电动汽车充电桩设计外文文献翻译最新译文
关于新能源充电管理系统的外文文献
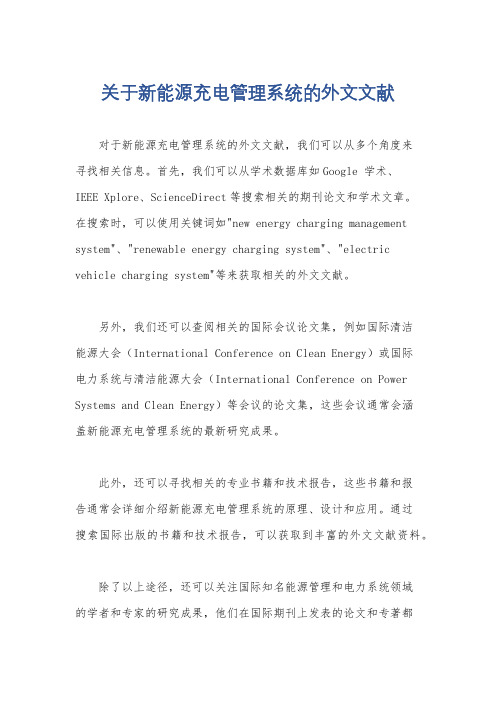
关于新能源充电管理系统的外文文献
对于新能源充电管理系统的外文文献,我们可以从多个角度来
寻找相关信息。
首先,我们可以从学术数据库如Google 学术、
IEEE Xplore、ScienceDirect等搜索相关的期刊论文和学术文章。
在搜索时,可以使用关键词如"new energy charging management system"、"renewable energy charging system"、"electric vehicle charging system"等来获取相关的外文文献。
另外,我们还可以查阅相关的国际会议论文集,例如国际清洁
能源大会(International Conference on Clean Energy)或国际
电力系统与清洁能源大会(International Conference on Power Systems and Clean Energy)等会议的论文集,这些会议通常会涵
盖新能源充电管理系统的最新研究成果。
此外,还可以寻找相关的专业书籍和技术报告,这些书籍和报
告通常会详细介绍新能源充电管理系统的原理、设计和应用。
通过
搜索国际出版的书籍和技术报告,可以获取到丰富的外文文献资料。
除了以上途径,还可以关注国际知名能源管理和电力系统领域
的学者和专家的研究成果,他们在国际期刊上发表的论文和专著都
是宝贵的外文文献资源。
总的来说,要全面了解新能源充电管理系统的外文文献,我们需要充分利用学术数据库、国际会议论文集、专业书籍和技术报告等多种渠道,从不同的角度获取相关信息,以便全面深入地了解该领域的最新研究成果和发展动态。
电动汽车充电系统及控制器外文文献翻译最新译文

文献出处:Pollet G. The research of electric car charging system and controller [J]. Electrochimica Acta, 2015, 5(3): 235-249.原文The research of electric car charging system and controllerPollet GAbstractThis paper puts forward the whole bridge main circuit topology and PWM control method effectively improves the reliability of the charging system and efficiency. Put forward and realized based on digital signal processing chip controller circuit intelligent PI control algorithm and variable parameters, significantly improve the control precision of the charging system voltage, current and response characteristics. Double proposes a CAN bus and RS - 485 bus communication network, realized the distributed control of the process of charging, the charging operation is flexible and reliable. Due to be able to provide a communication interface to battery management system and algorithm, charging system according to the state change of battery charging mode, optimizing the charging mode. The success of the charging system has important theoretical significance and engineering value. Keywords: Electric cars; Charging system, PWM, Intelligent PI, Distributed control 1 IntroductionElectric car, it is all or part of the electric drive system of power car, compared with conventional cars powered by gasoline as, electric cars in such aspects as environmental protection, clean, energy-saving occupy obvious advantages. Now each big international automobile manufacturer have invested a lot of money and manpower to electric car research and development, a variety of the electric car prototype appeared frequently, some have reached high industrialization scale. Now the development of the electric car industry has formed a hybrid vehicles, pure battery-powered electric vehicles (electric cars) and three main direction of fuel cell electric vehicles. Pure electric vehicle itself is not harmful gas emissions, can make full use of surplus power in the evening, improve the efficiency of energy utilization, and improve the economic benefit. Pure electric vehicles completely eliminateemissions of the vehicle running, fully use of secondary energy electricity, in line with the energy sustainable utilization strategy, along with the progress of the technical level, the pure electric vehicles has a broad development prospects. But at present, the development of the battery and charging system can't satisfy the requirement of electric cars, there are some theoretical and technical problems have yet to be research, serious lack of relevant standards and norms, has become the bottleneck of affecting the development of electric vehicles.2 The current situation of the electric vehicle charging systemAt the beginning of last century, as the secondary battery research is successful, and matching charging system arises at the historic moment. The charging system using the conventional charging method, which is USES small current for a long time to recharge battery. This way of charge due to the charging time is too long, can not meet the requirement of the electric cars and so on, the demand of the quick charge. Widely at home and abroad to carry out the study of fast charging system. Fast charging system produce roughly experienced three stages of development:(l) Groping stageIs the earliest in the 50 s of the last century, the United States as a result of the need of military, began to study fast charging technology, made the metal rectifying shape fast charging system, for 6 to 24 v lead-acid battery quick charging, the weight of 40 kg, have fast, medium and slow three charging modes.(2) The theory research stage1967 U.S. troops (Mas) have bubbles in the process of charging is studied, find the reason and law of gas, on the premise of minimum gas rate and find out the maximum charging current of battery can accept and acceptable charging current curve, discusses the theory of quick charge battery, and on the basis of practice, put forward the basic rules of quick charge battery.(3) The practical application stageMcCulloch electronic companies in the United States in 1970 made the lead-acid battery quick charging system, for 500A to 190AH battery charging current, and in 1200A discharge to deal with the polarization current for short periods of time, theresults 30 minutes to put the battery is good. In addition to the United States, such as Japan, other countries such as Britain, France, Germany, the former Soviet Union also has different degree of development in rapid charging technology. Britain's associated company invented "TEC total energy intelligent charging control technology" and its control system, effectively control the powder charging when the amount of energy needed, overcome existing corona charging system and friction type charging system caused various problems, to solve the "Faraday shielding effect" and "reverse ionization effect" and so on.At present the batteries of electric cars in use process, because of the limitation of the voltage of the power battery energy and need to adopt more battery in series combination, and power battery characteristics of highly nonlinear, individual difference is very big, therefore become the electric car battery management system, a necessary device. The most basic function of BMS is to monitor the working state of the battery (voltage, current and temperature of the battery), prediction of power battery (SOC) of battery capacity, battery management to avoid over discharge, overcharge, overheating and serious imbalance between monomer battery voltages, maximize battery storage capacity and cycle life.Current of the electric vehicle charging system is not very good with a serious defect currently has been relatively