“法兰盘”零件的机械加工工艺规程
法兰盘机械加工工艺规程及铣距Φ两侧平面工序专用夹具设计

法兰盘机械加工工艺规程及铣距Φ两侧平面工序专用夹具设计一、引言法兰盘是一种广泛应用于机械设备中的重要零件,其连接方式多样,常见的有螺栓连接和焊接连接。
机械加工工艺规程是指在机械加工过程中,对于加工工序和加工方法进行规范和指导的文档。
本文将介绍法兰盘的机械加工工艺规程,特别是涉及到铣距Φ两侧平面的工序和该工序所需的专用夹具设计。
二、法兰盘机械加工工艺规程2.1 加工工序法兰盘的机械加工通常包括以下几个工序:1.切割工序:根据设计要求,对法兰盘的原材料进行切割,通常采用数控切割机进行切割。
2.钻孔工序:根据设计要求,在法兰盘上进行钻孔,用于螺栓连接或其他配件的安装。
3.车削工序:根据图纸要求,对法兰盘进行车削加工,以获得需要的外形和尺寸。
4.铣削工序:根据图纸要求,对法兰盘进行铣削加工,以获得需要的平面和凹槽形状。
2.2 铣距Φ两侧平面工序铣距Φ两侧平面是法兰盘上的一种特殊加工工序,其目的是为了提供与其他零件的连接接口。
该工序通常需要使用专用夹具来保持工件的稳定性和精确性。
2.3 工艺参数在进行铣距Φ两侧平面工序时,需要注意以下工艺参数:1.切削速度:根据刀具材料和工件材料的硬度,选择适当的切削速度以确保加工质量。
2.进给速度:根据加工要求和工件材料的硬度,决定合适的进给速度,以确保加工效率和质量。
3.切削深度:根据法兰盘的设计要求,确定合适的切削深度,以确保加工精度和表面质量。
2.4 加工设备对于法兰盘的机械加工,通常需要使用以下设备:•数控切割机:用于对法兰盘的原材料进行切割。
•钻床:用于钻孔工序。
•车床:用于车削工序。
•铣床:用于铣削工序和铣距Φ两侧平面工序。
三、铣距Φ两侧平面工序专用夹具设计3.1 设计考虑因素在设计铣距Φ两侧平面工序专用夹具时,需要考虑以下因素:1.稳定性:夹具需要能够保持工件的稳定性,防止在加工过程中发生移动或变形。
2.精确性:夹具设计应该能够确保加工过程中的精确性,保证铣削结果与设计要求一致。
法兰盘机械加工工艺说明书

一、零件的分析(一)零件的作用题目所给的零件是法兰盘(见附图1),其为盘类零件,用于卧式车床上。
车床的变速箱固定在主轴箱上,靠该法兰盘定心。
法兰盘内孔与主轴的中间轴承外圆相配,外圆与变速箱体孔相配,以保证主轴三个轴承孔同心,使齿轮正确啮合。
(二)零件的工艺分析法兰盘共有两组加工表面,它们之间有一定的位置要求。
现分述如下:1.以Φ80孔为中心的加工表面这一组加工表面包括:Φ62±0.015孔及其倒角以及与其垂直的端面,Φ80h11外表面,两个M64×1.5的槽,Φ36 0+0.62孔以及与其垂直的端面,Φ52g6外表面B及退刀槽,三个互成120°的Φ16.5阶梯孔的两端面。
2.以A面为基准的加工表面这一组加工表面包括:三个互成120°的ф16.5阶梯孔,一个侧面C,一个平面D。
这两组表面之间有着一定的位置要求,主要是:Φ62±0.015孔对B端面的径向圆跳动公差为0.04mm。
由以上分析可知,对于这两组加工表面而言,可以先加工其中一组表面,然后借助于专用夹具加工另一组表面,并且保证它们之间的位置精度要求。
二、工艺规程设计(一)确定毛坯的制造形式材料为HT15-33。
考虑到法兰主要承受静压力,因此选用铸件。
(二)基面的选择基面选择是工艺规程设计中的重要工作之一。
基面选择得正确与合理,可以使加工质量得到保证,生产率得以提高。
否则,加工工艺过程中会问题百出,更有甚者,还会造成零件的大批报废,使生产无法正常进行。
(1)粗基准的选择。
按照有关粗基准的选择原则(如果必须首先保证工件上欲加工表面与不加工表面之间的位置要求,则应以不加工表面为粗基准),孔Φ62±0.015与B端面有0.04mm的圆跳动公差要求,现选择Φ52g6外表面B为粗基准,利用三爪自定心卡盘加持外圆A,并且使卡盘端面紧靠A端面,这样可以消除所有六个自由度,达到完全定位。
(2)精基准的选择。
法兰盘机械加工工艺规程
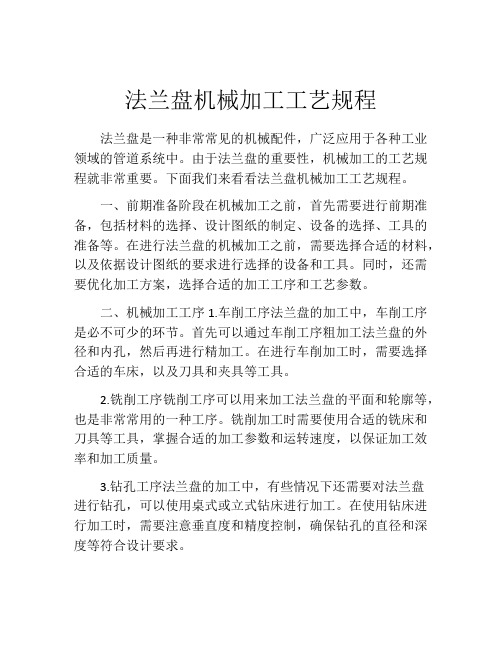
法兰盘机械加工工艺规程法兰盘是一种非常常见的机械配件,广泛应用于各种工业领域的管道系统中。
由于法兰盘的重要性,机械加工的工艺规程就非常重要。
下面我们来看看法兰盘机械加工工艺规程。
一、前期准备阶段在机械加工之前,首先需要进行前期准备,包括材料的选择、设计图纸的制定、设备的选择、工具的准备等。
在进行法兰盘的机械加工之前,需要选择合适的材料,以及依据设计图纸的要求进行选择的设备和工具。
