V法铸造技术
v法铸造工艺流程

v法铸造工艺流程
《V法铸造工艺流程》
V法铸造,又称垂直引流法铸造,是一种常用的金属铸造工艺,适用于制作各种形状复杂的铸件。
它主要通过在铸模中垂直引流金属液,实现铸件的成形。
下面将介绍V法铸造的工艺流程。
首先,选择合适的铸模。
铸模是V法铸造的关键,它的设计
要考虑到铸件的形状、尺寸和壁厚等因素,并且要具有良好的耐热性和导热性。
通常情况下,铸模会采用石膏模或者金属模具,以满足不同的铸造需求。
接下来,准备熔炼金属。
选择适当的金属合金,并将其熔化成液态,以备铸造使用。
在熔炼金属的过程中,需要控制好熔炼温度和炉内气氛,确保金属的纯度和流动性。
然后,进行垂直引流铸造。
将熔融金属液缓缓倒入铸模中,并通过垂直引流的方式,使金属液充满整个铸模。
这一过程需要严格控制倒注速度和倒注角度,以避免产生气泡和砂眼。
最后,待金属冷却凝固后,即可将铸模打开,取出成型的铸件。
接下来,对铸件进行修磨、清理等后处理工艺,使其达到设计要求的尺寸和表面质量。
总的来说,V法铸造工艺流程包括铸模选择、熔炼金属、垂直
引流铸造和后处理等多个环节,每个环节都需要严格控制和操作。
通过这些步骤的精细管理,才能最终获得高质量的铸件。
v法铸造工艺生产球墨铸铁件的技术总结

v法铸造工艺生产球墨铸铁件的技术总结
球墨铸铁是一种高强度、高韧性、高耐磨性的铸铁材料,广泛应用于机械制造、汽车制造、航空航天等领域。
而v法铸造工艺是球墨铸铁生产中常用的一种工艺,下面就来总结一下v法铸造工艺生产球墨铸铁件的技术要点。
v法铸造工艺的特点是在铸造过程中加入镁、稀土等元素,通过化学反应使铸铁中的石墨球化成球状,从而提高铸铁的强度和韧性。
在具体操作中,需要注意以下几点:
1. 铸型设计。
铸型的设计应考虑到球墨铸铁的特点,如热膨胀系数、收缩率等,以保证铸件的尺寸精度和表面质量。
2. 铸造温度。
球墨铸铁的铸造温度一般在1350℃左右,需要控制好铸造温度,以保证铸件的组织和性能。
3. 镁、稀土的添加。
镁、稀土的添加量应根据铸件的要求进行调整,一般在0.03%-0.05%之间。
4. 浇注方式。
球墨铸铁的浇注方式应尽量采用自由浇注或低压浇注,以避免铸件内部产生气孔和夹杂。
5. 热处理。
球墨铸铁的热处理一般采用正火+回火的方式,以提高铸件的强度和韧性。
除了以上几点,还需要注意铸造过程中的其他细节,如铸造速度、浇注时间、浇注位置等。
只有在严格控制每个环节的情况下,才能生产出高质量的球墨铸铁件。
v法铸造工艺是球墨铸铁生产中常用的一种工艺,通过控制铸造温度、添加镁、稀土等元素,以及严格控制铸造过程中的各个环节,可以生产出高质量的球墨铸铁件。
【热坛学习】V法铸造的优缺点对比
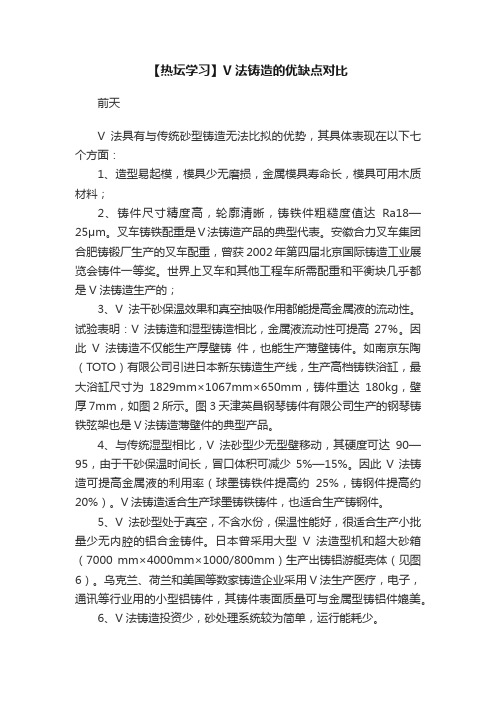
