煤基活性炭生产用斯列普活化炉生产工艺探讨
煤基活性炭制备工艺研究

煤基活性炭制备工艺研究【摘要】本文主要针对煤基活性炭制备工艺进行了深入研究。
在介绍了煤基活性炭制备工艺的概述和应用价值。
接着在详细讨论了煤基活性炭原料的选择与处理、制备工艺的研究、性能测试与分析、在环境治理和能源领域中的应用。
结论部分对煤基活性炭制备工艺研究的现状进行了总结,并展望了未来的发展方向。
最后提出了关于煤基活性炭制备工艺的建议和展望。
通过本文的研究,可以更好地了解煤基活性炭的制备工艺及其在环境治理和能源领域中的应用,为该领域的发展提供理论支持和实践指导。
【关键词】煤基活性炭、制备工艺、原料选择、性能测试、环境治理、能源领域、现状、展望、未来发展、建议、关键词1. 引言1.1 煤基活性炭制备工艺研究概述煤基活性炭是一种通过特定工艺制备而成的高效吸附材料,具有广泛的应用价值。
煤基活性炭的制备工艺研究是为了提高其吸附性能和净化效率,以适应不同环境治理和能源利用需求。
目前,煤基活性炭的制备工艺研究已经取得了一定的成果,但仍存在着一些挑战和问题需要解决。
本文旨在系统地总结煤基活性炭制备工艺的研究现状和进展,探讨其在环境治理和能源领域中的应用前景,为未来的研究和发展提供参考和指导。
通过对煤基活性炭制备工艺的综合分析和评价,旨在为提高煤基活性炭的性能和应用效果,推动其在环境治理和能源利用中的广泛应用。
1.2 煤基活性炭的应用价值1. 环境治理领域:煤基活性炭可以有效去除大气、水体和土壤中的有害气体和重金属等污染物,起到净化环境的作用。
在水处理领域,煤基活性炭被广泛应用于脱色、脱氯、脱臭等水处理工艺中,能够有效提高水质。
煤基活性炭还可以用于污水处理和废气处理等领域,发挥着重要的环境保护作用。
2. 能源领域:煤基活性炭在能源领域也有重要应用价值。
煤基活性炭可以作为传统煤炭的替代品,用于燃烧、发电等能源生产过程中,能够减少对传统煤炭的需求,降低碳排放和减少资源消耗。
煤基活性炭还可以用于储气、储氢等能源转化和存储领域,为能源产业的可持续发展提供支持。
煤基活性炭制备工艺研究

煤基活性炭制备工艺研究煤基活性炭是一种重要的吸附材料,具有高比表面积、孔隙度大、吸附能力强等优点。
本文对煤基活性炭的制备工艺进行研究。
制备原料:本实验采用的原料为褐煤,煤质为干基灰分12.5%,挥发分45.6%,固定碳34.8%,全硫1.78%,水分1.2%。
制备工艺:将褐煤粉末置于加热炉中进行焦化,焦化过程中,褐煤中的挥发分慢慢被热解出来,同时固定碳逐渐浓缩。
煅烧时分为两个阶段,第一阶段煅烧温度升至300℃,煅烧时间5小时,主要用于除去原料中的水、气态成分和杂质物质。
第二阶段煅烧温度升至800℃,煅烧时间4小时,将固体褐煤焦进行再生,使其分解出一部分孔洞,提高了其比表面积。
在煅烧的第二个时期中,将焦化后的煤粉放置于加热炉中,保持煅烧温度在800℃,加入氮气或水蒸气至2MPa的压力下进行水蒸气或煤气活化。
将煤基原料在800℃高温下气化,使其产生很多孔洞,增加其表面积和孔隙度,提高其吸附性能。
活化后,经水洗、干燥、烘烤后制成煤基活性炭。
控制工艺参数:在煅烧和活化的过程中,要注意控制工艺参数,以保证制备出的煤基活性炭具有较好的吸附性能。
控制的参数主要包括煅烧温度、煅烧时间、流动速率、气氛等。
煅烧温度适合在800℃左右,这样可以保证充分焦化并生成大量活性基团。
煅烧时间在5-6小时内,可以达到焦化的目的。
