电阻炉温度控制系统
基于单片机的电阻炉温度控制系统设计

基于单片机的电阻炉温度控制系统设计一、引言电阻炉是一种广泛应用于工业生产中的加热设备,其温度控制的准确性对于工艺过程的稳定和产品质量的保证至关重要。
本文将基于单片机设计一个电阻炉温度控制系统,通过采集温度传感器的信号,用单片机控制加热器的工作状态,实现对电阻炉温度的精确控制。
二、系统结构设计本系统由四个模块组成:温度采集模块、温度控制模块、显示模块和控制模块。
1.温度采集模块:使用一个高精度的温度传感器,如PT100,将电阻炉内部的温度转化为电压信号。
该信号经过模拟转数字转换器(ADC)转换为数字信号,传输给单片机。
2.温度控制模块:根据温度采集模块传输的信号,单片机通过PID算法计算出控制值,并输出PWM信号控制加热器的工作状态。
PID算法可根据实际情况进行参数调整,以达到系统稳定的控制效果。
3.显示模块:采用数码管或液晶显示器显示当前电阻炉的温度值,方便操作员实时监测电阻炉的运行状态。
4.控制模块:可以通过按钮或者触摸屏等方式进行设定和调整控制参数,例如设定温度范围、PID参数调节等。
三、系统工作原理1.系统初始化:单片机启动后,进行相应的外设初始化和参数设定,包括温度采集模块的配置、PID参数的设定、显示模块的显示等。
2.温度采集与转换:通过温度传感器采集电阻炉内部的温度信号,将其转化为模拟电压信号。
利用ADC将模拟信号转换为数字信号,并传输给单片机进行处理。
3.PID算法计算:单片机根据采集到的温度值,通过PID算法计算出控制值。
PID控制算法通常包括比例系数(P)、积分系数(I)和微分系数(D)三个参数的调整,根据实际情况进行调节以达到控制精度和稳定性要求。
4.PWM输出控制:根据PID算法计算得到的控制值,单片机输出对应的PWM信号。
该信号通过驱动电路控制加热器的工作状态,调整和维持电阻炉的温度。
5.温度显示:单片机将当前的温度值通过显示模块进行显示,使操作员能够实时监测到电阻炉的温度。
电阻炉温度控制系统ppt
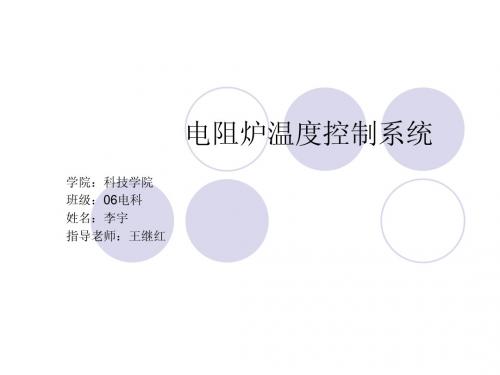
LED数码管显示程序设计
对多个八段LED数码管的接口方法主要有两 种:动态驱动法和静态驱动法。本文的LED 数码管显示采用串口静态显示 。这种பைடு நூலகம்法 用于显示位数较少,显示亮度较大的地方 效果较好 。
键盘程序设计
电阻炉温度控制系统
学院:科技学院 班级:06电科 姓名:李宇 指导老师:王继红
本文用8031单片机实现电阻炉温度的控制。 电阻炉是一类使用非常广泛的工业设备, 利用单片机实现温度的实时控制,对提高 劳动生产率和产品质量,节约能源都有着 积极意义。随着电子技术的发展,特别是 单片机计算机的出现,对被控制对象采用 功能强、体积小、价格低的智能化温度控 制装置进行控制成为现实。本文将介绍用 单片机对热水电阻炉进行温度控制的过程。
电阻炉温度控制系统原理框图
在温度控制系统中,温度检测及放大任务 通常用温度变送器来完成。为了降低成本, 简化结构,本系统采用了 OP07型温度变送 器的输入回路部份 ,本控制系统输入通道用 测温电路和精密放大器,省去可采样保持 器;输出通道取消了D/A转换器,执行机构 选用了可控硅控制器。从而使整个控制系 统结构简单,操作方便,控制精度高,具 有很高的性价比 .