【热坛学习】V法铸造的优缺点对比前天V法具有与传统砂型铸造无法比拟的优势,其具体表现在以下七个方面:1、造型易起模,模具少无磨损,金属模具寿命长,模具可用木质材料;2、铸件尺寸精度高,轮廓清晰,铸铁件粗糙度值达Ra18—25μm。
叉车铸铁配重是V法铸造产品的典型代表。
安徽合力叉车集团合肥铸锻厂生产的叉车配重,曾获2002年第四届北京国际铸造工业展览会铸件一等奖。
世界上叉车和其他工程车所需配重和平衡块几乎都是V法铸造生产的;3、V法干砂保温效果和真空抽吸作用都能提高金属液的流动性。
试验表明:V法铸造和湿型铸造相比,金属液流动性可提高27%。
因此V法铸造不仅能生产厚壁铸件,也能生产薄壁铸件。
如南京东陶(TOTO)有限公司引进日本新东铸造生产线,生产高档铸铁浴缸,最大浴缸尺寸为1829mm×1067mm×650mm,铸件重达180kg,壁厚7mm,如图2所示。
图3 天津英昌钢琴铸件有限公司生产的钢琴铸铁弦架也是V法铸造薄壁件的典型产品。
4、与传统湿型相比,V法砂型少无型壁移动,其硬度可达90—95,由于干砂保温时间长,冒口体积可减少5%—15%。
因此V法铸造可提高金属液的利用率(球墨铸铁件提高约25%,铸钢件提高约20%)。
V法铸造适合生产球墨铸铁铸件,也适合生产铸钢件。
5、V法砂型处于真空,不含水份,保温性能好,很适合生产小批量少无内腔的铝合金铸件。
日本曾采用大型V法造型机和超大砂箱(7000 mm×4000mm×1000/800mm)生产出铸铝游艇壳体(见图6)。
乌克兰、荷兰和美国等数家铸造企业采用V法生产医疗,电子,通讯等行业用的小型铝铸件,其铸件表面质量可与金属型铸铝件媲美。
6、V法铸造投资少,砂处理系统较为简单,运行能耗少。
7、与其他砂型铸造相比,V法铸造环境友好,生产现场噪音低,铸件抛丸清理量减少50%以上,劳动力减少35%以上。
浇注时,薄膜、涂料和树脂砂芯产生的烟气都被真空系统抽走,经过干湿过滤后排空,对大气污染少;V法固体废弃物少,干砂再生高达95%。
v法铸造工艺流程

v法铸造工艺流程
《V法铸造工艺流程》
V法铸造是一种高效、节能的金属铸造工艺,广泛应用于汽车、航空航天、能源等领域。
V法铸造工艺流程主要包括以下几个步骤:
1. 模具设计:首先要根据产品的需求设计出合适的模具。
V法铸造的模具一般采用耐磨材料制作,可以保证模具的使用寿命和产品的精度。
2. 熔炼金属:将金属料加热至熔点,然后倒入模具中。
V法铸造通常使用铝合金、镁合金等轻金属,因为这些材料具有良好的流动性和耐腐蚀性。
3. 冷却固化:金属倒入模具后,需要进行冷却固化。
在此过程中,金属会逐渐凝固成型,并且在模具内部形成产品的轮廓。
4. 处理表面:产品凝固后,需要进行表面处理,比如去毛刺、打磨、喷漆等,以提高产品的外观和表面质量。
5. 检验包装:最后,需要对产品进行检验,确保产品符合质量要求,并进行包装。
V法铸造工艺所制造出的产品通常具有较高的精度和表面质量。
