中频炉炉衬筑炉工艺
中频炉修筑炉与烘炉技术操作规程

中频炉修筑炉与烘炉技术操作规程1 适用范围与构成1.1 用于铸铁熔炼的无芯感应中频炉。
通常用石英砂和硼酸筑炉衬(修炉时加入耐火水泥),硼酸的加入量决定于炉子的工作温度,炉子的工作温度越高,硼酸的加入量越少。
1.2 本标准适用于阳极组装车间的中频炉。
2 生产技术条件2.1 石英砂:SiO2≥98.5~99.5%;三氧化二铁≤0.05%;水份≤0.5%2.2 硼酸≥98%;结晶粒度≤0.5mm ;水份≤0.5%2.3 石英砂配比: 6~8 mm:30%10~20 mm:25%40~70 mm:10%70~140 mm:10%>200 mm:25%2.4 硼酸用量:1%2.5 胶泥配比: 5~10 mm粘土砖块30%20~30 mm粘土砖块比:30%粘土粉(熟料):20%耐火泥(500#):20%水适量2.6 打结后炉衬密度:2.7 筑炉坩埚厚度:120~150 mm3 修筑炉前检查和准备3.1 检查炉子液压系统、电器系统、循环水系统和报警装置是否正常。
3.2 检查修筑炉用材料、工具和坩埚是否准备齐全。
现场是否打扫干净。
3.3 修筑炉用工具和坩埚使用前均需除锈,坩埚用前除锈后,涂上煤油和柴油。
3.4 石英砂和硼酸使用前应烘烤。
3.5 石英砂和硼酸在筑炉前应搅拌均匀。
3.6 筑炉人员筑炉前,不能将纸、铁屑等杂质带入现场,混入炉料中。
4 修筑炉操作4.1 炉盖修筑4.1.1 清理干净炉盖。
4.1.2 炉盖内铺一层石棉板。
4.1.3 将搅拌均匀的炉料加入炉盖内,进行振动打结。
要求炉料充分泛桨,排出气孔且密实。
4.1.4 每次加料量不大于250kg,打结到要求部位后刮平、修整。
4.1.5 炉盖三天自然凉干,如烘烤随炉衬进行。
4.2 大修炉的操作4.2.1 炉子底部及上口筑粘土耐火砖和轻质耐火砖(或用炉料修筑),要求砖缝小于1 mm,并要错缝。
4.2.2 检查感应线圈是否完好,如有损伤,应进行修补。
4.2.3 一切正常完好后,进行涂抹胶泥。
6吨中频炉筑炉烘炉及维护工艺
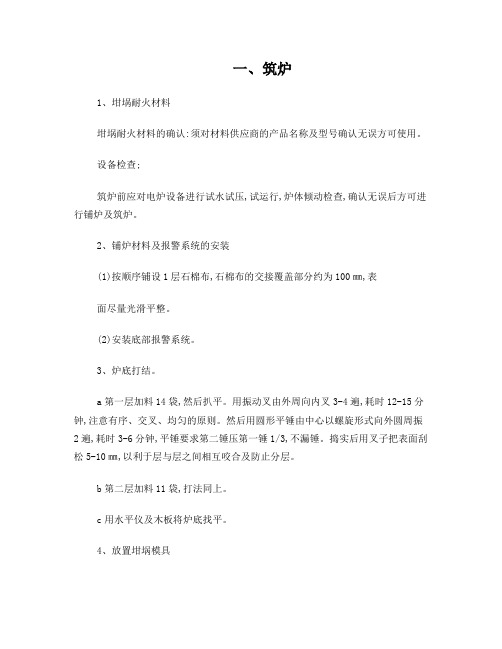
一、筑炉1、坩埚耐火材料坩埚耐火材料的确认:须对材料供应商的产品名称及型号确认无误方可使用。
设备检查;筑炉前应对电炉设备进行试水试压,试运行,炉体倾动检查,确认无误后方可进行铺炉及筑炉。
2、铺炉材料及报警系统的安装(1)按顺序铺设1层石棉布,石棉布的交接覆盖部分约为100㎜,表面尽量光滑平整。
(2)安装底部报警系统。
3、炉底打结。
a第一层加料14袋,然后扒平。
用振动叉由外周向内叉3-4遍,耗时12-15分钟,注意有序、交叉、均匀的原则。
然后用圆形平锤由中心以螺旋形式向外圆周振2遍,耗时3-6分钟,平锤要求第二锤压第一锤1/3,不漏锤。
捣实后用叉子把表面刮松5-10㎜,以利于层与层之间相互咬合及防止分层。
b第二层加料11袋,打法同上。
c用水平仪及木板将炉底找平。
4、放置坩埚模具a坩埚模具误差≤5㎜。
坩埚模具失圆将导致坩埚壁厚不匀,必须重新修整坩埚模具,使其符合图纸要求。
b坩埚模具排气孔直径为3-6㎜,间距为150-200㎜;模具如果锈蚀,应用砂纸打磨后方可使用。
c放置坩埚模具时,注意保证坩埚壁厚一致并和线圈同心,焊缝留于后半侧,保证前侧最厚。
d用三个木楔块固定坩埚模具。
