工程师
DFMEA工具的应用需要具备一定的专业知识和技能,因此需要培养一批具备专业知识和 实践经验的DFMEA工程师,以提高我国制造业的可靠性水平。
DFMEA工具的优缺点
优点
DFMEA工具能够帮助产品设计团队系统地分析产品设计的故障模式和潜在风险 ,并能够提出相应的改进措施,提高产品的可靠性和安全性。
缺点
DFMEA工具的应用需要一定的培训和学习成本,而且其分析过程相对繁琐,需 要投入较多的时间和精力。此外,DFMEA工具只能对产品设计中的故障模式进 行分析,而不能对制造、装配等其他环节的问题进行全面评估。
于更高效地进行分析。
如何保证DFMEA工具的质量
确认数据准确性
对于输入的数据,需要确认其来源和准确性,避免误导分析结 果。
对比分析
针对不同的分析结果,可以进行对比分析,找出差异并进一步 确认最佳方案。
充分考虑各方需求
在分析过程中,需要充分了解和考虑各方的需求和意见,以确 保分析结果具有实际应用价值。
DFMEA工具的历史 和发展
DFMEA起源于20世纪70年代的 美国国防工业,后来逐渐推广到 其他领域,如汽车、电子、医疗 等。
DFMEA工具的应用 流程
DFMEA工具的应用流程包括策 划、潜在故障模式分析、故障模 式影响分析、风险优先度计算、 制定改进措施等步骤。
DFMEA工具的应用案例
通过案例分析,学习如何运用 DFMEA工具进行系统或过程的 故障模式分析,包括故障模式的 识别、影响分析、风险评估等。
如何与其他工具集成使用DFMEA
DFMEA-培训教材(共40张)

推荐(tuījiàn)的DFMEA严重评价准则(参考)
后果(影响)
无警告的严重危害
有警告的严重危害
很大 大
中等
小 很小 轻微 很轻微
无
平分标准 在没有任何征兆的情况下发生的,影响使用安全或违反有关法律法规 的极其严重的故障模式
在有征兆的情况下发生的,影响使用安全或违反有关法律法规的极其 严重的故障模式
• 以其最严密的形式总結了设计一个零部件、子系统 或系统时,工程师/小组的设计思想 • 在最大范围內保证已充份的考虑到并指明潜在失效 模式及与其相关的后果起因/机理
• 在任何设计过程中正常经历的思维过程是一致的,并使 之规范化
第21页,共40页。
DFMEA的目的(mùdì)
✓ 评价对制造、装配、服务、回收要求所作的最初设计 ✓ 提高在设计/开发过程中已考虑潜在失效模式及其对系统和产品运行
主要目的:筛选着重点!
第12页,共40页。
FMEA 小组的守则
• 决定前召开小组会议 • 决定谁将参加
• 预先准备议题
• 主张进行会议笔记或记录(jìlù)
• 建立基本准则
• 遵守事先的议程
• 评价会议
• 不允许中断
成功的FMEA 小组
•控制方向和焦点
•建立自身的统一性
•负责并使用测量方法 •有全体的支持
频 度 数
现行设 计控制
预探 防测
不 易 探 测 度 数
D
风 险 顺 序 数 R
P
N
建议 措施
责任 和目 标完 成日
期
功能
(gōn
gné
ng)、
特征或 要求
后果 是什 么
会有什么问题 •无功能 •部分功能
《DFMEA培训资料》课件OK

未来,DFMEA将更加注重系统性的分析和全面的故障 覆盖,以避免遗漏潜在的设计问题。
同时,DFMEA也将更加关注跨学科的交流和合作,以 促进不同领域之间的知识共享和创新思维。
THANKS
感谢观看
3
分析对象的重要性划分
根据分析对象对产品性能和安全性的影响程度 ,将其划分为不同等级。
dfmea步骤3:梳理产品结构
产品结构的梳理
01
根据分析对级划分
02
根据产品结构的复杂程度,将其划分为不同的层级,便于后续
的分析和建模。
产品结构的属性定义
03
针对每个组件和子系统,定义其属性,包括功能、接口、材料
和制造工艺等。
dfmea步骤4:绘制故障树
确定故障类型
根据产品实际情况,确定需要分析的故障 类型,包括功能故障、接口故障等。
进行定量分析
对故障树进行定量分析,计算系统故障概 率和重要度指标,评估现有控制措施的有 效性。
建立故障树模型