在活化过程中,气氛要尽量保持惰性气体,以免对煅焦样品产生影响。
流量速率适合在20-30mL/min,可以保证反应充分。
检测煤基活性炭的吸附性能:通过检测制备出的煤基活性炭的吸附性能,可以评价其质量是否合格。
常使用的检测方法有恒重法、氮气吸附法、甲醇蒸汽吸附法等。
其中,氮气吸附法是一种比较直接、简单的检测方法,可以获得煤基活性炭的比表面积、孔径分布、孔体积等指标。
一般来说,制备出的煤基活性炭的比表面积应该在800-1200m2/g之间。
煤基活性炭制备工艺研究
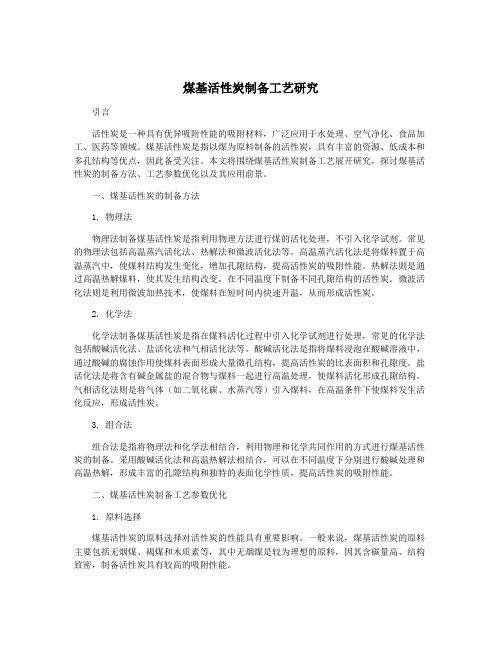
煤基活性炭制备工艺研究引言活性炭是一种具有优异吸附性能的吸附材料,广泛应用于水处理、空气净化、食品加工、医药等领域。
煤基活性炭是指以煤为原料制备的活性炭,具有丰富的资源、低成本和多孔结构等优点,因此备受关注。
本文将围绕煤基活性炭制备工艺展开研究,探讨煤基活性炭的制备方法、工艺参数优化以及其应用前景。
一、煤基活性炭的制备方法1. 物理法物理法制备煤基活性炭是指利用物理方法进行煤的活化处理,不引入化学试剂。
常见的物理法包括高温蒸汽活化法、热解法和微波活化法等。
高温蒸汽活化法是将煤料置于高温蒸汽中,使煤料结构发生变化,增加孔隙结构,提高活性炭的吸附性能。
热解法则是通过高温热解煤料,使其发生结构改变,在不同温度下制备不同孔隙结构的活性炭。
微波活化法则是利用微波加热技术,使煤料在短时间内快速升温,从而形成活性炭。
2. 化学法化学法制备煤基活性炭是指在煤料活化过程中引入化学试剂进行处理,常见的化学法包括酸碱活化法、盐活化法和气相活化法等。
酸碱活化法是指将煤料浸泡在酸碱溶液中,通过酸碱的腐蚀作用使煤料表面形成大量微孔结构,提高活性炭的比表面积和孔隙度。
盐活化法是将含有碱金属盐的混合物与煤料一起进行高温处理,使煤料活化形成孔隙结构。
气相活化法则是将气体(如二氧化碳、水蒸汽等)引入煤料,在高温条件下使煤料发生活化反应,形成活性炭。
3. 组合法组合法是指将物理法和化学法相结合,利用物理和化学共同作用的方式进行煤基活性炭的制备。
采用酸碱活化法和高温热解法相结合,可以在不同温度下分别进行酸碱处理和高温热解,形成丰富的孔隙结构和独特的表面化学性质,提高活性炭的吸附性能。
二、煤基活性炭制备工艺参数优化1. 原料选择煤基活性炭的原料选择对活性炭的性能具有重要影响。
一般来说,煤基活性炭的原料主要包括无烟煤、褐煤和木质素等,其中无烟煤是较为理想的原料,因其含碳量高、结构致密,制备活性炭具有较高的吸附性能。
2. 活化剂选择活化剂的选择对制备煤基活性炭也具有重要影响。
活性炭生产工艺简介

1.煤质活性炭主流生产工艺及产污分析(1)生产工艺流程煤质活性炭生产工艺主要工序为破碎磨粉、成型、炭化、活化、成品处理等。
回转炉炭化、斯列普炉活化工艺流程是国内煤质活性炭生产的主流工艺,主要分布在宁夏、山西,约占全国煤质活性炭生产企业总数的72%。
图1 活性炭生产工艺流程图合格的原料煤入厂后,被粉碎到一定细度(一般为200目),然后配入适量黏结剂(一般为煤焦油)在混捏设备中混合均匀,然后在一定压力下用一定直径模具挤压成炭条,炭条经炭化、活化后,经筛分、包装制成成品活性炭。
(2)生产过程中的排污节点、污染物排放种类、排放方式破碎磨粉工序排放颗粒物(煤尘),排放方式主要是有组织排放。
