数控加工工艺分析办法
数控零件加工工艺分析

数控零件加工工艺分析针对机械制造行业越来越普及的数控零件加工技术,对其加工工艺的分析显得尤为重要。
数控零件加工在过去数十年中经历了长足的进步,目前已成为现代制造业中应用最为广泛的一种制造方法。
本文将从数控加工工艺的基本概念、数控加工的特点、数控加工中的主要技术处理等方面进行分析论述,以使读者对数控零件加工技术有更深入的了解。
一、数控加工工艺概述数控加工工艺是指通过计算机程序控制机床或加工设备进行自动化加工的一种现代化制造技术。
具有高效、精度高、柔性、可靠性好、操作简便等特点。
与传统的手工或半自动化加工相比,数控加工能够提高生产效率,降低人为误差,减少人力和设备成本,从而在制造过程中提高了生产效率和质量稳定性。
二、数控加工的特点1. 高精度。
数控零件加工可以实现微米级别的精度,且加工精确度稳定性高,不易受到环境、人为等因素的影响。
2. 高效率。
数控加工能够实现机器加工的连续、自动化,生产效率比其他普通加工方法高出一个数量级。
3. 操作简便。
操作人员只需配置好加工程序,载入数控系统中,加工过程中不需要对设备进行频繁的调整。
三、数控加工中的主要技术处理1. 数控编程数控加工首先需要对零件进行CAD设计,然后再将设计图纸转化为数控程序,最终通过计算机传输至机床或设备中进行加工。
2. 数控加工轨迹规划加工轨迹规划是数控加工中比较关键的一步技术处理。
数控机床需要根据程序所编的轨迹精确定位进行加工。
轨迹规划需要考虑加工路径的时间、精度、运动平滑性等多个因素,以达到理想的加工效果。
3. 数控加工切削切削是数控加工中最重要的技术处理之一,加工质量的好坏、加工速度的快慢都与刀具材料、刃磨工艺、切削参数等有着密切关系。
数控加工中常用的切削方式有铣削、钻孔、车削、磨削等。
四、数控加工中的常见问题及解决方式在数控加工过程中,由于材料、设备、环境、程序等因素影响,常常会出现一些问题。
这些问题会导致加工件质量下降,工艺费用增加,使生产效率降低。
数控加工工艺分析
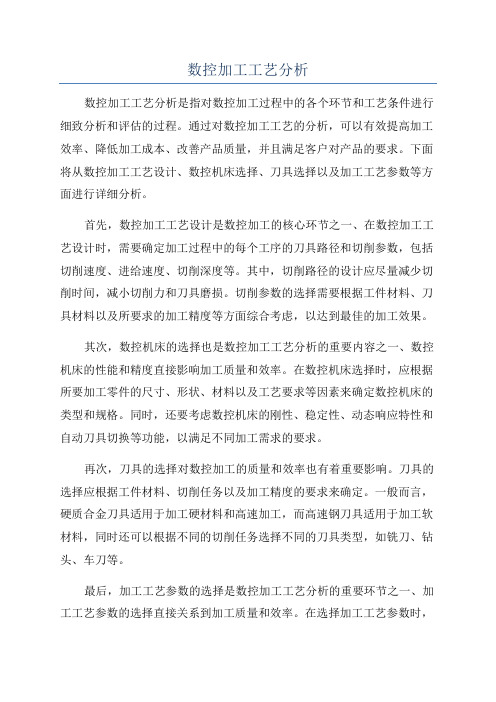
数控加工工艺分析数控加工工艺分析是指对数控加工过程中的各个环节和工艺条件进行细致分析和评估的过程。
通过对数控加工工艺的分析,可以有效提高加工效率、降低加工成本、改善产品质量,并且满足客户对产品的要求。
下面将从数控加工工艺设计、数控机床选择、刀具选择以及加工工艺参数等方面进行详细分析。
首先,数控加工工艺设计是数控加工的核心环节之一、在数控加工工艺设计时,需要确定加工过程中的每个工序的刀具路径和切削参数,包括切削速度、进给速度、切削深度等。
其中,切削路径的设计应尽量减少切削时间,减小切削力和刀具磨损。
切削参数的选择需要根据工件材料、刀具材料以及所要求的加工精度等方面综合考虑,以达到最佳的加工效果。
其次,数控机床的选择也是数控加工工艺分析的重要内容之一、数控机床的性能和精度直接影响加工质量和效率。
在数控机床选择时,应根据所要加工零件的尺寸、形状、材料以及工艺要求等因素来确定数控机床的类型和规格。
同时,还要考虑数控机床的刚性、稳定性、动态响应特性和自动刀具切换等功能,以满足不同加工需求的要求。