以分析对象为核心,建立故障树模型,将 故障类型逐层分解到基础事件。
详细描述:DFMEA分析结果应该用来反馈和优化设计 ,可以采用以下方法 根据故障模式和影响分析,优化组件和子系统设计
调整设计参数以优化性能、成本或可维护性
05
dfmea总结与展望
dfmea总结
DFMEA是一种系统化的故障模式与影响分析方法,用 于识别、评估和解决潜在的设计问题。
DFMEA的流程包括组建团队、分析故障模式和影响、 编制和评估风险矩阵、制定改进措施。
详细描述
航空航天行业的产品开发和制造过程中,需要考虑众多因素,如高温、低温、压 力等。dfmea的应用可以帮助企业系统地分析产品的潜在风险,提高产品的可靠 性和安全性,避免潜在的故障和安全隐患。
DFMEA培训资料

DFMEA培训资料一、DFMEA 简介DFMEA,即设计失效模式及后果分析(Design Failure Mode and Effects Analysis),是在产品设计阶段,用于识别潜在的失效模式及其可能产生的后果,并采取预防措施以降低风险的一种工具。
DFMEA 的目的是在产品设计过程中,通过系统的分析,提前识别可能出现的问题,从而在设计阶段就采取措施进行改进,以提高产品的质量、可靠性和安全性,降低成本,缩短开发周期。
二、DFMEA 的实施步骤1、确定分析的对象和范围明确要分析的产品或系统。
界定分析的边界和功能。
2、组建团队包括设计工程师、工艺工程师、质量工程师、售后工程师等相关人员。
确保团队成员具备相关的知识和经验。
3、收集相关信息产品的技术要求和规范。
类似产品的失效案例和经验教训。
客户的需求和期望。
4、识别潜在的失效模式从功能、性能、可靠性等方面考虑。
采用头脑风暴等方法,尽可能全面地列出可能的失效模式。
5、分析失效的原因深入探究导致失效模式发生的根本原因。
可以使用因果图、5Why 等工具。
6、评估失效的影响对产品的功能、性能、安全性、客户满意度等方面的影响。
确定影响的严重程度(S),通常采用 1 10 的评分标准。
7、评估失效发生的可能性考虑设计控制措施的有效性。
确定发生的频率(O),评分标准 1 10。
8、评估检测失效的难易程度现有检测手段的有效性。
确定检测度(D),评分 1 10。
9、计算风险优先数(RPN)RPN = S × O × D根据 RPN 值的大小,确定优先改进的项目。
10、制定改进措施针对高 RPN 值的失效模式制定相应的改进措施。
明确责任人和完成时间。
11、重新评估风险实施改进措施后,重新计算 RPN 值,评估改进效果。
三、DFMEA 中的关键概念1、失效模式产品或系统不能满足设计要求或预期功能的表现形式。
例如:零件断裂、功能失效、尺寸超差等。
2、失效原因导致失效模式发生的因素。
- 1、下载文档前请自行甄别文档内容的完整性,平台不提供额外的编辑、内容补充、找答案等附加服务。
- 2、"仅部分预览"的文档,不可在线预览部分如存在完整性等问题,可反馈申请退款(可完整预览的文档不适用该条件!)。
- 3、如文档侵犯您的权益,请联系客服反馈,我们会尽快为您处理(人工客服工作时间:9:00-18:30)。
9
2.过程FMEA的益处
· 帮助确认已列出的与产品相关的过程失效模式及它们的后果; · 指明相应的起因/机理; · 指明降低或消除失效出现的机会的措施; · 指明潜在的制造或装配过程失效的原因; · 指明过程变差,如果受控,可降低失效出现的频度或提高失效的探测度; · 帮助对纠正措施进行优先排序; · 对类似的制造过程是有用的参考; · 过程FMEA的实施记录。
潜在失效模式及后果分析 FMEA
Failure Mode and Effects Analysis
主讲:
1第一章Biblioteka 概论•什么是FMEA? •FMEA的历史 •为什么要进行FMEA? •由谁来做FMEA? •何时做FMEA? •SFMEA/DFMEA与PFMEA的关系? •小组练习
2
1
什么是FMEA ?
行方法。 探测度:失效模式/起因一旦发生,能否探测得出?