同时,还需要优化加工方案,选择合适的加工工序和工艺参数。
二、机械加工工序1.车削工序法兰盘的加工中,车削工序是必不可少的环节。
首先可以通过车削工序粗加工法兰盘的外径和内孔,然后再进行精加工。
在进行车削加工时,需要选择合适的车床,以及刀具和夹具等工具。
2.铣削工序铣削工序可以用来加工法兰盘的平面和轮廓等,也是非常常用的一种工序。
铣削加工时需要使用合适的铣床和刀具等工具,掌握合适的加工参数和运转速度,以保证加工效率和加工质量。
3.钻孔工序法兰盘的加工中,有些情况下还需要对法兰盘进行钻孔,可以使用桌式或立式钻床进行加工。
在使用钻床进行加工时,需要注意垂直度和精度控制,确保钻孔的直径和深度等符合设计要求。
4.车削内螺纹工序有些法兰盘还需要加工内螺纹,可以使用车床进行加工。
在进行车削内螺纹时,需要选择合适的车床和工具,掌握正确的加工参数,确保螺纹尺寸和螺距等符合设计要求。
5.钻螺纹孔工序另外,有些法兰盘还需要钻螺纹孔,可以使用丝锥进行加工。
在进行钻螺纹孔时,需要掌握正确的加工参数和技巧,确保螺纹质量和精度。
三、加工完成后的检测在机械加工过程结束后,需要进行检测和评估。
主要在工件的轮廓、尺寸和表面粗糙度等方面进行检测,确保加工完成的法兰盘符合设计要求,具有合适的质量和精度。
四、加工注意事项在进行机械加工的过程中,需要注意一些细节问题,以确保加工的效率和质量。
比如,在进行加工前,需要对加工设备和工具进行清洗和维护,保持工具的锋利度和加工设备的稳定性。
法兰盘机械加工工艺规程设计(1)

法兰盘加工工艺规程设计目录第一部分工艺设计说明书 (1)1.零件图工艺性分析 (1)1.1零件结构功用分析 (1)1.2零件技术条件分析 (1)1. 3零件结构工艺性分析 (1)2.毛坯选择 (2)2.1毛坯类型 (2)2.2毛坯余量确定 (2)2.3毛坯-零件合图草图 (2)3.机加工工艺路线确定 (3)3.1加工方法分析确定 (3)3.2加工顺序的安排 (3)3.3定位基准选择 (4)3.4加工阶段的划分说明 (4)3.5主要机加工工序简图 (4)4.工序尺寸及其公差确定 (11)5.设备及其工艺装备确定 (13)6.切削用量及工时定额确定 (14)第二部分第8号工序夹具设计说明书 (18)1工序尺寸精度分析 (18)2.定位方案确定 (18)4.定位误差分析计算 (19)5.设计钻套,连接元件及夹具体,钻模板: (19)6.夹具总装草图 (20)第三部分第4号工序刀具设计说明书 (20)1.工序尺寸精度分析 (20)2.刀具类型确定 (20)3.刀具设计参数确定 (20)4.刀具工作草图 (21)第四部分第15号工序量具设计说明书 (22)1.工序尺寸精度分析 (22)2.量具类型确定 (22)3.极限量具尺寸公差确定 (22)4.极限量具尺寸公差带图 (22)5. 极限量具结构设计 (23)第五部分毕业设计体会 (23)第一部分 工艺设计说明书1. 零件图工艺性分析1.1零件结构功用分析法兰盘是可用于连接其他零件或可用于增加其他零件强度的一种零件。
本法兰盘是回转面和平面的结合,内部由阶梯孔和螺纹孔组成,其要求有较高的耐磨性,较高的强度和回转稳定性。
1.2零件技术条件分析1)法兰盘本身精度:外圆φ8019.00-+尺寸公差等级IT11,表面粗糙度Ra 为1.6μm ,φ52029.001.0--尺寸公差等级为IT6,表面粗糙度Ra 为1.6μm ,φ1201±尺寸公差等级IT14,表面粗糙度Ra 为3.2μm ,内孔φ62015.0±公差等级为IT7,φ36002.0-+尺寸公差等级IT6,φ65表面粗糙度Ra 为1.6μm ,距离φ36002.0-+为34.580.030.0--的平面公差等级IT13。
法兰盘零件机械加工工艺规程及工艺装备

课程设计计算说明书法兰盘零件机械加工工艺规程及工艺装备学院课程专业班级姓名学号指导教师日期任务书目录一、序言二、设计任务三、计算生产纲领、确定生产类型四、零件的分析五、确定毛坯的制造方法、初步确定毛坯形状六、工艺规程设计1、定位基准的选择2、制定工艺路线择3、工艺方案的比较和分析4、确定加工余量、工序尺寸及毛坯尺寸5、确定设计参数七、夹具设计1、设计要求2、夹具设计的有关计算3、夹具结构设计及操作说明八、参考文献设计图纸和说明书联系QQ2576636538 六工艺规程设计1.定位基准的选择基面选择是工艺规程设计中的重要工作之一。
基面选择得合理,可以使加工质量得到保证,生产率得以提高。
否则,加工工艺过程中会问题百出,更有甚者,还会造成零件大批报废,使生产无法正常进行。