再次,刀具的选择对数控加工的质量和效率也有着重要影响。
刀具的选择应根据工件材料、切削任务以及加工精度的要求来确定。
一般而言,硬质合金刀具适用于加工硬材料和高速加工,而高速钢刀具适用于加工软材料,同时还可以根据不同的切削任务选择不同的刀具类型,如铣刀、钻头、车刀等。
最后,加工工艺参数的选择是数控加工工艺分析的重要环节之一、加工工艺参数的选择直接关系到加工质量和效率。
在选择加工工艺参数时,可以通过实验或者经验总结来确定最佳参数。
一般而言,切削速度应根据材料硬度、刀具类型以及切削任务来选择,进给速度应根据刀具的尺寸和刚性、加工表面的粗糙度要求以及加工工艺的稳定性来选择,切削深度应根据加工目标和刀具的性能来确定。
此外,还要注意加工中的冷却液、润滑剂的使用以及工件夹紧装置的设计与选择等。
综上所述,数控加工工艺分析是数控加工过程中十分重要的环节,通过对加工工艺设计、数控机床选择、刀具选择以及加工工艺参数的详细分析和评估,可以优化加工过程,提高加工效率和产品质量。
数控加工工艺的分析与处理

数控加工工艺的分析与处理随着科技的不断进步,数控加工技术在制造业中得到了广泛应用。
数控加工工艺的分析与处理是保证数控加工过程顺利进行的关键环节。
本文将从数控加工工艺的基本原理、分析方法与处理措施三个方面进行探讨。
一、数控加工工艺的基本原理数控加工是利用计算机控制数控机床进行精密切削或造型加工的一种加工方法。
其基本原理是将图纸上的几何尺寸、形状和位置要求转化为数学模型,并通过计算机编程的方式将这些模型转化为数控指令,进而控制数控机床的运动轨迹、切削参数等,实现零件的加工。
数控加工工艺的前提是要了解工件的设计要求和材料特性。
通过分析工件的几何形状、尺寸、表面质量要求以及材料的硬度、可加工性等参数,确定适合的数控加工方案。
在具体加工过程中,还需要根据工件的形状复杂程度、加工精度要求等因素,合理选择数控机床、刀具和切削参数等。
二、数控加工工艺的分析方法1.几何形状分析:对于复杂形状的工件,需要进行多视图的几何形状分析,确定加工的主要特征面、特征线和特征点。
2.加工工艺分析:根据工件的几何形状、尺寸和表面质量要求,结合加工设备和材料,分析出适合的加工工艺路线,并绘制出对应的加工工艺卡。
3.切削力与热量分析:分析切削力和热量对加工过程的影响,根据材料的可加工性和切削力的大小,选择合适的切削参数和冷却液。
4.程序分析:通过工艺分析,确定数控加工的主要工序和加工路径,在制定程序时,遵循合理、简洁、安全、高效的原则。
三、数控加工工艺的处理措施1.加工设备优化:根据工件的加工要求,选择合适的数控机床及其附件,提高加工效率和精度。
2.刀具选择与刀具磨损处理:根据工件材料和切削要求,选择合适的刀具,并进行定期检查和更换,及时处理刀具磨损问题。
3.切削参数调整:根据工艺分析结果,合理调整切削速度、切削深度和进给速度等切削参数,以保证加工质量。
4.刀具路径优化:通过选择合理的切削路径和切削顺序,减少进刀次数和加工时间,提高加工效率。
数控加工工艺分析的一般步骤与方法
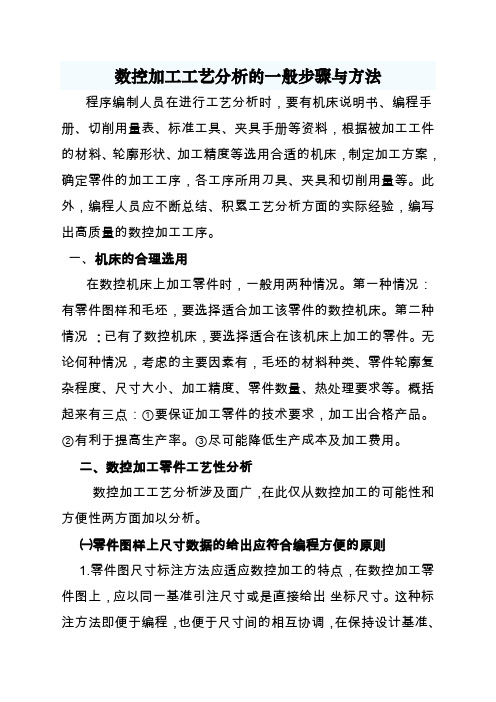