主程序设计
整个系统包括管理程序和控制程序两部分, 管理程序是对显示LED进行动态刷新,处理 键盘的扫描和响应、进行掉电保护的处理、 执行中断服务操作等。控制程序是对被控 对象进行采样、数据处理,根据控制算法 进行计算和输出等。
上限报警处理程序设计
本文采用音乐声报警。单频音报警单路, 简单实用,已能满足音响报警的一般需要。 不足之处在于音调单一,而且采用压电鸣 音元件,音量也较小,且不可调整。
8031芯片介绍
8031是由8个部件组成,即CPU,时钟电路, 数据存储器,并行口(P0~P3)串行口, 定时计数器和中断系统。 8031有五个中断源,即外部中断两个,定 时计数中断两个,串行中断一个,全部的 中断分为高和低的两个输出级 .
电阻炉温度控制系统
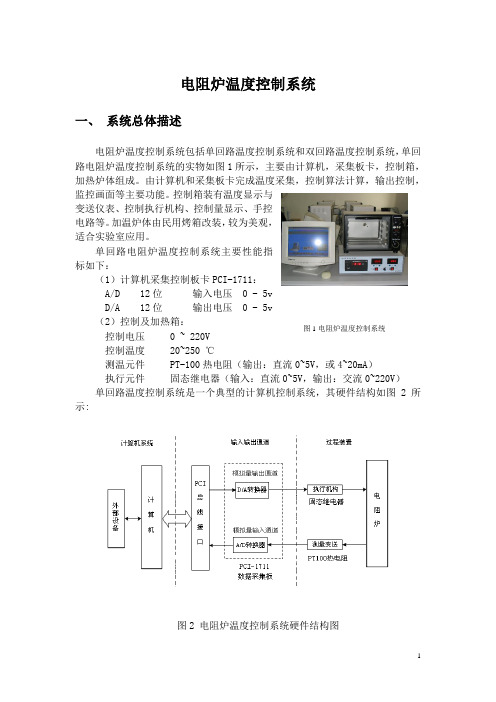
电阻炉温度控制系统一、 系统总体描述电阻炉温度控制系统包括单回路温度控制系统和双回路温度控制系统,单回路电阻炉温度控制系统的实物如图1所示,主要由计算机,采集板卡,控制箱,加热炉体组成。
由计算机和采集板卡完成温度采集,控制算法计算,输出控制,监控画面等主要功能。
控制箱装有温度显示与变送仪表、控制执行机构、控制量显示、手控电路等。
加温炉体由民用烤箱改装,较为美观,适合实验室应用。
单回路电阻炉温度控制系统主要性能指标如下:(1)计算机采集控制板卡PCI-1711:A/D 12位 输入电压 0 - 5vD/A 12位 输出电压 0 - 5v(2)控制及加热箱: 控制电压 0 ~ 220V控制温度 20~250 ℃测温元件 PT-100热电阻(输出:直流0~5V ,或4~20mA )执行元件 固态继电器(输入:直流0~5V ,输出:交流0~220V )单回路温度控制系统是一个典型的计算机控制系统,其硬件结构如图2所示:图2电阻炉温度控制系统硬件结构图图1电阻炉温度控制系统二、硬件系统设计系统的硬件设计包括传感器、执行器、A/D 和D/A 的设计,而PCI 总线接口属于计算机的系统总线,下面分别加以详细介绍。
1、传感器设计温度传感器有热电阻和热电偶,热电阻最大的特点是工作在中低温区,性能稳定,测量精度高。
系统中电炉的温度被控制在0~250℃之间,为了留有余地,我们要将温度的范围选在0~400℃,它为中低温区,所以本系统选用的是热电阻PT100作为温度检测元件,实物如图3所示。
热电阻中集成了温度变送器,将热电阻信号转换为0~5V 的标准电压信号或4~20mA 的标准电流信号输出,供计算机系统进行数据采集。
热电阻传感器是利用电阻随温度变化的特性制成的温度传感器。
热电阻传感器按其制造材料来分,可分为金属热电阻和半导体热电阻两大类;按其结构来分,有普通型热电阻、铠装热电阻和薄膜热电阻;按其用途来分,有工业用热电阻、精密的和标准的热电阻。
电阻炉温度控制系统设计
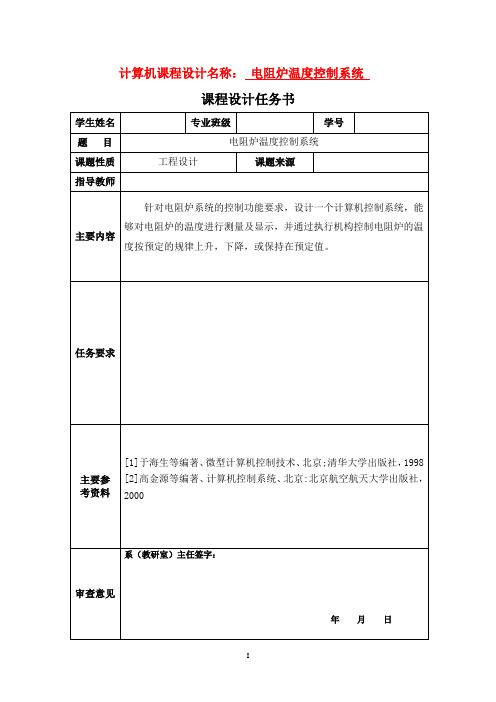
计算机课程设计名称:电阻炉温度控制系统课程设计任务书1 引言1.1课题背景自从发现电流的热效应(即楞茨-焦耳定律)以后,电热法首先用于家用电器,后来又用于实验室小电炉。
随着镍铬合金的发明,到20世纪20年代,电阻炉已在工业上得到广泛应用。
电阻炉是利用电流使炉内电热元件或加热介质发热,从而对工件或物料加热的工业炉。
工业上用的电阻炉一般由电热元件、砌体、金属壳体、炉门、炉用机械和电气控制系统等组成。
1.2控制对象电阻炉在化工、冶金等行业应用广泛,电阻炉中最重要的被控量就是温度。
因此温度控制在工业生产和科学研究中具有重要意义。
1.3功能及技术要求为了保证生产过程正常安全的进行,提高产品的质量和数量,以及减轻工人的劳动强度,节约能源,对加热用的各种电炉要求在一定条件下保持恒温,不能随电源电压波动或炉内物体而变化;或者有的电炉的炉温根据工艺要求按照某个指定的升温或保温规律而变化等等。