(1)粗基准的选择选择粗基准主要是选择第一道机械加工工序的定位基准,以便为后续的工序提供精基准。
选择粗基准的出发点是:一要考虑如何分配各加工表面的余量:二要考虑怎样保证不加工面与加工面间的尺寸及相互位置要求。
对本零件而言,由于每个表面都要求加工,为保证各表面都有足够的余量,应选加工余量最小的面为粗基准。
可以法兰盘右端 45的外圆及 90的右端面作为粗基准。
在车床上用三爪卡盘夹紧45外圆可同时削除五个自由度,再以 90的右端面定位,从而达到完全定位。
(2)精基准的选择主要应该考虑基准重合的问题,当设计基准与工序基准不重合时,应该进行尺寸换算。
2.制定工艺路线制定工艺路线应当使零件的尺寸精度、形状精度、位置精度和表面质量等技术要求能得到合理的保证。
在生产纲领确定为中批生产的条件下,可以考虑采用通用性的机床配以专用夹具,并尽量使工序集中来提高生产率。
除此以外,还应当考虑经济效果,以便降低生产成本。
(1)工艺路线方案一工序1 车柱体的右端面,粗车 90右端面,车槽3×2,粗车、半精车外圆,车右端倒角工序2 粗车 100柱体左、右端面,粗车 90柱体左端面,半精车 100左、右端面、 90左端面,粗车外圆 45 、 100、 90,半精车外圆 45 、 100、 90,车100柱体的倒角,车 45 柱体的过度倒圆工序3 精车 100左端面, 90右端面工序4 钻、扩、粗铰、精铰孔 20mm至图样尺寸并车孔左端的倒角工序5 半精铣Φ91圆柱面上离中心线34mm的平面工序6 半精铣Φ91圆柱面上离中心线24mm的平面工序7 精铣Φ91圆柱面上离中心线24mm的平面工序8 磨削Φ91圆柱面上离中心线24mm的平面工序9 钻 4孔,铰 6孔工序10 钻 4—9孔工序11 磨削外圆面 100, 90工序12 磨削B面,即外圆面、100右端面、90左端面工序13 抛光B面工序14 去毛刺工序15 刻字刻线工序16 镀铬工序17 检测入库。
法兰盘加工工艺规程设计

法兰盘加工工艺规程设计法兰盘是一种用于连接和密封管道、阀门、设备等的零部件,其加工工艺规程设计的目的是为了确保法兰盘的质量和性能符合要求。
下面是一份关于法兰盘加工工艺规程设计的详细介绍,超过1200字。
一、加工工艺流程设计1.材料准备:根据客户提供的图纸和规格要求,选用适当的材料加工法兰盘。
常用的材料有碳钢、不锈钢、铸铁等。
2.下料:根据法兰盘的尺寸和形状,在材料上进行下料,保证材料的大小和形状符合要求。
3.倒角:对下料后的材料进行倒角处理,以提高法兰盘的加工精度和外观质量。
4.车削工艺:将倒角后的材料进行车削加工,使其达到图纸要求的尺寸和形状,并保证其圆度和平面度等要求。
5.钻孔:根据法兰盘的图纸要求,在车削好的工件上进行钻孔加工,以便于后续的铆接和固定。
6.铆接:将钻孔的工件与其他部件进行铆接,确保法兰盘的连接牢固和密封性能良好。
7.磨光:对铆接完毕的法兰盘进行磨光处理,消除表面的毛刺和不平整,保证其外观质量。
8.热处理:对法兰盘进行热处理,提高其强度和硬度,以适应工作环境的要求。
9.清洗和包装:将加工完毕的法兰盘进行清洗,去除表面的污垢和切削液,然后用塑料薄膜包装,以防止氧化和腐蚀。
二、工艺参数的确定1.车削加工参数:根据材料的硬度和形状要求,确定车削加工的刀具种类、切削速度、切深和进给速度等参数。
2.钻孔加工参数:根据法兰盘的孔径、深度和材料的硬度,确定钻孔的刀具种类、切削速度和进给速度等参数。
3.磨光加工参数:根据法兰盘的尺寸和形状要求,确定磨光的刀具种类、转速和磨削时间等参数。
4.热处理参数:根据材料的种类和硬度要求,确定热处理的温度、时间和冷却速度等参数。
三、质量控制1.原材料检验:对进厂的原材料进行外观检查和化学成分分析,确保材料的质量符合标准要求。
2.加工中的质量控制:在加工过程中,对各道工序进行定期的检验和测试,以确保加工质量满足要求。
3.最终产品检验:对加工完毕的法兰盘进行尺寸、形状和性能等方面的检验,确保产品符合图纸和客户的要求。
法兰盘 零件
法兰盘零件(批量生产)机械加工工艺规程及工艺装备设计一、零件分析法兰盘是一个回转体零件,起联接作用,是一类重要零件。
根据零件图(见附图1)及技术要求,可以确定所需加工面有一组加表面以Φ20为中心,包括:Φ100 的端面,尺寸为Φ45的圆柱面,两个Φ90的端面及上面的4个Φ9的透孔。
Φ45的外柱面及上面Φ6的销孔,Φ90端面上距离中心线分别为34和24的两个平面。
这组加工面是以Φ20孔为中心,其余加工面都与它有位置关系,可以先加工一个端面,以其为定位基准,采用专用夹具加工另一个端面,接着加工其他表面。