数控加工工艺分析的一般步骤与方法程序编制人员在进行工艺分析时,要有机床说明书、编程手册、切削用量表、标准工具、夹具手册等资料,根据被加工工件的材料、轮廓形状、加工精度等选用合适的机床,制定加工方案,确定零件的加工工序,各工序所用刀具、夹具和切削用量等。
此外,编程人员应不断总结、积累工艺分析方面的实际经验,编写出高质量的数控加工工序。
一、机床的合理选用在数控机床上加工零件时,一般用两种情况。
第一种情况:有零件图样和毛坯,要选择适合加工该零件的数控机床。
第二种情况:已有了数控机床,要选择适合在该机床上加工的零件。
无论何种情况,考虑的主要因素有,毛坯的材料种类、零件轮廓复杂程度、尺寸大小、加工精度、零件数量、热处理要求等。
概括起来有三点:①要保证加工零件的技术要求,加工出合格产品。
②有利于提高生产率。
③尽可能降低生产成本及加工费用。
二、数控加工零件工艺性分析数控加工工艺分析涉及面广,在此仅从数控加工的可能性和方便性两方面加以分析。
㈠零件图样上尺寸数据的给出应符合编程方便的原则1.零件图尺寸标注方法应适应数控加工的特点,在数控加工零件图上,应以同一基准引注尺寸或是直接给出坐标尺寸。
这种标注方法即便于编程,也便于尺寸间的相互协调,在保持设计基准、工艺基准、检测基准与编程原点设置的一致性方面带来很大方便。
由于零件设计人员一般在尺寸标注中较多的考虑装配等使用性能方面,而不得不采用局部分散的标注方法,这样就会给工序安排与数控加工带来许多不便。
由于数控加工精度和重复定位精度都很高,不会因产生较大的积累误差而破坏使用性能,因此可以将局部的分散标注法改为同一基准引注尺寸或直接给出坐标尺寸的标注法。
2.构成零件轮廓的几何要素的条件应充分在手工编程时,要计算基点或节点坐标。
在自动编程时,要对构成零件轮廓的所有几何要素进行定义。
因此在分析零件图时,要分析几何要素的给定条件是否充分。
如圆弧与直线、圆弧与圆弧在图样上相切,但根据图上给定尺寸,在计算相切条件时,变成了相交或相离状态。
数控加工零件的工艺分析与数控铣削加工工艺

数控加工零件的工艺分析与数控铣削加工工艺数控加工是指利用计算机数控系统,通过编写程序控制机床工作来加工零件的一种加工方式。
在工业生产中,数控加工因其高精度、高效率、高灵活性等优点而被广泛应用。
其中数控铣削是一种常见的数控加工方式,本文将从工艺分析、数控铣削加工工艺等方面进行探讨。
一、数控加工零件的工艺分析工艺分析是数控加工的一项前置工作,它的目的是确定加工工艺,选择合适的加工设备和刀具,制定加工程序等,从而保证加工质量和效率。
具体而言,工艺分析主要包括以下几个方面:1. 零件的材质和形状:不同材质的加工性能不同,加工时需要选择相应的切削参数和刀具;而零件的形状和结构也会影响加工难度和精度,需要对其进行全面分析和评估。
2. 加工精度和表面质量要求:根据零件的要求,确定加工精度和表面质量目标,制定相应的切削参数和工艺措施。
3. 工序分析:对零件进行逐个工序分析,确定加工顺序、加工方向、加工路径和刀具选择等重要内容,同时把握好每个工序的加工质量和效率。
4. 刀具选择:根据加工材料、零件形状和要求,选择合适的刀具和刀具尺寸,保证零件的加工质量和加工效率。
5. 加工程序制定:通过数控编程软件,编写机床加工程序,包括各种切削参数、刀具路径、指令参数等信息,为数控加工提供参考。