总的来说,V法铸造工艺流程相对简单,但要求控制严格。
通过合理的模具设计和加工工艺,可以生产高质量、精密度高的
铸件,满足不同行业的需求。
随着科技的不断发展,V法铸造工艺也在不断改进和完善,将为工业生产带来更多的可能性。
V法铸造

V法铸造V法铸造和消失模铸造亦称负压铸造,因取英文Vacuum(真空)一词的字头“V”而得名。
它区别于传统砂铸最大的优点是不使用粘合剂,V法铸造是利用塑料薄膜密封砂箱,靠真空抽气系统抽出型内空气,铸型内外有压力差,使干砂密实,形成所需型腔,经下芯、合箱、浇注抽真空使铸件凝固,解除负压,型砂随之溃散而获得铸件。
V法铸造和消失模铸造与传统砂铸相比,具有以下优点:其一,因其采用负压浇注铸件砂眼气孔少、产品密实度高、表面光洁、轮廓清晰、尺寸准确;其二,节能高效清洁生产。
采用V法和消失模技术能使干砂反复利用,不用烘型,耗煤减少,但由于长期真空机作业,耗电量稍有增加,但极大的减少粉尘,节约人力资本,使得铸造工作更加有效,节约劳动力和极大降低劳动强度,在浇注过程中有害气体少,真正实现环保生产。
V法生产关键点在于选中真空抽气系统,在选用真空抽气系统的时候,首先要确定真空泵的容量,主要考虑以下因素:1、需同时在真空下工作的砂箱的尺寸和数量;2、同时浇注的铸型的数量;3、浇注的尺寸和形状;4、紧靠薄膜的铸型表面的透气性,它控制着通过塑料薄膜上的裂口而进入铸型的空气量,因而在浇注时,有必要使用少量的铸型涂料,它有助于为真空机提供一个“辅助密封层”。
V法铸造工艺1、制造带有抽气箱和抽气孔型板;2、将烘烤呈塑性状态的塑料薄膜覆盖在型板上加热,温度一般在80℃-120℃之间、同时,真空泵抽气使薄膜密贴在型板上成型;3、将带有过滤抽气管的砂箱放在已覆好塑料薄膜的模板上;4、向砂箱内充填没有粘结剂与附加物粒度为100-200目的干石英砂,借微震使砂紧实,刮平,放上密封薄膜、打开阀门抽去型砂内空气,使铸型内外存在压力差(约300~400mmHg)。
由于压力差的作用使铸型成型并具有较高的硬度,湿型硬度计读数可达95左右;5、解除模板内的真空,然后进行拔模。
铸型要继续抽真空直到浇注的铸件凝固为止。
依上法制下型;6、下芯、合箱、浇注;7、待金属凝固后,停止对铸型抽气,型内压力接近大气压时,铸型就自行溃散。
v法铸造薄膜
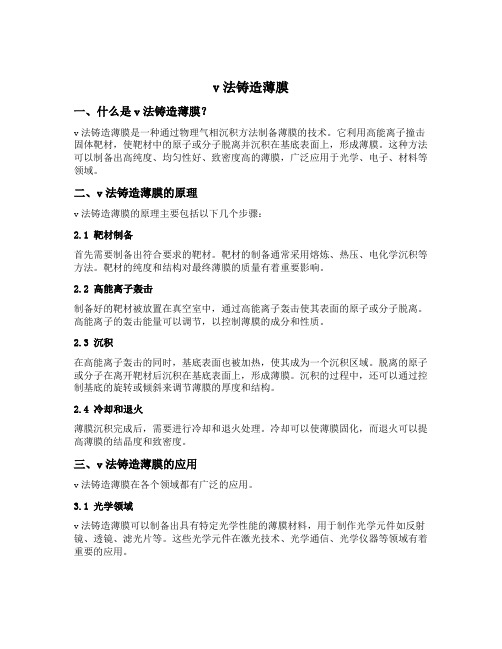
v法铸造薄膜一、什么是v法铸造薄膜?v法铸造薄膜是一种通过物理气相沉积方法制备薄膜的技术。
它利用高能离子撞击固体靶材,使靶材中的原子或分子脱离并沉积在基底表面上,形成薄膜。
这种方法可以制备出高纯度、均匀性好、致密度高的薄膜,广泛应用于光学、电子、材料等领域。
二、v法铸造薄膜的原理v法铸造薄膜的原理主要包括以下几个步骤:2.1 靶材制备首先需要制备出符合要求的靶材。