因此,对温度不仅要不断地测量,而且还进行控制。
对温度的控制要求是先进、可靠、经济、安全,能满足热处理工艺的要求,并保证工艺的稳定和再现性,节省能源,保护环境,改善劳动环境,降低生产成本,提高机械化和自动化水平。
2 总体方案设计2.1方案设计根据设计任务的要求,采用80C51单片机系统组成的数字控制器代替常规模拟调节器。
整个系统在规定的采样时刻经过A/D 转换采集由温度传感器ADC0809反馈回来的温度反馈测量值,并和给定值进行比较,将经过控制运算后的控制量输出给执行元件控制电阻丝的加热过程。
这样的系统属于直接数字控制(Direct Digital Control ,DDC )系统。
直接数字控制系统中的80C51单片机取代了多个模拟调节器,在不更换硬件的情况下,只要改变程序或调用不同子程序,就可实现各种复杂的控制规律。
此外,系统还应实现人机接口功能。
2.2 系统组成框图及工作原理系统的组成框图如图(2.1)所示。
整个系统由四部分组成,即:80C51单片机系统;温度检测通道;输出控制通道及报警显示系统。
电阻炉温度控制系统的设计
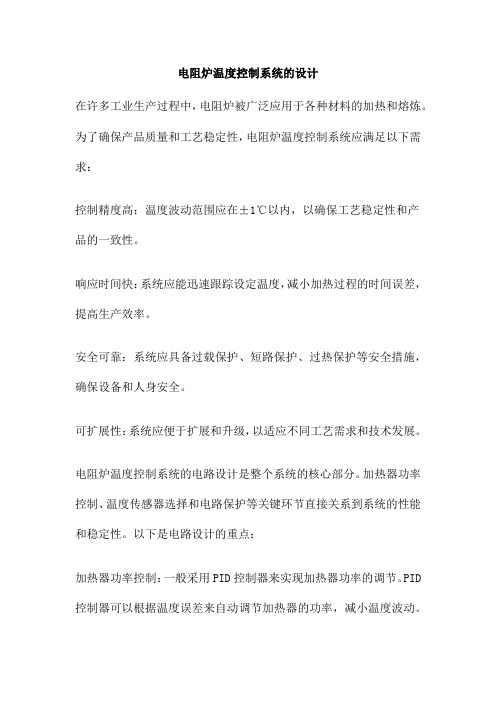
电阻炉温度控制系统的设计在许多工业生产过程中,电阻炉被广泛应用于各种材料的加热和熔炼。
为了确保产品质量和工艺稳定性,电阻炉温度控制系统应满足以下需求:控制精度高:温度波动范围应在±1℃以内,以确保工艺稳定性和产品的一致性。
响应时间快:系统应能迅速跟踪设定温度,减小加热过程的时间误差,提高生产效率。
安全可靠:系统应具备过载保护、短路保护、过热保护等安全措施,确保设备和人身安全。
可扩展性:系统应便于扩展和升级,以适应不同工艺需求和技术发展。
电阻炉温度控制系统的电路设计是整个系统的核心部分。
加热器功率控制、温度传感器选择和电路保护等关键环节直接关系到系统的性能和稳定性。
以下是电路设计的重点:加热器功率控制:一般采用PID控制器来实现加热器功率的调节。
PID 控制器可以根据温度误差来自动调节加热器的功率,减小温度波动。
温度传感器选择:常用的温度传感器有热电偶和红外测温仪。
选择合适的传感器对提高系统的测量精度至关重要。
电路保护:为防止系统故障对设备和人身造成伤害,电路应设计多种保护措施。
例如,加热器应配备熔断器、过载保护器和短路保护器等。
电阻炉温度控制系统的软件设计是实现整个系统智能化的关键。
软件应包括输入输出端口设置、算法实现等关键模块。
以下是软件设计的要点:输入输出端口设置:软件应设置必要的输入输出端口,以便于用户对系统进行控制和监视。
例如,软件应支持通过界面设置加热器的启动/停止、温度设定值等。
算法实现:系统软件应实现高效的温度控制算法,如PID控制算法,以实现精确的温度控制。
算法应具有自适应性,能够根据环境条件和材料属性等变化进行自我调整,提高控制效果。
在完成电阻炉温度控制系统的设计和调试后,需要对系统进行严格的测试与结果验证,以确保系统的性能和稳定性达到预期要求。
测试应包括以下步骤:测试环境搭建:搭建测试平台,选择合适的电阻炉、温度传感器、控制系统等设备进行联调测试。
空载测试:在无负载的情况下,测试系统的加热速度、稳定性和精度等指标。
电阻炉温度控制系统

电阻炉温度控制系统1. 确定总体方案在某煤气/焦碳生产企业中,为了把握工艺规律和控制参数,按比例制作了一台模拟炼焦炉,其中的煤炭采用电阻丝进行加热。
要求控制电阻炉中A点的温度按预定的规律变化,同时监测B点的温度,一旦B点温度超过允许值,就应该发出报警信息、并停止加热。
根据设计任务的要求,采用8031单片机系统组成的数字控制器代替常规模拟调节器。