成型工序排放颗粒物(煤尘)、挥发性有机物,多以无组织形式逸散。
炭化、活化工序排放的主要污染物为颗粒物、SO2、NO X、苯并[a]芘(BaP)、苯、非甲烷总烃(NMHC)及氰化氢(HCN),排放方式为有组织排放。
具体详见下表。
表1 煤质活性炭污染物排放方式、排放种类、行业特征污染物(3)无组织排放煤质活性炭工业生产过程无组织排放节点有混捏成型工序、煤焦油储罐区、炭化工序车间门窗处、成型料晾晒场等。
排放的污染物为挥发性有机物和一氧化碳。
污染末端治理(1)磨粉、混捏、成品筛分包装工序粉尘治理活性炭行业磨粉、混捏、成品筛分包装工序产生粉尘污染,磨粉工序生产设备内产生的粉尘经旋风除尘器及布袋除尘器收集,并作为原料回用,除尘效率98%以上。
新建和大型企业成品筛分包装工序有回收设施回收,规模较小企业存在无组织排放现象。
混捏工序无组织废气无处理措施,通过标准制定,引导企业治理后排放。
(2)炭化炉尾气治理炭化炉尾气主要化学组成是焦油蒸汽、CH4、H2、CO、N2、CO2、O2及沥青烟等,大部分为可燃或助燃气体,可回收利用。
焚烧法是把炭化尾气引入焚烧炉内在高强转化燃烧的情况下,使之转化为CO2、H2O等高温气体,高温气体的热能又用于余热锅炉产生蒸汽。
煤基活性炭制备工艺研究

煤基活性炭制备工艺研究煤基活性炭是一种具有高比表面积、孔隙度大等优点的重要工业材料。
其制备工艺的研究是制备高品质煤基活性炭的关键。
本文将从煤基活性炭制备的工艺流程、制备工艺参数优化以及材料特性等方面综述煤基活性炭制备工艺的研究进展。
1. 工艺流程煤基活性炭的制备工艺流程主要包括原料处理、干燥、炭化、活化等步骤。
1.1 原料处理煤作为煤基活性炭的主要原料,需要进行物理、化学处理,除去其中的杂质、灰分、硫等,以保证制备出的煤基活性炭品质良好。
此外,原料的粒度大小和煤种选择也会影响活性炭的品质。
1.2 干燥为了避免活化过程中水分蒸发带来的影响,需要将原料进行干燥处理,使其含水率降至一定水平。
1.3 炭化炭化是指在一定条件下将原料进行热解,使其中的有机物转化成碳酸盐以及一部分煤醚。
炭化的条件包括温度、时间、升降温速度等,会直接影响煤基活性炭的孔隙度、比表面积等特性。
炭化后的煤基材料需要进行活化。
活化过程可以分为化学活化和物理活化两种类型。
化学活化是将炭化的材料进行氧化处理,使其中的碳酸盐分解,产生大量二氧化碳和水,从而形成大量的孔隙结构;物理活化则是在相对较高的温度和压力下将炭化的材料与蒸汽或空气等作用剂接触,形成孔隙结构。
活化条件的选择与活化剂的种类、浓度密切相关。
在活化过程中,需要控制的参数包括活化温度、时间、活化剂种类和浓度等。
2. 工艺参数的优化研究表明,煤基活性炭的制备工艺参数对活性炭的孔隙度、比表面积等特性有着十分显著的影响。
下面就几个重要参数进行阐述。
炭化温度直接影响煤基活性炭的孔隙度。
随着炭化温度的上升,煤基材料的孔隙结构不断变大,孔径不断增大,孔隙度也不断提高。
但当炭化温度过高时,孔隙结构的增长速率减缓,同时炭与氧气反应的副反应也会增加,使得孔隙可操作空间缩小,煤基活性炭的吸附性能下降。
2.2 活化温度活化温度也是影响煤基活性炭孔隙度和比表面积的重要因素。
活化温度较大时,孔隙结构增大,但过大的活化温度也会导致孔隙结构破坏,产生孔堵塞现象。
活性炭炭化工艺和活化工序介绍