5、填筑坩埚壁a务必将底部与坩埚壁接触的材料扒松5-10㎜!b添加耐火材料,须仔细检查每一层,注意不要让任何包装碎片及其它杂物混入炉衬材料内!c如果炉衬材料进入铺设材料之间,需全部清除。
如无法清除,全部炉衬材料就必须拆掉。
d坩埚壁第一层加料5袋,加料后扒平。
然后用振动叉叉3-4遍,耗时12-15分钟,注意有序、交叉、均匀的原则。
再用侧锤振2遍,耗时3-6分钟,侧锤振动时应严防碰伤石棉布。
振实后将表面扒松5-10㎜。
e从第二层至炉顶,重复上面的操作。
f打结至1/3高度,可去掉楔木块。
g必须将炉衬一次性打完,严禁停停打打,因为此材料吸潮性强,加之铸造车间粉尘大、杂物多,影响炉衬寿命。
6、炉领封口及炉嘴炉嘴下部可铺一层10-20㎜炉衬材料干料,其它部位可用炉衬材料加水玻璃及水进行施工。
电炉炉衬修筑与使用工艺
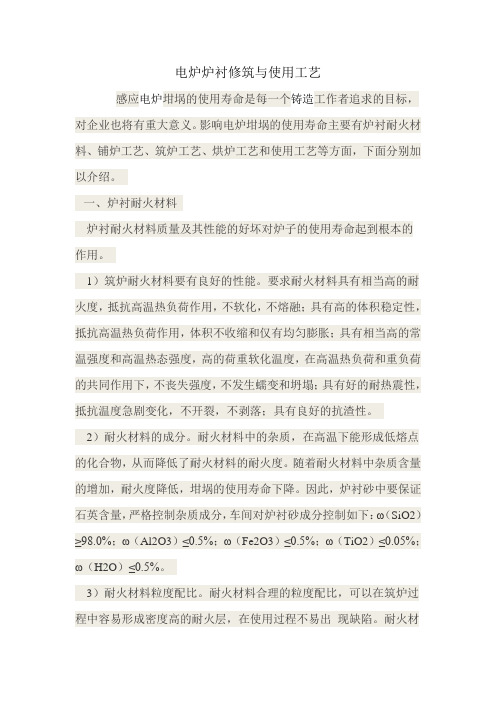
电炉炉衬修筑与使用工艺感应电炉坩埚的使用寿命是每一个铸造工作者追求的目标,对企业也将有重大意义。
影响电炉坩埚的使用寿命主要有炉衬耐火材料、铺炉工艺、筑炉工艺、烘炉工艺和使用工艺等方面,下面分别加以介绍。
一、炉衬耐火材料炉衬耐火材料质量及其性能的好坏对炉子的使用寿命起到根本的作用。
1)筑炉耐火材料要有良好的性能。
要求耐火材料具有相当高的耐火度,抵抗高温热负荷作用,不软化,不熔融;具有高的体积稳定性,抵抗高温热负荷作用,体积不收缩和仅有均匀膨胀;具有相当高的常温强度和高温热态强度,高的荷重软化温度,在高温热负荷和重负荷的共同作用下,不丧失强度,不发生蠕变和坍塌;具有好的耐热震性,抵抗温度急剧变化,不开裂,不剥落;具有良好的抗渣性。
2)耐火材料的成分。
耐火材料中的杂质,在高温下能形成低熔点的化合物,从而降低了耐火材料的耐火度。
随着耐火材料中杂质含量的增加,耐火度降低,坩埚的使用寿命下降。
因此,炉衬砂中要保证石英含量,严格控制杂质成分,车间对炉衬砂成分控制如下:ω(SiO2)≥98.0%;ω(Al2O3)≤0.5%;ω(Fe2O3)≤0.5%;ω(TiO2)≤0.05%;ω(H2O)≤0.5%。
3)耐火材料粒度配比。
耐火材料合理的粒度配比,可以在筑炉过程中容易形成密度高的耐火层,在使用过程不易出现缺陷。
耐火材料粗、中、细3种粒度配比不当将会降低使用寿命,车间使用的耐火材料为专业厂家提供,粗细配比如下:3.35mm~5mm、0.85mm~1.70mm、0.1mm~0.85mm、0.1mm以下的比例分别为17%、33%、20%、30%。
二、铺炉工艺铺炉质量对炉子的寿命和安全有着重要的意义。
铺炉时先检查线圈是否有损伤,如有,则在损伤部位涂刷绝缘漆,将其修复;再用水玻璃拌耐火泥修平炉墙,并将炉墙及炉底清理干净;依次铺设事先按尺寸剪好的云母板、报警不锈钢网、石棉布;用铜芯线接好报警不锈钢网穿出炉子线圈外,再用三个涨圈在铺好石棉布的炉子炉墙下、中、顶部涨紧;铺好的炉子,应盖好,避免杂物落入其中。
中频炉的筑炉、补炉、炉衬烧结工艺

中频炉的筑炉、炉衬烧结使用操作及维修目录一概念1、感应加热、熔化的工作原理 (5)2、工频炉与中频炉的概念 (6)3、工频炉与中频炉的比较 (8)二中频炉的安装、检测1、炉体安装 (11)2、水系统安装 (11)3、液压系统安装 (11)4、电气安装 (11)5、母线的布置 (12)三中频炉炉衬的筑炉、烘炉1、筑炉前的检查 (13)2、筑炉 (13)3、烘炉、炉衬烧结机理及三层结构 (16)四炉衬的损坏机理及预防1、过热 (20)2、裂纹 (21)3、剥落 (22)4、侵蚀 (23)5、炉瘤 (25)6、浸润 (25)7、其它延长炉衬使用寿命的措施 (25)五炉衬的修补1、热补法 (27)2、冷补法 (28)六中频炉的使用1、开炉前的准备及检查 (28)2、开机操作 (29)3、停机操作 (29)4、冷启动 (30)5、使用中的操作 (30)6、严格禁止的操作 (33)七中频炉的日常维护和检修要点中频炉的日常维护检修要点(见“周期表”) (34)八事故处理1、停电 (34)2、漏液 (35)3、冷却水事故 (36)九其它1、中频炉的熔化率与生产率 (36)2、冷却水泵供电 (37)3、冷却水 (37)4、中频炉熔化比工频炉快的主要原因 (37)5、中频炉比工频炉节能 (38)6、冷却水塔 (38)7、感应圈与磁轭间的绝缘材料 (38)8、关键元件的制造商(国外) (38)9、熔化炉额定功率的配置 (38)10、保温中频炉最小功率配置 (39)11、冷却水管接头卡篐材质要求 (39)12、磁轭的作用 (39)13、无碳胶管的作用 (40)14、坩埚(炉衬)的作用与厚度 (40)15、感应器及坩埚的高度 (41)16、影响熔化单耗指标的因素 (42)17、关于“防电蚀管” (44)18、感应炉冷却水的特点及对水质的要求 (44)中频炉的筑炉、炉衬烧结、使用操作及维修一概述1、感应加热、熔化的工作原理(1)一个无芯感应炉,主要由线圈及放入其中熔化的金属炉料所构成,运行的基本原理是电磁感应。
如何提高中频炉炉衬寿命的筑炉工艺技术
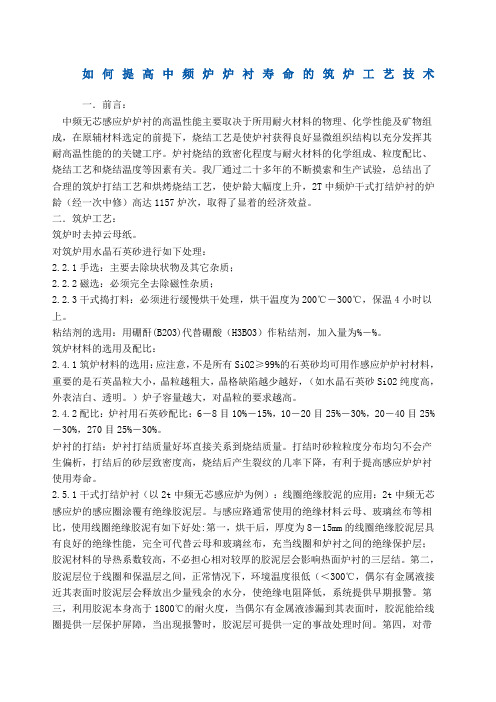
如何提高中频炉炉衬寿命的筑炉工艺技术一.前言:中频无芯感应炉炉衬的高温性能主要取决于所用耐火材料的物理、化学性能及矿物组成,在原辅材料选定的前提下,烧结工艺是使炉衬获得良好显微组织结构以充分发挥其耐高温性能的的关键工序。
炉衬烧结的致密化程度与耐火材料的化学组成、粒度配比、烧结工艺和烧结温度等因素有关。
我厂通过二十多年的不断摸索和生产试验,总结出了合理的筑炉打结工艺和烘烤烧结工艺,使炉龄大幅度上升,2T中频炉干式打结炉衬的炉龄(经一次中修)高达1157炉次,取得了显着的经济效益。
二.筑炉工艺:筑炉时去掉云母纸。
对筑炉用水晶石英砂进行如下处理:2.2.1手选:主要去除块状物及其它杂质;2.2.2磁选:必须完全去除磁性杂质;2.2.3干式捣打料:必须进行缓慢烘干处理,烘干温度为200℃-300℃,保温4小时以上。
粘结剂的选用:用硼酐(B2O3)代替硼酸(H3BO3)作粘结剂,加入量为%-%。
筑炉材料的选用及配比:2.4.1筑炉材料的选用:应注意,不是所有SiO2≥99%的石英砂均可用作感应炉炉衬材料,重要的是石英晶粒大小,晶粒越粗大,晶格缺陷越少越好,(如水晶石英砂SiO2纯度高,外表洁白、透明。
)炉子容量越大,对晶粒的要求越高。
2.4.2配比:炉衬用石英砂配比:6-8目10%-15%,10-20目25%-30%,20-40目25%-30%,270目25%-30%。
炉衬的打结:炉衬打结质量好坏直接关系到烧结质量。
打结时砂粒粒度分布均匀不会产生偏析,打结后的砂层致密度高,烧结后产生裂纹的几率下降,有利于提高感应炉炉衬使用寿命。
2.5.1干式打结炉衬(以2t中频无芯感应炉为例):线圈绝缘胶泥的应用:2t中频无芯感应炉的感应圈涂覆有绝缘胶泥层。