二、毛坯的选择(一)毛坯的制造形式零件材料为HT200,由于批量生产,零件的轮廓尺寸又不大,故采用金属模铸法,法兰毛坯比较简单,采用铸造毛坯时一般成对铸造,再进行机械加工。
不仅提高成产率,还保证加工精度。
(二)毛坯尺寸及公差在后面确定(三)毛坯图的设计1、确定圆角半径为减少铸件的应力集中,取铸件的圆角半径为R5。
2、确定分模面由零件的结构特征知,可以选过轴线的平面为分模面,采用两箱造型。
3、确定起模斜度由于铸件要求加工,按增加壁厚的规律确定。
查【1】《材料成型工艺基础表》2.7,取起模斜度1。
4确定毛坯的热处理方式铸件铸造后应安排时效处理,以消除残余的铸造应力,防止在机械加工过程中出现变形情况。
5、毛坯图见《附表2》三、加工工艺路线(一)定位基准的选择原则先基后它、先面后孔、先粗后精、先主后次各个工序的定位基础查看工序卡1至13。
(二)零件表面加工方法的选择本零件的加工面有外圆、端面、孔、平面槽等,材料为HT200,以技术要求及要求的各种技术参数,参考【2】《机械加工工艺手册》确定各个面的加工方法,如下:1、φ100的左端面:尺寸精度不高,表面粗糙度Ra1.6um,需要粗车、半精车、精车。
2、φ100外圆柱面:公差等级为IT6,表面粗糙度Ra0.8um,需要粗车、半精车、精车,3、B面:其中两端面精度不高,外圆柱面公差等级为IT9,但表面粗糙度都为Ra0.4um,需要粗车、半精车、精车、抛光。
法兰盘机械加工工艺规程编制与工时定额计算
目录1、零件的分析 (2)1.1零件的作用 (2)1.2 零件的工艺分析 (2)2、工艺规程设计 (2)2.1确定毛坯的制造形式 (2)2.2基面的选择 (2)2.3工件表面加工方法的选择 (3)2.4制定工艺路线 (3)2.5机械加工余量,工序尺寸及毛坯尺寸的确定 (4)2.6确定切削用量及工时 (6)3、夹具设计 (31)3.1 夹具分析 (31)3.2夹具设计 (31)3.2.1 定位基准的选择 (31)3.2.2考虑夹紧机构 (31)3.2.3 定位误差分析 (32)3.2.4 夹具设计及操作的简要说明 (32)4、设计小结 (33)5参考文献 (34)法兰盘(2)的机械加工工艺规程编制及工时定额计算1、零件的分析1.1零件的作用题目所给定的零件是CA6140车床上的法兰盘,法兰盘起联接作用是车床上的重要零件。
1.2 零件的工艺分析法兰盘是一回转体零件,有一组加工表面,这一组加工表面以Φ20045.0+mm的孔为中心 ,包括:两个Φ12.034.0100--mm的端面, 尺寸为Φ017.045-mm的圆柱面,两个Φ90mm的端面及上面的4个Φ9mm的透孔. Φ6.045-mm的外圆柱面及上面的Φ6mm的销孔, Φ90mm端面上距离中心线分别为34mm和24mm的两个平面.这组加工表面是以Φ20045.0+mm为中心,其余加工面都与它有位置关系,可以先加工它的一个端面,再借助专用夹具以这个端面为定位基准加工另一端面,然后再加工其它加工表面.2、工艺规程设计2.1确定毛坯的制造形式零件材料为HT200,由于该零件是中批生产,而且零件轮廓尺寸不大,故采用金属模铸造,法兰盘因毛坯比较简单,采用铸造毛坯时一般是成队铸造,再进行机械加工。
这从提高生产率,保证加工精度上考虑也是应该的。
2.2基面的选择基面选择是工艺规程设计中的重要工作之一。
基面选择得正确与合理,可以使加工质量得到保证,生产率得以提高。
法兰盘的机械加工工艺规程及铣平面工艺装备设计
辽宁工程技术大学课程设计题目:法兰盘的机械加工工艺规程及铣平面工艺装备设计班级:姓名:学号:指导教师:完成日期:一、设计题目法兰盘的机械加工工艺规程及铣平面工艺装备设计二、原始资料(1)被加工零件的零件图(草图)1张(2)生产类型:中批或大批大量生产三、上交材料(1)被加工工件的零件图1张(2)毛坯图1张(3)机械加工工艺过程综合卡片1张(4)与所设计夹具对应那道工序的工序卡片1张(5)夹具装配图1张(6)夹具体零件图1张(7)课程设计说明书(约5000~8000字)1份四、进度安排(参考)(1)熟悉零件,画零件图2天(2)选择工艺方案,确定工艺路线,填写工艺过程综合卡片5天(3)工艺装备设计(画夹具装配图及夹具体图)9天(4)编写说明书3天(5)准备及答辩2天五、指导教师评语成绩:指导教师冷岳峰日期摘要机械制造课程设计是在我们学习机械制造技术基础后进行的课程设计.通过此次设计对我们之前对所学各课程的一次深入的综合性的总复习,也是一次理论联系实际的训练,提高了我们的操作能力.这次设计的是法兰盘是CA6140卧式车床上的法兰盘,它位于车床丝杆的末端,主要作用是标明刻度,实现纵向进给.首先我们要熟悉零件,了解法兰盘的作用,接下来根据零件的性质和零件图上各端面的粗糙度确定毛坯的尺寸和机械加工余量。