7
FMEA基本要素的组成部分 FMEA计划
原因
失效模式
后果
频度
探测度
严重度
风险分析和潜在的失效模式及后果分析解释 执行建议措施并验证其有效性 实施措施
8
4
主要概念:水箱支架举例
原原因因 ((频频度度))
失失效效模模式式
后后果果 ((严严重重度度))
20
10
八、FMEA的分析时机
为达到最佳效益,FMEA必须在设计或过程失效模式被无意地纳入设计 产品之前进行。事先花时间进行FMEA分析,能够容易并低成本地对产 品或过程进行修改,从而减少事后修改的损失。 1.什么时候做DFMEA? · 开始于一个设计概念最终形成之时或之前; - 设计方案初步确定时应该开始FMEA初稿的编制 - FMEA作为设计活动的一部分,应该在设计任务完成(如设计图样完 成)之时完成FMEA工作; - 产品开发各阶段、设计发生变化、获得有关信息时,对FMEA的初稿 进行评审,不断进行修改; - FMEA是一个动态的文件
14
7
四、FMEA的目的
· 发现、评价产品或过程中潜在的失效与可能的后果,找出能够避免或减少这 些潜在失效发生的措施,将上述过程文件化。 —提高质量、可靠性和安全性。 —针对失效可能产生和各方面原因一个过程、设计或服务 —持续地减少失效的频度或持续地减少失效的后果。 —防止现有的/潜在的失效到达顾客处。 —失效的风险顺序量化以引导采取措施。 —优先使用行政的和工程的努力、时间、人力资源和其他资源。 —运用团队原则和持续改进方法以获得好的产品。
11
x 1993年2月美国三大汽车公司联合编写了FMEA手册,并正式出版 作为QS-9000质量体系要求文件的参考手册之一,1995年2月出版 了第2版,2001年7月了第3版,已由中国汽车技术研究中心翻译成中 文。 x 1994年,美国汽车工程师学会SAE发布了SAEJ1739–潜在失效模 式及后果分析标准。 x FMEA还被广泛应用于其他行业,如粮食、卫生、运输、燃气等部 门。 x 2001年,SAEJ1739修订,FMEA手册也修订为第三版,并已译成 中文。
获得顾客需求输入
DFMEA
PFMEA
更新PFMEA 控制计划 反应计划
过程怎样改 变
控制计划
PFMEA
过程变量
数据收集
进行适当的比较
不
过程改 变了吗?
是
确认/产品或服务的质 量
反应计划
29
十三、FMEA与控制计划
21
2.什么时候做PFMEA
· 开始于可行性阶段之前或过程中,在工装制造之前; - PFMEA在过程设计任务(如过程设计文件)完成之时完成; - PFMEA是一个动态的文件
22
11
九、SFMEA DFMEA与PFMEA关系
· 产品设计部门的下一道工序是过程设计,产品设计应充分考虑可制造 与可装配性问题,由于产品设计中没有适当考虑制造中的技术与操作者 体力的限制,可能造成制造失效模式的发生;
· PPAP - 第1部分 1.2.2.4 - 第2部分 1.2.2.6
27
十一、FMEA同GB/T 18305 idt ISO/TS 16949的关系
GB/T 18305 idt ISO/TS 16949:1999有关条款 -4.2.4.4多方论证方法 -4.2.4.5工具和技术 -4.2.4.9.2过程设计输入 -4.2.4.9.3过程设计输出 -4.4.2.2要求的技能
设计 问题
制造 问题 影响
现行测试
原因
现行控制 (CP)
25
FMEA 的时间顺序
DFMEA
PFMEA
概念
初始设计 设计完成 样件制造 设计/过程 生产开始 确认
DFMEA 开始早于过程,完成时间在早期的图样完成但任何工 具的制造开始之前
PFMEA 开始于基本的操作方法讨论完成时,完成时间早于生产 计划制定和生产批准之前
26
13
十、FMEA同QS—9000的关系
QS—9000有关条款 - 4.2.3.1产品质量先期策划 - 4.2.3.5 过程失效模式及后果分析 - 4.4.2 设计和开发的策划 - 4.4.5 设计输出 - 福特公司特殊要求、控制计划和失效模式及后果分析
· APQP - 第二章 产品设计和开发 2.1DFMEA;2.4设计评审 - 第三章 过程设计和开发 3.6 PFMEA
SFMEA
自SFMEA
的原因
PFMEA 问题产生的原因来自 和DFMEA相同的 详细的过程失效模
DFMEA
后果