靶材的制备通常采用熔炼、热压、电化学沉积等方法。
靶材的纯度和结构对最终薄膜的质量有着重要影响。
2.2 高能离子轰击制备好的靶材被放置在真空室中,通过高能离子轰击使其表面的原子或分子脱离。
高能离子的轰击能量可以调节,以控制薄膜的成分和性质。
2.3 沉积在高能离子轰击的同时,基底表面也被加热,使其成为一个沉积区域。
脱离的原子或分子在离开靶材后沉积在基底表面上,形成薄膜。
沉积的过程中,还可以通过控制基底的旋转或倾斜来调节薄膜的厚度和结构。
2.4 冷却和退火薄膜沉积完成后,需要进行冷却和退火处理。
冷却可以使薄膜固化,而退火可以提高薄膜的结晶度和致密度。
三、v法铸造薄膜的应用v法铸造薄膜在各个领域都有广泛的应用。
3.1 光学领域v法铸造薄膜可以制备出具有特定光学性能的薄膜材料,用于制作光学元件如反射镜、透镜、滤光片等。
这些光学元件在激光技术、光学通信、光学仪器等领域有着重要的应用。
3.2 电子领域v法铸造薄膜可以制备出导电性能良好的薄膜材料,用于制作电子元器件如晶体管、电容器、电阻器等。
这些电子元器件广泛应用于电子设备、集成电路等领域。
3.3 材料领域v法铸造薄膜可以制备出具有特殊功能的薄膜材料,如防腐蚀薄膜、防磨损薄膜、防反射薄膜等。
这些功能性薄膜在材料工程、表面处理等领域有着广泛的应用。
3.4 生物医学领域v法铸造薄膜还可以制备出用于生物医学领域的薄膜材料,如生物传感器、药物控释器等。
这些薄膜在生物医学诊断、药物研发等方面具有重要的应用价值。
V法造型
V 法造型
V法造型又称负压造型,它采用塑料薄膜抽真空使干砂成型的原理,是第三代造型技术,也是目前世界上最新的造型技术,其自动化程度高、精度高、铸件质量高,并且具体节能、无污染的突出优点,由于它不使用粘结剂,落砂简便,使造型材料的耗量降到最低限度,减少了废砂,改善了劳动条件,提高了铸件表面质量和尺度精度,降低了铸件的生产能耗,是一种很有发展前途的先进的铸造工艺,被称为绿色环保造型技术。
我公司自主创新设计完成的V法生产线,自动化程度高,工艺流程先进,设备的先进性,实用性及可靠性好,达到了国际同类产品先进水平,可以满足不同用户需求。
v法铸造工艺流程图:
v法生产线:。
V法铸造概述
V法铸造简介(一)工艺特点:真空密封造型(V法造型)与传统砂型铸造方法有很大的不同,是一种物理造型法,它将真空技术与砂型铸造结合,用不加水份和粘结剂的原砂造型,靠塑料薄膜将砂型的型腔面和背面密封起来,借助真空泵抽气产生负压,造成砂型内、外压差使型砂紧固成型,经下芯、合箱、浇注,待铸件凝固,解除负压或停止抽气,型砂便随之溃散而获得铸件。
(二)V法造型的工艺过程如下所示:1.制造带有抽气箱和抽气孔模板。
2.将烘烤呈塑性状态的塑料薄膜覆盖在型板上、真空泵抽气使薄膜密贴在型板上成型。
如图:3.将带有过滤抽气管的砂箱放在已覆好塑料薄膜的模板上。