与感应路通常使用的绝缘材料云母、玻璃丝布等相比,使用线圈绝缘胶泥有如下好处:第一,烘干后,厚度为8-15mm的线圈绝缘胶泥层具有良好的绝缘性能,完全可代替云母和玻璃丝布,充当线圈和炉衬之间的绝缘保护层;胶泥材料的导热系数较高,不必担心相对较厚的胶泥层会影响热面炉衬的三层结。
中频炉筑炉、烘炉等操作和日后维护

中频炉筑炉、烘炉等操作和日后维护中频炉坩埚筑炉、烘炉等操作和日后维护中频炉的坩埚规格中频炉坩埚熔化炉适用于铝合金压铸机旁边浇铸时的保温、熔化及小批量废杂铝的熔化回收。
中频电炉坩埚主要规格有150#、200#、250#、300#、350#、400#、500#、600#、700#、800#、1000#、1200#、1300#、1400#、1500#、1800#、2000#、2500#、3000#等,熔铝实际保持铝液容量约为坩埚号数的三分之一,每小时最大提供铝液量约为坩埚号数的六分之一。
(1)中频电炉筑炉之前要选择合适的坩埚模,坩埚模需采用6- l0mm厚的钢板卷制焊接而成,模体带有一定锥度,焊接处应作连续焊接(以免通电时接缝处打火,造成电流不稳甚至过流保护)。
模外表面焊接处应铲平磨光,清除氧化铁锈(以免渗入炉衬与之结渣,影响炉衬寿命);坩埚模外表面要光滑平整,特别是侧壁与底部相接圆弧应选择较大为宜(通常取炉衬内径的0.1倍为最大容许圆弧半径。
(2)中频电炉填筑新炉衬须严格按筑炉工艺,填筑过程中应避免铁磁等物质混入筑炉材料中:坩埚模放置时应紧压于感应线圈中心,夯结炉衬前可以在坩埚内装一定量干净炉料块,防止坩埚移动。
(3 )中频电炉严格按烘炉曲线烘炉烧结,通过调节电压严格控制中频输出功率以控制升温,烧结过程中最高电压不能超过额定电压的70%- 8O%.严格控制冷却水流量,在炉温升高过程中逐渐增大水流量、烘炉温度达1lOO左右时,应装入清洁无锈回炉料,逐渐提高功率至额定值,继续加料至金属液面与炉衬上端口齐平。
温度达烧结温度(约l550…《:)时,降低功率保溫3- 4h,出炉。
(4)每天熔炼结束时,为避免炉衬迅速冷却产生裂缝,可在坩埚内装入第二天需熔化的炉料,盖好炉盖,堵住炉嘴且适当调小感应圈冷却水流量。
(5)新筑炉衬须连续熔化三炉以上才允许停炉搁置。
(6)中频电炉炉台下,尤其水冷电缆落地处,不得堆放金属炉料及其它杂物,以免磨损水冷电缆绝缘外套或金属物中频感应发热损坏水冷电缆绝缘外套;炉台下不允许积水积油(以免水冷电缆长期浸泡而损坏等),5 中频电炉维护中频电炉水冷却系统经调查发现,中频电炉50%以上故障是由于水冷系统造成,故对水冷系统要做到:(1|做好点检、巡检。
中频熔炼炉最佳筑炉与起熔步骤详解

中频熔炼炉最佳筑炉与起熔步骤详解一筑炉1.主要筑炉工具振实捣固主要用具马丁振动器(气动):工作气压0.6MPa以上,由于压缩空气系统压力不够,现使用一台增压泵,压力可达0.8MPa。
六齿捣固叉;圆型捣固头;月牙型捣固头;捣固工具连接铁管;热电偶、多点温度记录仪。
2.筑炉前准备工作(1)中频感应电炉的检查及调试炉子的机械系统、液压系统、电气系统、水冷系统,必须在筑炉前调试完好,并做无炉衬冷态试验。
报警装置信号设定好报警值。
排除炉子运行中可能出现的意外故障。
(2)模具准备模具制作严格按图纸要求验收,模具表面要打磨光滑,表面进行除锈处理。
(3)启熔准备工作准备启熔块:3~5t,小块干净的废钢、生铁、小块干净的回炉料。
(4)热电偶铂-铑铂LB,温度范围0~1500℃,长度:2.5m、2m、1.5m 各一根(按标准型号配备),多点温度记录仪:1台。
补偿导线若干米(与热电偶配套)。