活性炭炭化工艺条件:炭化本应是在隔绝空气的条件下加热干馏,但在实际生产中,由于炭化炉内是负压状态,生产系统又不可能绝对严密,导致必须有部分空气带入炭化系统,及造成炉内炭化料的燃烧,甚至抽出物料堵塞设备管道。
根据经验炭化炉内负压应控制在30~100Pa之间。
炭化过程中最重要的因素是炭化最终温度和炭化升温速度,在实际生产过程中,炭化升温速度一般粒径 5.0~7.0mm的粗粒为8℃/min为好;粒径3.0~5.0mm的中等料以10℃/min为好;粒径小于 3.0mm以12℃/min为好。
炭化是生产活性炭的重要工序之一,炭化质量好坏直接影响下一步活化的操作以及最终产品的质量。
成型物料的炭化,是指在较低温度(600℃以下)条件下,物料中煤焦油低分子物质的挥发和煤及沥青的热分解和固化的过程。
由于从进炭化炉的低温到出炉的高温,成型物料在前进、上下运动中除了使颗粒变短变均匀外,更为重要的是将条料中的挥发分随温度的不断升高由炭粒间不断逸出,当炭化料最终出炉时达到规定要求。
活性炭活化工序是活性炭生产过程中最关键的工序,它直接影响到活性炭产品的性能、成本和质量。
活化采用斯列普活化炉活化,这是一种以水蒸汽和烟道气为活化剂的炉型。
活化温度是决定活性炭孔隙结构形成速度的主要因素之一。
活化主反应为可逆吸热反应,根据热力学反应定律,提高反应温度有利于正反应进行,即可提高活化反应速度。
但温度过高,活性炭的孔隙结构易发生变化,微孔减小,大孔增加,强度下降,得率减小。
而水处理用柱状活性炭对强度有较严格的要求,因此,活化温度的选择应兼顾吸附能力和强度二者的关系。
表7为活化温度对活性炭吸附性能的影响。
为维持正常的活化反应温度,须向活化炉加热半炉的不同位置加入二次空气,与混合气体中的可燃气体燃烧放出大量热量,主要反应如下:由于放出的热量足以使活化反应处于热平衡状态,两半炉之间定期交替运行,使活化温度稳定、活化效果好,产品质量均匀、吸附能力强。
斯列普火化炉烘炉经验技巧总结
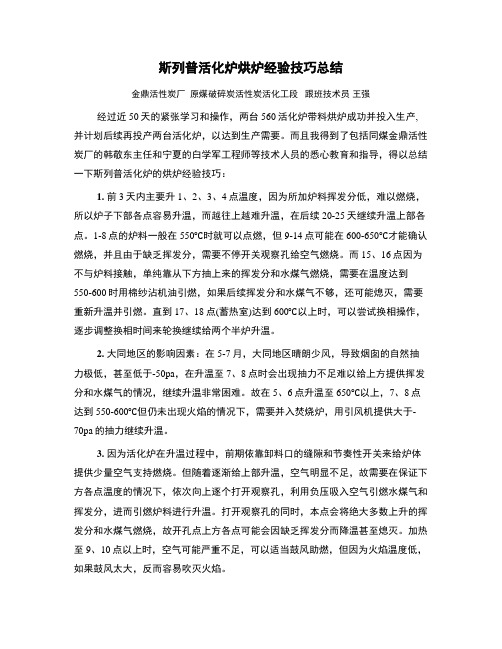
斯列普活化炉烘炉经验技巧总结金鼎活性炭厂原煤破碎炭活性炭活化工段跟班技术员王强经过近50天的紧张学习和操作,两台560活化炉带料烘炉成功并投入生产,并计划后续再投产两台活化炉,以达到生产需要。
而且我得到了包括同煤金鼎活性炭厂的韩敬东主任和宁夏的白学军工程师等技术人员的悉心教育和指导,得以总结一下斯列普活化炉的烘炉经验技巧:1.前3天内主要升1、2、3、4点温度,因为所加炉料挥发分低,难以燃烧,所以炉子下部各点容易升温,而越往上越难升温,在后续20-25天继续升温上部各点。
1-8点的炉料一般在550℃时就可以点燃,但9-14点可能在600-650℃才能确认燃烧,并且由于缺乏挥发分,需要不停开关观察孔给空气燃烧。
而15、16点因为不与炉料接触,单纯靠从下方抽上来的挥发分和水煤气燃烧,需要在温度达到550-600时用棉纱沾机油引燃,如果后续挥发分和水煤气不够,还可能熄灭,需要重新升温并引燃。
直到17、18点(蓄热室)达到600℃以上时,可以尝试换相操作,逐步调整换相时间来轮换继续给两个半炉升温。
2.大同地区的影响因素:在5-7月,大同地区晴朗少风,导致烟囱的自然抽力极低,甚至低于-50pa,在升温至7、8点时会出现抽力不足难以给上方提供挥发分和水煤气的情况,继续升温非常困难。
故在5、6点升温至650℃以上,7、8点达到550-600℃但仍未出现火焰的情况下,需要并入焚烧炉,用引风机提供大于-70pa的抽力继续升温。