然后我们再根据定位基准先确定精基准,后确定粗基准,最后拟定法兰盘的工艺路线图,制定该工件的夹紧方案,画出夹具装配图。
AbstractMachinery Manufacturing Technology curriculum design is after learning Machinery Manufacturing Technology base course technology and the most basic course after the specialized, which is our graduation project before conducting the various courses of study by an in-depth comprehensive review of the total, is also a Theory with practical training, therefore, in our four years of university life occupy an important position.This design is the flange is a CA6140 lathe horizontal flange, which is located lathe screw at the end, the main role is to indicate scale, to achieve vertical feed. First, we must familiarize themselves with spare parts, to understand the role of flange , the next according to the nature of components and parts diagram of the roughness on each face to determine the size and mechanical rough machining allowance. Then were-positioning the benchmark according to first determine the precise benchmarks determined rough benchmark, the finalization process flange road map for developing the workpiece clamping program, draw fixture assembly diagram.目录1、法兰盘的工艺分析及生产类型的确定 (1)1.1 法兰盘的用途 (1)1.2法兰盘的技术要求 (2)1.3法兰盘的生产类型 (3)2.确定毛坯绘制毛坯简图 (4)2.1选择毛胚 (4)2.2确定毛胚的尺寸公差和机械加工余量 (5)2.2.1公差等级 (6)2.2.2法兰盘铸造毛坯尺寸工差及加工余量 (6)2.2.3. 绘制法兰盘毛坯简图 (7)3. 拟定法兰盘工艺路线 (7)3.1定位基准的选择 (7)3.1.1.精基准的选择 (7)3.1.2粗基准的选择 (8)3.2表面加工方法的确定 (8)3.3加工阶段的表面加工方法的确定划分 (9)3.4工序的集中与分散 (9)3.5工序顺序的安排 (10)3.5.1机械加工工序 (10)3.5.2热处理工序 (10)3.5.3.辅助工序 (10)3.6确定工艺路线 (10)4加工余量、工序尺寸和工差的确定 (12)5. 切削用量、时间定额的计算 (12)5.1、切削用量的计算 (12)5.1.1精铣工步 (12)5.1.2粗铣工步 (12)5.2时间定额的计算 (12)5.2.1基本时间tj的计算 (13)5.2.2辅助时间ta的计算 (13)5.2.3其他时间的计算 (14)5.2.4单件时间tdj的计算 (14)6.夹具设计 (15)6.1提出问题 (15)6.2设计思想 (15)6.3夹具设计 (16)6.3.1定位分析 (16)6.3.2切削力及夹紧力的计算 (17)6.3.3夹具操作说明 (17)7. 体会与展望 (18)8.参考文献 (19)法兰盘零件图1、法兰盘的工艺分析及生产类型的确定1.1、法兰盘的用途题目给的零件是CA6140卧式车床上的法兰盘,它位于车床丝杆的末端,主要作用是标明刻度,实现纵向进给。