铁管或角钢:3根,2m、1.5m、1m各一根。
(5)耐火材料准备按每次所需要更换的耐火材料进行准备。
绝大多数都是更换炉膛耐火材料。
主要是:炉衬料:1001;炉口料:88A;炉嘴料:A76;滑动平面料(云母纸)。
(6)泄漏蛛网准备泄漏蛛网按图样要求制作2套,准备氧气橡胶管:长200㎜,16根3.炉衬耐火材料打结施工(1)检查炉底环、炉口环、线圈耐火材料是否完好,顶出块是否完好,如有裂纹、裂缝等缺陷要修补好或更换。
(2)清除炉内垃圾,吹净表面尘土。
(3)用A76料修筑出铁口与扒渣口,按型状打结成型,料表面扎若干孔,以利气体排出,并用干料将排气孔表面密合。
孔深度要求40~50mm。
(4)安装炉底泄漏蛛网。
先将融离表料铺好,将炉子侧斜一定角度,炉内留一人将不锈钢棒由预留孔穿出炉底,将泄漏蛛网固定完好。
(5)炉底铺料80~120㎜/层,用捣固叉由深至浅均匀叉四遍,第一层炉底捣固后,将表面刮松,深度达10㎜以上,再加入下批炉底料,打最后一层炉底料前要将泄漏蛛网不钢丝用胶管套好。
0.5吨中频电炉筑炉工艺

0.5吨中频电炉筑炉工艺0.5t中频感应炉筑炉及熔炼工艺规范前言必须提升感应器电炉的使用寿命,炉衬石英砂质量就是必要的关键条件,而筑城炉热田操作方式采用也就是提升电炉炉衬使用寿命的关键条件。
为提升感应器电炉使用寿命,降低消耗,确保正常生产,撰写0.5t中频感应炉筑城炉及选矿工艺规范,期望操作方式人员严苛按工艺规范展开操作方式。
编制日期标准化校对会签批准0.5t中频感应炉筑城炉及选矿工艺规范1范围本文件规定了0.5t中频感应炉筑城炉及选矿的工艺建议和操作过程,适用于于铸铁车间。
2筑城炉2.1筑炉前的准备2.1.1初次修炉:将炉口耐火砖拿起,用修包用的普通耐火泥将缝隙填平,压上铝盖板,松开螺栓。
挑三包线圈用耐火材料(线圈涂料),按10%~12%的比例提清水搭和烘烤光滑,用抹子涂至感应器线圈内表面,按炉口10~12毫米,炉底18~20毫米的厚度从上到下构成锥度,表面应当平坦不许存有凹凸。
等待涂料自然潮湿6小时以后,用电炉蒸煮12小时,并使水分不少于0.5%。
线圈涂料的研磨见到72.1.2一般大修:检查炉体耐火砖垫块是否完好,感应线圈耐火涂料是否松动剥落,如有损坏应修补。
为能使炉衬顺利顶出,在炉口上部感应线圈耐火涂料略薄些,约10~12毫米,下部厚些,约18~20毫米,使之有一定锥度。
2.1.3钢坩埚模尺寸应符合技术要求,使用前外表面的锈蚀应全部去除。
(钢坩埚模在库中放置时应当涂抹防锈油,采用时用棉丝盖住)φ4402.1.4施工现场打扫整洁,维持工作场地洁净,准备工作齐全筑城炉时采用的工具。
2.2铺炉2.2.1铺炉前清扫残留在炉体内的砂、灰等杂物。
2.2.2用一层石棉布铺设炉底,四周皱,900铺设必须平坦。
2.3筑城炉底2.3.1筑炉时要有专人组织、指挥,负责检查打结质量。
筑炉人员口袋中不装有任何东西,不允许筑炉人员在打结炉衬时吸烟因为所有杂物掉入可以影响炉衬质量。
φ3802.3.2炉衬石英砂(硼酐含量0.8%)拆袋后应当先放入整洁的容器内,辨认出纸屑等杂物及时清φ420除,然后用铁锹传至炉内。
- 1、下载文档前请自行甄别文档内容的完整性,平台不提供额外的编辑、内容补充、找答案等附加服务。
- 2、"仅部分预览"的文档,不可在线预览部分如存在完整性等问题,可反馈申请退款(可完整预览的文档不适用该条件!)。
- 3、如文档侵犯您的权益,请联系客服反馈,我们会尽快为您处理(人工客服工作时间:9:00-18:30)。