4.向砂箱内充填充有粘结剂与附加物的干石英砂,借微震使砂紧实,刮平,放上密封薄膜、打开阀门抽去型砂内空气,使铸型内外存在压力差(约300~400mmHg)。
由于压力差的作用使铸型成型并具有较高的硬度,湿型硬度计读数可达95左右如图:5. 解除模板内的真空,然后进行拔模。
铸型要继续抽真空直到浇注的铸件凝固为止。
依上法制下型6.下芯、合箱、浇注。
如图:7.待金属凝固后,停止对铸型抽气,型内压力接近大气压时,铸型就自行溃散。
(三)V法造型的特点:1、提高铸件质量:表面光洁、轮廓清晰、尺寸准确。
用较细干砂,铸型硬度高且均匀,拔模容易。
2、简化设备、节约投资、减少运行各维修费用。
省去有关粘合剂、附加物及混砂设备。
旧砂回用率在95%以上。
模具及砂箱使用寿命长3、金属利用率高。
V法造型中,金属活动性较好,充填能力强,可以铸出3mm的薄壁件。
铸型硬度高、冷却慢;利用补缩,减少冒口的尺寸。
工艺出品率提高,减少了加工余量。
二、基本工艺装备及设备1、SK型水环式真空泵:为V法铸造提供真空环境。
2、震实台:紧实砂型3、薄膜烧烤器:加热薄膜,管式电加热器作加热元件,也可用火焰或电阻元件加热远红外线板。
4、模板及芯盒:抽气孔ф2~3mm,要保证薄膜密贴模板,薄膜成型欠佳的部位需要加钻小孔。
5、有过滤抽气装置的砂箱及芯盒抽气方式:导管式、复合式、侧箱式。
消失模V法实型铸造工艺及装备研发生产方案(一)
消失模/V法/实型铸造工艺及装备研发生产方案一、实施背景随着制造业的不断发展,铸造技术及装备也在逐步升级。
消失模、V法、实型铸造等工艺作为现代铸造技术的前沿,对于提高铸件质量、降低生产成本、节能减排具有重要意义。
然而,目前国内铸造行业在这方面的研发生产投入相对较少,相关技术及装备仍存在诸多不足。
因此,开展消失模/V法/实型铸造工艺及装备研发生产具有迫切性和必要性。
二、工作原理1.消失模铸造(Lost-Foam Casting):利用泡沫塑料模样代替传统的木模或金属模,在浇注过程中模样逐渐被熔化,并由液体金属替代。
此方法具有尺寸精度高、材料成本低、生产周期短等优点。
2.V法铸造(Vacuum Casting):采用塑料薄膜或玻璃纸作为型壳材料,借助真空泵抽出型壳内的空气,使型壳内形成负压,从而将液体金属吸入型壳并凝固成铸件。
此方法具有表面质量好、尺寸精度高等优点。
3.实型铸造(Solid Modelling):利用树脂等快速凝固材料制作实体模样,在模样表面涂覆一定厚度的涂料后进行浇注。
此方法具有无模样消耗、适用范围广等优点。
三、实施计划步骤1.技术调研:对国内外消失模/V法/实型铸造工艺及装备进行深入调研,分析现有技术的优缺点及发展方向。
2.研发团队组建:组建涵盖机械设计、材料科学、铸造工艺等方面的专业研发团队。
3.技术研发:开展消失模/V法/实型铸造工艺及装备的关键技术研发,包括铸造材料、工艺优化、设备选型等。