设计“法兰盘”零件的机械加工工艺规程及Φ6和Φ4孔的工艺装备设计
一、设计题目设计“法兰盘”零件的机械加工工艺规程及Φ6和Φ4孔的工艺装备设计二、设计要求设计的要求包括如下几个部分:1.绘制零件图。
1张2. 绘制零件毛坯图。
1张3. 编制机械加工工艺过程综合卡片1张4.编制零件的机械加工工艺卡片。
1套5.绘制夹具装配图(A0或A1)1张6. 绘制夹具体零件图1张7.编写课程设计说明书(约5000——8000字)。
1份说明书主要包括以下内容(章节)(1).目录(2).摘要(中外文对照的,各占一页)(3).零件工艺性分析(4).机械加工工艺规程设计(5).指定工序的专用机床夹具设计(6).方案综合评价与结论(7).体会与展望(8).参考文献列出参考文献(包括书、期刊、报告等,15条以上)三、上交材料1.零件图1张2.毛坯图1张3.机械加工工艺过程卡片1张4.零件的机械加工工艺卡片1张5.夹具装配图6 夹具零件图6.设计说明书1份四、进度安排1.第l~2天查资料,熟悉题目阶段。
2.第3~7天,完成零件的工艺性分析,确定毛坯的类型、制造方法和机械加工工艺规程的设计并编制出零件的机械加工工艺卡片。
3.第8~10天,完成夹具总体方案设计(画出草图,与指导教师沟通,在其同意的前提下,进行课程设计的下一步)。
4.第11~13天,完成夹具总装图的绘制。
5.第14~15天,零件图的绘制。
6.第16~18天,整理并完成设计说明书的编写。
7.第19天,完成图纸和说明书的输出打印。
8.第20~21天,答辩五、指导教师评语此套设计有全套CAD图和卡片,有意者请联系我索取522192623@成绩:指导教师日期摘要设计内容:设计“法兰盘”零件的机械加工工艺规程及工艺装备,并绘制出法兰盘零件图、毛坯图、夹具装配图,填写工艺卡片,编制课程设计说明书。
设计意义:通过该课程设计,将所学理论与生产实践相结合,锻炼了自己分析问题、解决问题的能力,在这个过程中我独立地分析和解决了零件机械制造的工艺问题,设计了机床专用夹具这一典型的工艺装备,提高了结构设计能力,为今后的毕业设计及对自己未来将从事的工作进行了一次适应性训练,从而打下了良好的基础。
- 1、下载文档前请自行甄别文档内容的完整性,平台不提供额外的编辑、内容补充、找答案等附加服务。
- 2、"仅部分预览"的文档,不可在线预览部分如存在完整性等问题,可反馈申请退款(可完整预览的文档不适用该条件!)。
- 3、如文档侵犯您的权益,请联系客服反馈,我们会尽快为您处理(人工客服工作时间:9:00-18:30)。
学生课程设计说明书题目:“法兰盘”零件的机械加工工艺规程及工艺装备设计学生姓名: 学号:所在院系: 机电工程学院专业: 机械设计制造及自动化班级:指导老师: 职称:绪论机械制造工艺学课程设计使我们学完了大学的全部基础课、技术基础课以及大部分专业课之后进行的。
这是我们在进行毕业设计之前对所学各课程的一次深入的综合性的总复习,也是一次理论联系实际的训练,因此,它在我们四年的大学生活中占有重要的地位。
机械制造技术是一门非常重要的技术,人类的发展过程就是一个不断的制造过程。
因此,制造技术的重要性是不言而喻的,它有以下四个方面的意义。
1.社会发展与制造技术密切相关2.制造技术是科学技术物化的基础3.制造技术是所有工业的支柱4.制造技术国力和国防的后盾机械制造工艺学课程设计是在学完了机械设计制造工艺学、进行了生产实习之后的下一个教学环节。
它一方面要求学生通过设计能获得综合运用过去所学过的全部课程进行工艺及结构设计的基本能力,另外,也为以后作好毕业设计进行一次综合训练和准备。
学生通过机械制造工艺学课程设计,应在下述各方面得到锻炼:(1)能熟练运用机械制造工艺学课程中的基本理论以及在生产实习中学到的时间知识,正确地解决一个零件在加工中的定位、夹紧以及工艺路线安排、工艺尺寸确定等问题,保证零件的加工质量。
(2)提高结构设计能力。
学生通过设计借据(或量具)的训练,应当获得根据被加工零件的加工要求,设计出高效、省力、经济合理而能保证加工的夹具的能力。
(3)学会使用手册及图表资料。
掌握与本设计有关的各种资料的名称、出处,能够做到熟练运用。
就我个人而言,我希望能通过这次课程设计对自己未来将从事的工作进行一次适应性训练,从中锻炼自己分析问题、解决问题的能力,为今后参加祖国的“四化”建设打下一个良好的基础。