中频感应熔炼炉筑炉工艺和烘炉工艺筑炉工艺跟炉衬材料和熔炼炉容量及实际操作各有不同。
但是关键的环盯是:材质的正确选择,颗粒配比、添加剂、结合剂的选择与使用数量、打结前的准备工作以及打结操作工艺等。
合理的粒度配比可以使堆塀的气孔率最小,致密性最髙、饶结性好和耐激冷激热性好。
用于制作划祸的耐火材料一般分为粗颗粒、中颗粒和细颗粒三种。
在选择配比时,要考虑堆塀大小、打结方法及烧结工艺等因素;打结料的颗粒配比、熔炼炉的容量和打结壁厚度见表在打结堆塀时,所使用的耐火材料需要加入添加剂,如硼酸(H、BOQ、卤水(MgCl2)、水玻璃(NaSiO,)等。
其目的是改善耐火材料的烧结性能,降低烧结温度,提高烧结质量,有些耐火材料需要提髙抗拉强度,还必须加入微量的不锈钢纤维或者是碳化硅纤维。
镁砂的烧结温度为1750°C,石英砂的烧结温度是1450°C,加入量为打结料的0. 8%-1.5% 左右的硼酸后,硼酸加热分解,以形式存在于耐火材料中。
在温度到达1000〜1300C时EQ与镁砂中的MgO和S/Q等形成低熔点化合物(SiO/BQ,熔点1200 r; MgO•场(厶,熔点1142°C; 2MgO•坊O’熔点1342C:)使镁砂饶结温度降低,改善了烧结条件,提高了烧结质量,硼酸还可以调节堆竭体积的变化率,时炉衬裂纹倾向性减小。
硼酸除了对耐火材料烧结层有良好的效果,对英中烧结层可以起到使川塀和感应线圈之间有一层松软的过渡带,不仅会缓冲体积变化,同时也可以缓解应力,使裂纹引起的漏炉事故减少。
当使用镁铝尖晶石(MgO^Al2O^材料时,加入硼酸,可降低尖晶石形成温度,促进尖晶石形成,因而改善了烧结质量,提髙了划竭的耐压强度,在含氧化镁(MgO) 92%,氧化铝(Al2O3)8%的打结料中加入料重1.2%的硼酸后,改善了烧结质量,使圮祸的耐压强度也增加了1〜2倍。
但是硼化物表而活性大,对镁质耐火材料也有不利之处,所以硼酸的加入量不宜过多,要适量调整。
通过了解硼酸加入到耐火材料中的性能可以知道添加剂在筑炉工艺中的作用,而且比需要掌握加入量的大小比例。
筑炉方法从耐火材料的配比混合形态分为干式打结和湿式打结筑炉两种:干式打结是指在干燥的打结炉衬材料中加入干燥的黏结剂,经搅拌后进行。
湿式打结是指在干燥的打结炉衬材料中加入水、水玻璃、卤水、或硼酸水溶剂等黏结剂进行搅拌后打结。
筑炉方法从操作方法上分为手工(人工)打结筑炉法、电动振锤筑炉法和电动筑炉法及气动锤击筑炉法等,人工筑炉只适于小吨位(1.5吨以下)感应熔炼炉的筑炉电动气动等机器筑炉适用于大吨位感应熔炼炉的筑炉。
1、炉衬的打结工艺步骤(1)、准备打结所用工具、配制打结料及其他所用材料:(2)、准备堆塀模。
(划祸模的制作要考虑较好的几何形状和外壳强度,外表力求光滑无锈迹, 址烟模的斜度为1:10,随熔炼炉容量不同,珀塀模厚度一般为4〜12mm.J0为了保证筑炉捣击致密,大容呈的熔炼炉的划祸模可分为2〜3段。
为了便于烘炉时炉衬部气体和水汽的排出,在九塀模周用均匀钻有2〜5皿的排气孔。
)(3)、铺设隔热绝缘层;即堆竭壁与感应圈壁之间的填充物,其材料一般为云母纸、石棉板和玻璃丝布等:在铺设之前,应彻底淸除感应线圈表面灰尘和附着物,有漏炉报警装置,应按要求同时铀设。
用膨胀圈胀紧,要使绝缘层紧贴在感应圈上,铺设的材料应避免横向搭接缝隙, 纵向搭接应在100mm左右,并保证互相铺开、铺平、压紧。
(4)、人工打结或机器打结;打结炉衬的厚度要控制在要求圉。