4.实验验证:通过系列实验验证研发成果的可行性和可靠性。
5.产品化开发:将研发成果转化为实际产品,并制定相应的生产工艺和质量控制体系。
6.推广应用:与相关企业合作,推广消失模/V法/实型铸造工艺及装备在生产中的应用。
四、适用范围1.消失模铸造适用于各种复杂形状的铸件,如铝合金、铸铁等。
2.V法铸造适用于对表面质量要求较高的铸件,如精密零件、叶片等。
3.实型铸造适用于各种形状的铸件,特别适用于大型和复杂形状的铸件,如汽轮机叶片、船用螺旋桨等。
V法铸造工艺手册
⑦便于管理和组织生产。V法铸生产周期短, 工艺简便,操作容易,不需要很熟练的技 术工人。且工人的劳动强度大大降低。 ⑧适用范围较广 a. V法铸造适用于机械自动化大批量生产。 b.可用于铸铁、铸钢等黑色金属,也可用 于铜、铝、镁等有色金属。
缺点:
因受造型工艺的限制,生产率不易提高。 由于塑料薄膜延伸性的限制,目前生产几 何形状特别复杂的铸件还有一定的困难。 用真空密封造型法制芯,因太复杂,不如 采用传统方法制作。 造型时要时刻保证真空连接。
④节约原材料和动力。由于V法使用干砂,落砂 容易,砂子的回收率可达95%以上,采用V法造 型消耗的动力较小,仅为湿型法的60%,可减少 劳动力35%。
⑤模样和砂箱使用寿命长。因模样有塑料薄膜保 护,拔模力很小,只有微振且不受高温高压作用, 所以模样不易变形和损坏。 ⑥改善工作环境。 a.造型及浇注过程中产生的微量气体大都被真空 泵抽走,空气污染小。 b.落砂后,无大量废砂处理。工作环境基本可以 做到无尘化。
塑料薄膜在模型或芯盒内的成型能力的 好坏,直接影响铸件的光洁度和尺寸精度。 因此,塑料薄膜的选择、质量的控制及使 用方法是V法铸造的重要环节。 目前,国内大多采用乙烯醋酸乙烯共聚 体薄膜(向聚乙烯中加入比例18%EVA)。 而在铸型背面则采用普通农用的聚乙烯薄 膜就可以了,可以降低薄膜成本。 注意:有一种普遍使用的薄膜叫PVC。 在任何条件下不要在V法中使用PVC !薄膜 接触熔融金属后蒸发,产生一种有毒的氯 气破坏产品。
EVA薄膜加热覆膜过程:
薄膜加热时,可以看到成形过程有三个阶 段。
成形的第一阶段:加热开始时,薄膜膨胀 产生波动收缩,随之形成许多波纹。 成形的第二阶段:波纹消失获得一个类镜 面。薄膜开始发亮时,这时是覆膜的最佳 阶段。薄膜应在5S内覆于模具上。 成形的第三阶段: 对薄膜进一步加热,开 始出现孔洞,孔洞开始扩展,薄膜则不能 再用。
- 1、下载文档前请自行甄别文档内容的完整性,平台不提供额外的编辑、内容补充、找答案等附加服务。
- 2、"仅部分预览"的文档,不可在线预览部分如存在完整性等问题,可反馈申请退款(可完整预览的文档不适用该条件!)。
- 3、如文档侵犯您的权益,请联系客服反馈,我们会尽快为您处理(人工客服工作时间:9:00-18:30)。
V法铸造技术一什么是V法铸造?