由于个人能力所限,设计尚有许多不足之处,恳请老师给予指导目录绪论一、零件的分析 (2)1.1 零件的作用 (2)1.2 零件的工艺分析 (2)二、工艺规程设计 (3)2.1 确定毛坯的制造形式 (3)2.2 基面的选择 (3)2.3 制定工艺路线 (3)2.3.1 工艺路线方案一 (4)2.3.2 工艺路线方案二 (5)2.3.3 最终工艺路线 (6)三、夹具设计 (7)3.1 问题的提出 (7)3.2 夹具设计 (7)3.2.1 定位基准的选择 (7)3.2.2 切削力及夹紧力的计算 (7)3.2.3 定位误差的分析 (8)3.2.4 夹具设计及操作的简要说明 (9)参考资料 (10)致谢 (10)一、零件的分析(一)零件的作用题目所给的零件是CA6140车床的法兰盘。
主要是用来安装在机床上,起到导向的作用使机床实现进给运动,零件上精度要求较高的两个平面用以装配,4个9φ孔是用于连接其他机构或零件的。
(二)零件的工艺分析CA6140车床共有八处加工表面,其间有一定位置要求。
分述如下:1. 以φ1000.120.34+-为基准面加工表面这一组加工表面包括:00.01745φ+- ,00.01745φ+-的右端面并导角2.以00.01745φ+- 端面为基准,车00.645φ+-、0.120.34100φ+-、90φ外圆,并导1.545⨯︒,和145⨯︒。
3. 以00.01745φ+- 端面为基准, 先用16φ的钻头钻孔,然后再用铰刀铰孔由于孔与00.01745φ+-有跳动的要求,所以要以00.01745φ+-端面为基准。
4.要以孔0.045020φ++为基准,精车所有外圆面,使其达到要求。
由上面分析可知,加工时应先加工一组表面,再以这组加工后表面为基准加工另外一组。
同时保证它们之间的跳动要求和尺寸要求等。
二、工艺规程设计(一)确定毛坯的制造形式零件材料为HT200。
考虑零件在机床运行过程中承受交变载荷及冲击性载荷不大,零件结构又比较简单,故选择铸件毛坯。
(二)基面的选择基面选择是工艺规程设计中的重要工作之一。
基面选择得正确与合理,可以使加工质量得到保证,生产率得以提高。
否则,加工工艺过程中会问题百出,更有甚者,还会造成零件的大批报废,使生产无法正常进行。
(1)粗基准的选择对于一般的轴类零件而言,以外圆作为粗基准是完全合理的。
但对于本零件来说,应尽可能选择不加工表面为粗基准。
按照有关粗基准的选择原则(即当零件有不加工表面时,应以这些不加工表面作粗基准,若零件有若干个不加工表面时,则应以与加工表面要求相对位置精度较高的不加工表面作粗基准)根据这个基准选择原则,现选取孔00.01745φ+-外轮廓表面作为粗基准。
(2)精基准的选择主要应该考虑基准重合的问题。
当设计基准与工序基准不重合时,应该进行尺寸换算,这在以后还要专门计算,此处不再重复。
(三)制定工艺路线制定工艺路线得出发点,应当是使零件的几何形状、尺寸精度及位置精度等技术要求能得到合理的保证。
在生产纲领已确定为大批生产的条件下,可以考虑采用万能性机床配以专用工夹具,并尽量使工序集中来提高生产率。
除此之外,还应当考虑经济效果,以便使生产成本尽量下降。
1.工艺路线方案一工序一 以0.120.34100φ+-为粗基准,粗车端面及外圆00.01745φ+-,并导ο457⨯,选用CA6140机床。
工序二 以00.01745φ+-外圆面为基准,粗车0.120.34100φ+-、90φ外圆,并导1.545⨯︒,和145⨯︒。
工序三 以00.01745φ+-外圆面为基准,钻0.045020φ++通孔,先用钻16φ的钻头钻孔,再铰孔达到0.045020φ++的尺寸。
工序四 导00.01745φ+-右端面145⨯︒角工序五 以0.045020φ++内孔为基准精车0.120.34100φ+-左端面和90φ右端面并保证00.01745φ+-跳动在0.03内,并切32⨯槽。
工序六 以右端面和外圆面定位,利用两个端面夹紧,铣粗糙度为3.2的90φ外圆左平面。
工序七 以刚铣的平面定位,利用两端面夹紧,铣90φ外圆右平面,保证尺寸为24。
工序八 以一个铣好的平面定位,再利用另外一个平面夹紧,钻4φ的通孔,再扩孔到6φ孔,保证尺寸为L=7,再铰孔使其达到所要求的精度。
工序九 以0.045020φ++ 图表 2孔为基准面,利用专用夹具,钻4个9φ孔。
工序十 再用磨床磨外圆使其达到所要求的粗糙度。
工序十一 检查。
2.工艺路线方案二工序一 车端面及外圆00.01745φ+-图表 3 ,以0.120.34100φ+-为粗基准,选用CA6140机床。
工序二 以00.01745φ+-外圆面为基准,粗车0.120.34100φ+-、90φ外圆,并导1.545⨯︒,和145⨯︒。
工序三 以00.01745φ+-外圆面为基准,钻0.045020φ++通孔,先用钻16φ的钻头钻孔,再铰孔达到0.045020φ++的尺寸。