二、数控铣削加工工艺数控铣削是一种高速旋转的刀具在工件表面上进行切削的加工方式,它广泛应用于金属、塑料等材料制件的加工中。
数控铣削在工件制作中具有大量价值和应用,且数控铣削加工工艺也是半自动化和自动化制造中的重要工艺之一。
要把好铣削的关,需要具备以下几点:1. 刀具选择:刀具的选择是影响加工效率和加工质量的重要因素之一。
首先需要考虑切削材料,选择高速钢、硬质合金、陶瓷等材质的刀具;其次要考虑刀具尺寸和形状,根据零件的要求选择合适的刀具。
2. 切削参数:切削参数包括切削速度、进给量和切削深度等,这些参数的选定与零件材料、刀具材料、刀具尺寸和表面质量等因素密切相关。
数控加工工艺分析的一般步骤与方法

3)确定进给量
进给速度是数控机床切削用量中的重要参数,主要根 据零件的加工精度和表面粗糙度要求以及刀具与零件的材料 性质来选取。当加工精度和表面粗糙度要求高时进给量应选 择得小些。最大进给量受机床刚度和进给系统的性能影响, 并与数控系统脉冲当量的大小有关。
1)以零件的装夹定位方式划分工序 一般加工零件外形时以内形定位,加工零件内形时以外
形定位。可根据定位方式的不同来划分工序
2)按所用刀具划分工序 为了减少换刀次数,压缩空行程运行的时间,减少不必
要的定位误差,可以按照使用相同刀具来集中加工工序的方 法进行零件的加工工序划分。
数控车削加工工艺
3)按粗、精加工划分工序 一般情况下先进行粗加工,再进行精加工。通常在一次
0
50 100 零件批量
零件生产批量与总加工费用的关系
数控车削加工工艺
2.数控加工零件的工艺性分析
数控加工工艺分析主要从数控加工的可能性和方便性方 面分析: (1)零件图上尺寸数据的给出,应符合程序编制方便的原则
1)零件图上尺寸标注方法应该适应数控加工编程的特点 2)构成零件轮廓几何元素的条件要充分
(2)零件各加工部位的结构工艺性应符合数控加工的特点
1)零件的内腔和外形最好采用统一的几何类型和尺寸。这 样可以减少使用刀具的规格和加工中换刀的次数,使得 编程方便,生产效益提高。
2)应该采用统一的定位基准
数控车削加工工艺
3.加工方法的选择与加工方案的确定
(1)加工方法的选择
加工方法的选择要同时保证加工精度和表面粗糙度的要 求。由于获得同一级精度与表面粗糙度的加工方法有多种, 因而在进行选择时,要结合零件的形状、尺寸的大小和热处 理等具体要求来考虑。例如对于IT7级精度的孔,采用车削、 镗削、铰削、磨削等加工方法,均可达到精度要求。
数控铣削加工工艺分析
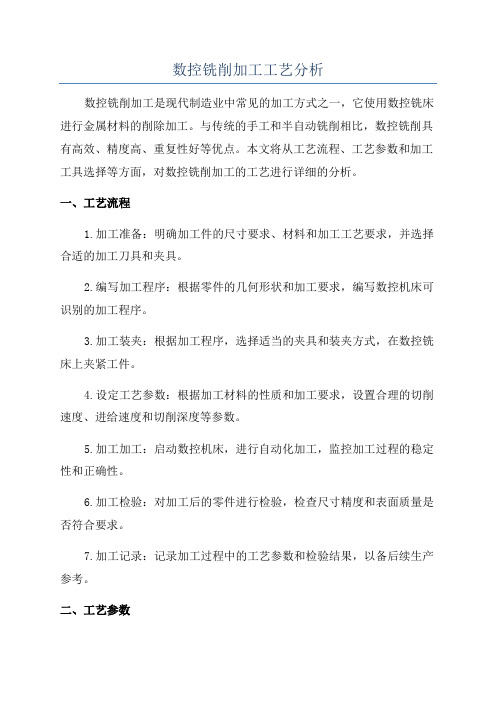
数控铣削加工工艺分析数控铣削加工是现代制造业中常见的加工方式之一,它使用数控铣床进行金属材料的削除加工。
与传统的手工和半自动铣削相比,数控铣削具有高效、精度高、重复性好等优点。
本文将从工艺流程、工艺参数和加工工具选择等方面,对数控铣削加工的工艺进行详细的分析。
一、工艺流程1.加工准备:明确加工件的尺寸要求、材料和加工工艺要求,并选择合适的加工刀具和夹具。
2.编写加工程序:根据零件的几何形状和加工要求,编写数控机床可识别的加工程序。