整个系统在规定的采样时刻经过A/D转换采集由温度传感器反馈回来的温度反馈测量值,并和给定值进行比较,将经过控制运算后的控制量输出给执行元件控制电阻丝的加热过程。
此外,系统还应实现人机接口功能。
系统总体框图如图1所示。
图1 模拟炼焦炉温度控制系统总体框图2. 系统硬件设计按前面的总体设计方案,该系统硬件的设计包括以下几个部分。
⑴人机接口电路本系统允许用户根据需要随时改变系统的工作状态和控制参数,为此设置了4位LED显示和相应的操作键盘,并由专用控制芯片8279实现与CPU的接口。
采用8279后,可以节省CPU用于查询键盘输入和管理显示输出的时间,降低了对CPU处理速度的要求,同时也减少了软件工作量。
⑵温度测量电路热电偶用来检测炉温,将温度值转换为毫伏级的电压信号。
为便于信号远距离传送,采用温度变送器,把热电偶输出信号转换为4~20毫安的电流信号,在接收端再经I/V变换使之变成适于A/D转换的电压信号。
在系统中,采用多路复用方式对两路热电偶信号、冷端补偿信号和标准电压信号进行A/D转换。
系统运行过程中,定期对标准电压进行采样,以修正A/D转换器的灵敏度、保证测控精度。
为提高系统抗干扰能力,在多路转换开关的控制电路A/D转换电路的数字部分中还采用了光电隔离措施。
⑶温度控制电路电阻丝由过零触发型的双向可控硅整流电路驱动,通过调节加热阻丝上的平均电压来控制加热功率,最终达到控制炉温的目的,其原理见图2。
MOC3021是可控硅型光电隔离器件,它只能触发小功率可控硅。
因此,本系统中通过MOC3021控制双向可控硅BCR1,再由BCR1控制主电路的双向可控硅BCR2。
电阻炉温度控制系统的设计

电炉温度控制系统设计摘要热处理是提高金属材料与其制品质量的重要技术手段。
近年来随工业的开展,对金属材料的性能提出了更多更高的要求,因而热处理技术也向着优质、高效、节能、无公害方向开展。
电阻炉是热处理生产中应用最广泛的加热设备,加热时恒温过程的测量与控制成为了关键技术,促使人们更加积极地研制热加工工业过程的温度控制器。
此设计针对处理电阻炉炉温控制系统,设计了温度检测和恒温控制系统,实现了根本控制、数据采样、实时显示温度控制器运行状态。
控制器采用 51 单片机作为处理器,该温度控制器具有自动检测、数据实时采集处理与控制结果显示等功能,控制的稳定性和精度上均能达到要求。
满足了本次设计的技术要求。
关键词:电阻炉,温度测量与控制,单片机目录一、绪论- 1 -选题背景- 1 -电阻炉国开展动态- 1 -设计主要容- 2 -二、温度测量系统的设计要求- 2 -2.1 设计任务- 2 -2.2 系统的技术参数- 2 -2.3 操作功能设计- 3 -三、系统硬件设计- 3 -3.1 CPU选型- 4 -3.2 温度检测电路设计- 4 -3.2.1 温度传感器的选择- 4 -热电偶的测温原理- 5 -3.2.1.2 热电偶的温度补偿- 5 -3.2.2 炉温数据采集电路的设计- 6 -3.2.2.1 MAX6675芯片- 6 -3.2.2.2 MAX6675的测温原理- 6 -3.2.2.3 MAX6675 与单片机的连接- 7 -3.3 输入/输出接口设计- 7 -3.4 保温定时电路设计- 9 -3.4.1 DS1302 与单片机的连接- 10 -3.5 温度控制电路设计- 10 -系统硬件电路图- 12 -四、系统软件设计- 13 -4.1 软件总体设计- 13 -4.2 主程序设计- 13 -4.3 温度检测与处理程序设计- 14 -4.4 按键检测程序设计- 16 -4.5 显示程序设计- 18 -4.6 输出程序设计- 19 -中值滤波- 20 -五、结论- 20 -参考文献- 21 -一、绪论1.1选题背景在现代化的工业生产中,电流、电压、温度、流速、流量、压力和开关量都是常用的主要被控参数。
基于单片机的电阻炉温度控制系统