3.因为活化炉在升温过程中,前期依靠卸料口的缝隙和节奏性开关来给炉体提供少量空气支持燃烧。
但随着逐渐给上部升温,空气明显不足,故需要在保证下方各点温度的情况下,依次向上逐个打开观察孔,利用负压吸入空气引燃水煤气和挥发分,进而引燃炉料进行升温。
打开观察孔的同时,本点会将绝大多数上升的挥发分和水煤气燃烧,故开孔点上方各点可能会因缺乏挥发分而降温甚至熄灭。
加热至9、10点以上时,空气可能严重不足,可以适当鼓风助燃,但因为火焰温度低,如果鼓风太大,反而容易吹灭火焰。
煤基活性炭制备工艺研究
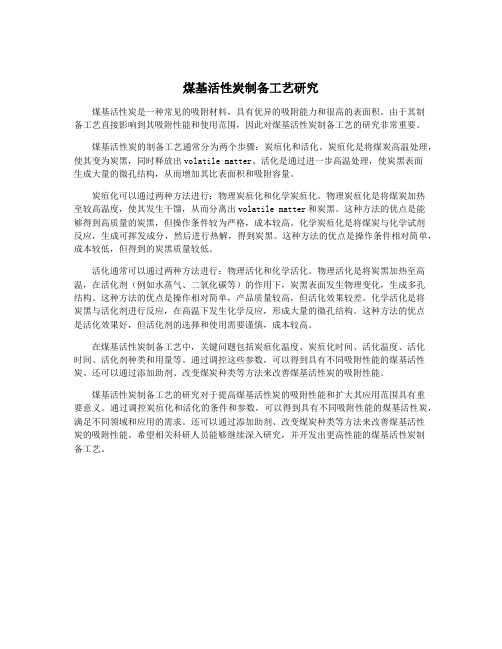
煤基活性炭制备工艺研究煤基活性炭是一种常见的吸附材料,具有优异的吸附能力和很高的表面积。
由于其制备工艺直接影响到其吸附性能和使用范围,因此对煤基活性炭制备工艺的研究非常重要。
煤基活性炭的制备工艺通常分为两个步骤:炭疽化和活化。
炭疽化是将煤炭高温处理,使其变为炭黑,同时释放出volatile matter。
活化是通过进一步高温处理,使炭黑表面生成大量的微孔结构,从而增加其比表面积和吸附容量。
炭疽化可以通过两种方法进行:物理炭疽化和化学炭疽化。
物理炭疽化是将煤炭加热至较高温度,使其发生干馏,从而分离出volatile matter和炭黑。
这种方法的优点是能够得到高质量的炭黑,但操作条件较为严格,成本较高。
化学炭疽化是将煤炭与化学试剂反应,生成可挥发成分,然后进行热解,得到炭黑。
这种方法的优点是操作条件相对简单,成本较低,但得到的炭黑质量较低。
活化通常可以通过两种方法进行:物理活化和化学活化。
物理活化是将炭黑加热至高温,在活化剂(例如水蒸气、二氧化碳等)的作用下,炭黑表面发生物理变化,生成多孔结构。
这种方法的优点是操作相对简单,产品质量较高,但活化效果较差。
化学活化是将炭黑与活化剂进行反应,在高温下发生化学反应,形成大量的微孔结构。
这种方法的优点是活化效果好,但活化剂的选择和使用需要谨慎,成本较高。
在煤基活性炭制备工艺中,关键问题包括炭疽化温度、炭疽化时间、活化温度、活化时间、活化剂种类和用量等。
通过调控这些参数,可以得到具有不同吸附性能的煤基活性炭。
还可以通过添加助剂、改变煤炭种类等方法来改善煤基活性炭的吸附性能。
煤基活性炭制备工艺的研究对于提高煤基活性炭的吸附性能和扩大其应用范围具有重要意义。
通过调控炭疽化和活化的条件和参数,可以得到具有不同吸附性能的煤基活性炭,满足不同领域和应用的需求。
还可以通过添加助剂、改变煤炭种类等方法来改善煤基活性炭的吸附性能。
希望相关科研人员能够继续深入研究,并开发出更高性能的煤基活性炭制备工艺。
- 1、下载文档前请自行甄别文档内容的完整性,平台不提供额外的编辑、内容补充、找答案等附加服务。
- 2、"仅部分预览"的文档,不可在线预览部分如存在完整性等问题,可反馈申请退款(可完整预览的文档不适用该条件!)。
- 3、如文档侵犯您的权益,请联系客服反馈,我们会尽快为您处理(人工客服工作时间:9:00-18:30)。
煤基活性炭生产用斯列普活化炉生产工艺探讨肖宏生,张文辉(煤炭科学研究总院北京煤化学研究所,北京 100013)摘要:讨论了煤基活性炭生产用斯列普活化炉合理工艺的控制,探讨了降低煤基活性炭生产成本、提高活性炭质量的途径。