3.加工装夹:根据加工程序,选择适当的夹具和装夹方式,在数控铣床上夹紧工件。
4.设定工艺参数:根据加工材料的性质和加工要求,设置合理的切削速度、进给速度和切削深度等参数。
5.加工加工:启动数控机床,进行自动化加工,监控加工过程的稳定性和正确性。
6.加工检验:对加工后的零件进行检验,检查尺寸精度和表面质量是否符合要求。
7.加工记录:记录加工过程中的工艺参数和检验结果,以备后续生产参考。
二、工艺参数1.切削速度:是指刀具在单位时间内切削的长度。
根据加工材料的硬度和切削性能,合理选择切削速度,既能保证加工效率,又能保证刀具寿命。
2.进给速度:是指刀具在单位时间内在加工方向上移动的距离。
进给速度的选择应考虑切削力和切削表面的要求。
3.切削深度:是指刀具在一次进给过程中所削除的材料层厚度。
切削深度的选择应使得切削力合理,既能保证加工效率,又能避免切削表面的质量。
4.刀具半径补偿:数控铣床会自动根据刀具半径补偿值进行补偿,使得加工轮廓与设计轮廓一致。
5.加工顺序:根据零件的几何形状和切削力的分布情况,合理选择加工顺序,避免零件变形和加工过程中的切削力过大。
三、加工工具选择1.刀具材料:刀具材料应具有一定的硬度、耐磨性和耐冲击性,常用的刀具材料有硬质合金、高速钢和陶瓷等。
2.刀具形状:根据零件的几何形状和加工要求,选择合适的刀具形状,如平面铣刀、立铣刀、球头铣刀等。
3.切削刃数:根据加工材料的硬度和切削性能,选择合适的刀具刃数,既能保证加工效率,又能保证刀具寿命。
数控加工工艺的分析与处理

数控加工工艺的分析与处理数控加工是一种现代化的加工方法,其与传统的手工雕刻、手动铣削有所不同,它是通过计算机程序控制工具进行雕刻、铣削、钻孔等一系列加工步骤的过程。
数控加工具有高效、高质、多样化等优点,其广泛应用于机械、电子、汽车、军工、航空等领域。
数控加工工艺包括材料加工、加工工具选择、数控程序编制等方面,下面我们来详细分析一下这些方面。
(一)材料加工数控加工材料的加工具有机床、工具等。
机床是数控加工中最基本的工具,根据不同的加工需求,可选择数控铣床、数控车床、数控钻床等机床,这些机床具有精度高、效率高、自动化程度高的特点,能够满足不同加工工件的需求。
而工具则是实现材料加工的关键,数控加工工具主要有刀具、钻头、铣刀等,它们的选择需要考虑工件的材质、所需精度、加工方式等因素。
(二)加工工具选择在数控加工过程中,选择适当的工具对于加工产品的质量和效率有很大影响。
在选择工具时,需要考虑工作量、所需精度、切削速度、切削力、工具耐用性等因素,需在这些方面进行权衡取舍。
例如,选择刀具时需要计算切削力和扭矩,这有助于预估切削时可能遇到的问题,并提前解决问题。
(三)数控程序编制数控程序编写是数控加工过程中的核心环节,它直接影响加工质量和效率。
在程序编写中,需要精确计算加工车床、铣床等机床的坐标轴移动轨迹,确定刀具在加工中的位置和切削方向、刀具的进给量等参数。
在编写程序时,还需要根据被加工件的材质、形状、尺寸等因素灵活调整加工参数,重点关注数值的精度和正确性。
另外,在数控程序编制中还存在着问题就是加工零件与实际加工结果存在误差,这是由不同机床、工具、环境等因素所造成的,需要通过后期调整以确保加工质量。