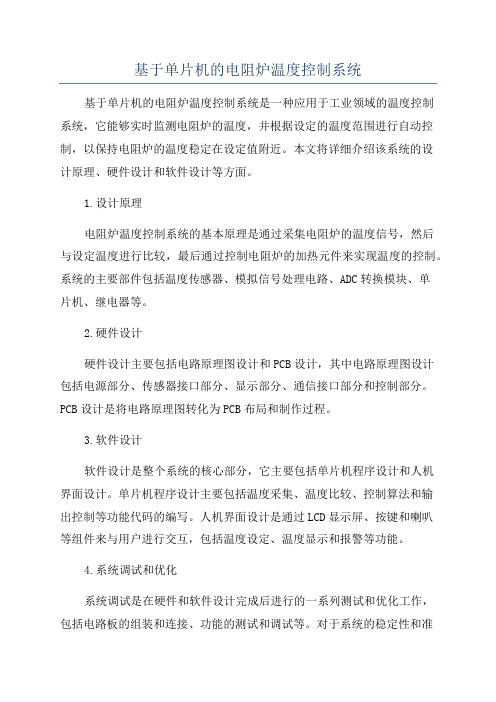
基于单片机的电阻炉温度控制系统基于单片机的电阻炉温度控制系统是一种应用于工业领域的温度控制系统,它能够实时监测电阻炉的温度,并根据设定的温度范围进行自动控制,以保持电阻炉的温度稳定在设定值附近。
本文将详细介绍该系统的设计原理、硬件设计和软件设计等方面。
1.设计原理电阻炉温度控制系统的基本原理是通过采集电阻炉的温度信号,然后与设定温度进行比较,最后通过控制电阻炉的加热元件来实现温度的控制。
系统的主要部件包括温度传感器、模拟信号处理电路、ADC转换模块、单片机、继电器等。
2.硬件设计硬件设计主要包括电路原理图设计和PCB设计,其中电路原理图设计包括电源部分、传感器接口部分、显示部分、通信接口部分和控制部分。
PCB设计是将电路原理图转化为PCB布局和制作过程。
3.软件设计软件设计是整个系统的核心部分,它主要包括单片机程序设计和人机界面设计。
单片机程序设计主要包括温度采集、温度比较、控制算法和输出控制等功能代码的编写。
人机界面设计是通过LCD显示屏、按键和喇叭等组件来与用户进行交互,包括温度设定、温度显示和报警等功能。
4.系统调试和优化系统调试是在硬件和软件设计完成后进行的一系列测试和优化工作,包括电路板的组装和连接、功能的测试和调试等。
对于系统的稳定性和准确性进行优化和改善,如增加滤波电路来提高温度信号的稳定性、使用PID控制算法来提高温度控制的精度等。
5.系统应用该系统可以广泛应用于电子厂、化工厂、冶金厂等工业领域,用于实现电阻炉的精确温度控制。
通过控制电阻炉的温度,可以保证产品质量和生产效率,避免过热或过冷对生产过程的影响。
总结:基于单片机的电阻炉温度控制系统是一种应用广泛的温度控制系统,通过实时监测电阻炉的温度,并根据设定的温度范围进行自动控制,可以稳定地保持电阻炉的温度在设定值附近。
该系统的设计原理、硬件设计和软件设计都有较为详细的介绍和说明,为实现电阻炉的精确温度控制提供了可行的方案。
如有兴趣,欢迎了解。
- 1、下载文档前请自行甄别文档内容的完整性,平台不提供额外的编辑、内容补充、找答案等附加服务。
- 2、"仅部分预览"的文档,不可在线预览部分如存在完整性等问题,可反馈申请退款(可完整预览的文档不适用该条件!)。
- 3、如文档侵犯您的权益,请联系客服反馈,我们会尽快为您处理(人工客服工作时间:9:00-18:30)。
计算机控制技术课程设计成绩评定表设计课题:电阻炉温度控制系统学院名称:电气工程学院专业班级:学生姓名:学号:指导教师:王黎设计地点:中原路校区2号楼402设计时间:2011.6.27~2011.7.03指导教师意见:成绩:签名:年月日计算机控制技术课程设计课程设计名称:电阻炉温度控制系统专业班级:学生姓名:学号:指导教师:设计地点:中原路校区2号楼421课程设计时间:2011.6.27~2011.7.03计算机控制技术课程设计任务书学生姓名专业班级学号题目电阻炉温度控制系统课题性质工程设计课题来源自拟课题指导教师王黎主要内容电阻加热炉用于合金钢产品热力特性实验,电加热炉用电炉丝提供功率,使其在预定的时间内将炉内温度稳定到给定的温度值。
在本控制对象电阻加热炉功率为8KW,有220V交流电源供电,采用双向可控硅进行控制。
任务要求第1天:熟悉课程设计任务及要求,针对课题查阅技术资料。
第2天:确定设计方案。
要求对设计方案进行分析、比较、论证,画出方框图,并简述工作原理。
第3-4天:按照确定的方案设计单元电路。
要求画出单元电路图,元件及元件参数选择要有依据,各单元电路的设计要有详细论述。
第5天:撰写课程设计报告。
要求内容完整、图表清晰、文理流畅、格式规范、方案合理、设计正确等。