以00.01745φ+-外圆面为基准,粗车0.120.34100φ+-、90φ外圆,并导1.545⨯︒,和145⨯︒。
工序四 以0.120.34100φ+-外圆面为基准,并导745⨯︒,和145⨯︒。
工序五 以0.045020φ++内孔为基准精车0.120.34100φ+-图表 4左端面和90φ右端面和00.01745φ+-保证跳动在0.03内,并车32⨯槽。
工序六 以右端面和一圆面定位,利用两个端面夹紧,先铣粗糙度为3.2的一面。
工序七 以刚铣的平面定位,,利用两端面夹紧,铣另外一面保证尺寸为24。
工序八 以一个铣好的面定位,再利用另外一个面夹紧,钻4φ的通孔,再圹孔到6φ孔,保证尺寸为L=7,再铰孔使其达到所要求的精度。
工序九 以0.045020φ++孔为基准面,利用专用夹具,钻4个9φ孔。
工序十 再用磨床磨外圆使其达到所要求的粗糙度。
工序十一 检查。
虽然工艺路线二的工序仍然是十一步,但多次加工00.01745φ+-表面,是精度要求和粗糙度的要求和有跳动的要求,另外00.01745φ+-表面是多次加工的基准,方案一中在加工其外圆表面的同时进行了导角,工序较为集中,也方便装夹,在一定程度上提高了生产效率。
所以选择第一个方案。
3.最终工艺路线工序一 以0.120.34100φ+-为粗基准,粗车端面及外圆00.01745φ+-图表 5 ,并导ο457⨯,选用CA6140机床。
工序二 以00.01745φ+-外圆面为基准,粗车0.120.34100φ+-、90φ外圆,并导1.545⨯︒,和145⨯︒。
工序三 以00.01745φ+-外圆面为基准,钻0.045020φ++通孔,先用钻16φ的钻头钻孔,再铰孔达到0.045020φ++的尺寸。
工序四 导00.01745φ+-右端面145⨯︒角工序五 以0.045020φ++内孔为基准精车0.120.34100φ+-图表 6左端面和90φ右端面和保证00.01745φ+-跳动在0.03内,并切32⨯槽。
工序六 以右端面和外圆面定位,利用两个端面夹紧,铣粗糙度为3.2的90φ外圆左平面。
工序七 以刚铣的平面定位,利用两端面夹紧,铣90φ外圆右平面,保证尺寸为24。
工序八 以一个铣好的平面定位,再利用另外一个平面夹紧,钻4φ的通孔,再扩孔到6φ孔,保证尺寸为L=7,再铰孔使其达到所要求的精度。
工序九 以0.045020φ++ 图表 7 孔为基准面,利用专用夹具,钻4个9φ孔。
工序十 再用磨床磨外圆使其达到所要求的粗糙度。
工序十一 终检三、夹具设计(一)问题的提出为了提高劳动生产率,保证加工质量,降低劳动强度,需要设计专用夹具。
本次设计加工φ6H9mm 孔的钻床夹具,本夹具将用于Z3025B 型摇臂钻床,刀具材料为高速钢,在法兰盘的φ45外圆表面上加工孔。
利用本夹具主要用来加工φ6H9mm ,这个孔内表面的粗糙度要求为2.3=a R ,在加工前先加工φ4mm 孔,且法兰盘的φ45h6mm 外圆表面和φ90mm 段两侧平面均已经过半精加工。
加工φ6H9mm 孔的整个过程包括钻、扩、铰三步,因此本工序的加工精度容易保证,主要考虑如何定位夹紧以节省操作时间提高生产率。
(二)、夹具设计⒈定位基准的选择由零件图知,φ6H9mm 孔对φ90mm 段右侧端面有一定的位置度要求,为了减少定位误差,以φ90mm 段右侧端面为主要定位基准面,以φ45h6mm 外圆表面和φ90mm 段一侧小平面为辅助定位面,共限制7个自由度,其中与φ6H9mm 孔轴线同方向的自由度被重复限制,但起到增强定位稳定性的作用,因此这一定位方案可行。
为了提高加工效率,缩短辅助时间,将钻套设计成快换钻套。
⒉切削力及夹紧力计算钻φ4mm 孔时切削量最大,切削力和加紧力也最大,这里只考虑钻φ4mm 孔时的切削力和加紧力。
刀具:高速钢麻花钻,φ4mm 。
钻孔时的轴向力查表1-2-7文献[1],NF k y Z C k f d C F F F F F Fy Z F F F 6400.13.047.4281.90.1,8.0,0.1,7.4281.98.00.10=⨯⨯⨯⨯======由于工件所受加紧力与切削力方向相互垂直,为防止工件在切削力作用下沿φ90mm 段较小平面侧边倾斜,使工件离开基面所需的夹紧力为:图表 8图表 9,因φ10mm钩型螺栓长度小于所需夹紧长度,为方便加紧,选用φ16mm的钩型夹紧螺栓夹紧,夹紧螺母上钻一φ16mm斜孔使之成为可快速拆装的螺母且定位套在φ45h6mm外圆段的定位套对工件有辅助支撑作用,使支撑更加稳定,因此选用该螺栓加紧足以满足加紧要求。