总的来说,数控加工工艺涉及多方面的因素,其良好的运用需要在材料选择、加工工具选择、数控程序编制等方面进行全面分析和处理。
- 1、下载文档前请自行甄别文档内容的完整性,平台不提供额外的编辑、内容补充、找答案等附加服务。
- 2、"仅部分预览"的文档,不可在线预览部分如存在完整性等问题,可反馈申请退款(可完整预览的文档不适用该条件!)。
- 3、如文档侵犯您的权益,请联系客服反馈,我们会尽快为您处理(人工客服工作时间:9:00-18:30)。
常用工件材料的高速切削速度范围表(m/min)
应用范围
目前,高速切削加工技术主要应用于车 削和铣削工艺,今后将涵盖所有的传统加工 范畴,从粗加工到精加工,从车削、铣削到 镗削、钻削、拉削、铰削、攻丝、滚齿等。
航空制造业、模具制造业、汽车制造业 等行业均已积极采用高速切削加工技术。
三、典型零件数控加工工艺分析实例
单元1 数控加工 工艺分析方法
广西机电职业技术学院
单元1 数控加工工艺分析方法
一、数控加工工艺分析方法
(一)零件图的工艺分析 (二)加工方法的选择 (三)工序的划分 (四)定位与夹紧方式的确定
(五)加工顺序的安排 (六)确定走刀路线和工步顺序 (七)切削用量的选择 (八)对刀点与换刀点的确定 (九)高速切削加工技术
二、典型零件数控加工工艺分析实例
(一)数控车削加工典型零件工艺分析实例 (二)数控铣削加工典型零件工艺分析实例
一、数控加工工艺分析方法
(一)零件图的工艺分析
1、零件图分析 (1)尺寸标注方法分析
注意基准统一原则,减少累积误差。 (2)零件图的完整性与正确性分析
几何图素条件要求充分。
(3)零件技术要求分析 尺寸精度、形状精度、位置精度、表面粗
(一)数控车削加工典型零件工艺分析实例
轴承套 数控车削加 工工艺(单 件小批量生 产),所用 机床为 CJK6240。
1、零件图工艺分析
采取以下工艺措施: 1)编程时取基本尺寸。 2)先加工左、右端面。 3)内孔尺寸较小,镗1﹕20锥孔、φ32孔及
15°斜面时需掉头装夹。
2、确定装夹方案
1)内孔加工时以外圆定位,用三爪自动 定心卡盘夹紧。
5、切削用量选择
根据被加工表面质量要求、刀具材料 和工件材料,参考切削用量手册或有关资 料选取切削速度与每转进给量,计算结果 祥见工序卡。
6、数控加工工艺卡片拟订
(二)数控铣削加工典型零件工艺分析实例
加工平面 凸轮零件上的 槽与孔,外部 轮廓已加工完 ,零件材料为 HT200。
0.021 0
3、平面加工方法的选择
4、平面轮廓和曲面轮廓加工方法的选择 方法有数控铣削、线切割及磨削等
对曲率半径较 小的平面内轮 廓,采用线切
割。
对平面外轮廓, 采用数控铣削。
对曲面轮廓,采用数控铣削。
(三)工序的划分
1.工序划分的原则 工序集中原则(数控加工常采用的原则):
减少设备投入,减少安装次数、有利于保 证加工精度。调整麻烦,生产周期长。 工序分散原则: 设备投入成本大,生产效率高。
(九)高速切削加工技术
高速切削的切削速度比常规切削速 度高5~10倍以上。高速切削加工技术体 系是机床、刀具、工件、加工工艺、切 削过程监控、切削机理等诸多方面的有 机集成。
高速切削加工视频
1、特点