主要参考资料(1) 潘新民,王燕芳.微型计算机控制技术.高等教育出社,2001(2) 马修水,李晓林.传感器与检测技术.电子工业出版社,2008(3)牛昱光,李晓林.单片机原理与接口技术. 电子工业出版社,2008(4)马春燕.微机原理与接口技术.电子工业出版社,2007审查意见系(教研室)主任签字:年月日目录1 引言 (4)1.1 课题背景...................................... 错误!未定义书签。
1.2系统功能...................................... 错误!未定义书签。
2 总体方案设计 (4)2.1设计任务...................................... 错误!未定义书签。
2.2工艺要求...................................... 错误!未定义书签。
2.3要求实现的系统基本功能........................ 错误!未定义书签。
2.4对象分析 (5)3 硬件电路设计 (6)3.1系统设备选型 (6)3.1.1计算机机型 (6)3.1.2设计支持计算机工作的外围电路 (6)3.1.3设计输入输出通道 (7)3.1.4元器件的选择 (8)3.2数字控制器的设计 (8)3.2.1控制算法 (8)3.2.2计算过程 (9)4 软件设计 ...................................... 错误!未定义书签。
4.1系统程序流程图............................... 错误!未定义书签。
5 总结 .......................................... 错误!未定义书签。
参考文献 ....................................... 错误!未定义书签。
附录系统原理图 .. (16)1、引言1.1 课题背景电阻炉在冶金工业中的运用相当广泛,其温度参数在生产过程中的自动控制系统也随着微机单片机可控硅技术在工业控制领域的推广、应用,正朝着高精度、高稳定性、高智能化的方向发展。
电阻加热炉是典型的工业过程控制对象。
其温度控制具有升温单向性、大惯性、大滞后、时变性等特点,且其升温、保温是依靠电阻丝加热,降温则是依靠环境自然冷却。
温度是工业对象中主要的被控参数之一。
尤其是在冶金、化工、机械各类工业中,广泛使用各种加热炉、热处理炉、反应炉等。
由于炉子的种类不同,所采用的加热方法及燃料也不相同,如煤气、天然气等。
但就控制系统本身的动态特性而言,均属于一阶纯滞后环节,在控制算法上基本相同,可采用PID控制或其他纯滞后补偿算法。
但对于电阻加热炉来说,当其温度一旦超调就无法用控制手段使其降温,因而很难用数学方法建立精确模型和确定参数。
而传统PID控制是一种建立在经典控制理论基础上的控制策略,其设计依赖于被控对象的数学模型,因此对于加热炉这类控制对象采用传统PID的控制方案很难达到理想的控制效果。
为了保证生产过程正常安全地进行,提高产品的质量和数量,以及减轻工人的劳动强度,节约能源,对加热用的各种电炉要求在一定条件下保持恒温,不能随电源电压波动或炉内物体而变化,或者有的电炉的炉温根据工艺要求按照某个指定的升温或保温规律而变化,等等。
因此,在工农业生产或科学实验中常常对温度不仅要不断地测量,而且要进行控制。
在电阻炉温度控制系统的设计中,应尽量考虑到如何有效地避免各种干扰因素而采用一个较好的控制方案,选择合适芯片及控制算法是非常有必要的本设计要用单片机设计一个电阻炉温度控制系统。
1.2 系统功能计算机定时对炉温进行测量和控制一次,炉内温度是由铂电阻温度计来进行测量,其信号经放大送到模数转换芯片,换算成相应的数字量后,再送入计算机中进行判别和运算,得到应有的电功率数,经过数模转换芯片转换成模拟量信号,供给可控硅功率调节器进行调节,使其达到炉温变化曲线的要求。