式产生的原因
24
12
设计 FMEA
零件
系统/设计/过程FMEA的联系
功能/性能
失效 模式
影响
原因
现行控制 (DVP&R)
过程 FMEA
零件
过程
历史资料
保修 外部质量问题 内部质量问题
失效 模式
FTA(Failure Tree Analysis)是“由上至下”进行分析
13
潜在失效模式及后果分析与失效分析比较
失效分析
潜在的失效模式及后果分析
y失效已经产生 y核心:纠正 y诊断已知的失效 y指引的是开发和生产
y失效还未产生,可能发生、但不是一定要发生 y核心:预防 y评估风险和潜在失效模式的影响 y开始于产品设计和工艺开发活动之前 y指引贯穿整个产品周期
y 不平道路引起的 振动与车体扭转 y 设计中应力集中 y 支架的材质不符 合强度要求
水箱支架断裂
功能:支撑
探测
生产者 消费者
y水箱后倾 y水箱与风扇碰撞 y产生异响 y水箱冷却水管被 风扇刮伤 y水箱冷却液泄漏 y冷却系统过热 y发动机气缸损坏
9
y汽车停驶
一个潜在的失效事件的发生,如果没有采取或来不及采取或事实上不可能采取措施,而 使之引起下游系统或相关系统产生链锁失效事件,我们称之为“失效链”。
12
6
三、FMEA和FMA、FTA
x FMEA是一种事前行为; FMA(Failure Mode Analysis)是一种事后行为。 FMA是对产品/过程已经发生的失效模式分析其产生的原因,评估其后 果及采取纠正措施的一种活动。 类似项目的FMA是FMEA的重要的输入参考资料。 x FMEA是“由下至上”进行分析
17
六、FMEA的益处
1.设计FMEA的益处 · 帮助确认已列出的潜在失效模式及它们的后果; · 指明相应的起因/机理,降低或消除失效出现的机会的措施; · 辅助设计要求及方法的客观评价; · 辅助起草制造及装配设计的要求; · 增加在设计阶段就考虑失效模式及后果的可能性; · 辅助设计试验及开发项目; · 从顾客的观点出发对失效进行评定; · 对风险降低措施进行跟踪和记录; · 对未来的分析及设计是好的参考; · 记录设计FMEA的过程。
水箱支架断裂 水箱后倾
(1失效原因) (1失效模式)
(2失效原因)
水箱与风扇碰撞
(1失效后果) (2失效模式)
水箱冷却水管被风扇刮伤
(2失效后果) (3失效原因)
水箱冷却液泄漏
(3失效模式)
冷却系统过热
(3失效后果)
时间
发动机气缸损坏 汽车停驶
10
5
二、FMEA的历史
x 世界上首次采用FMEA这种概念与方法的是在20世纪60年代中期美 国的航天工业。 x 进入20世纪70年代,美国的海军和国防部相继应用推广这项技术, 并制订了有关的标准。 x 20世纪70年代后期FMEA被美国汽车工业界所引用,作为设计评审 的一种工具。
- 产品设计FMEA不能依靠过程检测作为控制措施; · PFMEA应将DFMEA作为重要的输入,对DFMEA中标明的特殊性也必 须在PFMEA中作为重点分析的内容。
23
FMEAs 的关联
失效模式
后果
原因
SFMEA
问题的分支
问题
问题产生的原因
DFMEA 问题产生的原因来自 准确的后果定义来 设计失效模式产生
19
七、由谁来做FMEA?
1.谁来做DFMEA? · 由负责设计的工程师/工程师小组制定 — 依靠小组的共同努力 — 组成一个包括设计、制造、装配、售后服务、质量及可靠性等方面 的专家小组。 — 吸收与设计有关的上游(如供方、材料、上一个相关系统设计师) 和下游(如下一个相关系统的设计师)的部门 — 对有专利权的设计,可由供方制定。 2.谁来做PFMEA? · 由负责制造的工程师/工程师小组制定; — 依靠小组的共同努力 — 负责的工程师应直接、主动地同有关部门联系,这些部门包括:装 配、制造、材料、质量、服务和供方,以及负责下一总成的部门。
4
2
2.FMEA特点
z 失效还未产生,可能发生、但不是一定要发生 z 时机:在设计或过程开发阶段前开始 z 合作:小组由各种有经验和专业知识的人构成 z FMEA分析的文件 ——记录专用表格 ——作为动态文件使用 ——按照过程/产品/服务寿命周期期间要求更改 z 核心:预防 z 对潜在失效模式的风险和后果进行评定 z 是持续进行的 — 指导贯穿整个过程、产品和服务周期 z 动态的、文件化的、系统的小组活动