切削力随着切削速度的提高而下降; 切削产生的热量绝大部分被切屑带走; 加工表面质量提高; 在高速切削范围内,机床的激振频率远
走刀路线是刀具刀位点在整个加工工序中 的运动轨迹,它不但包含了工步的内容,也反 映了工步的顺序。
走刀路线的确定非常重要,因为它与零件 的加工精度和表面质量密切相关。
走刀路线确定原则:
1、应能保证零件的加工精度和表面粗糙度 要求。
铣削平面零件外轮廓时,刀具的切 入、切出应沿轮廓切线方向进行,避免 在工件表面形成接刀痕。且注意留有切 入长度和切出长度。
铣削外轮廓的 切入切出路径
铣削外圆的切 入切出路径
铣削平面零件内轮廓时,刀具切 入、切出点应选择在轮廓两几何元素 的交点处。若无交点,刀具切入、切 出点应远离拐角,或选择圆弧切入、 切出。
铣削内轮廓的 切入切出路径
铣削内圆的切 入切出路径
从拐角切入、切 出,容易产生过 切现象。
从直线中间圆弧 切入、切出。
XK714机床铣削工艺时: 粗铣:X、Y方向取刀具直径的75%
Z方向取刀具半径的1/4~1/6 半精加工:X、Y方向取刀具直径的50%
Z方向取刀具半径的1/4~1/6 精加工:X、Y方向取0.1~0.5mm
Z方向取0.1~0.3mm
(2)进给量(进给速度) 的选择
主要根据零件的表面粗糙度、加工 精度、刀具和工件的材料、刀具的刃数 等因素选择。 车削加工时: 粗加工:0.3~0.5mm/r 半精加工:0.15~0.25mm/r 精加工:0.05~0.15mm/r
2.工序划分方法 考虑生产纲领、设备、零件结构和技术要求。
要求遵循以下原则: (1)按所用刀具划分。如加工中心,减少换刀次数。 (2)按安装次数划分。减少定位误差。 (3)按粗、精加工划分。减少误差复映,提高加工精
度。 (4)按加工部位划分。减少空行程,提高效率。
(四)定位与夹紧方式的确定
正确选用定位方案和夹紧方式是保 证加工精度的条件。
离工艺系统的固有频率范围。
2、优点
有利于提高生产效率; 有利于改善工件的加工精度和表面质量; 有利于减少模具加工中的手工抛光; 有利于减小工件变形; 有利于使用小直径刀具; 有利于加工薄壁零件和脆性材料; 有利于加工较大零部件。
3、应用 加工材料
适于高速切削加工的工件材料包括铝 合金、钢、铸铁、铅、铜及铜合金 ,此外 还包括模具钢、钛合金、不锈钢、镍基合 金、纤维增强合成树脂等难加工材料。
到既定深度。 先打一个工艺孔,再从工艺孔进刀到既定深
度。
4、刀具选择
5、切削用量选择
凸轮槽内、外轮廓精加工时留0.1 mm铣 削余量,精铰φ20、φ12两个孔时留0.1mm 铰削余量。
选择主轴转速与进给速度时,先查切削用 量手册,确定切削速度与每齿进给量,再计算 主轴转速与进给速度。
6、填写数控加工工艺卡片
1、零件图工艺分析
1) 凸轮槽内外轮廓及φ20、φ12两个孔 的加工应分粗、精加工两个阶段进行,以 保证表面粗糙度要求。 2) 应以底面A定位,提高装夹刚度以满 足垂直度要求。
2、确定装夹方案
1) 加工φ20、φ12两个孔时,以底面A 定位(必要时可设工艺孔),采用螺旋 压板机构夹紧。
2) 加工凸轮槽内外轮廓时,采用“一面 两孔”方式定位,即以底面A和φ20、 φ12两个孔两个孔为定位基准。