2、总体方案设计2.1、设计任务用一台计算机及相应的部件组成电阻炉炉温的自动控制系统,并使系统达到工艺要求的性能指标。
2.2、工艺要求按照规定的曲线进行升温和降温,温度控制范围为50~350℃,升温和降温阶段的温度控制精度为±5℃,保温阶段温度控制精度为±2℃。
2.3、要求实现的系统基本功能微机自动调节:正常工况下,系统投入自动。
模拟手动操作:当系统发生异常,投入手动控制。
微机监控功能:显示当前被控量的设定值、实际值,控制量的输出值,参数报警时有灯光报警。
2.4、对象分析在此设计中,要求电阻炉炉内的温度,按照上图所示工艺要求的规律变化,首先从室温开始到50℃为自由升温阶段,当温度到达50℃,就进入系统调节,当温度上升到达350℃时进入保温段,要求始终在系统控制下,保证所需的炉内温度的精度。
加工完毕,要进行降温控制。
保温段的时间为600~1800s。
过渡过程时间:即从开始控制到进入保温阶段的时间要小于600s。
在保温段当温度高于352℃或低于348℃时要报警,在升温和降温阶段也要进行控制,使炉内温度按照曲线的斜率升或降。
采用MCS—51单片机作为控制器,ADC0809模数转换芯片为模拟量输入,DAC0832数模转换芯片为模拟量输出,铂电阻为温度检测元件,运算放大器和可控硅作为功率放大,电阻炉为被控对象,组成电阻炉炉温控制系统,另外,系统还配有数字显示,以便显示和记录生产过程中的温度和输出值。
3、硬件电路设计3.1 系统设备选型3.1.1、计算机机型:MCS—51 8031(不包含ROM、EPROM)系统总线:PC总线3.1.2、设计支持计算机工作的外围电路:键盘和LED显示器的连接图:图2-1为 4×4键盘与显示器链接电路图为4×4矩阵组成的16键盘LED静态显示接口与微机接口电路。
所谓静态显示,即CPU输出显示值后,由硬件保存输出值,保持显示结果.3.1.3、设计输入输出通道输入通道:因为所控的实际温度在50 ~ 350℃,即(350-50)=300所以选用8位A/D转换器,其分辨率约为1.5℃/字,再加放大器偏置措施实现。
(通过调整放大器的零点来实现偏置)这里采用一般中速芯片ADC0809。
ADC0809是带有8位A/D转换器,8路多路开关以及微型计算机兼容的控制逻辑的CMOS组件,其转换方法为逐次逼近型。
8路的模拟开关由地址锁存器和译码器控制,可以在8个通道中任意访问一个通道的模拟信号。
这种器件无需进行零位和满量程调整。
由于多路开关的地址输入部分能够进行锁存和译码,而且其三态TTL输出也可以锁存,所以它易于与微型计算机接口。
其具有较高的转换速度和精度,受温度影响较小,能较长时间保证精度,重现性好,功耗较低,故用于过程控制是比较理想的器件。
图2-4ADC0809应用接线图输出通道:据其实际情况,D/A转换器的位数可低于A/D转换器的位数,因为一般控制系统对输出通道分辨率的要求比输入通道的低,所以这里采用常用的DAC0832芯片DAC0832是8位D/A转换器,与微处理器完全兼容。
期间采用先进的CMOS工艺,因此功耗低,输出漏电流误差较小。
它的内部具有两级输入数据缓冲器和一个R-2RT型电阻网络,因DAC0832电流输出型D/A转换芯片,为了取得电压输出,需在电流输出端接运算放大器,Rf为为运算放大器的反馈电阻端。
图2-5DAC0832双极性电压输出电路双极性电压输出的D/A转换电路通常采用偏移二进制码、补码二进制码和符号一数值编码。
只要在单极性电压输出的基础上再加一级电压放大器,并配以相关电阻网络就可以构成双极性电压输出。
在上图中,运算放大器A2的作用是把运算放大器A1的单向输出电压转变为双向输出。
3.1.4、元器件的选择传感器的选择:铂铑10—铂热电偶,S型,正极性,量程0—1300℃,使用温度小于等于600℃,允差±1.5℃。