关键词:斯列普活化炉;工艺中图分类号:T Q 424 1 文献标识码:A文章编号:1006 6772(2001)01 0057 04收稿日期:2001-01-10作者简介:肖宏生(1965-),男,辽宁庄河人,工程师,长期从事活性炭产品开发和工程设计工作。
煤基活性炭是中国产量最大的活性炭产品,据统计,1999年中国煤基活性炭产量超过9万t,其中产品80%出口。
中国煤基活性炭生产主要采用斯列普活化炉,斯列普活化炉是活化炉的一种,由于其具有生产能力大、产品质量均匀稳定、产品的吸附指标高、能同时生产多种规格活性炭、正常生产时不需外加热源、炉子使用寿命长等特点,因而被国内煤质活性炭厂广为采用。
自20世纪50年代,中国从前苏联引进设计能力为1000t/a 斯列普活化炉后,经过国内几代科研人员的不断改进和重新设计,目前,斯列普活化炉已发展成设计能力为300t/a 、500t/a 、800t/a 、1000t/a 4个系列。
其中500t/a 斯列普活化炉因其造价较低,产出较为合理,国内煤质活性炭厂多采用此炉型,但是国内活性炭厂500t/a 斯列普活化炉工艺控制存在一定差别。
斯列普活化炉工艺参数控制的合理与否直接关系到活化炉的产量、产品质量及炉子的使用寿命。
斯列普活化炉工艺参数控制包括炭化料、加料与卸料、活化温度、蓄热室顶部温度、燃烧室温度、通入活化炉的蒸汽压力与流量、通入活化炉的空气压力与流量、炉内压力、加热半炉氧含量、加热半炉与冷却半炉切换周期。
本文根据笔者多年经验就500t/a 斯列普活化炉的合理工艺参数的控制、生产成本的降低和产品质量的提高进行了探讨。
1 炭化料质量对斯列普活化炉操作的影响炭化料是加入活化炉进行活化的原料。
炭化料的质量直接影响活性炭的质量、产量及炉子的使用寿命。
对炭化料的要求主要包括炭化料的热稳定性、强度、灰熔点、灰分含量、堆积重、粒度、挥发分、水分及水容量。
炭化料的热稳定性要好,其在高温下不能碎裂及有结块性。
炭化料若有结块性,其在活化炉的补充炭化带就会结块堵塞活化炉的产品道;炭化料若在高温下碎裂,则会使料层致密,活化介质不易穿透料层,造成活化不均匀,产品的吸附指标难于提高,活化料中常有过烧现象即白点或白条。
另外,由于炭化料的碎裂容易导致活化炉产品道膨料造成产品道堵塞。
国内曾有一活性炭生产厂尝试用斯列普活化炉直接活化宁夏太西无烟煤生产无烟煤破碎炭,结果表明产品的吸附指标很难提高,活化料中白点很多,过烧现象严重,产品道堵塞,尽管太西无烟煤挥发分很低,初孔结构比较发达,但是活化效果并不理想,这主要因为太西无烟煤热稳定性不好,在高温下碎裂,大颗粒碎成小颗粒,小颗粒碎成更小颗粒,致使料层致密,活化介质不易穿透,活化不均匀所致。
炭化料的强度低,活性炭成品的强度也低,同时也容易使产品道堵塞。
一般要求炭化料的强度不小于90%。
炭化料的灰熔点要大于1000 。
灰熔点低,一旦炭化料在活化炉内被烧成灰,灰就会熔化成玻璃态物质粘在活化炉产品道上,堵塞产品道且无法挽救,降低活化炉的产量,最终导致活化炉停炉更换炉芯。
灰分是活性炭中的无效成分,炭化料的灰分含量越低越好。
通常炭化料的灰分含量根据成品活性炭的灰分要求而定。
斯列普活化炉的基本原理是原料借助自身的重力沿产品道垂直向下移动,在移动的过程中不断与水平方向流过的活化介质接触发生活化反应。
炭化料的堆积重过低,炭化料容易在产品道内膨料,活化将不能有效进行。
一般要求炭化料的堆积重不小于0 4g/cm3。
加入活化炉内的炭化料粒度不能过大也不能过小,粒度过大过小都会造成膨料。