(3)切削速度的选择
根据已经选定的背吃刀量、进给量、 刀具材料和刀具耐用度等选择。
n =1000 Vc/πD 主轴转速=1000×切削线速度/(π×刀 具直径或工件直径)
高速钢刀具: 粗加工:V≈ 15m/min 半精加工:V≈ 25m/min 精加工:V≈ 45m/min 硬质合金刀具: 粗加工:V≈ 30m/min 半精加工:V≈ 50m/min 精加工:V≈ 100m/min 陶瓷刀具:5~10倍的硬质合金刀具
铣削无交点内轮廓的切入切出路径
确定孔加工路线时,若孔的位置精度要求较 高,加工路线的定位方向应保持一致。
YX
对刀点
①Ⅰ ② ③Ⅱ
ⅣⅢ
④
YX
对刀点
①Ⅰ
② ③Ⅱ ⅣⅢ
⑤
④
O
XY
存在(反a) 向误差
的加工路线
O
YX
பைடு நூலகம்
无反(b向) 误差
的加工路线
车螺纹时,为保证螺距的准确,应避免在进 给机构的加速和减速过程中切削,故应有引入距 离和超越距离。
•
任何一个行业,一个市场,都是先来 的有肉 吃,后 来的汤 都没的 喝。。2 0.8.112 0.8.11T uesday , August 11, 2020
•
年轻人欠缺经验,但请不要忘记:年 轻是你 最大的 本钱。 不要怕 犯错, 也不要 畏惧挑 战,你 应该坚 持到底 ,在出 人头地 的过程 中努力 再努力 。。11: 26:4811 :26:481 1:268/ 11/2020 11:26:48 AM
背吃刀量
进给量
切削速度
(2) 精加工时的切削用量的选择原则:
主要考虑保证加工精度和表面粗糙度, 其次是刀具耐用度和效率。
背吃刀量
进给量
切削速度
数控车削刀具、工件材料、切削用量选择视频 数控铣削刀具、工件材料、切削用量选择视频
2、切削用量的选择方法 (1)背吃刀量的选择(常规加工条件下)
CK6140机床车削工艺时: 粗车:≥3mm 半精加工:≈3~0.5mm 精加工:≈ 0.5~0.05mm
交错加工内、
外圈孔,减少
空刀时间。
孔加工最短走刀路线选择
对刀点 工步起点
工步起点
对刀点
工步起点与对刀 点重合,空行程 长。
工步起点与对刀 点分离,空行程 短。
粗车矩形循环进给路线选择
矩形进给路线, 适用于棒料毛坯, 进给路线较短。
三角形进给路线, 适用于棒料毛坯, 进给路线较长。
仿形进给路线, 用于铸、锻件毛 坯时进给路线较 短。
(5)减少刀具数量,减低 成本和减少定位误差。
R越大,加工 平面能力越差
。
(二)加工方法的选择
1、外圆表面加工方法的选择
2、内孔表面加工方法的选择
1、Ф 40H7孔粗糙度要 求较高,选择钻孔
—粗镗(或扩孔)— 半精镗—精镗方案。
2、Ф 13和Ф 22孔没有 尺寸公差要求,粗糙 度要求不高,选择钻 孔—锪孔方案。
粗车进给路线选择
3、应使数值计算简单,以减少编程工作量。 4、应选择使工件加工变形小的走刀路线。
对薄板类零件应采用分层切削或对称 切削的走刀路线。
(七)切削用量的选择
1、切削用量的选择原则
考虑切削力、切削功率、刀具磨损、 加工质量和加工成本。
(1)粗加工时切削用量的选择原则:
主要考虑保证提高效率和刀具耐用度。
先用行切法,最后 沿周向环切一刀, 光整轮廓表面,能
获得较好的效果。