mature and supporting the use of on-board BMS system, charging system is either not provide communication interface with BMS, or communication interface is not compatible with popular now BMS interface. BMS system has the most comprehensive, full of battery state of real-time data, if you can provide the charging system and its communication interface, can fundamentally solve the current charging system in the process of charging the battery status change resulting in without understanding the state of the battery charged blindly charging, thus reduce battery life.In addition, as the core of the electric vehicle charging system, the existing charging controller, the control process are mostly based on analog signal processing, and its control structure is a centralized control structure. The traditional charging system boundary is not clear, complex structure and each subsystem is unitized degreeis very low. Its applied electromagnetic environment, all kinds of high frequency signals could easily lead to serious interference of microcomputer control charging system failure. In the past, often using analog signal for each signal transmission is between the control systems. Various kinds of interference signal into analog signals, it is easy to lead to failure of the control system, its structure and the process may not apply to the requirement of the distributed control and the whole process of the digital processing requirements.3 The function of the electric vehicle charging system requirementsThe charging system in addition to providing communication interface with BMS, received by the BMS battery status parameters of transfer function, extract energy from power supply and charging system is passed to the battery in the right way, so as to set up between power supply and battery power conversion interface. Charging system is usually performed by the power conversion unit and process control of controller. The basic properties of the charging system requirements include the following:Security: electric vehicle charging, how to ensure that personnel's personal safety and the safety of the battery is very important. Easy to use: charging system should have high intelligence, operators don't need too much intervention in the charging process. Cost economy: economic and cheap charging system helps to reduce the cost of the whole electric cars, improve operation efficiency, and promote the commercialization of electric vehicles. High efficiency: efficiency is one of the most important requirements for modern charging system; the efficiency of the energy efficiency of high and low for the electric car has a huge impact. Low pollution to the power supply: the power electronic technology of the charging system is a kind of highly nonlinear devices, will produce harmful to the supply network and other electrical equipment of the harmonic pollution, moreover, because of the charging system power factor is low, the charging system load increases, its effect on the supply network also not allow to ignore.4 EV charging method4.1 Constant current chargingIn the whole process of charging and is always with constant current for rechargeable battery. In this way, to ensure that in the later stages of charging without a lot of gas, therefore can only use small current charging, so need a long time, the charging method has the advantage of simple operation, the current is too small, but in the beginning in the late charge and charging current is too large, charging time is long.4.2 Constant voltage chargingEarly charging current is quite large, as the charge and current decreases. For more battery discharge, the initial charging current is too large in order to protect cells from damage, at the beginning of the charging to limited flow measures to avoid the charging current is too large. Compared with constant current charging, the battery is not easy to calculate.4.3 Constant voltage charging current limitingTo remedy constant-voltage charging shortcomings, is widely used in constant voltage current limiting method. Set the maximum charging current, at the beginning of the charge, when the current exceeds the limit of flow value, with the current limiting value, when the current less than the current limit value, constant voltage charging. Thus automatically adjust the charging current, does not exceed a certain limit, the charging current is controlled in the early.4.4 Constant voltage charge after constant currentThis method is a combination of constant current charging and constant voltage charge, the previous constant current charging and accounting period of constant voltage charging way, on the one hand to avoid the constant voltage charging current is too large, in the early late again on the other hand to avoid the constant current charging phenomenon.4.5 Charge attenuationIn the process of charging, with the increase of voltage of the battery, charging current attenuation of charging method gradually. This is a kind of ideal charging method; charge saves time and prevents the sulfuric acid stratification and the plate vulcanizing. But this charging method implementation requires more complex control,compared with the constant current charging; the charging amount is not easy to estimate. Due to the battery and nonlinear dispersion, complexity, the problems in the process of charging, the battery charging has become a more complex issue. The traditional charging method is used to charging very troublesome, because often be charging for 10 hours, and in the process of charging must be manned. Quick charge is the problem to be solved in the process of charging current control, in the process of charging, if the charging current is not enough, to reach the purpose of quick charge. If the charging current is too large and will cause a large number of precipitation of gas, electrolyte temperature will rise quickly, easy to cause the battery plate is damaged, shorten the battery life. Also in the process of charging battery monomer battery consistency of difference, this factor must be fully considered.译文电动汽车充电系统及控制器研究Pollet G摘要本文提出了全桥的主电路拓扑结构和PWM的控制手段,有效的提高了充电系统的可靠性和效率。
毕业设计电动车电池参考文献英文
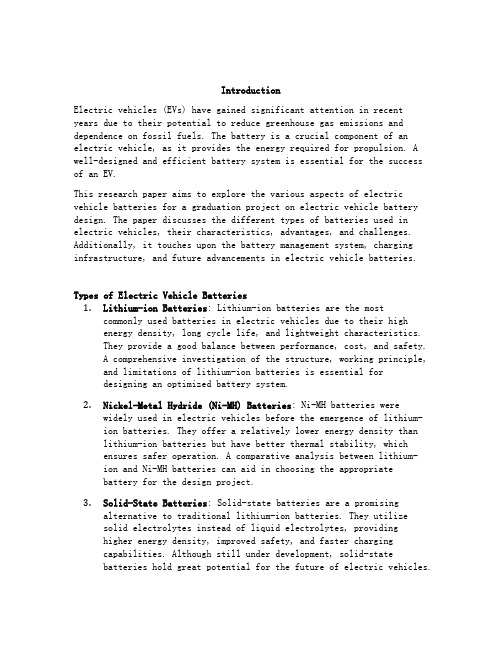