5.32炉衬的打结工艺(以人工打结为例)①、采用薄层加料,捣筑叉要能从上层捣到下层,避免层间出现分层:②、通常一层铺料厚度约为80〜100mm,以后每层均为40〜50mm,最高可髙岀炉底20〜30mm。
用平锤打实后,再把多余的部分铲除掉,并保持炉底水平;③、加料尽星低倒,并分散铺平,不能成堆,以免物料发生偏析:④、捣打是垂直向下一插到底,但不能把绝缘层和隔热层穿透,捣打先重后轻,下落点均匀, 以保证打结致密;⑤、捣筑顺序是先边缘后中心,有次序逐排打结,直到捣筑时有反挫力为准,打结后炉衬的体积密度应不小于2. 6g/cm=(碱性炉衬);第一层打结时间约为60min,以后每层不少于30〜40min;⑥、最好连续打结,若有中断,必须用塑料不覆盖,再次打结时,应将表面刮除,然后耙松加料再打结:⑦、在捣筑过程中,每次加料前,要测量圮祸底的髙度,方法是在炉口上方平放木条,从打结料层向炉口测虽,最后一次的测量位垃应刚好是安放川塀模的髙度:⑧、安放堆塀模。
安放是一般采用左位法和测量法,使川堀模中心严格固泄在感应器线圈的中心轴线上,以保证划竭壁的厚度尽可能的均匀。
⑨、捣筑划祸壁是必须注意:在堆堀底部与划塀壁交界处(即炉底与炉壁的拐角),是堆垠最薄弱的环节,此处的厚度较大,散热差,捣筑时要特别细心,其他部位的捣筑也应仔细。
捣筑也需使其尽可能致密。
⑩、修筑炉口和炉嘴时,可用水玻璃作为结合剂,使苴快速成型。
用适量的硼酸水、水玻璃与打结料混合,湿度要合适,能用手捏成团即可,先在已打好的炉口上涂上适量的玻璃水,然后用填筑混合料,用锤打实。
通常炉口和炉嘴应修成地外高的斜而,以防金属液外溢。
电动或机器筑炉程序和要求基本一样,只是代替了人工捣筑炉料,1T省了人力。
但也必须细心,不能错过每一个环节。
捣筑也要致密,用绕进行,打结方向要靠近模。
重外轻。
其配料和加料等都与人工筑炉相同。
2、炉衬的烘烤和烧结(即烘炉工艺)烘炉和烧结时炉衬获得优良髙温性能的一个重要环肖,在炉衬的打结完毕后即可进行烘炉和烧结,英目的是充分排岀炉衬中的水分,并使硅砂充分均匀变相,最后在髙温下烧结成具有高强度的密实的瓷表而。
这一环肖也会影响炉衬的使用寿命。
炉衬的烘烤和烧结应遵循低温缓慢烘烤、高温满炉烧结的原则,烘烤烧结时可加首批金属料, 并尽疑减少金属炉料之间的缝隙。
以W100C/h (对于大于15吨的熔炼炉升温速度应W85°C/h)的升温速度达到1000〜1100C并保温2〜6 (对于大于15吨的熔炼炉保温时间应24h)小时,继续以WlOO'C/h的升温速度使金属炉料熔化呈:达到90%,再以W220°C/h的升温速度达到正常金属炉料温度的50C后保温二小时后达到正常需要的溶液温度倒岀炉。
烘炉和烧结工艺受到熔炼炉容量和金属材料的要求各有不同。
一般按熔铁的工艺步骤烘炉和烧结。
烘炉和烧结的测温应用热电偶进行,热电偶在川堀模或熔模的上中下三个部位安装备以测量。
烧结温度不超过1600°C.(1)、炉衬的烘炉工艺注意事项:①、烘炉前要对冷却水系统、倾炉系统、控制回路及各种标记进行检査核对:②、烘炉时一泄要加入一泄数量的金属炉料,约为炉膛的70%左右,以保证温度升降的均匀性:③、尽可能选用无锈的炉料,以减少炉渣,大料装在四周,小料装在中心的原则在升温过程逐步加料;④、烘炉要采取低功率、慢升温,送电前要先通冷却水,熔炼钢铁升温速度为<100°C/h (对于大于15吨的熔炼炉升温速度应W8〒C/h)至800〜900°C:⑤、炉衬温度到达looor以上时,改用50$的供电功率,使划竭模和炉料换慢升温,炉料缓慢熔化,以减小冲刷作用。