合适的炭化料粒度一般为1~6mm,小于1mm不能超过0 1%。
目前,国内斯列普活化炉产品道宽度一般为11~ 20mm。
对于产品道宽度在16~20mm之间的,炭化料的粒度最大不宜大于10mm。
虽然产品道加宽有利于提高活化炉的产量,但却不利于小粒径产品的活化,这主要是因为产品道加宽相当于小粒径产品料层致密加厚,不利于活化介质的穿透。
实践证明,产品道宽度在16~20mm之间,对于小粒径产品的活化极不均匀,产品吸附指标难于提高,产品过烧现象严重。
笔者认为合适的产品道宽度为11~16mm。
炭化料挥发分含量的高低反映炭化料中焦油沥青的分解程度。
挥发分含量高,焦油沥青分解程度达不到要求,炭化料会在活化炉不充炭化带结焦堵塞活化炉产品道。
一级炭化料的挥发分为6%~ 8%;二级炭化料的挥发分为8%~10%;三级炭化料的挥发分为10%~12%。
炭化料的挥发分不小于15%极易在活化炉补充炭化带结焦,不宜加入炉内。
国内常有一些煤质活性炭生产厂将挥发分不小于15%的炭化料加入炉内导致产品道堵塞,活化炉不能正常运行的现象,影响活化炉的产量和寿命。
炭化料的水分一般要求不大于8%。
水分过高将会降低活化带上部温度,不利于活化进行。
另外,水分过高,炭化料表面易粘炭粉,造成活化炉产品道膨料、烧灰、结瘤,堵塞产品道。
炭化料要有一定的初孔结构,活化方能有效进行。
衡量炭化料初孔结构的指标则为水容量。
水容量越高,炭化料的初孔结构越发达,活化越容易进行。
但是炭化料的初孔结构是有限度的,初孔太多,炭化料的强度降低。
煤制炭化料的水容量一般为22%~40%,实际生产中一般都控制在30%左右。
2 斯列普活化炉加料与卸料周期的确定一般情况,活化炉每8h加料一次,特殊品种可4h加料一次,加满为止。
加料后的料槽,炭化料不得低于料槽口10cm。
不加料的料槽,不得提前打开水封盖。
一般情况下,活化炉料槽中的炭化料下沉深度不应超过80cm,当更换另一品种时,炭化料的下沉深度可允许不超过1m,否则活化炉炉顶容易喷火。
一般8h加料一次可满足活化炉料槽内下沉深度不超过80cm的要求。
活化炉不能长时间不卸料,否则产品道容易膨料。
一般情况,活化炉每隔1h卸一回料,每一回的卸料次数应根据活性炭的质量要求而定。
为了延长炉子的寿命,既不能频繁卸料,也不能长时间不卸料,料不能在炉内停留时间过长,即使卸出的料可能不合格,也要将料少许卸出。
3 斯列普活化炉操作温度的确定通常炭和气体的反应速度随着温度的升高而增大。
因此气体活化需在高温下进行,但活化温度不能任意提高。
温度太高,炭的孔结构会发生变化,微孔减少,反而使吸附力下降,特别是活化温度超过950 时,水蒸气的扩散速度的影响马上就表现出来,活化不能有效进行,比表面积的增加率变小。
另外温度太高,炭的烧失率增大,得率下降,又容易造成炭中的灰分在高温下熔融结瘤堵塞产品道。
若温度过低,又能引起产量下降,因此蒸汽活化法和烟道气活化法的活化温度一般控制在850~ 920 。
斯列普活化炉的活化过程即为水蒸气和烟道气的交替活化,故其活化温度应控制在850~ 920 ,实践证明斯列普活化炉在此温度范围内运行较为理想。
活化炉内各点温度要求尽量均匀,控制1~8点的温度不大于920 ,为了正确保持活化温度,可调节空气的加入量。
当炉内各点温度均高于规定的温度时,应关小空气总管的蝶阀;炉温局部过高,则应关小该处的空气蝶阀或盲板,减小空气的加入量,反之则应增加该处的空气供应量。