IntroductionElectric vehicles (EVs) have gained significant attention in recent years due to their potential to reduce greenhouse gas emissions and dependence on fossil fuels. The battery is a crucial component of an electric vehicle, as it provides the energy required for propulsion. A well-designed and efficient battery system is essential for the success of an EV.This research paper aims to explore the various aspects of electric vehicle batteries for a graduation project on electric vehicle battery design. The paper discusses the different types of batteries used in electric vehicles, their characteristics, advantages, and challenges. Additionally, it touches upon the battery management system, charging infrastructure, and future advancements in electric vehicle batteries.Types of Electric Vehicle Batteries1.Lithium-ion Batteries: Lithium-ion batteries are the mostcommonly used batteries in electric vehicles due to their highenergy density, long cycle life, and lightweight characteristics.They provide a good balance between performance, cost, and safety.A comprehensive investigation of the structure, working principle,and limitations of lithium-ion batteries is essential fordesigning an optimized battery system.2.Nickel-Metal Hydride (Ni-MH) Batteries: Ni-MH batteries werewidely used in electric vehicles before the emergence of lithium-ion batteries. They offer a relatively lower energy density thanlithium-ion batteries but have better thermal stability, whichensures safer operation. A comparative analysis between lithium-ion and Ni-MH batteries can aid in choosing the appropriatebattery for the design project.3.Solid-State Batteries: Solid-state batteries are a promisingalternative to traditional lithium-ion batteries. They utilizesolid electrolytes instead of liquid electrolytes, providinghigher energy density, improved safety, and faster chargingcapabilities. Although still under development, solid-statebatteries hold great potential for the future of electric vehicles.Battery Management System (BMS)The Battery Management System (BMS) is responsible for monitoring and controlling the battery’s performance, safety, and lifespan. A well-designed BMS ensures the optimal operation of the battery system, preventing overcharging, undercharging, and excessive discharge. It provides accurate state-of-charge (SOC) and state-of-health (SOH) estimations, which are crucial for maximizing the battery’s efficiency.The BMS consists of various components, including sensors, control algorithms, and battery balancing circuits. In-depth research on BMS architecture, functionality, and control strategies is necessary to design an effective battery management system for the electric vehicle.Charging InfrastructureThe availability of a robust charging infrastructure is essential for widespread adoption and convenience of electric vehicles. The research project should explore the different types of charging stations, including:1.Level 1 Charging: Level 1 charging refers to standard householdoutlets (120V), which provide a slow charging rate but are widely accessible.2.Level 2 Charging: Level 2 charging utilizes dedicated chargingstations (240V). It offers a faster charging rate compared toLevel 1 and is commonly found in residential areas, workplaces,and public charging stations.3.DC Fast Charging: DC Fast Charging, also known as Level 3charging, provides rapid charging capabilities by directlydelivering DC power to the vehicle’s battery. These chargingstations are typically located along highways and major routes.The paper should discuss the importance of a well-established charging infrastructure and address potential challenges and solutions to the deployment of charging stations.Future AdvancementsThe field of electric vehicle batteries is continuously evolving, with ongoing research and advancements. It is crucial for the researchproject to explore future developments, such as:1.Advanced Lithium-ion Batteries: Researchers are constantlyworking on improving the energy density, charging speed, andsafety of lithium-ion batteries. Advancements in materials,electrode designs, and electrolytes are expected to result in more efficient and long-lasting batteries.2.Solid-State Batteries: As mentioned earlier, solid-statebatteries hold immense potential for the future of electricvehicles. The research should discuss the current challenges faced in commercializing solid-state batteries and potentialbreakthroughs that can lead to their widespread adoption.3.Beyond Lithium-ion: Besides solid-state batteries, alternativebattery chemistries like lithium-sulfur (Li-S) and lithium-air(Li-Air) batteries are being explored for their high energydensities. Understanding these emerging battery technologies canpave the way for future advancements in EV batteries.ConclusionDesigning an efficient and reliable battery system is crucial for the success of an electric vehicle. This research paper provides a comprehensive and detailed analysis of different types of electric vehicle batteries, their characteristics, and the importance of a well-designed battery management system and charging infrastructure. Furthermore, it explores future advancements in electric vehicle battery technologies. By understanding these aspects, the research project can aim to design an optimized electric vehicle battery system that contributes to a sustainable and greener transportation future.Note: The content provided above is a suggested structure for the research paper related to the topic of “Graduation Project - Electric Vehicle Battery”. Please add relevan t and specific details from appropriate academic references to complete the paper.。
电动汽车发展:过去、现在与未来外文文献翻译、中英文翻译、外文翻译

Abstract
A vehicle is consider Green when it moreenvironmentally friendly than the traditional petroleumcombustion engine, in which includes any nontraditionalvehicle like, HEV, Plug In, EV, Fuel Cell, Bio fuel etc. thatimproves fuel economy. The development of electric vehiclehas been over a hundred years but failure to gain the publicacceptance in various stages due to various reasons whichexplained. While EV was never mass produced, Hybridelectric vehicle gains the momentum in recent years. Fordhas launched its second generation of HEV and GM alsoannounced the debut of the Volt in 2010. Comparing to theregular HEV, Plug in is the new trend in hybrid autodevelopment due to extend travel range in electrical modeand a possibility of a zero emission as long as travel distanceis less than charging threshold. However, more recently, anelectrification trend in automotive industry has been evolvedand will revolutionize the industry. With the correct policyand government help and advancement of electric vehicletechnology, the prospect of Electric Vehicle will be brightand the focus point of future development.