图1.1 V法工艺准备模型
图1.2 V法工艺薄膜加热
图1.3 V法工艺模型抽真空覆面膜、喷涂料
图1.4 V法工艺将砂箱放于模型上
图1.5 V法工艺将砂子加入砂箱、振实
图1.6 V法工艺砂型顶部覆背膜
图1.7 V法工艺砂箱抽真空、模型去真空、起模
图1.8 V法工艺合箱、浇注
图1.9 V法工艺铸件落砂
1 V法铸造原理。
V法铸造,也称真空密封造型法或负压造型法,取‘真空’英文字‘Vacuum’的字头,而简称V法。
这种工艺采用不含任何粘结剂的干砂造型,利用塑料薄膜和真空砂箱密封,依靠真空泵形成铸型内外的压力差,使干砂紧实成型,并在负压条件下浇注,待液态金属凝固后,除去真空,砂型溃散,取出铸件。
V法铸造和消失模铸造都是继机械成型和化学成型之后的第三代物理成型方法。
2 V法铸造工艺过程
见图1.1——图1.9,九个步骤:
1)准备模具。
模具上有透气孔与型板抽气室相连。
2)薄膜加热。
将EV A塑料薄膜放置在烤膜器下加热到软化状态。
3)覆面膜、喷涂料。
是关键工序,通过模具上的透气孔将负压作用于软化的塑料薄膜,使之与模具紧密贴覆;在塑模外喷涂料并烘干。
4)放置砂箱。
将负压砂箱放置在模具上。
5)加砂振实。
加干砂充满砂箱,通过振实台使干砂获得最大密度。
6)覆背膜。
上型将浇口盆与上型直浇道相连,冒口和排气孔要与大气相通;下型只需将砂子刮平覆背膜。
7)砂箱抽真空、起模。
造成砂型内外压差,使干砂得到紧实,同时释放模具抽气室的真空,并通入压缩空气反吹,将砂型与模具分开。
8)合箱。
将上型与下型合箱,准备浇注。
9)浇注、落砂。
浇注时砂型继续抽真空。
铸件冷却定形后,除去真空,砂型溃散,取出铸件。
3 造型材料
1)型砂。
石英砂,SiO2含量98%以上,粒度70-150目。
2)塑料薄膜。
○1.薄膜必须没有气泡滴和针孔等缺陷,。
○2薄膜必须有很好的延伸性。
○3.成型后的薄膜不再保留弹性。
○4.薄膜不应与模型粘住。
○5.一般常用乙烯醋酸乙烯共聚体薄膜(EV A),厚度0.1-0.2。
3)涂料。
根据铸件的材质、外形、壁厚等选用,需具有以下性能:○1.具有适合雾状喷涂的流动性和触变性,能牢固粘附在塑料薄膜上形成致密涂层,快速干燥,发气量较小;
○2.涂料层具备高耐火性能,对金属液有低润湿性,有良好的抗机械渗透粘砂的能力,可替代已熔化或汽化的薄膜,保持铸型完整性;○3.涂料含固量高,浇注后涂料形成烧结剥离层。
4 工艺装备。
1)真空系统。
口诀:V法铸造没有巧,全凭负压玩得好。
①真空泵有湿式和干式两种。
湿式真空泵又称水环式真空泵,固定安装;干式泵装在天车上,供铸型转运时抽气用。
V法铸造需要大流量低负压:造型保压0.03MPa-0.04 MPa,浇注保压0.04 MPa- 0.05MPa,浇注后立即降为0.02MPa ,10-15分钟后解去负压。
②稳压罐。
稳定真空系统的压力,缓冲压力波动对造型浇注的影响。
③除尘罐。
防止从砂箱内抽吸的细砂或粉尘进入泵内,磨损零件。
④真空管道、控制阀门及负压计。
2)造型设备
①砂箱。
有侧面抽气、侧顶面抽气、管式抽气和软管抽气四种形式。
②模型和型板。
③三维振实台。
④薄膜加热器。
3)砂处理系统其作用是落砂、降温、循环使用。
5 V法生产线的几种形式
1)固定式单机造型机组。
2)造型台车移动式。
3)一字型梭动式。
4)转台式造型机组(2工位、4工位、6工位、8工位)
6 V法铸造的优缺点。
A 优点:
1)造型易起模,模具少无磨损,寿命长。
2)铸件尺寸精度高,轮廓清晰,表面光洁。
3)V法干砂保温效果和真空抽吸作用都能提高金属液的流动性,利于生产薄壁铸件。
如南京东陶(TOTO)有限公司引进日本
新东铸造生产线,生产高档铸铁浴缸,最大尺寸为1829mm×