在调整空气流量时,严禁猛增或猛减,必须根据炉内各点的温度变化情况缓慢调整,以防止炉温猛烈跳动。
4 蓄热室顶部温度蓄热室顶部温度要求为1000~1100 ,在此温度下,才能保证炉内活化带的温度,并能把炉气中的CO充分燃烧。
若该点温度超过1100 ,由于蓄热室顶部是耐热混凝土构件,内部又是用普通粘土质耐火砖堆积起来的,容易被烧坏,影响蓄热室的寿命。
若该点温度低于1000 ,又会降低活化带上部的温度,不利于活化的正常进行。
调整蓄热室顶部温度的方法是通过调整上连烟道配风管的蝶阀或盲板,以增减进入上连烟道的空气量,温度过高将其关小,反之将其开大。
5 燃烧室温度燃烧室也称下连烟道,活化炉两半炉通过燃烧室连接起来。
燃烧室温度一般控制在900~950 ,在此温度下,才能保证活化炉1、2两点的温度,并能使冷却半炉活化反应过来的煤气部分燃烧。
若该点温度超过950 ,活化炉1、2两点的温度就会高于920 。
若该点温度低于900 ,活化炉1、2两点的温度就会偏低。
燃烧室温度的调整方法是通过调整燃烧室顶部配风管的蝶阀或盲板,以增减进入燃烧室的空气量,温度过高将其关小,反之将其开大。
6 通入活化炉的蒸汽压力与流量水蒸气是斯列普活化炉生产过程中的主要活化剂,为了保证炭与水蒸气充分接触,加速活化反应,提高活化效率,实际蒸汽的通入量必须大大超过理论需要量。
根据多年的生产实践,对于500t/a斯列普活化炉,蒸汽压力在0 20 02M Pa (表压)范围内,蒸汽流量控制在100025kg/h 比较合理。
若蒸汽压力不在此范围内,应根据蒸汽压力-流量校正表进行调整。
蒸汽流量过低,活化反应缓慢,产量下降;蒸汽流量过高,引起炉压上升,烧失率增加。
为了保证蒸汽流量和炉压稳定,必须控制进入活化炉内的蒸汽压力,一般控制在0 20 02M Pa(表压)。
进入活化炉的水蒸气管路上要设有疏水装置,以除去进入活化炉内水蒸气中的水分,否则水蒸气中的水分会使蓄热室底部的璇拱损坏,致使蓄热室内的格子砖坍塌,活化炉将被迫停炉。
7 通入活化炉内的空气压力与流量进炉空气压力不能过大也不能过小,进炉空气压力过大,活化炉烟道内的火焰太长,甚至会进入水平气道与炭燃烧,造成炭的烧失率增加,活性炭的得率下降。
由于活化炉是微正压生产,进炉空气压力过小,活化反应产生的煤气就会进入空气管道,引起空气管道爆炸,因此控制进炉空气压力十分重要。
一般进炉空气压力为294 2~343 2Pa比较合适。
进入活化炉的空气流量过大,炉温会过高,随之炭的烧失量增大,活性炭得率下降,并且容易引起炉内温度局部过热,导致炭中的灰分熔融成玻璃态物质堵塞产品道;空气流量过小,炉温下降,活性炭产量下降。
对于500t/a斯列普活化炉,其空气流量为1100m3/h左右比较合适。
通过调整空气总管蝶阀及炉体各点配风口处蝶阀或盲板可调整进炉空气压力及流量。
8 炉内压力活化炉必须微正压操作,炉内压力过高,容易从炉体各部位喷出活化气体,引起炉外燃烧,影响安全和炉子的寿命;炉压过低,甚至变为负压,就容易从炉外吸进空气,炉温急剧上升,使炉温无法控制,且炭的烧失严重,产品道容易堵塞,严重时,吸进空气中的氧与炉内活化反应的煤气混合,在高温条件下产生爆炸,所以应严格控制活化炉内各点的压力。
一般保持活化炉压力最低点(3、4点即下远烟道处)压力为9 8~49Pa。
控制炉压的方法是调节烟道总闸阀,开大烟道总闸阀,可增大抽力降低炉压,反之可提高炉压。