充电桩建设项目商业计划书范文

充电桩建设项目商业计划书范文英文回答:Executive Summary.The proposed electric vehicle (EV) charging station project aims to address the growing demand for EV charging infrastructure in the target market. The project involves the installation and operation of a network of fast-charging stations strategically located in high-traffic areas. Our market research indicates a strong need for reliable and convenient EV charging services, and we believe that this project will tap into a rapidly growing market.Market Analysis.The target market for this project is the rapidly expanding population of EV owners in the region. According to industry data, EV sales have been increasingexponentially in recent years, and this trend is expected to continue in the foreseeable future. This growth is driven by factors such as rising fuel costs, government incentives, and increasing consumer awareness of environmental issues.Site Selection.The locations of the charging stations have been carefully chosen to ensure maximum convenience and accessibility for EV owners. The stations will be installed in high-traffic areas, such as shopping malls, parking garages, and transportation hubs. This will allow EV owners to charge their vehicles while they are running errands or commuting to work.Charging Technology.The charging stations will be equipped with the latest fast-charging technology, which will enable EV owners to charge their vehicles in as little as 30 minutes. This will significantly reduce the time spent waiting for a charge,making EV ownership more convenient and practical.Financial Projections.The financial projections for this project indicatethat it is a sound investment with a strong potential for profitability. The project is expected to generate significant revenue from the sale of electricity and subscription fees. The operating costs will be relatively low, as the charging stations will be automated and require minimal maintenance.Environmental Impact.The project will have a positive environmental impact by reducing greenhouse gas emissions and promoting the adoption of EVs. By providing convenient and affordable charging options, the project will encourage more people to switch to EVs, which will reduce air pollution and contribute to a cleaner environment.Conclusion.The proposed EV charging station project is a well-conceived and financially viable opportunity to address the growing demand for EV charging infrastructure in the target market. The project will provide a convenient and reliable charging solution for EV owners, while also contributing to environmental sustainability. We are confident that this project will be a success and will make a significant contribution to the growth of EV adoption in the region.中文回答:执行摘要。
外文翻译---混合动力电动汽车机械和再生制动的整合
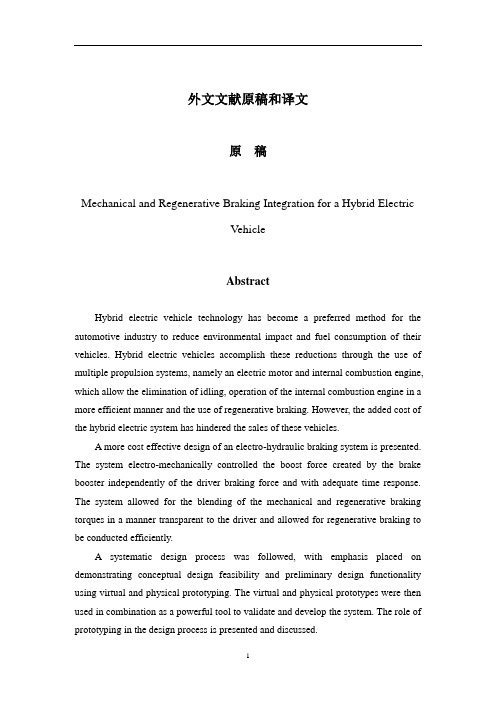
外文文献原稿和译文原稿Mechanical and Regenerative Braking Integration for a Hybrid ElectricVehicleAbstractHybrid electric vehicle technology has become a preferred method for the automotive industry to reduce environmental impact and fuel consumption of their vehicles. Hybrid electric vehicles accomplish these reductions through the use of multiple propulsion systems, namely an electric motor and internal combustion engine, which allow the elimination of idling, operation of the internal combustion engine in a more efficient manner and the use of regenerative braking. However, the added cost of the hybrid electric system has hindered the sales of these vehicles.A more cost effective design of an electro-hydraulic braking system is presented. The system electro-mechanically controlled the boost force created by the brake booster independently of the driver braking force and with adequate time response. The system allowed for the blending of the mechanical and regenerative braking torques in a manner transparent to the driver and allowed for regenerative braking to be conducted efficiently.A systematic design process was followed, with emphasis placed on demonstrating conceptual design feasibility and preliminary design functionality using virtual and physical prototyping. The virtual and physical prototypes were then used in combination as a powerful tool to validate and develop the system. The role of prototyping in the design process is presented and discussed.Through the experiences gained by the author during the design process, it is recommended that students create physical prototypes to enhance their educational experience. These experiences are evident throughout the thesis presented.1.1 Modern Hybrid Electric VehiclesWith rising gas prices and the overwhelming concern for the environment, consumers and the government have forced the automotive industry to start producing more fuel efficient vehicles with less environmental impact. One promising method that is currently being implemented is the hybrid electric vehicle.Hybrid vehicles are defined as vehicles that have two or more power sources [25]. There are a large number of possible variations, but the most common layout of hybrid vehicles today combines the power of an internal combustion engine (ICE) with the power of an electric motor and energy storage system (ESS). These vehicles are often referred to as hybrid electric vehicles (HEV’s) [25]. These two power sources are used in conjunction to optimize the efficiency and performance of the vehicle, which in turn will increase fuel economy and reduce vehicle emissions, all while delivering the performance the consumer requires. In 1997, the Toyota Prius became the first hybrid vehicle introduced into mass production in Japan. It took another three years for the first mass produced hybrid vehicle, the Honda Insight, to be introduced into the North American market. The release of the Honda Insight was closely followed by the release of the Toyota Prius in North America a couple of months later [35].Hybrid electric vehicles have the distinct advantage of regenerative braking. The electric motor, normally used for propulsion, can be used as a generator to convert kinetic energy of the vehicle back into electrical energy during braking, rather than wasting energy as heat. This electrical energy can then be stored in an ESS (e.g. batteries or ultracapacitors) and later released to propel the vehicle using the electric motor.This process becomes even more important when considering the energy density of batteries compared to gasoline or diesel fuel. Energy density is defined as the amount of energy stored in a system per unit volume or mass [44]. To illustrate this point, 4 kilograms (4.5 litres) of gasoline will typically give a motor vehicle a range of50 kilometres. To store the same amount of useful electric energy it requires a lead acid battery with a mass of about 270 kilograms [25]. This demonstrates the need for efficient regenerative braking to store electrical energy during driving, which in turn will keep the mass of the energy storage system down and improve the performance and efficiency of the HEV.1.2 Research Scope - Regenerative Braking SystemsThe scope of the research presented is to create a low cost regenerative braking system to be used on future economical hybrid vehicles to study the interaction between regenerative and mechanical braking of the system. This system should be able to control the combination of both regenerative and mechanical braking torque depending on driver demand and should be able