1067mm×650mm,重量180kg,壁厚7mm。
4)冒口体积减小。
金属液利用率提高。
5)投资较少,砂处理系统较为简单,运行能耗较低。
6)铸件成本降低。
7)V法铸造环境友好。
噪音较低;铸件抛丸清理量减少50%以上;
浇注时,薄膜、涂料和树脂砂芯产生的烟气都被真空系统抽走,
过滤后排空,对大气污染少;固体废弃物少,干砂回用高达
95%,符合节能减排要求,被称为‘绿色铸造’。
B 缺点:
1)受薄膜延伸性能的局限,不适宜生产外形复杂铸件。
2)V法制芯技术还不成熟。
3)真空系统始终要与砂型相连。
4)不适合生产小型铸件,生产效率难以提高;
5)铸钢易出现气孔和夹渣等铸造缺陷,低碳钢有较严重的增碳。
二V法铸造的现状和发展
1. 国外
V法造型工艺是日本长野县工业实验室和秋田株式会社20世纪60年代末发明的。
现在,世界上有十几个国家和地区约300条生产线在使用,生产设备逐步向大型化发展。
铸件材质有铸钢、铸铁和有色金属,铸件壁厚3~340mm。
2. 国内
我国从1974年起进行试验和研究。
目前,我国应用V法铸造工艺的约有200多个厂家,数百条生产线,生产铸件品种繁多,如浴盆、配重、铁路叉道、水泵壳体、阀体、变速箱体、耐磨衬板、锅炉片等。
材质有铸铁、铸钢及有色金属等。
经过多年经验证明,V法工艺与树脂砂和消失模工艺相比,在铸
件形状允许的条件下,应优先考虑V法工艺。
对结构复杂的铸件,可用V法加树脂砂或V法加消失模复合工艺。
V法工艺前景看好。
三我厂V法工程概况
1 车间概况
我厂铸钢,源于1969年老厂0.5吨电弧炉。
1982年新厂建成投产,铸工车间几经调整,仅保留铸钢,采用CO2硬化水玻璃砂造型水爆清砂工艺,配有1.5吨电弧炉1台、1吨一拖二中频炉1台。
2005年11月,简易10吨/时呋喃树脂砂生产线建成试产。
2007年5月,装备公司规划我厂以刮板输送机为主导产品,铸钢以槽帮为主,此后铸成630和764等槽帮。
2008年6月至9月和2011年9月至2012年3月又进行两次技改工程,改进树脂砂生产线。
截止目前,已铸造1250毫米以下的十几种槽帮和其它多种铸件。
2012年铸钢件产量达到2030吨,钢水利用率提高到66.3%。
但效率、成本和质量尚有一定差距,有待改进。
2 项目依据
2011年3月以后,组织人员去19个单位调研。
看到V法铸造工艺简单、质量较好、成本较低、比树脂砂至少降低500元/吨。
因此,要优先使用V法铸造工艺,力争过渡到以V法为主,树脂砂为辅。
3 技改原则
1)尽量利用现有厂房和设备,合理布局,统一规划,分期实施。
2)不影响现有树脂砂系统的正常生产,稳步过渡。
4 技改方案
1)砂处理系统。
暂用原有树脂砂系统,根据发展情况再行改善。
2)造型系统。
采用两工位的简单配备,一期改建一工位。
3)真空系统。
采用2BE-303-55KW真空泵,地沟式管道布置。
4)熔炼设备。
启用中频炉,过渡为中频炉为主,电弧炉为辅。
5)平面布置。
详见【V法铸造平面图(4)】。
准轨铁道以东,为V 法铸造场地。
一期利用原有小树脂砂库改建一工位造型线,二期新建二工位造型线。
中跨造型,北侧安装真空泵。
北跨合箱、浇注和落砂。
6)设备联系。
详见【V法铸造机械联系图】。
5 工程进度
2013年初编制项目方案,5月选定设备制造厂,6月选定模型制造厂,7月进行土建工程,8月设备安装,9月调试生产764铲板槽帮。
四下步想法
1 一期完工,生产764铲板,熟悉操作达到1小时造1型。
2 进行二期工程,造型达到2-3箱/时的能力。
3 优化工艺,改进操作,提高质量,降低成本。
增加品种规格,逐步扩大V法造型比重。
4 熔炼设备,启用中频炉,逐步过渡到中频炉为主,燃煤退火炉改为台车式电热炉。
方便生产,改善环境,充分体现V法绿色铸造的优越性。