⑥、熔液高于50°C,保持1〜2小时,使炉衬均匀烧结,第一炉烘炉烧结时间应不低于正常工作的2〜3倍时间进行。
最好连续熔化2〜3炉才能完成整个烧结过程。
若是烧结温度低,保温时间不够,冷却后炉衬容易开裂。
总之,烘炉时应遵循分级调压送电、低温缓慢烘烤、髙温缓慢烧结,初始加炉料应淸洁。
以下为列简单说明:①、2T铸铁熔炼炉的烘炉时间和烘炉方法:初次送电,送3min,停15min,保持4h,电源功率120〜150kW: 4h 后,送5min,停20min,保持2h,电源功率120-150kW: 6h 后送lOmin, 停40min,保持8h,电源功率100〜120kW; 14h后送20min,停60min,保持8h,电源功率100〜120kW; 22h后不间断送电,保持8h,电源功率lOOkW: 30h后化满铁水,保持8h,电源功率200kW; 38h后开始低温饶结,保持5k,温度在1350-C左右;43h后,开始高温烧结,保持5h,温度在1450°C, : 48h后出铁水,温度不低于1300°C:出炉前2h加7公斤左右碎玻璃。
②、烘炉温度曲线举例3、成型炉衬成型炉衬指的是以各种不泄形的耐火材料混合配制而成,采用炉外预制成型的方法制作的炉衬。
适用于中频熔炼炉熔化各类黑色金属及有色金属及有色合金的炉衬。
适用于2T以下炉衬的制作。
成型炉衬成型的方法有:等静压法、浇铸-振动法、逐层填料-逐层压实法:其工艺流程如下:选料配方f 充分磁选f 粒度级配* 添加结合制均勻丼料模成■塑升温脱挣窑焙烧一>自然干检验入库。
成型炉衬的形状为上端开口,中间空心,下部实底的圆柱形,其结构及力学性能如下:①、成型炉衬的外壁与外底而为直角,方便与施工,安装易紧实;②、成型炉衬的向的侧壁厚度由上至下逐渐增厚,有针对性的抵抗由上至下的逐渐增大的熔液静压力。
③、成型炉衬的壁与底部结合部分为弧连接,圆角半径大、结构预应力增强,更适宜承受热膨胀是的侧壁外扩与熔液向下的静压力联合作用的“撕裂作用”。
④、成型炉衬的底部较厚实,更适应于承受熔液的正向静压力。
成型炉衬和感应器线圈之间在使用时需要增加安全炉衬(也称为外衬),一般为未烧结层,能保护感应线圈的安全。
同时具有传递电磁能量、均匀散热的功能。
成型炉衬和密度较低的安全炉衬的结合也称为复合炉衬;安全炉衬一般用干式打结法施工。
英材料采用多级颗粒的配比,如石棉布、水玻璃、结合剂(1%的硼酸或硼肝)、捣筑料,结合剂;步骤是先安装成型炉衬、捣筑安全炉衬。
炉嘴和炉口采用传统方法制作。
4、中频感应熔炼炉炉衬的维护和保养(IX熔炼炉的炉衬维护和保养①、当炉衬壁出现纵向裂纹时,应采取缓慢升温方法,是裂纹弥合后在进行熔炼:②、当炉衬壁岀现横向裂纹时,按实际情况在裂纹填上细粉耐火材料,进行加热熔化。
③、当炉衬底倍侵蚀,可用炉衬料修补,修补后用金属炉料覆盖,低功率熔化一段时间再开满功率。
④冶炼结朿后短时间不用时,应在炉口覆盖石棉板或其他保温措施,让其缓慢冷却:长时间不开炉,在使用时应缓慢升温;(2)、熔炼炉的炉衬寿命的提高措施①、用于第一炉次烘炉和烧结的炉料选用不锈和干净的金属炉料;②、淸除回炉料上的型砂及附着物,以防炉衬结瘤:③、加厚渣线部分烧结层,及时出渣,在炉料过热前应先除渣一次;④、尽量缩短炉衬在髙温时的工作时间,炉料较少时应减小输入的电源功率;⑤、不超过炉衬耐火材料的坐高温度区间工作。