to do so smoothly and safely. Controlling the regenerative braking torque can be done using control algorithms and vector control for induction motors. However, controlling the mechanical braking torque independently of the driver pedal force, while maintaining proper safety back-ups, proved to be more of a challenge. To overcome this problem, a system was developed that would attenuate the pressure in the brake booster in order to control the amount of mechanical torque developed by the braking system.2.1 Hybrid Electric Vehicle OverviewHybrid vehicles have emerged as one of the short term solutions for reducing vehicle emissions and improving fuel economy. Over the past 10 years almost all of the major automotive companies have developed and released for sale their own hybrid electric vehicles to the public. The popularity of hybrid electric vehicles has grown considerably since the turn of the century. With enormous pressure to become more environmentally friendly and with unpredictable gas prices, the sales of hybrid electric vehicles have increased dramatically in recent years.2.1.1 Hybrid ConfigurationsFor the past 100 years the objective of the hybrid has been to extend the range of electric vehicles and to overcome the problem of long recharging times [35]. There are three predominant hybrid electric vehicle configurations currently on the market today. These configurations are known as series hybrids, parallel hybrids andseries/parallel hybrids.Each configuration has its advantages and disadvantages which will be discussed in the following sections.Series HybridsIn series hybrids the mechanical output from the internal combustion engine is used to drive a generator which produces electrical power that can be stored in the batteries or used to power an electric motor and drive the wheels. There is no direct mechanical connection between the engine and the driven wheels. Series hybrids tend to be used in high power systems such as large trucks or locomotives but can also be used for lower power passenger vehicles [18]. The mechanically generated electrical power is combined with the power from the battery in an electronic controller. This controller then compares the driver demand with the vehicle speed and available torque from the electric motor to determine the amount of power required from each source to drive the vehicle. During braking, the controller also switches the power electronics to regenerative mode, and directs the power being regenerated to the batteries [55].There are many advantages made possible by the arrangement described above. It is possible to run the ICE constantly at its most efficient operating point and share its electrical output between charging the battery and driving the electric motor. By operating the engine at its most efficient operating point, emissions can be greatly reduced and the most electrical power can be generated per volume of fuel. This configuration is also easierto implement into a vehicle because it is less complex which makes this method more cost effective.Parallel HybridsIn parallel hybrid configurations the mechanical energy output from the ICE is transmitted to a gearbox. In this gearbox the energy from the ICE can be mechanically combined with a second drive from an electric motor. The combined mechanical output is then used to drive the wheels [35]. In this configuration there is a direct connection between the engine and the driven wheels. As in series hybrids the controller compares the driver demand with the vehicle speed and output torque and determines the amount of power to be used from each source to meet the demand,while obtaining the best possible efficiency. A parallel hybrid also controls regenerative braking similarly to a series hybrid. Parallel hybrids are usually used in lower power electric vehicles in which both drives can be operated in parallel to provide higher performance [18].There are a number of advantages of a parallel hybrid over a series hybrid. The most important advantage is that since only one conversion between electrical and mechanical power is made, efficiency will be much better than the series hybrid in which two conversions are required. Since the parallel hybrid has the ability to combine both the engine and electric motor powers simultaneously, smaller electric motors can be used without sacrificing performance, while getting the fuel consumption and emission reduction benefits. Lastly, parallel hybrids only need to operate the engine when the vehicle is moving and do not need a second generator to charge the batteries.Series/Parallel HybridsCombined hybrids have the features of both series and parallel configurations. They use a power split device to drive the wheels using dual sources of power (e.g. electric motor only, ICE only or a combination of both). While the added benefits of both series hybrids and parallel hybrids are achieved for this configuration, control algorithms become very complex because of the large number of driving possibilities available.2.1.2 Degree of HybridizationSince most H EV’s on the road today are either parallel or series/parallel, it is useful to define a variable called the ‘degree of hybridization’ to quantify the electrical power potential of these vehicles.iceem em P P P DOH += The degree of hybridization ranges from (DOH = 0) for a conventional vehicle to (DOH = 1) for an all electric vehicle [25]. As the degree of hybridization increases, a smaller ICE can be used and operated closer to its optimum efficiency for a greater proportion of the time, which will decrease fuel consumption and emissions. The electric motor power is denoted by Pem and the internal combustion engine power isdenoted by Pice.Micro HybridMicro hybrids have the smallest degree of hybridization and usually consist of an integrated starter generator (ISG) connected to the engine crankshaft. The ISG allows the engine to be shut off during braking and idling to conserve fuel and then spins the crankshaft up to speed before fuel is injected during acceleration. The ISG also provides small amounts of assist to the ICE during acceleration and acts as a generator to charge the batteries during braking. Micro hybrids usually improve fuel economy by about 10 percent compared with non hybrids [53].Mild HybridMild hybrids have a similar architecture to the micro hybrid except that the ISG is uprated in power to typically greater than 20 kW. However, the energy storage system is limited to less than 1 kWh [35]. Mild hybrids usually have a very short electric-only range capability but can provide a greater assist to the ICE during accelerations. The electrical components in a mild hybrid are more complex than a micro hybrid and play a greater role in the vehicle operation. Fuel economy can be improved by 20 to 25 percent with a mild hybrid over non hybrid vehicles [53].Full HybridFull hybrids do away with the ISG and replace it with a separate electric motor and alternator/starter that perform the same function. The electric motor has the ability to propel the vehicle alone, particularly in city (stop and go) driving. The energy storage system is upgraded to improve electric-only range capability and the engine is usually downsized to improve fuel economy and emissions. Full hybrids can achieve40 to 45 percent fuel consumption reductions over non hybrids [53].Plug-in HybridPlug-in hybrids are very