执行元件的选择:电阻加热炉采用晶闸管(SCR)来做规律控制,结合电阻炉的具体要求,为了减少炉温的纹波,对输出通道采用较高的分辨率的方案,因此采用移相触发方式,并且由模拟触发器实现移相触发。
变送器的选择:因为系统要求有偏置,又需要对热电偶进行冷端补偿,所以采用常规的DDZ系列温度变送器。
控制元件:采用双向可控硅进行控制,其功能相当于两个单向可控硅反向连接,具有双向导通功能,其通断状态有控制极G决定。
在控制极加上脉冲可使其正向或反向导通。
3.2、数字控制器的设计3.2.1、控制算法:电阻加热炉温度控制系统框图:.整个闭环系统可用一个带纯滞后的一阶惯性环节来近似,所以其控制算法采用达林算法。
电阻加热炉温度控制系统模型为其广义的传递函数为:达林算法的设计目标是设计一个合适的数字控制器,使整个闭环系统的传递函数相当于一个带有纯滞后的一阶惯性环节,即: 通常认为对象与一个零阶保持器相串联, 相对应的整个闭环系统的脉冲传递函数是:11788.2)(40+=-s e s G s3.2.2、计算过程:连同零阶保持器在内的系统广义被控对象的传递函数]11788.21[)(40+-=--s e s e Z z G sTs])1178(1[)1(8.2401+-=--s s Z zz T]11781781[)1(8.2401+--=--s s Z z z T]1111[)1(8.211781141---------=z e zz z15945.01154.0---=z z系统闭环传递函数11[)()()(+-==Φ--s e s e Z z R z C z NTsTs τ 111)1(-------=z e e z TTN ττ数字控制器:)](1)[()()(z z G z z D Φ-Φ=)(])1(1[)1(111z G z e z e e z N TTTN ------------=τττ51510110105154.0945.01])1(1[)1(-------------=z z z e z e e z τττ511933.0007.01)945.01(448.6------=z z z]933.0933.0933.0933.01)[1()945.01(448.6)(432111------++++--=z z z z z z z D消除振铃现象后的数字控制器:111)945.01(448.6)(----=z z z D111945.0297.1297.1)()()(---⨯-==z z z E z U z D将上式离散化:U (Z )—U (Z )Z —1=1.279E (Z )—1.226E (Z )Z —1U (K )—U (K —1)=1.279E (K )—1.226E (K —1)最终得:U (K )=U (K —1)+1.279E (K )—1.226E (K —1)4、软件设计4.1、系统程序流程图a 、系统主程序框图主程序开始初始化参数设置调用温度采样子程序调用温度数值转换和BCD 码转换程序调用显示子程序温度大于上限设定值?温度小于下限设定值?启动继电器退出NN YY b 、A/D 转换子程序流程图设置数据段数据段缓冲区地址送BX开始启动A/D转换读入状态设置N转换是否结束Y读取数据并返回c、LED显示流程图开始设置5288A及延时系统D/A输出到存储器并待显示调用静态显示子程序设置指针及堆栈指向显示缓冲区模型取待高位BCD码显示取待地位BCD码显示修改指针,进行下一轮显示e、数字控制算法子程序流程图数字控制计算程序输入滤波后采样值及给定值采样偏差E(K)计算KI*E(K)计算KI*E(K)计算KP*E(K-1)计算KD*U(K-1)计算KI*E(K)-KP*E(K-1)传递数据为下一次采样做准备子程序返回5、总结经过一周的设计,我对这门课程有了更深的了解。