similar to full hybrids except that they have a much larger ESS that can be connected to an outside electrical utility source for charging. These vehicles use only the electric motor to propel the vehicle within the range of the batteries and then operate like full hybrids once the batteries have discharged to a predefined level.2.1.3 Fundamentals of Regenerative BrakingOne of the most important features of HEV’s is their ability to recover significant amounts of braking energy. The electric motors can be controlled to operate as generators during braking to convert the kinetic energy of the vehicle into electrical energy that can be stored in the energy storage system and reused. However, the braking performance of a vehicle also greatly affects vehicle safety. In an emergency braking situation the vehicle must be stopped in the shortest possible distance and must be able to maintain control over the vehicle’s direction. The latter requires control of brake force distribution to the wheels [12].Generally, the braking torque required is much larger than the torque that an electric motor can produce [12]. Therefore, a mechanical friction braking system must coexist with the electrical regenerative braking. This coexistence demands proper design and control of both mechanical and electrical braking systems to ensure smooth, stable braking operations that will not adversely affect vehicle safety. Energy Consumption in BrakingBraking a 1500 kg vehicle from 100 km/h to 0 km/h consumes about 0.16 kWh of energy based on Equation 2.2.221mv E If 25 percent of this energy could be recovered through regenerative braking techniques, then Equation 2.2 can be used to estimate that this energy could be used to accelerate the vehicle from 0 km/h to about 50 km/h, neglecting aerodynamic drag, mechanical friction and rolling resistance during both braking and accelerating. This also assumes that the generating and driving modes of the electric motor are 100% effici ent. This suggests that the fuel economy of HEV’s can be greatly increased when driving in urban centres where the driver is constantly braking and accelerating. Note that the amount of energy recovered is limited by the size of the electric motor and the rate of which energy can be transferred to the ESS.2.1.4 Methods of Regenerative BrakingThere are two basic regenerative braking methods used today. These methods are often referred to as parallel regenerative braking and series regenerative braking. Each of these braking strategies have advantages and disadvantages that will be discussed in this section.Parallel Regenerative BrakingDuring parallel regenerative braking, both the electric motor and mechanical braking system always work in parallel (together) to slow the vehicle down [48]. Since mechanical braking cannot be controlled independently of the brake pedal force it is converting some of the vehicle’s kinetic energy into heat instead of electrical energy. This is not the most efficient regenerative braking method. However, parallel regenerative braking does have the advantages of being simple and cost effective. For this method to be used, the mechanical braking system needs little modification and the control algorithms for the electric motor can be easily implemented into the vehicle. This method also has the added advantage of always having the mechanical braking system as a back-up in case of a failure of the regenerative braking system. Series Regenerative BrakingDuring series regenerative braking the electric motor is solely used for braking. It is only when the motor or energy storage system can no longer accept more energy that the mechanical brakes are used [48]. This method requires that the mechanical braking torque be controlled independently of the brake pedal force and has the advantage of being the most efficient by converting as much of the vehicle’s kinetic energy into electrical energy . The downfall of this method is that it brings many costs and complexities into the system. For this method to function properly a brake-by-wire system has to be developed which either uses an electro-hydraulic brake (EHB) or an electro-mechanical brake (EMB). Both of these types of brakes require brake pedal simulators and redesigned brake systems which can become costly. Since these systems are brake-by-wire there are also many redundancies required with sensors, processors and wiring for safety which add to the complexity of the system. 2.1.5 Current Regenerative Braking SystemsThe current regene rative braking system in most HEV’s (e.g. Toyota Prius) is the more costly electro-hydraulic braking (EHB) system. This system uses a brake pedal simulator, which is separate from the hydraulic braking circuit, to establish driver braking demand. The braking demand is then proportioned into a regenerative and mechanical braking demand. The mechanical braking demand is then sent to a system that contains a high pressure hydraulic pump, accumulator and proportional controlvalves. The proportional control valves allow the brake line fluid to flow to each wheel at predefined pressures determined by the braking demand.译文混合动力电动汽车机械和再生制动的整合摘要为了减少对环境的污染和车辆的燃油消耗,混合动力电动汽车已经成为汽车工业的首选方法。
关于新能源充电管理系统的外文文献

关于新能源充电管理系统的外文文献New Energy Charging Management SystemWith the rapid development of new energy vehicles, the demand for charging infrastructure has been increasing. In order to efficiently manage the charging process and ensure the stability of the power grid, a new energy charging management system is designed. This system integrates advanced technology to optimize the charging experience for users while minimizing energy waste and reducing costs.1. IntroductionThe new energy charging management system is a comprehensive solution that includes hardware, software, and communication networks. It aims to provide a seamless and convenient charging experience for users while ensuring the efficient use of resources. By implementing smart charging strategies, the system can balance the demand for electricity with the available supply, thereby reducing the strain on the power grid.2. Components of the SystemThe new energy charging management system consists of several key components, including charging stations, power distribution units, communication modules, and a central control system. The charging stations are equipped with advanced technology that allows for fast and efficient charging of electric vehicles. The power distribution units regulate the flow of electricity to ensure a stable and reliable charging process. Communication modules enable real-time data exchange between differentcomponents of the system, while the central control system manages and monitors the overall operation of the system.3. Smart Charging StrategiesOne of the key features of the new energy charging management system is its ability to implement smart charging strategies. These strategies take into account factors such as electricity demand, renewable energy generation, and user preferences to optimize the charging process. By dynamically adjusting the charging rate based on these factors, the system can reduce energy waste and lower costs for users. Additionally, the system can prioritize charging for electric vehicles that are in urgent need of power, ensuring that all users have access to charging facilities when they need them.4. Benefits of the SystemThe new energy charging management system offers several benefits for both users and energy providers. For users, the system provides a convenient and reliable charging experience, with the option to schedule charging sessions in advance. This helps to minimize waiting times and ensures that users can access charging facilities when they need them. For energy providers, the system helps to optimize the use of resources and reduce the strain on the power grid. By implementing smart charging strategies, the system can balance the demand for electricity with the available supply, ensuring a stable and reliable energy supply for all users.5. ConclusionIn conclusion, the new energy charging management system is an innovative solution that can help to optimize the charging process for electric vehicles. By integrating advanced technology and smart charging strategies, the system offers a convenient and efficient charging experience for users while minimizing energy waste and reducing costs. With the increasing demand for charging infrastructure, the new energy charging management system is a crucial tool for ensuring the stability of the power grid and promoting the widespread adoption of new energy vehicles.。
新国标电动汽车的直流充电桩控制系统设计
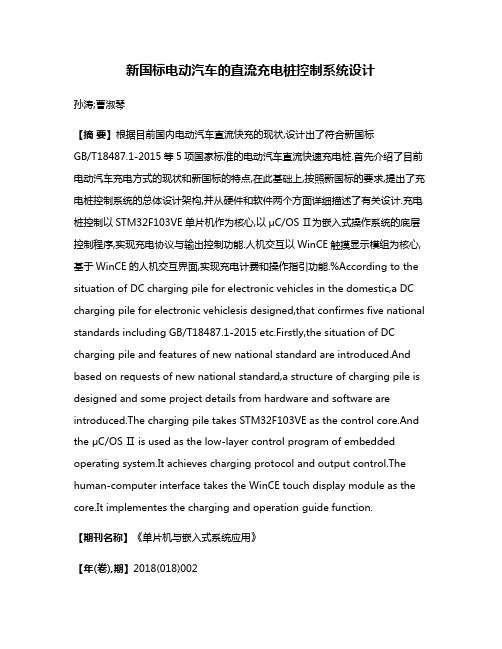
新国标电动汽车的直流充电桩控制系统设计孙涛;曹淑琴【摘要】根据目前国内电动汽车直流快充的现状,设计出了符合新国标GB/T18487.1-2015等5项国家标准的电动汽车直流快速充电桩.首先介绍了目前电动汽车充电方式的现状和新国标的特点,在此基础上,按照新国标的要求,提出了充电桩控制系统的总体设计架构,并从硬件和软件两个方面详细描述了有关设计.充电桩控制以STM32F103VE单片机作为核心,以μC/OS Ⅱ为嵌入式操作系统的底层控制程序,实现充电协议与输出控制功能.人机交互以WinCE触摸显示模组为核心,基于WinCE的人机交互界面,实现充电计费和操作指引功能.%According to the situation of DC charging pile for electronic vehicles in the domestic,a DC charging pile for electronic vehiclesis designed,that confirmes five national standards including GB/T18487.1-2015 etc.Firstly,the situation of DC charging pile and features of new national standard are introduced.And based on requests of new national standard,a structure of charging pile is designed and some project details from hardware and software are introduced.The charging pile takes STM32F103VE as the control core.And the μC/OS Ⅱ is used as the low-layer control program of embedded operating system.It achieves charging protocol and output control.The human-computer interface takes the WinCE touch display module as the core.It implementes the charging and operation guide function.【期刊名称】《单片机与嵌入式系统应用》【年(卷),期】2018(018)002【总页数】5页(P63-66,71)【关键词】充电桩;电动汽车;STM32F103VE;WinCE【作者】孙涛;曹淑琴【作者单位】北方工业大学电子信息工程学院,北京100141;北方工业大学电子信息工程学院,北京100141【正文语种】中文【中图分类】TP29引言电动汽车在行驶过程中,不会造成排气污染,对环境保护和空气洁净都是十分有益的。
- 1、下载文档前请自行甄别文档内容的完整性,平台不提供额外的编辑、内容补充、找答案等附加服务。
- 2、"仅部分预览"的文档,不可在线预览部分如存在完整性等问题,可反馈申请退款(可完整预览的文档不适用该条件!)。
- 3、如文档侵犯您的权益,请联系客服反馈,我们会尽快为您处理(人工客服工作时间:9:00-18:30)。
文献出处Hawkins S. The design of the electric vehicle charging pile [J]. SAE International Journal of Alternative Powertrains, 2015,5(3): 213-221.原文The design of the electric vehicle charging pileAbstractIn the world's oil resources shortage and the grim situation of global warming, the construction of low carbon vehicles will become the auto industry a new development direction. Current research of electric vehicles around the world has entered the white-hot. People try to make it become a mainstream in the 21st century the development of the automobile. Electric vehicle charging infrastructure is an important part of the electric car industry chain can not be ignored in, at the same time of developing electric vehicle industry also should fully take into account the development of the charging infrastructure, so the design of electric vehicle charging pile and its control method of study is very necessary.Keywords: Electric vehicle charging pile; Equilibrium control; The human-computer interaction1 IntroductionCountries in the world to promote energy conservation and environmental protection, of which the word "low carbon" everyone not unfamiliar, carbon emissions in today's car is bigger, the industry also gradually focus on low carbon field. The auto industry's carbon emission is higher and higher. To be raising industry development and the balance of environmental emissions, the automobile industry faced with the transformation of development. In the world's oil resources shortage and the serious situation of global warming, the global auto industry uniform standards will reference to carbon emissions standards, leading the global auto industry development better. Electric cars compared to traditional petrol powered cars, in terms of environmental protection and energy saving shows the outstanding advantages. The electric car has many advantages, such as less pollution emissions, high efficiency, low noise, low running cost, etc., it has these advantages in reducing air pollution and energy shortage is of great significance.2 Electric vehicle charging infrastructureThe key technologies of electric vehicle (EV) mainly includes: power battery and charging infrastructure as the core of energy systems:Drive motor and drive system as the core of the power system. In a coordinated control system, ensure the vehicle safe, efficient and comfortable operation as the core of the vehicle control system. For carbon reduction and environmental protection of electric vehicles, charging device is indispensable. Its function is to turn within the electricity to the electric vehicle battery power grid, to power electric vehicles.Charging infrastructure is mainly charging and charging pile. Charging stations within, usually equipped with a number of fast charging plugs and a few slow charging pile. Two kinds of charging infrastructure each have advantages and disadvantages, need to choose according to actual species suitable for local facilities. Given priority to with quick charge mode of charging station a short charging time is charging the advantages of high efficiency. At a high speed along the service area, selection of large charging stations and other places of power is to be able to produce 600 V / 300 A charging pile. Usually consider including the use of environmental factors, such as charging pile only in produce high voltage and large current, and power is larger (100 kw), to ensure that the electric car charging efficiency, the technology of charging methods and security put forward higher requirements. So charging stations than charging pile construction and management of cost is much higher, the size should be and petrol stations. Now automotive battery technology remains to be development, rapid charging pattern can cause greater damage to the battery. The expert thinks, quick charge mode is equivalent to in a relatively short period of time forced "into" power to the battery, after several quick charge battery, its life will be greatly reduced. In addition it is important to note that large-scale electric vehicle charging demand just rely on the charging station is fulfilled, and charging stations will be occupied land area, will produce a lot of management costs. Therefore, charging station is only applicable to charge for a small amount of public transport services. Charging pile covers an area of a few, the cost is very low, very suitable for the supermarket in the city, parking lots, construction of residential area of denseparking of vehicles, such as the area. And more importantly, charging pile mainly slow filling pattern, due to the need of the small current, thus to ensure the safety of its performance, and of great benefit to extend the service life of the battery. But the disadvantage of this schema also clear, have emergency operation requirements in the car, the charging is not implemented in time. Such as providing 220 V / 16 A home charging pile of ac power, the charger is small volume and simple operation of car charger. The charging pile is mainly provide service charge for private cars, the power is about 3 ~ 5 kw, charging time need 5 ~ 10 hours.3 Present situation of charging systemIn recent years from two level of products and technologies, charging system has made good progress: charging products with the development of control technology, artificial intelligence and other advanced technology, get rid of the simple, the direction of multi-function, safer intelligent. The field bus technology, such as development, RS485, LIN bus makes the monitoring system of the diversification of means of communication, high speed and security. French multi-purpose nuclear and hydroelectric power, the power generation capacity is enough, according to statistics, three-quarters of the total electricity from nuclear power plants in France, one 6 from hydropower station, and its power supply clean, cheap electricity, automobile industry developed, so it is the world's one of the first countries to develop and promote the electric car. The French government collaborative EDF (EDF) Company, company, Renault and PSA (Renault) motors, and other cooperation, developing electric cars. In LaRocheHe investment produces small four 50 vehicles, electric vehicles and built 12 (including 3 fast and nine common) charging stations, has been put into use and tested more than 2 years. Japan's new energy vehicles has been in the world leading level, the Tokyo electric power company has announced that it successfully developed large quick charger, the charger has greatly shortened the time, the Japanese electric car popularization provides the possibility of a larger. Charging pile design and control of the construction of the charging infrastructure, as early as the First Solar companies in the United States built 5 in California highway fast charging pile, can under the condition of 240 v / 240A, 3.5 hours to complete the charging of electricvehicles.4 Charging pile of functional requirementsWith electric passenger cars promote gradually, people to its corresponding charging infrastructure also gave high attention. If the charging station, charging pile, can carry on the security and intelligence to the electric vehicle charging, so the popularity of electric cars, progress will be accelerated. In order to realize intelligent charging pile in the management and application, you need to understand the function of charging pile demand. Electric vehicle charging piles need to have the following several main functions: to guarantee the normal work of the system, monitoring and protection measures necessary, charging posts must have electrical protection device, when the system failure occurs, the system of charging power supply is cut off quickly, within the stipulated time to ensure the personal safety of users. Charging pile must be reliable operation, charging pile equipment adopts modular structure; local fault cannot threaten the normal operation of the whole system, charging pile must also be able to parallel processing more than one event. All logins, control, exit the important operations, such as charging pile should have corresponding records, but also allows to query and statistic of operating records, charging pile have ensure data and system security protection of information is not theft and destruction. Charging pile should use the graphical interface in Chinese, the user according to the screen display can realize self-help charging; provide convenience for people intuitively clear charging operation. Users can query on charging pile to the charging time, place, and the historical data of the basic information such as rechargeable battery, charging pile should also install with embedded printers, convenient charging print statements. Charging pile should be according to the electricity information deriving from watt-hour meter, and calculate the user charge the amount spent, and can save data backup, convenient send to background monitoring system. Charging pile system should be able to practice the trapezoidal pricing mechanism.5 The integral design of charging pile systemThe electric car is ac charging pile used in ac, dc power supply, ac working voltage is 220 v or 380 v, can according to different types of electric vehicles, adoptsthe corresponding charging voltage grade, ordinary pure electric car charging pile to charge need 4 ~ 5 hours. The input voltage of dc charging pile using three phase four wire AC380V, frequency 50HZ can provide enough power, and the output of adjustable dc, therefore can meet the requirement of quick charge. Electric vehicle charging pile, concentrator, battery management system, charging management platform, such as complementary to each other, constitute the charging system. Battery management system (BMS) real-time information interaction with charging posts controller, the purpose is to monitor the battery voltage, current and temperature state parameters, forecast capacity (SOC) of batteries, batteries in to avoid bad phenomenon (over discharge, overcharge, overheating and battery voltage imbalance between monomer), it can maximize battery storage capacity and cycle life of assurance. The service management platform is mainly to the electric car battery charge information, IC and piles these data for centralized management of information. In general, the service management platform is important function for charging management and operation, as well as integrated query. To intuitively clear communication with the customers, charging pile has important information can be shown on LCD display convenient man-machine interaction. Electric vehicle charging, the screen will display the charging time, charging power, the main information such as the amount payable.Charging, the battery charging or owe electricity will damage to the battery inside, accelerate cell aging, will affect battery performance. According to the analysis, the inappropriate way of charging is the main cause of battery life cut short. Therefore, how to guarantee quickly and does not affect the battery life, has become an important research topic in recent years. Charging mode choice determines the length of the battery life, among them, the constant current, constant voltage charging and charging in stages of these methods is a common way of charging. Is the advantage of constant current charging control method is simple, but by the law of mass we know: rechargeable batteries can accept current capacity with the charging process is a trend of gradual decline. Late to charge, the charging current is much used for electrolysis of water, can produce gas, so that to get nothing. Constant voltage charging way earlyin the process of charging current is too large, the impact on battery life is great, and constant voltage charging mode battery plate bending easily, causing the battery scrap. Phase charging method is actually a constant current, constant voltage charging the method of combining more commonly used phase charging method includes two stages and three phase charging method.译文电动汽车充电桩的设计摘要在世界石油资源短缺和全球气候变暖的严峻形势下,建设低碳汽车将成为汽车产业一种新的发展方向。